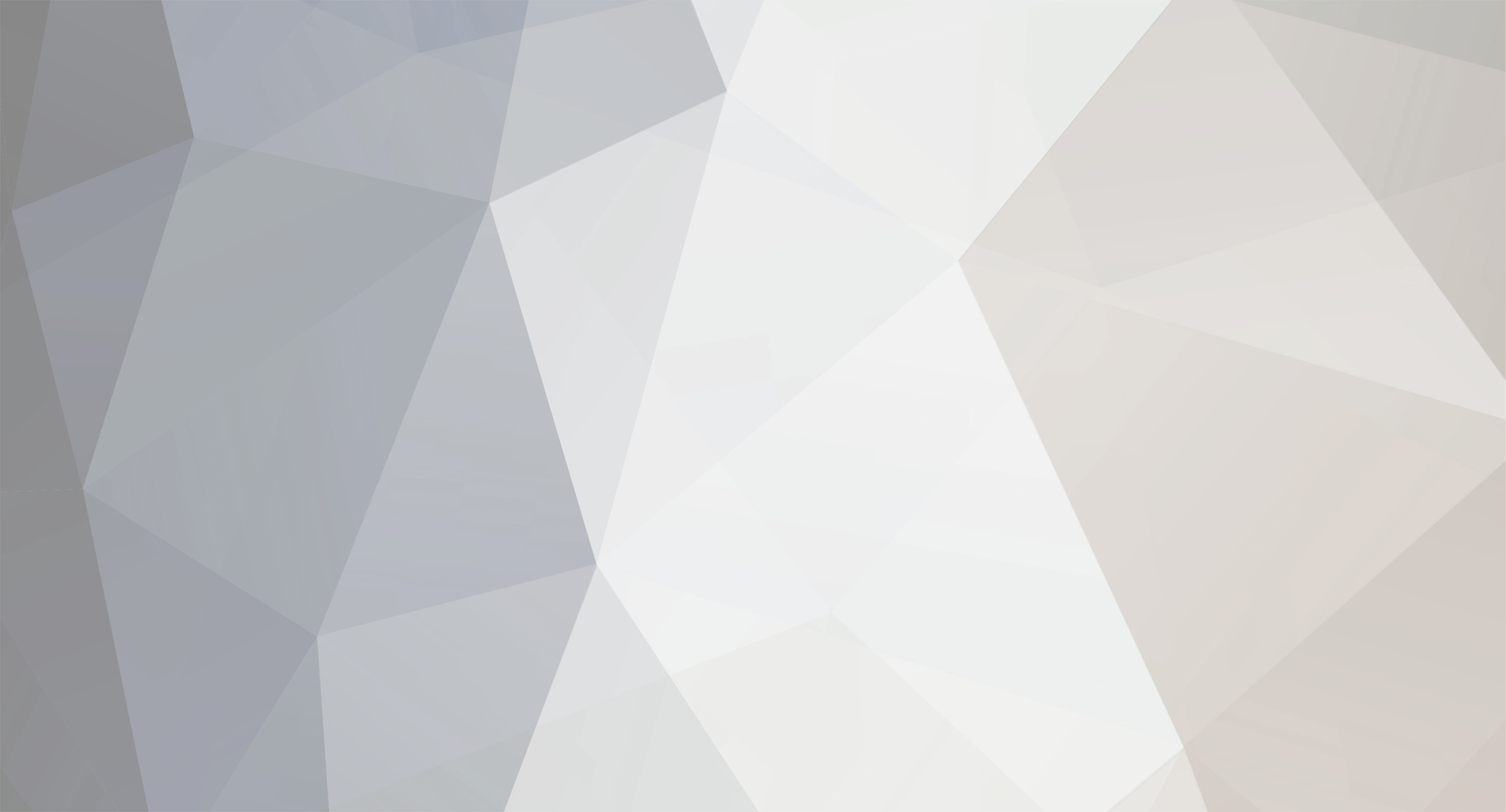
GTmike400
Members-
Posts
218 -
Joined
-
Last visited
Content Type
Profiles
Forums
Events
Gallery
Everything posted by GTmike400
-
6th Annual Hope it don't Snow Show 1-19-2013 Pics added 1-19
GTmike400 replied to Drgon63's topic in Contests and Shows
Is there a work in progress class? I would like to bring my Evo and its engine that I am working on. -
Dirk called me earlier and referred me to this build, and I have to say Bill, this is some fantastic craftsmanship. Great machine work, and I can't wait to see more of the brass chassis.
-
I guess it looks alright for an air-head. I really like the windscreen frame you were talking about earlier. I guess you can build models after-all.
-
1/12 Top Fuel Bike (Larry "Spiderman" McBride)
GTmike400 replied to ScrappyJ's topic in WIP: Model Cars
Looking sweet man, those parts are awesome! -
Time Attack/Circuit Racer Mitsubishi Evo V
GTmike400 replied to GTmike400's topic in WIP: Model Cars
Finally I have time to post an update. The engine block is finally nearing completion. I added the ribbing to the side of the block using .010" brass sheet. I added the brass strips into the slits I cut earlier to help hold the ribbing in place. After all 9 pieces were fit, I soldered everything together and sanded the edges. In this picture you can see I also added the small bosses on the side of the block for accessories and engine mounts. -
Time Attack/Circuit Racer Mitsubishi Evo V
GTmike400 replied to GTmike400's topic in WIP: Model Cars
Thanks for the kind remarks, guys. That is what I will attempt to do, keyword being attempt. It wont have bearings though, due to the tiny size. -
Time Attack/Circuit Racer Mitsubishi Evo V
GTmike400 replied to GTmike400's topic in WIP: Model Cars
Thought I'd take a break from the work bench and post a quick update. The other night I was in the shop until the early hours of the morning drilling a bunch of tiny holes and working on adding the block deck, as well as the front and rear plates. The first thing I did was solder a piece of .020" (.5mm) nickel silver sheet on the block. This will form the block deck. After soldering I began to drill holes using a .5mm drill with the sensitive drilling attachment for the coolant jackets and the head studs. After drilling I used a small 4 flute end mill to rough the block deck to size. I still need to be able to bolt the block upside down to my fixture plate for a few more machining operations so I plunged into the cylinder bores just enough to get to the threads. Using files, sand paper, and lots of beer I began to shape the block deck to the correct profile. The side closest in the pic is the finished profile. The opposite side still needs to be shaped, the pink markings are to indicate where to remove material. Once all the machining is complete I will remove .005" from the block deck to achieve the correct thickness. Now back to the bench to work on the ribbing and external bungs. Enjoy! -
Time Attack/Circuit Racer Mitsubishi Evo V
GTmike400 replied to GTmike400's topic in WIP: Model Cars
Last week I finally had a great opportunity to get some work done on the motor. Over the years I have remained in touch with my old high school engineering teacher, so in exchange for guest speaking in his classes I get to use the CNC mill on occasion. I used the CNC mill this passed week to machine out the crankcase. I’ll let the pictures to the talking: Roughing pass. The first roughing pass. After investing so much time in the block, I like to always double check my tool paths. I marked the block with a marker, then ran the tool path removing only .0005" to make sure it was where it needed to be. Finishing pass. After over 6.5hours of run time: Just a size comparison next to a US 1cent. I know the question is going to be asked, "Wont this all be covered?", and the answer is that I do not know yet. Right now its just a fun challenge for myself to expand my capability. Enjoy. Not a problem, I hope to meet you too one day, Jay. Hopefully at the NNL South in November! -
Time Attack/Circuit Racer Mitsubishi Evo V
GTmike400 replied to GTmike400's topic in WIP: Model Cars
Jay, no problem. Questions are fun to answer. The block has #4-40 threads through the entire block, that allows me to secure it right-side-up and upside-down on the fixture plate. The fixture plate is a must for machining something with such weird shapes and nowhere to pull a positive dimension other than the bores. Annealing is a process of normalizing the crystallization structure in the material. To anneal brass and copper a torch can be used to heat it. I used oxy-acetylene because it was available, but Butane, Propane, or MAPP will work just as well. When heating the material, be patient, if you heat it too fast you'll warp it or blow a hole in it. Heat it slowly and constantly move the heat around over the piece so that the entire piece is heating evenly. Continue the heating process until the material starts to become a dark cherry red (like in the pic above). Keep in mind it will not stay red hot for long at all, so just move the heat around (or you'll distort the material). Once you have evenly heated the entire piece back the heat away. Do NOT quench the material, let it air cool. Now you can work the piece pretty easily! Hope that helps, Jay. -
Time Attack/Circuit Racer Mitsubishi Evo V
GTmike400 replied to GTmike400's topic in WIP: Model Cars
Thanks for the support. Today I had some time to work on the engine block today. Just started machining out the area for the mains. First I used a center drill to position the beginning of the hole accurately and precisely. I use a drill that was slightly under-size. Drill bits tend to drill over-size in metal, so using a smaller drill bit is usually a safer route. Once the girdle is machined I will clamp it to the block and line bore the mains with a reamer. Using a 1/8" end mill I started to remove material for the mains and girdle. Enjoy. -
Time Attack/Circuit Racer Mitsubishi Evo V
GTmike400 replied to GTmike400's topic in WIP: Model Cars
Today I took a break from working on the engine block. Decided to work on something different - the doors. Unfortunately when I cut out the doors out, one of the passenger side window frames warped, so I'm going to attempt to build the doors out of brass now. Not only will the window frames be stronger in brass, but the door skins will also be a more accurately scaled. I first made a steel form to shape the brass over, then proceeded to anneal the brass. Annealing the brass with a torch. The steel form used to shape the brass over. Thanks for looking, hope to get back to the engine block this week! -
Time Attack/Circuit Racer Mitsubishi Evo V
GTmike400 replied to GTmike400's topic in WIP: Model Cars
Hey Jay, I don't have any formal training or schooling. I've just been figuring things out as I go, sometimes through books and discussions with other people. -
Time Attack/Circuit Racer Mitsubishi Evo V
GTmike400 replied to GTmike400's topic in WIP: Model Cars
Thanks for the great compliments, gents. I haven't had much time to do any work on the model since I have been rather busy with work and classes. However, I thought I should post what the block should look like once completed. Today at work I did a quick rendering of the 3D model I made to design the block. Tomorrow I hope to go into the shop and get some machining done on some jigs and fixture plates! -
Time Attack/Circuit Racer Mitsubishi Evo V
GTmike400 replied to GTmike400's topic in WIP: Model Cars
Nickel silver is not cheap compared to other metals. A 6" piece of 3/8"x3/4" bar stock is about $20. However, with the cost the advantage is having a part that is silverish in color and is able to be soldered. I had considered machining it out of 6061 but soldering 6061 is difficult, at best. Since I decided to machine the block out of multiple pieces, I decided to use something I can solder the other parts to. If I did the block out of 6061, I could glue the parts to it, but I just don't like the idea of gluing metal; it's not very resilient. Machining nickel silver appears to be easy, but it takes a lot to get a nice surface finish. It galls really easily, do your speed has to by high and your feed has to be slow and consistent. Don't bother using a tool that's been used before, it will just gall badly and make a mess. 6061 is a lot easier to machine, but for this application, nickel silver is better suited. As stated, the main advantage of nickel silver over 6061 is its easy to solder. Hope that helps, Jay. -
Time Attack/Circuit Racer Mitsubishi Evo V
GTmike400 replied to GTmike400's topic in WIP: Model Cars
Jason, the door frames are quite simple really; they're just built out of various sized strips of styrene. The main shape of the door frame was cut out of .015" styrene sheet, then strips ranging from .010x.020" to .100x.125" were used to build up the structure. Some brass rod was used in the B-Pillar to aid in holding its bent shape. If you flip back a couple pages you can see that I used .100x.125" strip styrene for the rocker area and drilled holes in it on the mill. Hope that helps. Jay, the block is machined primarily out of nickel silver. Nickel silver is a form of copper/silver alloyed brass, sometimes referred too as white brass. Some of the pieces are machined out of regular 360 cartridge brass. The parts out of 360 brass are parts that are not "wear" surfaces or surfaces that will remain unpainted. The nickel silver polishes out to a nice stainless steel color so the cylinder bores, crank journals, block deck, etc, once completed will look similar to a real engine and I wont have to worry about paint being scraped off from the motion of the pistons and crank. -
Time Attack/Circuit Racer Mitsubishi Evo V
GTmike400 replied to GTmike400's topic in WIP: Model Cars
I went up to a friends over the weekened to work on models while we watched the 24 Hours of Rolex Daytona and managed to get some work done on the engine. I added some 1/32" tubing to the side of the block for the coolant to flow through. I also did work on the seat and right side door frame, but nothing worth posting yet. I needed a new desktop, so I assembled what has been completed so far (which isn't much) and took a couple shots. Thanks for looking. -
Time Attack/Circuit Racer Mitsubishi Evo V
GTmike400 replied to GTmike400's topic in WIP: Model Cars
No worries, Cliff. Dirk and I go back several years; we have a sick sense of twisted humor. Thanks for the compliments. -
Time Attack/Circuit Racer Mitsubishi Evo V
GTmike400 replied to GTmike400's topic in WIP: Model Cars
Jay, thank you for one of the most humbling comments I have ever received. Dirk is a great guy and I have learned a lot from him, you're lucky to live so close. I really do not know what to say except thank you for the kind remarks, it truly is honoring and humbling. I told Dirk to invite you to our Southern NNL in November, it would be great for you to come and bring your work. I would like to meet you someday. What was I saying about Dirk being a great guy? I take that back. -
Eh...It's okay, I guess. I've seen better.
-
Time Attack/Circuit Racer Mitsubishi Evo V
GTmike400 replied to GTmike400's topic in WIP: Model Cars
Thanks for all the kind remarks, they are very motivating. For the past week I have been busy working on the block. Unfortunately I've spent so much time working on the block I haven't had much time to post an update, so now its time for a large update! To machine the angles on the right side of the block I needed to make some sine blocks. Sine blocks are fixture blocks with calculated angle to fix an object to. I've found turning the head of the mill is not the most accurate method to machine angles, so I opted for this route instead. After working on the block for awhile needed to machine the pieces that hold the counter-balance shafts. I used two pieces of round brass stock because I am lazy. Brass can be soldered to nickel silver, and these brass parts will not be wear surfaces like the journals and block deck. The first piece was drilled on the lathe. After drilling the first brass piece I mounted it in a square fixture with a C5 collet to hold the brass stock to machine it into half of a square. Once the first piece of the counter-balance shaft "casing" I proceeded to the next piece, I turned it down to the proper diameter first. After turning it down to the proper diameter I used the sensitive drill to drill it. The two pieces. I then separated the second piece from the stock and soldered it to the first piece. After soldering I did the final machine passes on the mill to make it the appropriate size. After making the two casings for the counter-balance shafts I went back to the block to machine the notches to hold the counter balance shaft. While I had everything setup in the mill I went ahead and machined some .010" slots to do the block ribbing later. The first counter-balance shaft casing and the engine. After making the second counter-balance-shaft casing I soldered it together: Thanks for looking, enjoy! -
Time Attack/Circuit Racer Mitsubishi Evo V
GTmike400 replied to GTmike400's topic in WIP: Model Cars
That was all done at work. But last week my old teacher called me to come teach a CNC class today, so yes. Thanks Bob! -
Time Attack/Circuit Racer Mitsubishi Evo V
GTmike400 replied to GTmike400's topic in WIP: Model Cars
The phenolic guide was removed after all the holes had been drilled. The primary purpose of the holes are so I can locate tubes to solder to the sides of the block. My workbench was a mess, and lots of Redbull was needed. The block was the flipped on the sides to mill away material exposing only half of the holes that were just previously drilled. This will be the rough deck width. I also began drilling .0625" x .0075" counterbores to locate the freeze plugs later on. Next I need to machine some sine blocks to machine some funky angles on the side of the block. That's all for now. Enjoy. -
Time Attack/Circuit Racer Mitsubishi Evo V
GTmike400 replied to GTmike400's topic in WIP: Model Cars
I've been quite busy in front of the mill recently making lots of chips. The engine I am machining is a 4G63T. Each part is designed in 3D against tons of reference pictures (thanks to Jimmy for collaborating pictures) and measurements. I've started with the block first as it is the most crucial piece. The block is being machined out of nickel silver. Nickel silver was chosen as the material because it can be soldered, and it has a silverish appearance, among many other reasons. The first piece to machined would be a fixture plate that I can attach the block to as a reference. The fixture plate is standard 6061 Aluminum. I first qualified all 6 surfaces, then drilled and countersunk clearance holes for a #4 screw flat head screw. An location index was drilled in the upper right corner that was reamed out to .1250" to use a dowel pin to locate the fixture in the vise to ensure that all dimensions were accurate. After reaming and drilling, the top and bottom surfaces were once again qualified to prevent any distortion from drilling. Moving on to the engine block. Once the engine block was roughed out (.020" over) it was tapped with a 4-40 thread where the cylinder bores will be located. The 4-40 threads max diameter is smaller than the diameter of the bore, therefore the threads will be removed as the block is finally bored. A drill guide was machined out of .125" linen phenolic to aid in drilling 1/32" diameter holes in the block. The phenolic is much easier to drill through than the nickel silver yet rigid enough to provide support of the drill bit. The phenolic was then glued to the block using spray adhesive. The use of a sensitive drill was necessary to drill the small 1/32" diameter holes in the block. Since sensitive drill uses a small 3 jaw drill chuck, the drill bit needed to be dialed in correctly using a dial indicator to remove all runout within ±.0005". After the drill bit was indicated I began drilling the holes in the block through the phenolic guide. The phenolic guide really helped support the drill. I used a syringe to apply lubricant to the work piece because the squirt bottle I typically use was flooding the piece too much. -
Time Attack/Circuit Racer Mitsubishi Evo V
GTmike400 replied to GTmike400's topic in WIP: Model Cars
Thanks for the kind remarks. It's a Bridgeport knee mill that I have at work. Here's a picture: I use the one on the left to make the bottom part of the door frame. It's not the mill I normally use for model parts, but since I was at work I decided to try it out. We also have 15" Clausing lathe at work that I plan to use too. At home in my shop I have a Sherline mill and lathe which is what I normally use for model stuff. -
Time Attack/Circuit Racer Mitsubishi Evo V
GTmike400 replied to GTmike400's topic in WIP: Model Cars
It's been some time since I've had a chance to actually sit down and work on this project. After talking with my mentors and friends at the Southern NNL I was inspired to start working on this again, but havent had time with school. Finally the semester is nearly over and time to get some work done. I had a few minutes at work yesterday so I started drilling out some .075" x .125" with a 1.8mm drill for the bottom of the door right door frame. The door frame is almost complete. I need to fill a few spots with some Evercoat but it is too cold outside to mix any putty. This needs to be done before I can make the flange that goes around the frame as seen on the opposite side. A couple pictures of the chassis with the door frames mocked up. They will be glued to the chassis permanently once they are finished. Note, the section for the exhaust will be cut out once the frames are permanently attached to the chassis. One last "mean" shot. Enjoy!