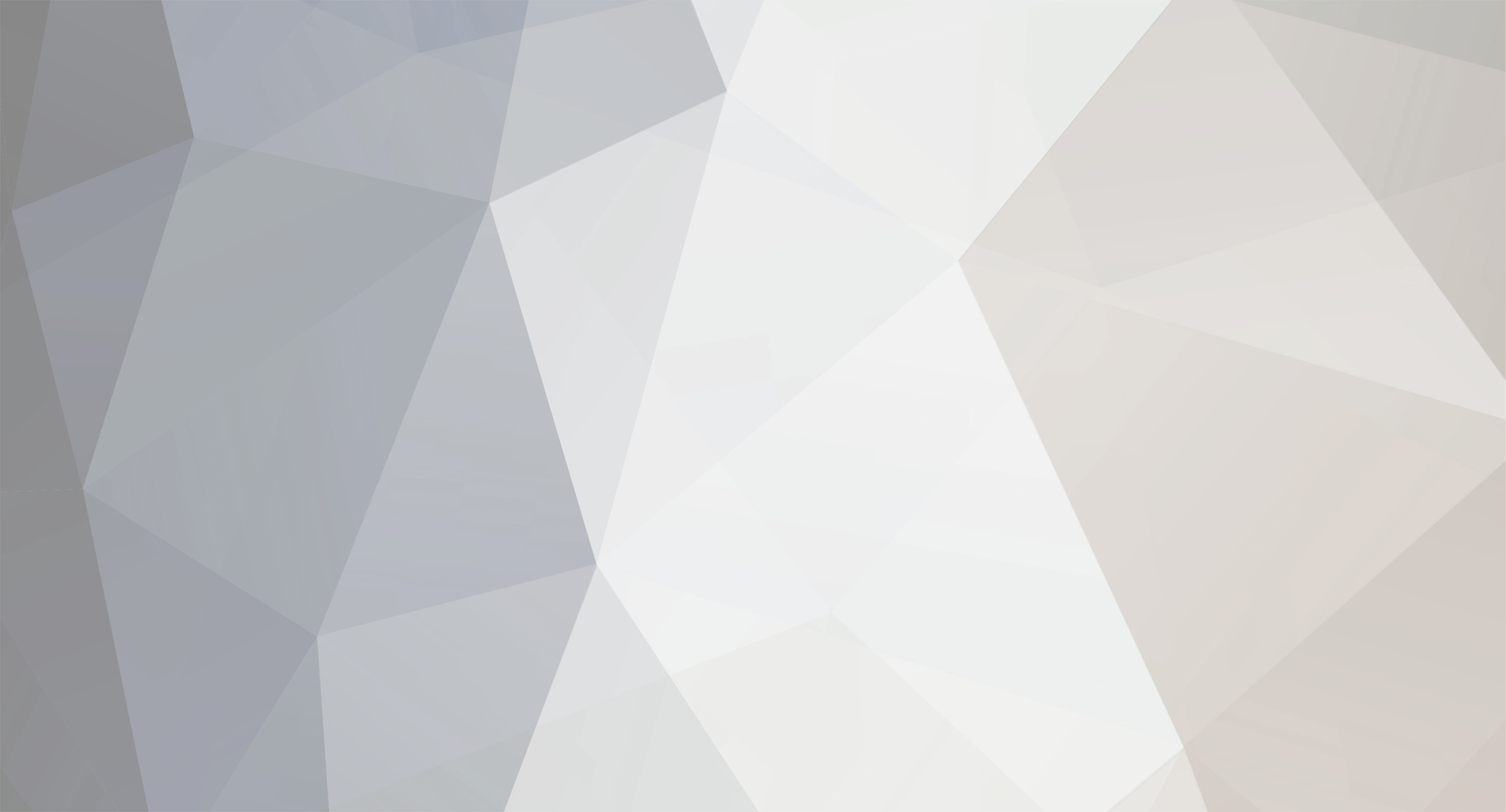
DaytonaTim
Members-
Posts
133 -
Joined
-
Last visited
Content Type
Profiles
Forums
Events
Gallery
Everything posted by DaytonaTim
-
The New TDR 427 Roadster Kit
DaytonaTim replied to DaytonaTim's topic in Car Aftermarket / Resin / 3D Printed
Actually the Miss E is offered in both 1/12 and 1/16 scale. I promise after we get this TDR 427 Roadster offered up to the public, hopefully before Christmas, I will seriously look at taking some of our products over to 1/12. These new rapid prototype processes should allow us to offer something up that will have an acceptable surface finish to them. Pssst......In case you have not heard.......TDR is having a 20% off everything we offer sale through the end of October.......just go to TDRcatalog.com to see. -
The New TDR 427 Roadster Kit
DaytonaTim replied to DaytonaTim's topic in Car Aftermarket / Resin / 3D Printed
Hey Syd, All the parts on the new 427 Roadster will be brand new and unique to this kit. -
The New TDR 427 Roadster Kit
DaytonaTim replied to DaytonaTim's topic in Car Aftermarket / Resin / 3D Printed
Len, you are working in the 1/12th scale, right? If so, I think there is a lot of promise using these new rapid prototyping processes to generate the 1/12th scale parts. The problem is that our parts are designed to be built at 1/8th scale. When we scale the parts down to 1/12 everything scales down including the thickness of the parts. The thickness is what can cause a part to not be printable. So, what I am driving at here is that we have discussed trying to offer more of our parts in 1/12 scale and this new RP process may make that possible. BUT.... we may have to redesing the parts to make the thickness printable and this takes time. Right now we are busy, to say the least, getting things designed in 1/8 scale for the 427 Roadster. I don't know when we could try this stuff in 1/12 but keep asking us and if we get some time we may be able to fit it in. -
The New TDR 427 Roadster Kit
DaytonaTim replied to DaytonaTim's topic in Car Aftermarket / Resin / 3D Printed
Ok, I wanted to show some individual pictures of some parts and talk about the new materials too. The tires and wheels were made out of a nylon material that is fused together with a neon laser. I had to place these parts under my 3X magnifying glass to find the half a dozen layer lines that exist. The material is very porous and needs to be sealed before painted. I sealed the tire with that spray sealer "Kilz" that you can buy at Lowes. It worked great and boy....does that stuff ever cover!!!! After the sealer dried I shot it with the black paint and then picked out the raised lettering with some white acrylic. Since the sealer worked so well I thought I would try just some high build primer on the wheels since it has more of a self leveling quality to the paint. I sprayed it on medium-heavy and let it dry and then I shot the Magnezium paint and some matt-clear coat and it turned out pretty good. Now the suspension parts are made out of a different material that is printed up very similar to an injet printer. Each layer is built up and cured with a UV light. Now this material has a waxy coating on it that appears to be able to be washed off with soap and water. I am waiting to get some new revised parts in and I will test cleaning the obsolete parts in some Blech-White, just like you do resin parts. Depending on how this test comes out will determine if we can use this material for production of some parts. If you cannot paint the parts there aint no sense putting them in a kit. So why do we even mess with these "waxy" parts...... the detail is incrediable and the parts are much stiffer than the fused nylon, so it has its advantages. All the suspension parts are made from this material. When I modeled the suspension parts I set them up so they would have a 1/2 hole in the arms where they mount to the chassis. I took the parts strait out of the box and inserted a 1/16 styrene rod (1/2" 1:1 scale) through the hole.....no drilling and no forcing anything. It was perfect!!!! Take a look at the suspension pictures and you can see that the holes are clean as a whistle.... a drill bit never touched any of these parts....now that is detail and even the styrene molders cannot come close to this kind of detail. So we are still doing some testing and research on these new materials in order to bring you guys something that will really knock your socks off!!! Well enough of the gabbing, here are some pics to look at. Take note at the small details that come through and remember that no sandpaper or drill bits touched any of these parts. All I did was wash them off in some soap and water. Look at the tread detail and the raised lettering on the tire! These shocks are designed to be a main structural member of the suspension part. So they had to be made strong. They are designed to accept brass rods that insert into one and other to form a very strong adjustable shock unit. The modeler can adjust the lenght of the brass rods to adjust the ride hieght to the desire location. Also the springs are metal and they look just right Now look at the details in this main carrier unit for the rear. Look at the bottom and you can see the the clamps that are manufactured in, even the split is ther that allows the clamp to work in the real world. Also, look at the "ears" on the brake caliper mount.... and look at the clean holes too!! This shows the mounting hole for the suspension arm. Remember no drill touched this part. -
The New TDR 427 Roadster Kit
DaytonaTim replied to DaytonaTim's topic in Car Aftermarket / Resin / 3D Printed
I know when I finally build mine I plan on having a cubside body next to a detailed chassis. I may be biased, since I worked up the chassis, but I think hiding the chassis under a body would be a crime. -
The New TDR 427 Roadster Kit
DaytonaTim replied to DaytonaTim's topic in Car Aftermarket / Resin / 3D Printed
Comp hit the nail right on the head. TDR's job is to provide the modeler the parts they need to help them build whatever specific car they desire. If the modeler finds they need a specific part to build the car of their dreams they need only contact us and we can talk it over. Just Ask Comp1839 about his toploader rear end. -
The New TDR 427 Roadster Kit
DaytonaTim replied to DaytonaTim's topic in Car Aftermarket / Resin / 3D Printed
Cato: One thing to remeber about TDR Innovations.........we are not locked in to one design like all the big model companies are. We are internet based and dynamic. We don't sell one box of parts. We are considering offering this kit in multiple Sub-kits that will all work together. So, let's say customer X does not like the ole Blue Dot bias ply tires.....say he wants some low profile moderern tires.....well he will not have to buy the Blue Dots......instead he can just purchase the tires he wants....No sense buying something you do not want. There will be more on this as things evolve but let's just say that there will be many many versions of this kit that the customer will be able to build as money and time become available. -
The New TDR 427 Roadster Kit
DaytonaTim replied to DaytonaTim's topic in Car Aftermarket / Resin / 3D Printed
Well that is where the Mad Fabricator comes in. We printed out a rapid prototype version of the TDR 427 Roadster body..........this is the expensive body......... and right now the Mad Fabricator is finishing out this RP body. Once it is finished he will pull some fiberglass molds from this finished RP body and will be able to produce "finished" fiberglass bodies that will cost a LOT less than the rapid prototype bodies and will require minimal finishing. -
The New TDR 427 Roadster Kit
DaytonaTim replied to DaytonaTim's topic in Car Aftermarket / Resin / 3D Printed
Here are a few pics of our "workhorse" prototype. I am using this to test fit all the parts to. This is the first time the parts are actually coming together in real life. We are just checking them out to see how they fit up and we are testing some new rapid prototyping materials. All the parts in white are the new RP materials and let me say I am very pleased with them. The tire and wheel that are painted had absolutely NO prep work done to them at all. All I did was shoot a sealer on them and painted them. Well enough of this, here are a few more pictures that say way more than I want to write and you want to read at this time. -
Well It was bound to happen........... TDR Innovations is finally bringing you our first complete model kit!!!!! We have only existed, in our current configuration, for about a year now. In that time TDR Innovations has brought you over 100 1/8th scale model kits. To date all of our kits have been of engines, suspensions, tires, wheels, trannies and frames that you could use to supplement existing kits that are on the market. Well, no more!!! After the Christmas sales rush of 2009 calmed down, Don posed the question to us, "What is going to be our big project this year?". Well it did not take long for all the partners to agree that we needed to come up with something big and that that something should be nothing other than the TDR 427 Roadster you see here. We have been keeping it secret until we were ready for prime time and that time has come. As I am writing this post, the Mad Fabricator is diligently putting the finishing touches on the body master. AJWheels is putting the final touches on that beast of a power plant and tranny. I am doing the initial fit up of all the chassis and interior components. We do not have a final part count yet, but the number of parts should well exceed 200. These parts will include a complete and detailed adjustable suspension, complete CNC fabricated interior sheet metal components (made from .007" thick aluminium), 427 SO engine with multiple induction setups, and a fiberglass body that can be easily tweaked to make multiple versions of the body (street, Semi-Comp, and Comp) Right now, as far as the chassis design goes we are focusing on the street version. Once that is complete we will move on to the more radical versions of the Roadster. Well that is enough talk for right now. Here are some pictures of the CAD models to start things off. There is more to be coming real soon.....I promise!! I am sure that AJWheels and the Mad Fabricator will be posting up some of there work too.
-
Well, I finally got around to getting the pics of the steeing wheel posted up to a host. I forgot you have to do that on MCM. So here they are. I decided to delete the 6 mounting bolt holes, in the center of the wheel. They should be covered up by the horn button anyway. Here are the metal parts of the wheel. The notchin the rim section are used to locate the spoked part of the wheel Here are how the wooden parts will be delevered. The modeler will have to sand the back of the wood, about 1/16", until the rims fall free. I carve the rims in some 3/16" thick wood veneer samples of exotic hardwoods.
-
Ok, I think I finally have this thing figured out. I finally found a good source of exotic hardwoods, a ready supply of nickel silver sheet metal, I have the mounting process figured out and I rewrote the CNC files so I would not be chucking anymore parts across my garage!!! So, I would like to announce that we at TDR have decided to start to offer these wheel kits for sale, I have a couple of ads up on Ebay right now. I will post up some pictures very soon.
-
Hey Greg, here is a link to a thread I did for a 1/18th body I finished out. It may prove helpful. http://docs.google.com/fileview?id=0B0brAPVJl8AhNTIwY2NhYzgtMzZhOC00ZjU2LWJhNzUtY2ZjZjY5MWZkZGVl&hl=en&pli=1 Also, if I can be of any help please do not hesitate to ask. Tim
-
Yes, I have seen his work before. As a matter of fact it was his steering wheel that inspired me to try my own version. The Motto Lita wheel, which I am working on replicating, actually has one solid grain running across the wheel. I have seen the segmented wheels too but this wheel is different. Here is a picture.
-
Now that is the kind of information I need!!! Thanks Cato!! Is your car a kit or the real thing? It looks very true to the original? Please don't take any offense the the "....kit or real thing....." statement. It is meant as a complement. I cannot see any differences!!! Thanks again!!
-
Thanks guys. I would like to work up some kits. I still need to work out making the rivit holes and then get some good material to use. I found some thick veneers that I can order for the wood. Since nobody has offered any suggestions on the wood type I will just get a variety pack and take pot luck. I have been doing some digging around on the type of metal to use and I came across a "nickle silver" metal. It looks a lot like brushed aluminium but it can be soldered. I may give it a try. Nothing like a true polished metal to really set the wheel off. Thanks David. I spend way too much time modeling things that never get build. This is kind of like therapy for me.....but with out the bill at the end of the month. We, TDR, have been looking into some PE work. It is possible that we may try some in the future, I thought a generic auto parts sheet might go over good. You know, stuff like true scale automobile washers, wormscrew clamps, guages........ stuf like that. It is pretty expensive, about $500 for the first sheet. Maybe carving them out on the mill will let us test the waters and see what the market is for PE before taking the big money plunge. Hey David, how is that 1/12 RP project coming? Have you made any headway on it yet? Cato, those were my thoughts exactly. I set this wheel up with a 3 inch dish (1:1) is that too deep for a Cobra? Does anybody know what the correct dish depth is for a Motto Lita Cobra wheel? If I am going to do it I should get it right the first time. One thing about it thought, the dish is somewhat adjustable. All you have to do is trim the spokes a little shorter and not bend them so much. If anybody has the correct dimensions for the Motto Lita wheel please let me know.
-
Well tonight I decided to up the challenge a little. Don asked me if I could maybe make the spoked part out of brass or aluminium. Since I had some .010" brass laying around I figured I would give it a try. I have never cut any metal on my mill before so this was a first for me. It did not turn out half bad. Not as good as a PE sheet but nothing that a few brushes of 400 grit sandpaper could not fix. I also decided to try and make the spokes a little more fancey so I put some cutout in them. It kind of takes away the "clunkyness....." of the last one. I still have to work on the wooden parts some. I may have to manually program something to bore the rivit holes. You can see the mill cut a few of them but not all. This is because the tool path just happened to pass right over the center of the hole so the .03125 end mill was able to bore them. If it does not pass directly over the center then it wont cut them. Any way here are some pics
-
Could that be a water cooled, oil cooler, on the front of the oil pan?
-
This thing is really working out!! I cut the front side of the steering wheel, the wooden face, just like I did the back. Then I tried something new and layed out the "metal" outer ring of the wheel. The part that gets sandwiched between the wooden parts. Then I layed out the spoked center part. I layed them out in the computer as just flat "sheet metal" like parts, and cut them out with the CNC mill. It worked perfectly. I cut them out of .015" styrene plastic. Then I just bent the spoked part of the rim up and glued it to the outer ring. Then I just glued the two wooden parts on. It all fit up perfect right out of the gate. I have attached some pics. It is hard to see but there is a plastic ring laminated between the wooden parts. I am wanting to try this out with some better wood. I figure since it is 1/8th scale I need a nice tight grained wood, so the wood grain will look in scale too. Does anybody have any suggestions. I was thinking mahogony might work. I only need the wood to be about 1/8" thick to cut the parts out of, so maybe a heavy veneer would work. I am curiouse what people think about this wheel. I don't know if anybody would be interested in purchasing one of these, through TDR. Any input on size, wood, or designs would be greatly appreciated. If enough people express interest I will try and work up some kits to put in our catalog. Anyway, here are some pics. Now remember this was just a test mule to see if this technique would work. No attempt was made to fancy up the design just yet.
-
Plastic Surgery for the 1/8th "Big T"
DaytonaTim replied to GrandpaMcGurk's topic in WIP: Model Cars
Hey Don....looking pretty good!! With all those holes in the chassis that thing should be able to whistle "My Little Deuce Coupe" or maybe something from the Beetles (keeping with the British origins of the Jag) while it is going down the road.... -
Hey guys. I have been pretty quiet lately on the forum. Been working on some around the house projects and have not had much time for modeling. On top of that I have been working on a "Super Secret" project for TDR. But this weekend I found some time to get back to the modeling bench......sort of I have been wanting to try an experiment and try using my 3 axis CNC mill to carve out a wooden steeing wheel in 1/8. Well I modeled one up in the computer, shook the cobwebs out of the CNC mill (I have not used it in about 2 years), found a scrap piece of pine laying around, and started carving it up. It did not turn out half bad for a first attempt and for using soft pine. Now I am going to have to try and find some nice hardwoods to carve this thing out of. Mind you, this is just the back half of the steering wheel. I did this half because it has the finger grips on it and I figured it would be the one with the most features. If I use some smaller tooling I should be able to get the rivit holes cut into the wood too. Putting some nice brass rods in them sure would set this wheel off. Oh, as far as the center, spoked part of the wheel goes, I have that figured out already and I will post it up when I get the chance to make one up. It wont be made using the mill, no it will just be cut out of some styrene. Anyway, here are some pic showing the machining process. I just brushed the wheel with some sandpaper and applied some stain I had laying around the house. I am sure it could be made to look a lot better with some hardwood, more sanding,using a sealer and what-not. This was just something quick and dirty.
-
New TDR Products and REVIEWS
DaytonaTim replied to arick's topic in Car Aftermarket / Resin / 3D Printed
I have actually found that using a Dremel drillpress works really nice on these rapid prototyped parts. I don't use the drill press in is usual way. Instead I just let the Dremel tool run in the drillpress and grip the part with both hands and move the part to the bit. By holding it in both hands you have a lot more control so when the bit "bites" into the material it does not jerk it out of your hands and cause problems. -
Now there is the beginnings of one heck of a buildup. The possibilities are endless!!!!
-
I managed to work in a little sanding today between the family activities. I wet sanded with some 400 grit paper and tried to concentrate on the areas that are hard to get to, so were missed on first two sanding passes. The primer really lets you see these areas. I tried to sand off most of the primer to reduce its buildup and still fill in the low spots. I also added little tabs to the door, hood, and trunk openings. This let these parts be placed while I was sanding to reduce the chance I would round off the edges around these openings. I will use these to mount these parts for final assembly. Here are a few pics to show where I sanded too.
-
LOL....David......keep the suggestions coming and don't assume I know anything.....I have only been back to building models for about a year now. So I have everything to learn!! I swore off of models when I was about 13.....that was about 35 years ago. I had just completed an old 1926 Mack truck model that I had spent about 2 months building, 2 months is a lifetime when you are 13. I had just put it up on my dresser for display........when my 5 year old cousin came to visit.......... It could not be salvaged.....parts were missing.....!! I guess I had modeling in my blood though and that is what got me into computer modeling. I can always make backups of computer models..lol. So I am just applying stuff that I have learned from 35 years of building 1:1 cars and I have never painted a car with a metalic paint. So please.....I need all the info I can get. I usually paint my cars black, just so I can find the bad spots in them. That is what I will probably do with this one. Paint it black, fix the bad spots, sand all of the black off, then paint it my final color. Just for laughs I have included a pic of my current 1/8th scale project with the AM in the foreground. LOL.....like I said before I usually work in the larger scale. Quite a difference in size, wouldn't you say!!!!! The Carb on the Allison is larger than the whole motor would be on the AM!!