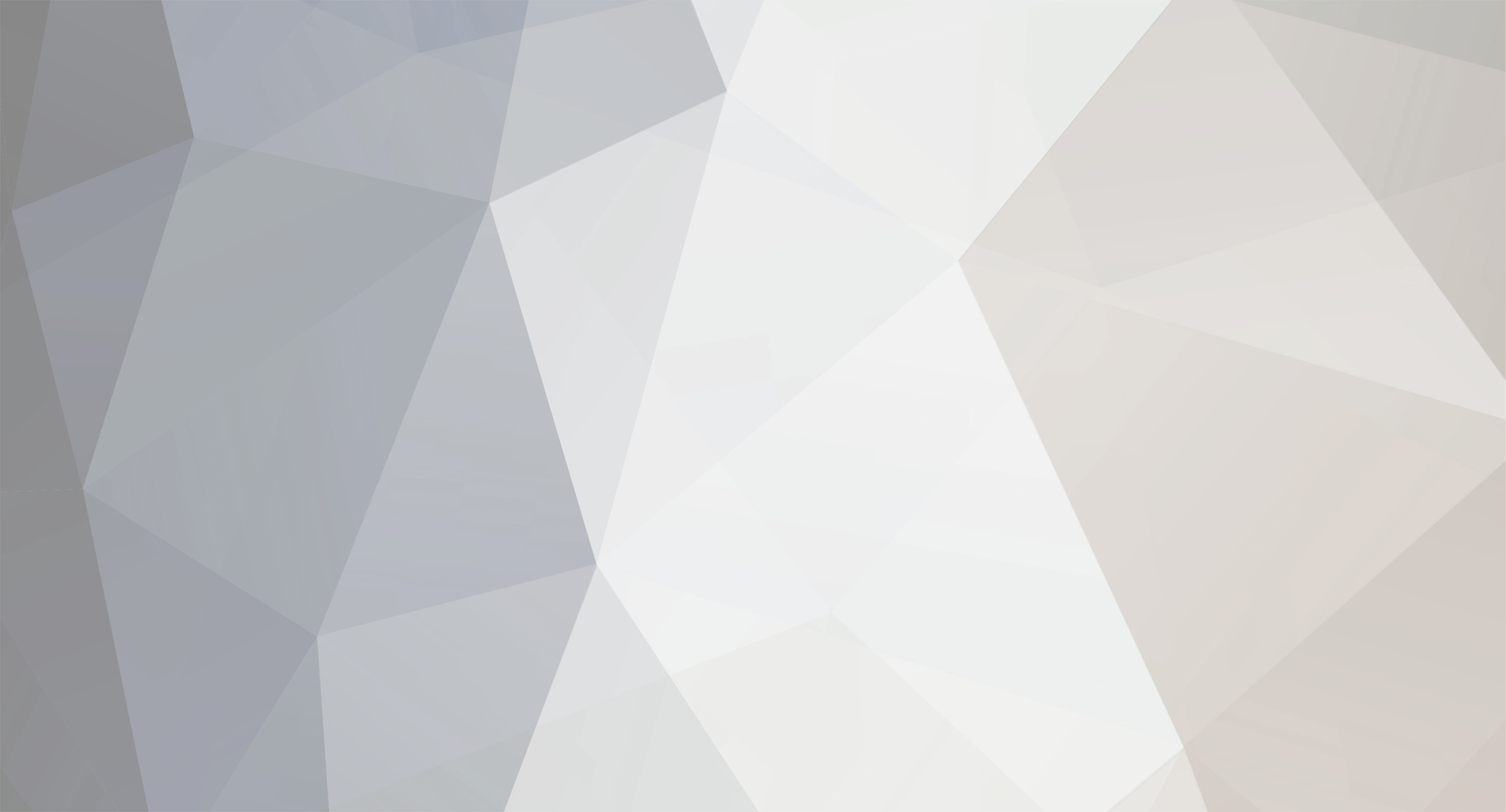
Biscuitbuilder
Members-
Posts
250 -
Joined
-
Last visited
Content Type
Profiles
Forums
Events
Gallery
Everything posted by Biscuitbuilder
-
The active ingredient in SuperClean is.............guess what? Sodium Hydroxide (lye), that time I looked at the label. Biscuitbuilder1
-
Drano, Liquid Plumbr, Easy Off (yellow can) all have, as their active ingredient, lye, or as it's chemically known--sodium hydroxide. This eats the aluminum vacuum plating (which is what model car chrome, in the kits, actually is), along with the clear protective coating, and the wet-look glossy base coat off the plastic entirely. The least expensive, AND in my experience, the easiest to use sodium hydroxide is Lewis Red Devil Lye, which comes in crystalline form, in plastic cans--find it at the supermarket in the middle of all the cleaning supplies. You simply add Lewis Lye crystals to a glass, china or plastic bowl of cool water (NEVER use aluminum vessels, as lye just gobbles up aluminum!), stir gently until dissolved, then just drop the plated parts in it, and watch the chrome disappear. Leave the parts there for say, an hour, and the base coat will be gone, or at least soft enough to be scrubbed away with an old toothbrush. Sodium Hydroxide in any form is highly caustic, will burn skin, and if you get it in your eyes, cause severe eye damage immediately, so hand and eye protection are to be a requirement. It rinses with water, and can be just poured down the drain as it not only is biodegradable (lye occurs naturally when wood ashes are soaked in water), but also helps clean sink drains. Just be sure to read and follow the instructions on the label. Price? I think about $2 a can--less expensive, and much lower fumes than sprayed on Easy-Off. Biscuitbuilder
-
Duesenberg Inc. never built any bodies of their own, although they maintained an in-house design studio, of which one Gordon Buehrig headed up for a few years, designing some of the most beautiful of all Classic Cars. Duesenberg Inc. themselves produced the rolling chassis with engine and complete mechanical and electric systems, the radiator and shell, cast aluminum firewall with dashboard mounted, steering column and steering wheel, fenders, running boards, splash aprons, headlights, driving lights, taillights bumpers, and of course, the distinctive 20" Dayton-built but Duesenberg-designed wire wheels with tires mounted. The factory also provided each coachbuilder a set of chassis drawings, showing the complete running chassis, with baseline dimensions for ease in engineering and producing the coachwork. While Duesenberg maintained, for several years, a catalog of body styles, none were completed except to customer order, and with that, colors, details, upholstery and trim were up to the customers' whims. In addition, the larger coachbuilding houses (such as Derham, Rollston, Willoughby, Murphy) also had their own stylists, and a couple of American coachbuilders were actually owned early in the J's production life by stylists themselves (LeBaron, Hibbard & Darrin for example). At the beginning of Model J production, in late 1928, Duesenberg Inc., upon receiving an order for a particular body style, might well order a couple of duplicate bodies to be built alongside the paid order, the extra bodies being delivered "in the white" (unfinished in primer only, no upholstery or trim) on the speculation that there would be buyers for them (and until the Depression tightened its grip on the economy, this worked pretty well!). Murphy Body Company of Pasadena, California most notably produced more than a few bodies which were for all intents and purposes identical, and certainly they had very distinctive touches that spoke "Murphy" rather forcefully, if politely. Most all custom coachwork of the day was composite in construction: A frame, made generally from ash, with perhaps a bit of oak here and there where extra strength might be needed, was cut, assembled, with the wood framing being shaped by planing, power sanding, even some steaming and bending, to get the wood frame to assume the general shapes of the particular body. This was then covered in either sheet steel or sheet aluminum, largely hand-formed by craftsmen, generally using planishing hammers and the English Wheel for shaping work--these tended to have little if any filler (which would have been body lead), the coachbuilder expecting the highest craftsmanship from their metal shaping artisans. Duesenbergs were arguably the most expensive cars ever done in this country (even compared to today, if one factors in inflation over the past nearly 80 years), with the Duesenberg-built chassis, drive train and identifying components priced at a nice, round, $9000 (more than the price of the top line Packard, or enough money to buy 18 Model A Ford Coupes, and have change left over to fill their tanks with 10-cent a gallon gasoline). The least expensive coachbuilt body might run about $5000, the famed 1933 Arlington Sedan by Rollston costing Duesenberg Inc. slightly over $20,000, bringing that car the nickname "Twenty Grand", by which most everyone today knows the car. Only the wealthiest of car buyers could afford one--the list of owners included chewing gum magnate William K Wrigley (4 Duesenbergs went to the Wrigley family), Mrs. John Jacob Astor, William Randolph Hearst bought a Willoughby Town Car for his mistress--the Hollywood actress Marian Davies; Howard Hughes, Gary Cooper (2 cars, including the first of two SSJ's), Clark Gable (2 cars), and San Francisco playboy financier George Whittel, who bought SEVEN Model J's 1929-33. Foreign buyers included the Maharajah of Indore (India), King Alphonso of Spain, King Zog of Rumania, Actress Greta Garbo. Truly the car for the rich, the famous and the discriminating, Duesenberg Inc.'s sole sales pitch was "He (or she) drives a Duesenberg, accompanied by sketches of the wealthy in poses such as the lady instructing her gardener about how she wanted her property to look, a distinguished-looking man of substance, smoking a pipe as he skippered his huge sailing yacht. Biscuitbuilder
-
Nice cars, zeb, but neither one is a town car, unfortunately. The top one is a convertible coupe, body by Derham, the lower one is a sport phaeton, body by Derham. For a town car, think of a limousine or sedan body, but with the top eliminated over the chauffeur's seat up front. Swanky cars, but definitely very formal, used primarily for driving one's employers to the club, a restaurant or nightclub (for a night on the town), or for going to the opera--in short, a car for what definitely were "society" occasions. Occasionally, town cars got used for touring, or long trips, hence the need for a trunk out back--but then, most closed cars used a separate, added on trunk, mounted on a folding rack, the trunk itself being removable when not in use. Biscuit
-
That kit is the 500K Coupe Limousine, as built for, I believe, Rudolph Caracciola, in 1935. JoHan issued that kit in 1965-66 time frame, right after the Sindelfingen Cabriolet. Original color was, I believe, maroon. Biscuitbuilder
-
Real or Model #37 FINISHED!
Biscuitbuilder replied to Harry P.'s topic in Real or Model? / Auto ID Quiz
I'm gonna go a bit farther, and say that it's the Pocher 1/8 scale Profile Coupe. Biscuitbuilder -
Trying to sort out classic kit quality
Biscuitbuilder replied to ICMF's topic in General Automotive Talk (Trucks and Cars)
ICMF, Pretty subjective question, and even more subjective answers most likely. By "quality" I prefer to think of how well the kit was produced, once the tooling was cut, as opposed to the level of perfection of the model kit itself, tooling wise. You will run across, in this genre' almost the entire gamut of the development of model car kit tooling, from the early 60's through the middle 1980's. From MPC (AMT/Ertl), JoHan, Monogram (now Revell-Monogram), Italeri or Heller, there is not truly a badly done Classic Era model kit. Now, some may well be a bit outdated in the way they were engineered (Monogram's kits tended to have rather large locating lugs to capture locating pins, for example), or have limitations as to how the particularl company had to tool them (Italeri didn't have the capability of making one-piece body shells -- which require "slide core" mold technology -- for example). But these aren't truly "dings", they just mean that it takes a different approach sometimes. Coming from the aircraft side of things, I suspect you are well-versed in the multitude of different kits of the same plane, by different manufacturers, each with its own idiosyncracies. In the model car world, however, duplicates of the subject aren't all that common (unless we are talking stuff like Camaro's, Mustangs, or Corvettes, for example). Rather, if you are looking at a classic car kit from one mfr, most likely that is the only kit done of that subject, and even more likely is that it will never be done by anyone else. However, almost without exception, companies like MPC, Monogram, and such "pulled out all the stops" to make their Classic Car model kits the best they could do at the time they did them. There will be anomalies, for sure, but nothing that a competent modeler can't overcome, and with some patience and perseverance, masterpieces are pretty easy to come up with. BTW, Lindberg's Bugatti Royale Convertible Victoria is a sleeper of a kit--it's far, far better than the brand name would suggest, but of course, it's also 40-some year old tooling, and a lot of things have been learned in the meantime. Well built though, it need not hang its head in the presence of kits from any other manufacturer. Biscuitbuilder -
Cleaning and prepping questions on Resin
Biscuitbuilder replied to crispy's topic in Car Aftermarket / Resin / 3D Printed
Matt, Some misinformation here, bordering on "urban rumor". First of all, silicone RTV rubber is NOT the same as the silicone contaminants you fight in an auto body shop. Second, PVA and PTFE aren't the most common mold release/barrier agents in use anymore. If the resin body has a "slippery" or even slightly greasy feel to it, chances are the caster used a parafin based spray as a mold barrier (yes, that stuff does extend mold life, by preventing much of the leaching of resin chemicals and solvents into the RTV--which in itself is very absorbent of that stuff). The most common variety of this is Price-Driscoll Urethane or Polyester ParFilm. That can be removed by Westleys, any TSP compound (dissolved in water), or Naptha (sold in bulk up to gallons in a lot of stores, this is also known as lighter fluid). Trust me on this, with 11 years of resin casting experience, I have never seen Westleys (which is trisodium phosphate or TSP), or naptha damage urethane resin or for that matter neither does sodium hydroxide, which is the chief ingredient in Easy-Off oven cleaner, also sold in stores as Lewis Red Devil Lye. Considering that monthly, I had to clean and prep over 2500 resin parts for plating, I think my experience stands for itself. Lacquer thinners do not "craze" urethane resin, for exactly the same reason none of the solvent-based plastic cements work on it either--they do not affect the surface of the resin in any way. Witness how many modelers use acrylic lacquers on resin bodies with nary a hint of crazing. What is an absolute no-no on urethane resins are any of the professional grade degreasers, and God forbid, DOT-3 brake fluid. Those will soften a resin body into a rubbery piece of junk very quickly. Be aware that there are soaps & detergents, and there are soaps and detergents. Many are worse than doing nothing, frankly. For example, one of the worst sources of silicone contamination are dishwashing liquids, particularly those that promise a "clean down to the shine"--silicones abound in those. Many hand soaps have skin softeners/moisturizers in them, which while not silicones, will leave a contaminant on the surface that will produce fisheye. A good bath soap, such as Dial, works great, been using that for years on my personal projects, both resin and styrene. A good rule of thumb is, "squeaky clean", if your finger wants to "squeak" silently over the freshly cleaned surface, then most likely, that surface is perfectly ready for paint. Biscuitbuilder -
Welp, got the inner door panels done this afternoon. Made from .010" styrene, with holes done with a homemde hole punch (7/32" brass tubing, sharpened), spaced away from inside of body with some .015" strip stock. More details to come, just thought I'd let all know that this one is progressing: Art
-
Most of the old Aurora tooling was cut in berylium copper, which was ( and may still be) nearly at the level of a precious metal on the commodities market. People I knew at Monogram have told me that a lot of Aurora tooling simply did not meet the then-standards at Monogram, and when the deep recession of 1981 hit, the company sold off a lot of that tooling as scrap, which I am told essentially helped save the company from oblivion. If that is so, then so much the better, simply because it would have saved an iconic company that has kept us supplied with cool stuff for decades. Biscuitbuilder
-
....Model T and Model A parts combined into a vintage hot rod. Here it is, with body set on the frame, finally up on wheels! Biscuitbuilder
-
Aardvark Models Website Is Back
Biscuitbuilder replied to Modelmartin's topic in Car Aftermarket / Resin / 3D Printed
Except that Super Clean has an industrial alcohol base, which I believe can damage resin. Biscuitbuilder -
'27 T Street Rod, On Scratchbuilt Model A Frame
Biscuitbuilder replied to Biscuitbuilder's topic in WIP: Model Cars
Well, it's just about ready to go up on wheels! Engine now has mounts in the chassis (after a few fits and starts!), bellhousing and tranny can be mounted up, torque tube is shortened and fixed to the "Banjo" center section of the rear axle--Ford parts are so much fun to work with! Here's this week's pic of the project: Biscuitbuilder -
Resin Flip Open Fuel Cap?
Biscuitbuilder replied to Jairus's topic in Car Aftermarket / Resin / 3D Printed
The old Indy car (front engine roadster era) fuel doors were a "cam and lever" design that originated in the 1920's, from Harry A Miller Company (Miller '91 race cars). USAC specified this type of fuel door until the dawn of the aircraft-style refueling nozzle/receptical setups of the late 1960's. Biscuitbuilder -
1958 Biscayne, Part 2
Biscuitbuilder replied to Ron Hamilton's topic in Car Aftermarket / Resin / 3D Printed
Ron, Just curious--why the chromed upper door frame, B-post and upper edge of the rear quarter window framing? Biscuitbuilder -
What's not to like about a Stutz????? One of my favorite cars, built a couple of them over 30yrs ago, time for me to revisit the subject once again, as well! Biscuitbuilder
-
Mmmm Mmmm GOOD! Biscuitbuilder
-
Hint: When photographing models outside in natural light, try if possible to take pics on days when the sky is at least lightly overcast--you get the same fullness of light, but without the harsh "hot spots" of glare, and shadows tend to be softened out quite a bit. Flash for fill in lighting is good, though! Biscuitbuilder
-
'27 T Street Rod, On Scratchbuilt Model A Frame
Biscuitbuilder replied to Biscuitbuilder's topic in WIP: Model Cars
It's getting a magneto, the almost generic sort that looks like a miniaturised mail box (horseshoe magnets), that will be located inline with a centrifugal water pump driven off a gearbox to the righ to the front of the block. Water pump and mag will be on the same accessory drive shaft, very much like a lot of engines from the 'teens and twenties were, particularly the Duesenberg Model J. Speedway Motors' Gerber blocked Fronty T has this sort of setup, and it really trips a trigger for me. Biscuitbuilder -
'27 T Street Rod, On Scratchbuilt Model A Frame
Biscuitbuilder replied to Biscuitbuilder's topic in WIP: Model Cars
Yup, that's where I got the idea! Biscuitbuilder -
'27 T Street Rod, On Scratchbuilt Model A Frame
Biscuitbuilder replied to Biscuitbuilder's topic in WIP: Model Cars
Engine underway!!!!! I have been enamored with the Frontenac 16-valve chain drive DOHC cylinder head that Louis Chevrolet produced in the 1920's for the Model T, and decided early on that this would be the engine for the '27 T street rod. However, two things pushed me away from using a Model T block--first, that engine block was made, by Ford, to work only with their famed, and contankerous, planetary transmission, which doesn't really lend itself to high powered applications; and second, there just isn't any really good Model T engine out there in scale--too much of the details are molded in place, so...... In looking for references, I found pics of a Johnny Gerber Fronty engine. Gerber cast up a new iron block for Ford Model T internals, but a much more conventional (for the 20's, anyway) layout, with a bolt-on flywheel housing, making it perfect for adapting Ford V8 bellhousing and tranny. Here's the engine, with scratchbuilt block and oil pan. The AMT Frontenac head with its cam covers, and the camshaft chain drive housing are used, but the chain drive housing was revised in order to add in the upper water outlet that AMT completely missed. This piece will be polished aluminum, so it had to be very smooth, and that meant getting rid of the molded on bolt detail, cleaning up the rest of the housing, then adding a scratchbuilt water outlet, adding that to the housing. Also, I filled in the back of this unit, as the real ones are closed up entirely, to keep the oil where it needs to be. Still to add is the oil pump, which goes on the front of this housing, as well as the front main bearing housing on the front of the oil pan, the rear main housing, and the cast-on gussets down the sides of the pan (the oil pan on this engine was cast aluminum). Also, need to add bolt details to the water jacket access plates on the sides of the block yet. Biscuitbuilder -
Some of your problem may well be lighting that is too intense (Halogen bulbs are very BRIGHT), and perhaps a light box that is just too small, too limiting. About 25 yrs ago, at a meeting of Lake Michigan Model Car Club in surburban Chicago, Monogram's in-house photographer gave quite a clinic (several key players at Monogram were club members, BTW!), and it was quite the eye-opener. The photographer brought in a light "tent" he used for all of Monogram's box art pics in those days: It looked very much like a small quonset hut, about 30" wide, perhaps 3' deep, with a curved frame front and rear, open at the ends, about 18" high or so. Over this, he fixed a sheet of frosted clear plastic sheet, making that curved "Quonset Hut" type structure. For lighting, he was using 100-watt floods, in those inexpensive spun aluminum reflectors, positioned one to each side of the frosted clear plastic, one above, toward the front, but angled slightly to the rear. For the "base" inside, he used ordinary poster board, sprayed a very light gray, the rear of which was curved gently up to the back wall of this unit (curved, so that no creases or breaks would be seen). When the lights were positioned, and turned on, there was no harsh light (the frosted plastic took care of that), and when a model car was positioned inside, no harsh shadows either. The model was just bathed in soft, white light. At Playing Mantis, the graphics art guy and I built this same sort of fixture, used blue insulation styrofoam and a hot-wire cutter to make the arches for the ends, a piece of the styrofoam insulation to make the base. I sprayed some posterboard with a light gray autobody primer for the base. With modern digital cameras, we got gorgeous shots of not only Johnny Lightning diecasts, but also of Polar Lights model cars as well. The soft lighting made a huge world of difference! Also, a good photo-editing software works wonders. I use MS Picture-It 9, which is cheap as heck (about $11-$12), and has cropping, brightness/contrast, and tinting features (including "auto tint" which is what I use with nearly every pic I take). As far as camera settings go, I just set my Fuji S5000 on "Auto", use Macro, and let the camera do the rest of my work--then crop and adjust on the puter as needed. Most generally, I get pics that tell the story. Now, here at home, I have yet to make one of those light boxes, so I use my dinnertable, a table lamp for back lighting, and flash--with some printer paper for a base/backdrop--that works too, although I do use the flash with this setup--with some practice, that's worked pretty good for me. Hope this helps a bit. Biscuitbuilder
-
'27 T Street Rod, On Scratchbuilt Model A Frame
Biscuitbuilder replied to Biscuitbuilder's topic in WIP: Model Cars
Just so nobody thinks I've given up on this one, I haven't. The project is in the engine phase right now (having the engine and transmission at least sub-assembled is pretty critical to determining the length of the torque tube, and rear radius rods. Not much to show yet, but the basic engine block is built, to fit the Frontenac DOHC chain drive 16-valve head from the AMT '27 T kit, still have to add the skirting to the lower block, which is the top of the crankcase, then build up the oil pan, add a flywheel housing to the rear, and the accessory drive system to the front (for the waterpump and magneto). Pics when it gets a bit further along. Biscuitbuilder