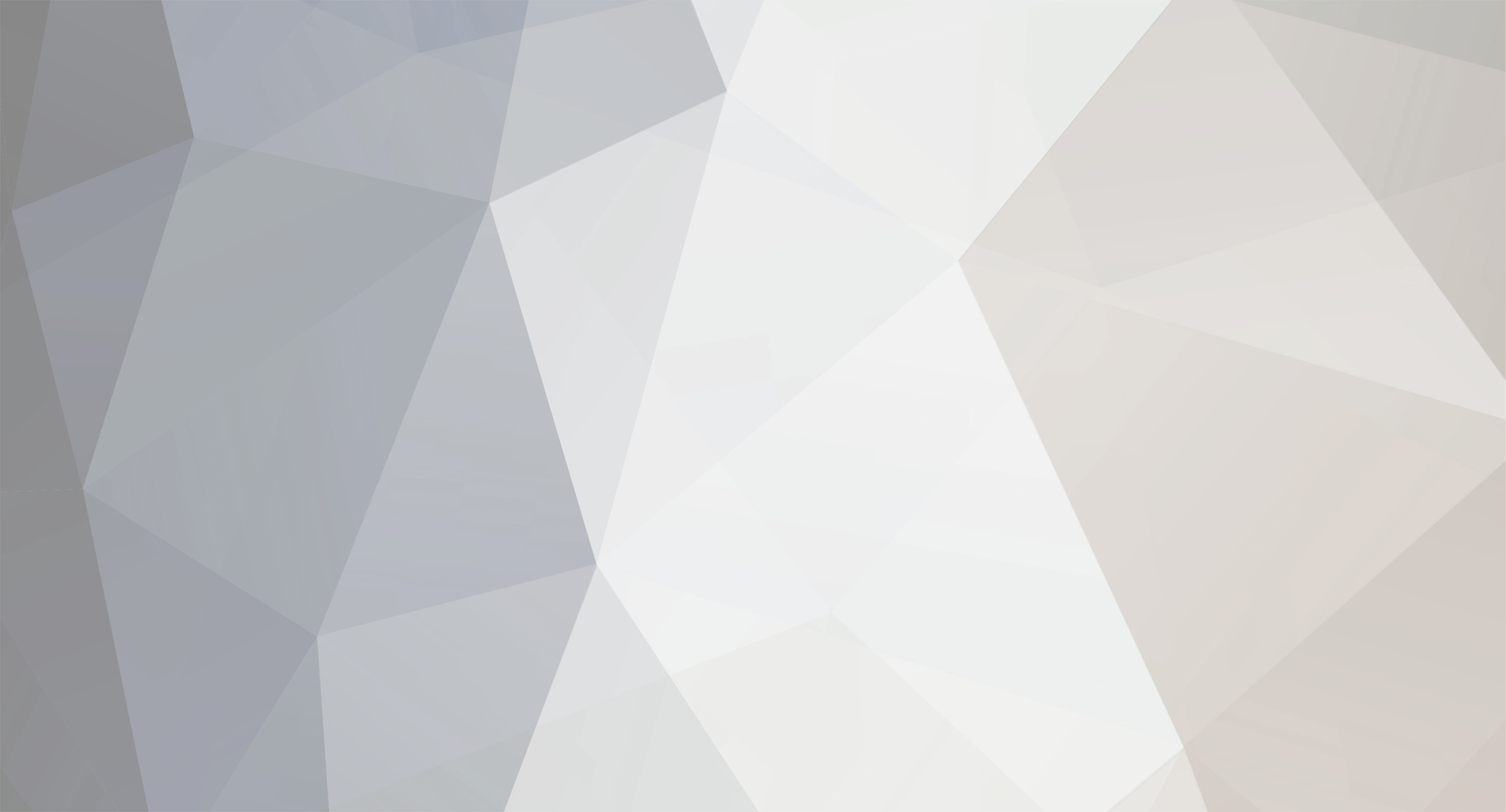
E St. Kruiser50
Members-
Posts
1,474 -
Joined
-
Last visited
Content Type
Profiles
Forums
Events
Gallery
Everything posted by E St. Kruiser50
-
I LOVE THIS You guys got me - Got a long hate PM to boot today from one of you guys accusin me of bein' a charlaton and a fake - guess it must be true, 'cause ya'll say so. YA'LL MUST BE TIRED OF MY LYIN', LOOKIN' FOR ATTENTION, AND CARRYIN' ON AND SUCH THAT'S OK. I'll just wait 'till yer all done before I post anymore on this thread. Guy that PM'd me said the leather looked like it came from an elephants a$$ - HEY, MAYBE IT DOES . GUESS THIS SIMPLE PLASTIC HOBBY STUFF JUST TURNED INTO SOMETHIN' WAY MORE SERIOUS . HEY - YA BETTER TELL MODEL MARTIN TO VOID HIS THREAD ABOUT ME IN 1962 AT THE WINTER NATIONALS, 'CAUSE IT'S PROBABLY JUST A LIE THE GUYS TOLD IN THE MAGAZINE . - SEE YA
-
GRAVEL-ROAD CHROME. Now back to the leather .
-
The texture of the grain is pretty amplified by the magnified close-ups of the pics. In person the leather has a rich, soft, smooth, pleasing look, that only comes from real leather. All the vinyles I've seen, are way thicker, not nearly as soft and stretchy, and the grain doesn't appear nearly to scale as some leathers. Flatliner brings up a good point about choice of materials. That's why, to me, "HANDS ON" in choosing any of your material is always the best . And yes, there are leathers that are much smoother, or with some experience you can accomplish that yourself. (See yellow car with black interior in the preliminary pics - very smooth, but the same tan leather that appears bumpy in other pics, due to how I "Enhanced" the leather with a little helpful processing) .
-
Here's a pic of some of the skins I have. Mostly goat, some pig, and one deer skin. Here's a pic of the two leather's I'll be using for the project. I like contrast, and these two colors are pretty neutral, but very rich, especially in person, and go with most any body color combo's. The tan I use more than any other color just for that reason, and it seems to show the leather graining and all it's best attributes. And here's the color combo as seen in the last pic, in a finished project of mine that's in a private collection. He owns 20 pieces from me.
-
Snake skin uhh-I don't think so, but if you GOOGLE, I think you'll find what you're lookin for, maybe in your area. Good luck - dave
-
No parade here David, but we do get a lot of rain in Oregon . Hope you enjoy the thread. Hope to see some helpful idea's from you in the future also .
-
Or you could stay with the portable breakdown idea, and use Velcro pieces in the four corners of the sheetmetal box . Plus 3M makes an inexpesive role of soft spongy sealing material for sealing home windows, that could form a seal between the pieces of Velcro, so there is no gap to cause fume leakage. Any Home Depot-like store could supply you the seal, and Joanne fabrics could take care of the velcro.
-
For me .040" is way too thick to do anything workable or scale. Do a little "detective work", in your area and see what you can find. Originally I had the same problem, but I didn't settle 'till I found what I wanted. It took me a while, but I did find it .
-
Several of the cars in the pics have real wood, and some are "Faux" painted, a wet 'N' wet multi-color painting technique I use. Been a wood worker for decades, and love exotic woods from around the world, so whenever I get a chance or a whim , I'll head across town to a place that supplies rare woods all over the world - LUCKY ME that it's so close here in town. One of my favorites is a beautifully figured "THUYA BURL" from Algeria and Morocco in Northern Africa. Incredbly beautiful and rare, a very small sliver of this wood can cost $75 - $100. I save even the smallest scraps in a baggy. It's rarity and popularity go back to the time of Christ, and the Greek and Roman Empire, and was originally called thyine wood - highly prized and rare even then. Knowing the history of things like this, and using them this way in my hobby, adds to the romanticism of the world and culture we all share. I love history, and knowing about the world around me. Instead of just building plastic models, you add a little "Class" .
-
First off, I need to qualify how I post a thread. Guys have at time's complained over "CAPITAIZED TEXT", as they feel they're being yelled at - "I DON'T YELL - EVER". I capatalize to get attention, and to make a point about what I think is important - PERIOD . To me sharing is something we should all do to help each other. If someone is afraid to share their "Secrets", then to me they probably have a pretty shallow sense of their own skills and abilities - SAD. Never been afraid or threatened by trying something new - I LOVE A CHALLANGE - IT'S EXCITING TO ME . Something in my nature or mentality, as well as my curiousity, always seems to push me forward to continually get better at what I enjoy doing. I love research, and trying new things and materials, especially at times when I see that no one else is doing it, like when I first started doing urethanes and my water-based chrome system that works so well. Like any new medium, leather is challanging. As in the past, I had no articles or anyone to help me in any way, so it was kinda fun and exciting to venture into uncharted teritory . All my career I was a problem solver in one degree or another, and a research guy as I stated earlier, so I set out about 10 years ago, to find some leather goods that were of the quality I figured I would need. I have never tried to build anything as cheap as I could, in my model building or any other part of my life, as I've found that you only get what you pay for. ENOUGH SOAP-BOX . I found two good leather shops here in Portland, and after visiting them settled on one that at the time had the best supply of the kind of leather I wanted. There is pig skin, goat skin, dear skin, cow hide, etc. That's where personal choice comes in like brands of paint and rattlecan or airbrush. We choose according to our style of building. I wanted a leather that was "THIN", supple, and "STRETCHY". Also soft to the touch, with a nice grain and over-all appearance. "THIS IS WHERE HANDS ON RESEARCH COMES IN". I find a leather that is between .012" - .017" thick is optimal.. Anything over that and the "STRETCHY" DISAPPEARS QUICKLY, and the extra thickness, becomes a HUGE ISSUE FOR SCALE AND APPEARANCE. A lot of this I won't be real specific, because I think each of you need to do the "Leg-Work and Research" yourself to make the choices, and get educated. "KNOWLEDGE AND INFORMATION IS POWER" , thats why I know so much - I PAYED MY DUES . Not only are leather shops a good place to get what you want, but so are thrift stores. Ladies purses, gloves, coats, pants, etc., can be inexpensive suppliers for the leather and colors you want to use. What was really cool was that after working with very thin, very nice leathers from the leather goods store, your hands get a sort of "Sixth Sense" as to thickness and quality when you go to thrift stores to look for your treasures. Thickness of the leather is one of my top considerations, as it affects every step of the process. I use a set of digital calipers to select the skins I'll purchase. I say skin, because I buy full skins of animasl that has been processed and tanned - mostly goat and pig skin, small animals. Remember too, that every skin or piece that you get from a thrift store varies in thickness, so always measure the thickness of the area of the piece your considering to use - never assume anything. Most of the skins available today at most suppliers, are now from China, and so finding good quality leather will be a bit more difficult and a bit more pricy. I got mine from Denmark and Sweeden many years ago, and are wonderful. Most of you guys here are married, so trying to convince your wife this is a needed expenditure may be a bit of a leap , been single myself for several years, so for me not an issue . TOOLS The tools I use to trim the leather are mainly razor sharp scissors that cut a clean fine edge, and new very sharp #11 xacto blades, and a steel straight edge. The only surface I've applied leather to is styrene plastic, so I've found that Testors old fashioned glue in the orange and white tube work incredibly well. The glue attacks the styrene really well and absorbs well into the back of the leather, without going through to the surface - so a win win. I've never had an occasion to try it on wood or any type of metal, so some room for experimenting for those who want to try. NEXT POSTS I'LL need to select a piece of flat plastic stock and and choose some leather, and design a simple door panel set - front and rear, for the next post in a few days. I'll go through the steps of cutting out the plastic pieces, trimming them to size for clearance, and then gluing and checking for a good interferance fit, and how to trim every thing for a crisp, clean appearance. I can also show you guys how to stain and finish the leather for a nice smooth supple look. SO, THE TOOLS YOU'LL NEED TO START. Digital calipers. Very sharp scissors. I use several sizes. New sharp #11 xacto blades. Steel straight edge. Testors glue. Patience . And a willingness to make mistakes.
-
1932 ford
E St. Kruiser50 replied to E St. Kruiser50's topic in General Automotive Talk (Trucks and Cars)
I hope the new thread helps . -
Last examples. This one has a red leather interior - hard to see.
-
More pics
-
Like in painting or anything else, I think you should be able to have some sucess and experience at what your sharing, and be qualified to show others how to do something. So I'll start out by showing some finished examples of my previous work. Several of these have won awards at major shows in the past, in Calif., Oregon, Washington, and at the GSL in Utah, as well as being in many magazines, inluding a cover shot and a feature article. In the next few days I'll discuss such things as the tools and supplies you'll need, the various leathers, where to get leather, how to apply it using some very easy basic steps, to get some experience and grow from. The biggest challange for some will be the "PATIENCE" it takes to do this and make mistakes, and keep going 'till you get it right - THIS IS NOT PLUG N PLAY - MISTAKES AND FAILURE ARE PART OF LEARNING . Here are some of the cars I've built with scratch-built leather interiors. Scratch-built 1935 Duesenburg SJ Airflow Coup' Scratch-built Hollywood Graham.
-
1932 ford
E St. Kruiser50 replied to E St. Kruiser50's topic in General Automotive Talk (Trucks and Cars)
Sure Harry, in 1/8th scale Pocher kit that the leather comes with it . -
I've has several people ask me about doing a tutorial on doing leather covered seats, and door panels Is there any interest in me doing that?? I would include where to look for materials, the process for adherring it properly, and design techniques and considerations.
-
Epoxy fail?
E St. Kruiser50 replied to Jon Cole's topic in General Automotive Talk (Trucks and Cars)
I have used this product for nearly ten years, and it sticks to everything I have used it on in my model building, including alum, brass pieces, and every paint and plastic I have used it on. In my town I get it at a variety store or auto parts store. It's made by Permatex, a well known company in the auto industry, so shouldn't be too difficult to find. -
After reading posts here on mills, I went to Ebay and typed in "SHERLINE". This complete mini-shop came up that is at $350.00 right now with 8 1/2 days left. Tons of support pieces and a few upgrades - a complte set-up. Who knows what it will go for, but thought that there are some here who would at least be interested in checking it out.
-
Harbor Freight Mill
E St. Kruiser50 replied to CAL's topic in General Automotive Talk (Trucks and Cars)
My next "big boy toy" in miniature This a 4 axis table top CNC - almost a machining center, but no tool changer available yet - I'M WAITING. The table moves 18" X 10" X 10" on the Z axis, with a very small footprint - around 18" X 24". The computor controlled rotary table is the 4th axis. You can also order it with an embedded computor. Also available is a touch-probe digitizer with all the software for copying any existing item, and then duplicating it as many times as you want, in whatever material you want. Comes turn-key with all the software, and modeling capabilities. Lots of accessories available. Under 5 grand as you see it with the embedded computor installed. Just need to add keyboard and monitor. -
Hey Sam - You should post more pics - Came out very nice .
-
Contest question
E St. Kruiser50 replied to Jon Cole's topic in General Automotive Talk (Trucks and Cars)
We have about 6 or 8 contests a year locally in the Portland area. Most of the guys build enough that we always see new stuff from most, but there are a few who like to keep bringing back the same models year after year. I think it's up to the builder. People enter contests for a lot of different reasons. As long as no rules against it, WHY NOT . For me, I enter 3 or 4 of the local contests a year, and then retire the cars, or go out of state. The Washington guys have several contests a year too, with the Canadian guys coming down, so I can always go up there to see some of my friends. For me thats what it's mostly about now is hangin' out, visiting with friends, and going out to eat lunch . -
Not sure, but this may be the car kit you're referring to. I'm sure this is the one Andy is talking about. Very, very nice kits. Super detailed, with a ton of parts, and everything fits beautifully. Got this one started with opening doors and so forth. Also have a 500 K Special Roadster started that is a modified version of the 1934 Mercedes JoHan roadster. Nice kit also. These are available on eBay most of the time for what I think is a reasonable cost most of the time. Here's a pic. As Andy stated, this is from the Gold Cup Series.
-
I hate watching paint dry
E St. Kruiser50 replied to hellonwheelz3's topic in Tips, Tricks, and Tutorials
Having more than one project going at a time helps to take your attention off one project, and focus on doing other things. Hurrying is to me, the worst enemy to completing any type of project properly , including model buiding of any kind. That aside, I think James idea really is pretty cool . -
Plasticoat T-235 Primer
E St. Kruiser50 replied to Len Woodruff's topic in General Automotive Talk (Trucks and Cars)
The only Plasticote Primer I've ever used successfully is their white T-237 sandable primer. Lays down smooth and sands beautifully when it dries for at least 24 hours. The other primer I use is a gray Duplicolor High-build primer, which can be decanted and thinned, and sprayed through an airbrush for those who think it builds up to much. Sands wonderfully also. The thing to remember about priming and painting is that the conditions under which you spray makes all the difference. That's why real-time car painters spray in a heated, lit and well ventilated spray booth. Most guys here from what I've read, spray out-doors or in a un-heated garage, which especially in the winter months leaves a lot to be desired for spraying conditions, and really affects every aspect of painting. So, if you are spraying out-doors, there's a lot more to consider than just the paint or primer when there's problems. I have a walk-in 5X10 spray booth that is heated, well lit, and ventilated, and I have complete control over the temp. I usually spray my paint at around 80 degree's any time of the year, here in cold, rainy Oregon. Paint and primer lays down like glass . -
I agree with Bob Downie and others here that "Best" is a relative term that each of us determine for ourselves. We all have our own favorite "WEAPONS OF CHOICE" that we deam the best for each of our "Mini-Treasures" we build. Time and experimentation with different paints and polishing products will settle the question for you. It boils down to lot's of practice and samples to you find that "Majic Formula" that is the "BEST" for you, and suits your style. My 2cts. - I don't use enamels or hobby paints much except Tamiya lacquers, and never their clear, as I have an automotive spray lacquer clear by Plastikote that so far, is compatible with all the auto paints and Tamiya, so sort of a no-brainer for me. Haven't stripped a paint job in nearly ten years. It polishes to an amazing finish , and can be totally rubbed out in less than 24 hours after the final coat of paint. By far the best clear though for me when I'm doing urethane, is HOK UC35, and it's reducer and catalyst. When I do urethane paint jobs, you can spot it from all the rest on an event table, as the quality and finish make it a stand out - urethanes are amazing for depth, intensity, brightness and clarity.