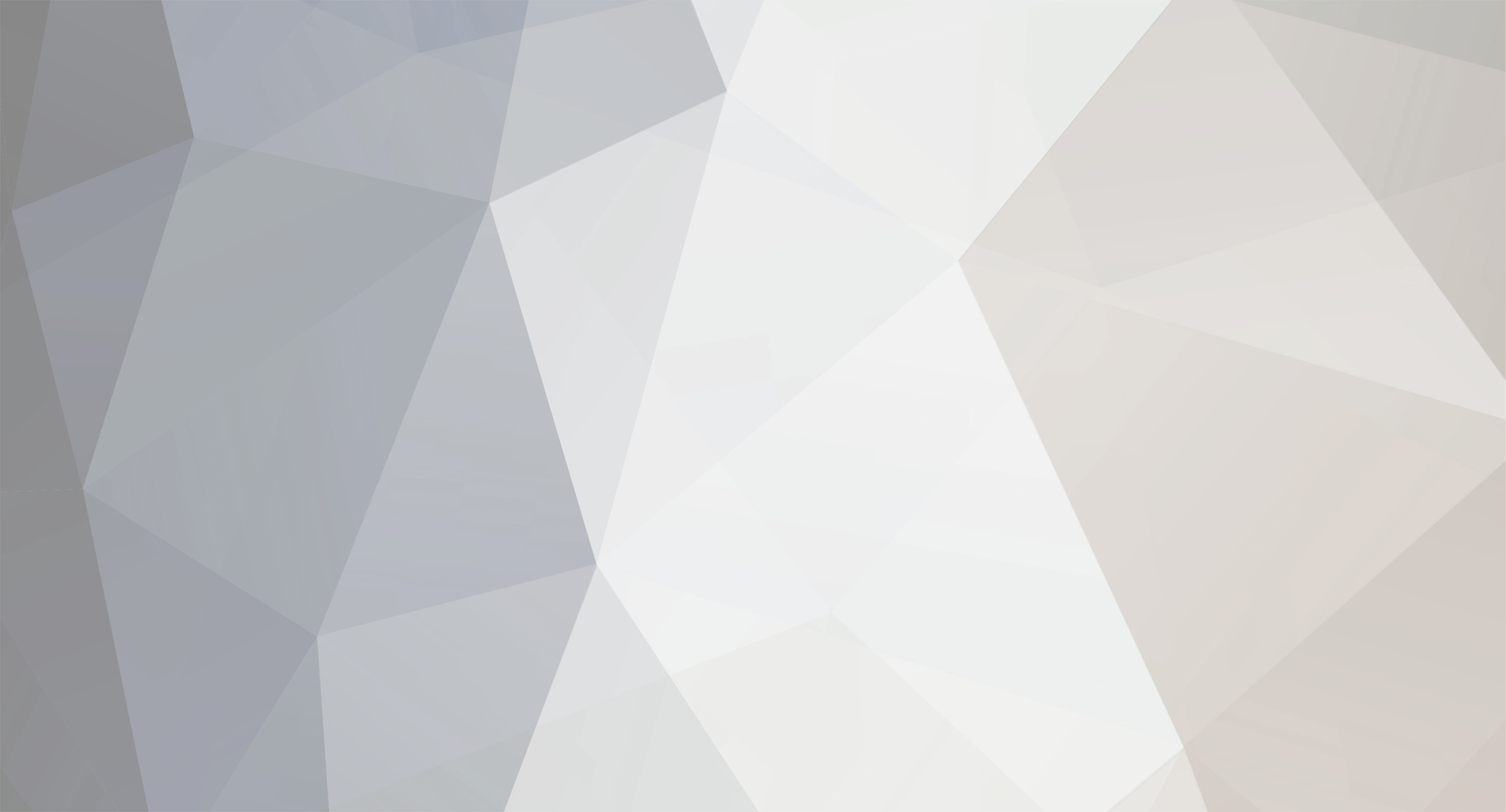
Art Anderson
Members-
Posts
5,052 -
Joined
-
Last visited
Content Type
Profiles
Forums
Events
Gallery
Everything posted by Art Anderson
-
Uh, for starters, from 1941 (the first year that a station wagon was offered in the Mercury line, through 1948 (the last model year of an all wooden constructed station wagon body at Ford, Mercury used exactly the same station wagon body as was offered by Ford. As for a need to modify the AMT '49 Ford front clip to fit the Revell Mercury wagon--IF both companies have their dimensions in line here, there should be no need for any mods to the Ford front clip, save for cutting it free from the coupe body. This is where a digital caliper comes in very handy! Art
-
any Jaguar XJ 6 kits made? any scale
Art Anderson replied to 62rebel's topic in Model Building Questions and Answers
K&R Replicas, out of the UK, offers a 1/24 scale Jaguar XJ-6 kit, in cast metal--looks to be pretty comprehensive kit. Price? Approximately $152, depending on the rate of exchange between the US Dollar and British Pound Sterling. http://www.grandprixmodels.com/searchdetail.php?ref=KAR2427%26%2FK%2D%26%3B%2DR%2DReplicas%2D1%3A24%2DJaguar%2DXJ6%2DSeries%2D3%2Dmodel Art -
any Jaguar XJ 6 kits made? any scale
Art Anderson replied to 62rebel's topic in Model Building Questions and Answers
Did not Revell make one back in the 1980's? Art -
Lorin Sorenson's excellent book on Ford Motor Company's woodie station wagons, 1929-1951 covers the '49-51 Ford and Mercury wagons in great detail! Those wagons shared EXACTLY the same body shell all three of those years. The only differences in the real cars are in the front clips, side doors, instrument panels and steering wheels--that is it. The station wagon doors (and rear quarter panels as well) are set inward about 1/2 inch or so, in order that the molded, laminated birch "framing" could be flush with the surface of the front fenders, which meant that both the Ford and the Mercury used a door structure that was different from the rest of their respective lineups of passenger cars. So, yes, the windshield openings and glass are identical on both the Ford and Mercury station wagons. The bodies themselves were devoid of any surface sheet metal, save for the roof, A pillars and cowling, and of course, the C-pillar, along with a sheet metal sill below the rear tailgate. In place of sheet metal door and rear quarter skins, Honduran Mahogany was laminated into plywood, then molded under heat and pressure to their curved shape, as were all the hard maple "framing" strips (which were trim only--having no real structural purpose). These panels and their framing were then given a couple of coats of spar (marine) varnish, and once dry, were bolted into place on the body sides. The upper door frames, and the framing around the rear quarter windows were solid maple. The interior side panels were also mahogany plywood, as was the inner panel of the tailgate "drop gate". 1949 and early 1950 wagons had their lift-gate and drop-gate framed entirely in hard maple (Ford's traditional station wagon framing wood), with amahogany plywood surface, trimmed with hard maple. Starting fairly early in the 1950 model year, Ford's Iron Mountain MI plant began installing stamped sheet metal lift and drop gates, and Ford had planned to begin using sheet metal panels covered in mahogany "Di-Noc" (which is basically PVC shelf paper today!), but the outbreak of the Korean Conflict and the sudden rearmament due to the Cold War lead to steel rationing for civilian products, so very few Ford or Mercury wagons got those sheet metal panels, which remained in production through the end of the 1951 model year. Hope this clears things up a bit. Art
-
Model kit when flying
Art Anderson replied to kangee's topic in General Automotive Talk (Trucks and Cars)
More than once, I've had TSA agents (the ones who scan carry-on items) remark that I must be going to a model car contest as my destination. Built, or unbuilt is no problem. Tools, on the other hand, as a general rule, should be in checked baggage, but I've carried small bottles, even a rattle can or two, in my carryon with no problems. For advice, go to TSA's website--they have very good instructions there--I even called their 800-line once, just to confirm, and was very politely told, no problem. On the other hand--I had to unbolt a trophy last fall, coming back from Boston after Classic Plastic Got waved through as a senior citizen, only to have some fresh-faced agent seriously question what that long steel bar with threaded ends, and hex nuts on it was--a more experienced agent walked over, took a quick glance "That's just a danged trophy, son! If you look closely, it is too tall to fit in this small suitcase fully assembled." End of problem. Art -
As for the station wagon bodies themselves--both Ford and Mercury used the same body shell for 1949-51 Station Wagons, the only difference being in the side sheet metal--Ford's front fenders are taller than those of the Mercury, nearly level the the hood, while Mercury front fenders are considerably lower than the hood line, and their shape blends into the front doors. So, in order to adapt the '49 Mercury body to a '49 Ford front clip--the front doors will have to be changed over to those from the Ford, then the wood paneling/framing replicated on that. Art
-
how to two tone model cars?
Art Anderson replied to foxbat426's topic in Model Building Questions and Answers
I second Roger's advice. I've been doing two (and sometimes three or more) color paint jobs on model cars since the 1960's, when real masking tape was the only game in town. I still use regular masking tape, and replace the roll after it's been around for more than say, 3 months or so--this ensures that I use tape that has fresh adhesive, and it's not all that much of an expense either. Like others have suggested, a piece of plate glass and a metal straight edge are excellent tools, along with a fresh #11 Xacto blade in my knife handle, for cutting a truly sharp edge on the tape I use--most certainly when that piece of tape is going to be the demarcation between colors. I then burnish the tape down tightly (my fingernail does most of that) and where I come to some detail or body shape that makes the tape want to "tent" away from the surface, I'll work the tape gently down into that area with a .5mm push-click mechanical pencil Burnishing the tape down can also go a long way to preventing the second color of paint from "running down" into a door line or other panel line on the model surface. That generally is not a problem when using an airbrush due to the much finer spray mist of paint as compared to a spray can--but even then I've almost never had a problem with it as long as I burnish the tape down. One point of caution might be in order here: Virtually all hobby paints are formulated to "dry" quickly--to the touch of your fingers--but they aren't really dry enough to withstand serious handling, certainly not the stress of masking tapes.. With lacquers such as Modelmaster or Tamiya, the drying time can be just a few days--although the heavier (thicker) the paint job, the longer it will take for all the solvents to evaporate out of lacquers. I'd let a lacquer paint job dry for at least a week before doing any masking. With Testors enamels, the drying process takes a lot longer--upwards of a month or so, before the paint is completely cured. This is because enamel paints such as Testors dry in two stages: First the solvent has to evaporate, which it will do from the outside inward, and second, the resins in enamels cure by contact with the oxygen in the surrounding air--that's what makes them into a hard finish, given enough time. This is one reason why I (and others) have spent a little money on a food dehydrator, as that speeds up the drying process quite a bit. If you rush to put masking tape on, before the paint (lacquer or enamel) hasn't cured out hard yet--the tape can mark the surface of the paint on which it is applied, and you may or may not be able to polish that completely out. Even leaving the masking tape on longer than necessary can cause this effect as well--words of advice from my nephew, who is a museum-certified (to among others, the Smithsonian) furniture restorer and top-of-the-line cabinet maker. Even with all I mask using masking tape, there are times when I have to go to using Bare Metal Foil to get an edge in a tightly cramped area where there are sharply raised details that masking tape just won't seal down on long enough to get a paint job done. Others have already described how to do that, so I'll not belabor the point any further. Art -
Harbor Freight Dehydrator
Art Anderson replied to mole53's topic in Model Building Questions and Answers
My dehydrator is an Oster, which looks surprisingly similar to the HF unit, made from the same materials, same setup, only the shape of the lid on top is different. The Oster is pre-set to a temperature of 120F, which is just fine for styrene bodies and parts--I've had body shells in it for as long as 12 hrs, with absolutely no problems whatsoever. I would be very cautious, however, with resin bodies, as polyurethane resin is much more temperature-sensitive. For temperature control, you can use one of the inexpensive "sliding rheostat" extension cords that are sold for use with table lamps and the like--a decent oven thermometer would help you in finding a certain temperature setting if you need it to be lower than the factory settings too. As for modifying it for model car use, I simply cut the "grating" out of the very top shelf, which gives it plenty of clearance for any 1/24-1/25 scale car body I've put into it--should I need more height inside, I can always remove the grating from a second shelf. Art -
Are your models collecting dust?
Art Anderson replied to angelo7's topic in General Automotive Talk (Trucks and Cars)
As I have very little space for displaying, the models that I don't display here in my apartment get stored in those foldup boxes from a nearby Sports Collectible shop. The 550-card box works perfectly for just about any 50's and later cars. I bought some cotton tricot scraps (T-shirt cotton knit) that are sold for dustrags in a lot of the "big box" stores, and use that rolled up as padding around the sides and across the ends, and simply lay a piece of it loosely across the top of the model. Those boxes are very dust-tight, never a problem with dust, and in the bargain, those make excellent carriers for taking models to shows. For taller cars, there are "mailer" boxes that are higher and wider, with the same dust-resistant design. Art -
I can confirm the actual color of the Futura as built and shown by Ford: When I was doing product development for Johnny Lightning, my first "from the research up" project was the 1/64 scale JL Lincoln Futura. Given the emphasis on as much accuracy that could be packed into a 1/64 scale diecast car selling at #2.99 retail, I had to be as accurate as possible for the color. I found references in text referring to the actual color being a light blue pearl, while the existing color photo's show the car being slightly green in shade. A phone call to Matt Usher, then working in the licensing department at Ford got me the information. According to Matt, the color was called "Ice Blue Pearl", and the base color was copied almost exactly as 1963 Ford Glacier Blue, which that very light blue (sometimes looks almost white!) used in '63-'64. He suggested we try that color, with a pearl clear coat over it, which worked just fine. Matt further went on to relate that those original color pictures were in the library of the former Ford Rotundra Building, which burned in the early 1960's, and a lot of historical photo's and their negatives were damaged to some degree. From my memory--those old Kokak color prints weren't all that stable, and tended to "yellow" over time--which would account for the rather off-color in official pictures of the Futura dream car. Art
-
Paint Booths & Safe Ventilation?
Art Anderson replied to Synister's topic in Tips, Tricks, and Tutorials
Speaking from experience here: I've got a Pace, which exhausts the paint fumes, and the overspray particulates (those get trapped in a common furnace filter at the back of the booth), and yet it DOES not have enough velocity to pull dust or dirt into the booth itself. If one is getting dust, then that dust is likely bits of lint in the air--something that a good cleaning of one's work space will go a lot way to curing. Art -
The "Why?" was answered to me by Bill Coulter himself, when we were at AMT Corporation's Maple Road headquarters the first weekend of May 1976, as part of a judging team for a high school shop class truck model building contest hosted by AMT. Tom Valmassei, then the art director for AMT, confirmed to us that Bill had it right. As a "reward" for help on some new kit projects, AMT offered to kit a subject recommended by Bill, who responded "1941 Plymouth Sedan Delivery", but AMT's management couldn't see a sedan delivery being much of a sales draw at that time, so coupe it was. Art
-
Engine Straight 6 - identification
Art Anderson replied to southpier's topic in Model Building Questions and Answers
Actually, Bill...... That's a SIX cylinder ALF engine. It has three "two cylinder" blocks, on a common crankcase, but it's a perfect example of a T-head engine: Intakes on one side, exhaust outlets on the opposite side. Art -
How to shrink rubber tires?
Art Anderson replied to aurfalien's topic in Model Building Questions and Answers
Not knowing the tires you are wanting to mount on what wheels, a short answer is--other than cutting the tire, removing a slice from it (cross-section) then figuring out how to glue it back together cleanly, about the only thing I can think of is to wrap a thin, flat strip of Evergreen styrene around the wheel before mounting the tire. Art -
Question on wet sanding primer.
Art Anderson replied to lghtngyello03's topic in Model Building Questions and Answers
Some may call me a heritic, but I never use anything more coarse than 4800 grit polishing cloths to wet sand primer (I still use lacquer red oxide primer on everything!). Reason? I want as as smooth a surface for my color coats as possible, as I am a firm believer in maximum color coverage with minimal paint (the more paint, the more surface detail I paid money to get!). This has worked for me since at least 1970--not likely I am going to change a successful method! Art -
Engine Straight 6 - identification
Art Anderson replied to southpier's topic in Model Building Questions and Answers
Ya know, it could also be a 4-valve T-head engine! On the T-head design, intake valves are on one side of the block, exhaust on the other side--not an uncommon engine design a century ago. Art -
Lindberg 31 Bugatti Victoria
Art Anderson replied to Petetrucker07's topic in Car Kit News & Reviews
BAck to the LIndberg Bugatti Royale. As others have stated, the engine could benefit by being replaced with the much better, more accurate-for-factory-stock Italeri unit--but beyond that, this kit should surprise you for a vintage Lindberg product--it's actually very nicely done. Art -
(NEW Update! 6/19/15) IN progress, ICM '13 Model T For
Art Anderson replied to Art Anderson's topic in WIP: Model Cars
John, I liked the idea that ICM at least tried to do a proper tire for the era, but what most people today don't know is that prior to about 1930, in natural light such as light colored tires came off in pictures as starkly white--even the early carbon-black inpregnated natural rubber tires. Fortunately, here in Lafayette, in addition to a Michael's and a Hobby Lobby, we have several small artist's supply shops, plus two large and well-stocked college campus bookstores, all of which carry a wide variety of drawing and painting supplies. The Chartpak Light Sand ink marker I bought was a stab in the dark, frankly--there is only a 1.5 inch bit of sprue that connects the ICM tires in pairs--not much room for a test (yeah, I tried a spoon test, but those are hard plastic, and often soft plastics with a dull finish behave differently). At any rate, it was a worthwhile experiment, even though the dirty tread color isn't as even as I'd have liked--but then, who ever said that dirt is perfect anyway? Art -
(NEW Update! 6/19/15) IN progress, ICM '13 Model T For
Art Anderson replied to Art Anderson's topic in WIP: Model Cars
Yeah, 1/8" in 1/25 scale is a very wide 5-thousandths of an inch--far narrower than the finest paintbrush tip, and certainly tinier than the smallest available gel pen. I think I'll just say that the orginal owner polished all the striping off his new '13 T roadster! Art -
(NEW Update! 6/19/15) IN progress, ICM '13 Model T For
Art Anderson replied to Art Anderson's topic in WIP: Model Cars
As tiny as pinstriping is, it's not likely I will even attempt it. Art -
(NEW Update! 6/19/15) IN progress, ICM '13 Model T For
Art Anderson replied to Art Anderson's topic in WIP: Model Cars
That simplifies my job a good bit. Thanks, Eric! Art -
(NEW Update! 6/19/15) IN progress, ICM '13 Model T For
Art Anderson replied to Art Anderson's topic in WIP: Model Cars
Eric, It should be easy! Just get some 1/25 scale paintbrushes, working 1/25 scale painters and paint away! Don't forget to wait about 4-5 weeks for that paint to dry, then varnish! BTW, on the '13 T, while I know the body was painted a very dark blue, some pics of a restored 1:1 show the hood and rear hood "shelf" as painted black? Was that factory practice? Art -
What is the web site for OEM paint colors
Art Anderson replied to jw78z28's topic in Model Building Questions and Answers
Not to mention that Jameston Kroon, owner of Scale Finishes, uses much finer grade metallic powders in his mixes, in order to get a much more scale appearing metallic paint. I use his colors, fantastic paints for model cars! Art