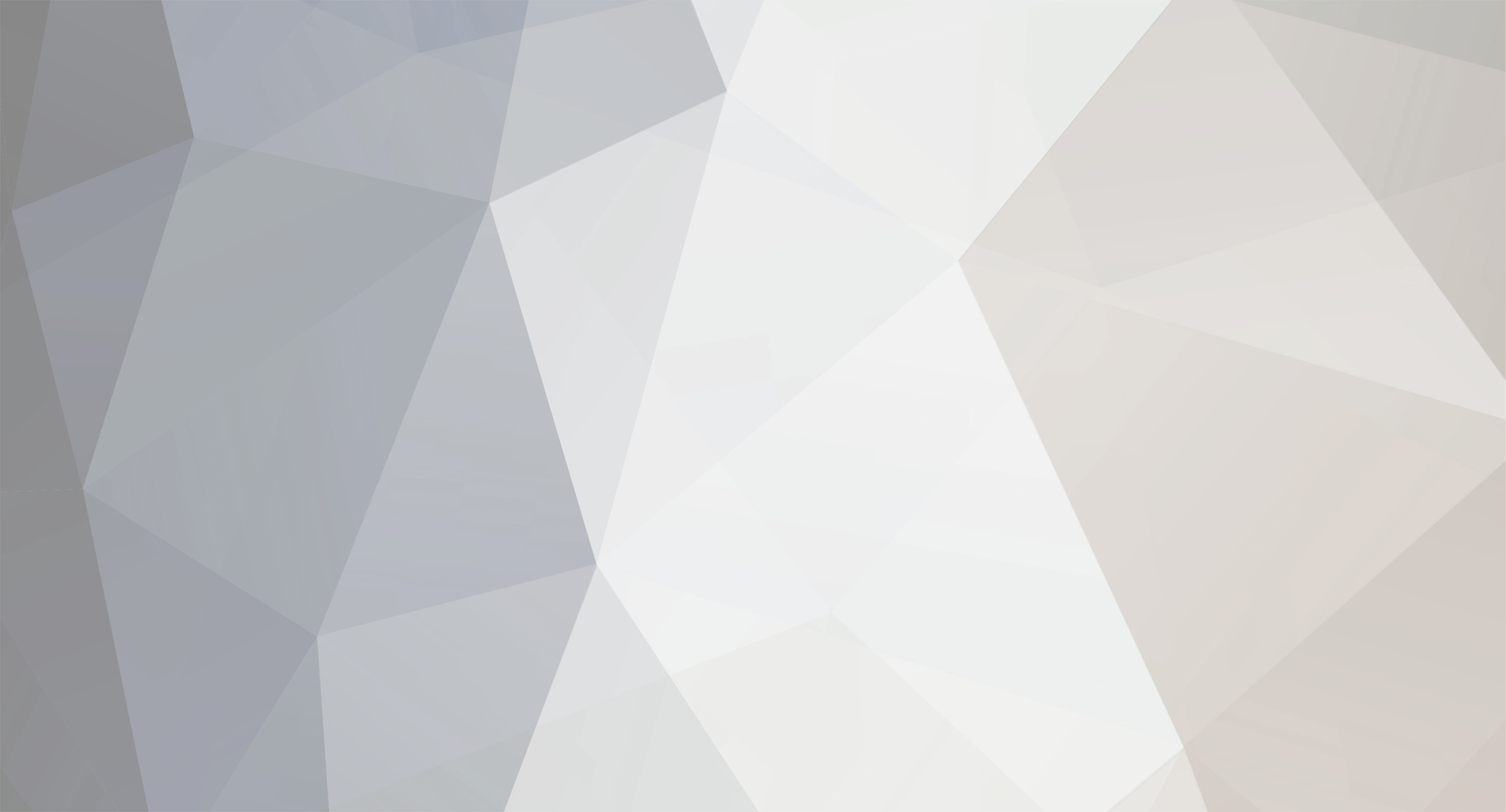
Art Anderson
Members-
Posts
5,052 -
Joined
-
Last visited
Content Type
Profiles
Forums
Events
Gallery
Everything posted by Art Anderson
-
How can I paint really thin stripes?
Art Anderson replied to alex112666's topic in Model Building Questions and Answers
I've used what I call a "three tape" method for laying out stripes on a model car body for airbrushing: First, I lay a strip of masking tape on a piece of plate glass, then measure out the width of the stripe I want to paint, and cut that from the tape with an Xacto knife and a metal straight edge. I then lay that narrow strip of tape on the model car body in the pattern or shape I need. Next, I cut two more strips of masking tape in the same manner, but a bit wider, and lay those on the model body shell right next to the "stripe" tape. Once I am satisfied that I have what I want, I simply removed that first strip of tape (the middle of three side-by-side strips of tape) and then mask off the rest of the surrounding area, and airbrush the stripe color on. It's a bit more time consuming, but a method I've used numerous times over the years. Art -
GMC 302 cid Straight Six
Art Anderson replied to zelkam's topic in Model Building Questions and Answers
i believe, although I could be wrong, that GMC began their OHV 6's in the 30's, from what was to have been a Buick inline 6 that Buick's management nixed in favor of being exclusively straight 8's. In addition, is not the GMC 6 a 7-main bearing engine, while the Chevy 216/235 sixes had just 5 main bearings (that would account for the difference in length?) Art -
Numerous times, in my years of concentration on building models of Indy cars, I simply airbrushed a coat of clear lacquer (back then, after AMT dropped their line of spray lacquers and before Tamiya and Testors introduced theirs') on any sheet of decals that worried me that they might break or crack. I simply used clear automotive acrylic lacquer, appropriately thinned for airbrushing. It's been my observation that decals crack for two major reasons: First (and this happens in production at times) the clear lacquer that most decals are printed on didn't get applied to the decal paper before the colors were printed on. It's that layer of clear lacquer that has the strength, not the printed ink for the graphics. Second, with old decals, given that decal paper is simply thin blotting paper, coated with a layer of gelatin (which is water soluble and sticky as it dries), the decal paper can absorb water simply from the moisture in the air, which will cause the paper to curl up (or at least try to), and once it's dried again, any attempt to flatten it out can cause the clear lacquer decal film to simply crack apart. Spraying a light coat of clear lacquer over a decal sheet in advance, particularyly if one has any concern whatsoever about the integrity of that sheet of decals, has always worked for me--and in the end result, the treated decals have laid down just fine for me, even reacting well with setting solutions. Art
-
A current Indy car would be a cool kit, but I have to wonder just how well it would sell, particularly considering the costs involved just for licensing (IndyCar, IMS, Driver, Car Owner, Major and secondary sponsors, along with Firestone, the chassis mfr, and the engine mfr), plus the tooling. Traditionally, Indy car model kits never sold particularly well outside of about a 500-mile radius of Indianapolis--that could be an issue as well. Art
-
According to the caption on the webpage where I found the picture, it was built in Oldsmobile's Engineering Department. In a way, it kinda sounds like the '76 Eldorado that pulled into the restaurant across Maple Road in Troy MI as I was having lunch with a group of AMT Corporation staff (back in the day when I was doing a bunch of box art models for AMT--was there delivering several. That Eldo had a second door on the right-hand side, for easier access to the rear seat. Other than the extra door, we couldn't see any interior alterations, as the window tint was too dark. Oh, and it had a Michigan "Manufacturer" license plate on it. Dave Wilder, then the art director for AMT told me that seeing such apparently prototype cars on the street was quite common. Art
-
William, Time was when you could see "engineering prototypes" being driven on the streets, around Detroit, and I would assume (considering that the Toronado Wagon was built in Lansing (the home of Oldsmobile), and quite probably in Flint, where Buick and Chevrolet were both hatched. In addition, Studebaker prototypes were often seen in on the streets of South Bend IN, Nash and AMC prototypes in and around Kenosha WI. Art
-
Corvair Van measurements needed
Art Anderson replied to Psychographic's topic in General Automotive Talk (Trucks and Cars)
Yes, the Corvair Rampside pickup. Art -
Is there a site that decodes paint numbers ?
Art Anderson replied to greymack's topic in Model Building Questions and Answers
Gary, you might take a look at http://www.autocolorlibrary.com/ That site has paint chip charts going all the way back into the early 1930's for every make of US car and a great many imports as well. In addition, there's a little clue on paint charts to tell you if the color is metallic--look for the simple word "poly", meaning polychromatic, which is how automakers once described their metallic colors. Art -
AMT and JoHan Maverick & Comet Kit Questions
Art Anderson replied to VW93's topic in Car Kit News & Reviews
AMT Corporation marketed several JoHan kits under the AMT brand name back in the late 60's/very early 80's, as AMT, being the big dog in the pack of model car kit mfr's back then had the brand recognition and a much broader customer appeal than JoHan ever did, particularly among hobby shop owners. Art -
Corvair Van measurements needed
Art Anderson replied to Psychographic's topic in General Automotive Talk (Trucks and Cars)
Yes, in both commercial van form (Corvan) and as a passenger van (Greenbriar). -
Well, would it not be reasonable to assume that those engineers built the car at the direction of upper management, to see what it might actually do on the street--in other words, test the concept? In that role, the car was a "test mule", not a styling exercise--had it been the latter, you'd have seen perhaps pics of a styling clay mockup. As for the Toronado being a "personal luxury car", along the lines of say, Thunderbird (which car pretty much invented that concept in post WW-II America), it was more of a 6-passenger 2-door hardtop (remember, Thunderbird went from a 2-seater (55-57) to a 4-place car in 1958, and remained so untill 1968, when a Thunderbird FOUR door sedan was introduced--by that time T-Bird was sharning its basic body structure with Lincoln). I though the idea was interesting, still do, and wonder how it might have been received had it actually been worked up into a real Toronado station wagon. But, we'll never know that, of course. Art
-
Unfortunately, model kits of movie and/or TV cars don't have a very good record--most tended to be "one-hit" wonder model kits from shows that lasted perhaps a couple of seasons on TV (some shows for which model cars were done or at least planned never made through their first season). "77 Sunset Strip" was aimed squarely at a young audience (don't forget that 45rpm single "Kookie, Kookie, Lend Me Your Comb"--hardly music fare for our then "Big Band" nostalgia parents), and of course, the show came and went before there was a huge following among us kids or teenagers for a model kit of the Norm Grabowski "Fad T". Still though, it's interesting to consider all the potential model car subjects that could have happened, back in the day! Art
-
1/24 Wiring Harness
Art Anderson replied to Metalmad's topic in Model Building Questions and Answers
I've done a few scale harnesses over time, all were the old-fashioned taped wiring harnesses though: I simply used very fine beading wire, twisting several strands very lightly together, with the various "out-takes" separated and bent outward from the otherwise twisted wire. I then simply coat the harness itself with a thin coating of 5-minute epoxy, just enough epoxy to smooth out the bundled wire. Once the epoxy has started to harden (dry to the touch but still flexible), I bend and shape the harness to the space in which it has to fit, and just leave it there until it's completely hardened, stiff. The last step is to paint the harness itself (generally a semi-gloss black to simulate the color and slight sheen of black PVC tape, install the harness, and hook in the various wires to where they go (drilled holes generally), and last I paint the indivdual wires between the harness and the equipment its attached to in appropriate colors. Art -
For every part in a model kit, there is a cost, and that is a given. In addition, there is the factor of time, production time to consider. The plastic model car kits we buy and build are, simply put, a mass production item. With the limitations inherent in injection molding for mass production, to make a carburetor as intricately detailed, and accurately done as those by Chief Joseph, but in injection molding, would require several molds in the tooling, and quite fiddly assembly by a model builder. Of such are complaints about "over-engineering" a model kit born, unfortunately; not to mention the ultimate selling price of such kits. Like it or not, plastic model kits are necessarily designed to a pretty common denominator, meaning a kit that can be afforded by the largest customer base possible, and readily built by that same largest customer base. The more intricacies in a model kit, the higher the price will be, and the smaller the customer base for it, which is surely understandable. Now this isn't written to discount some of the now-more-common criticisms, such as "floating" generators, alternators, power steering and AC pumps, those issues can be corrected in future kits, some already have been addressed by model companies over recent years. But I do think it's reasonable to point out the limitations imposed by costs, even more complicated and highly delicate assembly which could well turn off a lot of model builders. For these reasons, some superdetailed parts are probably best left to the aftermarket. Art
-
Ford also produced Model T's in Canada, where many T's were built for export to British Empire colonies, so they were also RHD
-
Where to get laquer for airbrushing
Art Anderson replied to atomicholiday's topic in Model Building Questions and Answers
If I might add to what others have said, I'd not discount the idea of MCW automotive finishes. Bear in mind, Dave Dodge pretty much pioneered the idea of making available factory-match colors, mostly aimed at model cars for which no rattle cans exist. Another possibility is Scale Finishes. While Jameston has yet to develop a line as extensive as MCW, his paints are above reproach in my opinion, even though he works with automotive acrylic enamel rather than lacquer. You can get just as nice a finish with acrylic enamel as you can with lacquer, and although this stuff takes longer to dry and cure out, it polishes out extremely well, and being enamel, it has less tendency to orange peel due to the slower drying rate allowing greater flow-out. Again, both lines of aftermarket paint colors do seem expensive--but they are great paints, both--and for cars out of the 50's through the 70's/80's, the factory color choices are far greater than anything that might be available over-the-counter. Art -
If that is truly an English Model T Ford, that third seat would have been termed a "Dicky Seat", A/K/A in the US the "Mother-in-Law Seat". Art
-
Your Model T kit appears also to have been released by Revell at some point in the fairly recent past. The pics I found of it clearly show that it is RHD, which says to me that your's has a British heritage in it's prototype (1:1) Art