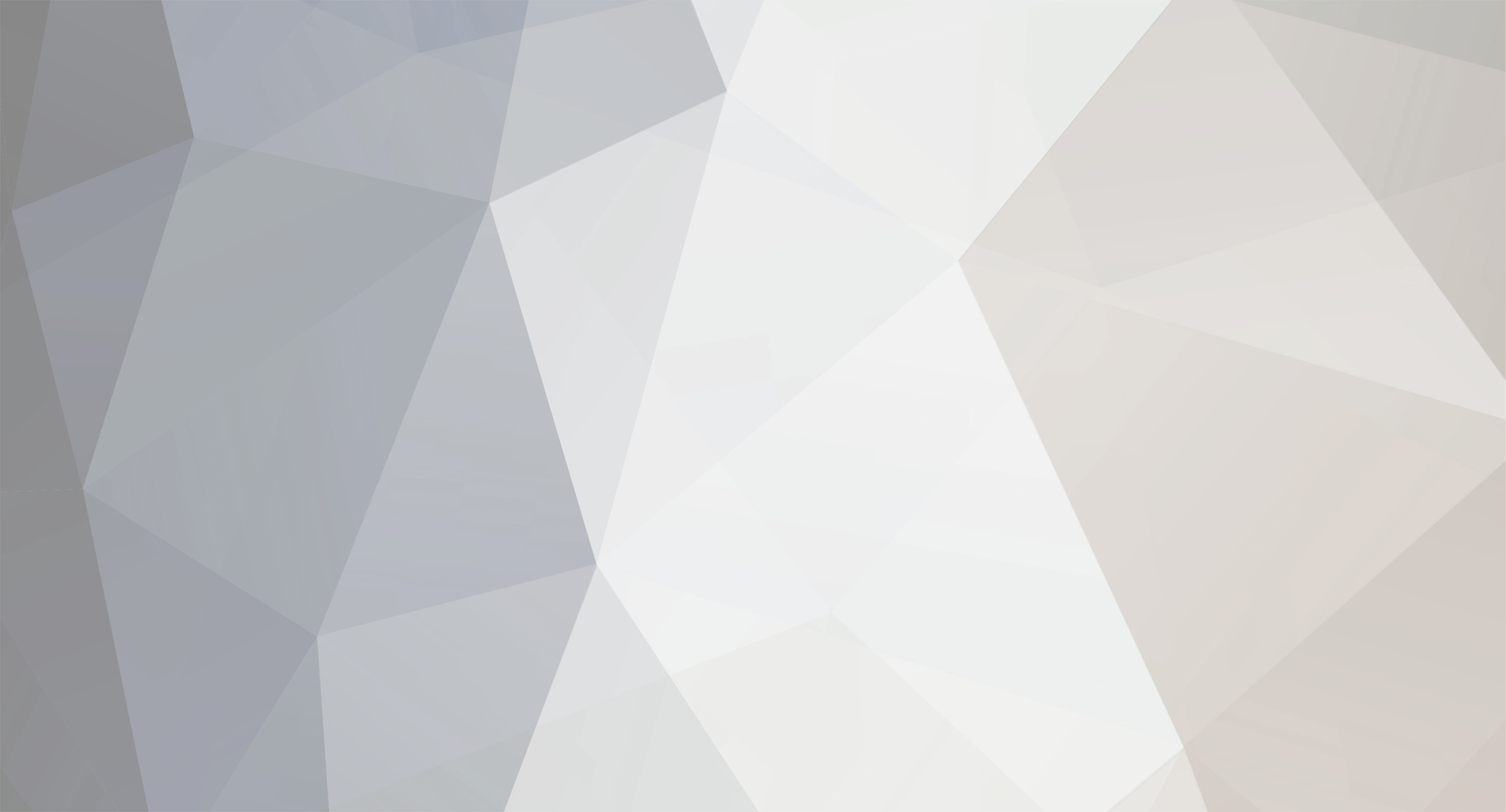
Biscuitbuilder
Members-
Posts
250 -
Joined
-
Last visited
Content Type
Profiles
Forums
Events
Gallery
Everything posted by Biscuitbuilder
-
Works now, but didn't when I posted my response. Thanks John! (Car on a pole, anyone? 8) ) Biscuitbuilder
-
Dan, The link you have seems to be broken? Biscuitbuilder
-
Engine turned dashboards or other parts
Biscuitbuilder replied to Paul Payne's topic in Tips, Tricks, and Tutorials
Back in the early 80's, I scratchbuilt a 60's Watson USAC Dirt Championship car, which needed an aluminum firewall and instrument panel. But, how to "engine turn" the aluminum! I had a sudden idea! Old-fashioned typing erasers are impregnated with a mild abrasive, that will scuff aluminum! So, I bought one, ran it through a pencil sharpener to get a point on the end of the rubber, then cut the wood pencil-style shank and drilled into the cut end to superglue a length of brass rod in it, and firmed up the sides of the rubber tip with superglue as well. I simply chucked in my Dremel tool, and mounted the tool in my drill press. Voila! After a bit of pracice, the thing worked perfectly--good enough to help that car win First Place at the 1985 IPMS Nationals in Indianapolis. I wish I had the car to photograph, but I sold it to a model race car collector about 6 weeks after the Nats, for more money than I ever would have guessed anyone would pay for a builtup. Biscuitbuilder -
How old are you??
Biscuitbuilder replied to KT EASTMAN's topic in General Automotive Talk (Trucks and Cars)
Old enough to know better, but too young to care! Biscuitbuilder -
1:25 scale. Chassis is Revell '29 A Rat Rod, body is modified AMT '29 A roadster, with a lot of the body moldings replaced by strip styrene, and opening doors. The firewall and front of the gas tank are reworked with strip styrene to correct stock appearance--no need back then to punch clearance depressions into these panels, as a flathead Ford V8 will fit just fine in the same space as the 4-cylinder did. Biscuitbuilder
-
Yup, those are working brass hinges! They are model RR items, scale "barn door" strap hinges, that I get here locally at a huge RR shop--they are very nearly to scale, work great. I discovered these hinges probably about 30 years ago, have used them several times on various cars over the years. Biscuitbuilder
-
AMT also issued this basic tooling as a "Jr. Craftsman" kit about 1963 or so. Biscuitbuilder
-
Fergit the "warped mind"! We just BIOP! Biscuitbuilder
-
Bill, I read your post when you first put it up--tried posting a reply right then, but for some reason it never showed up! Cool build of a cool car--Bob Downie did a heckuva job on the master as well. I got a fair amount of ribbing over it, due to its being a "funny little furrin car" but it was reasonably well received, although I've not seen very many of them built up. The MGB-GT resin was an outgrowth of something Roger Sill of American SatCo set up--he had Bob Downie make up a master for a left-hand-drive dash for the MGB kit he was importing, and put Bob in touch with me at Toledo--after some talk, and a bit of persuasion, Bob decided to try the GT body shell. Like your build, BTW! Art
-
Pat Brady, sidekick of Roy Rogers, was on the 50's Roy Rogers Show, which, at least here, ran on TV on Saturday mornings, before the coming of cartoons in that time slot. The opening trailer showed Pat driving Nellybelle at speed, alongside Roy Rogers on Trigger. Biscuitbuilder
-
Actually, It's kinda funny story as to how I came up with the Jeep pickup masters: In March of '96, as I was heading to the Toledo Toy Show on a Friday afternoon, passing through the tiny little town of Rockfield, Indiana, I spotted a Jeep pickup parked in a cow pasture on the edge of town. Making mental note of it, I drove on, and on the way back through Rockville that Sunday, I stopped along the road for a longer look. On my way to Parsippany two weeks later, I took my camera, and a notepad (Indiana SR 25 goes from Lafayette to Logansport, where I picked up US-24 all the way to Toledo -- to go on to Parsippany, I simply hit I-80 at Toledo, then reversed the process on the way home). Back to the pickup: I drove up to the farmhouse, and knocked on the door, answered by a young guy and his wife, who had just acquired the place from his grandfather. Getting permission to climb the gate into the pasture (and being assured that no livestock were gonna be there!!!) I walked over to the truck, and proceeded to do a full "walkaround" with my camera. Finally, after getting perhaps 20 pics of the thing (rusty, but solid), I took measuring tape in hand, and proceeded to get the dimensions I would need for the box, fenders, that sort of thing. All at once, out of the corner of my eye, there stood about 2000 lbs of black angus bull, and he didn't look at all happy to have me as a guest in HIS part of the world. I grabbed my camera from atop the front fender, and clutching camera, notepad and ballpoint, I stepped around the front of the truck, just as that bull buried his hard head (horns attached) into the passenger side door, denting it inward at least a couple of inches. Without so much as a wave goodbye, I hightailed it to the gate, up and over I went, as the critter charged after me--he must have taken a smart pill that morning, because he stopped short of the gate, with me on the other side. Ahh, the things a model car builder will go through to get the references needed, huh? Biscuitbuilder
-
MCM Forum Chat Room
Biscuitbuilder replied to Gregg's topic in General Automotive Talk (Trucks and Cars)
The chat room has always been available 24/7 since it was established over 4 years ago. However, the busiest time is 8-9pm any nite, but of course, many stay lots later than that on Friday and Saturday nites. Biscuitbuilder -
1932 Ford 3 window coupe top chop
Biscuitbuilder replied to Paul Payne's topic in Tips, Tricks, and Tutorials
Basically, with a '32 Ford closed body, there are two ways to work this out: Either lengthen the roof itself, because of the slanted windshield, or increase the slant of the windshield (the A-posts) to lay it back at a greater angle so that it meets the lowered, unlengthened roof. Biscuitbuilder -
Dave, Too bad! Unfortunately, due to the very smoothly curved body of an Airstream, there is no decent way to have made the body shell in any sort of halves, so it could be cast--at least not in any sort of manner that I could have accepted. A couple of casters and I did talk about the idea, but I just couldn't see it being a viable product because of this, so it's strictly a one piece, hollow shell. Biscuitbuilder
-
Bill, and others! Thanks for all your encouragement! Frankly, I got so discouraged with a problem on the underbelly of the Airstream, that I simply had to put it away, lest I make an Airstream-shaped dent in the workroom drywall. To explain a bit: The Airstream is a completely streamlined trailer. Where virtually every other trailer produced, including a lot of Avions (built in Michigan, very similar in appearance) had simply an open bottom, with a conventional chassis of channel steel frame rails, with some sort of cross-bearer floor joists (either steel, or wood(!) ), fitted with all the usual plumbing, springs, axles exposed to the open air, the Airstream had a center "spine" of tubular steel, to which steel channels were welded, crosswise, those channels formed to a curve at their ends, all to create a smooth shape once covered with aluminum sheet. They were as sleekly belly-panned as any Indianapolis roadster or Bonneville streamliner. This belly pan was smoothly fitted to the sides, and riveted in place, the side panels overlapping it, much the same as on an aircraft fuselage (Wally Byam, producer of the postwar Airstream, spent the WW-II years working at Lockheed, building warplanes, and became very well-versed in the structure of airplanes of the day). On the model, in order to give the fiberglass upper shell stability (the glass shell is only about .020" thick), I cut the floor from 1/8" thick styrene sheet, for the floor and glued that in place, inside the bottom edge of the shell. Then, strips of 1/8" styrene were used to build a "gridwork" on the bottom, and rough-filed to shape to make a permanent template for catalyzed putty which was used to create this bellypan. These "ribs" were laid in such a way as to give the riveting rows that were needed for correct appearance. What I DID not bear in mind in all this is that catalyzed putty does shrink oh-so-slightly when it sets up and cures (it shrinks approximately 1/10 of 1 percent, generally imperceptible. However, in doing so, it pulled away ever so slightly, from the edges of the exposed styrene grid, but a few days after it was applied, and AFTER some 600 rivets were installed! So now, I had little hairline cracks in a grid pattern on the bellypan, and every one of them on either side of a line of rivets. Now, I really like doing rivets with styrene rod set into drilled holes--it's just one of those things I see as giving a detailed surface that extra little bit--it's kinda my thing, I guess. But it sure is time consuming, and more than just a bit nerve-wracking. Needless to say, I was most frustrated to realize that I would have to sand smooth all those rivets on the underside, correct the cracks (I've experimented, and CA glue, applied to these cracks after I open them up slightly with a dental burr in my cordless Dremel--sort of like dentistry on a model!), sand all smooth again, and THEN do all those 600 rivets all over again. So, it just got parked, until my disgust cooled down. Now, I think I've gotten past all those hard feelings, so maybe now, it will get finished. As for a tow vehicle, I have a Modelhaus '56 Mercury HT planned for it, but in thinking, I might just upgrade that to one of their excellent 57's. Stay tuned--as they say, it ain't over until the fat lady sings--and she hasn't showed up with the door keys to the Airstream! Biscuitbuilder
-
....or an Airstream trailer? This is a 26' Airstream circa 1956-1960 that I started a couple of years back. The shell is laid up in fiberglas, using the really fine, lightweight glass cloth from the RC section of the hobby shop, along with polyester resin. It was laid up over a buck carved from laminated Dow-Corning blue insulation styrofoam (scraps I grabbed at a nearby construction project). As early Airstreams (prior to the early 70's) used exposed rivets, there are rows of rivets all over the skin of this piece, based on reference pics in books, and online. They are .025" styrene rod stock, set into holes drilled in the fiberglas shell, secured with CA glue, then trimmed to just above the surface, and rounded down with 4000-grit polishing cloths to give the effect of round-headed aircraft rivets--something like almost 2000 of them installed to this point. Here it is, in a couple of pics, to give you an idea where it's at right now: For more detailed pics of how this one came about, check my Fotki album on the Airstream: http://public.fotki.com/modlrA/125_scale_26_airstr/ Biscuitbuilder