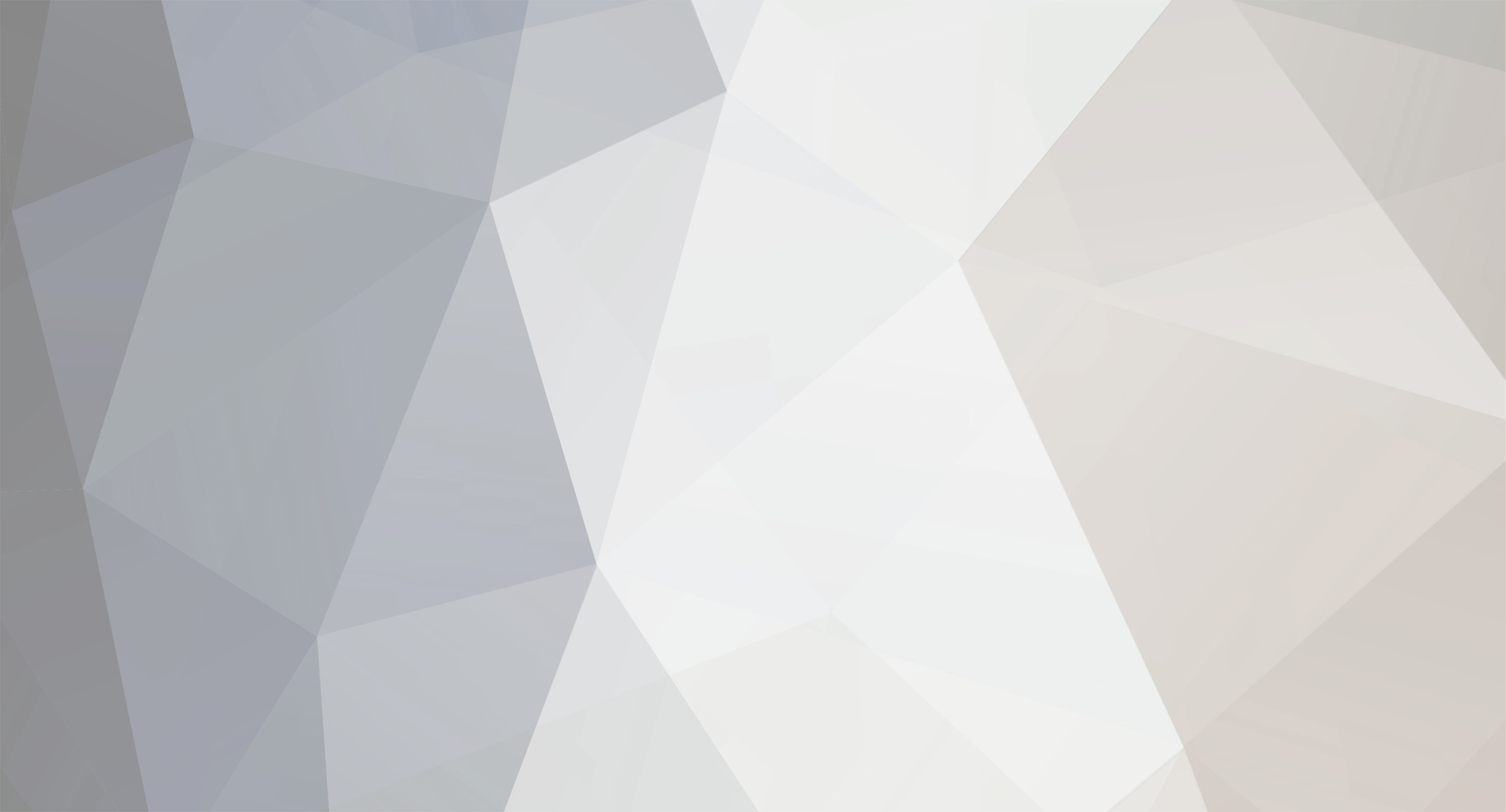
robdebie
Members-
Posts
387 -
Joined
-
Last visited
Content Type
Profiles
Forums
Events
Gallery
Everything posted by robdebie
-
Bump after four months.. Still looking! Rob
-
So everything new is mo better, huh?
robdebie replied to Ace-Garageguy's topic in General Automotive Talk (Trucks and Cars)
Make that McDonnell-Douglas, instead of Lockheed. Rob -
Do you make notes/memory aids as you build?
robdebie replied to Mattblack's topic in Model Building Questions and Answers
Barry: one more route is making website reports of your builds, and that's what I do. I often switch from model to model, and it's great to read back your own report to restart a project. Here's one example, of the Nunu 1/24 Kremer Porsche 935 K3. It's extensive because I did a lot of shape corrections. https://robdebie.home.xs4all.nl/models/kremer-k3.htm I'm using old-fashioned basic HTML for the website coding, so that's not much work. The photo shooting is considerable extra work, but generally I like the shots, so that's a reward in itself. Plus they are often useful in forum threads. Rob -
large scale Large Scale, Paint, airbrush size
robdebie replied to Jon Haigwood's topic in Model Building Questions and Answers
Watch this video, you'll be impressed! https://www.youtube.com/watch?v=lCKZ_fo4eW0 I bought a Paasche H after seeing this, and it gives me identical results. Here are some tests with all enamel brands that I had in stock. No polishing, no clear coat, one paint session. Rob -
resin casting and molds
robdebie replied to Paul Payne's topic in Model Building Questions and Answers
Did you leave the lids off for the outgassing? If so, the resin absorbed moisture, and foamed because of that moisture during the cure. I try to limit my resin's exposure to air / moisture as much as possible, but with every opening you let in fresh air with new moisture. When I reach the bottom of the bottles, they have had maximum exposure, and the mixed resin will foam, if not put in a vacuum. Fresh casting resin should not have any of these problems though. Rob -
1/8 scale aftermarket Entec JPS decals
robdebie replied to jpolacchi's topic in General Automotive Talk (Trucks and Cars)
Best Balsa has a great decal set: https://www.bestbalsakits.com/tamiya/tamiya-detail.asp?kitnumber=3239 Rob -
resin casting and molds
robdebie replied to Paul Payne's topic in Model Building Questions and Answers
I use the 7-minute Smooth-Cast 305 (with some black dye), and I'm happy with its material properties after curing. I cast some fragile parts, like the jet nozzles right from center and the bomb fins in the center, and never had failures. On the other side, since the cure is slow, the resin doesn't heat up, and a hot cure of a fast resin might give better material properties. The drawback of a hot cure is that you'll have more shrinkage. Rob -
I'm looking for the DVD-ROM 'Scale Auto Enthusiast - The First 35 Years'. In return I can do custom decals, or parts casting, or 3D part design and printing, or maybe something else. More on decals and casting can be seen on my website: https://robdebie.home.xs4all.nl/models/customdecals.htm https://robdebie.home.xs4all.nl/models/casting.htm There are eleven pages about 3D CAD and printing projects on the main modeling page: https://robdebie.home.xs4all.nl/models.htm I joined this forum in 2016., and made 379 posts so far. Rob de Bie Delft, The Netherlands
-
Building on Peteski's comments, maybe you can scrape the resin parts, to release the original smell. Rob
-
That's an amazing story - I had never heard of resin shrinking after being cast. I do know that polyester can shrink a bit after curing, in boats etc the 'fiber print through' will often develop over a week of so. But I'm guessing these car bodies are polyurethane as usual, and I've never ever read accounts or warnings of shrinkage after curing. Maybe your account of the two body halves contains a clue: it sounds like the paint caused the shrinkage. But even that I've never heard of. It's probably no help to you, but here's what I wrote about shrinkage on my webpage about vacuum casting (https://robdebie.home.xs4all.nl/models/casting.htm😞 - - - - - - Shrinkage A few words on the subject of shrinkage. Shrinkage can occur both in the mould and in the casting: regarding the mould: one of the reasons for choosing addition cure (platinum catalyst) silicone rubber over condensation cure (tin salt catalyst) silicone rubber is that the former has close to zero shrinkage. The latter shrinks during cure, and (amazingly) continues to shrink during its life. Therefore my choice is simple: I use addition cure silicone rubber, and the mould will not show shrinkage. regarding the castings: polyurethane resin itself shrinks very little during the curing reaction. However, there's a big 'but': when the resin heats up during the cure, because the cure is exothermic, it expands, pushing out some resin from the mould cavity. When it cools down after the cure reaction, the natural thermal shrinkage occurs, making the part smaller than the mould. The resin's potlife mostly determines the shrinkage: a fast cure means it gets hot, and a slow cure means it will hardly heat up. Fast curing resins can get so hot that they form steam bubbles in the centers of the castings! I use a 7 minute potlife resin (SmoothCast 305), and I never felt a temperature increase in the small parts that I produce. Therefore the resin hardly shrinks. SmoothOn lists less than 0.1%. I tested the above theory by measuring my largest casting, the ALE-2 chaff pod. The master is 87.5 mm long, and of the five castings that I measured, four were 87.7 mm, and one 87.9 mm. I blame the length increase on temperature differences of the days I cast the mould, and the days I made the castings. Silicone rubber has a large coefficient of thermal expansion: I found values ranging from 200 to 300E-6/°C. Compare that to polystyrene 70E-6/°C and aluminum 21-23E-6/°C. That means a 10 °C difference makes a 0.25% larger silicone rubber mould, and that equals the size increase from 87.5 to 87.7 mm of my ALE-2 pod. - - - - - - Rob
-
In my experience, epoxy putties don't stick well during application, so that might create the impression that it won't work. But once cured they are attached solidly. Rob
-
Video of a fabulous kit collection
robdebie replied to robdebie's topic in General Automotive Talk (Trucks and Cars)
Yep.. It helps a lot to freeze the film every few second (use space bar), and study what you see. Each frame is quite sharp. Rob -
Video of a fabulous kit collection
robdebie replied to robdebie's topic in General Automotive Talk (Trucks and Cars)
Here's a third video: https://www.youtube.com/watch?v=MlSOAy21qmA Rob -
I want to discuss puttys and fillers.
robdebie replied to ctruss53's topic in Model Building Questions and Answers
One more vote for epoxy clay, like Milliput, Tamiya epoxy, or Apoxy Sculpt - I use the latter. No shrinkage, no solvents that make the plastic swell, good hardness after cure, nice to sand. If required, you can use water to smoothen the putty. The drawback is the mixing required, but for me the advanteges outweigh that completely. I do the mixing by squashing the two compenent under a modeling knife, and repeating that a number of times. I try to limit skin contact as much as possible. Here are some recent examples of work with ApoxySculpt. Rob -
Video of a fabulous kit collection
robdebie replied to robdebie's topic in General Automotive Talk (Trucks and Cars)
Here's another video of the same collection, showing lots of different areas of the collection room: https://www.youtube.com/watch?v=bVN-5upkwXk The filming is shaky, but it's again worthwile. Rob -
Video of a fabulous kit collection
robdebie replied to robdebie's topic in General Automotive Talk (Trucks and Cars)
Sorry, I hadn't seen that this video was already mentioned in the thread '40 year model car and airplane collection.' But it's nice to see that I wasn't the only one blown away 🙂 Rob -
Like Peteski, I glue nearly everything with CA. Transparent parts are the exception, I use epoxy for that. But I never use plastic glue. I am the exception in our club though. Rob
-
You on the other hand have a very good eye for shapes, something that is rare in my experience. I've studied 'seeing shapes' among modelers, and I think only 10% sees shapes and shape errors. Just to be sure: I wasn't talking about different wall thicknesses, I only observed the outer contour of the cab-to-hood lip. Rob
-
Again I love what you're doing here. I designed a new grille and hood for my 'Duel' 281, a club member printed them for me. To design the hood, I needed the cross-sections on the front and rear sides. I had designed the grille piece earlier, so that gave me the front side shape. I scanned the cab to find the rear side shape. Next I tried to find simple geometric shapes to define the shape, so I could copy them in my 3D CAD software. I used a rectangle (blue), two circles (red) and an oval (yellow). An 'interesting' discovery was that the hood shape wasn't symmetrical; I've drawn in an 0.6 x 0.6 mm square (white) to illustrate the deviation. This could explain why some built AMT Peterbilt 359 models look slightly twisted in front view. Rob
-
Steve, I just found your thread, great stuff! I will comment on a few things. I'm slowly (slowly) converting a 359 to a 281, to build the 'Duel' movie truck. First that wheel/tire size. I'm very happy to read that you too think that the kit wheels and tires are too small. Most 'Duel' models looked wrong to my eye, and one problem appeared to be the wheel/tire size. A photo analysis with two known dimensions, 202" wheelbase (measured on the front rear axle, since this truck has a tag axle), and 120" (119 1/4 actually) cab size. I kept measuring tires in the 44-45" diameter range. The kit tires are the equivalent of 40.5" diameter. AMT's Part Pack PP028 'Semi tractor tall tires 11.00-22' are the equivalent of 41.4". I did another photo measurement that established the wheels were 22", see the rest of the analysis here: https://robdebie.home.xs4all.nl/models/peterbilt-3d-1.htm Therefore the tires must have been 11.00-22s. I looked for period tire data books on Ebay and Worthpoint. I found very little, but one brochure listed 44.1" diameter for a Goodyear Unisteel 11.00-22. Hakan Persson found a US supplier of 'old style' tires: 11.00-22 14PR G STA Super Transport TT listing a 44.7" diameter. Those values fit my analysis, and I'll go for 44" or thereabouts. Apparently no model truck tires are available with this diameter, but I'm happy you designed them yourselves. I'll probably do the same. Conclusion: I agree with your 'larger wheels/tires' theory, at least for my movie truck. Of course I don't know what other Peterbilts had fitted. And I'm happy that you have an eye for shapes, and noted too that the wheel/tires were too small. Rob
-
resin casting and molds
robdebie replied to Paul Payne's topic in Model Building Questions and Answers
Robert Tolone did a video on using different pressures, but it doesn't really answer our question. I would even dare to say that he did not consider the air absorption theory. Rob -
resin casting and molds
robdebie replied to Paul Payne's topic in Model Building Questions and Answers
In the past, I did quite a lot of vacuum infusion of composite parts. The biggest was 10 by 3 meters 🙂 We would always de-air the epoxy resin thoroughly, and if the injection went as planned, we produced totally void-free parts. But if you would get a small dry spot, with the injection encirling a spot, the tiny amount of air present would often be absorbed, solving the problem. I know that research was done on the de-airing process, but I did not participate in that. Here's one example of such research, but as far as I can see, it does not discuss 're-absorption' of air, after de-airing that same resin. But if the gasses got in the resin before de-airing, they surely must be able to 'get in' after de-airing too. https://www.sciencedirect.com/science/article/abs/pii/S1359835X20300567 The paper does not discuss the effect of pressurizing the resin-air combination. But that must have been studied extensively for autoclaving of composites, so I expect scientific literature on that too. All in all, I still can't prove my assumption, but I'm pretty sure that I witnessed air absorption in practice, with epoxy. It should be fairly easy to test the assumption, by curing polyurethane samples at increasing pressure, then cutting the samples and study for air bubbles. Actually, that might be a good question for Robert Tolone, who has a great Youtube channel: https://www.youtube.com/@RobertTolone/videos Rob -
resin casting and molds
robdebie replied to Paul Payne's topic in Model Building Questions and Answers
I don't know if it's of use, but here's how I copied a truck tire with single-piece mold and vacuum casting. I filled the master tire with Apoxie Sculpt to make it solid. Worked perfectly. Rob -
resin casting and molds
robdebie replied to Paul Payne's topic in Model Building Questions and Answers
I agree that vacuum casting makes more sense. But pressure casting works very well too 🙂 Maybe there's another mechanism with pressure casting: I have a feeling that small bubbles do not get compressed to a smaller volume, but that they are actually absorbed by the resin. Why do I think that? I have never seen tons of tiny bubbles in cured pressure-cast items. It's interesting to look at the numbers. A 1 mm diameter bubble has a volume of 0.52 mm3. Compress it to 5x ambient pressure, and the volume becomes 0.10 mm3, and that gives a 0.6 mm diameter. So, the bubble size reduction is not very impressive. So one should see lots of tiny bubbles in a cured part - but you don't. I'm sure there are technical papers and studies on this subject.. Rob