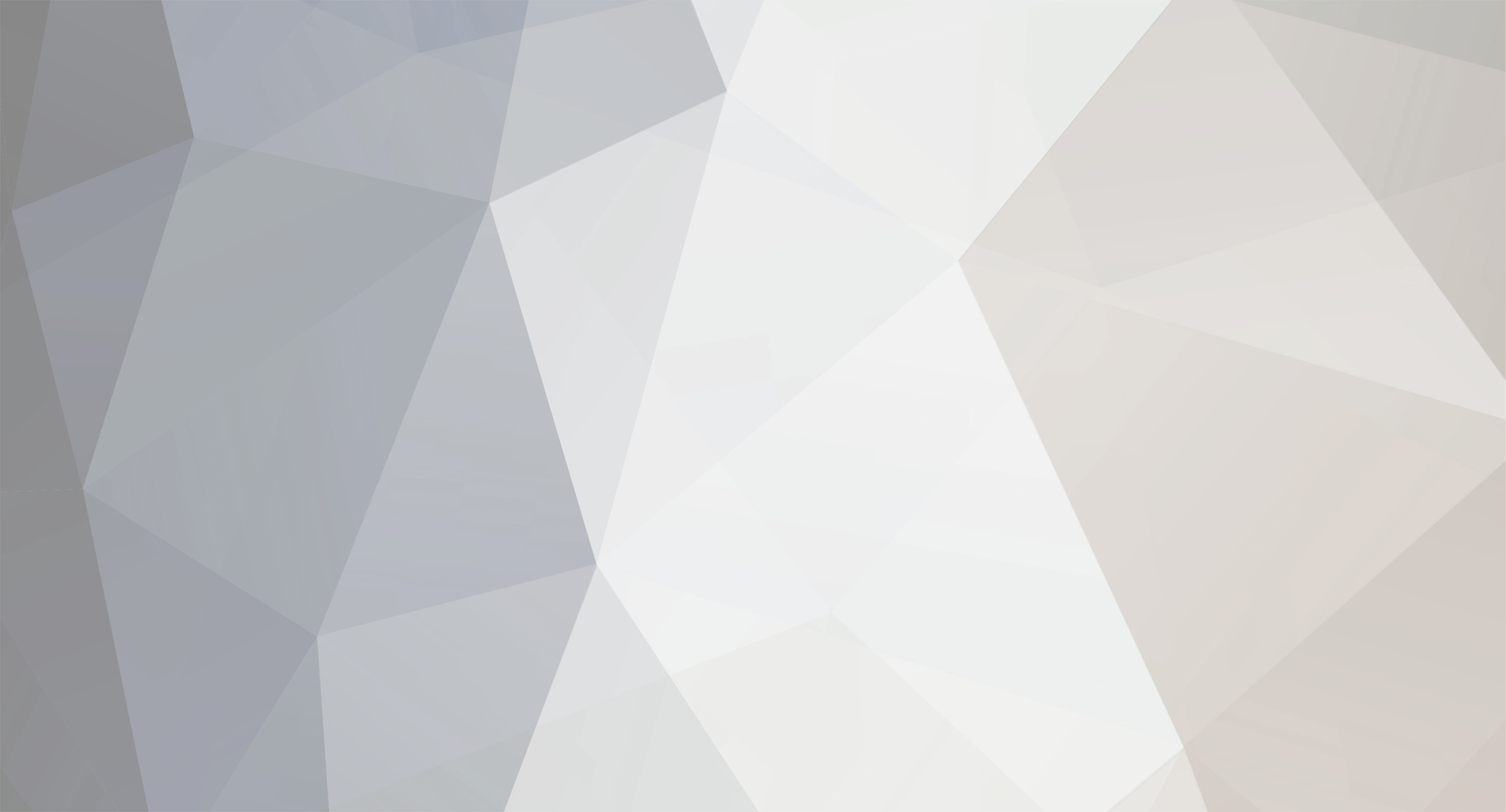
GMasterG
Members-
Posts
102 -
Joined
-
Last visited
Everything posted by GMasterG
-
Many of these SalvinosJR kts contain the same parts so there is not much to be added by posting the same progress pictures over and over again save for the purposes of gauging one's own improvement. To that end, below is the engine fitted into the engine bay. This is without a doubt my best effort to date. It is symmetrical, the exhaust headers are placed/spaced perfectly to receive the exhaust dumps and a test-fit of the fan and radiator confirmed sufficient tolerance to make everything fit with no room to spare. I used silver chrome from DSPIAE and I'm delighted with the finish it's given me; having the engine drop in so effortlessly without spoiling the finish was quite a relief. The other aspect of the finish that I find very visually satisfying is the use of automotive 1k clear which has given a sense of depth and definition to the surfaces that I haven't previously obtained on other similar builds. I've found some opportunities to incorporate some more 3d-printed parts such as the red spark plug caps which add a nice bit of detail. The distributor is also 3d-printed. I forgot to trim the base to lower the overall height which I was reminded of when I tried to fit the breather cross-pipe which now doesn't sit so I've had to bend a new one out of 2mm brass pipe. I seem to have had success with it so I will paint it up and fit it during the week. I've not secured any of this yet because experience has taught me that some not-so-minor structural adjustments to the lower engine mount might be required once the air filter is fitted to allow clearance for the hood to sit flush. There is nothing that frustrates me more than a proudly-sitting hood. Not only is it visually distracting but also speaks volumes about one's own inability to plan ahead and foresee potential pit-falls.
-
Patto's Place has many options and variations of ETCC Group A racing livery for this model. I am currently building this kit as the '85 Hahne-Goss Bathurst 1000 winner.
-
Well it's certainly been more than a moment since I posted any progress in this build diary but since the end of January I've finished Richard Petty's 64 Plymouth Belvedere and Bobby Allison's Dodge Charger from 1971. And now returning to this group of four they will be the beneficiaries of the new standards that I've set myself having completed those two models. Firstly, I took delivery during the week of some Meguiar's Polishing creams and compounds so I set to and gave the Foytmobile a polish. The automotive 2k has really responded well to it. Secondly, I added bare-metal foil to the front and rear window surrounds; something I now regret not having done to Allison’s Charger. Thirdly, I added the rear window. In the process I smeared a little resin glue in the top left hand corner which the Meguiar's Plastix polish removed without fuss and it has left the clear plastic looking very good. Finally, I finished the underside and it is here that you can notice a few details that this car has inherited from the Charger build, namely; the detailed drive shaft, heat-shrink tube between the exhaust headers and pipes, and a little weathering with Hot Metal Sepia from Alclad. Tomorrow I can insert the front glass and unite the body with the chassis before adding the wheels and calling it done - what could be easier?!!
-
Thank you Todd. I consider myself a student of history so I appreciate the context and also the automotive anatomy lesson. I also appreciate your kind words regarding the build. I really like the NASCARS of the 50s through to the mid 70s and especially the Dodges and Plymouths. I have Bobby Isaac's K&K Charger slated as my next build to begin but for the next couple of months I'm going to focus on completing the four Oldsmobiles.
-
-
I’ve had a very productive morning fitting the engine into the bay and connecting the wire from the ignition coil to the distributor: The exhaust headers needed a little manipulating to get them to sit on the pipes and so for neatness and a finished look I added some heat-shrink tube which I think looks smart and I even got a little too willing with the cigarette lighter which has resulted in some nice weathering around the joins: At first I wasn’t sure what benefit there would be in separating the transmission from the engine save being able to paint the two separate parts easily. In the end it proved a master stroke allowing me to locate the engine correctly and then have the ability to simply drag the transmission into place and set it with a couple of beads of superglue. I then added the remainder of the cooling and radiator system: The engine, radiator and air intake all sit very plumb; it's the cross-over breather tube that sits a little crooked that gives the impression of a poor fit. Then it was time to add the clear windows, join the body to the chassis and add the chrome. I used UV light-activated glue to fix the clear parts and it worked very well: And it's worth mentioning for anyone wondering about how the Cartograf decals react to clear coats: there is an acrylic lacquer clear sprayed liberally over the top of the Dodge decal in the picture immediately above. I applied all the decals with Markfit and once set I burnished them into the plastic with Markfit Strong. This one had been sitting on the chrome piece for a number of weeks prior to spraying the clear which I did on Thursday morning (I think). The decal was unaffected by it. Notwithstanding all of the success, the morning’s labours were not without some minor incidents that proved a little frustrating, but which weren’t insurmountable. I managed to flick the air cleaner onto the windscreen and get a couple of smears of superglue on the clear plastic. Fortunately the larger of the two is obscured by the hood when it’s in place. However, the smaller of the two will be visible and I’m in two minds as to whether I should try polishing it out. I thought I’d cracked the interior cage trying to fit the body to the chassis but fortunately it was just two parts breaking at the joint which I was able to fix with some CA glue. Now it’s time for lunch and an episode of something on Netflix.
-
The progress is slow but it’s steady with a focus on doing whatever it takes to maintain quality control to the best of my current skill level. So far I’m happy with the results. Tonight a little work on the underside with the exhausts fitted and the front section that I broke two days ago successfully rebuilt with brass rod, installed, and paint patched. I used some Alclad hot metal sepia on the exhaust pipes as well as some Tamiya panel-liner and although you can't see it in this picture I drilled out the ends of the pipes and weathered them as well: I’ve painted, detailed and installed the driveshaft: as well as the front air intake: you can also see that I’ve ground down the cross-member onto which the engine mounts to allow myself some comfort that I won’t be stuck with a hood that won’t close.
-
Anyone with a sharp eye will notice in the pictures above that there is a section of the under-carriage missing: Whilst test-fitting the chassis to the body I managed to snap one of the arms underscoring the adage that a build ain't over until it's over and it is these last stages of putting everything together that can prove to be the most fraught with peril. I recall something similar happening late last year when I built Allison's Hardee's car and I simply glued the broken piece of plastic back into place. It's a measure of how far my skills and my confidence in them have come that last night, in an attempt to look on the bright side, I saw this as an opportunity to build something better: Fortunately, the 4 Oldsmobile Cutlasses that I am in the midst of building, despite having a different front-end setup, still include this part (I have no idea what it's called) on the sprue and I only needed one of them. I drilled 0.2mm pilot holes into the cross-member and into the section of the part still attached to the chassis of the Charger. I then drilled 0.8mm holes for the brass members. The brass rod is 0.81mm so I tapered it at the ends to make it fit snugly. On the bright side, the test-fit seemed to indicate that the car's overall ride height and stance is good, and I think I will even manage to fit all of the engine into the bay including the airfilter (although I've had to grind out all of the profile underneath) with a bee's dick of clearance to the under-side of the hood.
-
-
Finally I have the engine to a standard I’m happy with and I’ve progressed to doing a little detail on the trunk assembly. I found a picture of a 73 Dodge Charger that showed some very simple technology for the fuel cell: a fuel-in pipe that was ribbed; a breather pipe that wasn’t ribbed; and a much thinner fuel-out line that went through the rear firewall. The engine required so many touch-ups and so many breaks from frustration but it was well worth it. I was just determined that I would not accept anything less than what I know is work to the best of my current ability. Now that I’ve shown myself what that standard is I won’t accept anything less in future builds.
-
Dan I've just purchased this kit to build and I'd like to use this post as a build diary. Have you made any further progress since your last post?
-
I wasn’t happy with this engine’s assembly so I pulled it apart and started again. By the end of the weekend I’d managed to add spark plug cables using 0.4mm solder. By refusing to accept poor workmanship and keeping clear focus we can all improve the final results.
-
Thank you.
-
-
I really like the way that you've weathered this car - very authentic and very well done. What did you use?
-
Thank you. Yes, it's a very eye-catching color scheme. I was fortunate enough to have a full bottle of engine orange and it happened to be so close to an exact match.
-
Hi Todd. Thank you for the encouraging words. You may have noticed from my subsequent posts that this certainly won't be my last. I know nothing about NASCAR but I actually really like making these models
-
Thanks Chris
-
Thank you Donato.
-
Thank you Larry
-
Thanks Zak
-
Thank you Steve
-
Some progress on the engine today. I’m happy with the finish of the individual parts but I was a little absent-minded and forgot to test fit everything before painting and gluing and it shows. I’m sitting here scratching my head and wondering how I could forget to do something so basic. Notwithstanding that, I’m happy with the detail I’ve added such as the spark plug tubes to take 0.4mm solder and the 3D-printed MSD dizzie which I detailed with some panel liner.
-
Time to now pay some attention to building the engine before fitting together the two halves of the chassis. Previous experience with the Oldsmobiles tells me it’s best to leave fitting the steering wheel until after fitting the section of the steering column that runs between the firewall and the steering tie rod.
-
Test-fitting the roll cage. I initially assembled the 3 sides, top cross-bar, and rear cross-stays and fit them in place. Next came part 80 running from lower passenger-side front to the rear. Parts 77A & B aren’t long enough to connect to the locations they are meant to be placed so I’ve made new ones with 2mm round styrene. The other little detail that pleased me was the rectangular piece on the passenger's side floor. I have no idea what it is but I used it as an opportunity to apply some different-colored washes over the base silver. I don't think that I've truly appreciated the purpose of using such materials until now. The brown and black tones that I've used have created some really nice subtle shading. The highlights and contrasts have created depth and realism to the part (whatever it is). While I'm at it, I should give myself some praise for the metal bezel around the fire extinguisher gauge. Compared to the first two that I made for the Oldsmobiles that I am building, I fashioned this one with greater ease and affixed it to the extinguisher's face with greater precision and cleanliness. It's by these tiny milestones that we measure the development of our skills as modelers and it's important that from time-to-time we pause to recognise that progress.