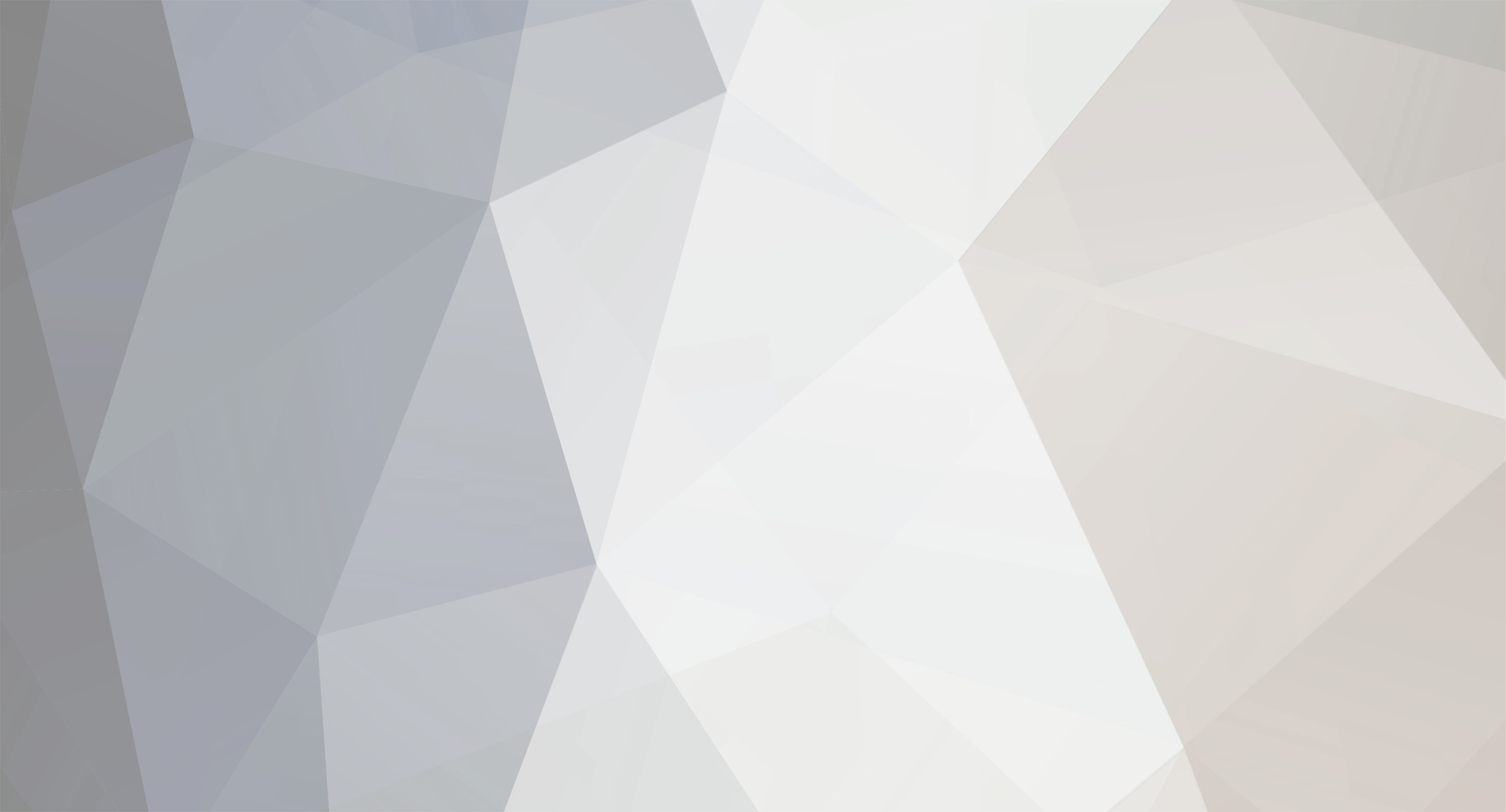
Art Anderson
Members-
Posts
5,052 -
Joined
-
Last visited
Content Type
Profiles
Forums
Events
Gallery
Everything posted by Art Anderson
-
Z'd, ZEED FRAMES SIMPLIFIED TUTORIAL
Art Anderson replied to Ace-Garageguy's topic in Tips, Tricks, and Tutorials
Easiest way to do that is to use a second frame, which will allow you to make the kicked up portion at the rear longer to compensate for the shortening effect that would otherwise have to happen. Art -
Source for throttle return springs
Art Anderson replied to Bonekrosha's topic in Tips, Tricks, and Tutorials
Another quick source for "throttle return springs" is the coupler jaw spring from Kadee HO model RR couplers. They are sold as replacement parts, a dozen to a package, already formed, and made in finer wire than you can wind over a bit of rod stock and pull off. Being phosphor bronze, they don't crush easily either. Art -
1950 Oldsmobile clear hoods.
Art Anderson replied to Scalefinishes's topic in Model Building Questions and Answers
That's a modern-made hood though. Oldsmobile had a small run of those hoods made for new-car introduction time in the fall of 1948, for dealers to install, to show off the new Rocket V8. The clear panels were trapezoidal in shape though, straight sides and ends, and didn't come all the way to the front of the hood like the show car pictured. They did wrap downward on the sides of the hood though. It would be easiest to make from clear sheet plastic, as those clear panels had a fairly simple curve to match the sides of the hood, no compound curvature. It's interesting to note, however, that this was not the first time plexiglas was used to make a transparent hood to show off a new engine! Ford had some made in 1932, full hoods for the Deuce, which showed off the new Ford V8 engine. Those were 4 piece plexiglas (plexiglas had just been introduced by DuPont about the same time as the '32 Fords), hinged just like the stock sheetmetal '32 hood. Art -
I've been doing some research into early tires, and have found some interesting stuff: Early on, automobile tires, indeed rubber products of all sorts, came in a variety of colors, back in the years before the First World War! Straight gum rubber, of course, had poor wearing characteristics, and it was also very subject to deterioration from ultraviolet light, along with the pollutants stemming from automotive use (grease, oil, even gasoline). Very early on, additives were used to extend the useful life of gum rubber in automobile tires, including zinc oxide, which of course is stark white in color. Zinc oxide gave hardness and durability to gum rubber, in much the same manner as carbon black, and even iron oxide was used. Automobile tires in those early years apparently could be rather colorful--Goodyear Tire & Rubber made their first "Blue Streak" tires (blue sidewalls!) in 1916, along with red sidewall tires as well. Red rubber was, of course, quite common, well into the 1920's (Model A Fords used red rubber for radiator hoses and fan belts straight from the assembly line!), and even the new, 1928 Model A used red hard rubber in their molded steering wheels (keep that in mind should Round2 follow up on a reissue of the AMT 1928 Model A Tudor--they have found the tooling, and have run test shots of it, I was told at NNL East by their representative!!!). However, regardless of the type of material mixed in gum rubber to extend its serviceable life, carbon black was by far and away the most popular, being the most plentiful and least expensive--it was a common industrial byproduct, as opposed to specially made pigments having other colors. Additionally, by 1910, there were at least one million automobiles and trucks in use in the US, a number that would increase dramatically over the next few years, as Ford was attaining production numbers equal to the entire rest of the auto industry by 1913--with a resulting demand for tires that could be produced quickly and inexpensively. Another thing I found, which reduces to a myth, is the notion that Ford Motor Company used Firestone tires exclusively--apparently they did not. It sort of makes sense, given the massive production numbers achieved by Ford even by 1914 (when they produced over 400,000 Model T's) that Ford had to source tires and other rubber products wherever they could find them. While I haven't seen them, I read that photo's do exist of Model T's and Model A's coming off assembly lines at times, with tires of different brands ON THE SAME CAR. So, there is a lot more to the story of tire colors than even I would have imagined. But one thing stands out: There seems to be no definitive date or time when Fords ceased coming with "white" or very light colored tires and settled on black rubber. But then, the concept of annual model or styling changes didn't come about at Ford until 1933, most all changes coming as new parts were designed, and added to the mix on the assembly line, as "running changes". Art
-
White tires/Black tires
Art Anderson replied to Harry P.'s topic in General Automotive Talk (Trucks and Cars)
Bill, And, how many owners of Ford pickup trucks 1928-52 are aware that their trucks were built without exposed wood whatsoever in the bed? That's right. During that time period, Ford built pickup boxes with oak floors, then covered the oak with a section of sheet metal (with drain holes at the front corners), some years even having skid strips stamped into them! Art -
White tires/Black tires
Art Anderson replied to Harry P.'s topic in General Automotive Talk (Trucks and Cars)
I believe Coker Tire Company did make a run of "buff-colored" tires in the high-pressure, clincher-rim design several years ago. Art -
White tires/Black tires
Art Anderson replied to Harry P.'s topic in General Automotive Talk (Trucks and Cars)
If there was a perceived market for such, yes. Art -
I really didn't much care for the oversimplified, almost crude frame from Revell's '37 Ford pickup kits, but what to do? I got to researching Ford V8 chassis, and discovered that except for minor details, Ford passenger car and light commercial frames were essentially the same design (and a lot of identical parts) from 1933 to the end of the 1940 model year (1941 in the case of pickups and sedan deliveries). Knowing that Revell's '40 Ford convertible/coupe kits have a really nicely done set of cross members, I did some comparisons, discovering that with just a bit of cutting and filing on the '37 frame, the '40 parts fit like a glove. Here's the result: The result speaks for itself, I think. While it would be neat to have the side rails molded in channel section, like the real thing--that would have meant a completely multi-piece frame, and aligning that could be a real nightmare--I am OK with the side rails as they are. However, the oversimplified crossmembers in the 37 kit frame just don't hold a candle to the '40 units, given their "swiss-cheese" holes, and at least a hint of the channel section for the X-beams themselves. Another consideration is that I want to install complete mechanical brake detail, along with a fuel line, spedometer cable--and some of that detail, along with the exhaust system, will run through the X-member framing. Oh well, one complication leads to another, I guess! Art
-
Dispelling Modeling Myths
Art Anderson replied to JollySipper's topic in General Automotive Talk (Trucks and Cars)
I see neither truth nor falsehood in any of these so-called "myths", but rather that regardless of tools or materials that may be available, many of us prefer techniques which we have developed over the years, that work well for us. Bear in mind, not everyone has seen with their own eyes, nor had available locally, many of the tools and materials that can be found in the hobby and related marketplace nowadays. Additionally, not every modeler likes every possible tool that has come down the pike, being comfortable with the tool or technique that has served them well over time. For some modelers, it's the trip to the finished project that is important, for others, it's the finished project--regardless of the route taken to achieve it. Art -
White tires/Black tires
Art Anderson replied to Harry P.'s topic in General Automotive Talk (Trucks and Cars)
Harry, I dunno, unless it's for the same reason that people restore old cars with incorrect finishes on some parts. The white tire thing in restorations comes, I suspect, from owners seeing, and mis-interpreting the colors of things from old, rather primitive black & white photographs. If you go to antique or classic car shows, stop and look at some of the restored trucks, for example: Older trucks had a lot of exposed wood in them, which was painted when they were originally built, oak being the primary wood for bed floors, stake fences and such. But, one can see at shows, and in most pictures of "restored" old trucks not only clear finished oak, but walnut, mahogany and the like. On a pickup bed floor? More highly finished than a concert grand piano? Not hardly--but people do it, because they think it looks properly restored. I could go on, but my reference to wood in antique cars and trucks is an illustration of how "over restoration" crept in over the years. Art -
White tires/Black tires
Art Anderson replied to Harry P.'s topic in General Automotive Talk (Trucks and Cars)
To start with, as Longbox55 correctly pointed out in the now-closed thread on this topic, there never were white tires on early cars (from the beginning to about 1914 or so), and for that matter, there weren't any truly black tires until the advent of synthetic rubber made from petroleum byproducts during WW-II. Prior to our entering WW-II, all rubber used in the US was made from natural latex, which is milky when harvested, but turned a buff color when vulcanized. But why do those early tires show up white in contemporary photographs? Very simple: Prior to the 1930's, when all photography was black & white, the camera's of the day, along with the photographic emulsions available, were very poor at "translating" the myriad colors into innumerable shades of gray--hence the often stark contrast, particularly in bright sun, making light colors seem almost bright white, and many darker colors appearing as coal black. Such photo's, when they are shown (in books, newspapers, magazines and yes, online!) always seem to perpetuate that myth that early car tires were white. To see what color those tires actually were when newly mounted, take a look at a "classic" 10-speed bicycle tire--the one with those light yellowish-tan sidewalls--up until the late 1990's, those bicycle tires had sidewalls in natural latex rubber, combined with black synthetic rubber for the treads and covering the bead. True white rubber on car tires really didn't come into use until the late 20's, when the first whitewall tires became available. With the addition of carbon black to latex rubber, tires became gray, the darkness of the gray depending on the concentration of carbon black in the mix. Just as with paints, no matter how much black pigment you add to white (or in the case of vulcanized latex rubber, "buff"), you cannot come up with a true black. And, if one looks at pics of even new cars pre WW-II, the tires come across as dark gray, not truly black in color. As for the change from natural latex color to "black" tires at Ford, that would have hinged on two factors: When Firestone (the exclusive rubber supplier Ford--tires, hoses, belts, floor mats) from 1903 until the fiasco of tire failures on Ford Explorers, changed their rubber blend would have been the key. I believe that would have been somwhere during 1913-14, and probably happened as black tires became available in quantity. Hope this helps! Art -
mom and pop vs. big hobby shop
Art Anderson replied to Q tip's topic in General Automotive Talk (Trucks and Cars)
Certainly, the days of the "hole in a wall" hobby shop as I knew them growing up is over, done, finis. It takes serious capital to fund a viable retail store, hobby shops included; in the range of $200,000 and up just for inventory (time was, a person could make it go with perhaps $35,000 in inventory, backed up by agressive, almost daily re-ordering, but that was 35 to 40 years ago. All that said, I much prefer going into a retail store for my hobby needs--while I do order online, seldom is that for anything I cannot access locally. I look at it this way: If I want my LHS to have that bottle or spray can of paint, glue, perhaps some styrene, then I had better be willing to grace their cash register with the purchase price of kits as well. Nobody is going to make it on a dollar here, five dollars there in the hobby business. (Spoken as one who worked both full and part-time in a large hobby shop for years, owned my own for 8 years). Art -
Recommend a pin vise please
Art Anderson replied to Jantrix's topic in Model Building Questions and Answers
I've got several pin vises, and the only time any of them has failed to hold the smallest of drill bits was when the collet that should close completely for the smallest of drills had some bit of debris caught in a slot. My cure for this? Remove the collet from the pin vise, and slip a single thickness of 400-grit sandpaper (use a piece that is fresh, never used nor folded here), then simply slide it back and forth in each of the two slots. This has always removed whatever tiny bit of crud from inside the slots, allowing the collet to close up infinitely. Art -
Considering that Modelhaus, arguably the "gold standard" of resin casters, has their bumpers, grilles, wheel covers/hubcaps, and small chrome parts plated by exactly the same process used on plastic kits, yes, resin parts can be plated in the very same manner, by any aftermarket plater. Art
-
There are acrylic paints, and then there are acrylic paints. "Acrylics" as we know them in model building started out, chemically, as "rubber-based" or latex paints in the 1950's, first marketed as house paints, for interior use, and finally as exterior paints. Very quickly, companies such as Grumbacher and others in the artist's paint industry began working with the basic formula's to create artists colors that could be used without linseed oil and turpentine (artist's oil paints). Artist's acrylics are very thick in texture however, allowing the painter to work with them in ways quite like working in oils. Polly "S" Corporation came on the hobby scene about 1966 or 1967, with a line of model railroad colors, followed in a couple of years by their line of military colors, all using that same "latex" formula as the artist's acrylics, or for that matter, even latex house paints, but with thinner consistency, and MUCH more finely ground pigments. "Latex" based acrylic paints are almost always flat finish, even the so-called gloss latex paints are at best only semi-gloss. With the explosion of interest in "crafts" that began in the early 1970's, several lines of flat finish acrylic paints come on the market, to feed the craze for what was called "folk art" (painting wooden objects to "represent" Pennsylvania Dutch artwork and household pieces. Brands of acrylic latex flat finish paints such as Delta Ceramcoat, Folk-Art, and Apple Barrel were in craft shops all over the place--along with brushes designed for the various painting techniques used in this art form. I believe it was the Japanese model companies who first came up with water-borne acrylic enamel for hobby use though. The first line of such paints aimed at modelers to see wide distribution in the US was Tamiya, but Gunze Sangyo and others followed quickly in the early 80's. Acrylic enamels use plastic polymers to create that glossy finish, much shinier than was ever (in my opinion anyway) than was ever possible with the older latex based water-born acrylics, such as Polly S. Both Pactra and Testors brought out their own lines of acrylic enamels in the early 1980's, and with RPM's buyout of first Testors, and then Pactra, the original Testors formula went away, replaced by their newly acquired Pactra formula--Pactra was much nicer, easier to use, and gave better finishes, certainly IMHO. As for the craft-store acrylics, these are still latex based, and considering what they are formulated for, are quite thick in consistency--but they can be thinned for working on model car parts--most notably interiors. Once thinned, they can be brushed with very little in the way of brush marks, and can be airbrushed beautifully, but when airbrushing, the plastic parts need to be "squeaky clean" as any surface contaminants, such as fingerprints (skin oils) will prevent them from sticking. A lot of builders, myself included, have been known to airbrush a coat of thinned lacquer primers on interior parts, before using flat finish craft-store acrylics, which gives great adhesion, and absolutely no "beading up" of the water-borne acrylic paints. Over on the military model side of things, pretty much water-born acrylics seem to rule, due to military modelers wanting absolutely flat finishes, and very thin coating as well. As for "name brand" VS craft store acrylics, both lines of paints are "name brands" within their respective markets, chemically identical in all respects--the differences being in the consistency required for craft work as opposed to scale model work. And, of course, the color varieties are vastly more with craft paints, given their focus on interior decor around the house, as opposed to scale-correct colors for model builders. But, for finding colors that at least approximate interior colors on say, cars of the 1950's--a great place to look for them is in the craft paint racks. Art
-
Help me get back to basics - tools...
Art Anderson replied to Brett Barrow's topic in Model Building Questions and Answers
Sprue "nippers" are a standard feature on my workbench! I second your recommendation about Tamiya's--have a pair of those, they get the call a lot. In addition, last time I was in Hobby Lobby, I picked up a pair of miniature jeweler's "side cutters", essentially the same kind of tool, but much smaller and finer. All side cutters have a flat side, which is the side to use against the part being removed from the sprue. Often with very small parts, however, it seems almost impossible to get the "nippers" into the space where the sprue attachment points are--that calls for a bit of "creativity". When confronted with that situation, I have learned to cut the section of sprue away from the parts tree, then attack those bits of sprue piecemeal until I can get the nippers into where they need to be to remove the remains of sprue from the part. It now works for me every time I do it. Art -
What to use to fill sink holes
Art Anderson replied to o-man's topic in Model Building Questions and Answers
I hit on using "gap filling" CA glue for filling sink marks years ago. I use it with Bob Smith Accelerator which sets the CA quickly, does not damage the styrene; and finish off with needle files and sandpaper. It may well take several applications to do this, but it works quickly, and never shrinks. Art -
Making A Small Sanding Block!
Art Anderson replied to goodguyinar416's topic in Tips, Tricks, and Tutorials
I've also done this using .250" square Evergreen styrene strip--with 400-grit paper glued to it, makes for even smaller sanding sticks. Art -
All the ones I mentioned in the long list have been reissued many times over the years, with the exception of the Monogram '30 Cabriolet, which hasn't seen the light of day since the mid-1970's, so it should have been listed alongside the AMT '28 Tudor Sedan). Art
-
I got intrigued by this version of the '37 Ford pickup when I found a small black & white picture of one in the section on '37 Ford trucks in the excellent Crestline book "Ford Trucks Since 1905" about 20 years ago or so. It got me to thinking: AMT added a platform stake body to their '34 pickup kit back in the 1970's (I built one for the box art for their 1976 reissue with that bed), but Ford didn't offer such a body for a pickup until 1937, even though the bed will fit any Ford light truck chassis 1933-40. However, when Ford did introduce it as a production line option in '37, it came equipped with modified pickup rear fenders (in 1937 only), which made for a very classy looking little stake truck. When Revell introduced the '37 Ford pickup kit in the 1990's, I did master one and cast it in resin, all based on that very small black & white picture. Fast forward to August 2012: Vintage Truck magazine had a very nice color photograph of a restored one, with an excellent feature article inside on this rather rare little truck. I was hooked. First up was to scale out everything, based on the Revell kit, and the truck in that article. The process of interpolation gave me what I believe are correct dimensions for the platform bed, which is built using Evergreen styrene strip stock to build the steel parts of the bed floor, and 1/16" basswood for the oak planks. Skid strips are something I have made before, using .015" X .100" strip styrene, and homemade .020" half round styrene strips (I have a brass tool I use to lay .020" round styrene stock in, and scrape that down to half-round with an Xacto knife--works very well). The stake pockets surrounding the bed in the "steel" framing were done by laminating bits of Evergreen to create them. Here's the bed floor: The stake fences required not only some precision, but also absolute uniformity, so that they are interchangeable side to side, front to rear, and have to match the stake pockets exactly in order to be easily installed and removeable. I built a simple jig on a sheet of thick Evergreen styrene (for stability), with strip stock to make the guides to hold the stakes and the fence "boards": Here's thei tool, with a couple of fences in their respective jigs (the empty jig at the top was the first attempt, it came out very wrong!): These beds were mounted to the pickup truck chassis on very large oak planks set on edge, cut to match the shape of the tops of the frame rails (bear in mind, Ford, just like almost every other carmaker of the era, used passenger car chassis for their early pickup trucks). That made for some carving, starting with 1/8" X 3/4" basswood strip--this took two attempts to get them right!). Here's the bed, test fitted to the frame, with cab and front fenders included. Some adjustment will be needed, as I was guessing at the final height of the wood beams, they are a bit too tall. The tops of the pickup truck rear fenders were "notched out" in production to clear the side rails of the bed floor: Art Addendum! In checking reference pics, and doing some measurements based on those--the wooden support beams for the stake platform are surprisingly the correct height! There is, however, a bit of incorrect dimension to the pickup rear fenders as Revell molded them: They are approximately 2 scale inches too low at the front, and on the real trucks, the fenders were mounted with a bit of upward "angle" toward the rear, making the rear bottom edge of the fenders a good 3" higher than the line of the running boards and lower edge of the front fender--adding .080" to the front edges of the fenders, then angling them upward toward the rear will make them correct. In addition, Revell molded the rear fenders far too narrow, which was probably done for parts fit, seeing as the pickup box is a bit too wide as well, and the running board unit having its valance panels spaced out too far from the frame rails. On the real trucks, that valance panel (splash apron if you will) is of course, 20'gauge mild steel sheet, and is fixed very close to the frame rails. Of course, on this truck, the splash aprons don't extend past the rear corners of the cab, which makes for a serious gap between the kit fenders and the frame and wood beams--they will need to be split down the middle, and widened out approximately .100", which will give them a very correct cross-section as well. Art
-
Stripping weathered tires?
Art Anderson replied to Stuntman Mike's topic in Model Building Questions and Answers
IF Castrol Purple Power is sold in Germany, where Kevin is posting from. Art -
Model A Ford kits in 1/25 scale kits include: 1928 Roadster Pickup (MPC, later AMT) 1929 Roadster (AMT) 1929 Station Wagon (MPC, later AMT) 1929 Roadster/Closed Cab Pickup (Revell) 1930 Coupe (Monogram) 1930 Cabriolet (Monogram) 1930 Standard Phaeton (Monogram) 1931 Station Wagon (Revell) 1931 Tudor Sedan (Revell) (AMT molded and marketed a 1928 Tudor in 1/25 scale in 1964, model was developed very early in MPC's history) (Monogram produced a 1930 Station Wagon as a street rod only kit, but it can be combined with any of their factory stock Model A kits to make the woodie stock. Monogram also did a very rare variant of the 1930 Station Wagon, the 1930 Deluxe Delivery, which was the station wagon body with plywood panels where the windows behind the driver's seat would have been. It too can be combined with their stock '30 Model A kits to make a factory stock model). Art
-
Trans Am dashboard Question
Art Anderson replied to CrazyGirl's topic in Model Building Questions and Answers
I think you are referring to what is called "engine-turning". "Engine Turning" is a simple process, whereby a round tool is spun against metal with an abrasive compound of some sort. This creates a "swirl" on the surface of the metal. On flat metal surfaces, such as sheet aluminum, this is generally done in a drill press, with some sort of guide to allow the work to be moved both side to side, and forward to back, in precise increments so as to create a regular pattern. Generally, the setup is such that it allows each succeeding "swirl" to slightly overlap the previous ones, which creates the look. I've done this once before, back in 1985, when I built a 1/25 scale USAC Championship dirt car, Offenhauser powered. I made the firewall and instrument panel out of the thinnest K&S sheet aluminum available, creating a guide on the table of a Dremel Drill Press for moving the metal in a straight line side-to-side. Given the limitations of that drill press, I had to re-set that guide by eye for each row of swirls, but with some practice, I was able to make engine-turned sheet stock that was pretty precise, looked like the real thing. For the tip I fitted into the Dremel Moto-Tool, I used a "pencil-style" typewriter eraser (dunno of those are even available anymore though!), as typing erasers are rubber impregnated with a very fine abrasive. That sort of typing eraser was made like a pencil, with a cylindrical rubber eraser instead of a rod of graphite. I sharpened it carefully in an ordinary pencil sharpener, and then hardened up the rubber part with some thin CA glue. After that, I simply sliced off the end to get the diameter I wanted those swirls to be. Even though the rubber typing eraser material had fine grit embedded into it, it tended to clog up quickly, but I found that using a medium-grade automotive rubbing compound worked very well, just had to stop periodically, wash off that tip with some enamel thinner, and put more rubbing compound on it. To make a section of pencil-style typing eraser mount in my Dremel, I cut off a section of the wooden/rubber eraser, drilled it out by hand to accept a short length of 1/16" music wire (spring steel), and after a couple of attempts, got one to fit rather precisely. That I secured into the hole with some 5-min epoxy--crude but it worked! I don't know that this method would work with BMF though, as Bare Metal Foil is quite delicate--however something similar could work if done by hand, not using any power tool to spin the tool. Art -
Cobra Daytona Coupe in plastic.
Art Anderson replied to Steve D.'s topic in General Automotive Talk (Trucks and Cars)
I'll see it when I believe it. Art -
Doesn't it all depend on the type/era/venue of the race car in question? Let's take a look: In the early days of motorsport, cars were painted by brushing, not spray-painting (spray-painting didn't really begin until the advent of sprayable lacquers in the early 1920's (thanks DuPont!) and the development of spray guns. The same with plated parts on race cars (Nickel plating was around before 1900, but chromium plating didn't come into being until the late 1920's (Oldsmobile was the first production car to feature chrome plated bumpers and trim, in 1929). Of course, the major league of American racing, AAA's Contest Board-sanctioned "Championship Racing" reached a zenith of sorts in the 1920's, with highly tuned, and highly finished Miller race cars (Harry Miller's 122 and 91 cubic inch straight 8 DOHC powered race cars were built and finished like fine jewelry), with their Duesenberg competitors less highly finished. This all came to very much a screeching halt in 1930, due as much to the onset of the Great Depression as anything else. However, by the late 1930's, AAA Championship cars, especially as they appeared at Indianapolis each May, tended to be very highly finished, at least those campaigned by major race teams. Of course, many lesser cars weren't all that well presented, due to the limitations of available money, but they tried for sure. Grand Prix cars of the 20's and 30's also tended to not be as highly finished, with of course, a few exceptions, as most were privateer entries as opposed to factory teams; but even factory team cars weren't often showpieces (the early Auto Union rear engine cars were covered largely in aircraft linen, doped in the same manner as fabric covered aircraft, which resulted in rather dull silver finishes. Some Mercedes cars showed up in unpainted aluminum a few times as well. Fast-forward to the postwar racing scene, which brought some real showmanship to racing in the US: Midgets were often very highly finished, at least at the start of the season, with the chips, dents and dings of dirt track racing taking their toll over months of racing 3-4 times a week. Indianapolis cars (Championship Division of AAA and later USAC) generally were very highly finished, with incredibly shiny and showy paintwork at least at the start of the Month of May at Indianapolis, and often those cars that qualified for the 500 got repainted and re-trimmed (sponsor graphics) during the week between the last day of Qualifications and the start of the 500 on Memorial Day--after all, Indianapolis was (and still is) perhaps the biggest media event in motorsports, and car owners and sponsors wanted (and still want) their cars to stand out, appearance-wise. Of course, most of those paint jobs tended to wear badly during the 500, and more often than not a Champ car would run the entire season without repainting unless damaged in a crash. A very good example of what a USAC Championship car in the Offy roadster era looked like by the Bobby Ball Memorial 150 at Phoenix AZ (for a long time the last race of the USAC Championship Season in October) is the 1964 Sheraton-Thompson Watson-copy Offenhauser roadster driven by AJ Foyt to Victory Lane at Indy, and the USAC National Championship that year--it started out in May with an absolutely gorgeous Dean Jeffries pearlescent white paintjob, that rivaled any show car that Jeffries painted for the custom and rod show circuit that year--and it had candy red and candy blue accents, the blue scallops even faded by Jeffries light-to-dark for accent. All the sponsor graphics were hand-painted by a professional sign-painter, the Sheraton-Thompson (co-sponsors were the presidents of Sheraton Hotels and Thompson Industries (forerunner of Thompson-Ramo-Wooldrige, now TRW) logo's were in gold leaf, edged with shiny sign-writers' paint. Only the accessory, or "secondary sponsor) logo's were decals, even a couple were glossy paper stickers. That car, as it has stood in the Indianapolis Motor Speedway Museum since 1965, is as it finished the 1964 season though, worn, the candy red nose somewhat faded, with all manner of chips and dings on the forward portion of the nose and the external oil tank on the left side, (added for the 200 mile race at Milwaukee the Sunday after the 500 that year. The forward portion of the chrome-plated exhaust header has numerous small dings in it from track debris kicked up by the left front tire, as well as from cars Foyt came up on and passed on his run for the season championship. But, I saw that car on race day morning--it was a brilliantly finished show car that ran fast. The same was true with other race teams as well: There were cars in the starting field at Indy in those last years of roadster dominance with metalflake and candy paint jobs, done by some of the biggest names in custom car painting (consider that many of them were owned and maintained by California-based racing teams back then). Wasn't it very much the same with the top level of drag racing also? I tend to think so. When Can-Am rose up to prominence, with major sponsor and car owner money flowing into the top race teams, Can Am cars tended to be very well finished. Now, SCCA cars in general, and even Formula 1 cars before sponsorship graphics graced their bodywork, often tended to be somewhat drab, not necessarily highly finished (I've seen more than a few rather crudely finished Team Lotus cars back in the day). With graphics, be they decorative or sponsor-oriented, bear in mind that very few sponsor logo's were decals, and of course, computer designed, laser cut graphics didn't come along until what, the early 1980's or so? So the era of car should be considered as well--there's a great deal of difference between laser-cut mylar and vinyl and masked/sprayed graphics, even hand-painted logo's done by professional sign painters. Likewise, no matter the type of racing or the venues involved, there will be a great difference generally, between what a car looked like at the start of the season, or even a major racing event, than at the end of such a major race, certainly at the end of a long season--particularly true with short-track racing (certainly on dirt!) and also depending on the bank account of the car owner. However, clear-coating a model race car for that "show-car" look almost always makes it look less realistic--clear coats greatly thicken the paint finish, and while shiny, clearing the model does tend to give a car a one-piece shine all over, where there would have been differences in sheen on the actual car, going from rubbed and polished lacquer to hand-lettered team and sponsor names done with the likes of One Shot signwriter enamels. Certainly accessory decals or stickers stand out on the surface, not buried under clear coats. Art