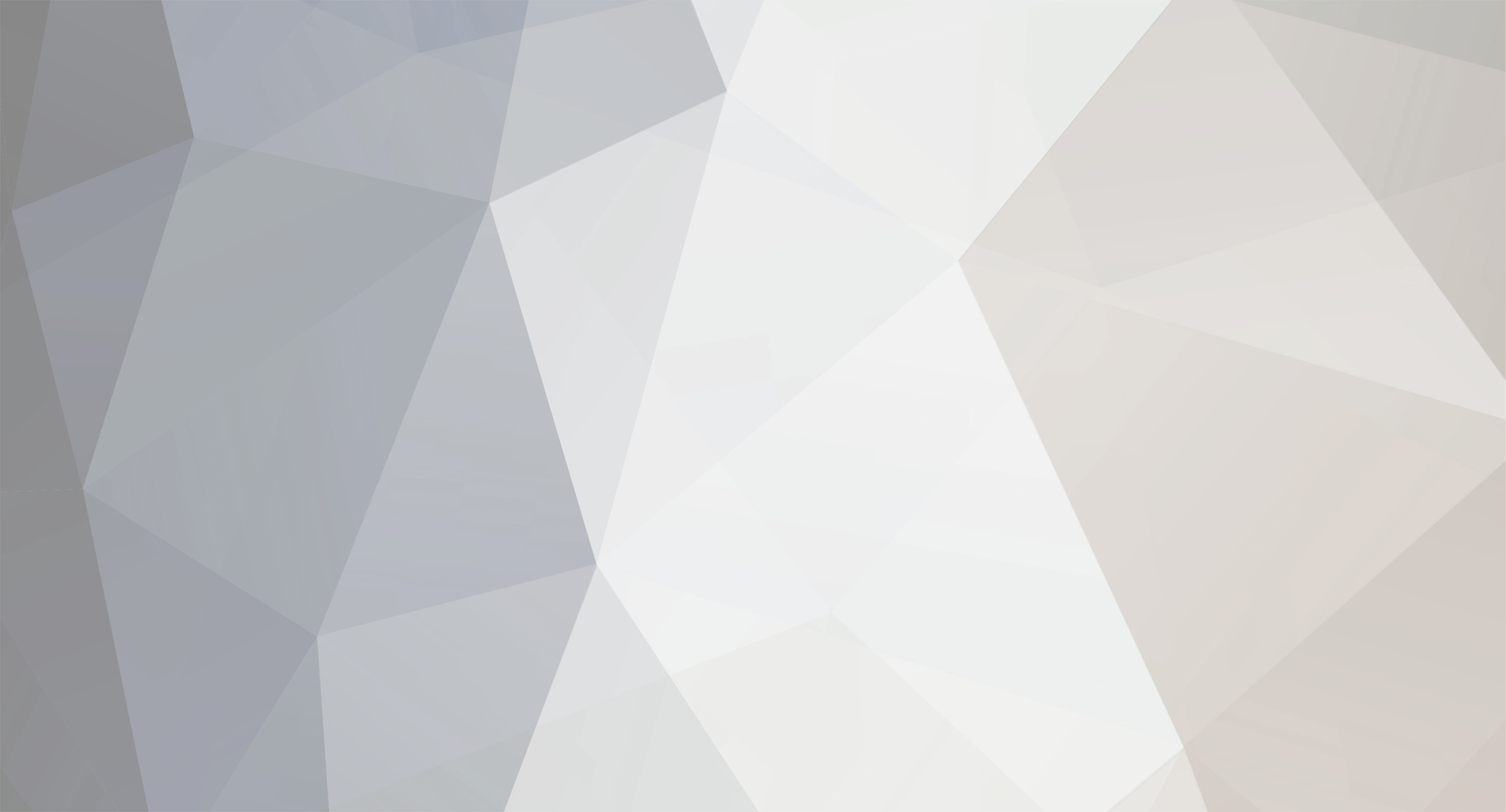
Art Anderson
Members-
Posts
5,052 -
Joined
-
Last visited
Content Type
Profiles
Forums
Events
Gallery
Everything posted by Art Anderson
-
Resin casting parts - legal?
Art Anderson replied to Jantrix's topic in Model Building Questions and Answers
What Tom said. The auto industry does seem, at times, to be uneven in their protection of such things as design, trademarks, trade dress and the like, but not as lax as some might believe. GM, for example, can be extremely anal in regard to certain makes of cars--some they consider more "iconic" than others, and they have been known to be extremely restrictive in regard to those. Others not so much. But of course, such depends on how "visible" the scale model or toy product might be. Some automakers follow the model car scene with internal staff, others use "licensing agencies" who work on commission. In the US, however, copyright and trademark owners do work under a principle of "protect it or lose it" in that in order to protect their copyrighted designs, their trademarks, they are at least "under the gun" so-to-speak in this: If say, Automaker A is to successfully protect the styling of a car from copiers, then that also means protecting those designs from aftermarket parts suppliers from all over, as well as toy and hobby companies wanting to produce miniature toys or model kits of those cars. This was strongly reaffirmed by the Supreme Court of the United States almost 30 years ago, in regard to replacement parts, from the likes of piston rings & other engine parts, AND crash parts being made in countries such as Taiwan, they being labled and packaged in cartons clearly marked with pirated names and even Company A's own trademark logo's. The Court ruled in favor of Automaker A, with a big stipulation: They were obligated to also protect those same items which were at issue even if the parts in question were done in miniature as either toys, hobby products, even the likes of logo's on caps, tee-shirts and the like. I work at a major, leading US University, albeit not in the academic side of things, but rather as part of the service staff. However, each year, near the start of the fall semester, I (along with every other University employee) receive a pamphlet outlining our rights and responsibilities under US copyright law. Basically, US law generally allows for "fair use", that meaning that one can reproduce a copyrighted item for one's own exclusive use (I can scratchbuild a model or parts of a model to look exactly like the real thing, but in miniature, just for me, with no fear of reprisal), but from there on, it gets more restrictive, to the point that I cannot reproduce say, an entire book for the purpose of selling my own copies, without the express written permission of the copyright owner. This applies as much to say, a model of a real car, as virtually all styling and/or design work done by industry gets copyrighted, even if a patent also exists on those items. Even a model company has some copyrights as well--not so much the styling of a particular car, but certainly the design of the parts, how they go together, that sort of thing. However, in resin-casting, seldom is a particular model car part able to be reproduced exactly, due to the limitations of both the resin material and the type of molds used to make those parts. And in any event, model companies seem to be generally rather happy to see aftermarket parts produced that enhance their kit offerings. That said, however, I see it as a very gray area if an aftermarket person decides to simply copy say, a wheel, an engine or whatever, from a newly released model kit, with the implied purpose being to simply make it possible for a modeler to buy those parts without having to spring for the entire kit. To at least some extent, it seems to me to do such is working at cross-purposes with the model companies who invest big $$$ to produce kits that feed our "addiction". A few resin casters today can trace their roots back to a time, some 20-30 years ago, when there were seemingly innumerable model car kits that had once been produced, but hadn't seen a reissue in so long as to lead modelers to believe that they would never again be rerun. As such, some of those casters began their businesses by reproducing often lost or broken parts which could be used to restore old model kits and promotional models. That eventually grew into reproductions of entire kits--but the "bloom" fell off those flowers once model companies realized that there might be money to be made in rehabilitating old tooling and molding out newly reissued kits of once long-dead model subjects--resulting in those early resin casters either going out of business, or evolving into molding models of cars never before done in plastic scale model kits--and that is what drives the resin cast aftermarket "industry" today. But, in general, the model car aftermarket is full of producers so small as to be correctly termed "cottage industries", and thus do fly well below the "radar screen", and as such just don't get much scrutiny from say, Detroit, Stuttgart, Wolfsburg, or even Marinello. Art -
This is an area where actually "fudging" on scale accuracy is almost a must, given that 1/25 scale is rather small to begin with. For those who are metrically challenged, 1/25 scale is .040" to the inch. So, for example, if a push or pull rod for carburetor linkage in real (1:1) life is 1/4 inch diameter (.25") then in 1/25 scale that comes out to just .010", which is about double the thickness of a sheet of high quality paper stock--awfully small. But, if one uses say, .015" or even .020" for such linkage rods, the size is still small enough so as to be believable, and it will still add scale realism to the project. In the model railroad hobby, there are suppliers offering fine brass rod stock in such small sizes. Check http://www.walthers.com/ for brass wire--their stock STARTS at .006" (six thousandths of an inch), really small. Art
-
Anne, While not cheap, Scale Hardware offers a neat line of miniature rivet, nut, bolt and even working bolts and nuts in metal in some unbelievable small sizes. These are machined in brass, some come plated as well. http://www.scalehardware.com/ I've used some of them, and believe me, they do add scale realism. Art
-
Airbrush- Which one for a beginner?
Art Anderson replied to DailyGrindCustoms's topic in Model Building Questions and Answers
A lot depends on your expectations, frankly; as well as what you perceive your capacity for patience in learning is For a bulletproof (as nearly bulletproof tough as it can be) airbrush for a beginner, it's hard to top the Paasche H series. This is an "external mix" style airbrush, where compressed air and the paint meet outside the body of the unit, but inside a venturi chamber which serves to create the bit of vacuum needed to draw paint up out of the color jar The H is pretty much the standard for quality and precision in this type of airbrush, which is great for doing really good but simple paintwork. The better Paasche H setup comes with three different material control units, finel (#1) medium (#3) and coarse (#5) which are easily changed out, and in the bargain, the unit's simplicity makes cleanup between colors and after you are finished painting as easy as 1-2-3. By contrast, the Badger 200 is an internal mix unit, which utilizes a long, thin needle fixed inside the body of the airbrush, extending through a tapered nozzle, which regulates the flow of paint and air which come together inside the body of the airbrush. It is a very precise instrument, and capable of not only body finishes that are first rate, but also can be stopped down to make it possible to replicate the delicate fading of colors one to the enxt for custom paintjobs, certainly painted flames. But those features/advantages do come at a higher price, both in dollars and in learning how to use it There is a slight disadvantage to the Badger 200, in that it is a far more delicate instrument, and thus requires a lot more care in handling and cleanup (one slip, drop the thing on it's nose, and you will be replacing that needle for sure). Both of these airbrushes are "single action" meaning that the control button or "trigger" on the airbrush controls air flow only. In contrastl, a dual action airbrush button can control BOTH the flow of air, and the flow of paint, by pushing down on the button for air, and rocking that button backward or foward to increase or decrease the flow of paint. And therein lies a big difference in how quickly most people master one or the other. The Paasche H is almost "plug and play", while there will be at least some learning curve with the Bager 200. In a nutshell, it will be your decision, I've simply laid out the differences, advantages and disadvantages of each one as I see them. Art -
As for swap meets and model car shows vis-a-vis eBay--well, at a show, the "dealer" is gonna ask the price he wants, and the buyer may haggle--perhaps they come to a price, perhaps not (pretty much the way the guys on Pawn Stars do it too), where if at auction on eBay, it is an auction, subject to bidding by whomever, however many bidders take a swing at it. So, the price at one venue versus eBay can vary a lot, in both directions at times. Art
-
Call me old-fashioned if you will, but I still want to have a local hobby shop that will be there to cater to my car modeling wants when I stop in. Having said that, the LHS has to earn that position from me, and currently, the one true hobby shop here in town hasn't--so, I bundle my wants together for a periodic trip to Indianapolis, where I can practice that same philosophy. But, why you ask, do I shop at local hobby shops? Plain and simple: I want the guy to be there when I want something, and don't want to wait for merchandise to be shipped to me. A LHS is not going to survive on just the occasional bit of glue, some Xacto blades on occasion, or the sale of a couple of bottles or spray cans of paint--that's a fact of life (spent too many years in retail hobby merchandising to believe otherwise). As for kit prices, well those tend to reflect inflation and pretty much always have, save for about 15-20 years when kit prices were dictated by the larger "Big Box" mass retailers. That situation, more than anything else, is what drove plastic model kit production out of the US--the costs of doing that production in the US ultimately made off-shoring a necessity (when a major retailer is willing to buy up half of your production of any item, AT their price--you surely can see where that leads!). Of course, that situation (off-shoring) may very well be ending, due to serious inflation in the Far East due to fast rising wages and other costs associated with industrial production, but for the time being we have to live with the situation as it exists. For whatever "savings" result from using lower cost (both by living standards and by currency exchange rates) labor overseas are now being eaten up by higher feedstock costs (styrene plastic is made from petroleum), shipping (it costs frightful money to sail one of those 100,000 ton container ships across almost 8000 miles of ocean. Then there is the cost of offloading that ship in port--and the Longshoreman's Union doesn't work inexpensively. Neither do the railroads nor trucking companies. Additionally, hobby shops don't often buy their model kits and supplies directly from the manufacturers due to the very large quantities they would have to commit to in that case--so they (and the manufacturers) use wholesalers to service small independent retailers for perhaps 90% of all the hobby merchandise the LHS stocks--and that of course comes at a price as well. A lot gets said about "inflation", but the acknowledged rate of inflation as reported by government and the media is but an average--some things may stay very stable in price (actual number of dollar bills) while others accelerate rapidly, while some items may only go up by smaller amounts. Even with that being said, domestic brands of model car kits haven't, except in a few "spikes" gone up that dramatically compared to 50 years ago, although the market for any individual model car kit is a fair bit smaller than it might have been in 1963--but that's at least in part due to there being vastly more different model car kits available today than a half-century ago. Thus, to amortize (put money spent on new tooling back into the company's bank account) takes longer now than it did in 1963, and that doesn't take into account that there are fewer car model builders today than at the height of the baby boom generation reaching an age where they got interested in model cars and building them. Additionally, a new, "21st Century State Of The Art" model car kit is in many ways light-years ahead of where common model car kits were just 30-35 years ago, let alone the comparision to kits produced in the 1960's. All of this should help explain the costs, and why the prices. Now, most online retailers can only "discount" a kit so much, and when they add in the cost of shipping, pretty much on a newly produced model kit, the total cost to the phone/mail/online customer will be pretty close to what he might expect to pay in a "briick and mortar" store. Of course, there are advantages to buying multiple kits, for if the online seller is really on top of it, he can lump several kits together in a shipping box, and pay less per kit for shipping than if each kit were sent separately. Most online sellers probably do this, probably some do not. With reissues of kits from older, existing tooling, sure the tooling may have been amortized years ago, but there will still be upfront costs to effect a reissue while making it a salable product (rehabilitating the tooling as needed, perhaps adding a few new parts, possibly creating a new decal sheet or instruction sheets, and certainly new box art--even making retro-copies of old box art isn't exactly cheap). BUT, almost without exception, the sales of a reissued model kit will be but a fraction of that for a brand new release, so the requisite costs will be spread over a much smaller volume of production and sales--generally, that rather balances out pretty closely. Lastly, it's the sale of existing model subjects and the reissuing of older kits that provide the upfront money for new tooling, and that is a situation that has never changed. Unlike many other industries, the hobby and toy industry isn't going to be able to establish vast lines of credit in order to finance new product--the risks are much greater there than say in the 1:1 auto industry. Hopefully, this helps background the discussion at least a little bit. Art
-
Did Hubley make promos ?
Art Anderson replied to Ace-Garageguy's topic in General Automotive Talk (Trucks and Cars)
Yes, Hubley made promo's. They did 1960, 1961 and 1962 Ford station wagons and 4dr sedans. In addition, they also produced their Renault Dauphine and AMC Metropolitan in promo-style toys. Art -
40 Ford p/u drivetrain question
Art Anderson replied to mnwildpunk's topic in Model Building Questions and Answers
Actually, the '61-'63 Pontiac Tempest setup is NOT a torque tube arrangement! The first series Tempest used the same transaxle and rear suspension setup as the 1961-63 Corvair, swing axle independent suspension. The square, tubular unit supported a flexible driveshaft. Notice that this "tube" actually curves down and then back up at the rear. That was a system to reduce the driveshaft "hump" in the floor in the rear seat area. The driveshaft was supported by a series of bearings to hold it in a bend while rotating. There may be some misunderstanding as to just what a torque tube does: It's purpose is to "locate" the rear axle housing and secure it from trying to "react" to the torque in the rear axle shafts themselves--very much like traction bars installed on muscle cars. On Fords from 1905 through 1948, the transverse rear spring could not resist the axle housing from rotating, so the torque tube was absolutely essential (Ford front axles in that era used a "wishbone" radius rod setup that not only kept the front axle firmly located at 90-degrees to the center line of the frame, but also served to keep the front axle from twisting the transverse front spring upon braking. Many cars equipped with parallel leaf springs also used torque tubes to keep the rear axle from trying to "wrap up" the rear leaf springs, or in the case of the late 30's Oldsmobiles (which were among the very first cars equipped with coil springs in the rear) to keep the rear axle housing from trying to wrap those around the axle under acceleration and braking. Oldsmobile and the rest of the GM lineup went to traling arms for that purpose when GM Divisions abandoned torque tubes and used coil springs in the rear. Those trailing arms also functioned as radius rods when used with rear coil springs (think 1958-64 Chevrolet and Cadillac in this regard, along with 1960-66 Chevy/GMC pickup trucks. Fords equipped with transverse springs and torque tube drive used radius rods to firmly tie the rear axle and torque tube precisely, while cars using parallel leaf springs and "Hotchkiss" drive (Hotchkiss was the name of the French engineer who first came up with the open driveshaft with U-joints at each end) could rely on the parallel leaf springs to function as radius rods. Art -
40 Ford p/u drivetrain question
Art Anderson replied to mnwildpunk's topic in Model Building Questions and Answers
Torque tube. Art -
Reference Photos 41 Chevy Engine
Art Anderson replied to hooterville75's topic in Model Building Questions and Answers
Unfortunately, that is not a '41 Chevy six--rather it is the 1953-62 235cid Blue Flame 6. The Chevrolet 216 "Stovebolt" 6 was visually the same from 1937-53 (that year saw the introduction of the 235 Blue Flame 6, which first appeared in Corvettes, then across the line as the standard, basic inline 6 through 1962's full size Chevrolet's). The 216 cid engine appears in model form in the following 1/25 scale kits: AMT 1937 Chevrolet Coupe and Cabriolet, Galaxie Ltd. 1948 Chevrolet Aerosedan and Sedan Delivery, and in the AMT 1951 Chevrolet Bel Air Hardtop & Convertible, and that year's Fleetline fastback 2dr sedan. Art -
More than likely red oxide primer, with body color overspray at the outer edges, with body color on the firewall and inner fender areas, as those are part of the unit body construction on AMC's. Body all over the underside of car bodies really didn't get started until the advent of robotic spray painting in the middle 1980's or so. Art
-
Sanding films question
Art Anderson replied to mnwildpunk's topic in Model Building Questions and Answers
Any Micro Mesh polishing kit (they package those for any number of suppliers, have been for about 25 years now!) will have the polishing cloths you are looking for. Try hobby shops, and if not there, Micro-Mark Tools (they do business online). Art -
Can't cut BMF nice and even?
Art Anderson replied to Johnt671's topic in Model Building Questions and Answers
Practice holding your #11 Xacto blade at a very shallow angle to the surface of the body shell. That will let the blade follow the edge of the chrome spears. It does take some practice, and a bit of patience, but it does work (been foiling model cars for a good 40 years now. Art -
Correct for Bonneville?
Art Anderson replied to Austin T's topic in Model Building Questions and Answers
OK, keep in mind the dimensions of the Kurtis Midget. They had a standard, mandated wheelbase (set first by AAA's --American Automobile Association--Contest Board, way back when AAA Contest Board was the principal sanctioning body for American closed course auto racing; and pretty much maintained out to today) of 72" (6 feet). In addition the tread base (distance between the centerline of the tires) was also specified. Revell's Midget trailer is modeled from one built to carry a car such as that. Also, an AAA/USAC MIdget is a fairly light race car, weighing in at perhaps 700lbs dry, where say, a stripped out Model A Ford roadster with a 4-cyl can weigh at least twice that. Also, the Hawk streamliners, nice that they are, are a good bit larger than the Midget, both wider and longer. Just some thoughts. Art -
Every pin vise I've ever had, and the ones I use today, have one collet (chuck if you will) that will close down to "infinity" (completely closed), which will work with any of the smallest drill bits you will ever use. While the drill sets sold by Xacto, Micro-Mark etc. are great, particularly for their drill index storage cases, individual drill bits from them are expensive. A few years back, when doing some pretty serious model car machining (yeah, I have a lathe and vertical mill here), I went looking online, and settled on http://www.discount-tools.com/CATALOG.htm which is an online tool jobber, who will sell to us ordinary mortals, as well as to industry. They sell those same numbered twist drills that come in the hobby oriented drill sets, in packs of a dozen of any one size, for very reasonable prices (around $3 per dozen). They sell online, and their delivery is prompt (small packages such as those are shipped via USPS). Given that those very small high-speed steel (HSS) drill bits are fragile (they break very easily), this makes it very easy to keep a stock of your favorite sizes handy. (very satisfied Discount Tools Company customer here!). Art
-
OK, this is actually a rather easy question to answer: If you've ever seen tarnished brass (old brass musical instruments will show tarnish were the lacquer clear coat has been worn off, for example, or perhaps an older brass table lamp), it "tarnishes" due to exposure to air. Tarnish is different than corrosion, in that brass, being an alloy of copper and zinc, can corrode upon contact with chemicals, even water, which is a bluish-green color (Turquoise, the semi-precious gem stone, is actually the result of corroded copper in nature). Early, so-called "brass era" automobiles used polish brass trim and radiators simply because the technology of really good electroplating hadn't yet been developed, although nickel was used on occasion. However, nickel doesn't stay bright on its own very well at all--goes dull on exposure to air, and being a fairly soft metal, nickel wears off rather quickly with frequent polishing. Chromium wasn't used for plating on automobile trim until introduced by Oldsmobile in 1927, once chemists figured out how to plate it onto steel. Now, how to "tarnish" model car "brass" trim, such as your Model T kit: Unfortunately, this is a job that calls for at least a basic airbrush, as in my experience, it's best done with a thin "wash" made from Testors "Rubber" (#1183TT) which is a flat brown-black color, in the little square bottles. I put a small amount of this in an airbrush color jar, then add enough lacquer thinner to make a thin wash. The lacquer thinner thins the paint to about the consistency of ink, which means too thin to apply by paintbrush. However, when airbrushed lightly on those "gold-toned" plated model car parts (your brass trim), it gives that brownish cast that looks very much like tarnished brass, along with a very dull, flat finish. With a bit of practice on the sprues, you can vary this shading to get the degree of tarnish you like, and unless you go overboard with it, the bright plating will still show through, albeit toned, or dulled down greatly. If you, or anyone has ever seen the second issue of the old AMT 1907 Thomas Flyer "New York to Paris Race" winning car, with photographs of the built model on the box art, I am the person who built that model for Lesney-AMT back in 1979. The brass trim on that model is tarnished as I described, and it did come out surprisingly realistic. Art
-
The steam powered LSR car was the "Oldsmobile Rocket". Art
-
What is the skinny on model molding?
Art Anderson replied to mnwildpunk's topic in General Automotive Talk (Trucks and Cars)
Bill, in more cases than one might imagine, the reissue of an older tool which didn't do particularly well when first released has, upon latter day reissues,generated some very nice sales. Two such kits that come to mind are the AMT '53 Studebaker Commander, and the Studebaker Avanti. I was doing the plastic model kit buying for a very large(for the times) hobby shop here when both of those kits hit the shelves. Both sold only so-so in the 1960's (I was told that by a now-deceased exec at AMT Corporation in the late 70's), and did poorly in their 1970's reissues--enough so that he questioned whether either one would ever be produced again. Of course, both kits came out at the point in time where Studebaker was very much like an old horse, wandering around, looking for a comfortable place to lay down and die. That didn't help things back when it was kids from perhaps 10 or 11 to perhaps 16 or so who were the primary market for model car kits. They were much more enamored with anything Bowtie, certainly GTO's, Mustangs, Corvettes and the like then. Strange as it may seem, even Mopar subjects tended to gather a bit of dust on store shelves, compared to their Ford and GM competition, and AMC's--fuggedaboudit back in the 60's. Some of us were there, working at some level of the hobby industry, we saw it happen. Fast forward to today--both of these subjects likely have surpassed, finally, the numbers necessary to have paid back the tooling costs (I would bet that AMT wrote both sets of tooling off at a loss, for tax purposes years ago--but had the wisdom to pump some cosmoline into the tooling to preserve it). Reissues of older kits probably are not cash cows, given that production runs of older tooling as reissues almost never generate anywhere the number of sales as a highly anticipated, new-to-the-marketplace subject. But, I have been told that the costs to reissue an older kit are but a fraction of the upfront costs for a new model kit. More than likely at least a bit of tooling rehabilitation, and of course, the requisite setup costs incurred whenever a set of tools gets reloaded back into the injection molder. I would be fairly certain, for example, that such is part of the business plan at Round2, and likewise, to a lesser percentage at Revell, even the European and Japanese brands. With that in mind, I have to wonder just what reissues will some of the companies with hundreds, if not thousands of old model kit tooling in their "libraries" spring on us these next few years. Art -
Why aren't all model kits awesome?
Art Anderson replied to Henchmen4Hire's topic in General Automotive Talk (Trucks and Cars)
Uh, if you recall, I made that comment in relation to shapes and contours. Art -
Why aren't all model kits awesome?
Art Anderson replied to Henchmen4Hire's topic in General Automotive Talk (Trucks and Cars)
Bill, I have wondered over the years, why such components as an engine assembly aren't tooled from the same mockup as a previous kit using the same engine. While of course, it may well not be possible to do that with every car subject using the same engine, given the kit layout engineering that may have to be different one kit to another, but in so many instances (pre-WWII V8 Fords come to mind here, that should not be a problem. But in any event, it's sad (but not a terminable offense) when an engine (or any other major component) that is used in more than one real car cannot seem to be exactly the same when installed more than one model kit, especially when that is both an accurate installation. Art -
Oops, I did almost forget though! The other day, after work, I painted and foiled the steering wheel. Gloss black (which matches what original interior pics I can find) got the call, along with some tedious BMF work on the horn ring and hub. But, what to do about the decal for the center, the horn button? I decided to make a 1/8" hole punch, by whittling out the inside of the end of a piece of 1/8" brass tubing. Centering that on the decal (still on it's backing) a short, sharp tap with a small hammer and I had the medallion decal, which then got secured in the hub with a small drop of CA. Last came the clear, domed button which covers the medallion--so a small drop of Devcon 5-min epoxy got the call there. The pic shows it: Art
-
No pics at this time, but I just got done installing the kit tires on the '50 Olds--doesn't ANYONE make a set of 1/25 scale tire tools for mounting tires on this thing? Seriously, once assembled, this kit has perhaps the nicest wheel and tire units ever on a pre-1980 car--just the tires along have to be seen to be believed. Well, once I get the chassis and floor pan assembled, with the exhaust system sandwiched in where it goes, and the engine installed, there will be a pic or two. Art
-
Why aren't all model kits awesome?
Art Anderson replied to Henchmen4Hire's topic in General Automotive Talk (Trucks and Cars)
Casey, Some flaws in your otherwise excellent and quite correct message here: For starters, in the now-largely departed era of hand-carved tooling masters--before the digital revolution reached the design studio and tool shop, the camera was the researcher's principal tool. Add to that some very basic hardware store tools: Folding carpenter's rule, a pair of measuring tapes (steel tape where it can be used, and a non-stretching dressmaker's cloth tape measure for stretching across a painted surface (funny how owners of real cars don't want a steel tape on their thousands of dollars paint jobs!), a notebook and ball point pen for making notes about this-and-that. Even a common stepladder can be handy IF one has a vehicle with room to carry one! In almost innumerable ways, 3D scanning can take much of the work away from such "analog" methods, but still, anyone researching a real car for creating a miniature is wise to take hundreds upon hundreds of pictures from every angle imaginable (and with high-quality digital cameras, this has become less expensive than a cheap suit!). Why so many photographs you might ask? Well the answer is quite simple: Photo's that show the crown of a roof from all angles go a long way to confirming (or denying) the accuracy of what the digital 3D scanner might see, and can aid in making such small corrections of shape that make the miniature believable to the human eye (bear in mind that our eyes, given their "binocular" vision, with the visual field of each eye overlapping that of its neighbor can make an EXACTLY accurate shape in miniature appear not quite the same as the full-sized 1:1 scale original. As for such small details as a drip molding, that can be tooled exactly to scale, but it can also become so small as to make it simply disappear under even the thinnest coat of paint (one of my pet peeves has always been scripts and badges engraved so faintly in scale that they simply disappear, when only a slight adjustment in just the depth of those details will make them pop out in a decently done paintjob, even with a rattle can). Now, with measurements: Never a good idea to rely on equipment to give exact dimensions crack out of the box. Wherever possible, measuring tools need to be used, to establish firmly what correct height and width should be. A carpenter's rule (and I have a couple of them!) having every other inch blacked out, and laid across say, the '32 Ford firewall you mention, will give, instantly, in a photo,the width of that panel--and it's pretty easy to figure that down to a fraction of an inch just from the picture (bear in mind, at .040" to the inch in 1/25 scale (or 1mm to the inch--doesn't much matter) a scale quarter of an inch comes down to .010", which is pretty nearly the tolerance any modeler can achieve with a needle file or 400-grit sandpaper. That same, marked up carpenter's rule, or even a dressmaker's cloth measuring tape, similarly blacked out every other inch, can clearly show the placement of chrome trim, scripts, badges, even door handles and lock cylinders; in addition to confirming the height of say, the windshield, side windows, even the lengths of such. With engines and all the other greasy stuff, it gets more difficult: While of course, there should be little tolerance for major dimensional errors, simply finding say, a 392cid Hemi OUT of a car isn't always as easy as it may seem. It would be great if they were just sitting around, on engine stands, just waiting for a model company researcher to come around, measure and photograph it. Every once in a while, one does find an engine in such a situation: The 308 Twin H-Power engine that Moebius was able to reference IS on display at the Hostetler Hudson Museum in Shipshewanna IN, about 35 miles or so from Dave Metzner's front door (I have a full walkaround photo spread of that engine that I took on Labor Day Weekend in 2011, and it helped immeasurably when I bullt my two Hudsons (and will get the call once again, when I decide to superdetail one!). While I cannot vouch for what happens at Revell, the Moebius tooling mockups are done IN 1/25 scale, not in say, the old-fashioned manner of 1:10 scale which would require pantographing down to 1/25 scale injection molding dies. That alone removes a huge set of steps in the tooling process. In addition, they do have the appearance of having been carved out by CAM, with probably some small detailing added by skilled hands, but I won't speculate as to what or which. Enough of that. One thing I learned when doing major body conversions for resin casting was to ALWAYS evaluate shape and countour by studying the body shell during that work by holding it as nearly exactly the same angle as the car in a picture which I was comparing it to. Additionally, I also closed first one eye, then the other, so I could see the body shell in my hand as close to the manner in which the camera saw it--one-eyed, or monocular. Given the curvatures of any car body, that's the best and most accurate way of judging shapes of the model that I was ever able to come up with. Economics do necessarily come into play with the development of any product, be that a model car kit or anything else you can think of in our world. There are definite limits to the money that can be spent, at all stages of product development, and tooling costs are but one factor. Time constraints also do come into play, just as they do with the real car. Art -
Why aren't all model kits awesome?
Art Anderson replied to Henchmen4Hire's topic in General Automotive Talk (Trucks and Cars)
Tom, Interesting you said that! Way back in the 60's, the former Car Model Magazine visited MPC in Mt.Clemens MI--kinda one of those "show modelers just how a model kit comes about" articles. A very prominent picture in the article showed a 1927 Lincoln Roadster having been rolled in, through a garage door into what may well have been the warehouse/shipping & receiving area of their facility--and several people were studying the car, over-under-around-and-through, with measuring tapes and CAMERA's. Art