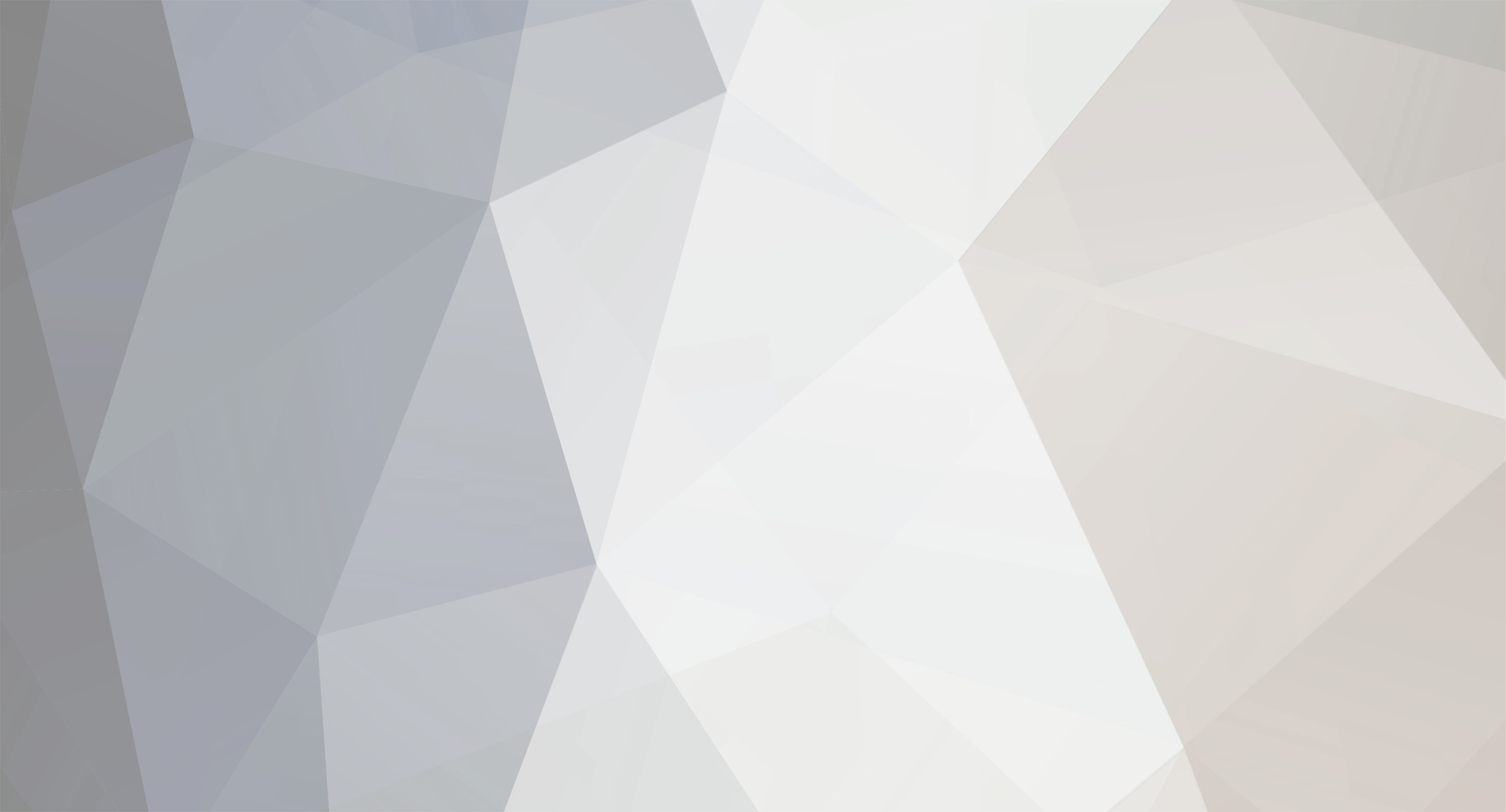
Art Anderson
Members-
Posts
5,052 -
Joined
-
Last visited
Content Type
Profiles
Forums
Events
Gallery
Everything posted by Art Anderson
-
'37 windshield replacement?
Art Anderson replied to Jantrix's topic in Model Building Questions and Answers
Rob, It all depends on the type and thickness of the clear plastic used. Have you looked at the clear acetate folders available in office supply stores? Art -
Bare Metal Foil
Art Anderson replied to Midget Whisperer's topic in Model Building Questions and Answers
I've used, for years now, a .5mm push-click mechanical pencil for burnishing BMF into tight details. The graphite lead is self-lubricating, so it slides over the foil with far less danger of snagging and tearing it. Art -
Of course, it should be wise to remember that the Ford pickup kit in question here is a 1/2 ton unit, and using as small a pickup as one of those as a wrecker would have meant sending a small boy to do the job of a full-grown man. In point of fact, a 32-34 Ford pickup itself weighs barely more than 2,000 lbs dry, less than the weight of a Deuce or '33-'34 Ford Model 40 passenger car. Nearly all pics I have seen of early 30's tow trucks are of rigs built either on 1.5 ton chassis, or even modified large luxury cars for that very reason. Art
-
As long as model companies exist, and as long as they reissue older kits, there will be this disconnect with those modelers too young to remember that years ago, that kit they just bought as a reissue, is a look back at model car kits as they once were. That is a conundrum, pure and simple. We older modelers love to see "an old friend" come back to the hobby shop shelves, but younger builders (not necessarily kids, but still 20 yrs or so younger than us sextegenerian modelers, see them as substandard--given that their experience never included those AMT/MPC/JoHan 3in1 annual series kits of now yesteryear. Art
-
No. R&D Unique was started by Dave VanDerwal in the early 1980's, concentrating on doing fine-quality white metal aftermarket model car parts of all kinds. His first foray into resin was a series of antique gas pumps that he himself mastered--then in the late 1980's, R&D Unique bought out Mini-Exotics who were located just over the border from Seattle in British Columbia. In the late 1990's, Dave VanDerwal sold R&D Unique to the man who was doing all the resin and white metal castings, Tony Willing. This sale included not only the business with all equipment, but also all mastering. Tony Willing continued the business until a divorce entered into the equation, at which time he closed it, until the divorce is settled. That is pretty much where it stands today. Art
-
condensation problems in air gun
Art Anderson replied to rustisacolour's topic in Model Building Questions and Answers
OK, a bit of a tutorial here: Air, when compressed, heats up, and when the pressure is let off, it cools down. With high humidity (and yes, in Indiana from spring until late fall, the air is humid a fair amount of water vapor in it) when air is cooled suddenly, the water vapor will condense on almost any surface, and that includes on the inside of an airbrush hose. This condensation then moves down the length of the hose, and will come out of the nozzle of any spray gun, from a body shop spray gun down to an airbrush. This is where a moisture (water) trap becomes necessary. In my experience, a moisture trap is best used in the middle of an air line (not right at the outlet from the compressor or air tank), as this gives some length of hose (or pipe, doesn't matter!) for the moisture to condense, the movement of the air down through the hose pushing the condensation to the moisture trap (and this is something most hobby shops don't know, but anyone knowledgeable will). I have used my moisture trap for 50 years now (a Binks unit I had to get for my Binks Wren airbrush (same concept as the Badger 350 and Passche H) and their compressor. The setup uses a 6' length of hose between the compressor (which is now a Badger 180-1) and the moisture trap, with the common 6' hose between the moisture trap and the airbrush. This setup dries the air supply completely (I NEVER get moisture spitting through my airbrushes!). Putting the moisture trap directly on the compressor outlet just doesn't quite do it, as the water vapor needs that length of hose to act as a condenser so that liquid water can be moved to the moisture trap. All based on now 50+ years of experience airbrushing. Art -
Yup! In 100 years, on December 12, 2112. Art
-
The quick answer is: No. AMT made the '64 Galaxie 500XL in three kit versions over the years. In 1964, they produced a full detail (as full detail as existed in 1964) of both the hardtop and the convertible. In the mid-1980's, as the first of AMT/Ertl's "Blueprinter" series of kits (marketed to subscribers to the Ertl Blueprinter magazine) was the '64 Galaxie XL500 hardtop, but that used the old promo tooling, which meant having no engine detail, the hood molded one-piece with the body shell. The 3in1 kits have not been seen in stock form since 1964, while the hardtop 3in1 was modified into a Nascar stocker in 1968--and the tooling apparently cannot be restored to stock configuration. Art
-
1921 Olds 4-cylinder
Art Anderson replied to Pat Minarick's topic in Model Building Questions and Answers
The Beverly Hillbillie's Truck is a 1921 Oldsmobile Model 43A, which could be had with either the 4-cylinder (made by Northway, IIRC) or a new V8 engine. In a book I once had, by George Barris in which he described the various TV and movie vehicles they built, the BHB truck wasn't modified particularly, rather just cleaned up, engine given a tuneup, and the various props added to it. It is a 4-cylinder car, actually and still exists, in the the Ralph Foster Museum on the campus of The College of the Ozarks, Point Lookout, Missouri. Art -
I used the technique for creating resin casting masters, most notably on a couple of dashboards, the primary example being the AAM '62 Studebaker GT Hawk. But the technique can be used for scripts, badges, door handles. The caveat is, of course, the ability of a modeler to do all the really delicate work involved, and it can be very delicate indeed! As for "coloring" the script, that's what BMF was created for--again, more delicate work! Art
-
If you have an industrial plastics supply company anywhere near you (the kind of place that sells, among other things, acrylic plastic, AKA plexiglas), chances are they have Weld-On #3, which if not the same stuff as Tenax, is a very close relative!) you are in like Flynn! About 6 years ago, I bought two half-pint cans (8 fluid ounces) of Weld-On (incidentally this stuff is sold by Plastruct!) that I got at the Meyer Plastics shop here in Lafayette (Meyer is based in Indianapolis IN). I simply decant the stuff by means of a large eyedropper from that can into an old Tenax bottle, and use it from there. Sometimes in our hobby, it takes some searching, some creative looking, but the stuff I like to use is still out there--just do some looking if you can. BTW, I got both cans of the stuff for less than $8 each! Art
-
What I wrote on that forum was a description of the way Juha Airio made foil-cast scripts. It might be wise to point out however, that with many model car bodies, the scripts have been engraved into the tooling pretty much to scale as regards the "height" of the detail (thickness of the script above the body surfaces) which can make any casting of such details a very delicate matter indeed. In thinking about this factor, I reached back into my "memory bank" to an earlier time: Back in the 70's, I was very deep into replicating Indy cars, and found myself in need of instrument details for race car cockpits. Not wanting to tear up a possibly difficult-to-replace dashboard or instrument panel, I hit on the idea of making my own epoxy resin castings of instruments thus: I used, for making small molds of instruments, "Silicone II clear sealer" which back then was a GE product, but is now produced by DAP, and is available in just about every hardware/home improvement section of the big box stores, not to mention Home Depot, Lowe's etc. This is the old fashioned air cure silicone rubber sealer used to seal up shower stalls against the rim of a bathtub, and is thick enough to not require any sort of "damming" around the detail you may wish to copy. To start with, you will need something to act as a :"mold release", as DAP Silicone II does stick readily to styrene. This can be Vaseline petroleum jelly, but it takes only a little bit, wiped on, and then wiped down thoroughly to rid the surface (and the cavities in whatever script or detail you want to copy) so that the Vaseline doesn't have a buildup which would obscure a lot of that detail. Next, squeeze a small drop of the stuff onto the detail, and use a toothpick to ensure that no airbubbles are trapped against the script or emblem. Next, squeeze out a large blob of the stuff on top of that, gently spread it out a bit, but try for say, a 1/8 thick layer over the area where that script or raised detail is, and then let it dry thoroughly--generally about 24 hours. Once cured, you simply peel the cured Silicone II blob off that surface, and you have a mold! Now, I always smoothed the back side of such molds by shaving any peaks off of the cured silicone rubber, the idea being to get it to lay reasonably flat on the workbench. Next I mixed up some DevCon 5-minute epoxy, spread that onto the mold, and again used a toothpick to make certain that all the details in that mold are filled, and not worrying about how thick the layer of epoxy might be. After the epoxy has cured, it will still be a bit rubbery (flexible), so I simply would put the castings on an old cookie sheet, and bake them in a tabletop oven, but nowadays, a food dehydrator will do the same thing, at a lower temperature, but of course it will take a bit longer. This hardens the epoxy considerably. Finally, to thin down such details, I simply used a sheet of 400-grit Wet or Dry sandpaper, laid grit side up on a flat surface (used to use the kitchen countertop, but now use a sample of thick plate glass), with a small puddle of water between the back of the sandpaper and the flat surface, which keeps the sandpaper flat, and prevents it from moving around easily. Next, I put a few drops of water on the grit, and placing the casting detail side up, simply scrubbed it gently in circles on the sandpaper, until I had sanded away the excess material to just the thickness of thin flash as one might see on model kit parts. That flash could then be trimmed away with a brand-new #11 Xacto blade, and the detail will be ready to attach to the model. Yeah, it is possible to break the epoxy details made this way, but if you break one, just make another one. Art
-
Pearl Harbour - 71 years Ago
Art Anderson replied to impcon's topic in General Automotive Talk (Trucks and Cars)
Every day, I find myself (born at the climax of WW-II, in the summer of 1944!) remembering the sacrifice of the the millions of men and women who did what they had to do, to make this world a safe place for a little kid like me to grow up! Thanks to all our veterans, and my prayers of thanks and support go up daily to those who paid the ultimate sacrifice! Art Anderson -
Finally bought paint booth (Update 12/21/12)
Art Anderson replied to dougp's topic in Model Building Questions and Answers
I have the 30" Pace, and love it, one of the very best pieces of equipment I've bought for my hobby in the past 60 years. Being an apartment dweller, exhausting the fumes of airbrushing from my apartment is a critical issue, especially as this apartment is in a converted house with central HVAC (NO way do I want to upset either of my neighbors, expecially the elderly woman downstairs!). In the past, I have used my old Badger spray booth (talk about spraying into a microwave!!!), and hooked it up to the dryer vent (that apartment had a laundry room, but given that there was an open laundry facility just down the hall, no point in my buying a washer and dryer), with no problems whatsoever. My other parameter has been, for years, the removal of particulates from the surrounding air in my home--I hate the fine overspray dust that happens--I prefer to build model cars, not dust dried overspray off of everything--that is an interference in my free time for building model cars (and were I married still, I am sure I would get a ton of interference from the distaff side if I wasn't doing something about all that colored dust. Art -
Inkjet printing on BMF?
Art Anderson replied to sjordan2's topic in Model Building Questions and Answers
I've been using BMF since 1970 (when it was first introduced) and never experienced any sort of coating on top of the original chrome BMF. Art -
And yet, the vast majority of model car builders ages 55 and up started with glue-kits for one simple reason: There were not snap kits around back in our younger years. And learn? We learned by doing, mostly on our own--very, very few of us had fathers with much understanding of model kits, and many lacked even the older brother--so learn by doing it was, seriousl. Yeah, it's nice to have a mentor, even fun to be a mentor in this hobby, but at the same time, for the mentor to push this way or that can often be disingenuous, even overwhelming. Better to first gauge the level of interest in the subject matter, and if that is there, with at least a bit of passion, gentle and positive encouragement. Art
-
Larry, not trying to diss what you have said here, but a couple of things from my research over the years: The pics you show of the fastback 88 and the 2dr sedan show the very same door, up to and including the upper window framing. Second, if I am hearing you right, you are saying that the windshield glass on the station wagon is itself taller than on the sedans and coupes? That's pretty hard to understand, given that in any automobile body, the firewall/cowling/windshield frame/A pillars is the single most expensive part of the body shell, and next to the engine, the single most expensive part of a car (certainly from the 50's and 60's--source none other than the late GM stylist, David Holls, who was in GM Styling at the time the '49 GM bodies were being styled--I knew Holls in his later years, BTW) Even harder would be to feature that for 1950, the station wagon was the lowest production body style of all, and yet it used a taller windshield glass? Or, do you mean there was a lower roofline on the fastback vis-a-vis the coupe and sedan bodies, and that the station wagon roofline was taller than any other Olds body that year (that is true, of course). I know the convertible and Holiday hardtop had a lower windshield, but I would be interested to see the camparison from say, a windshield glass exchange manual--that to me would be the definitive source. Art
-
Paasche Single Action - Which Tip?
Art Anderson replied to Ken McGuire's topic in Model Building Questions and Answers
I've used the #3 tip exclusively for painting model car bodies for years--lacquers, enamels, water-borne acrylics. It has always done a great job for me. Art -
Status of Lindberg?
Art Anderson replied to Casey's topic in General Automotive Talk (Trucks and Cars)
Not quite! J Lloyd is based in Cedar Rapids IA, and they were producing their kits in China--the last Lindberg kit I bought was the Dodge Charger police car, and it clearly states on the box "Made in China". There's been enough intrique with J Lloyd/Lindberg to make for a fairly long-running soap opera though. Art -
Working brass shim stock.
Art Anderson replied to Pete J.'s topic in Model Building Questions and Answers
If you are going to anneal brass for working, it's pretty much accepted that you would anneal the entire piece that you are going to work. Art -
Working brass shim stock.
Art Anderson replied to Pete J.'s topic in Model Building Questions and Answers
Pete, the old-fashioned guillotine type will work quite well for shearing truly thin sheet brass--probably no thicker than .010", best done if the metal is annealed before hand. For thicker brass stock, then yes, a jewelers' saw or fine toothed razor saw. Art -
Spray Booth - Fan Location
Art Anderson replied to hooterville75's topic in Model Building Questions and Answers
Then, why, oh why, do commercially built airbrushing spray booths come with filters? Hmmmmmmm? Better safe than extra-crispy, my friend. Art -
Spray Booth - Fan Location
Art Anderson replied to hooterville75's topic in Model Building Questions and Answers
Pat, you miss my point. While of course I referred to Liberty Mutual, but the annals of industries where spray painting is used are filled with anecdotes of fires from accumulated dried paint dust--autobody shops, furniture factories, cabinetmakers, the whole gamut. Not to mention, the accumulation of overspray in one's house, messy of course, and stains on the outside of the house at that. For the small price of a decent quality filter, why risk tens of thousands of dollars in potential damage, not to mention the lives involved? Also, bear in mind that not just a few members here live in apartments--landlords will not take kindly to paint overspray dust all over once a tenant moves out. Things to consider, methinks. Art -
From my resin casting experience (I calculated from my production logs from AAM last winter--just shy of one million individual castings made from January 1989 to early 2000!): Polyurethane resin is impervious to the solvents in lacquers at least from spray painting, so the adhesion can be less than expected, and with enamels, very much the same thing. This is why I suggested, above, getting some "adhesion promoting primer" (my experience was with the SEM product, which I used on all parts that were headed to the plater--as I was doing several quite delicate antique car bumpers (most notably the rear bumper for my '40 Ford Woodie Station Wagon transkit. I experienced a serious problem early on with the plating simply flaking off that bumper, due to it's delicate, very flexible nature, so I went looking, found the SEM adhesive clear primer. I used that stuff on a run of bumpers, and when they came back I performed the following test: I simply took a bumper, twisted it almost to a pretzel (the type of resin I used was flexible enough to do that), and let it spring back into shape. Not only did the plating stay put, but when the bumper returned to its original, as-produced shape, there was NO evidence of any flaking--I actually built up the house display woodie with that bumper, and today, 18 years later, it still looks just as good as it did on the plating tree. So, I know that the stuff works. Any really good professional supply house for autobody supplies will have several different brands of this sort of primer. Art