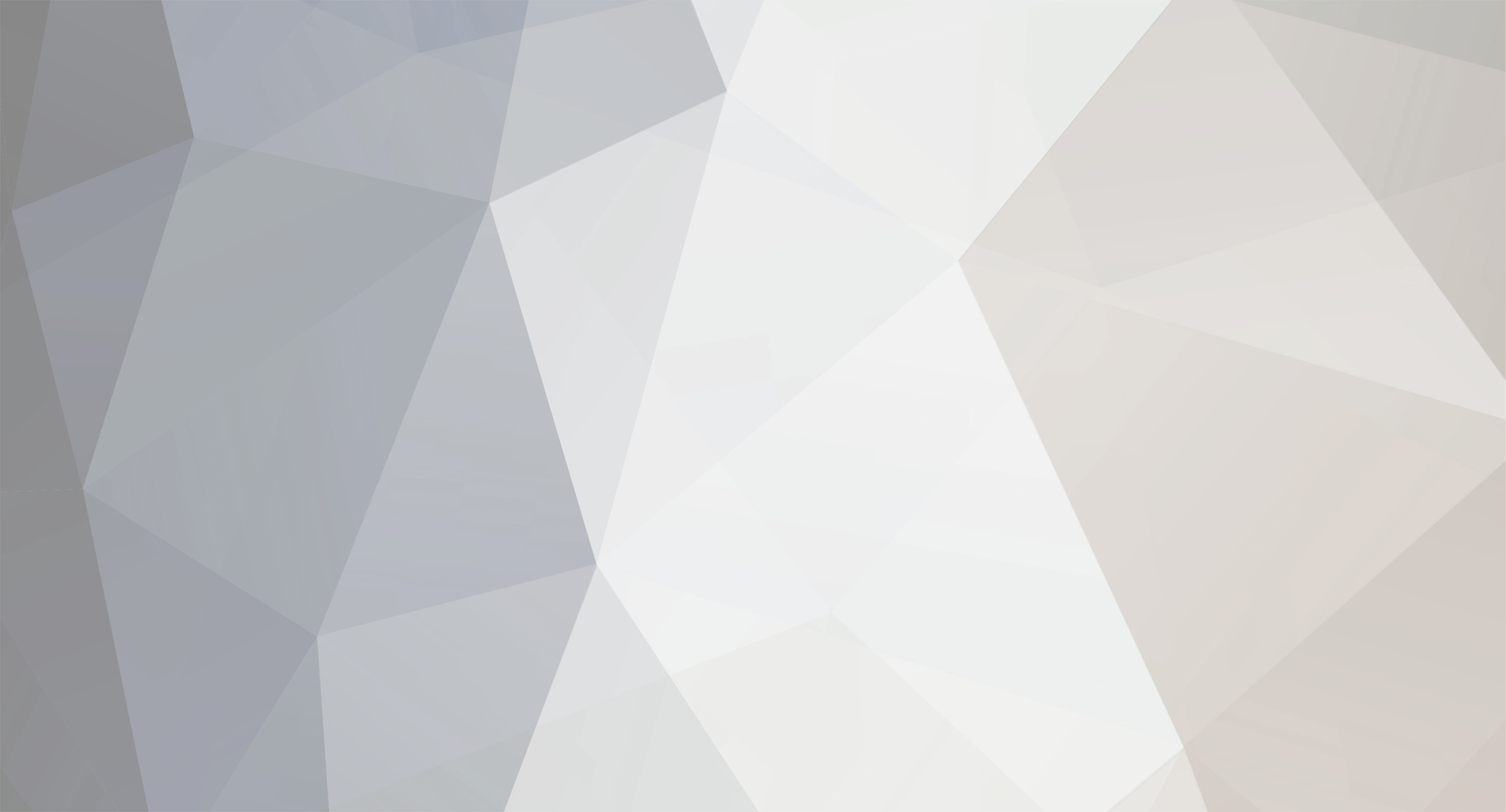
Art Anderson
Members-
Posts
5,052 -
Joined
-
Last visited
Content Type
Profiles
Forums
Events
Gallery
Everything posted by Art Anderson
-
1976 Chevy Caprice kit questions
Art Anderson replied to Nitromethane's topic in Model Building Questions and Answers
A very good source for reference pics is simply to do a Google search for the year/make/model of car in question. When the search comes up, simply click on "Images", and whatever images (pics) of that car that Google knows about will load--be not afraid to repeat the search every few days though, as pics online do come and go. Art -
Consider this: Revell introduced Challenger I in the fall of 1962, at a time when Mickey Thompson was at the top of his game with record-setting cars, and Revell was looking to truly break into the market for really decent model car kits. Same with Ivo's Showboat, although that came a couple of years later. By the time Golden Rod hit the scene, the market for models of such cars had pretty much evaporated. Art
-
Upsides and downsides to Lindberg kits?
Art Anderson replied to dantewallace's topic in Model Building Questions and Answers
That is pretty much as Lindberg tooled and produced this kit back about 1961, with the exception of the hubcaps and lakes pipes. Art -
Poor Parts Fit
Art Anderson replied to raildogg's topic in General Automotive Talk (Trucks and Cars)
Michael, that's a very good question! Back 50-55 yrs ago, when I'd stop into the hobby shop, cruise through the model car kits on their shelves, EVERY one of them, for the most part (Premier/Palmer being a prime exception) was "state of the art" for that time, so in most ways, I along with my peers pretty much knew what we were getting into. However, now, in 2013, that is not quite as simple. Nowadays, walk into a hobby shop (or shop online) for a plastic model kit, unless one has been around the hobby for at least a couple of decades or so, it can be pretty near impossible to always determine if that '62 Buick Electra 225 is a modern 21st Century level kit, or something straight out of 1962 (it is the latter, of course!). In far too many hobby shops today, expertise among the staff tends largely to be limited to the highly technical RC models and/or model railroading--I don't remember when the last time was that I stopped into a hobby shop anywhere and actually found somebody who really knew much about the plastic kits on their shelves. So, in that regard, the Latin warning "Caveat Emptor" (buyer beware) does come into play. That's one of the really great things about web-based message boards such as this one--anyone can ask the questions, and more often than not, get an answer about such things. That said, model companies aren't going to stop reissuing old kits--they are part of the mix that helps provide capital (hopefully) for tooling new products. Some older kits out there weren't truly all that great when they were first introduced, not by a long shot: For example, AMT Corporation built up a pretty wide variety of 1/25 scale model kits of heavy duty trucks between 1970 and 1977, but many of them were highly problematic as to parts fitting as they really should have, particularly their frames and suspension systems--some of them took a fair amount of care in assembly, taking the time to make sure that the frame assembled flat, true and square. Compared to the likes of the newest kits from Revell (notably their '50 Olds, which is on my bench as we speak) and the Moebius Hudson and Chrysler 300 kits, parts fit is generally VERY precise, in fact precise enough so as to require careful reading and study of the instruction sheets to ensure that the kit goes together as advertised (omit this, and you may not get the thing together at all correctly!), but that's a matter of complexity, not of real or perceived poor quality. We as adults have come to demand ever-increasing accuracy, more and more parts count, all of that. Back in the 1950's, Lindberg was one of the fledgling companies in the field of plastic model kits, and their instruction sheets had (even with the arguably very simple aircraft kits they produced back then) a warning in bold type: "Please, before you try to build this your way, try it our way!" which when I look back at that (I'm getting pretty close to 70 years old these days) it was, and still is, good advice. So, when you or anyone else has a question about some kit that you aren't sure about it's derivation, or how many years ago it may have been designed and tooled, please ask here, or on the Spotlight Hobbies Message Board--between these two forums, there are literally centuries of experience, and a ton of knowledge, and I'm certainly not the ultimate repository of that. Art -
What is a peaked roof?
Art Anderson replied to Ken McGuire's topic in Model Building Questions and Answers
Somehow, I doubt that "repairability" was frequently taken into consideration during the styling process though. Rather, I suspect that the short "crease" above the center of the windshield on say, the 49-51 Fords or Mercury's was anything more than a bit of a styling cue. "Peaking" any body panel refers, I believe, to the customizer's practice of adding what stylists call a "windsplit", or a pronounced, raised crease running some length of say, a hood, trunklid, the tops of front fenders or rear quarter panels, even the full length of a roof. At the extreme, some customizers were known to "peak" the headlight bezels on cars such as '55-'56 Fords and Merc's, often drawing that peak out forward, even curving it downward a bit, before leading in the sides of it for a finished appearance. Art -
Poor Parts Fit
Art Anderson replied to raildogg's topic in General Automotive Talk (Trucks and Cars)
I meant to say, above, that all that hand-work meant, many times, for rather ill-fitting parts. About 10 years ago, while working at Playing Mantis, Tom Lowe asked me to build up the old MPC "Tognotti's King T". Now that is a kit that has intrigued me for decades, but I'd never built mine. Frankly, I found the parts fit to be not just difficult, but downright lousy, particularly in the area of the suspension parts. A few small parts, seemingly indifferently tooled, almost defied assembly, frankly. A lot of Revell kits from back in the 60's suffered at least to some degree, pretty poor parts fit--still others very delicate indeed (the front axle assembly of their '29 and '31 Model A Fords stick out as prime examples of this), even though Revell tended to do a very masterful job of making those parts extremely accurate (having owned and restored a couple of real Model A Fords back in those days, I was--and still am--pretty conversant with how they go together, and what the various parts should look like. Enter the 1970's: By 1970, the popularity of promotional model kits of real cars declined rapidly, with the coming of ever-larger new car dealerships, whose "floor plans" allowed for inventories including just about every trim level and body style, and of course, other forms of advertising. That lead to a drop in the variety, and the sales, of new "annual series" model kits, the decline of customizing at the time taking away a lot of the reasons for true 3in1 Customizing kits. This all translated into a slide in sales for companies such as AMT, MPC, and certainly JoHan of such kits. In addition, recurrent recessions accompanied by rather serious inflation ate into development and tooling dollars, and it showed. Monogram tended to really stand out, especially given their widely diverse line of model kit subjects, so they were not nearly as affected. By the end of the 70's, AMT had been folded into Lesney, as a subsidiary, JoHan was limping along with reissuing old promo tooling, and such kits from the 60's and early 70's as they could scrape together the tooling, Revell (once the King Kong of plastic model kits) was owned by a French toy company of questionable sustainability. IMC, Hawk, Aurora were all gone from the scene except for such tooling as the likes of Testors and Monogram chose to reissue. A further complication was the concept of "price points", artificial price levels that the burgeoning "big box" retailers (KMart was the big dog in the litter then) dictating to their vendors, model companies included, the MSRP of kits they had to meet or lose shelf space. Radio control was the big buzz-word in the hobby industry by 1980, and electronic games entered the fray which took consumer dollars away from more traditional hobbies. All this meant cost-cutting wherever possible. All that conspired, I think, to push model companies into more and more a "reissue mode", which meant dusting off old tooling, and using those tools with new, less expensive blends of styrene (meaning softer, more flexible, but less breakage) as petroleum prices continued their inexorable rise. The situation vis a vis mass retailers continued throughout the 80's, into the 90's and into the decade now just past, until the Big Box retailers pretty much pushed model kits off their shelves in favor of other merchandise which could be sold much faster, and in greater quantities compared to the in-store "real estate" needed. That leads us to today: The cost of developing new kits today, while expensive, is nowhere what it was, relative to say 40-50 years ago, and the introduction of computerized design, tooling and such has truly made a difference--just take a look at any of the truly new kits from Revell and Moebius this past year: They are light years ahead of anything tooled up even 20 years ago. But the problem still remains how to explain to younger (and by that I mean under the age of say, 45yrs old) that so many of the kits out there on store shelves are from tooling cut decades in the past, were created when a computer took up an entire building (or certainly a very large room!) and operated by teams of engineers who were depicted in cartoons wearing white lab coats, peering through thick glasses, with bald heads and beards. Times have changed, model kit wise, vastly for the better--let's hope this is a trend that will continue. Art -
Is that John Kaelin perchance? I have an email from him, with a link, but am unsure about opening it. Art
-
Poor Parts Fit
Art Anderson replied to raildogg's topic in General Automotive Talk (Trucks and Cars)
Every model company has had their share of "klinkers" to be sure, but it might be wise to consider that many model kits (not limited to model cars, BTW) are reissues from a day and age when the "science" (if you will) of creating a plastic kit was nowhere what it is today in the 21st Century. Many of the so-called "iconic" model kits of the 1960's weren't all that good when compared to the newest of tooling from the likes of Revell or Moebius, and for a number of reasons: For starters, if there was ever an "analog" era of model car kit design, the first 20 years or so of plastic model kit design were analog personified. By that I mean, there was no CAD, there was no CAM back then. A master modeler back then, termed a "pattern maker", had to carve by hand each and every part of a model kit, from wood! To facilitate that, those pattern makers (and the early ones were not particularly miniaturists, but rather came out of the die-casting industry, and while they could certainly read a set of drawings and interpret them, they had to do that interpretation in a scale several times larger than the final injection-molded model kit. Generally with model cars, that meant using say, 1:10 scale wooden masters for a 1:25 scale model car, or 1:12 scale for a 1/24 scale kit, those larger scale sizes being easily "dialed down" numerically to their respective final scale sizes. Body shells were universally sculpted in wood, SOLID wood blocks, every bit and piece of the engine, chassis (even fairly delicate suspension parts and exhaust systems) fabricated in wood. These masters were often then pressed into blocks of clay, from which an impression could be made by using rubber molds for pouring resin into, to create further masters for the molds (dies). Once both halves of a master mold (still in the larger scale in which the wooden master parts were fabricated/carved) were made, the resulting master mold could be clamped together, and some form of liquid resin injected into them, giving hardened resin castings that could then be test fitted, and the master molds "adjusted" to the point that they could get parts to fit as they should. Once that worked out, the master molds could be transferred to a mechanical 3-axis "pantograph" which had both a "stylus" for following the shapes and contours of the approved master mold, and a rotary milling cutter which would translate those shapes into blocks of steel (or often times, a tooling metal alloy "beryllium copper", all the while reducing the "scale" from say, 1:10 scale down to 1:25 AND making a "female" shape in that steel while following a "male" shape on the larger master mold. Those solid wood body masters (also done in the same larger scale as all the little parts) were cast in a resin material, and then the multiple slide mold cavities pantographed into steel, the mold slides separated where they needed to be, in order to allow a one-piece body shell, and the inside or core mold created in a rather imprecise manner, which is why so few model car kits from 35yrs ago on back had any sort of true engine bay molded into the body shell. All of this not only cost a ton of money, but also meant very long lead times for new model car kits. In addition, it made really good parts fit, especially if the kit was designed with lots of intricate parts. One last thing here: Plastic model kits were engineered back then for different, harder grades of styrene plastic than are generally used today. That older plastic was a lot harder, more brittle, yet was far less susceptible to shrink marks with those older, thicker body shells. Art -
Poor Parts Fit
Art Anderson replied to raildogg's topic in General Automotive Talk (Trucks and Cars)
Every model company has had their share of "klinkers" to be sure, but it might be wise to consider that many model kits (not limited to model cars, BTW) are reissues from a day and age when the "science" (if you will) of creating a plastic kit was nowhere what it is today in the 21st Century. Many of the so-called "iconic" model kits of the 1960's weren't all that good when compared to the newest of tooling from the likes of Revell or Moebius, and for a number of reasons: For starters, if there was ever an "analog" era of model car kit design, the first 20 years or so of plastic model kit design were analog personified. By that I mean, there was no CAD, there was no CAM back then. A master modeler back then, termed a "pattern maker", had to carve by hand each and every part of a model kit, from wood! To facilitate that, those pattern makers (and the early ones were not particularly miniaturists, but rather came out of the die-casting industry, and while they could certainly read a set of drawings and interpret them, they had to do that interpretation in a scale several times larger than the final injection-molded model kit. Generally with model cars, that meant using say, 1:10 scale wooden masters for a 1:25 scale model car, or 1:12 scale for a 1/24 scale kit, those larger scale sizes being easily "dialed down" numerically to their respective final scale sizes. Body shells were universally sculpted in wood, SOLID wood blocks, every bit and piece of the engine, chassis (even fairly delicate suspension parts and exhaust systems) fabricated in wood. These masters were often then pressed into blocks of clay, from which an impression could be made by using rubber molds for pouring resin into, to create further masters for the molds (dies). Once both halves of a master mold (still in the larger scale in which the wooden master parts were fabricated/carved) were made, the resulting master mold could be clamped together, and some form of liquid resin injected into them, giving hardened resin castings that could then be test fitted, and the master molds "adjusted" to the point that they could get parts to fit as they should. Once that worked out, the master molds could be transferred to a mechanical 3-axis "pantograph" which had both a "stylus" for following the shapes and contours of the approved master mold, and a rotary milling cutter which would translate those shapes into blocks of steel (or often times, a tooling metal alloy "beryllium copper", all the while reducing the "scale" from say, 1:10 scale down to 1:25 AND making a "female" shape in that steel while following a "male" shape on the larger master mold. Those solid wood body masters (also done in the same larger scale as all the little parts) were cast in a resin material, and then the multiple slide mold cavities pantographed into steel, the mold slides separated where they needed to be, in order to allow a one-piece body shell, and the inside or core mold created in a rather imprecise manner, which is why so few model car kits from 35yrs ago on back had any sort of true engine bay molded into the body shell. All of this not only cost a ton of money, but also meant very long lead times for new model car kits. In addition, it made really good parts fit, especially if the kit was designed with lots of intricate parts. One last thing here: Plastic model kits were engineered back then for different, harder grades of styrene plastic than are generally used today. That older plastic was a lot harder, more brittle, yet was far less susceptible to shrink marks with those older, thicker body shells. Art -
There were length and wheelbase differences to be considered here: Yes, in length and width, a '34 Ford pickup box is the same dimensionally as the '32 Ford. However, the spacing of the rear wheels/fenders along the sides are markedly different between the model years: The '32 Ford Model B/Model 18 has a wheelbase of 106", where beginning in 1933, Ford went to a 112" wheelbase, which is why, if one ever gets to see a true '32 Ford pickup, the box has an exaggerated overhang at the rear. Now, Model A Fords had a 102" wheelbase, which makes for an even shorter length of bed between the rear fenders and cab, and the Model A pickup box was considerably shorter than the '32 and later units. Winfield's "Grasshopper" is a mix of Ford sheetmetal, and does appear to have been built on a Model A frame. Also, the R&D Unique '30 Model A pickup resin/whitemetal aftermarket kit is done off the Monogram 1/24 scale 1930 Model A Coupe, with a new back panel for the cab having been scratchbuilt, the coupe body cut off at the rear edge of the doors--it's pretty close though. I suspect that the pickup box used in that resin kit is the bed from the Monogram Blue Beetle ('29 Model A roadster pickup) which could provide the fenders/running boards/splash aprons, the '30 Model A coupe giving the upper hood panel, and Revell's redone '30 Model A Woody the '32 Ford grille shell. The problem will be the pickup box, Grasshopper appears to have either a late 1931 Model A pickup box (which predicted the longer, deeper box used 1932-about 1937) and that box doesn't exist in scale. The AMT '34 pickup box could be modified to fit, but here you'd run into the scale difference between 1/24 and 1/25. Hope this helps at least a bit. Art
-
It seems to me that a lot of the time, we tend to get hung up in EXACT scale measurement down to the proverbial "gnat's eyelash". when in fact many measurements that are even being discussed in this thread are not readily discernible to the ordinary, unassisted human eye. In addition, when discussing wood (balsa, basswood, or even hardwoods) that's a material that is virtually impossible to cut micrometer perfect and have it stay that way, due to it's being a porous, moisture-sensitive material. For example, basswood cut to perfect shape at a factory someplace will NOT hold the same width or thickness in say, Phoenix AZ in July as it might have in other parts of the country with much more humid conditions (ever wonder why a cabinet door (or even wooden door that is part of one's dwelling) doesn't always fit the same at differences throughout the year? Five or even ten thousandths of an inch in the thickness or width of a 1/25 or 1/24 scale basswood 2X4 stud frankly will not be seen by even the most discriminating viewer of a diorama building, as long as its in a wooden structure, not something laid onto a finely machined surface (and who among us does that either in metal or plastic to combine with wood?). All that said, in the field of model railroading, there do exist 1/48 scale ("O Scale) sizes of scale lumber. Now, 1/48 scale is exactly half the size of 1/24 scale, so a scale 4X8 plank in 1/48 scale will be a 2X4 in 1/24 (true 2X4's are cut to 2" X 4", and then planed down to remove all the rough splintering before they are sold for building a house (originally as much for fire prevention as anything else), and if one is replicating a wooden frame building constructed say, prior to the late 1930's, unplanned structural lumber was pretty much what they used. Another thing is the "Illusion of real" here: In scale modeling, we often put up with little compromises, for varied reasons, but if the end result looks realistic, minute variances in thickness and weight of material really do tend to disappear, because the whole presentation just seems to scream "REAL" and/or "ACCURATE". Just some thoughts I have on the subject. Art
-
I'm sorry, but I quite fail to understand all the handwringing over cars being damaged/destroyed in the making of motion pictures or TV shows. With only a few exceptions (such as the one and only Lincoln Futura dream car being cobbled into the TV Batmobile), the cars used as props in Hollywood are, and pretty much have been for decades, mass-production items. Somebody check me if I'm wrong here, but when a Movie/TV studio does rent a collector car, they generally do not damage it in any way--but if it's to be "expendable" in the making of a film or TV episode, virtually always the car is one of a mass of the same thing. So, can we get a break from all the whining over "they destroyed (however many) 1968 Whatchamightcallit GT's to make that awful movie"? Art
-
OK, so this is the first engine I've detailed out since late 2004. Added are plug wires, through .020" holes drilled through the wire looms (those raised ribs on the valve covers, which cost me 3 drill bits!). The fuel line sediment bulb was made by chucking a piece of 1/8" styrene rod stock in my cordless Dremel, then turned to shape using a couple of needle files. Art
-
Back in my Indy Car building days, I used to overpaint just about all the decals I used, given the generally poor quality lithographed decals most kits had in them back in the day. I found it pretty easy to paint over them, using the original printing as a guide, almost exactly the same as working with old-fashioned paint-by-number sets that were popular in the 50's and 60's. I also found that after learning how to do that, I could easily hand-paint my own graphics, without the benefit of having a decal to use as a guide. I built this AJ Foyt Coyote (1977 Indy winner, AJ's historic 4th trip to Victory Lane) in 1988, all the graphics are hand painted, except for the accessory decals:
-
Resin casting Tip?
Art Anderson replied to one_eyed_croaker's topic in Car Aftermarket / Resin / 3D Printed
The one problem I see with this approach is the fairly short "pot life" of polyurethane resin. This is the reason why professional resin casters, such as Modelhaus, Missing Link Resin Castings, Scale Models by Chris and others who do resin casting as a professional business use pressure tanks, as they can pressurize a tank, with the uncured resin in the molds inserted, quickly enough to literally crush out small air bubbles by the pressure of several atmospheres before the resin starts to "kick". That said, it is very possible to "chase" small air bubbles out of little castings simply by pushing them out of small details by using a toothpick. Art -
Lemme see here: Roadster--check Cabriolet Sport Coupe 3-window Deluxe coupe--check 5-window standard coupe--check Phaeton Convertible Sedan (B-400) Victoria Tudor Sedan--check Fordor Sedan Station Wagon (requires a pickup radiator shell and hood though!) Roadster Pickup Closed Cab Pickup Closed Cab pickup Art
-
School bus question
Art Anderson replied to Harry P.'s topic in General Automotive Talk (Trucks and Cars)
Harry, actually the worst danger to kids re: school busses is not a wreck, but the stupid idiots who refuse to stop when a school bus stops to board or let off kids! The incidence of children being injured in school bus accidents, at least here, is actually quite low--the last serious crash here involving a school bus severely injured the granddaughter of a cousin of mine, when the school bus she was in was rear-ended by a truck driver not paying any attention to stopped traffic ahead. Rachel's injuries were severe, it took about 5 years and several surgeries to repair her lower legs which were badly injured. Art -
School bus question
Art Anderson replied to Harry P.'s topic in General Automotive Talk (Trucks and Cars)
Not really. While school busses in the Midwest, certainly the Great Lakes region, used to be yellow all over, white roofed school busses have been around in the hotter parts of the US for decades--and for the very same reason that white roofs on 2-toned cars became popular--white reflects a lot of the sun's heat in the summer! Indiana school busses were Yukon Yellow from the the 1940's forward (the dark orange school bus used in the iconic film "Hoosiers" wasn't accurate from my memory, never saw an orange school bus as a kid!) all over. The white roof thing started here about 1980, but it isn't universal even today--Lafayette and West Lafayette school corporations don't have them, but Tippecanoe (county) School Corporation busses have white roofs. A lot of that stems, I think, from the old traditional school year for rural schools here, stemming from the era when rural schools here started their year in the 2nd week of August, and ended with the first weekend in May every year, so farm kids could help with corn planting, then go back to school after the summer grain harvest (winter and spring wheat, barley and oats), where we city kids got to be free until the week after Labor Day, and stayed in school until generally the first or second of June every spring. In addition, at least in Indiana until the late 1960's, most rural schools relied on farmers who contracted to operate school busses. In that earlier system, a farmer would buy the school bus chassis, have a body fitted to it, and ran his route every morning and afternoon during the school year, generally replacing the chassis about every 4-5 years, having the body transferred from one chassis to the next. But increasing concerns about safety and liability concerns lead the then-newly-formed school corporations (back 60 years ago, rural schools here were the property of the various townships in rural Indiana), the newly consolidated school districts opted to take over bus transportation themselves, the result being considerable uniformity. As for aerial surveillance, Indiana State Police no longer operates that sort of thing, due in part to variable weather for flying, and costs, so few, if any school busses here have any sort of numbering or logo's on their roofs. Art -
Today January 11, 1913
Art Anderson replied to Madd Trucker's topic in General Automotive Talk (Trucks and Cars)
Not really. Horse drawn carriages used names based on such as Greek mythology (Phaeton, for example), or the name of a famous person for whom one was built (Victoria), or a particular city or town (Landau), or it's particular use (Hansom Cab or "Cab"). The most plentiful closed 4-place carriage style was the "coach" of course, but those had two bench seats, facing each other (the passengers in the front seat rode facing to the rear). The oldest reference to the term "Sedan" as used in conveying people that I can find is the "Sedan Chair" which held one or two passengers, but was not a wheeled vehicle at all, but rather a closed "box" with a door on either side, suspended between two wooden poles, and was carried by 4 strong men. I believe the Sedan Chair originated in Italy, possibly Naples. One of the framers of the US Constitution used one during the Constitutional Convention in Philadelphia, one Benjamin Franklin, who was, by that time over 80 years old. True sedans, as the name refers to automobiles, were almost impossible to build in the early days of the auto industry, due to the inability of manufacturers to make truly stiff frames, back in the days of open channel frame rails and riveted, rather than welded joints between frame rails and crossmembers. In addition, car bodies were wooden in nature, having only sheet metal skins attached to wooden framework. This meant a lot of flexibility in both frame and body structures; in other words, the entire car literally twisted as it went over rough and rutted roads, even city streets. As a result, the first closed car bodies produced were either 2-place coupes or the more opulent chauffeur-driven "touring cars" (not the open variety) which had a closed compartment for passengers in the rear, with an open driver's seat, often with a roof canopy over the driver, which was not attached to any windshield. That, along with very heavy wood construction, allowed such bodies to be carried on those early, very flexible chassis without the body simply being twisted apart. In the "teen" years, a couple of things happened: Pierce Arrow developed a body shell made from thin aluminum castings, which while not all that popular, did point toward the possibilities of body shells with torsional resistance. In 1915, Edward Budd (the same Budd whose company made truck wheels, bodies for Ford Motor Company, and of course, stainless steel streamlined railroad passenger cars later on) developed the first all steel car bodies, and very quickly was supplying body shells to Dodge Brothers. Also, in 1915, Ford introduced the first mass-produced sedan, the so-called "Center Door", which was a true sedan body, but with door access in the middle of the body side only (you entered the car from those doors, and crawled between the two, narrow individual front seats to sit down, there being a full-width bench seat in back). However, even that body shell had it's problems with torsional rigidity, and being an extremely tall body, the car was noticeably top-heavy. In the early20's, Essex, a make produced by Hudson, pioneered the concept of the modern 2dr sedan, a body style they termed the "Coach". It was a very sturdy car, due to a fairly heavy frame, and a substantial wooden body framing structure, and began the trend to closed cars for good. Ford, Chevrolet, Dodge and others followed suit, the first Model T 4dr sedan being introduced in 1924, Chevrolet about the same time. But, all those early 4drs tended to creak loudly when traversing seriously uneven road surfaces. In 1929, the Cord L-29 introduced a true chassis stiffener, the X-Member, which pretty much ended the serious flexibility of channel steel rail frames, and generations of sturdy, reliable, quiet sedan bodies have followed ever since, aided of course by unibody technology. Art -
Thin Styrene Strips vs. Glue
Art Anderson replied to Lunajammer's topic in Model Building Questions and Answers
I've got Evergreen styrene strip stock here that is a good 30 years old, and it's still as good as the day I bought it. However, few observations if I may, from years of using thin strip styrene for body details: 1) CA Glue (cyanoacrylate glue, AKA Super Glue will make a bent piece of thin styrene break almost as quick as you can say "break", for whatever reason) for that reason I try never to use CA glue for this purpose. That said, I have a kit-bashed '25 T Touring Car (done from two AMT '25 T roadsters with a good bit of catalyzed putty work to blend the two body shells together, on which I had to add new raised moldings to the extra two doors, as well as replace the kit moldings on the forward half of the body where I used putty to blend the surfaces of both roadster bodies together. For the moldings, I was using .020" Evergreen rod stock, shaved to half-round, and given the catalyzed putty surface, CA was the only choice. I was able to pre-bend the home-made half-round, and by CAREFULLY using the tiniest bit of CA on the flat sides, got those to lay down without any breakage (needed a couple of good stiff drinks afterward though!) 2) Both types of Testors liquid cements have a pair of characteristics that I do not like at all. First, they are a slow drying solvent, which allows the liquid to stay wet long enough to dissolve thin styrene badly. Second, both liquid cements still use a bit of cellulose thickener in them, which just exacerbates the problem. 3) Solution. Flexi-File offers a really great "touch & flow" applicator for the really thin, fast drying solvent liquid cements (Flexi-File packs a bottle of this type of liquid with the applicator, but it works equally well with Weld-On #3, Ambroid liquid cement as well. If you cannot find the Flexi-File applicator, try Hobby Lobby, they sell the item right there in their model car aisle, and they are available online as well. If that is not an option, a really fine, long-bristle artist's paintbrush, called a "liner" also works great--but go for one of the types of liquid glues I mentioned (Weld-On #3 is what acrylic plastic fabricators use to "weld" clear acrylic together, and it works great on styrene as well. The secret here is to hold the styrene strip stock to the surface you want to glue it to, and simply touch that applicator or liner paintbrush with the liquid cement to the seam, it will flow instantly into the seam by capillary action, and in the bargain, it evaporates VERY rapidly, before it can dissolve the strip styrene (in fact this type of liquid cement dries so fast, that you cannot wet one surface, then the other one, stick the two together before it dries!). Hope this helps, if you need more information, please post back or PM me! Art -
Travelling with models
Art Anderson replied to Burnout's topic in General Automotive Talk (Trucks and Cars)
I've taken models to shows, including GSL, traveling by air and nary a problem! When first I did this, to GSL in 2005, I wondered all the same things that any first-time air traveling model car builder must wonder: I looked at the TSA website, but that didn't answer my questions (would the model cars be subjected to a physical examination by some agent at the security area, stuff like that). I then called TSA's toll-free line, and a very polite woman answered my questions perfectly. She told me to pack the models as I would ordinarily do, and they would simply run the bag though the scanner--no need to open up any boxes and such. She also explained to me that the baggage scan is done by magnetometer, which would allow them to see everything inside my carryon's, and that would be it. OK, so off I go. At Midway Airport in Chicago, I did as the TSA rep said, just put the case with my models on the conveyor, along with my suitcase, the basket with my worldly goods in it, and my shoes, jacket at cap. When I got to the other side of the scan, as I started collecting my stuff, the agent doing the scanning walked over: " Sir, those look like fantastic models in your bag, are you going to that big model car contest out in Salt Lake City?' "Yes, I am." "It must be something pretty big, you are at least the 20th person through this gate this morning!" With that he just waved me on, told me to have a great trip and have fun at the contest! Since then, I've made perhaps a dozen flights with models, they never open the boxes to see them, just wave me on through once I've passed the full body scan--and never a hint of any damage to any model carried in this fashion! Art -
While I agree that there surely are modern-day customs and rods that would be great if offered in model kit form, I wonder just how lucrative most of them would be in the long run. In any discussion along these lines, older modelers bring up the kits of "iconic" cars that were produced 40-50 years ago. Yes, it's quite true, more than likely, that some of those kits sold in HUGE numbers, even for the day and age when they were first kitted; but what happened to the tooling after that initial rush of popularity? Some tooling got altered, modified (fill in your own blank) based on decisions that made good sense commercially in later years (regardless of what we modelers think of those decisions today, what were model companies to do with tooling for kits which had run their course in the hobby shops and variety stores of the late 1960's-early 1970's? Let that tooling just take up storage space, gather dust, even rust? As a model car builder for now better than 60 years, and having some experience in both the retailing and the kit industry, the car kits I see as having had the longest runs of popularity have been those kits which were primarily factory stock models, albeit with added custom parts, changes of wheels and tires, while still leaving a lot of room for modelers' imaginations and tools to run wild. Of those kits, beyond the very long-in-the-tooth AMT '32, '36, and '40 Fords, I believe the single model car kit having seen the longest production run of all was the original-tool AMT'57 Chevy Bel Air Hardtop, which was cataloged by AMT, Lesney-AMT, and AMT Ertl every year from 1962 to 1996--34 years. Another old kit I see as lighting fires whenever it sees a reissue from that era is the AMT '57 Ford Fairlane 500. One thing I believe we all tend to forget is, that back in the 1960's, the apex of custom cars and still with a lot of hot rods being built and shown, model car kit subjects were a lot fewer in number, and sales were much higher for just about any new release the model companies put out than kits of today. I can see, almost hear, in my own mind the discussions that would go around the conference table at any company's product planning meeting if the subject of seriously teaming up with a top flight custom car builder for a kit or series of such cars: "OK, so you think this (fill in the blank here) would be a hot subject? Just how many do you estimate we can sell within the first year?" "OK, what can you do as a second release off that tooling, with perhaps a body change?" On and on, such questions do get asked when new model kit subjects come to the table in meetings like that, and they should--tooling $$ don't grow on trees, and wholesalers & retailers will have to be persuaded that any model subject that does make it past the initial planning stages will generate profit dollars for those who will ultimately market the new kit(s) to us modelers. The higher the likelihood of a particular model car subject being a "one hit wonder" with very little possibility of being able to be altered into another version (by adding tooling to the mix, NOT re-cutting the existing tools) the less likely such a subject will make the cut. On the other hand, a model car subject that can, by adding additional, optional tooling say, for a different body style, different engines and so forth will tend to get a lot more positive read from the people who have to approve, and more importantly, commit the capital to making it happen. That has been my experience, as I am sure just about anyone who has ever worked in the industry at some level. Art
-
Welcome, Matija! From Lafayette, Indiana. Art