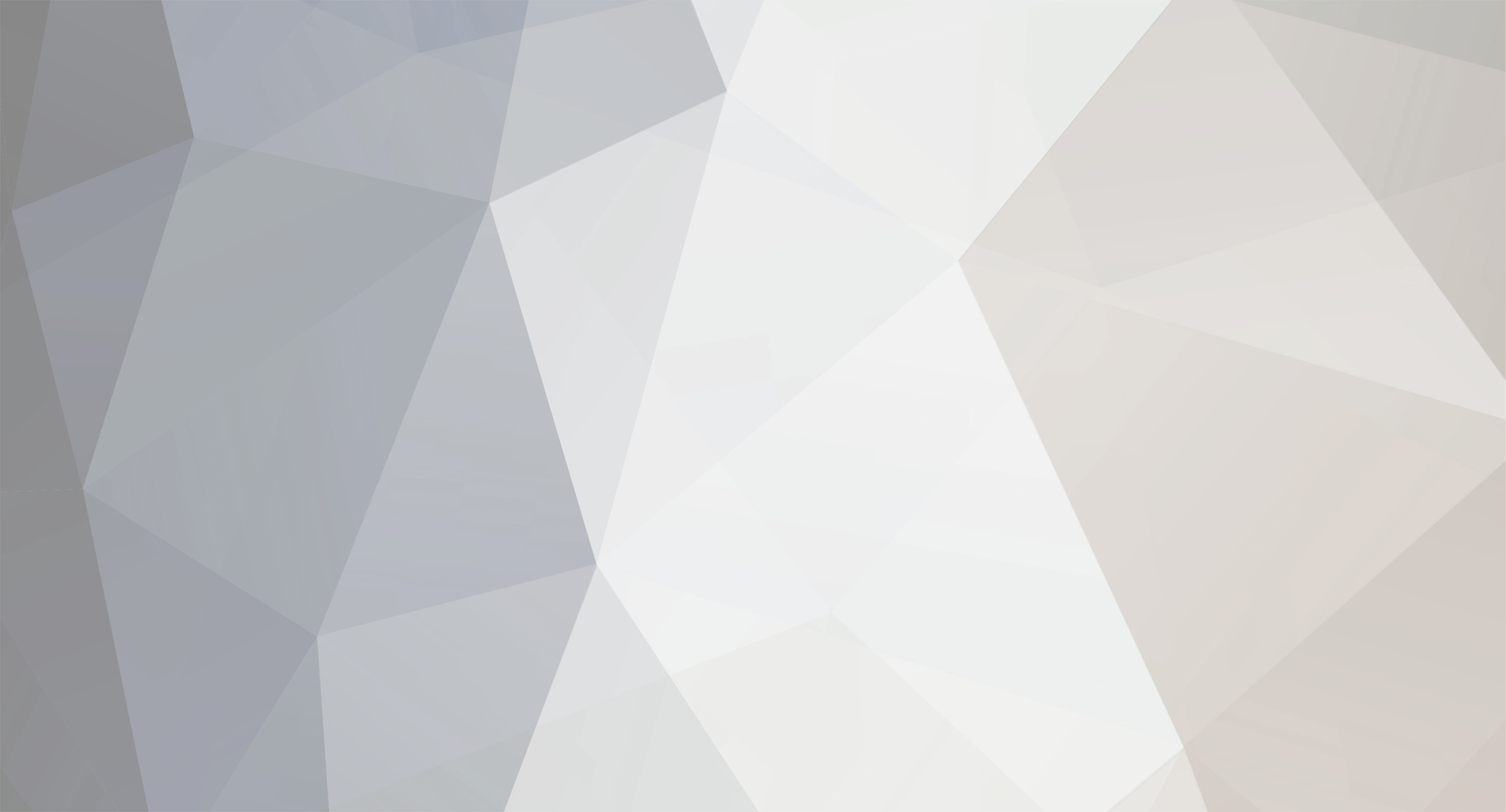
Art Anderson
Members-
Posts
5,052 -
Joined
-
Last visited
Content Type
Profiles
Forums
Events
Gallery
Everything posted by Art Anderson
-
Tunneled, recessed, frenched
Art Anderson replied to crazyjim's topic in Model Building Questions and Answers
All three terms come from the "lead sled" era of customizing which started just before World War II, and reached its zenith in the early 1960's, and refer to bodywork. What Chas SCR referred to as "tunneling" actually was called "Channeling" back then: Channeling was the technique used by early postwar hot rodders to lower the body shells of Model T's, Model A's and '32 Ford bodies down over the frame, by means of cutting the floor framing loose from the body sides, raising them up into the inside of the body shell then welding into place, which created a "channel" of sorts that allowed the body shell to be dropped down over the frame rails, generally with the "sills" of the exterior of the body at or just below, the bottom of the frame rails. This first originated on the Dry Lakes in Southern California for the purpose of reducing the frontal area of the car being modified, in order to lessen wind resistance at speed. It picked up popularity with the "track roadster" era, in which these same types of Ford body shells were channeled over their frames, to lower the center of gravity in hot rods being built up for racing on oval dirt tracks. "Tunneling" referred to the technique of setting headlights (and in many cases, taillights) deeply into their respective fenders/quarter panels by means of using or creating a sheet metal tube matching the shape/diameter of sealed beam headlights and round or oval taillight fixtures. The resulting "tube" resembled the concept of a tunnel, with the headlight or taillight set well into the bodywork, behind the original lines and shapes of the fenders or quarters. It's hard for a lot of modelers today to remember when car radios were extra-cost options, and when a radio was ordered and installed, the antenna was merely mounted over a hole cut in the top of the right front fender, just ahead of the corner of the windshield. One of the customizer's "tricks" became to recess the base of that antenna at the bottom of a short length of steel electrical conduit tubing an inch or two below the top surface of that fender, and this was called "recessing" the antenna, albeit the process being very much like "tunneling" as described above. This also referred to the idea of setting taillights slightly into the rear corners of a customized body, while the concept of setting say, '59 Cadillac "bullet" taillights deep into the sides of the rear quarters, say on a '46-perhaps ;52 or thereabouts GM car, certainly on a '49-51 Mercury or Lincoln, where the fabricated "tunnel" as described above was deep only on the inner edge, with the outer edge necessarily exposing a lot of that taillight lens. Actually by the 60's, this term, "recessed" became somewhat synonymous with "tunneling"/ "Frenching" referred to the technique of blending in headlight bezels with the surrounding sheet metal, by the use of lead (when headlight bezels were stamped steel) and catalyzed body putty when Detroit began transitioning to diecast white metal bezels). I believe this term hearkened to the looks of French custom body companies, such as Saoutchik, who created numerous voluptuously styled custom bodies for luxury cars such as Delahaye, etc. in the years immediately after the end of WW-II. Frenching was also used with taillights in many cases as well--but in any event, the technique was used to create a smooth, coachbuilt look as opposed to multiple separate parts assembled on a factory assembly line. Hope this helps! Art (whose been around since 1944!) -
Remember when?
Art Anderson replied to Porscheman's topic in General Automotive Talk (Trucks and Cars)
Growing up in West Lafayette IN, in the 1950's, I had all manner of choices: Cridercraft Hobbies at the bottom of State Street Hill (5 blocks from home), Stroebel's Variety store in "The Village" (our little business district just to the east of the Purdue University Campus--but the real prize came when I discovered Bell Auto Supply in downtown Lafayette (just across the Wabash River of song and legend)! That was THE mother lode of model car kits for me, all the way through HS. Of course, nearly every supermarket and drug store carried at least some model kits--had my parents not restricted my available spending money I'd have spent all of it on model car kits back in the day. Art -
The overspray on the underside of car bodies in the 50's through the 70's or early 80's came about because of factory practice in the days before robotic spray painting (and when the vast majority of American cars were built body-on-frame). In June 1960, as a 15yr old, just out of school for the summer (finished my Sophomore year in High School), I took a trip (earned by selling subscriptions to the Indianapolis Star as a paper boy) to St Louis, Missouri. During that week in St Louis, one of the highlights was a tour of the Chevrolet Assembly Plant, which then was the largest, highest production automobile assembly line in the world. There we kids got to watch a new 1960 Chevy being built, all the way from a bare frame, and for the purposes of this discussion, the body itself go from bare sheet metal stampings to painted and trimmed, to a finished car. The group of paperboys I was with followed a '60 Impala convertible on both lines (body, and final assembly), and it was where the body shell was painted that this description comes from: We didn't get to see the body shell being welded up (Chevrolet certainly didn't want to shell out for a bunch of kids getting their eyes damaged from watching welding without goggles or welder's shields!), but saw the raw body shell go through painting. The body shell (1960 Impala Convertible) was lowered onto a heavy cart, which positioned it about 2 feet above the factory floor, on iron wheels, and pushed by hand into the paint room. There, a team of three workers attacked it with ordinary spray guns, each hooked to a double set of hoses, one for the Roman Red Dupont acrylic lacquer, one for compressed air), Two painters sprayed the sides (one worker painted the firewall, a second the rear panel and underside of the trunk lid) while a third worker sprayed all the upper surfaces. The two painters spraying the body sides and ends, as they worked, ducked down with their spray guns, and sprayed the bottom sides of the rocker panels (on that era of Chevy, the rocker panels are about 4" wide, and about 2" below the underside of the floor pan) to get color coverage there. That step alone meant overspray along the outer edges of the floor pan, memory telling me that the overspray extended perhaps 8" in from the sides of the bottom of the body shell, as well as across the front of the toe board at the bottom of the firewall (no such overspray at the back, as the rear splash apron was not installed at this point in assembly). Chevrolet, at this plant at least, used red oxide primer, which was applied by dipping the entire body shell into a huge vat of primer--this was not sprayed on!. Within mere minutes, the body was pushed to a conveyor, which carried it into a long baking oven (LOTS of infrared light bulbs, in a long tunnel), which process took a good 20 minutes or so to traverse, during which time we were shown the masking and second color paint steps while our convertible was being baked dry. Fast forward to June 1970: I got a call at work one morning that my newly ordered 1970 Barracuda was being delivered to Fireproof Garage in downtown Lafayette. As I was the assistant manager at Weber's Hobby Shop then (plastic model and HO model trains buyer, among other things), I hustled over to the dealership (2 blocks south) in time to see my Barracuda on the haulaway. I clearly remember seeing the overspray on the bottom of that car as well--pretty much as it would have been on that Chevy body back 10 years earlier (Rally Red over grey primer), so little had changed in factory practice). Now, when I watched my 1990 Plymouth Grand Voyager being prepped for me at Twin City Dodge-Chrysler-Plymouth in April of that year, I first saw that car on a lift during prep--the entire underside was a nicely finished in the darker metallic blue as the lower body sides, evidence I suspect, of robotic painting, so there was no color overspray on the bottom of that unibody. But in any event, the overspray on the underside of those earlier body-on-frame cars wasn't much more than 6-8 inches in from the sides, NEVER reached up into the rear wheel wells due to the lower, skirted wheel arches in the rear, and NEVER on the frame rails (as all this was done before the body was delivered to the body drop area). Art
-
Tamiya over Testors?
Art Anderson replied to johnbuzzed's topic in Model Building Questions and Answers
No reason why not! Both Testors Model Master lacquers and Tamiya lacquers are non-penetrating formula. I've used both interchangeably, with no detrimental results. Art Anderson -
Interior colors for WWII airplane
Art Anderson replied to my80malibu's topic in Model Building Questions and Answers
Testors #1184 is the correct Zinc Chromate primer color for WW-II US Military aircraft (in fact, correct for metal US aircraft from the early 1930's through the early Century Series era of jet aircraft. It's a rather garish yellow-green flat finish color, and was applied all over aluminum aircraft, inside and out, before any camouflage colors were sprayed on. Standard for US Army Air Corps, US Army Air Forces, and US Navy. Find it in the rack of those little square 1/4 ounce bottles--never was available in spray cans, though! Art -
If there is any interest, I took a full walkaround series of pics of a real '57 Ford Custom 2dr, restored and appears very factory correct, at the GoodGuys Rod & Custom Show at Indianapolis Motor Speedway back in September! Art
-
Cool cars your grandparents owned
Art Anderson replied to Fat Brian's topic in General Automotive Talk (Trucks and Cars)
I never got to know either of my grandfathers, as Granpa Jacoby died in 1935, and my Grandpa Anderson passed away in 1940 (I came along in July 1944), but both grandfathers started out driving Model T Ford touring cars in the 'teens--Grandpa Anderson's 1913 Model T having been the subject of MANY stories from my Dad, who was 9yrs old when it arrived on the farm north of Chase IN that May. (Tonka produced a neat 1/25 scale kit of this car in their "Tonka Diorama Series" which came out in 1975--two cars in that series, the Model T Touring, and a kit of the 1903 Winton Runabout which made the very first transcontinental run, from San Francisco to New York City in 1903). I have a couple of those kits in my build pile--so ONE OF THESE DAYS! My Grandpa Jacoby was the Delphi Indiana dealer for Star automobiles (produced by William C. Durant, founder of GM after his second ouster as GM President in 1922), and then reverted to Fords once more. But there's more, at least from my extended family! Perhaps the most legendary (both from the history of the automaker, and from family stories!) is the 1925 Essex Four Coach ("Coach" was the name attached to 2-door sedans back then!) in which my Uncle Chuck (Charles Groninger) dated my Aunt Kathaleen and drove on their honeymoon in 1931. According to Uncle Chuck, he was the only person to ever have driven this car before he gave it to his younger daughter, my favorite cousin of all in 1990 (Uncle Chuck NEVER knew that my Grandfather--his father in law--stole a surrepticious drive around Delphi IN once!). The car still exists, complete with a half-empty box of vintage condoms, found there by his 16yr old grandson in 1992!) This is what that year Essex Coach looked like: Essex, a lower priced make from Hudson, popularized the closed, two-door sedan very quickly, both Ford and Chevrolet adopting this body style quickly, and by 1926, Model T Tudor's outsold open touring cars by a wide margin. In the fall of 1950, when I was in first grade, My Uncle Harold (then having lost his factory job in South Bend when the company closed up) moved his family to rural Lafayette, and Dad located for him a 1935 Hudson Terraplane--which was Hudson's performance car of the 1930's--I seem to recall that car as having been the supercharged model--it would move out!. As a boy growing up in the shadow of Purdue University in from 1944 into the early 1960's, I got to see all manner of cool cars! Most of the really neat ones were owned by Purdue students, coming out of Military service and studying under the GI Bill. Many of those who had served in Europe in the late 40's and early 50's brought home some pretty exotic stuff for the time: Many what we would today see as Classic Cars (in the sense of the Classic Car Club of America), such as Alfa Romeo's, Mercedes Benz's, Rolls Royce's, and more modern cars--I still remember the very first Porsche 356 I ever saw, probably about 1956--that car had no muffler, and with its gearing, the flat four aircooled engine--sounded like it was going 100mph just starting out in 1st gear! In 1955, Dad rented for the winter, a hitherto never used stall in our garage to a Purdue Student, who needed winter storage for his 1933 Alfa Romeo roadster! But, the real piece' de resistance? My Mom's 1932 Chevrolet Confederate Coupe with rumble seat, that she bought new in '32, and drove through the end of the summer of 1950 (she maintained that car meticulously!). Imagine the looks I got from my Kindergarten and 1st grade classmates, when on nice days, I got to ride to school in that rumble seat! Unfortunately, I have no pictures of that car for some reason! Art -
The Stutz revival car, while using much of the lines of the original Exner renderings, really isn't done exactly as Virgil Exner designed it though, due as much to its having been introduced several years after Virgil Exner Sr's death in the late 1960's (the pontoon shaped front fenders with 'bubbled" clear plastic headlight covers being the principal change--headlight covers were not allowed on US spec automobiles for many years). There was a fourth "Exneresque" revival car proposed for production, the 1966 Duesenberg from a new, startup company, The Duesenberg Corporation, which used a lot of Exner themes though. Just one prototype was built, on a Chrysler Imperial platform, bodywork again from Ghia--for showing to potential investors in the company, as well as to prospective buyers. The Duesenberg Corporation even enlisted Fritz Duesenberg, son of Augie Duesenberg--brother of the legendary Fred Duesenberg, himself the designer of the famed Duesenberg Model J of 1929-37. Fritz Duesenberg was made an honorary director of Duesenberg Corporation, but took no actual role in that company--he was in rather poor health, and by the early 1970's, was a resident of the Indiana Soldiers Home (now Indiana Veteran's Home) at West Lafayette IN, and passed away there in 1976, having been virtually an invalid ridden with arthritis for several years. This car never reached production, as not enough investor interest resulted in capital needed to start making them for sale. 1966 Duesenberg Model D: This car still exists, on display at the Auburn-Cord-Duesenberg Museum in Auburn IN, resting there in company with several actual Duesenberg Model A's, a Model X, a Model Y, and a nice collection of Model J's. Of the two exact copies of Exner's Revival Cars, the Mercer-Cobra, and the Bugatti Type 101C, the Bugatti comes forth as the only car ever built EXACTLY as Exner intended, given his ownership of one of three Type 101C rolling chassis, and was built to his instruction by Ghia for his personal use. The Mercer became the Mercer Cobra, built under commission for the American Brass and Copper Institute, a trade organization of companies producing brass, copper and bronze products, as a means of proposing to the auto industry the use of polished brass, copper and bronze trim on automobiles. As such, it was built on a stretched 289 Cobra chassis, but is probably a bit smaller than what Exner might have envisoned originally--but it sure does capture very well the concept as Exner intended. I have a couple of each of those in my build pile still--one of these days! Art
-
Hobby shop name stealing?
Art Anderson replied to Howard Cohen's topic in General Automotive Talk (Trucks and Cars)
That sort of thing has happened over time in the US, of course--and not limited to hobby shops. While of course, I know next to nothing about Canadian law, but in the US, it is possible to register a trade name at both the state and federal level. If a hobby shop owner doesn't do that, he or she does stand to lose the exclusive use of that trade name. But yeah, on the face of it, it almost sounds as if the owners of this new hobby shop are perhaps pirating a known store name. Art -
F-1 has always had a US fan base, but it's always been quite small--and I somehow doubt that is going to change anytime soon. Consider this: In the US, there is more racing action happening in any one series than in the entire rest of the world. All one has to do is to consider the sheer number of racetracks, of all sizes and shapes in the US, and the sheer number of types or race cars, to understand why with the exception of NASCAR, none of the others are even close to dominant. Art
-
This is true of any creative pastime, model cars included. It's been shown, time and time again over the years, that anything which stimulates learning, and creativity stimulates the brain. In fact, there was a neat article in our local newspaper about Purdue students working with Alzheimer's patients on art projects--allowing them to draw, paint, sculpt--and the results so far are interesting to say the least. Art
-
Look at a fabric store (or Michael's or Hobby Lobby) for the type of ribbon known as "grosgrain" (pronounced "grow-grain"), which is a slightly coarse but tight weave, and in miniature, can be very convincing for racing seat belts. Grosgrain ribbon, due to its weave pattern, is also quite flexible, so it can be made to lay down pretty tightly, with a bit of contact glue on the back side. Another source for this type of weave is Dermicil Surgical tape (the stuff used in hospitals, and Dr's offices. Some professional pharmacies sell this stuff, but I've not seen it in Walgreen's or CVS for a long time. Art
-
Bowl fuel filters - resin - scratch?
Art Anderson replied to Daf57's topic in Model Building Questions and Answers
That's both a fuel filter, of sorts, and more importantly, a water trap (notice the drain petcock on the bottom of the glass bowl). Now how to make one that looks realistic? I can think of how I would do it, of course! Step 1) While it is possible to find transparent acrylic plastic rod as small as 1/8" diameter in craft stores such as Michael's or Hobby Lobby, it might be quicker to use a length of sprue, chucked in an electric drill. Simply start the drill, and use a needle file to cut down the sprue to 1/8" diameter (most of those moisture traps I've seen over the years have bowl approximately 3" in diameter, which is pretty much right at 1/8" for a 1/25th scale part. I'd use the regular colored plastic sprue for this, as clear styrene is quite brittle. Simply file the spinning bit of sprue with a needle file to get the diameter and shape, then polish as smoothly as you can make it. Step 2) Get a tube of DAP Silicone II clear sealer (the stuff you can get to seal the corners of a plastic shower stall to keep water from leaking behind it), squeeze out a good sized blob of the stuff onto a disposable surface, such as a piece of stiff cardboard. Grease up your shaped bit of sprue with a bit of Vaseline but wipe it smooth, to make the "master" easily removeable from the Silicone II once it has dried, and push that into the blob of Silicone II, and allow it to dry and cure out completely (overnight). Step 3) Use some clear epoxy gluje (2-part), mix that up carefully so that you don't mix airbubbles into it, and with a toothpick, fill the hole in the cured Silicone II with the epoxy and let cure completely. Now you can remove your clear part, file the blunt end as square as you can, and glue to the body of the moisture trap, which you will have to scratchbuild from a bit of sheet styrene, with a length of styrene rod stock to make the fuel passage that goes across the top of the unit. To make the clear "bowl" show up really clear, brush a fairly thick coat of Tamiya clear water borne acrylic enamel on the clear bowl--or if you wish to give the effect of leaded gasoline, use Tamiya Clear Yellow waterborne acrylic. Art That would work as well! Especially the yellow LED! Art -
Renwal closed up in the late 1960's or early 1970's, one of the original makers of plastic toys and hobby kits. Some tooling was bought by Revell (Renwal was the original mfr of the "Visible V8" kit for example). Some model car kit subjects from Renwal made it into Revell's lineup, notably the 1/12 scale '65 Mustang Fastback and the 1/12 scale Mercedes Benz 300SL Gullwing coupe, along with much of the armor kits that Renwall produced in the late 1950's. Some other Renwal tooling was acquired by Glencoe Models as well. As for the "Revival" series of car kits--those started in the mind of Virgil Exner Sr., who was the chief stylist at Chrysler from 1953-l962; as renderings for an article about what the great Classic Cars of the 20's and 30's might look like in 1966 if still in production (Mercer, Stutz, Duesenberg, Packard, Jordan Playboy, Bugatti), in Esquire Magazine about 1964 or so. Two of the designs were actually built as real cars: The Mercer-Cobra, coachbuilt by Ghia on a 289 Cobra chassis for the American Copper & Brass Association (all the trim, and the cast wheels, were in copper, bronze and brass), and the Bugatti 101C also got coachwork by Ghia on one of just 3 or 4 T101C chassis & drive trains that Exner spotted on a visit to Molsheim in eastern France in the late 1940's, buying that rolling chassis from Le Patron himself. Both cars still exist today, in the collection of General William Lyons USAF Ret. in California (I've seen both cars, and they are stunning). Renwall introduced those Revival kits in either late 1965 or early 1966, but they were notoriously poor sellers--several hobby wholesalers still had unsold stock of them well into the early 1980's, believe it or not. I think it's doubtful that even if the tooling could be found, they'd do very much in the marketplace today. Art
-
My first reply to this was a bit too brief, and a bit too flippant: Most people assume that when a model kit tool is seriously modified, say as in the case of the pickup kits that were converted from stock configuration to monster or crusher truck model kits, that the original steel dies were merely re-cut. In all likelihood that was not the case; rather it's more than likely that new inserts for the body molds were created for the altered wheel arches, etc. To explain this more thoroughly: To create the tooling for a one-piece body shell (car body, truck cab for instance) requires a series of movable sliding "core molds" that in the injection molding process, move inward to close up the body mold, and then once the molten plastic has been injected and has cooled to solidify, slide back or outwards to release the molded shell so that it can be removed (ejected) from the mold. That's where all those mold parting lines we modelers love to hate come from. For almost any one-piece body or truck cab, it takes at least six sliding cores to mold it: Inner core (inside surfaces), front core, rear core, right side core, left side core and upper core. Now, if only say, the body sides are to be changed as dramatically as with the monster truck kits, just the two side sliding cores need be changed--given the nature of hardened tool steel, that's not easily done, so more than likely new side slide cores and a new inner core mold were created to fit the original body tooling. The question then becomes--do the original slides that were changed out still exist (likely they do) and if so, are they in a usable condition today? IF they were preserved with a coating of cosmoline then likely yes, if not, rust likely will have made them unusable today. Next comes the job of finding all that stuff: While the main mold bases probably are readily identifiable, a lot of the tooling inside them was done as "inserts", smaller steel blocks engraved to make various parts, and those may well have been removed, replaced with newly cut inserts for subsequent versions. Finding and identifying those could be a major problem, particularly for AMT tooling, given that AMT's tooling has changed hands several times over the past 35 or so years, and been moved at least three times over hundreds if not thousands of miles (from Troy MI to Baltimore MD, then to Dyersville IA, and now to South Bend IN) and most all of it was made before the introduction of computer databases to track all those various bits and pieces of tooling--even the internal "house" codes used to ID a lot of those changed several times--it now becomes a matter of someone who is knowledgeable about this stuff to literally sort through probably several hundred tons of tools (those old original mold bases weigh at minimum, at least a ton apiece--you aren't just going to pick one up with your bare hands, open it up to see what's inside), and all those extra tool inserts are likely in a myriad of heavy wooden crates as well. This means literally looking at each and every bit of tooling, and identifying them as to what subject they truly are. All of this is the basis for my earlier comment that it may well be less expensive to simply make all new tooling than to try and rehabilitate something cut decades ago--meaning that in either case, it is likely to be a major investment. Art
-
I've used straight pins more than a few times to make really durable radio antennae (back when those were always mounted on the upper rear corner of the right front fender panels), by drilling a hole in the fender, putting a little drop of epoxy on top of the fender, then pushing the pin (with head clipped off, and the cut end smoothed down, to give a "base" to it. I then clip off the sharp tip, and put the tiniest drop of epoxy on the end--which when given a drop of silver paint, makes a perfect ball-tip to the antenna. On the second of the '50 Olds kits I am working up right now, ball-head straight pins will get the call for "curb feelers", those spring steel, ball tipped pieces of plated steel rod that were used to warn a driver that he was getting close enough to a curb when parking, to scuff his whitewalls. Art
-
MIke, actually it would cost more money than you might think--in fact, you could prolly buy a couple of top-end Corvettes for what it might cost to rehabilitate some of those old tools, particularly if major elements have to be re-cut. Far too many people think that to put an old tool back into shape for new production is as simple and cheap as duck soup--but I am here to tell you that it is not that way! Technology, be it 21st Century or something harking back to what some people today think of as the dark ages--it will cost $$. Now the question becomes: "Do you want to see the same old, same old kit from 40-50 yrs ago, or would you rather see something done as state of the art 2012?" You can think about that, then answer. Art
-
HAPPY BIRTHDAY, MARINES
Art Anderson replied to crazyjim's topic in General Automotive Talk (Trucks and Cars)
My favorite uncle when I was a kid growing up was a Marine in WW-II. So, Uncle Charlie, this is a shout out to you--93 yrs young and still going! Thank you for your service, and the fact that you (and your buddies) did what you did for then-little kids like me! Art -
Models in the movies
Art Anderson replied to ReptileGuy's topic in General Automotive Talk (Trucks and Cars)
Models of cars have played a huge role as props in Hollywood movies over the years. Starting in the late 1920's or early 30's, studios hired model makers to create exacting miniatures of cars, mostly in larger scales, such as 1/10, 1/8, even in 1/6 scales, for studio shots of street scenes, even crash scenes. Today, whenever someone puts up one of those survivor studio models for auction (forget eBay, or Barrett-Jackson--try Sotheby's or Park Bernett) they bring MAJOR dollars. Art -
Models in the movies
Art Anderson replied to ReptileGuy's topic in General Automotive Talk (Trucks and Cars)
AMT never kitted that Porsche--however, Revell did a slightly later Porsche racer, way back about 1959. Art -
New guy on here
Art Anderson replied to wheaton79chris's topic in General Automotive Talk (Trucks and Cars)
Just ask the question (whatever that might be) and more than likely you will get more answers than you can shake a stick at! Welcome to the fun! Art -
Jesse, allow me to share what I know of the demise of Aurora tooling here: First of all, I (along with Professor James D. Russell, School of Liberal Arts & Education at Purdue University in West Lafayette IN) were both heavily involved in doing both box art and trade show display models for AMT Corporation at the time, and had made a trip to AMT, at 1220 Maple Road in Troy Michigan to deliver several built models to AMT. Once we'd completed that mission, we drove the approximately 1.5 miles or so to the offices of MPC, in Mount Clemens MI, where we met Tom West (then the Product Manager for MPC and MPC-Lionel Trains), to discuss the possibility of our doing for MPC what we were doing for AMT. Now, this was a year or two after Aurora had shut down, Second, from 1981-89, even though I live in Lafayette IN, I was a member of Lake Michigan Model Car Club, then meeting at the Village Hall in Western Springs IL (SW suburb of Chicago), then and still, the oldest model car club in the US and likely in the World (started in 1951 as the home chapter of International Association of Automotive Modelers -- IAAM). Several members of LMMCC were employees of Monogram Models. One of those was the late Jack Willer, then a pattern maker for Monogram Models, and he gave me the most plausible explanation of what happened to all the Aurora tooling that has apparently disappeared: Now, to preface this: For those old enough to remember clearly, the model car kit industry was seriously on the skids by the late 1970's, and the Reagan Recession of 1981-82 was pretty much the Hurricane Sandy for the industry, and also our hobby. During the Christmas 1981 shopping season, I was astounded to see, in the Marsh Supermarket where my now Ex- and I shopped for groceries, a massive pile of Monogram model kits, easily the volume of two 48' semi trailers, all priced at about half the then-normal retail price for model car kits. The market for model kits was THAT BAD. In fact, during the first quarter of 1982, Lesney-AMT shipped the grand total of 6000 model kits (which was lower than abysmal). The situation was just as bad at Monogram, and Revell. The Aurora tooling, according to Jack Willer, was all received at Morton Grove, in varying condition (and Jack never mentioned any damage due to accidents in shipping!). Aurora, as with several other model kit makers in the 50's and 60's, did all their tooling in "beryllium-copper alloy", which was more easily cut by the then-common milling operations used. Now, beryllium is at the level of a precious metal, not unlike silver or gold, and copper has been, and certainly is today, nearly a precious metal. Given the dire situation that every model kit maker in the US faced in late 1981 and early 1982, Monogram saw but one choice, sell the tooling that they could no longer see as making saleable product for scrap. Most of it was stuff that Monogram management determined was not up to the very high standards they'd come to expect (and that model kit buyers also had come to expect as well from Monogram), so that was the tooling that got scrapped. Jack Willer went on to tell me that this was one of the principal things that saved Monogram, and I for one am happy that it all worked out. Now I know all about the stories of a train wreck, and the more fanciful tale about the tools being loaded on a ship to travel the Great Lakes from the St Lawrence to Lakes Ontario, Erie, Huron and Michigan, to Chicago, and a shipwreck, but even Jack scoffed at that. Jack's story of what happened is the one that has always had the most plausible reputation--I knew how bad it was in the industry in that 6 months or so, having held a 1" pad of legal documents detailing the Lesney-AMT bankruptcy (I was a creditor to the tune of almost $3,500 for unpaid invoices for built up models--I did get paid, in late August 1982, in full with interest!). But this is what I know and believe to be true. Art Anderson
-
1950's diesel engine source?
Art Anderson replied to Chuck Most's topic in Truck Aftermarket / Resin / 3D Printed
Check me if I'm wrong, but weren't the majority of Detroit Diesels in the 50's inline engines? That's where Detroit's started in the very late 1930's, inline 2, 3, 4, 6 and 8 cylinder engines. I want to think that Vee-block Detroits began appearing in the late 1950's. Art