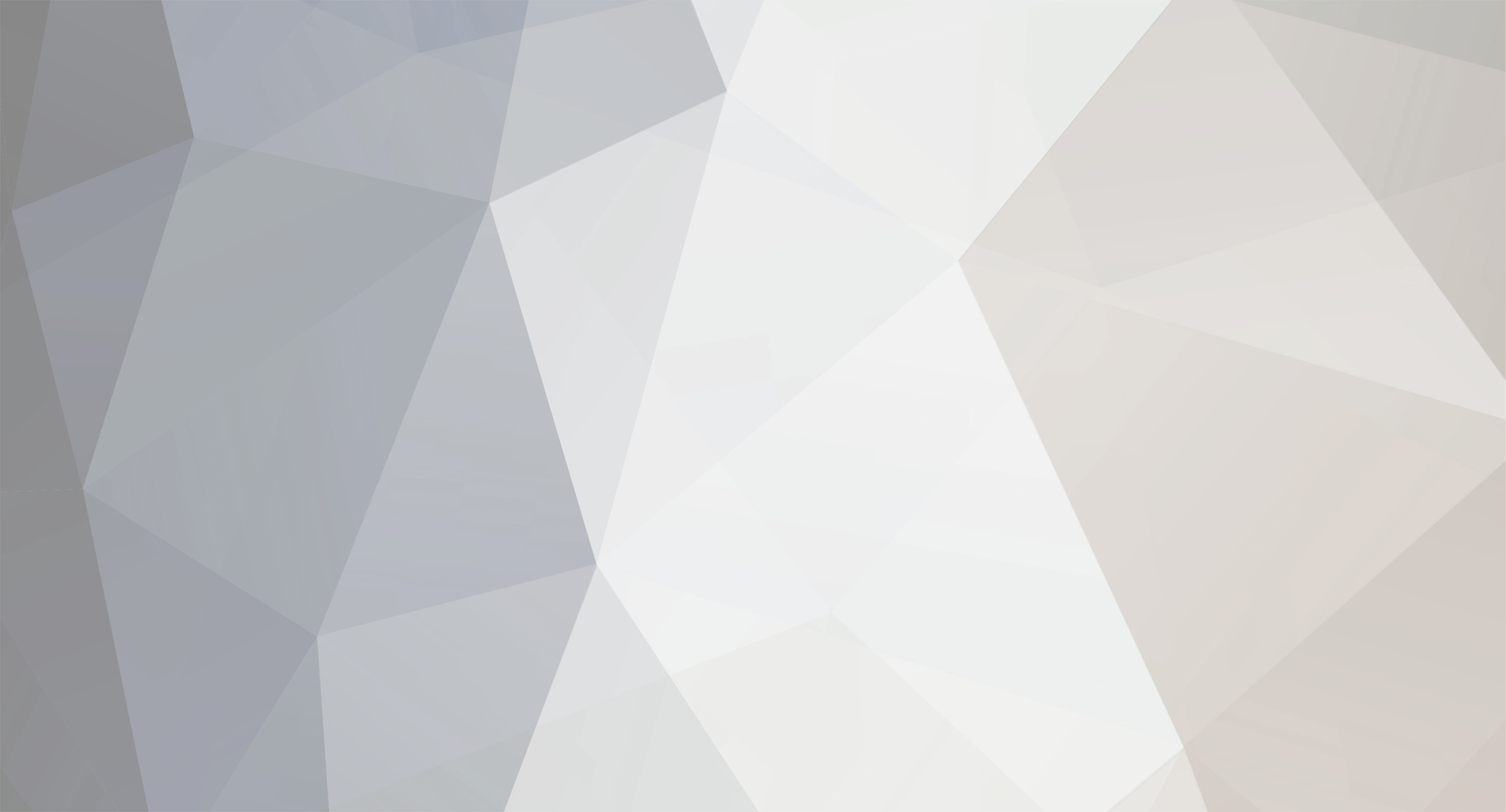
Art Anderson
Members-
Posts
5,052 -
Joined
-
Last visited
Content Type
Profiles
Forums
Events
Gallery
Everything posted by Art Anderson
-
JO-HAN Molds?
Art Anderson replied to gbdolfans's topic in General Automotive Talk (Trucks and Cars)
To begin with: JoHan, compared to the really big operation that AMT Corporation once was (in the 60's, AMT was producing 10's of millions of model car kits every year!) was really a quite small company. John Hanle, the founder and owner was, from all I have been told, very much a "one man band" much of the time--a highly talented modeler (Hanle was known for his hand carved collection of 1/72 scale WW-1 and WW-2 aircraft, which collection was displayed for several decades in the USAF Museum at Wright-Patterson AFB in Ohio), who did work on a lot of the mastering for the model car kits bearing his name. I've also been told by a couple of model car personalities who actually worked for JoHan for a few years, that his injection-molding machines were rather primitive, dating from the early days of injection-molding during WW-II. While JoHan produced a lot of subjects that would be quite popular today, it's wise to remember that in the 1960's, kids were not enamored with model kits of AMC Ramblers, Rambler Americans, Cadillacs, full-sized Oldsmobiles, Studebaker Larks. Likewise, while HARD to believe today, Plymouths, Chryslers and DeSoto's were pretty low on the popularity scale with the kids who were the 1960's primary market for model car kits. This factor alone dictated that for the most part, JoHan kits were pretty low on most 12-16yr old model car builders' radar screens. Add to this that JoHan NEVER displayed at any of the Hobby Industry Association of America trade shows back then either (I was at every HIAA trade show from 1964 through 1986, and JoHan was always conspicuous by their absence. Again, more reason why JoHan never achieved the level of visibility, of marketability that the "biggies" such as AMT, Revell, Monogram and even Aurora enjoyed back then. JoHan's injection molding presses, being as obsolete as they were by 1960's standards, also were much smaller machines than those in use at Revell, Monogram and AMT, which presses could handle injection molds that were approximately 24 X 48 X about 18 inches, all solid blocks of steel (with just a few "inserts" which were the tooling for wheels and of course the sliding cores for molding one-piece body shells). JoHan also apparently insisted on using a fairly valuable alloy for tooling inserts in their molds, beryllium copper (an alloy used a lot in Europe as well). While a fairly hazardous metal, beryllium is in the range of semi-precious metals, and as such, those inserts had a pretty high scrap value. In addition, so I've been told, Mr Hanle could be a rather difficult person to work for, which apparently lead to a lot of dissatisfaction and hard feelings among his employees (and allegedly many of his production workers didn't come from the best side of the tracks either). As the story goes, apparently a number of fairly small tooling inserts (those beryllium copper inserts had to be press fitted into steel mold frames or blocks, and could be changed out rather quickly) disappeared, more than likely in someone's lunchbox at the end of the shift, and found their way to any one of a number of scrap dealers in the area. This would seem to explain the missing tooling parts that have been mentioned many times whenever JoHan is discussed. JoHan was not alone in the realm of missing tooling inserts. At a Mike's Miniature Motors Model Car Swap Meet in Waukesha WI in 1994, a customer appeared at my table (AAM), and invited me to take a look at some model car injection molding tooling, should I be interested. What he had were about a dozen sets of "wheel hobs", the inserts AMT used to mold the outer and inner halves of wheels (these were a light press-fit into the much larger steel mold frames that AMT traditionally used). I have no idea today just what wheels those were , but in any event, I excused myself and went back to my table, as there was no practical way of my using them for anything other than paperweights. As an aside here, all too often modelers assume that a model company can just change out this part or that almost willy-nilly, but that's far from true! That can only happen IF the kit tooling was designed and built, from the get-go to have the potential for such changes in subsequent runs of product. Art -
JO-HAN Molds?
Art Anderson replied to gbdolfans's topic in General Automotive Talk (Trucks and Cars)
What you see are tooling "inserts", which had to be placed into a much larger mold base (or frame, if you will). AMT, MPC, and I suspect even Monogram and Revell used essentially the same sort of system. Art -
The quick way to tell if your resin is "polyester" is the odor of it. Polyester resin will smell just like the 2-part body putty used in shops that repair dented sheetmetal on real cars--that putty is polyester based. I'm pretty certain that you can access urethane or polyurethane resin in The Netherlands--there is quite a bit of resin casting done in Europe for model builders. Art
-
Ben, I had forgotten about fiberglas (polyester) resins! That's likely why the resin refuses to cure out "click hard" on the surface in contact with the rubber mold. Silicone RTV rubber will "leach out" the hardener from the resin in contact with the mold, leaving a thin layer of sticky, uncured resin right there. Years ago, like 30-35 years ago, I tried making model parts from polyester resin, and nothing I did would solve this problem. Polyurethane resin, say such as Alumilite, doesn't have this problem. In addition, a large, fairly complicated thing like the Merlin engine is far better cast as separate parts, just as they come in the plastic kit from where it came. That way, there are no vents that need be added to the molds, and no unsightly marring of visible, exposed surfaces either. Art
-
Your resin appears to have pretty serious moisture contamination--that is what causes those bubbles throughout your casting. That's indicative of a container that did not seal properly, or old resin. Urethane resins are hygroscopic, meaning that in liquid form, they can and will absorb water vapor out of the surrounding air. I'm afraid your batch of resin may be rather liquid toast. Speaking as one who's had that very thing happen a couple of times in my 12 years of resin casting, that's what I am seeing. Art
-
Kurtis Kraft Midget
Art Anderson replied to Fortheloveofgassers's topic in Model Building Questions and Answers
The kit tires are pretty accurate replica's of mid-late 1950's Firestone Deluxe Champion dirt tires, but without Firestone lettering and logo's on them. Art -
Riprap Machines for detail?
Art Anderson replied to Chas SCR's topic in General Automotive Talk (Trucks and Cars)
All very nice indeed--but not yet something that even a significant minority of model car builders are going to adopt, I'm afraid! Art -
2012 iHobby show - Round2 2013 Announcements
Art Anderson replied to Tom Kren's topic in Car Kit News & Reviews
Dave, you have it very, VERY RIGHT! A trade show is just that, a trade show. Now, let's take a look back at hobby industry trade shows in their heyday (and that was decades before RCHTA (Radio Control Hobby Trade Association and "iHobby": From the 1930's until its breakup, it was the Hobby Industry Association of America (HIAA), and their annual trade show began on the 3rd Sunday of January, EVERY year, held in Chicago (for the first 40 yrs or so, Chicago and Suburbs was THE epicenter of the hobby industry, and Chicago was the heart of hobby wholesaling (Companies such as Trost Modelcraft & Hobbies--where I first got to know the late Bill Lastovich, United Model Distributors, Midwest Hobby Supply, Walthers -- the train people--were just up the road in Milwaukee, Sig Manufacturing--balsa and airplane kits was a couple hundred miles west in Iowa, Midwest Model Products in Hobart IN). With the exception of Revell (California back then) and Aurora (West Hempstead NY), the major plastic model companies (certainly in the model car field), AMT, MPC, JoHan, Monogram were all within 250 miles of the Windy City. Chicago was the most centrally located city in the US with tremendous access by road, railroad passenger trains, and airlines (even Greyhound and Trailways). Those early HIAA shows were held in downtown Chicago (the Loop), at the former Sherman House Hotel, where they took up every ballroom, meeting room, banquet room in the building. HIAA shows opened at 8am sharp on the 3rd Sunday in January, to a literal mob scene (pretty much equivalent to a movie premiere in a basketball arena).. Hobby dealers from ALL OVER the country were there. There was no public admission--one had to be a "member of the trade" in order to gain admission. In the spirit of a true trade show, deals were offered, and deals were made back then, at HIAA (the show continued through the coming week, with serious buys being made by anyone who was a buyer for a hobby shop, department store, even chain stores. There were no "advance showings" back then (today, trust me, the relatively few hobby wholesale houses and buyers from large retail chains stocking hobby or model kits will have seen the new announcements well in advance of iHobby or the NY Toy Fair!). From the first of July 1964 through the middle of August 1973 (with leaves of absence in the summer of 1966, 1967, and the 12-months from June 1969-May 1979) to finish my college degree, I worked for Leo and Berdina Weber and alongside their younger son Mike, here in Lafayette--Weber's Hobby Shop, then one of largest, most comprehensive hobby shops in the Midwest outside of Chicago or perhaps St Louis. In pretty short order, I became their plastic model kit and HO model railroading buyer (subject to Leo's approvals, of course!). So, by the time I was 20 years old, the Weber's annual trek to HIAA was when I became a young man on a mission--to scope out all the new announcements (and they were many!), and with Leo's guidance, putting together my recommendations as to what (Weber's would stock most anything in hobbies--at the minimum of "onesy-twosy" to case lots of kits I was convinced would sell very well. So there I was, only a couple of years out of high school, rubbing shoulders with not only other hobby dealers from all over the US, but also marketing guys, design/product development people, you name it--I had to be the one to dig into newly announced product lines, determine was being carried over into the new year, learn what the projected release dates were--in short, see all the glitter, glamor and excitement, but also learn enough to be able to tell my boss what we should bring into the store in the areas of my interest and knowledge. (Sure, I made my mistakes over those years, but Leo would always remind me of Green Monkeys--he kept telling me he had to have been drinking Green Scotch when he ordered in those things in the early 1950's!). By 1967 or so (the year the HIAA Show was nearly called off by the Great Blizzard that year, I found myself having to sign pre-orders based on what is called "Open To Buy" (a dollar amount that a buyer is authorized to commit to on behalf of his company/employer). Looking back, even though that notion really frightened me at the outset, Mr. Weber was more than supportive, and if I made a mistake, ordered in something that didn't sell well, or too much of something, he was entrepreneur enough to cover my rear end, and help me look good (something for which I will always remember him--my mentor for sure!). But the bottom line is, that is what a classic trade show was all about--and there were some funny, certainly interesting things. Take the AMT Peterbilt 359 "California Hauler" for example: AMT first offered that, based on a box art painting, at the 1968 HIAA Show--not enough interest, so it didn't happen. 1969, same painting, same result. 1970 (and the Webers paid for a hotel room so that I could come in from Iowa--where I was a Senior at Parsons College at Fairfield) so I could be there--it was very apparent that the Webers, Father, Mother and Son, wanted me back as soon as i graduated --in fact they matched the starting salary I could have wangled from even a Fortune 500 Company to achieve that!), and what did I see? The IMC Dodge COE, AND a hand-built prototype of the AMT Peterbilt 359 California Hauler! Now that was how things often happened in the industry back then. w But, a trade show should be a trade show, first and foremost--and both RHCTA and iHobby pretty much forgot that, if they ever knew it. When Hobbico sets up to sell to hobby dealers on the early "Trade Days" and then quickly takes down the Hobbico sign and plasters up "Tower Hobbies" for the general public to see on Saturday, well who does that offend? Yeah, your LHS. As a result, more and more, LHS owners simply have ignored iHobby and its predecessor, RCHTA--why should they go, and see their arch-competitor right in their face? And, along those same lines, with the internet and a website, why does a model company even need to show up at iHobby, get exposed to a very limited audience of very mixed interests, when they can, as did Revell and Moebius, hit NNL and the Collector's Toy Fair in Sylvania, and reach an audience specific to what they were announcing? Hmmm? Art -
My bottom line is this: It doesn't matter one whit to me just how a model was built, be it a putty custom or one having a completely scratchbuilt body, for example. Same with the engine, the other greasy bits, the interior. It is, however, the "end result" that counts. We each have our own favored techniques, be it in modifications, construction, detailing and trim, even paint work---is any one trick or process necessarily better than all the others? IMO, no. It's what the builder winds up with that matters, that is all any spectator can see, and even all that any contest judge can see. I had to wonder about the concept of "Degree of Difficulty" consideration that reared its head several years back--that becomes, to me as rather severely subjective when I think of it. Does it really matter if a builder used real silk, or silk made out of a sow's ear? Art
-
I have, and unfortunately it's a flat finish color, fine for USAF Euro camouflage, but consider that automotive engine colors are almost always glossy colors, it just isn't that correct. That's why I went looking at Humbrol. Even the Humbrol color chip online shows Brunswick Green to be lighter than it actually is (Humbrol paints the lids of their tinlets with the same exact color as contained in the tinlet in question) I find that color to be oh-so-close, and yes, Humbrol paints can be difficult to find in many cities--but it is most definitely available online. Art
-
Enamel cut with lacquer thinner
Art Anderson replied to Cato's topic in Model Building Questions and Answers
I've used lacquer thinner to reduce enamels (including Testors) for airbrushing since the late 1960's. It's always worked very well for me. Art -
Sticker shock!
Art Anderson replied to Harry P.'s topic in General Automotive Talk (Trucks and Cars)
Harry, Harry, Harry!!!!!!!!! 53 years ago, 1959, when Pactra first sprang 3.5 oz rattle can paints on me at the ripe old age of 15, the price was a whopping 59-cents a can (for comparison, '59 AMT 3in1 kits sold for $1.29 -- Annual Series kits, and the first of the Trophy Series, the '32 Ford roadster was a horrendous $1.49--but a new Chevy Impala convertible, fully loaded was about $3,600!). Fast forward to today: A rattle can of model paint at $6.19? 10.50X the 1959 price. $1.49 for a then-state-of-the-art model car kit (1959)? Try $21 plus today. And that fully tricked out '59 Impala convertible? How many 2013 Impala's you want at upwards of $35,000? Inflation, my friend, inflation. Art -
After reading quite a thread about what to use for the green color of a factory stock '50 Olds, I did some looking beyond the usual suspect paint lines and colors. Having started using Humbrol paints for things like interiors and underpinnings, I went to the Hornby Humbrol website, searched out gloss colors, and decided to stick my neck out, order their #3 Brunswick Green gloss enamel (comes in a 14ml tinlet) Well, it came today--and WOW! It's just so close to the dark green engine color that shows up in pics of those early Olds V8's as to be uncanny! So, that is my recommendation. Art
-
Whatever year it is, Norm Grabowski's "Kookie's Kar" T-bucket started out with a touring car body, not a roadster (look closely at the pic, you can see the extended body sides at the curvature from sides to back panel (to the point where the touring car's rear doors were, there is a break just aft of that door line in the body sill below). That can be replicated by fairing in a bit of sheet styrene (I'd use .040 Evergreen sheet stock, as Model T body sides weren't much more than an inch or so thick. I believe that Kookie's Kar used a '23 or earlier T body, given the very tight cowl and small, low firewall--Aurora made that body in their '23 T roadster kit, and I believe the Revell Parts Pack T roadster body is also of that vintage (it's a good bit different than the '25, which is the year AMT kitted). Art
-
Kit Building Then, and Now
Art Anderson replied to Tom Setzer's topic in General Automotive Talk (Trucks and Cars)
Pretty much on point! 50 years ago, I was a newly minted HS graduate, morphed into a fresh-faced college freshman with just enough dark peach fuzz on my upper lip and forward of my ears, along with enough curly brown hair on my chin to remind me that I needed to shave every 2-3 days. Back in those days, I was building straight from the box for the most part (although over the winter of '62, I'd taken two chopped '25 T coupe bodies, and used them to create a stock height tall T coupe!). As we didn't have any really good model putty (and I'd not yet discovered that real automotive spot putty could be used on a plastic body), my efforts at body shell cleanup were limited to filing and sanding down sprue attachment points and the inevitable mold parting lines. So, my concentration became focused such as really nice paint jobs (anyone else ever use GLEEM toothpaste as a rubbing compound?), learning to use an airbrush (bought my first airbrush--Binks Wren--along with compressor, hoses and water trap on December 26, 1961 with Christmas tips from my paper route customers!), and by going out on a limb, learning to use automotive touchup lacquers then hitting in rattle cans (a few fits and starts there, a few disasters, and some real successes there!). In midwinter that Sr year in HS, I sprang for some REALLY exotic tools--my first Xacto knife (which I still have, around here someplace), a razor saw, a set of 6 needle files (a neighbor guided me into a local wholesale tool dealer, who had those for tool & die makers!) and Heavens to Betsy, a pin vise and a set of miniature drill bits! It was with this latter that I was able to use bits of telephone cable wire (a cousin of Mom's was an Indiana Bell installer) instead of sewing thread for plug wires. About 1967, I began what was to become an absolute passion for the next 16 years, replicating cars that faced the green flag on race day at Indianapolis. Consider that through 1980, there were only 17 model kits of Indianapolis cars ever done in 1/25 scale (of which 5 were the rather crude Best/Aurora Famous Race Cars--1920 Monroe, 1922 Murphy Special, 1931 Bowes Seal Fast Special, 1939-41 Boyle Maserati and the 1953 Fuel Injection Special--all a curious blend of 1/25 and smaller scales in the same kits--all extremely crude even by mid-1960's standards). But, hooked I was--and over the years 1967-84, I built, modified, kitbashed, and even scratchbuilt well over 100 models of Indy cars. I concentrated (along with a total of 4 other local modelers) on cars that had won Indy, significant pole-sitters, and a few also-rans that were just so unique or famous--think the Novi here, that they just begged to be done. These became a big part of a HUGE Indy car model display put on every month of May in the front window of our local downtown hobby shop. Those cars forced me to learn to research (bear in mind that 25-40 years ago the reference materials for such cars was a lot more limited--only a handful of books with usable pictures and such 8X10 glossies that could be bought at the Speedway photo shop). They also taught me most of what I know today in terms of conversions, materials and techniques for scratchbuilding, and in the bargain--how to work through a problem to get a model to where I want it to be. So yeah, it's a hobby that almost mirrors growing up (something I still refuse to do!), and being persistent (and patient) enough to search out every possible reference to obtain that correct look. A far cry from where I was as a young kid, when like most all here, I was much more enamored with just getting the car built and finished, then raising the needed cash to buy another kit, do the same. Art -
Vellejo Primer peel...
Art Anderson replied to Johnag4004's topic in Model Building Questions and Answers
Both true and untrue! I've used self-etch primer (Duplicolor, if my memory serves me right) on a couple of diecast models that were converted using styrene model kit body panels. Of course, I airbrushed it rather than using the rattle can. Art -
Are you trying to spray "fluorescent" (also better-known as Day-Glo) colors over a dark surface? If so, that doesn't work, as Day Glo colors are NOT pigmented paints, but rather use light-enhancing dye to create that brilliant, "knock your eyes out" color. Painting with Day-Glo colors is a three-step process: First, you need a white ground base (almost always white paint), then a coat of Day-Glo, followed by a clear coat--the white is what picks up the light, reflects that back THROUGH the translucent Day-Glo color, and the clear coat protects the dead-flat surface that most all Day-Glo paints will have, to prevent fingerprints (your skin oils along with airborne dirt) from ruining the color. This is what I learned from spending 4 days at Indianapolis Motor Speedway in 1966, with a garage pass (STP Racing Team had to repaint their cars nightly during practice, as debris chipping left white spots, so STP shipped in their Day-Glo red by the 33-gallon drums weekly during the then-three-weeks-of-practice for the Indy 500). I got to see Lotus 38 nose cones being repainted each time I was there at the Speedway that Month of May so saw it happen in all three steps. This does need to be a spray painting operation, as Day-Glo colors brushed on will be very "blotchy" given that even the smoothest hand brushed paint surface will have thick and thin areas--brush marks if you will--resulting in differences in shade all over the work. Also, the white paint you use needs to be smoothly sprayed on, otherwise noticeable "orange peel", along with any runs or sags, or even bits of dust or dirt in the white will be greatly enhanced in the sprayed on Day-Glo. Last, the clear coat not only seals the Day-Glow's flat finish (meaning no shine whatsoever in almost all cases, brands and types of the stuff), but will also enhance the color a bit, deepening it only slightly while retaining it's brilliant shock value, and enabling you to get that gloss finish. In doing all this, you should be absolutely sure that the white base color, the Day-Glo color, and the clear coat are compatible. Most Day-Glow paints are either enamel based, or water-borne acrylic flat finish materials. While neither of those will affect a cured enamel white base, and certainly won't bother a lacquer white, for sure a lacquer clear will spoil things very quickly. I had to learn how to use this stuff 44 years ago when MPC released their 1/20 scale kit of the 1967 STP Turbine Indy Car, which was painted entirely in Krylon Rocket Red (the STP Corporate color back then!). It took two tries for me to figure it all out, but the effect was stunnning! In 1969, while finishing my college degree, I did all three versions of the MPC 1968 STP Lotus Turbines in the method I described, and used those cars in an annual display of Indy cars at the hobby shop downtown here in Lafayette. You could see those cars at night, in that lighted display window from half a block, they were that bright (so were the real cars on the track at IMS!). Day-Glo, Fluorescent and Neon often get used interchangeably, and regardless of what you call the colors, if it's got that super, eye-watering brightness, it will be the same thing. It should not be confused with some automotive colors, which were termed "Neon" this or that by actual carmakers--those are just extra bright pigments, NOT light enhancing dye such as used in Day-Glo/Fluorescent paints. Hope this helps! Art
-
Vellejo Primer peel...
Art Anderson replied to Johnag4004's topic in Model Building Questions and Answers
For metal, particularly diecast (or Zamak) as the alloy is known, it really takes an etching primer to adhere completely. Check for self-etch primer wherever you buy automotive touchup paints. Art -
MsDano85gt, "Annual" as it refers to model car kits, refers to those model car kits which were spun off the ready-assembled, curbside "promotional models" that automakers used to buy for use at dealerships to promote their new cars. These were quickly morphed into model kits, first by AMT in 1958, then by JoHan for 1959, and finally by MPC in 1965. At the time, among the kids we all were once upon a time, there was very little interest, generally, in any model kits of "Last Year's Cars" (they were, after all, so "Last Year"!, so model companies either set those tools aside, or were able to alter them into the coming new year's new cars (that happened a lot back in the 60's!). It was AMT Corporation who really fed the interest in iconic cars of the past (as the "past" was in 1959, when they introduced the first of their "Trophy Series" kits, a '32 Ford roadster, followed quickly by a '32 Ford 5-window coupe. Those were done, from the get-go, as 3in1 kits, following on the success of AMT's Annual series of 3in1 customizing kits, the Deuces being buildable as factory stock, street rods, or drag cars. MPC got their start primarily with annual series kits of new cars, and quickly did a series of antique/Classic cars, the Gangbusters series. JoHan did likewise with their Gold Cup series of Classic era cars as well. Art
-
You speak of "The heyday of model kits", and lament about "whatever happened to MPC"? If there ever was a "heyday" of plastic model kits, that, IMHO would have been the 10 year period roughly 1955-65, when almost anything, any subject area you can think of was done in plastic model kit form (planes, trains, automobiles, animals, birds, anatomical models--you can fill in just about any subject here you can think of!). However, while Revell pretty much introduced plastic kits of cars over 60 years ago (their legendary "Highway Pioneers" kits, and Monogram issued, as their first plastic model kit, #PC-1, a 1/20 scale so-so Kurtis Midget, it was AMT Corporation, by 1957 the biggest maker of promotional model cars for the auto industry who pioneered for 1958, a series of "Annual" model kits, based on their promotional offerings, which were customizing kits of then-new American cars, most all of them in both hardtop and convertible form. Key to AMT's success was the "one piece body shell", which for 1/25th scale model car kits, something very new! Yes, Monogram had done a pair of gorgeous 1956 Cadillac Eldorado kits in 1/16 scale, even Ideal Toy Corporation had produced a full detail (with opening doors, no less!) 1956 Lincoln Continental in 12th scale with opening doors, but those were the exception. Revell introduced several 1/25 scale model car kits in 1957, a pair of Dream Cars (the 1955 Lincoln Futura and the '55 Pontiac Club DeMer, along with a '57 Cadillac Eldorado Brougham and a '57 Ford Country Squire wagon, but those all had multipiece body shells, mostly indifferently modeled and tooled, the exception being the Squire, which is truly quite well done (tooling disappeared when it was redone into a rather inaccurage '57 Ranchero), but AMT was the first to do model car kits as we've come to know them. But, as they say on late night TV infomercials, there's more. By the early 1960's, AMT, solely on the strength of model car kits, became the King Kong of the plastic model kit industry, surpassing Revell's vast line (mostly ships, aircraft with only a few model car kits thrown in), their annual sales reaching toward the $200 million level by the mid-60's (Wall Street Journal wrote up AMT on their front page in the summer of 1965, as the "Largest carmaker in the world, on sheer numbers of units, which were in the millions at that time). Model Products Corporation was started in late 1963 by a then-former AMT engineer, George Toteff (who BTW had bought up Lindberg around 1990, found the AMT '34 Ford pickup kit tooling gathering dust in a tool shop in Windsor Ontario a couple of years later, and also introduced several pretty nicely done 1/25 scale model car kits in the middle 1990's). For 1965, MPC unveiled a small series of "Annual Series" 3in1 model car kits based on their line of promo's made for GM and Chrysler, some of which were actually produced for them at AMT (the 1965 Dodge Coronet being a prime example, along with a couple of show rod kits). MPC (as Model Products Corp became known much better) was an independent company for approximately 3 years, being sold to the Big G, General Mills of breakfast cereal fame circa 1967, and placed into a division of hobby/craft companies at General Mills, which included Craftmaster, the maker of then-very popular paint-by-number sets of famous paintings. This is what became known ultimately as Fundimensions. MPC began a sort of partnership with Airfix, the British 1/72 scale model aircraft producer (nothing like seeing model kits of SBD Dauntless US Navy Dive Bombers with chrome plated customizing parts--yeah, they made them!). By the early 1970's, General Mills had bought Lionel Trains from an investment house who'd acquired that line upon the passing of Joshua Lionel Cowen, the man who'd made Lionel Trains a household word by the late 1940's). Fundimensions was spun off from General Mills in the mid-70's, and MPC products began being molded by Kenner Toys, another Fundimensions brand. Enter the middle 1970's now: The business of designing and producing model car and truck kits hit a severe decline with the series of recessions, and what was called back then, "stagflation", that is, inflation even in recessionary times, which drove costs up dramatically, tooling costs were increasing on almost a weekly basis. To go along with that, the customer base for model car kits, us late "war babies", along with the baby boom generation had passed beyond what was the traditional age for model building as it had been, that being approximately ages 10-16, and although there were boomers still growing up, they were a lot fewer in number--the rest of us were too busy with military service, college and trade school, landing (hopefully!) that good job, getting married (and divorced) buying houses, raising and supporting families. By 1978, things did NOT look good at all for the future of this hobby, nor for any of the companies, save Monogram who were far better known for very nicely done model aircraft kits at the time. In the fall of 1978, AMT was bought up by Lesney (Matchbox Toys) just as their attorneys were preparing a plea of bankruptcy in the US District Court in Detroit. Early players such as Hawk and Aurora had already disappeared from the scene (Hawk tooling was bought by Testors), IMC--who had hit the model car scene in 1964 with a Lotus Ford kit had also sold their tooling to Testors. Model paint lines diminished by a third when AMT abandoned their excellent line of lacquer paints by 1993. Even us modelers were completely bereft of any magazines whatsoever aimed at car modelers. Lesney AMT went bankrupt in March of 1982, and things really began to look bleak. In 1983, Monogram bet some serious tooling dollars on their initial NASCAR offerings, along with a couple of IMSA racers, and Ertl began reissuing selected AMT kits, and all of a sudden a trickle of now adult boomers, former model car builders in their teenage years, began calling up local hobby shops (my experience was exactly that, as a fledgling hobby dealer in 1984--and I was one who had never quit building model cars). In the same time frame, model car clubs began to spring up seemingly everywhere, and the few clubs that had been around saw a real upsurge in interest. Now such legendary gatherings as the NNL in Maumee OH (now in Sylvania OH) and The Greater Salt Lake City Model Car Contest started up. A die was cast, believe me. From those new beginnings in the very early 1980's, continuing out to the present day, yearly we modelers have been presented with completely newly tooled model car kits not just from the likes of Monogram, Revell (Revell-Monogram since 1988), even MPC in their final, dying days (MPC became an Ertl brand in 1967) but also a host of Japanese companies became household words at model clubs, the hobby shops, and at the rapidly expanding model car show circuits. Indeed, by 1980, the French company Heller, and the Italian maker, Italeri made their products well-known in the hobby as well. "Heyday of model kits" you ask? IMHO, we are, and have been, for the past 30 years been living in them! By the late 1990's there were at minimum, over 400 different model car kit subjects available, not only from the two US domestic brands still standing, but from all over the industrialized world--that's probably more than 4 times the available model car kit offerings around in say, 1965. Included in that were not only dozens upon dozens of newly tooled kits, but many old favorites had been reissued (and this continues to be a big part of the story). I suspect that were someone to sit down, audit all the model kit offerings out there in just these past 5 years or so, it would be found that the vast majority of model car kits available in 2012 are those tooled up as new kits SINCE 1980. So, with all this in mind, isn't this still the heyday of model car kits, and model car building? I think so. Art
-
Your college years
Art Anderson replied to Greg Myers's topic in General Automotive Talk (Trucks and Cars)
I attended Parsons College, off and on, from June 1962 until I received my BA in June of 1970. There were, back then, a number of us students who were model car builders, and we built what we built right there in our dorm rooms (well, when I joined "Turner House", which had been the nicest hotel in Fairfield IA until bought by the college, and turned into the men's "Honor Dorm" for students with high GPA's--our Head Resident took a very dim view of hobby stuff in the rooms!). Going back to campus in 1966 after a 2-yr layoff, (Turner House had been destroyed by fire in the meantime), and being by that time a bit of an older student, I was given my own room in Howard Hall (the other two beds were blocked), I could build a model car without any interference. Same in 1967. After laying out for 1968, I returned, this time as a full time student, back to Howard Hall, again a private room, and I built a dozen Indianapolis Car models from June 1969 through May 1970 AND maintained a 4.0 GPA for those three trimesters. For some silly reason, the resident counselors (the college tried to get me to take that role, but I wanted nothing to do with that!) were more concerned about a periodic "burning rope" aroma (pot) than with my occasional airbrushing of automotive or AMT lacquers! As a sidebar: In the fall trimester 1969, I took an elective course, "Art & Design", and used as my class project, a scratchbuilt model of George Souders' 1927 Indianapolis Winner, the Duesenberg that Peter DePaolo won with in 1925, down to hand laced wire wheels, with a body and chassis done from scale drawings I made from an early book on historic Indy cars. Now, that was fun! Art