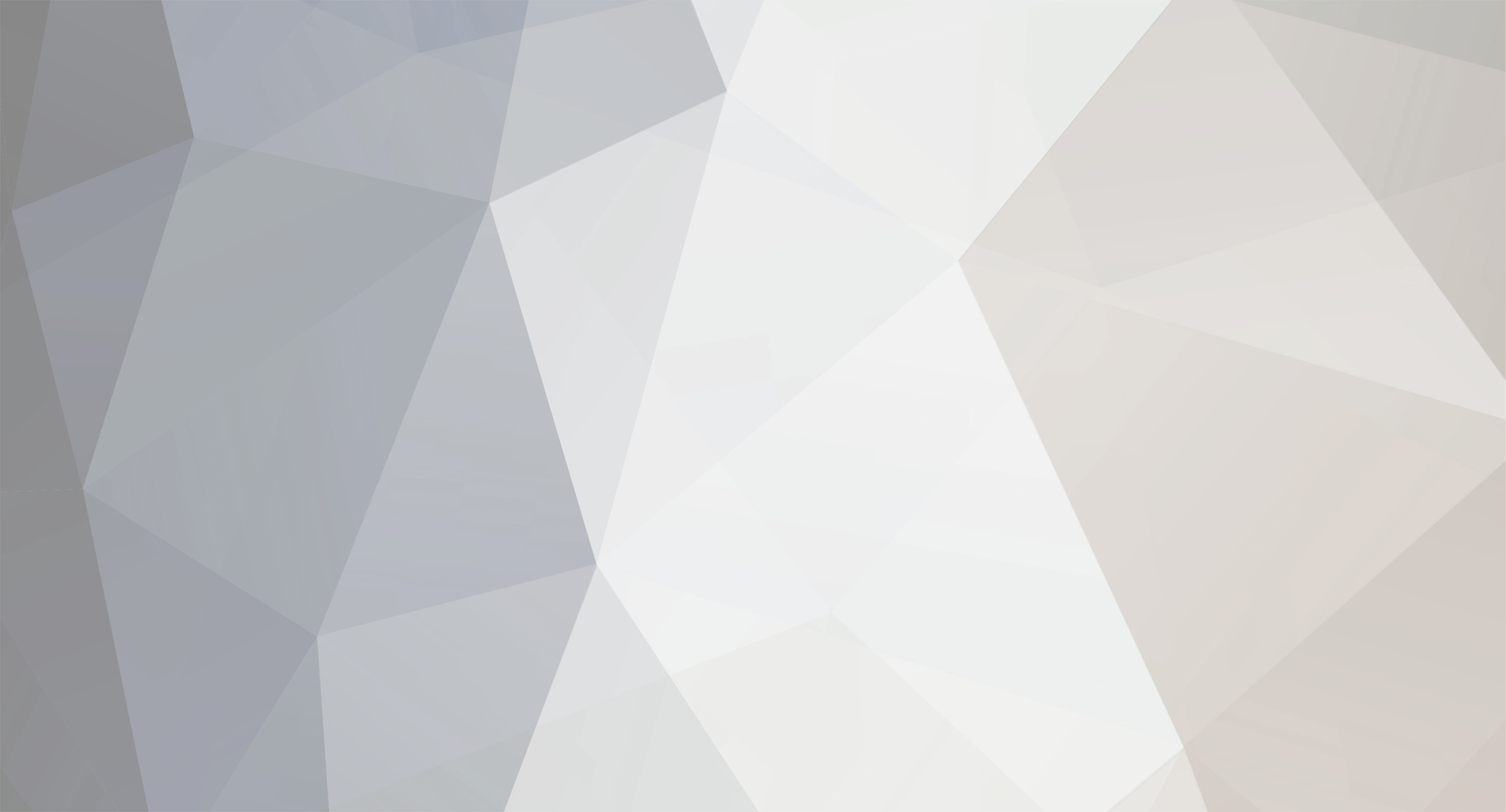
Art Anderson
Members-
Posts
5,052 -
Joined
-
Last visited
Content Type
Profiles
Forums
Events
Gallery
Everything posted by Art Anderson
-
Studebaker simply shut down engine production in South Bend in December 1963, due to high costs, and an extremely limited market. After shutting down all production in South Bend, Studebaker retained the Hamilton, Ontario assembly line through 1966, to fulfill their contractural obligations to such dealerships as there were left. But, production of approximately 20,000 Canadian Studebakers in the calendar year 1964 showed their decision to be a correct one: Use engines mass-produced at a much lower price rather than continue to struggle to make ends meet by producing their own. Art
-
Source needed for plastic tubing
Art Anderson replied to my80malibu's topic in Model Building Questions and Answers
Evergreen's largest plastic tubing (from their website/product list) is 1/2" OD. Plastruct has 5/8" and 3/4" in their butyrate plastic line, but no 11/16". Art -
Revell/Monogram 1/25 '29 Ford Rat Rod 3'n1?
Art Anderson replied to IronMunkie's topic in Truck Kit News & Reviews
One thing! With the rat rod version, Revell-Monogram FINALLY made the closed cab with a correct rear window! Art -
Pactra paint help please
Art Anderson replied to cchapman195's topic in Model Building Questions and Answers
OK! Pactra RC paint was always a lacquer based product. It must be thinned in order to airbrush, if you are using the bottled variety. Thin the stuff to the consistency of 2% milk, cut down your airpressure a good bit, it will spray very nicely, albeit with a flat finish (bear in mind, with clear Lexan RC bodies, you are painting on the inside, so the gloss finish is that of the clear plastic body!). To solve the flat finish, clear coat it. Art -
Ink Jet Decal Printing...
Art Anderson replied to Johnny Racer's topic in Model Building Questions and Answers
Just to clarify here! It isn't whether or not you use clear or white decal paper (incidently, decal paper cannot be clear--you will never see clear paper). Rather, it's a matter of whether the decal film applied to that paper is clear, or white. Art -
tire molding Tin VS Platinum
Art Anderson replied to Lownslow's topic in Car Aftermarket / Resin / 3D Printed
Platinum Cured Silicone RTV rubber is very susceptible to both sulphur AND contamination from tin-cured RTV! For platinum-cured RTV to set up properly, use mixing bowls and spatula that have NEVER been used for mixing tin-cured RTV, and if using clay, make certain that it's a completely non-sulphur-containing clay! I ran into this problem back when I was casting professionally, did as I suggest here, and had absolutely NO problems thereafter. Art -
Johan Mercury Comet
Art Anderson replied to tvandmoviecars's topic in Car Aftermarket / Resin / 3D Printed
And, if I might add, this one is JoHan kit quality--it IS that nice. So, Kevin, take a bow please! Art -
Model Cars worldwide...
Art Anderson replied to Harry P.'s topic in General Automotive Talk (Trucks and Cars)
From Indiana (Hoosier by birth, Boilermaker by the grace of God!) -
Cars that killed their "parents"...
Art Anderson replied to Harry P.'s topic in General Automotive Talk (Trucks and Cars)
More than likely, Willys had the tooling for the Americar (all the other automakers managed to "mothball" civilian car body dies during the war). However, Willys was right in seeing the potential of an all new line of vehicles inspired by the by-the-legendary Jeep. But, even with wartime profits in the bank, Willys lacked the money to do the multiple dies needed for all the restrikes necessary for those voluptuous curves of "fat fendered", streamlined automobiles, not to mention the manufacturing costs involved. Also, and probably more telling, was the shortage of the types of sheet steel needed for deep-drawn body shapes (the Big Three experienced that big time as well). So, Brooks Stevens (the legendary Wisconsin industrial designer) was commissioned to draw up very simple, slab sided bodies for the likes of the Jeep Station Wagon, a pickup truck, and ultimately the Jeepster. And thus, three iconic motor vehicles were born. Art -
The clay I mentioned, and used throughout my years in resin-casting is AMACO (American Art Clay Company) X-11, which is a moist, grey pottery clay. It's real clay, which softens with water, and cleans up with water as well. Look at Hobby Lobby, Michael's or any good craft or art store. Comes in 5lb quantities, and lasts for a long, long time when stored in an airtight container. Art
-
Johan Mercury Comet
Art Anderson replied to tvandmoviecars's topic in Car Aftermarket / Resin / 3D Printed
Here's the Missing Link Maverick Grabber resin kit that I reviewed in MCM: This is one VERY nicely done resin kit--I am certain that once built, one will never guess that it's a resin kit! Art -
I produced a '53 Willys Overland Station Wagon (Jeep Station Wagon, modified from the Liberty SpecCast '53 Jeep panel delivery) for several years in the 1990's. This has shown up on eBay more than once, keep your eyes open. Art
-
About 16-17 years ago, an acquaintance in France (whose name escapes me now!) sent me a color picture of a 1/24 scale plastic model (built and painted) of a 1974-46 era Lincoln Continental MkIV he'd found and restored. The story I got was that it was a kit produced by a French toy company that went under soon after, I've never been able to find any more information on that company, or the model kit.' Art
-
noob question, what is resin modeling?
Art Anderson replied to blueoval92's topic in Car Aftermarket / Resin / 3D Printed
Gregg (boss of MCM) and I have worked up a series of articles in the magazine on resin casting--the next installment should be on making a mold for a complete body shell. Check for back issues of Model Cars Magazine, and look forward to the next issue, the body casting article ought to be in that one. Art -
noob question, what is resin modeling?
Art Anderson replied to blueoval92's topic in Car Aftermarket / Resin / 3D Printed
"Resin", in the model car sense, generally means bodies, parts, even full kits molded in urethane resin. Resin parts, generally cast in RTV rubber molds can be as simple as reproductions of existing kit parts (most generally those from long out-of-production kits; or parts that have been either modified from existing kit parts or in many cases, parts that were scratchbuilt by a modeler, then duplicated in resin. Several resin-casters offer model car kits in two basic ways: As a full kit, meaning that all, or nearly all, parts, from chassis up through the body are provided. Most resin kits however, are what are called "transkits", meaning that they are intended to be used with an existing model car kit--this results in a different version of a particular car or truck--someone will have done all the conversion work ahead of time, then duplicated the results in resin. Urethane resin is the material of choice almost always for many reasons. It behaves a bit differently from the polystyrene plastic that commercially produced plastic model cars are made from, in that the glues used for styrene often will not work, as plastic model glues work by dissolving the plastic slightly, allowing mating parts to be "welded" together. Resin parts on the other hand, cannot be dissolved in this manner, so either epoxies or cyanoacrylate (CA, or just think "Super Glue" here) are what has to be used. Being a Newbie, stick around, read and look, resin stuff gets talked about a lot on these forums, and in Model Cars Magazine as well! Art Anderson -
Yes! It was a great show! Met up with a lot of old friends, made a couple of new ones. Art
-
Open Invitation - Diorama Exhibit
Art Anderson replied to KHamilton's topic in General Automotive Talk (Trucks and Cars)
Will you be signing autographs at NNL East next April? Art -
A diiferent way to ship cars
Art Anderson replied to charlie8575's topic in General Automotive Talk (Trucks and Cars)
Before the tri-level auto rack or the vertical stacking system developed for the Chevy Vega, new cars were shipped by rail in ordinary boxcars! Ford became the largest shipper of new cars by this method in the days of the Model T, as well as shipping subassemblies from Highland Park and Dearborn to Ford assembly plants all over the US (in such places as Indianapolis, Elizabeth NJ, Des Moines IA, Minneapolis, Los Angeles, Oakland CA, Portland OR, Seattle, Atlanta, Birmingham AL, Houston and Dallas TX) for final assembly. They could ship far more cars for assembly at remote points than was possible from the Detroit area. Enter the 50' automobile boxcar: http://searcharchives.vancouver.ca/uploads/r/null/9/2/927275/4bef4346-3c96-4df6-87d8-8552eebbb545-A28948.jpg These were perhaps the first specialized non-refrigerated boxcars built for wide use, starting in the 1920's. Notice the very wide door opening, and the wide double sliding doors. Now, imagine if you will, maneuvering a new car into a 10' wide space, being careful to not scrape against the edge of the door opening, straightening it out as if being parallel parked, then positioning it over the necessary tie-downs in the floor for securing the car for transport. At best, only 3 modern full-sized cars could be loaded thus; and in the case of say, Cadillac, Packard, Lincoln or Chrysler in the days of the rather long wheelbase "Classic Era" luxury cars, only two, and sometimes, perhaps only one auto could be carried in this type of boxcar. Pretty inefficient and costly! In some cases, once new cars became lower in overall height, in the 1950's, new auto's could be loaded into boxcars such as this by using a raised platform inside the car, but only holding two more automobiles, one at each end of the boxcar. Art -
A diiferent way to ship cars
Art Anderson replied to charlie8575's topic in General Automotive Talk (Trucks and Cars)
Considering that this method did not survive the Vega, it really didn't work. By far and away, the "tri-level" 85' autorack railcars have proved out to be the best way to transport new cars from factory to distribution points. Living where I do, on Norfolk Southern's main line serving the midwest, with direct rail links into Detroit, Toledo, Cleveland and other points where new cars are built (including Subaru Indiana Automotive here in Lafayette) I have seen hundreds of those railcars move through the city. Loading them takes no fancy infrastructure whatsoever; nothing but a set of ramps at the end of a siding, over which autos can be driven directly up into a string of autorack freight cars, then down the full length of each string of cars (SIA has these cars spotted, at the plant, in strings of up to 8 cars at a time, on 8 or 10 parallel spur tracks. the size automobiles built here allow for 5 cars per deck, or 15 per rail car, with only a small crew required including drivers and tiedown crews. Several times each day, NS loco's pull out loaded autoracks, and replace them with empties, so that the process need not stop at any time along the process. It's not uncommon to see a transfer train of these being moved from the yard next to SIA (which also serves a large Tate & Lyle Corn Sweetener plant (one of two here in Lafayette) from this "South Yard" down through our dedicated rail corridor along the river, and up the grade to NS North Yard for coupling into trains either east or west bound. Some also get transferred to CSX at their yard near downtown Lafayette, for transport south to Louisville and beyond, or north to Chicago for transport to the upper Midwest and on to the Pacific Northwest. In this way, new cars are transported with no worries as to engine or transmission fluids leaking into areas where they don't belong, and once the crews learned how not to tie these new cars down (some years ago, Cadillacs suffered some damage to rear axles by crews chaining those cars down by the axles, which wreaked havoc on rear axle bearings). The bilevel container concept never worked out either, abandoned before it ever really got started, as other railroads and auto companies shied away from the much more expensive equipment needed to load and offload those containers, and then unload the new cars from them. It's interesting to note, I think, that the most common type of trilevel autorack cars were developed from 85' piggyback flatcars developed in the late 1950's by a consortium owned by the various major railroad companies: Trailer-Train" or as their reporting marks and trademark says, TTX. Even though the 85' piggyback flatcar is almost a thing of the past, save for some transcontinental use hauling UPS "pup" trailers from coast to coast (due to their being designed in the age of 40' semi-trailers, and obsoleted when the 48' and 53' trailers became legal on the highway, and the railroad limitation on car length (virtually all railroad mainlines were laid out to handle cars no longer than 85', also the standard length for railroad passenger cars from about 1910 onward). Starting about 1962 or so, TTX began welding uprights and ramps in two formats, bi-level for handling such as vans and taller new vehicles, and tri-level, for hauling the ordinary automobile. As cars have become smaller, shorter, these railcars can carry up to 18 subcompact cars, 15 mid-sized cars, or 12 full-sized ones. Of course, with vandalism being a problem, all auto-racks have been sheathed in various styles of perforated sidewalls, which make it very hard to see what's inside, and of course, much harder for "taggers" to work their spray can havoc on new cars. Art -
I'm not at all sure that those Mercedes-Benz wire wheels weren't bright chromium plated when new! I know I've seen newsreel/propaganda film footage of say, Adolph Hitler's entry into Vienna in 1938, his car (a Mercedes 500 or 540 Phaeton) turning a street corner in bright sun, the wheels flashing brilliantly in the sunlight. That says "chrome plated" to me). For all the quality of German camera's in the 1930's, those black & white images don't really show the brilliance and sparkle of chromed parts anywhere on the car that one would have seen outdoors, or certainly in person. Chrome plating was all the rage by 1935, having been introduced to the auto industry in 1927 by Oldsmobile Division of General Motors that year (prior to that, automotive brightwork was polished metal (brass, nickel silver, aluminum) or nickel plated (which was never as bright as chrome, nickel having a slight "brownish" cast to it in addition to dulling very quickly in use). I'd be very sure that Daimler Benz built their cars with steel wire wheels, aluminum alloys not having reached the point by that time of being capable of holding the stresses (particularly the rims and hubs of wire wheels) imposed by cars weighing at least 4,000lbs (and that would have been at the lighter side of the weight scale for a top-line Mercedes-Benz (380, 500 or 540 K engines) of the 30's, bearing composite (sheet metal over heavy wood framing) bodies (pretty much standard with low-volume production luxury cars of the 1930's, even beyond that in some cases). Even the straight 8 engines used by Mercedes back then surely weighed, on their own, upwards of 800--perhaps close to 900lbs, just as with their American counterparts. All this points me to saying that those wheels were steel rims, steel hubs, and steel spokes, chromed rather than merely polished (chromium was touted for it's ability to resist rust over time, when properly applied over layers of copper and nickel--triple plating). One of the biggest problems with plastic model kit wire wheels has always been that the spokes, in order to have wheels strong enough to withstand the less than gentle hands of younger builders back when say, Monogram and Johan were tooling up their Classic Car kits in the middle 1960's; made wire wheel spokes that are much larger than the true scale size of their full-sized counterparts. In addtion, rather than being round in section, they are "triangular" which only exacerbates their out of scale thicknesses. All this said, it might be worth darkening in the spokes themselves with a black wash, wiped off the outer, sharper edge, to de-emphasize their excessive width, and accentuate the sharp outer edge. Worthy of thought I think. Art
-
Newbie To Resin
Art Anderson replied to kenshapiro2002's topic in Car Aftermarket / Resin / 3D Printed
The known health hazards for polyurethane resins all tend to come from the liquid components themselves, due to their nature. Yes, resin dust is a hazard, particularly in industrial situations (think furniture factories--a lot of those "carved wood applique decorations applied to otherwise wood furniture are often resin-castings), factories making automotive soft trim such as soft bumper covers, factories making "faux stone" countertops for kitchen and bathroom use, and more and more, factories making urethane resin decorative wall tiles) where the cured resin is either sawed or sanded in large quantities. There, dust is a very real issue, and for the same reasons it is around fiberglas fabricating, even woodworking. Solidified cast urethane resin is, for all intents and purposes, inert to any water or water-containing situations--it does not dissolve in water, thus no contaminants are likely to be released. However, the dust, being inert as regards water, won't break down in the human body (from all I've read over the past nearly 25 years), but the dust can collect in breathing passages, and remain there essentially for life. All that said, the vast majority of model builders' contact with urethane (or for that matter, polyester) resin is in the form of already cast articles, which generally need at least a bit of trimming or cleanup around the mold parting lines, or edges. Cutting tools, such as your Xacto knife, razor saw, files, or the rotary high-speed or carbide cutters used in a Dremel or similar tool create almost all "chips" as they work, and relatively little dust, unlike sandpapers or sanding discs or drums. If one watches the waste coming off a razor saw in action, those chips fall very readily to the floor, they don't float in midair. Nor do the chips coming off a rotary cutter, those come off in a stream that gravity pulls down to the floor, and very little in the way of dust. In our hobby, the most dust gets created by using sandpapers dry--and most of us do not do that. No, we tend to use Wet or Dry sandpapers, soaked in water, which captures the sanding dust, leaving a muddy surface on the model being sanded, and in the dish, bowl or cup of water being used (and a lot of us do that sort of sanding at a sink, with running water. At stages during a project, we do tend to wash down the body shell or whatever is being sanded, which takes the dust and flushes it down a drain someplace. At any rate, the amount of dust we release into the surrounding air is at best, miniscule, particularly in comparison to spray painting with either rattle can (a HUGE source of dried paint dust, BTW) or airbrush (much less overspray dust from those as a general rule). So, use your own common sense here--if you feel that a facemask is necessary, by all means use one. However, if one does not view the occasional bit of dust from any source in the model room to be a hazard, probably little to worry about. As for carcinogens, I just read several assorted MSDS (Manufacturer's Safety Data Sheets, required under OSHA for all chemicals or chemical-based materials sold for use in industry or consumer use) for polyurethane resins. Nowhere in those did I find any concerns expressed about potential cancer causing materials. I spent 11 years actively casting resin model car parts of all kinds and sizes, and by the 10's of thousands. Others, such as Don Holthaus, have by now produced well into the millions of resin parts over their careers. Of all the resin casters I've known, two passed away years ago, both from cardiovascular situations apparently not related to their casting model car parts in urethane resin (both worked at it part-time, alongside their regular day jobs). But in any event, if one is doing so much sawing and sanding of any material, including metals, resins, or wood, to the point that dust is settling on every horizontal surface, then yes, by all means WEAR AN APPROPRIATE face mask (and this certainly applies to any spray painting unless you are doing it out of doors, or have a proper exhausting spray booth to remove both overspray particulates and the solvent fumes from your surrounding environment (your model building room or space). Art -
"An organism must grow in order to survive. When it stops growing, it starts to die" is a quote I heard from the late Ray Kroc, founder of McDonald's Corporation in 1955 (while at a McDonald's Manager's Convention in 1980 or thereabouts). Well, learning is a part of growing, so in a very real way, it seems to me that when we stop learning, we start to die away. With that, I cannot begin to enumerate the sheer number of things, of techniques, of materials, that I've learned from other model car builders over the past now 60 years of building model cars (Yeah, I know, I'm a moldy oldy!) Art
-
How do I degas a mold?
Art Anderson replied to raildogg's topic in Car Aftermarket / Resin / 3D Printed
It's the mixing of the rubber with the catalyst that stirs in air bubbles into the RTV. Some will rise to the surface, of course, but not all. Some have mentioned that it's all right as long as no airbubbles are right on the surface of the master, but that's only partially true. Bear in mind that virtually all catalyzed RTV rubber shrinks ever so slightly as it cures; the really good quality stuff generally no more than 1/10 of one percent (not enough to affect the fit of parts) which also will compress any air bubbles in the rubber slightly. However, if an air bubble of any size larger than say, the head of a straight pin is within as close as 1/64 inch to the surface of the master (particularly in a large mold such as that for a body shell, that air bubble will expand slightly once the master is removed from the mold itself, forming a raised spot on the surface of the mold cavity itself. When this happens, the resulting casting can, and generally will, have a slight "depression" at that spot in its surface, almost as if a BB was shot at it. It's for this reason that professional resin casters will use a vacuum pump and chamber to draw out those air bubbles. In order to do this, they use vacuum pumps capable of pulling a mechanically perfect vacuum, which is expressed as 29" of mercury. At that vacuum, the liquid rubber will rise, like a nice souffle', with a huge head of foam on top of the rubber, which as the vacuum decreases, will "fall", as the air bubbles begin bursting, and the rubber settles down to the point that it looks like a thick soup boiling on the top of your stove. Once the air bubbles die down to few enough to count, the rubber is about as degassed as it will get, and once the vacuum is released, those airbubbles get crushed down by atmospheric pressure to insignificance. That ends the problem of air bubbles in the mold, trust me on that one. Used vacuum pumps can be found a lot of the time, being sold off by retiring HVAC techs (refrigeration and A/C techs), and also at a lot of colleges and universities who replace them with newer ones for their various scientific laboratories. (I got mine at the University here back in 1989, just for the asking--it had been produced in 1940, rebuilt in 1959, and hadn't been used since the late 1960's, but that would be a pretty rare thing to have happen). Vacuum chambers are often made from VERY heavy glass, almost like a punch bowl, that is an inch or more thick, with a very close-fitting heavy glass lid--break that lid, and the chamber itself is toast, due to it's having been fitted exactly to that glass lid. I made a new lid for mine with 1" thick clear Lexan, with a thickwall Lexan tube 3/4" OD, and used a length of clear PVC flexible tubing between that and the vacuum pump (mine had a "nipple" on it, smooth brass with a rounded lip around the end, which captured that PVC tubing perfectly air tight. But your experience may vary depending on what manner of vacuum pump you can find. As for pressurizing: This is done with resin once poured into a mold. Polyurethane resin is just thick enough consistency that when one mixes the catalyst in it completely, air gets stirred into the resin. Putting the filled mold into a pressure pot and pumping it up to say, 75psi will crush those airbubbles to insigniicance, as the air bubbles formed at normal atmospheric pressure. This must be done within the "pot life" of the mixed resin, in order to work, so working quickly is essential. Campbell-Hausfeld makes 2.5 gallon pressure tanks for use with power paint rollers, these are probably at least in the $125 range or so (I paid perhaps $75 apiece for the 5 that I used in production line resin casting, starting back in 1989). As for the air source, a decent shop type air compressor, with at least a 3-gallon tank works the best with these, along with the appropriate pressure hose and fittings, AND good, reliable pressure gauge. Those run a fairly wide range of prices, but you need not buy the most expensive one. Note that no professional resin casters I know of try to degas Urethane resin by vacuum--that actually can release more gasses than just the air that got mixed into the liquid, and the vacuum process will take longer to do than the pot life of the resin--usually 90-120 seconds at room temperature. That would leave you with a foamy mess rather than a solid casting. Hope this clears up these two issues at least a little bit. Art Anderson -
Cars that killed their "parents"...
Art Anderson replied to Harry P.'s topic in General Automotive Talk (Trucks and Cars)
Well, we Jr High aged car nuts called it exactly that, back in 1957! Art