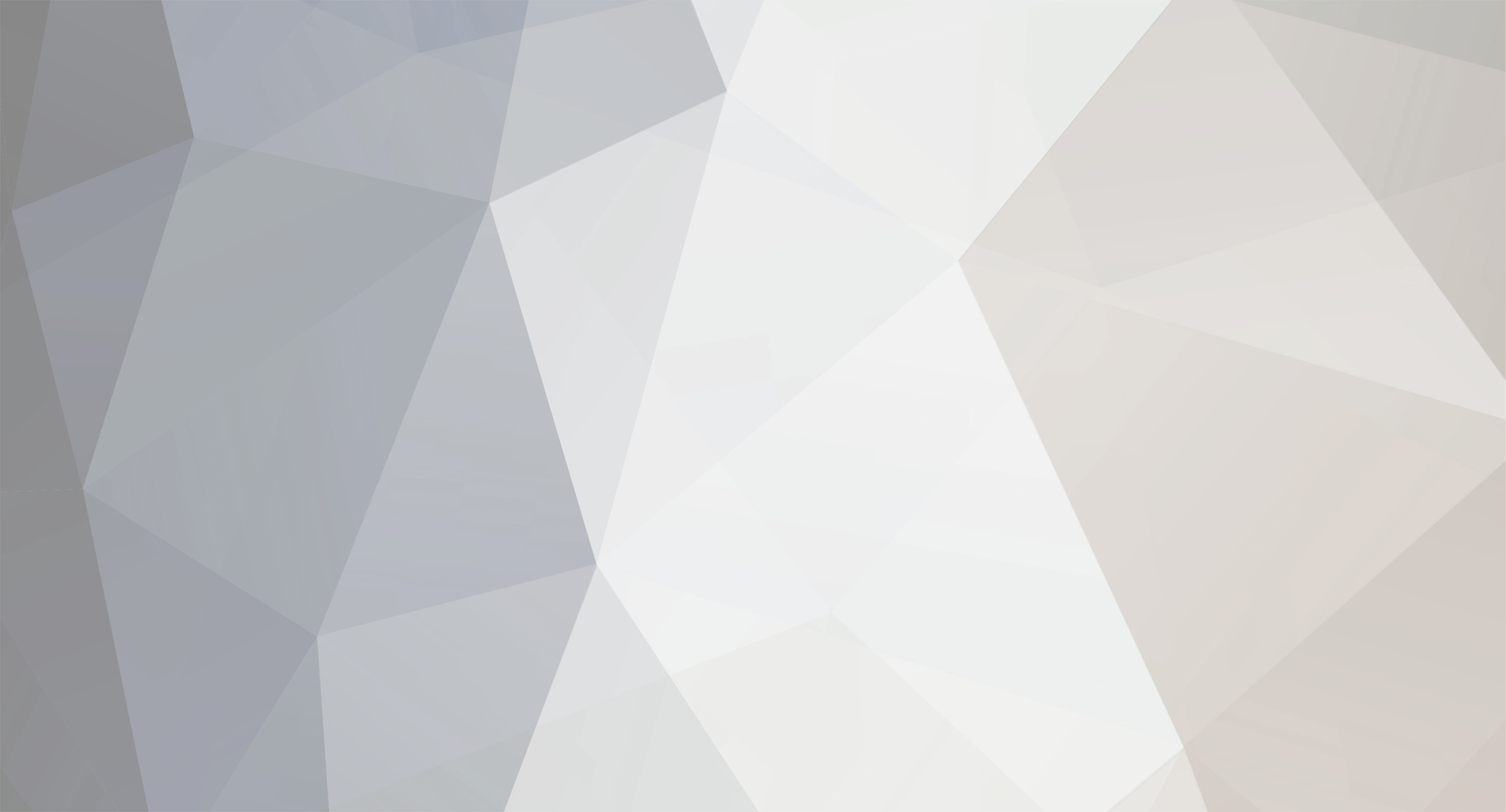
Art Anderson
Members-
Posts
5,052 -
Joined
-
Last visited
Content Type
Profiles
Forums
Events
Gallery
Everything posted by Art Anderson
-
Lets give a round of applause for
Art Anderson replied to mnwildpunk's topic in The Off-Topic Lounge
More of us than most people imagine got started in this hobby during at least a period of time on the "disabled list". That's when I got started. 60 years ago right now, as an 8yr old, I was finally being allowed to sit up in bed after a severe bout with rheumatic fever (which generally caused a heart murmer due to damage to the mitral valve of the heart, which in my case it did). Dad was my "savior" in all that, introduced me to Revell Highway Pioneers, and even after I got back on my feet, I was hooked, and Dad realized he'd created a monster! So, I have had every incentive to aid a disabled person who wanted to try building models, all these years, and have done so on more than one occasion, almost always one-on-one though. Art -
Is it too late?
Art Anderson replied to Hedgehog's topic in General Automotive Talk (Trucks and Cars)
It's never too late (or for that matter, almost never too early!) to take up this or any other hobby or craft. Some of us here have been building model cars for decades (I just turned 68, started building model cars 60 years ago at the age of 8). Some others, like an old (now in his early 80's) friend of mine from Northwestern IN, didn't get into scale model building until their 50's, even 60's, and quickly learned to create awesome masterpieces. But no matter whether one is a Gerald Wingrove or just somebody who loves puttering around with a plastic kit--it's all good, it's all fun, and the cameraderie' in this hobby just doesn't let newbies fall by the wayside without a bit of a struggle, in my experience. So, have at it! Art Anderson -
To paraphrase an oft-overused cliche' "Perfection is in the eye of the beholder." Art
-
What's the deal with Johan
Art Anderson replied to Kaleb's topic in General Automotive Talk (Trucks and Cars)
That was Revell, in the summer of 1963. Art -
Actually, "cheap" wasn't the primary reason. The early popularity of Fords as hot-rodding material goes back to the early 1920's, given that Model T was the most plentiful car in the entire world (by the early 20's, one out of every two cars produced worldwide was a Model T Ford). Nearly 50 different high performance cylinder heads were produced for the Model T, almost nothing in the way of speed equipment seems to have been produced for any other make of car back then. With the advent of the Model A, parts interchangeability began to happen across model years and major design changes, something that really didn't happen with most other makes of cars (for example, that really didn't begin to happen at Chevrolet until the late 1930's). Another factor was weight! A Plymouth weighed a bit more than a Model A, due to its type of construction (Plymouths were being built with composite (sheetmetal over wood framing body construction) bodies across the board, as were Chevrolet's, while structural wood in a Model A Ford coupe was minimal, and nonexistent in a Model A roadster save for the wooden floorboard in front of the seat. This type of body structure required a heavier frame (by contrast, I have picked up, carried a bare Model A frame clear across a farmer's field one-handed!). In addition, Ford's transverse springs made for a lot less unsprung weight (something that an engineer should understand as it relates to the handling of any car on the road), and with radius rods fixing the caster angle of the front axle firmly in place, no spring "wrap up" on rough pavement or under hard braking--totally unlike the dual longitudinal leaf springs used on the front axles of just about every other automobile up through the introduction of early IFS systems. With the introduction of the flathead V8 in 1932, Ford had an engine with even more hot-rodding potential than the Model T or Model A, and a lighter engine in the bargain (in general, the flathead weighed a good bit less than a comparable displacement inline 6 (The same thing was true when Chevrolet introduced their small-block V8 in 1955, that engine is quite a bit lighter than the 235cid inline 6). Now, a bit of history that seemingly contradicts some of the above: Prior to WW-II, the most popular engines for hot-rodding were NOT Ford flathead V8's, from all the historical information I have seen. Rather, it was 4-cylinder engines. Oddly enough, seemingly, the last series of Chevy 4-cylinder engines were widely used, and early rodders learned that the 4-cylinder heads from Oldsmobiles (think the Beverly Hills Truck here!) were fairly easy to adapt to that Chevy 4, with a bit of machining (it seems that the cylinder spacing was so close to that of Chevy that it worked!). Also, the serious hot rodders of the 30's tended to be older, guys in their 20's to 40's, than the largely teenaged crowd who kept the home fires burning during WW-II, when flathead V8's could be scrounged out of junkyards fairly easily, even in the face of the tremendous scrap drives for the war effort. But, by the end of the war, it was Fords, from Model T's through the early flathead years that had survived (even as late as 1980, nearly half of the 5 million or so Model A's produced were still in existence, and many if not most of them were still registered cars here in the US!). Model T's had a high survival rate as well, and still are the most restored cars out there. By contrast, those pre-1933 Plymouths, and Chevrolet's were largely gone, as much due to the deterioration of their wood-structured body shells as anything else. Of course, Model A and '32 Ford 4dr sedans had nearly as much structural wood in them as their counterparts, but then, rodders were much more interested in the lighter weight body shells, and there, Fords excelled. So, I think all that explains why Model T's , A's and of course the Deuce tended to rule as hot rod subjects: Light weight, durability, availability, and a wide interchangeability of parts and major subassemblies across the years 1928-48 also played a huge part in this. Art
-
Silly color question
Art Anderson replied to mnwildpunk's topic in Model Building Questions and Answers
Originally, those sedan deliveries used what was called "Battleship Linoleum" on the floor of the cargo platform, edged with extruded aluminum angle material. Art -
Kit Manufacturers in General
Art Anderson replied to Miatatom's topic in General Automotive Talk (Trucks and Cars)
First of all, I've never seen a badly designed, tooled or molded Tamiya model, and that includes their early 1/24 scale model car kits, which for the most part were "curbside" (no engine, no opening hood), and designed to be motorized with a small battery motor and a couple of AA penlight batteries. Over the years, Tamiya has made many fantastically designed and tooled model car kits. If Art -
Not quite that simple, Harry! In pad printing (AKA Tampo Printing) the soft rubber pad picks up ink (pigmented rather than dye oriented) from a plate which is photo-etched with whatever design is needed, and then transfers that "design" to the surface being printed. Usually thought of when discussing finished diecast models, a graphic design might be one color, or it might be multi-colored, as in racecar graphics, flame patterns, or even say, the Vee and Crest for a Cadillac model. In the case of multi-colored graphics or emblems, each color requires a separate pad-printing operation. By contrast, an ordinary rubber stamp itself carries the design, as raised detail on the rubber surface of the stamp, picks up ink from a solf pad saturated with the stuff, and then transfers that design to whatever surface is to be printed, in the same manner as oldfashioned type in a letter press printing press. Pad printed templates are created from artwork, by photoetching each part of each design as slightly recessed from an otherwise very smooth, polished metal (usually copper) surface. The first step is to add the pad printing paint or ink (as thick in consistency as probably a fresh bottle of Testors enamel), and then a squeegee scrapes all the excess paint off that photoetched plate, leaving the ink or paint in the recessed portions that were photoetched down into the surrounding metal. Next, the pad is pressed onto the plate, and picks up the color remaining, and then transfers that to the surface being pad-printed. In production, particularly with diecast model cars, this process takes mere seconds, and the paint or ink dries within a couple of minutes. This is then repeated, at a different station for each color, and each portion of the design or emblem, until all the colors are applied. That's how it's done on diecast miniature cars, and even on molded plastic promo's. Pad printing has limitations however: On a compound curved surface, as most car bodies have, if the pad-printed graphics are to "wrap over" curves, then the pad-print artwork gets divided into however many sections are needed in order to get a graphic that appears to have been masked and sprayed, yet in practice, is printed. This is not generally used for doing say, a 2-tone paintjob on a diecast, however. That gets done by "spray-masking" in which process a masking template is made by forming soft sheet copper to the contours of the body to be given a second color (say, a white roof on a red '58 Impala), which is then cut out to make the shape of the color separation line on that body. Once this is done, the copper is hardened, and mounted in a frame so that it can be locked to an enclosed spray painting nozzle or two (or more depending on the scale and correspondingly the size of the model), Each time the operator positions a diecast body shell (with it's principal color already sprayed on and baked dry and hard) up against that mask, and steps on a foot pedal, the machine puts out a short shot of spray enamel onto the exposed area of that body shell. Having spent almost 3-years in product development at Johnny Lightning starting a little more than 10yrs ago, I got pretty familiar with pad printing, and pretty quickly at that. Art
-
Kit Manufacturers in General
Art Anderson replied to Miatatom's topic in General Automotive Talk (Trucks and Cars)
As others have mentioned, any general discussion of "kit makers, plusses and minuses.....etc." would be almost pointless, frankly. Every model kit manufacturer today has either been in business for a lot of years, is the successor to an original company from years ago, or is a new, almost-startup company using the model kit technology that has developed over the past 40-plus years. Virtually any question on a forum such as this that goes "What company makes the best model car kits" generally just gets bogged down in opinions based more on a particular subject matter rather than anything really coherent, IMHO. Now a better comparison or discussion might well be a particular kit. But in doing so, one ought to pay attention to what older builders might have to say, as to when (what era, how many decades ago and so forth) that kit was first introduced. Bear in mind that, for example, the "iconic" US domestic brands of kits (AMT, MPC, Revell, Monogram, Aurora, IMC, JoHan to name perhaps the best known, go back 50-55 years, given that this is the country where model car kits and building first really took off. Many kits by such makers were excellent even for their day, but the learning curve was underway back then, in addition to the expected consumer being a lot younger than today's builders (yeah, us grey-headed builders were kids once upon a time, most of us dating from that time frame). Also, the "price point" that model car kits were expected to sell best had its limiting factor as well--the expected selling price of a kit along with expected sales of same, go a long way toward determining the amount of capital that can be invested in any particular model car kit tooling. Add to this the fact that many kits of yesteryear not only reflect the state of the art for the day they were first introduced, they also reflect the types of mold machines then in use, subject matter that was considered important enough to be produced, and to a very great extent they also reflect the artistic skills of industrial pattern makers of the day (no CAD or CAM back in the 1960's or 1970's that would have been financially available to a model kit manufacturer) did almost all their work by the human hand, human eye, utilizing the then commonly practiced industrial drafting instruments (pen on paper, T-squares, pantographs, French Curves and such), and pattern making by the process of hand-carving each and every part that would be needed so that those could be rendered in steel tooling. So, with virtually any model kit mfr, their line of kits is going to reflect some evolution (yeah, even Tamiya, Hasegawa, Fujimi made kits that if reissued today, would be considered pretty much "klinkers" today), but yet perhaps the subject might just sell as reissued, but not be seen as having enough sales potential to warrant the immense investment in all new tooling. So, better to ask about an individual kit or subject, it seems to me. Art -
Early Model Builder Pioneers
Art Anderson replied to Dr. Cranky's topic in General Automotive Talk (Trucks and Cars)
Dave Shuklis, Don Emmons, Joe Henning, Budd Anderson (no relation) all come to mind as early "pioneering" builders of car models as most of us come to know it. Art -
Supply and demand. Consider that Ford built more than 5,000,000 Model A's from December 1927 through early January 1932 (US domestic only, this doesn't count Model A production beyond US borders), but only slightly more than 250,000 Model B's (4cyl '32 Ford) and Model 18's (V8 '32's) from March 1 through November 1932. Even "back in the day", hotrodded Model A's far outnumbered the Deuce, to the point that '32 V8 cars were seldom rodded prior to WW-II. A perusal of period literature shows that prewar hotrodders much preferred the Model A, along with hopping up 4-cylinder engies. It wasn't until wartime that HS kids, too young to be drafted, started playing around with the flathead V8. Art
-
Earl, well said. Let me add something here: Just as an example, 50 yrs ago, when I was a newly minted high school graduate and college freshman, on the threshold of being 18, the '32 Ford was a 20yr old car. As such, people were already starting to ask "How long are rodders going to want to build Deuce roadsters? Well, fast forward to 2012, the Deuce is now an 80yr old car, and it can arguably be said that there are, in all forms (gennie restorations, original steel-bodied rods, reproduction fiberglass copies, even reproduction steel bodied Deuce roadsters) MORE Deuce roadsters on the streets today than Ford ever built! Now, given that it's fairly true that "art mirrors life", don't we still see modelers doing Deuces? Yes, we sure do. And while the big boom in this hobby happened just as "baby boomers" hit their early teens about 1959 or so, there is already a solidly placed second generation out here today--kids of the boomers, and guess what, a great many of those guys (and some gals who are modelers) have been building a third generation. Even in the late 50's, not every kid built model cars, although it sure seems as though they did. An awful lot of kids back then at least tried, but only a portion of them stayed with it. And that can be said of each generation or so that has come along since. I'm less than a week from being certified as a 68 yr old, and while I have no kids, technically, I could have easily become a grandfather to near teenagers today--chances are that had I a son, he'd have at least given a model kit a shot, same with a grandchild, and even possibly a great grandchild. However, I think I'm smart enough to realize that just as not every kid in all my years on this planet built a model car, there's no reason to expect that succeeding generations would be any different. As for reissue after reissue after reissue: Of course, in the end, it's pretty much always new product that drives sales, but even at that, reissues of subjects that still have some popularity can be just that extra bit of revenue that helps fund new tooling. Time was, with the exception of recognizable hot rodding subject matter, a model company could not hope to sell very many kits of cars that were more than 2-3 years old--that is how it was 50 years ago. However, as I mentioned above, there are a great many subjects today (a '32 Ford is but one example) that can be kitted, and sold, and sold in comfortably large numbers--and I somehow doubt that will go away any time soon. And given that our hobby is not one that is dependent on "Fortune 500" companies for model kits or supplies, the sheer number of model kit producers worldwide, along with those manufacturing everything else from paints to all the aftermarket stuff one can imagine--this hobby is going to continue for a few more decades at least--surely far after I've assumed room temperature. But to get into "hand-wringing" over what will happen to our hobby when all us current members of it leave this earth--why bother? Go for the gold while we are still here, still able. If some of what we do sticks, so be it, if not, well....I think we all know the answer. I don't think I've ever seen a crystal ball that gave perfect vision into the future, and to me that's OK. Art
-
giving casting a motor a shot
Art Anderson replied to Lownslow's topic in Car Aftermarket / Resin / 3D Printed
Amaco X-11 moist pottery clay works beautifully, and cleans up with water. Art -
How do I figure out scale?
Art Anderson replied to mnwildpunk's topic in Model Building Questions and Answers
Seriously, 1/25 scale is one of the easiest in which to work with scale measurements! For those who prefer the metric system, 1 inch is equal (certainly close enough for our hand tools!) 25.4mm. If one uses 1mm to equal a 1/25 scale inch, the difference between that and micrometer accuracy is but a small fraction of the thickness of an Xacto #11 knife blade. Now, 5 ten-thousandths of an inch makes a real difference in precision machining of metal parts, but it's infinitesimal when one thinks of razor saws, Xacto knives, and sandpaper of any grade. So, seriously, for someone steeped in metric, 1mm can readily be used to represent an inch in 1/25 scale. For those who prefer English measure (you know, feet and inches and fractions thereof), divide 1 by 25, and you come up with .040" as a scale inch in 1/25th scale. Common fractions of an inch in this scale are equally easy: .020" is a half inch, .010" is a quarter of an inch, and .005" is but an eighth of an inch in this scale. When scratchbuilding, Evergreen and Plastruct make it even easier--both companies offer styrene sheets and strips measured in thousandths of an inch, and thus in most all common scale fractions of an inch. Math is a wonderful skill, but sometimes, a little bit of thought also works. Art -
Tastes change ...... ?
Art Anderson replied to Jantrix's topic in General Automotive Talk (Trucks and Cars)
Wasn't it Jim Jacobs (the "Jake" of Pete & Jake's) who pretty much started the thing about doing a hot rod that was not all chromey, with a miles-deep paint job ('29 Model A Phaeton that was well-built, but painted red with a brush and then had Rod & Custom covers and magazine pages varnished down over that? Anyway, 60 some years ago, to see a rod or a custom on the streets more often than not meant seeing a work in progress: Bodies in primer (but NEVER rusted out!!), hot rods that gained a chromed part here and there as money allowed. I vividly remember a 19yr old here in Lafayette, the son of a preacher (literally!) who spent most of the 1950's customizing a 1949 Chevy convertible. When the chrome came off, he filled the trim mounting holes, and simlly spotted those with red oxide primer (the car was originally black). For almost a year, he ran it around town with a stock taillight on the left, and a newly welded in and leaded '49 Cadillac tailfin and taillight--now that looked pretty odd for a while. But above all, those cars from the past that pretty much inspired the rat rod thing today, were far better built, almost NEVER showing any rust damage, and by and large, the various pieces, parts and sheet metal all seemed to have been selected for how well they "fit" together in the builders' eyes. I would submit that nearly all those early rodders and customizers were striving tor good looking cars (at least in their own eyes), not just slamming bits and pieces of junk, rotted out sheetmetal, through some rattle can primer on the whole mess, take it down to DMV for license plates. Just my $.02 worth. Art -
Plant-based plastic isn't all tht new; Henry Ford experimented with making an "acetate plastic" from soybeans back in the 1930's, in fact even had an experiimental version of a '41 Ford Tudor sedan built with body panels made from the stuff. Ford also used soy-based plastic materials in the production of the Model T, the Model A (both used pyroxylin plastic as the surfacing for artificial leather seats in open cars, and for the top material used on roadsters, touring cars and even the fabric top inserts on coupes and sedans. With the introduction of the Model A, Ford used pyroxylin based lacquer for painting body shells as well. Art
-
Harry! I agree heartily! While Alclad and other silver paints have their place, restoration of model car chrome isn't one of them IMO. Art
-
Easy Off Oven Cleaner will strip that enamel, especially since it's rather freshly painted. Be sure to do it outdoors, and wear rubber gloves and eye protection. Spray on, watch the paint blister up, wash off with clean water. Art
-
What is a magneto?
Art Anderson replied to mnwildpunk's topic in General Automotive Talk (Trucks and Cars)
OK, anyone up for a bit of a science lesson here? (actually, I learned this in 7th grade electrical shop class--Dr Lloyd Neher, Dean Emeritus of the College of Technology at Purdue University, was our teacher back then, fresh out of Purdue himself); Pass an electric current through a wire, and a magnetic field is created around that wire (think Direct Current here). With direct current (which is what your car's battery and starter use, BTW), an old rule called "the right hand rule" will show you the direction of that magnetic field, by simply wrapping the fingers of your right hand around a wire (no electrical current is required for this demonstration, in fact it's NOT recommended AT ALL!) with your thumb laying along that piece of wire. Your thump points in the direction that DC current would flow, your fingers wrapped around that wire shows you the direction of the magnetic field created. Now, if you "create" a magnetic field around a loop of wire (by spinning that wire loop between the two poles of say, a "horseshoe magnet), doing so with create a magnetic field around that loop of wire, and that will send electric current THROUGH the wire. That is how a Magneto, even an old-fashioned DC generator works. Now, both a Magneto and a DC Generator will create more voltage of electricity the faster you turn their armature (which is nothing more than a whole lot of wire loops wound around the segments of the armature). Both a magneto and a generator do the same thing, produce direct current, but the magneto puts out lots higher voltage, where the generator puts out more amperage (volts are a measure of "pressure" -- think pressure in a water pipe or compressed air line -- while amperes are the measure of capacity, or how much electricity can be produced). Early automobiles relied on magneto's to provide electricity for the ignition system, which was OK in the years before electric lights, electric starter came about, and the introduction of storage batteries into the automotive equation. Magnetos are actually quite simple, just that concept of spinning a loop of wire between the two poles of a magnet in order to create current. The faster the mag spins, the higher the voltage (and it's voltage that creates spark at the sparkplug), which made magneto's the electrical generation of choice for early automobiles. Ford Motor Company likely made the most magneto's of any carmaker: 15 million plus Model T Fords ALL used magneto's to provide electricity for ignition--Model T flywheels contain dozens of bar-type permanent magnets, which spun in close proximity to a wire coil which surrounded the flywheel, creating direct current which was routed by means of a "timer" (a primitive sort of "distributor") to a type of induction coil called a "buzzer" coil, one for each sparkplug. That ensured a hot spark for each plug in time with the cycle of each of the 4 cylinders. When Ford adopted electric lighting, and an electric starter, a generator, a cutout (early type of voltage regulator) and a battery were added, but from 1908 until June 1927, EVERY Ford car used magneto ignition. Race cars of all types relied on magneto ignition until electronic ignition systems came into use in the 1960's, that's the simplest, and often most reliable way to ensure that no matter the engine RPM's, the spark generated at the plug is the highest voltage, the fattest, hottest spark that could be had. In a street automobile, one can use magneto ignition, but if the car is to be driven on the street, and relies on an electric starter motor (as opposed ot either a hand-crank or remote power starter) then a generator and storage battery are also required. The same is true if a magneto ignition automobile has electric lights--a mag would simply blow out head and tail lights once the engine rpm's reached a certain point. Another use for magneto's, and one that has seen an awful lot of screen time in movies and on TV, is the old "hand-cranked" wall telephone. While those phones relied on 6-volt "dry cell batteries" to provide the low voltage necessary for talking and listening on those phones, a way to let the operator know you wanted to be connected with your Aunt Mabel across town had to be available. Enter the magneto! You picked up the receiver, wound the magneto crank a few rapid turns, and a "door bell Briiinnnngg!" went off at the operator's switchboard. She'd see the light on her board of YOUR phone, plug in, and ask "Number Puleeeze?". I hope I've helped you understand what those old-style magneto's did, why they were used and so on, along with the difference between a magneto and a generator or alternator. Art -
Is flash a measure of quality?
Art Anderson replied to Lunajammer's topic in General Automotive Talk (Trucks and Cars)
Those heavy mold lines were a serious issue--AND Dave Metzner took the factory to task over that, trust me! The Chinese company who does model kits for Moebius is one that both Dave and I have a lot of experience with--to my mind's eye, the first run of the Hudson Club Coupe was an anomaly. Just opened my production kit of the Convertible (bought off the shelf, not my complimentary kit from Moebius) and the body shell in that kit is El Perfecto! Nary a mold alignment problem--in fact this body shell rivals anything done by any model company, anywhere, any day. Art -
Am I Crazy Or Seriously Addicted
Art Anderson replied to Big Daddy's topic in General Automotive Talk (Trucks and Cars)
Yeah, it's an addiction--but what an addiction to have, huh? Just think about it: ZERO calories, non-fattening, won't stunt your growth, no nasty hangovers the next morning, doesn't leave your teeth feeling all fuzzy; all the while guarranteed to be fun and frustrating all in the same breath! CAUTION: Any edible or otherwise ingestible additives may cause your results to vary from this warranty!) Hmm, almost sounds like a formula for a long, happy life to me! Art -
I seldom buy model kits anyplace but a LHS, and I don't quibble too much about the price either. I figure it this way: I WANT that LHS to be there the next time I visit, and the next, the next, the next and the next. If all any of us did was to rely on an LHS for just glue and paint--how long do you think they would stay in business? (having spent a 30-yr stretch of my life working in, and owning a LHS, I can tell you, none of them will last very long selling only paint, glue and miscellaneous supplies. So call me old-fashioned, but trust me, if the time ever comes when model car kits completely lose shelf space in a retail store (Brick & Mortar), it won't be but a pretty short time and you will see NO model car kits, even online. There is a "HIGH COST" to low prices, more often than most people think. Art
-
Is flash a measure of quality?
Art Anderson replied to Lunajammer's topic in General Automotive Talk (Trucks and Cars)
"Flash" on a styrene kit is the result of at least one of two causes: Most think of flash as the result of poorly mated tooling halves, which of course can be true. However, the biggest cause of flash in a plastic model kit, as told to me by a production engineer at AMT Corporation years ago, is improper temperature control. Styrene is very much like pancake syrup in this respect: The hotter you heat it, the thinner the consistency, and not hot enough makes for a much thicker "syrup" of styrene. Too much heat, the styrene gets very thin, and can flow out in the minute clearances between the parts of a mold, resulting in flash. Too little heat, and the plastic may well not flow as it should through all the sprues and injection passages, which results in "short-shot" parts. (Many of use have seen both!). It is a measure of quality, but more in terms of production quality, rather than a severe defect in the tooling, Art -
Those pics of the Marmon Wasp are of the actual, original car--I can even see the Story Board about the car, that accompanies it wherever it is sent by Indianapolis Motor Speedway Hall Of Fame Museum. Art