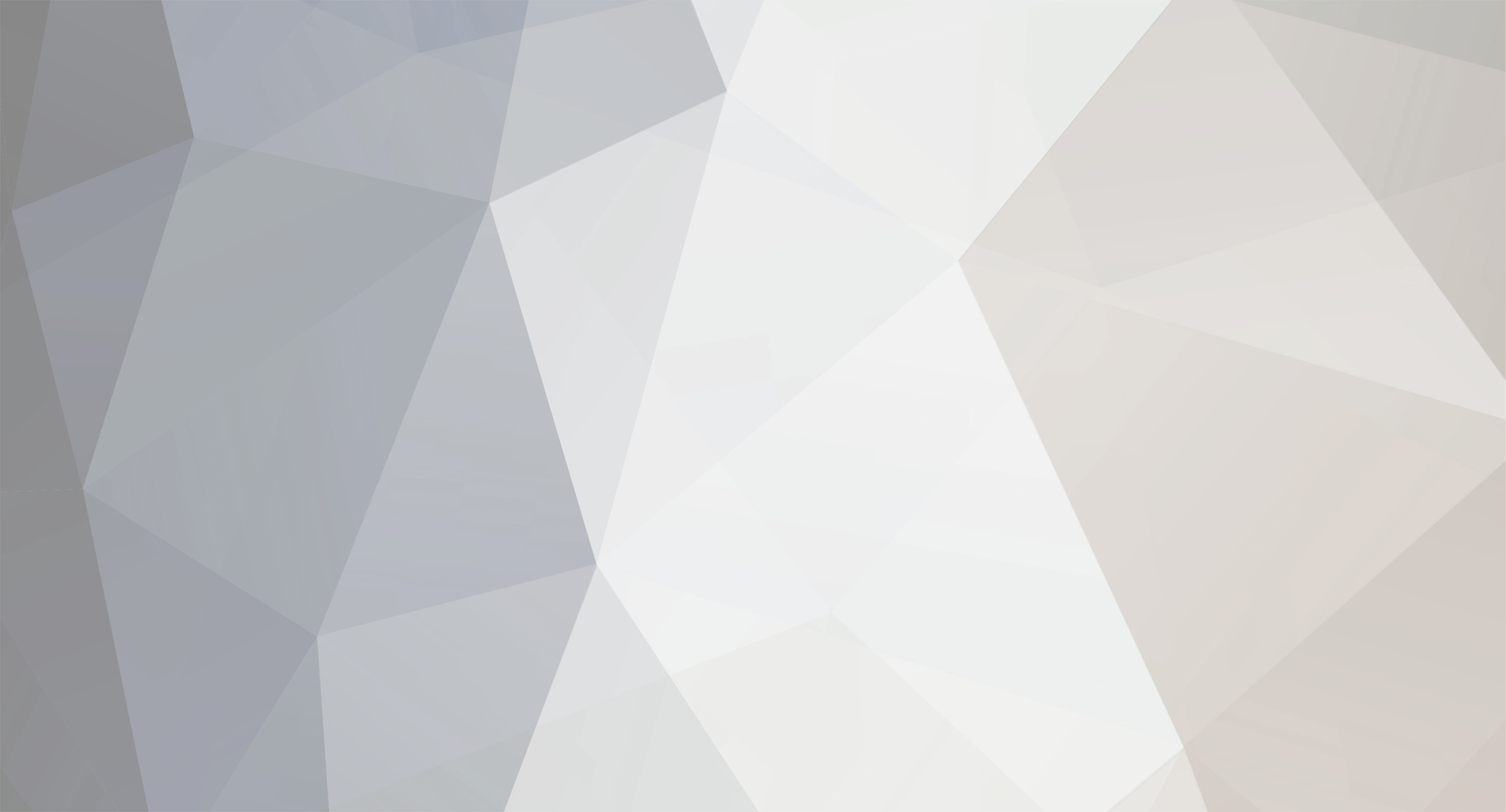
Art Anderson
Members-
Posts
5,052 -
Joined
-
Last visited
Content Type
Profiles
Forums
Events
Gallery
Everything posted by Art Anderson
-
A "Rivet Counter" speaks up!
Art Anderson replied to MrObsessive's topic in General Automotive Talk (Trucks and Cars)
Not always has this been the case! The annals (and the archives of kits from every country where plastic model car kits have been designed, tooled and produced) will have its share of real klinkers! There is one big difference though, from what I've learned over the years: Japanese modelers seem to prefer accuracy and perfection way over low price. Art -
A "Rivet Counter" speaks up!
Art Anderson replied to MrObsessive's topic in General Automotive Talk (Trucks and Cars)
Mr Obsessive wrote: With CAD, 3D scaling, Internet, a plethora of car shows, clubs, magazines, etc-------there’s no reason why a major model company can’t get the details right. I know I've said this before, but here I go again: All the modern technology in the world is great, when it comes to creating plastic kits of scale models, but in all the talk about CAD, 3D scaling, and what other high-tech stuff I fail to include, in the end, the bottom line, there still needs to be the human factor in creating a scale model of anything, particularly cars. However, one simply must understand that CAD was not around when say, the 1955 Chevrolet was being styled and engineered. Why? Very simple. While we view both the real thing, even photographs, and of course our model cars with the same pair of eyes, those eyes see each version (real car, model of it, pictures of it) differently! Let's take a look at the issues here. Given whatever spacing each of us have between the center of the pupils of our eyes, we see the real car much differently than the model. For example, if one looks at an accurately done 1/64 scale model of any car, one will see MORE of that car than is ever possible to see of the real thing. It's called "visual perspective". Our eyes can see, if looking dead straight on, down BOTH sides of that 1/64 scale model, because it fits (when viewing straight on from front or rear) between the centers of both our eyes. But, viewing the real car in the same manner, we can barely see past the headlight bezels on say, a '53 Chevy, so right there is one of the issues. Additionally, with even a 1/25 scale model car, we can see that model at angles, and at heights which can only be achieved for example, by borrowing the fire department's aerial ladder or snorkel rig, or by having the real car on a body rotisserie so it can be spun in front of us at any angle we choose. In short, we DO get to see more of the model than of the real thing. This can really play tricks on us "rivet counters"! In 1984, just as I was opening my own hobby shop (The Modelmaker here in Lafayette IN), Tamiya released a very informative video titled: "The Design And Development Of A Plastic Model Kit". In it, the viewer sees the development process (Tamiya actually had a Porsche 911 in the lobby of their headquarters in Shizoka City Japan). Kit designers with notebooks, measuring tapes and rules and cameras were all over that thing. Next came the drawings (before CAD had reached down to the plastic model industry). Next you could see the making of tooling mockups (back then, a 1/24 scale car was mastered in 1/12 scale, in wood). Finally, with the body shell "done", the patternmaker along with a team of designers, pored over that beautiful 1/12 scale master for the Porsche 911, studying the subtle curvature and contours of every body panel, marking all over the thing with Sharpies or something similar. The narrator described the entire process in English, climaxing with the strong statement (and I remember it vividly!) "It is possible to make a model car numerically accurate, and yet it may not look right! And sure enough, in the next scenes, one could see the patternmaker slightly adjusting some of the shapes, to give the impression of accuracy, as seen by human eyes accustomed to viewing the real thing. With photographs, it's also often difficult to judge accuracy of shapes and contours, as photographs are by their nature, just 2-dimensional. The camera is no different than a human looking at the subject, with one eye completely covered--NO DEPTH PERCEPTION. In addition, photos in magazines, even photos taken by us ordinary mortals at say, car shows, tend to be what are called "beauty shots". Seldom do we get the chance to really capture every little detail, every subtle curve, and certainly not many of us carry measuring sticks or tapes to car shows to photograph with dimensional data, any car. When developing a model kit, any savvy product development specialist will take hundreds upon hundreds of pictures of the subject. In addition to a full walk-around series, he or she will shoot a myriad of pictures taken at angles which show curvatures, a particular line, the shape say of a roof from enough angles to show the curves and contours. Additionally, a product development specialist often will lay an old fashioned carpenter's folding rule up next to a detail, could be a grille (or section thereof), a taillight lens, the door for length, all of that (the carpenter's rule having been marked before hand--every other inch blacked out so the inches show up in the pics clearly!). Now, modern technology has given us the "laser scan", which can "see" depth, and even the curvature of items giving that depth, and the price of laser scanners have come down, WAY down in price, making them attractive for those charged with the development of a new kit. But in the end, making that last bit of realism, it still takes a trained eye, to ensure that once done, the mockup and the final production kit, turn out not only right, but that they look real to our own eyes. Art -
1925 Model T Front Suspension Options
Art Anderson replied to rhs856's topic in Model Building Questions and Answers
Well yeah, quarter-elliptic springs were iffy, unless the builder used two per side, in the manner of say, a Miller 91 front drive race car, even the Cord L-29 front drive. Art -
1925 Model T Front Suspension Options
Art Anderson replied to rhs856's topic in Model Building Questions and Answers
Ace-Garageguy, on 24 September 2012 - 03:26 PM, said: Unfortunately, in 1:1 it's a terrifying arrangement to drive. The axle is very far ahead of the front crossmember, and with virtually zero lateral location of it, steering is rather point-and-pray. Windup of the springs under braking is pretty thrilling too. But, you are missing a few details here: For starters, transverse springs (which Ford used on all their production cars from 1906-1948) require radius rods (either the wishbone setup which was stock on a Ford) to single radius rods (split wishbone--which my '27 T street rod project has) to 4-link) which not only hold the axle square with the centerline of the frame, but also fix the relationship of the axle to the frame and to to the road surface in this way: A Ford front axle's radius rods actually set the caster angle of the front spindles very firmly--by absolutely preventing spring "wrap-up"--which you can see by looking at how that sort of radius rod is "clenching" the axle just as visibly as if you were holding it tightly between thumb and forefinger. There simply cannot be any distortion or twisting of the front (or rear spring) with proper radius rods. This didn't change with splitting the Ford front "wishbone" radius rods, nor does it change with the use of 4-link radius rods either. This is entirely different from the "windup" that leaf springs can undergo with extreme acceleration (rear springs on any car using them longitudinally) or extreme braking (front and rear springs on any car with longitudinal springs on all 4 corners), absent any sort of traction bars. As for any lack of lateral control, it doesn't matter whether the spring is mounted to the frame INSIDE the front or rear crossmember (or, the manner in which leaf springs were mounted to the frame of a stock '32 Ford, for example) or suicide style--in either case, the center of the spring does not move side-to-side, or front-to-rear, period. What does happen with ANY transverse sprung automobile is, that since both ends of the spring must be on shackles, with unevenness in the road surface, and certainly going around sharp corners, the transverse spring will "swing" side to side on the shackles perhaps an inch or so side-to-side. That made for some interesting gyrations (albeit within a very limited range) when driving on bumpy roads. From the early 1920's until the demise of two-spring midget and sprint cars (and not a few Indy cars as well from the middle 1930's into the early 1950's) transverse leaf springs AND suicide front (and often rear as well) spring mounting in this manner ruled. However, given the oval track racing venues, left turns only, those old race cars had their springs shackled on the left side only, the right side used a conventional shackle (not unlike the leaf springs on most cars in the rear from the early 20th Century out to today on say, a pickup truck, shackled at the rear, solidly bolted to the frame at the front). But in the bottom line, it was the radius rods that held the axle not only square with the frame, but also held the axle solidly so as to provide a constant caster angle to the front spindles. Art -
1925 Model T Front Suspension Options
Art Anderson replied to rhs856's topic in Model Building Questions and Answers
The AMT '25 T street rod version has a front suspension based on the '37 Ford tubular front axle. It's not all that bad, certainly considering that this kit was first released about this time in 1961, or 51 years ago. Given that this kit has a suicide front spring perch, you've got some real room for a fairly wide choice of front axles and springs. Here's one, the really nice dropped Model A front axle setup from the Revell '29 Model A pickup kit: Art -
Try Duplicolor or Krylon in rattle cans. I'll defer to others here who are more current as to what is available from both those manufacturers, as to primer. As for clear coats, Modelmaster has clear lacquer in a spray can--I've used that numerous times now with great results. Art
-
MPC and AMT both produced 67-68 C10's back in those two years respectively. Art
-
You really should airbrush this paint on, over an acrylic lacquer primer, as it's a lacquer meant to "attack (bond tightly to) clear lexan RC car bodies. This paint will not be glossy, as clear plastic racing body shells are painted on the inside, the clear Lexan giving it a high shine, so clear coating it will be necessary. But, it does work when used carefully and properly. Art
-
If you look closely at that very shiny base coat that is applied to parts before they are plated (the plating is actually aluminum, which is vaporized in a vacuum tank and transfers almost instantly to the plastic parts), you generally will see that the clear coat has munged, sometimes even obliterated a lot of fine detail. Stripping that clear coat away will reveal, often times, very sharp, clear surface details that you paid good money for. Art
-
Hey Harry, how about this idea?
Art Anderson replied to meaneyme's topic in General Automotive Talk (Trucks and Cars)
Harry! Go for it! Art -
For those of you within driving distance, GoodGuys opens up tomorrrow, Friday, September 21 at 8am, The show is at Indianapolis Motor Speedway, Friday and Saturday, 8am-5pm, and 8am-3pm on Sunday the 23rd. Model car and pedal car contest will be in the Pavillion, which is right across the walkway from the South Tower Terrace (just a bit south of the Bombardier Timing & Scoring Tower, entrance 1A. Other than admission to the grounds, no charge to enter the contest. Models can be entered any time up to 1:00pm, judging will start at that time. For anyone wishing to leave their models on display overnight (there will be security on the grounds, the Pavillion will be locked up) your entry in the contest gives you a free pass to come back the next day. Art Anderson
-
What color do they mean exactly?
Art Anderson replied to epi4561's topic in Model Building Questions and Answers
Shelltone Ivory likely is the same as Chevrolet Ermine White from that year--GM used many of the same colors in any given model year across several divisions. Go to autocolorlibrary.com, you should be able to find out there if that color is in fact a common color for several GM marques. Art -
Co2 gas as propellant for airbrush
Art Anderson replied to Paul Bunyan's topic in Model Building Questions and Answers
CO2 can be gotten in 25lb bottles from just about any beverage wholesaler. You will need a pressure regulator made for use with the extremely high psi in one of those commercial bottles, plus a good quality pressure regulator to reduce the pressure for use with an airbrush. CO2 is a dry gas, no moisture whatsoever, so no water trap will be necessary, and as the gas is also clean, no filter will be necessary either (after all, beverage CO2 is a food grade gas). One thing to keep in mind though,is safety! Break that brass valve off, and your CO2 tank will behave like a rocket--I experienced that at a McDonald's where I was a manager years ago--that bottle (50lbs) fell over, knocked the valve system off of the top, and it shot across the storeroom, and punched a hole in the concrete basement wall. So, secure the tank upright, with a length of light weight chain so that it cannot fall over. Those tanks generally are sold on a returnable basis, a deposit on the tank, and quite possibly on the valve and regulator as well--in effect, you only pay for the gas used. Art -
Also, be careful with BB shot, as most of that is at least copper coated. Some types of paint will actually corrode copper or brass, which will infuse a blue-green "stain" into light colored paint (such as white or yellow). That is a hard lesson I learned perhaps 40 years ago with decanted AMT lacquers, which were VERY similar to our modern Tamiya and Modelmaster non-penetrating lacquers. A small nickel-plated nut or short bolt will do the job. Another caution: The use of too heavy a metal piece as an agitator can increase the likelihood of breaking even a small glass paint bottle, so be careful when shaking that bottle! Art
-
Neat way to decant paint with condiment cups
Art Anderson replied to lanesteele240's topic in Tips, Tricks, and Tutorials
Most any hobby shop with a good RC Airplane section should have these polypropylene (cloudy translucent plastic that is impervious to just about any paint or solvent we modelers are likely to use) in bulk packs. Chances are the polybag package header will say either K&B or Hobbico on them. Also check craft stores--these get used a lot in mixing clear polyester resin for clear resin cast craft projects. They're not very expensive either. and are the same little cups that hospitals use to bring pills to your bedside. Art -
Remember when?
Art Anderson replied to ROY AVERY's topic in General Automotive Talk (Trucks and Cars)
Actually Harry, It's NOT the paint that is expensive--the glass bottle is probably a good 80% or more of that price. In addition, don't forget the weight of glass bottles--a carton of a dozen Testors square bottles is a pretty high density item (speaking as one who over a period of nearlyh 30 years handled thousands of bottles of Testors paints.) Art -
Remember when?
Art Anderson replied to ROY AVERY's topic in General Automotive Talk (Trucks and Cars)
IIRC, Testors PLA enamels in the square1/4 oz bottles hit the market about 1957, at the outrageous price of 5-cents. Art -
The common sizes of K&S tubing translate pretty easily to scale inches in 1/25. Just use the factor .040" to equal one inch, and do the long division (either on paper or with a calculator. For example, 1/8 equals .125. Divide .125 by .040 and you get 3.25, or in 1/25 scale, 3 1/4 inches. Now, who's going to see a quarter scale inch? Practically nobody. Art
-
But, all it takes is for bits of dust or lint floating in the surrounding air to settle on a wet paintjob. Art
-
For starters, 100F has never damaged any kit I've ever owned (if 100F would damage plastic, those of us who use food dehydrators would certainly have ruined a lot of styrene, given the approximately 125 degree temperatures inside most of them!). On the other hand, a model kit left on say, the seat of your car in direct sunlight on a very hot summer day can be damaged--simply because of the much higher temperatures inside a closed car in strong sunlight. Model kits, and even paint and glue get shipped all the time in non-climate-controlled situations (think intermodal containers, semi-trailers, even your friendly neighborhood big brown UPS truck). They get subjected to extremes of both heat and cold, and that's BEFORE you get to split the shrinkwrap. Even wholesale warehouses (or for that matter, a warehouse at the factory too!) are not climate controlled in most cases--and the temperatures at the top of those high shelves can be more than a little bit warm in summer (even the province in China where many model kits are produced is tropical in nature). I have a lot of unbuilt kits, and even some older builds that have been in a lock-n-store for years now, and whenever I've pulled one out, it's still just as good as the day I bought it. All that said, I have had model cars ruined from being in direct sunlight, especially if they were displayed in any sort of closed showcase. That's because if the model is in direct sun, yet encased behind glass (or even a clear plastic single model showcase), the model heats up, then the trapped air does as well, with no circulation--so it just gets hotter and hotter inside that clear but closed space. Eventually the plastic does get hot enough to soften and deform. Years ago, there was a photo that circulated regularly, of a factory built display model from Revell--their highly popular mid-1950's model of the battleship USS Missouri. Now, Revell used to issue factory built up and finished samples of new kits, each in a clear plastic display case (Model companies did a lot of that through the mid-1960's--a hobby shop could order a case lot --12 kits--ahead of release [so-called "pre-orders"] and when those arrived in their store, along with them came a display model) Back to the USS Missouri: A newspaper photographer shot a pic of a factory display Missouri, her bow and stern drooping downward, her midship sagging, supported by the display stands included with those kits. Again, sun's heat, trapped inside a clear case, in this case in a store show window which let bright sun straight in. A lot has been said about the so-called "vinyl (Revell) tire disease". That's caused mostly by chemical action, rather than simply heat. Polyvinyl Chloride (PVC) is by it's nature a hard, dry plastic, which has been around for more than 100 years. Take a scrap of PVC pipe for example (the white plastic pipe one finds in the plumbing department of just about any hardware or home improvement store) and lay it up against a piece of styrene, and there will be virtually no ill effects suffered from that piece of plastic pipe. It's when a "plasticizer" is added to PVC to make it soft that troubles can happen. Early AMT 3in1 kits (1958-60) had rather hard black PVC tires that builders had to PRESS the wheels into, and that didn't attack the styrene wheels, not even the clear coat over the chrome. But, when AMT and others began to make kits with soft, rubber-like vinyl tires, the problem of tires sometimes attacking and softening styrene started to creep in. It was not unusual to buy a new model car kit, open it up, only to find the imprint of a tire in a hood, deck lid area, or worse, the clear styrene "glass". Revell had the worst problem of all model companies, given that they concentrated on really soft vinyl tires. However, by the late 60's, pretty much all model companies were able to access PVC feed stock for their molding machines that didn't have nearly as much plasticizer in the mix, and the "tire disease" pretty much went away for the most part. However, one can experience the very same thing even today: Just wrap up a model car or even parts in Saran Wrap (or any other clear clinging food wrap, and within days, you can have ruined paint, ruined chrome (I learned that the hard way early on with AAM, when we tried wrapping up chrome parts with the stuff) costing a lot of time, and not an inconsiderable amount of money to replace several hundred sets of chrome (we went to ziplock poly bags immediately--end of that problem). Certainly by the late 70's, PVC monomers (the plasticizers) went away in favor of other material, after a huge cancer scare in the injection molding industry. Had Dupont and other petrochemical companies making PVC stocks not figured out how to get rid of the hazardous stuff, PVC would have disappeared, it was that seriously regarded by both government and industry. But with the rise of China and other Pacific Rim countries, especially when they started producing model kits, the problem came back, UNTIL they learned the errors of their ways, just as had manufacturers here in the US. For that, and all the other reasons mentioned, it makes sense to wrap up PVC tires in poly bags (even sandwich bags work!) if one is going to store a model car kit for any length of time). Along the same lines, it makes good sense to put decal sheets into a ziplock bag as well, in order to keep humidity from causing the paper to swell up and curl. But back to the main thrust here: In general, the extremes of weather, both heat and cold as most all of us experience them, really won't harm most of our models, either built or unassembled, as long as one keeps them out of direct sunlight in the summer. Certainly, freezing temperatures don't, absent any major putty work--and that is from my experience as well. Long-winded, I know, but all of this comes from my years of experience in storing both unbuilt kits and finished model cars, some of them for a decade or more, and in Indiana, we experience both extremes of heat and cold. Art
-
Paint Booth Venting
Art Anderson replied to FASTBACK340's topic in Model Building Questions and Answers
Pat, I've now used two commercially available spray booths, both with fairly powerful squirrel cage blowers for extracting air through filters: The old Badger unit from the late 1980's (too small for my purposes), and a Pace Peacemaker which I really like a lot. The Badger used fiberglas furnace filter media, which is fairly course, and that did leave a very light amount of overspray "dust" on the screen in my then-apartment bedroom window, which I simply removed with my vacuum cleaner. The Pace uses a HEPA grade corrugated home HVAC filter, and when fresh, that filter passes the air with quite a bit of force. For those living in apartments, it is critical to avoid leaving any permanent "stains" behind from our hobby work. I have found that with the exception of the little bit of dried overspray dust that the rather primitive Badger unit left on the window screen, I've never had any permanent discoloration of anything either inside or outside of my apartments--and even more importantly, using those spray booths has prevented any complaints from neighboring apartments as to the smell of paint, or any overspray dust. In the bargain, my Pace is literally conversation quiet--step out of the room, you can't even hear the thing run. Art -
For starters, any chunk of any sort of debris large enough to be seen in a freshly sprayed (from an aerosol can even) paint job more than likely didn't come from the spray can, given the very tiny size of the opening in the spray valve. I'd be checking my work area for dust and dirt, and if it's there, vacuum it up. Also, if you are spraying with an open window nearby, be sure it has a screen in it, and if windy outside, postpone spraying until the winds die down. Just a couple of thoughts on your situation. Art
-
Adventures in Scale Modeling was sponsored by, and at least partly funded by, Testors Corporation, with help from IPMS/USA. Each of the seven segments showcased a different subject area of scale modeling, heavily weighted, of course to plastic models. The series ran on PBS for a couple of years back in the late 1980's, and featured known model builders of the time (one of them, when they discussed 1/72nd scale aircraft, was a local model building personality, Mrs. Doris Reeves, AKA the "First Lady of IPMS" (the late Doris Reeves was one of the founders of IPMS/USA in the early 1960's, and quite well known around IPMS.). Testors offered VHS tapes of the show segments for at least a couple of years after the show left the air on PBS. Art