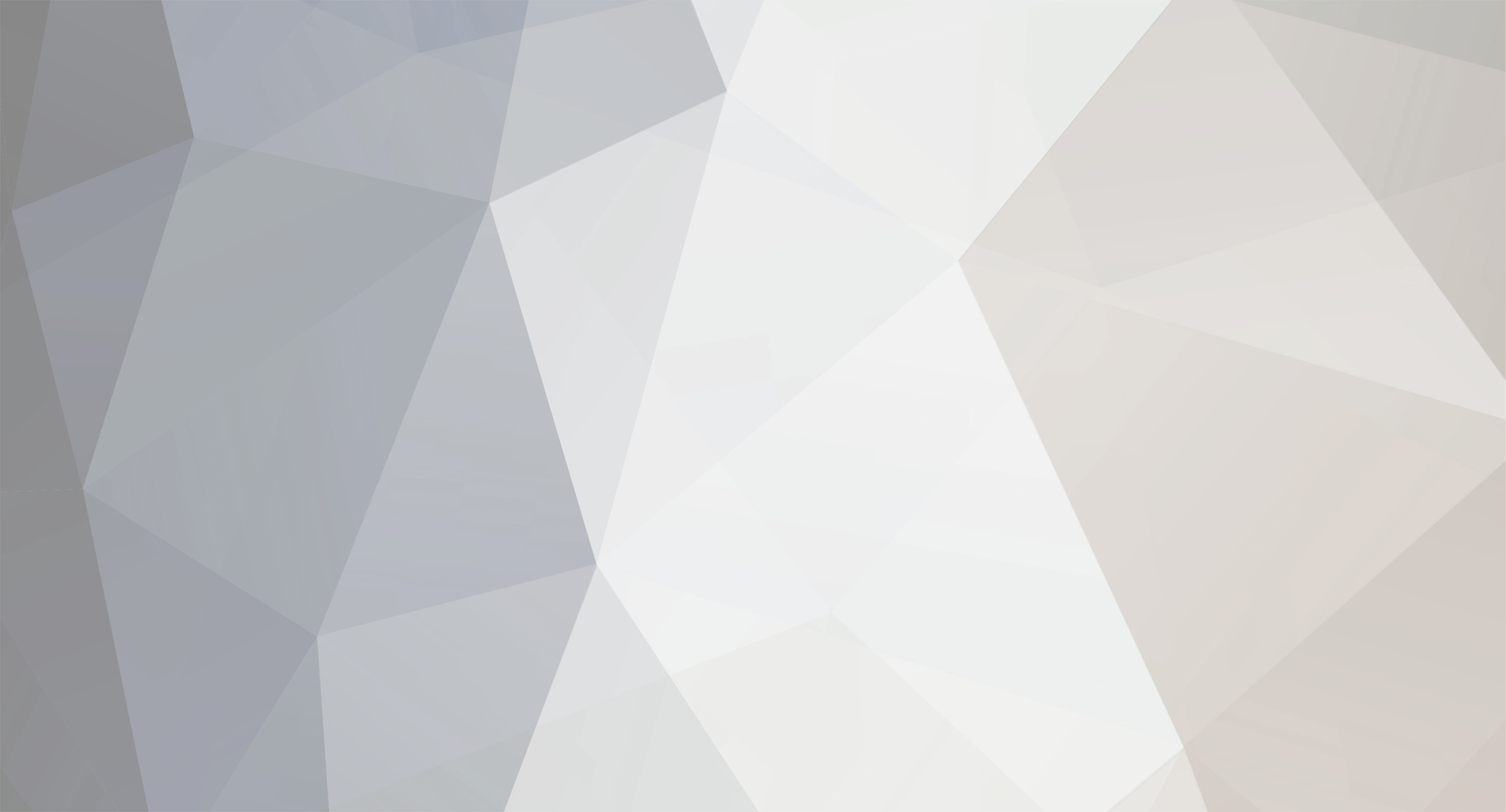
Art Anderson
Members-
Posts
5,052 -
Joined
-
Last visited
Content Type
Profiles
Forums
Events
Gallery
Everything posted by Art Anderson
-
She does look to be headed for a "wardrobe malfunction" for sure! Anyway, the figure is from Motorhead Miniatures (Paulette #394), www.motorheads4u.com Art
-
Finished this one this afternoon (still have to go to ACME plate maker, make an Indiana license plate for it though): Art
-
A '35 Ford transkit would require the grille, hood, fender & running board unit (all 4 fenders on the 35 are markedly different than those for a '36!), and a set of 6:00-16 Ford wire wheels and hubcaps. 1935 was the last year that Ford used wire wheels on all cars and pickups, they were 16" diameter. Art
-
This is a little trick I'd thought of doing for several years: How to recreate the clear plastic medallion (badge of a particular marque of car) on a model. Just a bit of history here (like I ever forget history, huh?). In the early 1950's, with the advent of injection molding of plastics, carmakers discovered a way of giving their products a striking, very visible full color "crest" (if you will) of their marque that could be attached to a hood, a trunklid, even made into a horn button for the steering wheel. These were molded from clear acrylic (think Plexiglas here), having the detailing of the crest engraved into the back side. By spray-masking both transparent colors and opaque colors on the back side, then vacuum-metalizing aluminum over the back side of that (same process by which we modelers get chromed plastic parts, BTW), and the front or outer surface having a polished, somewhat curved shape, they could get a very visible, almost jewel-like crest that spoke volumes about the car it was mounted on. At some point in the 50's, virtually every car of note carried these. Now, I've (as probably many of you here, have foiled (or used the ocasional separate plated hood or grille crest) and then hand-painted in the colors of say, a Chevrolet Crest. But, how to make it look real, take it to that next level? Moebius made it easy with their Hudson kits, by providing a neat little decal to be applied to an appropriately shaped flat spot in the middle of the top bar of the grille. Put that decal on, and you KNOW you are looking at a Hudson grille--but yet, it's still flat, no 3-dimensional character to it. So, what to do? With my '53 Hudson Hornet Club Coupe, I decided to go out on a bit of a limb, try making that medallion (crest) truly 3D, by using Devcon 5-minute epoxy. This was done, first and foremost, by mixing the epoxy parts together on a Post-It Notes pad with the large, smooth, rounded end of a paintbrush handle, to minimize any airbubbles (tried it with a toothpick, and that stirred in a lot of bubbles!), then applying the mixed epoxy to the badge area, over the previously applied decal (which I let dry for several hours!), being careful to use only a small amount of epoxy on the end of a toothpick, dragging that carefully around to just the edge of the flat space Moebius provided. Here is the final result--one very accurate Hudson Crest! Notice the difference? Now it has a clear, but 3D presence, which makes that little decal detail really pop, which it should (the real ones stand out prominently!). Now I know that Devcon Epoxy may well "yellow" slightly with age, but then so does acrylic plastic that is exposed to sunlight and the various gasses and pollutants in the air, so IMHO, it's all good. Here's a look at the grille of my '53 Hornet Club Coupe, on which I first tried this little gimmick, just to show one more time what it is: Oh, and by the way, Norbie approves of both the techique, and this message. Now, back to your regularly scheduled programming! Art
-
Custom Tire Material
Art Anderson replied to tsroark's topic in Model Building Questions and Answers
Delrin makes an excellent raw material for turning in a lathe, and should be available in round bar stock at any good industrial plastics supply house. However, acrylic (think plexiglas) bar stock works much better, even though it has to be painted. The trouble with PVC pipe is, it's fairly thin in section, and has to be laminated to get the thickness needed for tires. Art -
Meijers is carrying models again.
Art Anderson replied to 2000-cvpi's topic in General Automotive Talk (Trucks and Cars)
Walmart, unlike the other big box retailers, didn't start out in the big cities (ala KMart, Zayre, Woolco, Shopper's World, EJ Korvette etc.), but rather as small town (think county seat towns in rural middle America) variety stores, eventually growing into small town discount department stores, then by the late 80's/early 90's moving into bigger cities, even the outskirts of major metropolitan areas. Art -
I've often referred to this very thing as "the illusion of real". Let's face it, short of replicating EVERY single part, piece, nut, bolt, washer and cotter key (does anyone even remember cotter keys anymore?) exactly to scale, then figuring out just how to assemble those thousands of bits and pieces in exactly the same manner as the real car, we can only have that "illusion" that somehow the model we are building will be an exact scale replica. Dealing, as nearly all of us on these forums do, with molded styrene plastic model car kits, just think of all the compromises that must be made (and they are inevitable) in order to come up with a kit for a scale model that when built and finished, looks like the real McCoy but miniaturized. Just the mere act of creating a one-piece body shell for a model car is compromise all over the place in so many ways. Given that the real car's exterior sheet metal is made up of upwards of 20 individual sheet metal stampings (perhaps even more), BEFORE any trim goes on, while we modelers expect that body shell to be made in one piece except for an opening hood, perhaps an opening trunk, and it's very easy to come up with a body shell having at least some compromise someplace, in order for it to come out of the molds at all easily. And, even IF the shapes and contours are exactly copied in miniature, there will be necessary compromises here or there due to the required material thicknesses (an exact scale thickness body panel in say, 1:25 scale will be gossamer-thin, impossible to even pick up without denting it beyond use. Extend this thinking to every part of a model car, and the required compromises multiply. All that said, if the model looks right once built (and that's as much subjective as objective) then it seems to me that that's about as far as it all can go. Art
-
IMHO, "Scale Accuracy" can only carried to a certain point, at which the law of diminishing returns sets in. By this I am referring to an endless search for more perfection, more scale correctness with each model kit, or each of a builder's projects. At some juncture, there will be a "tipping point". For certain, no model car kit that any of us likely would afford will ever have scale thickness body surfaces--that would be foil thickness or at least very close to that. Not likely we will ever see exact scale reproductions of fabric, leather or vinyl interior upholstery, due to the limitations of injection molding tooling. Scale thickness paint jobs? Not hardly, not even with the finest of airbrushes used with the most delicate of techniques. However, we can and should expect to be able to create "an illusion of realism, of accuracy", starting with the model kits we buy (and there are some out there that do fill that bucket pretty nicely. Art
-
Seriously, Ford first offered a pickup based platform stake truck in 1937! The bed was raised up above the frame of the truck by means of heavy oak planks, which were shaped to fit the curvature of the rear of the frame, but flat on top. On this was mounted a steel framed platform bed with wood flooring. The width of the bed required Ford to notch out the insides of the tops of the pickup rear fenders, which gave a very stylish, finished look to the whole package. This project necessitated a lot of thought, and figuring, of dimensions, and just how to go about making components that were identical, as well as being straight and true all along the way, so the the removable stake fences are interchangeable side-to-side and front-to-rear. That meant jigs for assembling them. The first jig turned out to be not quite square, so a second jig had to be made for the side fences, me making darned sure it was square this time around. That jig was repeated in design to assemble the longer, 3-post end fences. The bed floor is made from 1/16" x 3" basswood, scribed on the underside to give the effect of individual boards, while on the top, scratchbuilt skid strips were made to cover where those joints would ordinarily have been seen. Skid strips were made from .100" Evergreen strip .010" thick, the raised ribs on either side are half-round stock made from .020" Evergreen rod stock, scraped down flat on one side, using a brass bar with a milled Vee groove in it, sized to fit .020" styrene rod. The individual bolt head detail was made by inserting short pieces of .020" rod into holes drilled into the flat part of the skid strips before the half-round was added, then rounded off to look like round-head bolts. When done and painted, these should be very convincing. The side and end rails have stake pockets within them, and were made with .015" flat styrene strip for the inner and outer surfaces, with blocks of .060" styrene strips making the stake pockets, spaced to fit the stake posts on the fences: Under the bed floor, you can see the heavy wood beams that support the bed on the truck frame, made from 1/8" X 1" basswood, carved and sanded to fit snugly on the model kit frame rails. More soon! Art
-
Except, Ford didn't use lacquers on any cars until 1926, and the return of colors other than black on Model T's. At the outset of Model T production in the summer of 1908, Ford, just like every other automaker, used a long and laborious process of brush painting, starting with enamel primer that had to be let dry, and then wet-sanded smooth, over which colored enamel (Model T's came in pretty much any color EXCEPT black then, although black fenders, running boards and splash aprons ruled at Ford through the 1932 model year). was brushed, then set aside to dry. Now, anyone here who's in their 50's and older surely remembers the old "4-hour enamel paints" that were common well into the 1970's, which took upwards of 4 hours to dry to "tacky", and 24-36 hours to dry tack-free, and several weeks to dry hard. Essentially, those early colored enamels were little more than old-fashioned varnish, with pigment added. After the color dried, and was wet-sanded smooth, clear varnish was brushed on, at least a couple of coats, and then the bodies were set aside in large warehouses to allow the varnish to dry and harden thoroughly. Now, for a car company making fewer than a thousand cars a week, that was not nearly the problem that Ford faced by 1913, when their production soared past 350,000 cars for the year. Ford Motor Company bought their hand tools from Stanley Tool Company back then, and given that chrome plating of steel objects hadn't yet been figured out (that happened at GM in the mid-1920's, and was first introduced on cars by Oldsmobile in 1928), Stanley used a black "japan" enamel that was baked on their hand tools, which gave a finish that while in hard use could chip or scratch, would not just peel and flake off, unlike the enamels then in use on car bodies. The official history of Stanley Tool Company shows that Ford was intrigued, Henry Ford tried to obtain the formula for that Japan enamel (Japan drier is a material well-known to artists who paint in oils--it's what makes artist oils dry reasonably quickly); but Stanley considered that formula to be a trade secret, so no deal. Ford Motor Company allegedly tried to buy out Stanley, but that company's directors refused to sell. Ultimately, Ford bought black Japan enamel through Stanley, and that is what they used through 1925 for the entire car, all metal parts. Ford's method of applying Japan enamel was two-fold: Small parts, from iron castings such as engine blocks and heads, to springs, frames, front and rear axle assemblies, to fenders, hoods, splash aprons and radiator shells, even dashboards, was to dip them in Japan enamel, then run those parts through low-temperature infra-red light heated baking ovens, which produced a hard, baked enamel finish. With body shells (certainly open bodies such as roadsters and touring cars--which were the vast majority of Model T production until about 1926 or so) those bodies were assembled, and trimmed, with their black "artificial leather" upholstery, and then run down a paint line conveyor, where workers sprayed (or rather "squirted"!) black Japan enamel from pretty much ordinary garden hoses and nozzles. Below that line was a long trough, which captured the excess paint that ran and dripped off, from where it was drained, filtered, probably a bit more thinner added, and then it was recycled back through the painting process. The painted bodies then traveled through an even lower-temperature drying oven several hundred feet long, the temperature controlled to a level low enough so as not to damage the considerable wood framing from which those early car bodies were built (the only sheet metal pretty much was the body surface back then). This dried, but didn't really harden the enamel so it was not uncommon for a new Model T to be delivered by a dealer with areas of the paint soft enough to take a permanent fingerprint (a lesson which my 9yr old father learned to his dismay in the late summer of 1913!). Japan enamel could have been pigmented in any color, but in baking, lighter colors tended to darken, or "burn" just a little bit, so black it was--and strictly for mass-production reasons, no other. Dupont developed the first sprayable lacquer in 1922, Duco. It was introduced on automobiles at GM in 1924. Ford went to lacquer for body colors starting in 1927, but retained Japan enamel for fenders and all sheet metal below the body sills though 1932. Art
-
No, Harry! Model T's came with brass radiators (1908 to sometime in 1916) and all brass acetylene headlights and all brass kerosene cowl lights and taillamp well into 1913 when black painted steel light casings replaced brass, leaving brass only for the rims of the lenses, and that went away by sometime in 1915. Sometime in 1916, the small, angular brass radiator and hood went away, in favor of a taller, wider radiator, contained in a stamped steel shell, painted black. This style radiator and hood continued through 1925, but got taller and wider in late 1922-early 1923, to the size and shape seen on the AMT '25 T kit. Nickel plated radiator shells and headlamp bodies started in 1926, and continued through the end of Model T production in the US in June of 1927. Just a historical note here: With Model T, there really weren't any "annual" updates or styling changes. Rather, the changes in lines, sheet metal shapes, transition from polished brass trim items to plain black all happened as those parts were developed, put into production. As "running changes", Model T Fords could be said to have followed something that Volkswagen used to advertise back in the late 50's and early 60's: Most any part from a "new" Model T would fit any earlier Model T, and for the most part, that was absolutely true. Art
-
Over the years (( started building model cars right about this time in 1952--age 8, 60 6yrs ago), I avoided taking any commissions for building model cars. About the time Monogram released their 1/72 scale B-52D (1967), while working in a local hobby shop, a middle aged couple asked me what I would charge to build up one for them (their son was piloting one out of Guam to North Vietnam then), and I told them $25, which at first they declared that was expensive, I was building stuff for fun. I had to explain to them that I built my models for me, for fun; but if I did it for someone else, the fun part went away--and they finally understood. So, $25 it was, on top of the kit, and paint. I built the thing, delivered it to their home, they were pleased, and paid me cash money. It wasn't until late 1974 that the idea of building model cars for pay surfaced again, only this time it was AMT Corporation calling. They had learned that I had a bit of a reputation for building models of cars that had faced the green flag at Indianapolis on Race Day, "would I be interested in doing some Indy car builtups for them?". I said yes, and that started a 7-yr relationship with AMT Corporation and subsequently, Lesney-AMT, for box art, catalog, trade show display, and presentation models. That gig pulled in $2500 to perhaps $3500 a year (Dennis Doty built a lot of these models for AMT as well, until Lesney Corp filed for bankruptcy in early April 1982, owing me nearly $3000 (they paid me off in full plus interest upon settling the bankruptcy that August.) In January 1989, I started All American Models, and the model-building for pay thing started up again, this time in earnest! What had been a hobby quickly morphed into more than a full-time job, and model building for fun ceased to exist here. So yes, I've done model building for profit, but no longer. When I have time to build, it's just for me, and me alone. Art
-
injection molding issues fix?
Art Anderson replied to Brian_B's topic in Model Building Questions and Answers
What you may be seeing is the "flow" pattern of the molten plastic into the molds during the injection molding process. Styrene plastic is heated to the consistency of warm pancake syrup, then injected into the molds under tremendous pressure (upwards of 100-tons or more) and then the molds are cooled by circulating cold water through a water jacket which is quite similar to the water jacket in your car's engine. This solidifies the molten styrene so that when the mold is opened, and the parts ejected out, they are solid plastic parts. However, all the stresses pressed into those cavities of the mold will be present in the resulting parts, and upon painting with certain types of paints (lacquers, for example), those stresses tend to be "relieved" at least a bit, showing up as a pattern of "frosting", even severe crazing on the surface of the model part (body shell). Sometimes, those flow lines, especially on the largest surfaces of any model car kit (the body shell) can be visible, even felt at least slightly, but they can be dealt with almost always. Art -
Model Master enamel paints
Art Anderson replied to Ironman63's topic in Model Building Questions and Answers
To elaborate here a bit: Model Master military colors follow, where US military colors are concerned, the United States General Services Administration "Federal Standard (FS)" number code system. The FS 595a color list shows every color of paint specified for just about anything the Federal Government buys; aircraft, ships, military field vehicles, even office furniture and the paint used both interior and exterior on buildings and other structures. All ModelMaster military colors which are mixed to match the colors used on USAF, USA, USN, USMC and Coast Guard aircraft will have a 4-digit number for their stock number. To tell if the color is gloss, semi-gloss or flat finish, look at the first digit of the FS number on the bottle or spray can: 1- for gloss, 2- for semi-gloss, and 3- for flat finish colors. ModelMaster colors which do not have an FS number are those colors which they make to match either the military colors of other nations, or US military colors used prior to the development of the FS system (as regards US Department of Defense), or are common colors which we builders might use across all subject areas of model building. Those colors will have the word gloss, semi-gloss or flat (perhaps even matte, which means "flat") as part of their color name. Hope this helps! Art -
Could be both, actually! The only way to tell is to assemble the model, then dig out the information as to dimensions, and slap a digital calipers on it (I bought my digital calipers at Harbor Freight, 3 yrs ago, for $12, about half the price of a new model car kit today!), see how long, wide and tall, AGAINST known dimensions of the real thing (i.e. from The Standard Catalog seris of American cars, such reputable magazines as Hemmings Classic (or Muscle) Cars (both picked up were their older title, "Special Interest Autos" left off several years ago). See which is accurate, the 1/25 (easy conversion to scale--.040" equals 1 scale inch in English, for all intents and purposes 1mm equals one scale inch in Metric (I know there are dozens of engineers reading this who will insist that it's not EXACTLY 1mm, but it's far closer than perfectly to the nth degree, given that we work with files, sandpaper, and razor saws, not precision machine tools--got that?). Now if you want to compare further--the difference between the same model subject in 1/25th 1/24th is 1/25 scale is 3.41% smaller. That is far less than the photographic comparo's I am seeing in this thread, seriously! 3.41% means that 100 inches in 1/25 scale is 3.41 inches shorter than 100 inches in 1/24 scale. But in the end, no comparison of a 1/25 scale kit of whatever subject you want to talk about with the same subject in 1/24 scale, without knowing the actual dimensions of the real thing means not a hill of beans UNLESS you know that at least ONE of the two kits in question is TRULY accurate dimensionally. To do oherwise is very much a case of the "blind leading the blind". Art
-
James, back in 1969, when I had my first exposure to Computer Science in college--THE watchword was "GIGO" which stands for "Garbage in, garbage out" (meaning of course, no computer knows anything more than what imput it receives) CAD/CAM is virtually omnipresent in model kit tooling and design nowadays (drawing boards, draftsmen with pencils, and pattern makers carving 1/10 or 1/12 scale solid wood body mockups and all the rest of the parts for a new model kit have all but disappeared), trust me on that one--I've seen more than one example of it. It is now possible, for example, to 3D scan a real car, come up with the essential CAD files for scaling the bodywork down to any scale you want. However, there are some things that cannot be gathered by scanning, short of tearing down that real reference subject to the last part, nut and bolt, so a lot of work has to be done from photographs (often multiple shots of the same part or detail), and from that, CAD files created). Typically, a minimum of 200-250 photo's can be taken of the real, 1:1 reference subject, not just of the whole car, but any details that need to be shown more clearly. In addition, one thing that still remains in the toolbox for a photoshoot is an old-fashioned folding carpenter's rule, with every other inch blacked out, so that when the rule is laid over say, a vent wing, or to ensure the correct location for a badge or script, the kit development people in the tooling shop can see clearly what the spacing is to be, top to bottom--left to right. Factory information is an absolute Godsend, but with many cars, such archival historical references are nearly non-existent, particularly with an orphan car (the Hudson kits come to mind here, being orphaned when AMC dropped Hudson 55 years ago, and that after closing the Detroit plant in the summer of 1954--tons of reference materials likely were lost forever then!). With modern cars or trucks, those which were designed with CAD, often the manufacturer will have those CAD files available, and if one has a license with the manufacturer in place prior to developing the kit--most times, the automaker will be more than happy to supply those to the licensee (I've dealt with that in my past life as a product development specialist for Johnny Lightning diecast cars) and I am pretty sure that just about anyone developing new plastic model car kits has had, and is still experiencing that sort of input. As for your comment (lament?) about model companies being perhaps lazy or cheap by holding onto the past--if you mean by that they are unwilling to do new renditions under today's state-of-the-art technology, I can't agree that this is the situation, nor the reasoning: I would be pretty certain that anyone who's ever been in the position of developing new product in any area of scale models, has gone through the process of proposing that their employer (or their company that they own themselves) offer a new, perhaps better version of an existing product. Now, we all know accountants--generally speaking, "Bean Counters". In any properly run company of any size, the accountant serves at least two functions--that of a "record keeper" as well as being an advisor to the owners/managers. One question the accountant (today the buzz words are "Chief Financial Officer" --CFO) will ask is along the lines of "If we invest X dollars as you suggest, how many more units will we sell of that subject. Trust me: If one does not have a ready and decent answer to that question, more than likely the idea will be turned down (reasoning: Why spend scarce capital for no additional gain?). If a product is still selling well, and there is no assurance that spending money in 6-figures will result in added gain to the company--then why do it? Now of course, there are other considerations, to be sure, but the financial question is sure to come up. Case in point: AMT Corporation released a 1957 Chevrolet Bel Air Sport Coupe (hardtop) in early 1962. That kit stayed in continuous production for the next 34 yrs. It appears that AMT/Ertl, seeing the very real possibility that Revell-Monogram could well expand their fledgling "Tri-Five Chevy" line of kits to include that subject (actually, that original AMT '57 Chevy hardtop, nice as it seemed in 1962, simply was way outdated by modern standards in 1996). So the die was cast--make new, more up-to-date tooling that reflects modern model car builders' tastes and expectations, and in the bargain, try to rectify the numerous and obvious (to the trained, knowledgeable eye) scale and detail problems. So they did, and the rest, as they say, is history. No other model company has ever done that version of a '57 Chevy hardtop in a full detail 1/25 scale kit. Protect your position, but that gets done only if a company's top selling product is in danger of being overshadowed by a competitor. I hope this helps answer some of your concerns. Art
-
Harry, on one point from the person whom you answered here, with certain "categories" of model car kits, 1/25 scale is pretty much proven to be what the vast majority of builders want. Just look back 20 years ago, when Monogram brought out their first new tool of a factory stock US car in 1/25 scale--sales of that '59 Cadillac Eldorado convertible took off like a rocket, compared to many of their 1/24 scale US street automobiles. I suspect the same holds true for drag racing cars and street rod kits. However, due to their popularity having been established in 1/24 scale kits, such as Nascar, Foreign sports and passenger cars--it has never made any sense to try and market those in 1/25 scale--their category as model kits was largely established in 1/24 scale (not dissing 1/43rd here, but a comparison between 24th and 25th scales), long before Revell Monogram decided to make the change to 25th scale for Detroit iron. I owned The Modelmaker Hobby Shop here from 1984-1992, and if only I'd collected at least 50-cents for every lament I heard "Why don't they make (such and such) in 1/25 scale> Art