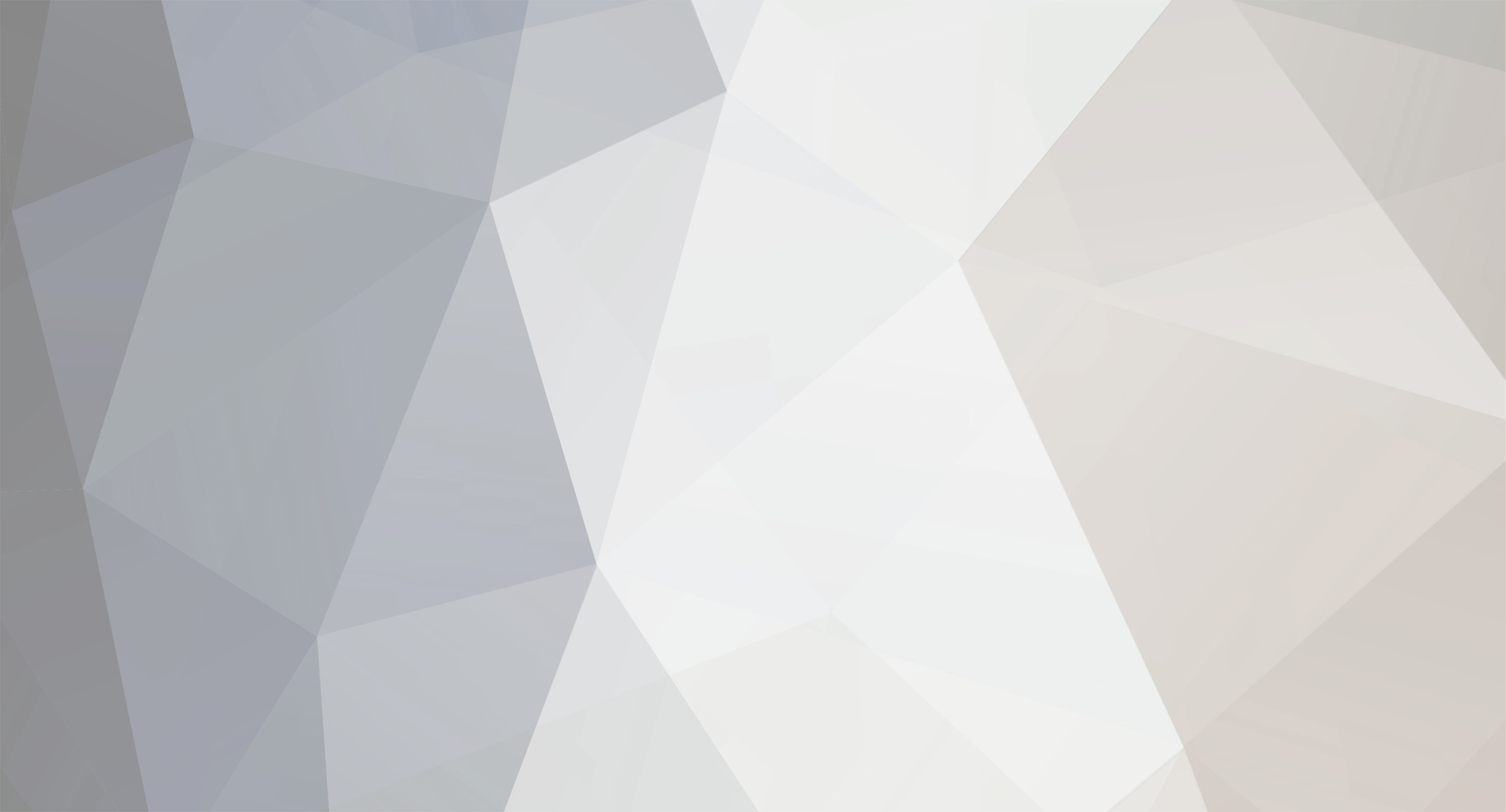
Art Anderson
Members-
Posts
5,052 -
Joined
-
Last visited
Content Type
Profiles
Forums
Events
Gallery
Everything posted by Art Anderson
-
I spent most of the years 1963-73 employed in a very large hobby shop, and there is one glaring thing that sticks out about this 1968 Corvette kit: AMT Corporation didn't shrink wrap their kits in 1968--not until at least 1969-70. In addition, the wrapping used at the time by most other companies didn't have that heat melted "seam" around the box either. Those companies that were clear wrapping plastic model kits were still using mechanical wrapping and sealing processes. A sure fire way to tell if a model kit has been "re-shrink-wrapped" from the heat-melted seam era: Look closely at the shrink-wrap itself--there should be a hole in it somewhere on the top of the box--AMT used a common soldering pencil, on an arm that came down, the soldering pencil melted a hole in the wrapper simultaneously with the heat shrink operation--this kept the wrap from trapping air underneath. Art
-
Off white roofs on 50's cars
Art Anderson replied to Jon Cole's topic in General Automotive Talk (Trucks and Cars)
Jon, If you are doing a factory stock color scheme, Hudson had no white in 1952-53. They did have "Honey Cream" which is about a Pantone shade lighter than MM Phoenician Yellow, which in real life comes across as a slightly yellowish white. Art -
Off white roofs on 50's cars
Art Anderson replied to Jon Cole's topic in General Automotive Talk (Trucks and Cars)
having here, a Martin-Senour (NAPA's virtual house brand of automotive paints) chip book that covers the 45 years from 1947-92, I can state that nowhere in those paint chips is there a "pure" (as in appliance) white; none, nowhere, no how. In fact, almost all automotive paint colors from those years, certainly from the beginning of my color chip book through at least the late 1960's are fairly muted, only black being a really stark color. Why? My theory is, and has been for years, that paint pigments for years have been less than stable in UV (sun) light, prone to both fading and color shifting over time, with the purer pigments being the most suseptible. Also, with lighter colors, certainly white, visible air pollution had to be a factor (bear in mind, in the US, and indeed throughout Europe well into the 1960's, a majority of buildings in larger cities were heated with coal, with the resulting brown smog and all the brown particulates that entailed--and given the nature of lacquers, even enamels of the day, discoloration would have been a problem. Hence, virtually all white paint chips in this book actually appear to be at least slightly cream-colored, some darker, some lighter, but with a fresh paintjob, teamed up with another, darker color on the lower body, they looked very much snow-white, but that had to be an illusion, now that I look back on it. To have seen those lacquers mixed for use in a body shop, almost to a color, black toner was one of the first toners added to just about every can of paint, again, muting the colors to some degree. Art -
Question in regards to decanting spray paint
Art Anderson replied to fatkidd's topic in Model Building Questions and Answers
To put it quite simply: Some colors, and some kinds of paints may well not be available in bottles, and of course, vice-versa. Far more places stock the rattle cans of auto touchup paints than stock the corresponding 'scratch and fix" bottles of the same stuff. Art -
As for the active ingredient in Easy-Off, yellow label: It's Sodium Hydroxide, which chemical your grandmother knew as "Lye". Lye is a base, highly caustic, which is why it strips enamels, some lacquers, and of course the micro-thin aluminum we know as vacuum-plated "chrome" model car parts. Lye will "burn" your skin, and is even more unkind to mucous mebranes, which means your nose, mouth and throat--which is why the overspray fumes (even the fumes given off from dissolved crystals of lye (Lewis Red Devel Lye), so adequate ventilation and PPE (Personal Protective Equipment) is a very good idea. Personally, I use Nitrile examination gloves (those blue or purple "rubber" gloves that EMT's and police officers use when investigating, or treating victims at accident or crime scenes. Nitrile gloves are non-allergenic (many people have an allergy to latex rubber), powder free. While the $16 for a box of 100 gloves at Walgreen's might seem expensive, that comes out 32-cents per pair, not a bad deal at all (some sources may have them cheaper). A simple dust filter covering my mouth and nose seems to capture any of the overspray droplets for me. Some modelers use chlorine bleach for cleaning and stripping, so a word of extremely important caution hereth Never, NEVER mix anything containing Sodium Hydroxide (Lye) with household (chlorine bleach!!! Doing so will release chlorine gas into the air, and chlorine is a deadly poisonous gas (used as such as a WMD during WW-I, BTW). It can damage lung tissue, and breathing the stuff is often fatal--so if you have both chemicals in your lexicon, make absolutely certain you keep them very separated, please! All that said, I simply use yellow-label Easy-Off (or a generic brand of the stuff) by putting the parts to be stripped in a glass bowl, then spraying a generous amount of the oven cleaner into the bowl, enough to more than cover all the parts being stripped, and let that stand for 10-15 minutes, after which the chrome, and the paint (if it is at all stripable with sodium hydroxide) will have disappearned. Been doing it for roughly 50 years, so I know it works. Art
-
Old Monogram Parts Restored ?
Art Anderson replied to Pete L.'s topic in General Automotive Talk (Trucks and Cars)
The Monogram '40 pickup when first released had a fully stock version possible, except for the "diamond tufted" interior. Art -
Fiberglass Question
Art Anderson replied to regular guy's topic in Model Building Questions and Answers
You say, Fiberglass? Does that mean you are using actual glass cloth, to make a body shell? If so, why not use regular polyester resin, which is what fiberglass is almost always laid up with? I've made several fiberglass model car bodies over the years, all of them Indy car bodies from back in the day when that was my particular passion. Works far better than epoxy resins, frankly. Art -
Question in regards to decanting spray paint
Art Anderson replied to fatkidd's topic in Model Building Questions and Answers
I've been decanting rattle can paint into airbrush color jars since about this time in 1962 (50 years now), and I NEVER worry about letting the paint "gas out", unless I am trying to change the shade by adding more paint of another color to it, and need to shake it up. Seriously, if you are using the color exactly as it comes from the spray can, there is no need--after all, you can't de-gas paint sprayed on a model directly from a spray can--and I have NEVER had any problems airbrushing the stuff thus. I simply put on a pair of Nitrile Gloves (the exam gloves that EMT's use) so as not to get paint on my bare hands, and GENTLY spray from rattle can to my airbrush color jar (if you are using a gravity feed cup, you will need to do this into a color jar first, of course, then pour into the gravity cup). Art -
Johnny ligthing/Amt question
Art Anderson replied to martinfan5's topic in General Automotive Talk (Trucks and Cars)
The Johnny Lightning kits from AMT/Ertl were a bit of a reversal on what Al Pletcher (My predecessor in product development at JL.Playing Mantis) and Tom Lowe cooked up, called "Classic Plastic". The CP series (and there were several) teamed up a set of JL replica cars with a miniature model kit box of an actual model car kit of the same subject. So, it was pretty easy for AMT/Ertl to do the same thing in reverse after RC2 bought up Playing Mantis, including Johnny Lightning diecasts. Art -
Datsun is making a comeback
Art Anderson replied to martinfan5's topic in General Automotive Talk (Trucks and Cars)
A "label slap" is a "label slap". -
1940 Mercury coupe
Art Anderson replied to blazefox's topic in General Automotive Talk (Trucks and Cars)
Mercury began in 1939, as a mid-priced car for Ford, to bridge the gap between the Ford and the Lincoln Zephyr. 1939-40 Mercury bodies are completely unique, not a single panel (and not even the window glass) matches anything found on a '39-40 Ford, except in basic styling themes. Mercury rolled on a 6" longer wheelbase than the comparable Fords from 1939-48, but 1941-48 Mercuries used the same body shell (same panels, same shapes, different trim of course) as Ford, but with a 6" longer front clip to accommodate the longer chassis and wheelbase. Visually, the V8 engine was the same for 1939-40, the only difference being internal (Ford 221cid, Mercury 239cid--the difference being handled by the factory going to one standard block with the larger bore for the Merc, sleeved down to the Ford bore diameter). The chassis layout is the same, all standard Fomoco practice, with just the frame rails themselves being longer forward of the main engine mounts (at the flywheel housing). All this would make a '39-40 Mercury body a very serious conversion of the 39-40 Ford, enough so as to almost warrant scratchbuilding one. Art -
Scale chain-link fence
Art Anderson replied to Harry P.'s topic in General Automotive Talk (Trucks and Cars)
Harry, The stuff is called plainly "Nylon Netting". Surely you have a Michael's or Hobby Lobby somewhere not too far from you, or for that matter a fabric store? Any craft store or fabric store should have the stuff. It comes in various sizes of openings, go for as large as you can as chain link fencing is what, 2" squares? The netting is quite stiff actually, and is hexagonal rather than in squares, but it can give the effect of chain-link fence reasonably convincingly. Art -
open testors paint jars help please.
Art Anderson replied to robdot's topic in Model Building Questions and Answers
For really stubborn Testors square bottles, I have been known to take a small screwdriver having a fairly large handle (3/32" or 1/8" wide blade), and pushed that in between the glass and the cap, and gently twisting the screwdriver, which pushes the steel cap slightly away from the bottle itself--I simply just repeat that process all the way around the cap, and almost always, that loosens the cap enough to allow me to twist the cap off in the more conventional way. Art -
Harry and all! To be a bit more specific here: Lacquers and water-borne acrylics dry solely by evaporation of their solvents (lacquer of course, the solvent is lacquer thinner--almost always "industrial alcohols" with perhaps some acetone in the mix). Water borne acrylics use both some form or another of industrial alcohol along with water). The drying time of lacquers is dependent almost totally on the ambient air temperature, which of course can be varied by the use of lower-temperature rated lacquer thinner at say, ordinary room temperature. Water-borne acrylic drying time is greatly affected not only by the ambient air temperature in the room, but ALSO by the relative humidity. Enamels are a different story altogether: Enamel paints in their most traditional and basic form are pretty much a varnish, with pigments added for color. Varnishes are a resin-type material, reduced ordinarily by mineral spirits, so there are two stages to their drying: First, the mineral spirits must evaporate, which is a lot slower than say, lacquer thinner. Once the reducer (thinner or mineral spirits if you will) has pretty much evaporated, the "wet enamel becomes sticky or "tacky" in nature. This is where the second stage of the drying process happens--the varnish-type "resins" actually oxidize (combine with oxygen from the surrounding air, which has the effect of hardening them, and that can take some time. As enamel resins are oil-based (traditional enamels used linseed oil, for example), a drying agent is generally added to the mix (anyone here who has ever done oil painting--think Van Gogh or Rembrandt here should know what "Japan Dryer" is, a chemical which when added to enamel greatly speeds the drying time). Again, the amount of "dryer" added to enamel paints along with the ambient air temperature greatly determines the drying (and curing!) time. In the days when body shops used either nitro-cellulose or acrylic lacquers, the rule of thumb was, no color sanding or rubbing out until the lacquer finish had dried for at least 30-days, but then, lacquer applied with a production (body shop style) spray gun results in a coat of lacquer far thicker than a modeler's airbrush will give, although rattle cans come pretty close to the thick coatings of a full sized spray gun). As a rule, when I use automotive acrylic lacquers on a model, which for me definitely means airbrushing, I let the paintjob sit untouched for at least 48 hours before polishing out. With the non-penetrating lacquers (real nitro-cellulose and acrylic lacquers have reducers that are so "hot" they can actually penetrate styrene plastic, which is what causes crazing) and as such, are slower to dry thoroughly than their automotive counterparts, so I prefer to let such body shells sit for a minimum of one week before polishing. All that said, a very good (and not all that costly!) option is to buy a food dehydrator (once summer comes on, and fruits and veggies start coming in out of the garden (or the produce department, or some "farmers' market", dehydrators take up a fair amount of space in retail stores. A food dehydrator makes a very good drying chamber, not so hot inside as to damage a styrene body shell (although with resin, due to that material's much lower tolerance for heat, ordinary air drying is highly recommended!), and can completely dry lacquer in a few hours, and certainly cure out enamels hard in a day or so. But, absent any artificial drying method, everyone's experience will vary, given the effects of temperature and humidity. Art
-
When do we retire Micro-Mesh?
Art Anderson replied to Chillyb1's topic in Model Building Questions and Answers
My parameter has been, since my first Micro-Mesh polishing kit back about 1980, has been when I see tiny chunks of the abrasive gone from the polishing cloths--it's time to discard, buy a new kit! Art -
Actuallly, less than an 8th of a sheet--lotta chrome there, of course, but all in fairly narrow strips. Art
-
Erik, I've had trouble finding the type of light bulbs which would make that color more true to life. I adjusted the colors a good bit, but you are correct, the actual Phoenician Yellow is much lighter than the pics show. Art
-
"No side view mirrors?"
Art Anderson replied to modelmike's topic in General Automotive Talk (Trucks and Cars)
Left side outside rear view mirrors became a requirement in 1966, for all new cars and pickups purchased by the US General Services Administration. Right side outside mirror was a requirement as of January 1, 1970. Art -
1950 AND 1951.
-
Well it does have its flaws, enough so that I will never enter it in a contest! But thanks just the same--it's a nice 3' model car, best viewed 3 feet away. Art
-
Closeup of the plexiglas cloisonne badge in the center of the upper grille bar. Most cars of the 1950's (even out to the 70's) had some sort of clear plastic badge up front, carved out on the back side, colored in with translucent tints, and then vac-plated to look like an expensive glass or crystal badge--Hudson was no exception! To do this on the Hudson (and it's the first time I've ever tried it) I applied the kit decal to the base of the emblem provided on the upper grille bar, and then added a drop of Devcon 5-minute epoxy to create the illusion of that sort of badge. I think the technique captured the concept very well! Art
-
and yeah! I just realized I forgot to install the gas cap cover door before photographing the model! Mea Culpa! Art
-
..and in 2011, 2010, 2009, 2008, 2007 and 2006! Moebiius 1953 Hudson Hornet Club Coupe, in Honey Cream (I used MM Phoenician Yellow which is Oh-so-close!) and Ebony Black. Yes, the paint scheme is factory correct, in fact the two colors could just as easily been reversed (my Dad had a 4dr in the same colors, cream roof, black middle body, cream lower panels): Colors are "Honey Cream" and "Ebony Black". Modelmaster Phoenician Yellow ('57 Ford color) is so close to Hudson's Honey Cream it's scary! Art