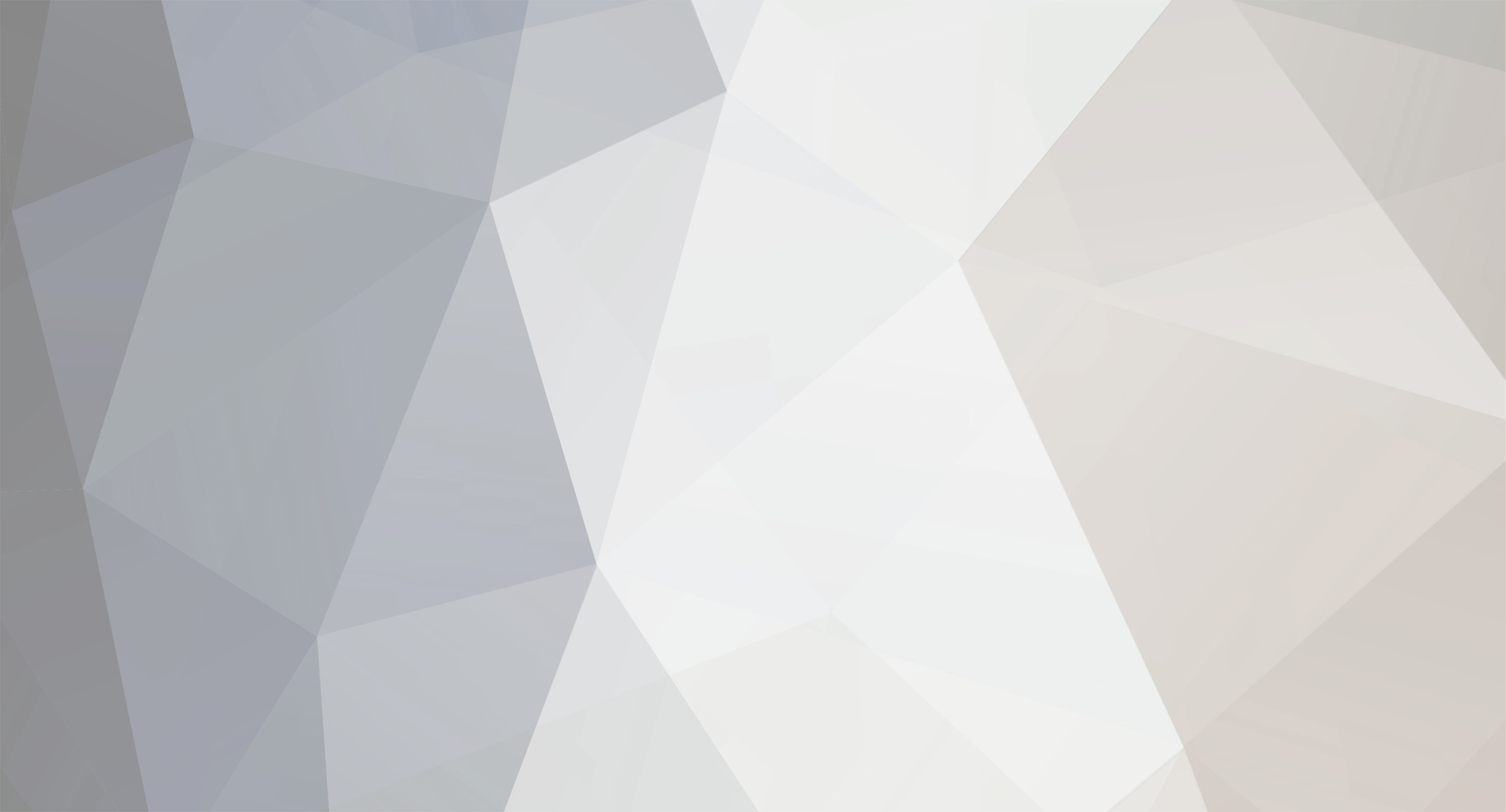
Art Anderson
Members-
Posts
5,052 -
Joined
-
Last visited
Content Type
Profiles
Forums
Events
Gallery
Everything posted by Art Anderson
-
Harry is correct in this! "Silver Streak" was a slang term invented decades ago to describe Pontiac's with those chrome "silver streaks" down the hood and trunk. Incidently, that silver streak trim motif was developed by an entrant in the Fisher Body Craftsman's Guild contest back then. His name? Donald Burnham, who later grew up to become the CEO of Westinghouse in the 1950's (GM retained the right to use any styling motif presented on a FBCG model entered). Don Burnham grew up in the house next door to where I grew up in West Lafayette IN--his Dad was the longest serving mayor of WL, something like almost 40 years. Art
-
Well, for truly stock, the upholstery on all 1925 T open bodied cars was a semi-gloss black--however, so far, your model looks so nice! Art
-
Well, an old acquaintance here in Lafayette does have a Kurtis with a V8-60 up front--planning on visiting him this summer, getting as many reference shots as I can. While I won't do it with this one, the kit as produced has two too many gauges on the instrument panel for a midget as raced back in the 50's--the only gauges that most of them had was a tachometer and an oil pressure gauge. Given that the racing action was fast and furious on short tracks (most tracks were 1/4 mile) a 50-lap feature covered just 12 1/2 miles distance. Most drivers paid attention only to the tach, and then sparingly, oil pressure gauge might have gotten looked at in hot lapping, or if the power seemed to "go off" a bit. Fuel gauge would not have figured into the equation, given the very short duration of heats, consolation, and features. Consider that those old midget drivers had their hands very full: In addition to the traffic on the racetrack (and the quick maneuverability of a midget), coupled with the driver having to frequently work the hand pump on the left side of the body to keep the fuel tank pressurized (even fuel injected Offies needed this, as there was no separate mechanical fuel pump on those cars), grabbing the brake lever to set up for the turns at least twice per lap, they were BUSY indeed! So, I'll be making new instrument panels for future midgets to reflect this. Also, it would be neat if some PE maker would do a St Christopher medal for the instrument panel--an awful lot of racers years ago mounted them on their instrument panels. Art
-
It's been 26 years since I've done a race car of any sort, so this Midget is a trip back in time for me. So far, so good, engine is wired, fuel injection pump was added to the intake cam tower and that's plumbed to the injectors (fuel line will be installed when the firewall is ready). Here's a look at it so far: Art
-
It's great when a model kit development person can get sprue attachment points positioned so that they do not show, but when Revell did that with the quick change rear end on their otherwise pretty excellent Kurtis Midget--they blew it, IMO. To do this almost always means putting the attachment BEHIND the back surface of the part, which is what Revell apparently approved on the 2-halves of the QC, plus the rear gearbox cover. Only one problem though: Doing that meant having a pronounced (for the size of those three parts at least) "nub" directly on the mating surfaces, which has to be removed completely for those three parts to glue together wilh only the most minimal seam possible. Now, it would not be a problem IF the rear gearbox cover plate didn't rely on a raised "rib" on either side for the purpose of making alignment easy, but as tooled, it was a bear! Art
-
I must disagree with this one: All my references, including Collectible Automobile, and an excellent Wikipedia along with several owner-identified photographs online, refer to this car as a 1948 Pontiac Streamliner Custom Coupe. "Torpedo" was used on this body style when it was introduced in 1941, and for the truncated 1942 model year. Beginning with 1946, Pontiac labeled the car "Streamliner", which name carried over through the last of the fastback Pontiacs in 1952. Art
-
This concept is nothing new, frankly. The 1936 Cord 810 introduced a remote shifter, which was merely a very small "stalk" on the side of the steering column, with a very small lever with a slotted "track" that corresponded to the then standard "H" pattern manual shift. It was a preselector, meaning you moved the lever from say, 1st to 2nd gear, and then, when you were ready, depressed the clutch pedal--and presto, the electric shift moved the gears from 1st to 2nd. Repeat the process for shifting into 3rd, and so forth (Hudson also offered this very same electro-shifting system). Art
-
Whats the most tooled car ?
Art Anderson replied to 57peppershaker's topic in General Automotive Talk (Trucks and Cars)
Don't overlook Corvette. I believe that every year of Corvette has been made at some time or another, in plastic, promo, kit, diecast, even cheap polyethylene plastic toys, and stamped tim. Art -
Old trick, goes back many years--worth repeating though! Art
-
what to use for 1/8 spark plug wires?
Art Anderson replied to Wilesbd's topic in Model Building Questions and Answers
If you consider plug wires to be approximately 1/4" in diameter, for 1/8 scale, that comes out to just a shade over .030". Lots of phone wire is about that diameter with the insulation. Art -
Got it.
-
Pearl Ex pigments,Help please.
Art Anderson replied to Austin T's topic in Model Building Questions and Answers
Mike, I second what Mike said: Future is not really the best stuff for a clear coat, and all pearlescent finishes are done as clear coats, with pearl powder added. Best to use a hobby grade clear coat, such as Tamiya's T13 or ModelMaster's clear coat--then only a small about of the pearl powder in it. That has worked every time I've tried it! Art -
Should work! Both Tamiya spray lacquers and the Testors ModelMaster lacquer system are made with non-penetrating solvents. I've used the colors from both manufacturers over each other, both Testers > Tamiya, and the reverse, and it's worked every time just fine! Art
-
Another sad day
Art Anderson replied to bbowser's topic in General Automotive Talk (Trucks and Cars)
I always liked the Bartles & Jaymes theme song by Flatt & Scruggs! -
Duplicolor paint health concerns?
Art Anderson replied to CEKPETHO BCE's topic in General Automotive Talk (Trucks and Cars)
Exactly! Our paints have changed over the decades--no longer are lead or other heavy metal pigments used, for example. Even the solvents and thinners that get used have changed as well--some of the ones that were common 40 years ago have disappeared from the scene due to their health hazards. All the arguments presented regarding the health problems suffered by professional auto body shop painters need to take into account the sheer volumes of paint used to paint a 1:1 car--it can take nearly a gallon of old-fashioned nitrocellulose or acrylic lacquer to paint say, a '57 Chevy body completely. Given the tendency for decades of car painters do do their work sans any sort of even basic dust masks, it's little wonder that so many suffered disability and even an early death from the effects of breathing in not only the vapors, but also the overspray particles. But let's take a good look at what we as modelers do: For starters, even a model car rattle can is a fairly small amount of paint--3-3 1/2 fluid ounces plus propellant (propellant used to be Freon, but with the banning of CFC propellants more than 30 years ago--propane and butane (both highly flammable gasses BTW) are what is used in aerosol cans of all kinds today. However, the sheer volume of paint that comes out of the nozzle of a spray can does present some problems. Three hazards do exist with spraying any sort of paint we might use on a model car body: Inhalation of the vapors of the solvent, inhalation of the particulates (dry or semi-dry droplets of overspray itself, and fire (every so often, the news media reports about a flash fire in the exhaust system of a furniture factory, where dried overspray from the lacquers used has caught fire, destroyed the plant completely). The best way I know of to eliminate, or at least minimize exposure to solvent vapors and airborne particulate matter from spray painting is a good quality paint booth that exhausts to the outdoors--while a bit pricey to buy, this is a one-time buy for just about any modeler, and will go a LONG way toward preserving one's quality of life, and of course, domestic tranquility (keeps wives and families happy as they don't smell the paint, and the overspray doesn't settle in the house as a very unattractive dust all over the place). Another, very good tool to use is an airbrush! OK, now I'm sounding off seemingly highly technical, but an airbrush puts out only a fraction of the paint emitted by a spray can, and the much smaller, tighter spray pattern means that more of the paint lands where it's intended, and much less overspray into the surrounding are compared to a rattle can. In the bargain, while an airbrush and its compressor are also a bit pricey, using a hundred rattle cans of paint over time (and a prolific modeler can do that easily in say, 5 years time) will amount to far more than the price of airbrushing equipment which in itself is also a one-time buy. With a well-designed spray booth, such as say, any of the Pace Peacemakers (or a properly designed and constructed unit of your own making) I find virtually no need whatsoever for a respirator, as all the overspray and solvent vapors are pulled out of the room to the outdoors, and leaving the thing run for say, half an hour after any paintwork will also suck out the majority of the fumes from drying paint in the bargain. Just for explanation here: I find that when I set up paint for airbrushing, I will use perhaps 1/8 fl. ounce (half the volume of a square bottle of Testors) of paint in the color jar, followed by perhaps 1/4 ounce of thinner (almost always lacquer thinner by the way), which is enough paint for most model car bodies--per coating of paint (think this for primer, color coat, and clear coat when the paint job needs to be cleared). Now, this isn't all that much more paint than a woman might use to paint fingernails and toenails (I can almost guarrantee that no woman uses any sort of exhaust system when she does that!). If one is using rattle cans, the best way to eliminate most all the risk is to spray outdoors, but that's not the easiest thing to do in winter, I know. But in any event, I see no need to make mountains out of molehills here, just learn to be careful, take precautions, and use equipment, from spray booths to respirators if no spray booth is in the cards (PPE--personal protective equipment is never truly a bad idea--but consider that spray booth as PPE, which it is). Art -
Question in regards to decanting spray paint
Art Anderson replied to fatkidd's topic in Model Building Questions and Answers
OK, logic here! If you spray paint straight from a rattle can, do you let the paint "outgas the propellant" before you spray? Of course not! So why worry about it if you decant the rattle can into an airbrush color jar for spraying? Answer: Nope! Just decant the stuff and airbrush away. End of story. Art -
I'd take a page from Revell's very successful "Make it and take it" program, which is what Goodguys uses for the model car part of their very popular outdoor rod and custom car shows: SNAP KITS. Face it, at this time in the school year, a 5th grader will be anywhere from 11-12 years old, depending on the age cutoff in a school district for starting school (in my school days of 1949-62, a kid had to be 5yrs old by January 31 of Kindergarten--nowadays that's been moved way back to as early as July 31 BEFORE the start of Kindergarten, so 5th graders can be as much as a full year older than someone my age would have been. That said, for most kids in the 5th grade, any model kit is very likely to be the very first model kit they will have built, and with the mix of older so-so model car kits out there (you know the kind--parts fit that isn't what it should be) all the way to more modern kits with great fit, plus a high parts count just to build the model absent any custom parts options. Also, chances are, the kits will be provided up front, at school--which means a very limited selection, laid out in front of kids who may or may not have a burning desire to learn to build one all of a sudden. Therefore, I would suggest snap fit Revell kits, simply because they fit that sort of program quite well, and they don't require a long attention span in the bargain. From 1986-94, I co-taught a class in plastic model building in a program at Purdue University called "Super Saturday", which was a 10-week course, every Saturday morning from 9-11am. Kids in Super Saturday (which is run Purdue's Center for gifted and exceptional children, in the College of Liberal Arts & Sciences) and any interested child from 4th through the 7th grade has to be recommended by their school principal or guidance counselors to be admitted. Now while this is a good bit different from what you are putting together, some of the lessons we (the Plastic Model Building Course was designed by a long time friend of mine, a Professor in that College at Purdue AND himself a model builder) as the teachers learned was that interests varied widely in each class as to subject area--some brought cars, others airplanes, even some ships and armor. But the big difference was: Each and every kid was there because he or she (and about 25Z% of each class was girls!) wanted to be there. The results were fascinating for me: The very first class started with a "pre-test" designed to gauge each child's level of knowledge going in, and then the building started. Jim and I worked closely with each kid after demonstrating the use of a particular tool or tools (one difference here from what you are thinking was that each child had to bring their own model to class, along with a few basic tools--Xacto knife and blades, nippers or small side cutters for removing parts from the sprues, glue, and whatever paint they were going to use along with brushes and thinner for cleaning), and then building time. Along the way as well, each child was expected to research a bit about the model they were building, the history of the real thing, find out the paint colors and such. At the end of a particular "semester", we administered a "post test", which showed us, and the kids themselves, how much they had learned, and on the last day of class, we provided refreshments, and invited parents to come in for the last hour of that class, to listen to their kids as they showed off their completed models, and told the class about them, and a bit of the stories they'd learned about the real thing. Those "show and tell" moments on that last day of class are still memorable--seeing the pride each kid had as they showed off their work (no prizes, no letter grades), AND the pride the parents had in their child's accomplishments as well. Some of those kids are still model builders today, I've run into them as young adults at shows In Indianapolis numerous times. Others, who are from this local area I've run into in subsequent years, and even if they never built another model kit after Super Saturday, I've still heard how much they enjoyed the 10 weeks of getting up early on Saturday morning to spend a couple of hours in a college classroom, with a real college professor (and this layperson) teaching them something that we each knew and loved doing ourselves. In many ways, times are a lot different than they were when I was a boy growing up, building model cars (which I began at age 8), given that for the most part, none of us had mentors with any experience whatsoever, coupled with a lot of parental disapproval to start with--meaning that most all of us early model car builders were on our own, truly self-taught! Art
-
The whole business about "dangers" from polyurethane resin "dust" comes from what is/was one of the biggest industrial uses of the material, that being in the low-medium-priced furniture industry. Furniture manufacturers, when making reproductions of styles common in the 19th Century (think "American Country" oak furniture, which was highly popular particularly in the Midwest (the styles having carved "applique" decorations glued to solid (or veneered) oak bedsteads, dressers and commodes, would carve a master for a particular appliqued decoration, then make RTV molds off of those, use them for resin castings, which had to be faced off on their back sides to a flat surface for gluing to the oak background. That meant a lot of dust in the air, and for sure, that sort of dust is very irritating to breathing passages, due to its being tiny, sharp particles (incidently, the same cautionary statements appear in OSHA regulations regarding the sanding of most hardwoods as well in industrial settings!). However, fully cured, hardened urethane resin is not particularly toxic, toxic meaning poisonous--the stuff is pretty nearly inert, as it doesn't dissolve in water--and we humans are made up of primarily......water. One other cautionary statement, which shows on any MSDS sheet for urethane resin is flammability, not only of the liquid components, but also of the mixed and cured resin itself--to test that for my own education when I was using the stuff in quantities of 10-20 gallons a week, I actually set fire to some scraps of flash and defective parts (outdoors), and yes, the cured resin is quite flammable once ignited. However, most modelers have learned to file carefully, and wet-sand, which pretty much eliminates fine dust particles in the air, and from experience using a Dremel on resin, there is really NO dust, just a fine stream of particles that arc up into the air, fall directly to the floor. As a former resin-caster, I find all the misinformation, and "fear-mongering" to be, at the very least, disappointing. Art
-
Columbia Two Speed Rear End
Art Anderson replied to styromaniac's topic in General Automotive Talk (Trucks and Cars)
Columbia 2-speed rear axle? Last I knew, those were pretty much a thing of the past by the 50's--installed mostly on flathead-era V8 Fords. I believe both Revell (1948 Ford station wagon and convertible) and AMT/Ertl (1941 Ford station wagon) both included them in kits. The Columbia unit was an "Overdrive" setup that was made for the old Ford V8 rear axle assembly, and was fitted in place of the right side rear axle and housing (remember, those old Fords had a three-piece rear axle unit--right side, left side, and center "banjo" which carried the differential. This was a much simpler conversion for those Fords than the more conventional overdrives that mounted on the rear of the transmission, given Ford's torque tube drive setup. Most all other automakers were using the more common one-piece rear axle housing, but had open "hotchkiss" driveshafts, with universal joints at both transmission and differential, so using a transmission-mounted overdrive involved only shortening that type of driveshaft--in fact, some automakers offered them as factory-installed options built that way. Art -
That Jeep pickup is a recast of the one I did back in 1998. As for resin dust, no--it's not toxic--polyurethane resin is so stable, the scraps of the stuff I sent to the landfill over the years will be their hundreds, if not thousands of years downroad. As for resin dust itselt--easily overcome by wet-sanding, that can get washed down the drain pretty easily. Art
-
Spray paint issues
Art Anderson replied to hotrod59f100's topic in Model Building Questions and Answers
DITTO!!! Art -
You're experiencing the same thing I did, in early January 1962 when I fired up my Binks Wren airbrush for the first time--all that surface detail that rattle can paint buried, just jumped right out! Enjoy the experience--an airbrush can move your model car building light-years down the road for ya! Art