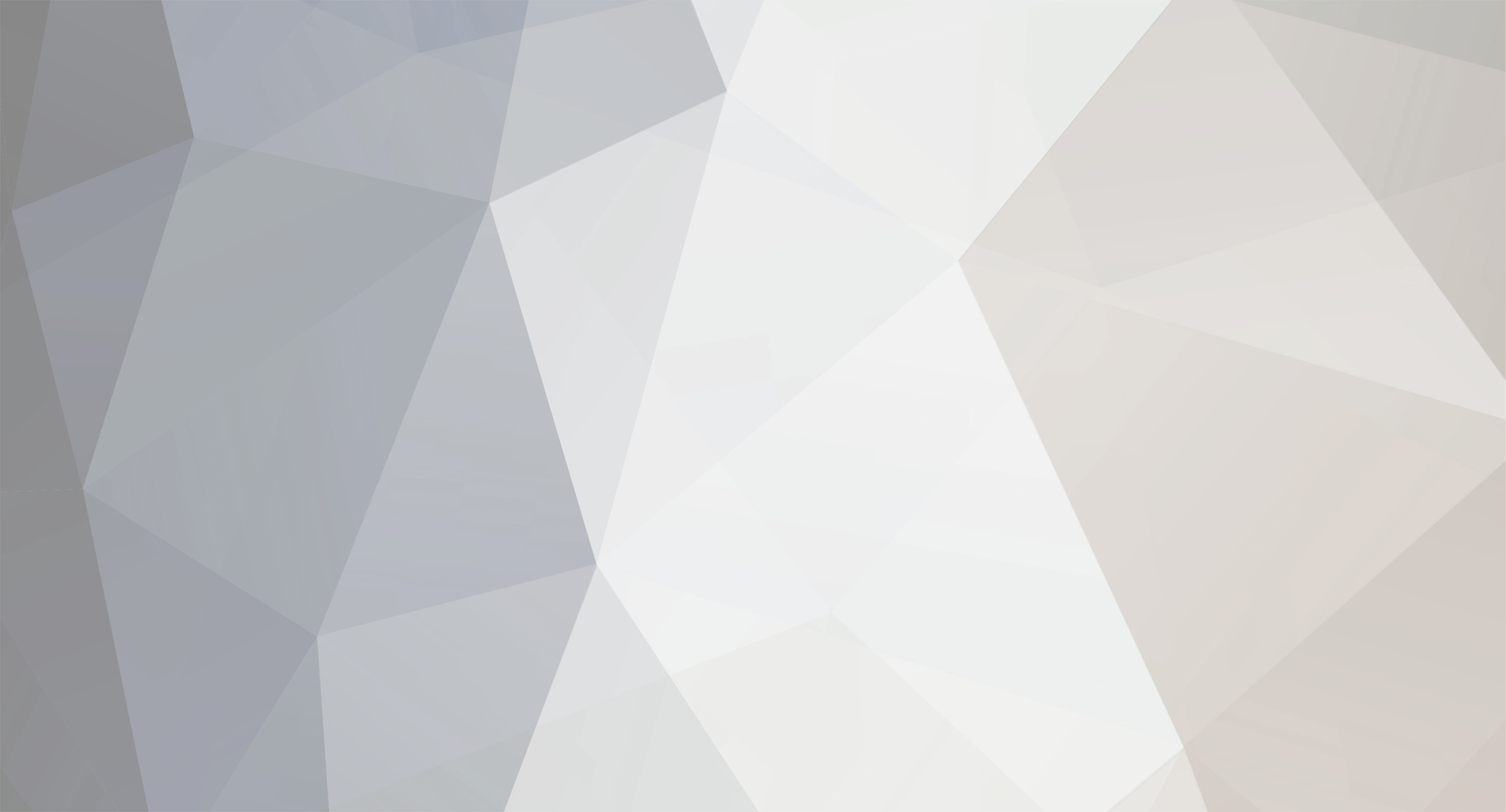
Art Anderson
Members-
Posts
5,052 -
Joined
-
Last visited
Content Type
Profiles
Forums
Events
Gallery
Everything posted by Art Anderson
-
80's Chevy or GMC PU
Art Anderson replied to Stephen H's topic in General Automotive Talk (Trucks and Cars)
Of all that generation of Chevy/GMC pickups, the only ones having correct cab and box shapes were the MPC kits, frankly. There was quite a family of this series, starting with the MPC snap-kit '77 Blazer, then the '78 2wd Chevy Stepside, followed by a gaggle of 4X4's with short boxes and lift kits. If you want one with a Fleetside box, the only one done by MPC was the "Fall Guy" truck, which is, IIRC, in the era 1980-82 GMC. MPC's Chevy 4X4's were 1981-82 only, no 83-87's were produced by them. Pretty much everything between all the pickups is interchangeable, even the '77 Blazer snapper can be adapted to the later kit parts for more detailed suspension (Modelhaus' Suburban of this era was mastered from that '77 Blazer by a modeler out in Kansas, who did an excellent job of it). If you try mix-and match of MPC parts with say, the Revell '76 Chevy pickup, you likely will be disappointed, as Revell didn't do a very good job at all capturing the lines and shapes (first issued as "Billy Carter's Pickup"); and the same would be true with any Monogram Chevy or GMC from that era, Monogram wasn't nearly as accuracy conscious then as they became later. Hope this helps! Art -
What is happening here is that the "soft" PVC (Polyvinyl Chloride) tire is reacting with the hard styrene it's touching--that's been an issue off-and-on for as long as model car kits have had PVC tires. The "plasticizer" used, if not recaptured in the manufacturing process, "leaches" out of the PVC, and performs it's softening action on styrene, and whatever paint is applied to it (regardless of the type of paint--be it enamel, lacquer, or acrylics, it will be attacked as well). Back in the 1960's and early 1970's, Revell kits were NOTORIOUS for this--so much so, that the melting of styrene plastic wheels was termed "Revell Tire Disease". The only cure for the problem is at the factory level, and they can solve the problem. As for prevention, yes this can be prevented, but it takes a thin layer of metal or epoxy glue to prevent the PVC plasticizer from penetrating ajacent paint or styrene. Perhaps the easiest is to use a strip of Bare Metal Foil on the rims of the wheels, but a thin coating of say, DevCon 5-minute epoxy has been known to work as well. Art
-
An easy way to grasp the concept here is to think of building any structure: For example, at Purdue, where I work, construction is planned on a new Health Sciences complex along with a large parking garage. Now, the Health Sciences building is to be done in reinforced concrete, with masonry etc.--in essence, scratcbuilt from raw materials along with brick, limestone and concrete block--pretty much built from scratch on location (of course, there will be some pre-cut structural steel involved. However, the parking garage will be a gigantic "kit"--all the support columns, beams and floor panels will be pre-stressed concrete components, produced offsite, then trucked in, set up by cranes, all interlocking together (like a gigantic Walthers Model RR building if you will). Art
-
part 3: Fast forward out to the 1990's and into this Century: The old methods of creating model kit tooling began to change by the middle 1980's--Tamiya started using EDM (Electro-Discharge Machining) whereby tiny electric arcs are used, in a bath of cooling oil, to remove bits of metal from the blocks of tooling steel--and CAD/CAM slowly entered the model kit industry. Now, a toolmaker need not stand there, making every move with a pantograph, EDM literally allowed the operator, once setups were done, to push the start button, and the rest became almost automatic. This certainly found a lot of use in the creation of diecast model tooling. In addition, wood began being replaced as a pattern making material by, get this: Styrene! Yup, to look at a tooling mockup for either a diecast, or a plastic model kit today, is to look at a body shell and related parts, representing the finest scratchbuilding you will ever see, bar none. Also, with laser scanning technology, the laborious drafting of drawings has gone digital, CAD has taken over, done before the first tooling mockup parts are created. But it's not all a simple matter of loading files, then clicking "START". Laser scanning and both CAD and CAM have a limitation, and that is simply do to how we actually see a miniaturized version of a real automobile. So, along the way, particularly with body shells, a lot of plain old visual study by human eyes, comparing to pictures (and to properly reference a real car for shrinking down into an acceptable scale model can require often a couple hundred photographs of the actual subject, pics shot for shapes, contours, small dimensions, definitely not "Beauty Shots" for the likes of Hemmings, or Collectible Automobile Magazine). Still the human equation becomes the final arbiter here. I know Dave Metzner has sweat bullets over the Hudsons and the upcoming Chrysler C300, along with the designers, engineers and pattern makers in China--that is still a big part of the game, has always been, and not likely to ever go completely away. In the bottom line, it can still take upwards of 12-18 months to get that kit right, particularly of older cars for which only limited factory drawings may have been preserved (most were consigned to dumpsters decades ago), and certainly no modern CAD files either. In fact, it can take as long as 2 years to get to a final product that you, me and the other guy too can and will accept as being a model car we'd build--and that probably isn't all that much different no matter what continent, no matter the model kit mfr. I hope I have added something to the equation here: it's not so much the materials from which model kit tooling is cut that is the cost factor--it's the WHOLE process, all the skills of all the skilled people involved, and added to that mix, a passion to make any kit produced, as good as it can be. So some things will probably remain the same where tooling materials are concerned. For every "magic bullet" of technology, there still remains the human factor, and that's not gonna change anytime soon, I suggest. End! Art
-
Part two: And here is the rub: A couple of generations ago, a newly tooled model car kit could reasonably be expected to see hundreds of thousands, if not millions of units produced, and in a relatively short period of time. In the 1960's, there really weren't that many model car kit tools in existence--AMT Corporation, for example, might have had a couple of dozen "Annual Series" subjects, along with not more than that in Trophy Series, or other kits projected to be run for multiple years. The same would have been true over at JoHan, MPC, Monogram, and Revell (the latter two were still far better known for non-automotive subjects in the industry back then, believe me!). With a $2.00 MSRP model car kit laying less than 80-cents in the till at AMT, they ran on sheer volume. In the fall of 1966, my Dad brought home the Wall Street Journal, with a FASCINATING article about the World's Largest :"Automaker": It wasn't any of the Detroit Big Three, not even close. AMT Corporation was making more model car kits (the number 100,000,000 sticks in my mind here!) than all the world's automakers put together in the world of real cars. To a lesser extent, the story was the same with other model car kit manufacturers. That alone dictated the use of steel tooling. AMT Corporation's largest selling plastic kit perhaps of all time wasn't a model car kit, but rather their first kit of the TOS USS Enterprise from Star Trek! I was told in the late 70's that the original tooling for that kit was cut in aluminum, they figuring it would be a "flash in the pan", quick popularity then die--within a year or so they had multiple steel dies squeezing out millions of the Enterprise, and its popularity far outlasted The Original Series of Star Trek by at least a couple of decades. One model car kit in particular, the original Trophy Series 1957 Chevy Bel Air Hardtop remained in continuous production from early 1962 all the way to 1997, when it was supplanted by the newer tooling introduced that year--millions were produced over those 35 years, probably the most produced model car kit of all time. End part 2
-
To a great extent, this thread seems to be more about "reinventing the wheel" than anything else. Hard steel injection molding dies are used simply because they work and can work for a long, long time. And steel is probably the least expensive of all materials from which to cut injection molding dies when all factors are considered. Yes, aluminum can and has been used, but aluminum doesn't hold up nearly as long. 30-40-50 years ago, model kit tooling mockups (patterns) were made by hand, from wood. Every part of a kit was carved largely by hand by skilled patternmakers in a time-honored fashion born of the metal casting trade. Generally, those wooden model kit patterns were created in a scale larger than what was to be produced--1/12 scale for a 1/24 scale model, 1/10 scale for a 1/25 scale model, as these scale relationships could easily be dialed in to the analog (mechanical) milling pantograph machines then the common standard for injection molding tooling. As the parts were developed, they would have been test fitted together, and once approved, were then used to create impressions that could be turned into large scale wood and resin mold cavities exactly like the final steel cavities would be cut. These molds could then be filled with a liquid resin to create "model kit" parts not unlike the final products, again tested for fit, mold alignment etc. One deviation from what I am pointing out here were the patterns for body shells. Those were done as SOLID wood masters, just the exterior shapes and contours carved--the creation of the inner surfaces being done from the large scale wooden tooling mockups with various clays etc., to allow the creation of the internal "core" die(s) that would make possible the molding of hollow, one piece body shells. This is why those older kits have thicker, more uneven inside surfaces, quite unlike the "state of the art" model car kit bodies we see today. The cutting of steel dies was done by a 3-dimensional "pantograph" milling machine, (old time draftsman will remember 2D pantographs which were used to either enlarge or reduce a drawing on the drafting table--3D pantographs worked in very much the same way, but on three axes, length, width and depth). This was one of the major costs in tooling back decades ago--a toolmaker had to guide the cutting tools using a stylus which followed the shapes of the final wooden mastering for the various molding cavities to create the final tooling. Long, drawn out process, very laborious, very tedious as well. Along the way too, the various moving sections of the tooling had to made to close precisely, particularly that for the one-piece body shells we came to demand in model cars by 1957 or so. In a day when so much depended on the human hand and the human eye, it's little wonder that there were mold misalignments that happened--to a great extent, they were practically inevitable. Once that tooling was cut, it was on to "test shots", the new dies loaded into an injection molder, and molten plastic shot through the runners, and what often came out left lots to be desired. Material thickness errors would crop up, either that roof was too thick, or perhaps so thin in a spot or two as to actually be a hole. Adjustment time! Same with every part of the kit. Once all the fitments and tolerances were corrected to at least an acceptable level, then the adding of small details. And this is where the toolmakers really earned their pay--artistry had precedence over science. If one but thinks about say, a recessed door line in a model kit body, realize that is created by machining a "raised ridge" in the tooling, tooling being exactly the mirror image of the plastic production part. Scripts, badges, chrome spear details--all that required intense hand work, jeweler's work if you think about it, all done as recessed details in the tooling. End part one
-
Scratchbuilding for me began with serious modification of existing kits. My first serious conversion was about this time in 1962, 50yrs ago, when I decided to replicate a Great Aunt's 1924 Model T Coupe, using the AMT Double T, actually 2 of them. I pestered Dad to go with me out to Boswell IN, where Aunt Minnie lived, to take a look at her T coupe--never bothered to take a measuring tape, no camera, no nothing. Dad and I eyeballed the car in her garage (it was still her daily driver, around that little town, to the grocery, to her garden club, to church that was it --what the hey, she was 88yrs old, but still spry, and I was one of her favorites.) I had but a couple of pics in a book on Model T's, and between those, and my visual recollections of studying her car, I started in, and with just two tools, a penknife (back then, EVERY self-respecting teenaged boy had a pocketknife, I was no exception, and every Saturday afternoon was knife sharpening time with my dad--no restrictions back then as to carrying a pocketknife to school--it was expected, a rite of passage) and an early Zona razor saw. So, cut two chopped T coupes apart, glue them back together, with the roof raised to "stock height" (hey it looked right, so go ahead!) and glue the parts back together. That is where the replica stopped, and the street rod began! It took but a moment or two, and the next thing, I'd cut both doors open, and figured out how to hinge them. Full fendered, SB Chevy up front, home made headers running forward to look like nerf bars ala Joe Cruces, wire wheels from a 61 or 62 AMT Tbird, Pactra Candy Strawberry paint, white pinwale corduroy for the rolled and pleated interior, I was on my way. The car won Best of Show in the largest model car contest ever held here in Lafayette, some 2500 models entered at Bell Auto Supply downtown, and then, come summer and me off in college at Parsons College in Fairfield IA, the car went to the Iowa State Fair, for the Iowa State Model Car Championships, where it won its class. OK, so what does this have to do with scratchbuilding? The skills I picked up in this exercise started coming into play a few years later, when I started building models of race cars that had actually faced the Starter's Flag at Indianapolis Motor Speedway. That lead me to create all manner of race cars, from a 1911 Case, 1911 Stutz (the Car that Made Good In a Day), and eventually a rendition of the Marmon Wasp. Along the way came a scratchbuilt 1927 Duesenberg Indy Car (driven to victory by Lafayette's own George Souders, whom my mother got to know back then), several scratchbuilt Miller 91's, and a bunch of Indy cars out of the 1930's. Today, I have far more tools, much more sophisticated equipment (including a Sherline lathe, and their mill with ALL the toys), airbrushes, the whole nine yards. But, it all started with that AMT Double T Kit, a trip to Aunt Minnie's, a pocketknife and an early razor saw. Art
-
Muscle Cars - Old vs Modern
Art Anderson replied to Stang88's topic in General Automotive Talk (Trucks and Cars)
It's more a matter of plain economics: In the product planning meeting, if a new state-of-the-art tool for an existing subject is brought up, sooner or later, someone (most generally the accountants-whose job it is to keep an eye on money in--money out) is gonna ask something like this: If we invest X dollars in new tooling, HOW MANY MORE kits will we sell than what we are doing now? Almost invariably, the answer isn't all that positive. If the art/science of model kit tooling were only so simple that a "little tweak here, little tweak there" was all that would be required, the answer would be quite a bit different, but unfortunately, almost every time, it involves cutting a lot of new tooling steel, and to what end financially? I know I've often wished that some of the really gnarly older tooling could just be stood, opened up in the men's room, as dividers at the urinals, the problem would be solved, but unfortunately, nobody in the industry seems to think that'd be a good idea. Art -
In most any craft store, there are dyes that are used with clear casting resins (clear polyester resin) to create transparent colors. I've used those with epoxy in the past, but prefer using Tamiya clear colors OVER a lens (be it a clear styrene kit lens or home-made epoxy) rather than mixed in, as those dyes in any serious concentration do interfere with the epoxy.
-
Polishing tires
Art Anderson replied to Haubenschild's topic in Model Building Questions and Answers
DoubleD, I first noticed the brown-black sidewall tires in the summer of 1999, when I spent 4 months as a salesman for Bob Rohrman Auto Group here in Lafayette. I saw the phenomenon on both import and domestic cars as well. Art -
Actually, the original Revell Stone, Woods & Cook '41 Willys coupe, AND the AMT '40 Willys coupe and convertible do have a stock Willys chassis under them--that was the way Willys gassers were built back in the 60's--I think they even had basically the stock Willys front axles as well. In addition, a stock Willys "Go Devil" flathead 4-banger is readily available as well--it's the engine in the Hogans Heroes Willys M38/CJ2A jeep kit! Even the suspension in those three Willys gasser kits is basically stock in planform--although the leaf springs are arched more severely--those cars used parallel leaf springs front and rear. As for the Ford Thames--Revell's body shell is very very close to stock if not pretty much accurate for stock. Skipper's Critter and the Pie Wagon kit bodies should be a great place to start, and I bet with a bit of research online, and/or in books, even brochures, one could come up with enough info to create the stock frame, floor pans and interiors. Engines might be a different matter altogether though. English Ford Thames: And, just for giggles, an Anglia UTE! These two were found in the car corral at Kruse Auction Grounds, Auburn IN, 9/3/04. Art
-
MPG estimates vs. reality
Art Anderson replied to Harry P.'s topic in General Automotive Talk (Trucks and Cars)
Well, the lawsuit happened in Kalifornia, the Moonbeam State, so go figure. In any event however, EPA mileage figures are about as accurate as any other statistic the Federal Government puts out--most are about as useful as oats that have been through the horse. Art -
Polishing tires
Art Anderson replied to Haubenschild's topic in Model Building Questions and Answers
I'll give you another thought as well: Most all modern tires are not totally black rubber either. If you walk a new car sales lot in bright sun, especially after the car washing contractor has been on the lot, cleaned everything up, and the cars have been dried, tires have had time to dry, you should notice that many tires, particulary older-style "high aspect ratio" tires, have sidewalls that are actually "brown black" (just about the same color as Testors or Modelmaster "Rubber"), with more pure black tread (which will show for about an inch or so on the sides of the tread, where that rubber meets up with, and blends into the sidewall. Just an observation of mine. Art -
Westley's Bleche White is little more than "Trisodium Phosphate" or "TSP" as it's known in many places. TSP can be found in any paint store catering to furniture refinishers, as furniture restorers and cabinet makers use TSP a lot to clean up raw wood prior to staining and finishing. Generic TSP is lots less expensive than branded products containing TSP. Also, if you can't find generic TSP easily, it can be had in just about any supermarket in the land: "Spic & Span"!!!! Art
-
Newbie questions
Art Anderson replied to SynShadowzz's topic in Model Building Questions and Answers
If you like Ronsonol, you will love the price of it as its generic name: NAPTHA (seriously, that is what cigarette lighter fluid is, always has been!). You can get naptha in quarts or gallons at places such as Walmart, home improvement stores, even your friendly local paint stores (the ones that sell like, house paint). Art -
Paint on the glass
Art Anderson replied to hotrod59f100's topic in Model Building Questions and Answers
No reason why not! the 'glass" in a plastic model kit is simply clear styrene, nothing more, nothing less. Art -
Purdue Alum Virgil "Gus" Grissom is memorialized at Purdue University by the naming of the Aerospace Engineering Building "Grissom Hall". Roger Chaffee, also a Purdue Alumus, has Chaffee Hall at the airport (Aviation Technology Campus of Purdue). Of course, there is the Neil Armstrong Hall of Engineering, one of the largest buildings on the Engineering Campus (opened and dedicated in 2009), funded by gifts from members of the Purdue Class of 1955, Armstrong only reluctantly allowing them to name the building for him (Neil Armstrong is known for his not wanting to live in any sort of spotlight just for being the first man to set foot on the moon). This is a continuation of a tradition at Purdue, starting with Amelia Earhart, who was a frequent lecturer on the Purdue campus in the 1930's, and a special adviser to women students and staff while there. The plane she was flying when she disappeared over the South Pacific was funded by Purdue Research Foundation, at the leadership of David Ross, longtime engineering professor and trustee, himself the developer of the Ross Steering Gear which guided many a car and truck on our highways. Earhart is today remembered on campus by Earhart Residence Hall and by the presence of her personal belongings and papers in the archives of the Library. Art
-
I give my hat down to the Navy SEALs.
Art Anderson replied to '08SEAL's topic in General Automotive Talk (Trucks and Cars)
The US Navy has been at the forefront of confronting piracy since 1803, when the Navy mounted a campaign against the Barbary Pirates, starting with Libya and Tripoli. In less than a year, our Navy achieved what the two largest world powers, England and France, were afaid to do, take the battle to the bandits directly! And in the middle? USMC. Art -
who's seen "Flight of the Phoenix" ?
Art Anderson replied to 62rebel's topic in General Automotive Talk (Trucks and Cars)
No, the movie plane was a Fairchild C-82, the first iteration of the "Flying Boxcar" aircraft. C-82's came along right at the end of WW-II, flew some in Korea, and were phased out in favor of the much better Fairchild C-119. There were a few C-82's used in civilian service in the 50's and 60's though. Art -
New X-Acto Blades
Art Anderson replied to Modlbldr's topic in General Automotive Talk (Trucks and Cars)
I still swear by Squadron Shop #11 surgical scalpel blades. -
Why were there no GM aero cars?
Art Anderson replied to Fabrux's topic in General Automotive Talk (Trucks and Cars)
Most today are unaware that during the Kennedy/Johnson years of the 1960's, the Anti-Trust Division of the US Dept of Justice was preparing an anti-trust case against General Motors, who by that decade held over 55% of the US new car market--putting GM allegedly in conflict with the provisions of the Sherman and Clayton Anti Trust Acts. (the same laws which were used to break up ATT&T and IBM in the 1970's). In order to forestall any bad publicity, GM officially pulled out of sponsoring any form of racing activity--although some was still done "out the side door". Coupled with these issues was the increased scrutiny by the likes of Ralph Nader and the fledgling auto safety movement in Washington DC, GM having been given a pretty black eye over a couple of their marques. Art -
humbrol enamel
Art Anderson replied to Lownslow's topic in General Automotive Talk (Trucks and Cars)
Two things: I've found the Modelmaster squeezebulb plastic "syringes" perfect for decanting Humbrol enamel into my airbrush jar (they clean up readily by flushing with lacquer thinner), and that negates the mess from trying to pour paint from those little tinlets. Second, sounds like this is a perfect reason to adopt a food dehydrator to speed up the drying time. Humbrol is a classic enamel, slow to cure out, but very nice when dried. Art