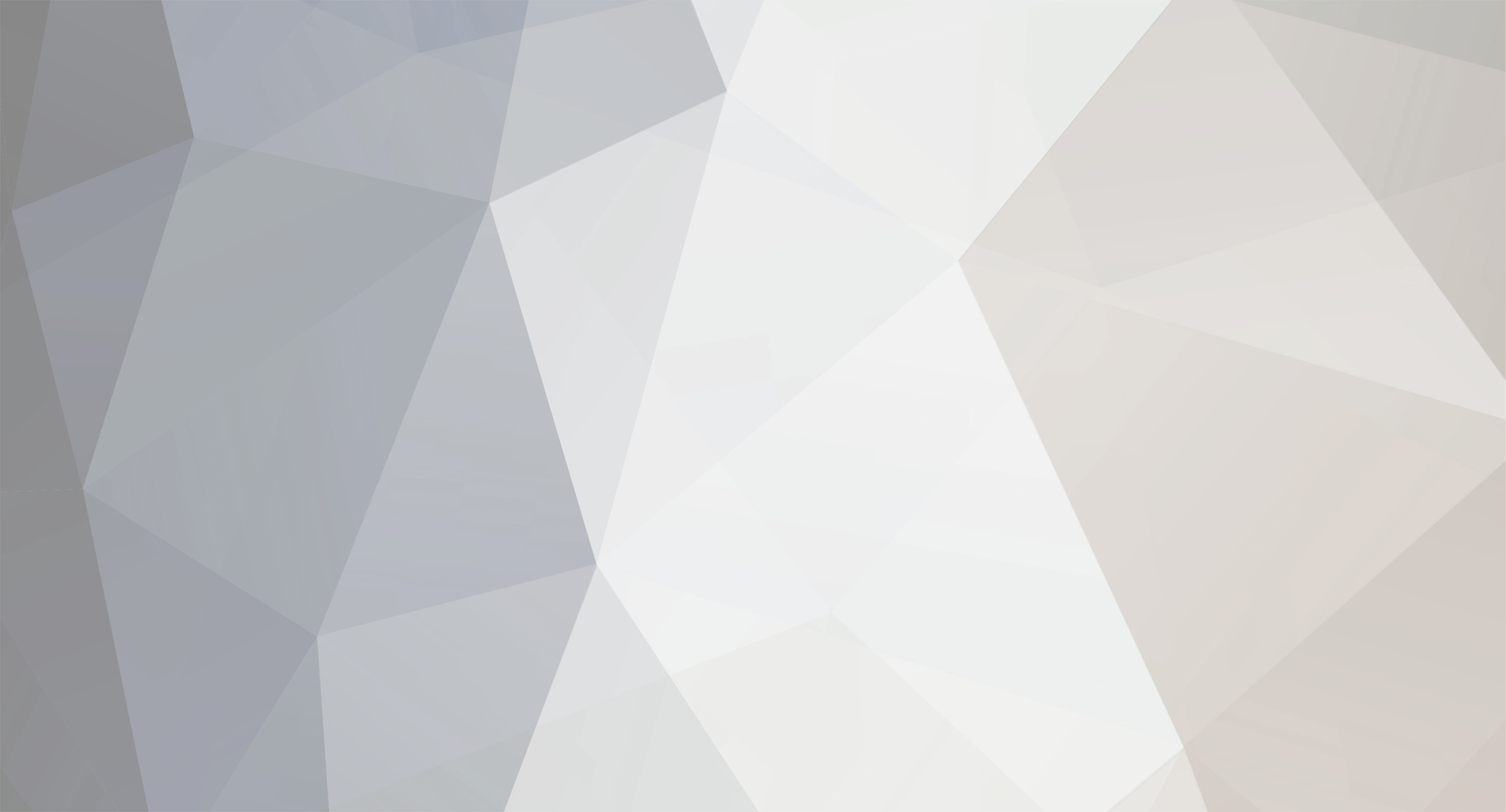
Art Anderson
Members-
Posts
5,052 -
Joined
-
Last visited
Content Type
Profiles
Forums
Events
Gallery
Everything posted by Art Anderson
-
Stripping paint from a resin?
Art Anderson replied to disabled modeler's topic in Model Building Questions and Answers
Westley's active ingredient is TSP, or Tri Sodium Phosphate--which can be had in other forms. TSP is widely used in the restoration of antique furniture for stripping lacquers and shellacs (which is what most furniture is finished with). You can get TSP at most home improvement stores, or paint stores--as well as at your local supermarket (Spic & Span). Hope this helps out a bit! Art -
"32 Ford article
Art Anderson replied to Pete L.'s topic in General Automotive Talk (Trucks and Cars)
There really is no good way to do that fender "reveal" on the AMT Chassis, as it is actually recessed into the side, or "web" of the frame rail. Art -
"32 Ford article
Art Anderson replied to Pete L.'s topic in General Automotive Talk (Trucks and Cars)
It would be much easier to just use the currently available Revell '32 frame actually. One caveat on that one though: The actual frame has the line of the front fender trailing edge, the running board, and the lower front edge of the rear fender pressed into it, for one simple reason: Ford, looking for both styling and simplicity, omitted the "splash apron" between the body sills and fenders & running boards for 1932, due in large part to the greatly increased width of the Deuce frame over say, that of Model A or Model T. While Revell did this "reveal", for assembly purposes, they made the bottom edge of the "reveal" squared off and flat in cross section, where the actual frame rails had this as a rounded, almost body molding look. In addition, Revell tooled the "dimpled in" part with a sharp corner at the top of the lower edge of the reveal. To correct this is simple: Round off the edges of that bottom edge of the reveal (looks like a "lip" running down the bottom edge of the frame rail; then add a little "fillet" of your favorite putty along the upper edge of that "lip" to round out the corner that's molded into it. This will take a special too--go to Michael's, Hobby Lobby, or any art supply store and buy the smallest stainless steel artists's pallette knife you can get (these look like a miniature masonry trowel, and the smallest ones out there have a very tight radius to their very tip, perfect for spreading body putty, BTW), Then with some careful sanding (use some worn wet or dry sandpaper ,rolled up very tightly, and carefully sand that putty until you have a reveal lip that looks in cross-section like a tiny letter S. Art -
Actually, the only difference between the '55 C-300 and the '56 300-B was the dashboard! '55 had the selector for the Powerflite automatic transmission on the dashboard, '56 300B had the first of the Torqueflyte pushbutton consoles to the left of the steering wheel. Art Luc, is that an assination threat?
-
I have test shots here, of the wire wheels, as well as the wheelcovers! As for the wires--let's just say if those spokes were hardened steel, they'd cut your finger as surely as a #11 blade! Beeeeyoooootifulllllllllll! Art
-
I just got done cleaning up and painting a sample of the convertible--and sanding off the mold lines took less that 15-minutes! I also have a sample of the coupe kit that was done pursuant to complaints, and it's the same way. Mold parting lines are a fact of life with injection molded styrene plastic bodies--always have, and always will be--but the bodies I have here now are a testament to the millwrights in the factory--as perfect as perfect gets! Art
-
Just started another Hudson!
Art Anderson replied to Art Anderson's topic in General Automotive Talk (Trucks and Cars)
Oh, it happened all right! Pics when I get the clear on the red--really kinda hate that ModelMaster base coat/clear coat process though! -
Sample of the upcoming Moebius Hudson Hornet Convertible. I am tickled that the factory corrected all those nasty body mold alignment issues that a lot of people complained about--shows that the millwrights in the factory truly earned their pay in doing the setups (have a sample of the coupe body that is also just as nice now!). Seriously, it took me just 15 minutes to clean up the very faint mold parting lines--the way any model car body should be, in my never-to-be-humble-opinion. Great job Moebius!!! This one's gonna be bright red (a convertible any other color is just bland!) with red leather interior as well. There will be pics of this as it progresses--thinking about wiring the engine on both cars now. Art
-
diecast paint removal?
Art Anderson replied to diehard44's topic in Model Building Questions and Answers
Aircraft grade paint stripper works, and works very quickly. Use protective rubber gloves, and a cheap paintbrush (hardware store type). That will take all the paint off your diecast in mere minutes. Art -
Non-Tip Tenax Holder (Cheap)
Art Anderson replied to von Zipper's topic in Tips, Tricks, and Tutorials
Given that Tenax isn't readily available, here's my solution: I bought, about 10yrs ago, a pint can of Weld-On #3 (so very similar to Tenax, it works exactly the same), for the unbelievable price of $8, at an industrial plastics supply house here (most cities of any size at all have somebody who deals in plexiglas and the liquid cements --generally Weld-ON--look in the yellow pages, or White Pages online). I use a common turkey baster to transfer Weld-On as needed to my Tenax bottle, works like a charm! I second the idea of using rattle can tops to provide a spill resistant carrier for those pesky little bottles, too! Great idea! Art -
Fingernail Polish. Yes, but...
Art Anderson replied to Lunajammer's topic in Model Building Questions and Answers
It's been a few years since I've sprayed fingernail polish, but ordinary lacquer thinner will thin it for airbrushing. Art -
The Hess Training Van was a very good rendition of the GMC Motor Home circa 1973-80, in 1/25th scale as well. Art
-
"Klingon Kruiser"!
-
Bare Metal Foil brand decal paper?
Art Anderson replied to RickRollerLT1's topic in Model Building Questions and Answers
They don't actually make the stuff, rather they have sold clear decal film for a lot of years--stemming from when Eldred Mason of BMF was pitching the foil primarily to aircraft modelers for natural metal finishes. They offered a small line of aircraft markings in those years as well. Art -
Resin Casting Wheels
Art Anderson replied to steve7119's topic in Model Building Questions and Answers
A bit more complicated. MOdelhaus does this kind of whitewall tire--black resin tire, with white resin whitewall insert pressed into it. To master this will take a small lathe, and some practice to get masters that fit cleanly together. Art -
USAF Museum's Dora is a testament to how crude German planes became toward war's end: Ill fitting panels, including horrid gaps between sheets of aluminum, lumps and bumps everywhere (not planned, just a severe lack of attention to ensuring that shapes and contours matched, panel to panel. That paddle-bladed prop was anything but smooth--USAF's appears to have been made from laminated wood blades, covered over with bands of cotton-reinforced black rubber. By contrast, the all-original Ju-87 Stuka (North Africa, 1941-42) that hangs in the transportation gallery at Chicago's Museum of Science & Industry is a masterpiece of the craftsmanship Germany was known for in non-crisis times. Art
-
Not Andy, but yes, the Tognotti King T uses a mix of 1914 and 1915 bodywork and sheet metal. Before anyone wonders, that wasn't an unusual thing at Ford, or for that matter, most any other carmaker in those years before WW-I. There was no such thing as a "model year" back then, no annual styling changes--just the "running changes" of new parts being slipped in constantly, for whatever reason. It wasn't at all uncommon for say, 1915 rear fenders to be bolted onto 1914 cars as they became available--of course assuming that they'd fit properly. Art
-
TESTORS paint prices....OUCH.!
Art Anderson replied to AMT4EVR's topic in General Automotive Talk (Trucks and Cars)
With hobby paints, it's not the paint itself that is so expensive, but rather the little glass bottles! I just looked up, for reference, the list price for a Badger 3/4 oz glass bottle--$1.82, and that's with a plastic cap! Now, the production cost for a 1/4 oz glass bottle can't be all that much different--just the cost of the glass material itself--many other factors to consider here. In short, just as with many other liquid products, it's not the product in the package nearly as much as the packaging itself. Also, take into account the weight: The little bottles of paint we use are shipped generally in either dozens or half dozens, depending on the size of the bottle of paint. In the scope of plastic model building, paint is the heaviest by weight/carton volume of anything we buy for our hobby. Weight affects shipping costs more than volume, given the weight limits necessarily imposed on individual shipping cartons, and the trucks & other conveyances used to deliver those products to the stores we buy from (the same thing comes into play when ordering by mail, phone or online--weight is a major factor in the shipping cost to you as well. The enamels and lacquers we all like using are also petrochemical based (even the waterborne stuff relies on petroleum for at least some of its feedstocks), and I've been noticing for years that the price of petroleum has trended upward dramatically in the years since I bought my first bottle of model paint, certainly since I bought my first gallon of gasoline to fuel the lawnmower which provided a few $$ with which to buy model kits back in the late 1950's. Ever wonder why returnable glass bottles disappeared from the soft drink and dairy industries? The same thing, the cost of those heavy bottles, both in manufacture and in the cycling the empties back through the bottling plants and dairies. Also, think of the sheer weight of those Coke bottles, the pint, quart, half gallon and gallon glass milk bottles--the added weight made for shipping considerations to and from the bottling plants. I can still remember the first 1/4 oz bottles of Testors I bought--from a neighborhood Five & Dime store--ten-cents----back in 1957! It took only about 2 years for those bottles of Testors to go up to 15-cents each, and then about 1971 or so, 20 and then very quickly, 25-cents due to inflation at that time. A rattle can of spray paint? Well, in the summer of 1959, I bought my first AMT '40 Ford Coupe kit, and right there was a rack of Pactra 'Namel spray paints. The price of that first rattle can of Pactra (Testors was a year or two away from introducing their spray cans)? 59-cents, which price held for less than a year before they went up to 69-cents. Now, that was a time when that first AMT '40 Ford kit cost me $1.49, and no sales tax--but still, for a 15yr old kid, that could be a major purchase back then. Imagine the sticker shock, when in 1962, AMT Corporation introduced their line of spray lacquers formulated for use directly on styrene: 5-oz spray can would set you back 89-cents, fully 20-cents more than the smaller cans from Pactra and Testors. It wasn't until 1964, when AMT changed their packaging down to the 3.5oz size the others were selling. In short, the costs of model kits and the supplies we use, absent uncontrollable shifts in the prices of raw materials, is, and has almost always been, relative --shifting upward right along with everything else. Art -
Resin Casting Wheels
Art Anderson replied to steve7119's topic in Model Building Questions and Answers
I suspect that there will be an article on casting wheels (both the modern 2-piece type and the older, one piece "wire axle" wheels from years past) in the pages of MCM in the fairly near future. In the meantime, if you want advice on how to do it, feel free to contact me. Art -
Izzy! Welcome back!!! Model car building (and the skills you acquired) is kinda like riding a bicycle: Once you learn, you never really forget! Art
-
Jeep chassis question
Art Anderson replied to Kris Morgan's topic in General Automotive Talk (Trucks and Cars)
Kris, Do a little bit of online research here. Search for Jeep vehicle specs, particularly wheelbase--if the wheelbase of the '69 Jeepster and the Commando are the same, then most likely the frame is the same for both. In this, Google can be your very best assistant! Art -
Acrylic runs when cleared?
Art Anderson replied to VooDooCC's topic in Model Building Questions and Answers
I suspect that waterborne acrylics can be penetrated by additional coats of the same basic carrier--in much the same manner as lacquers behave. -
Need quieter compressor
Art Anderson replied to Steve362's topic in General Automotive Talk (Trucks and Cars)
I have a Badger 180 that I simply set on a folded, LARGE beach towel--that makes it literally whisper-quiet, and the old lady who lives right under my model room NEVER hears it! I would guess that is more than quiet enough, and fairly inexpensive too! (Apartment dweller I am!) Art