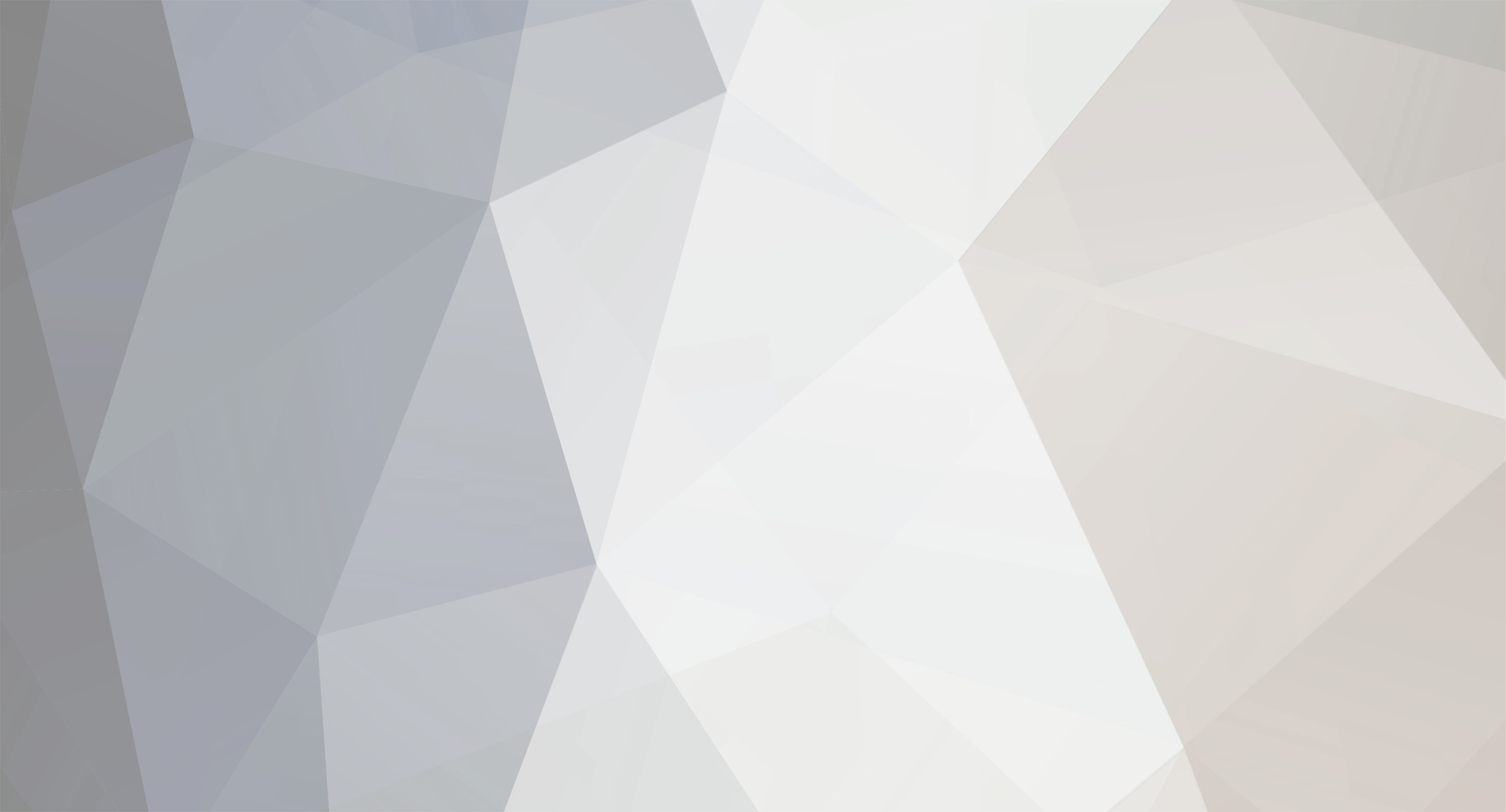
Art Anderson
Members-
Posts
5,052 -
Joined
-
Last visited
Content Type
Profiles
Forums
Events
Gallery
Everything posted by Art Anderson
-
Happy 236th Birthday Marines
Art Anderson replied to Clay's topic in General Automotive Talk (Trucks and Cars)
As a historical note: The Continental Congress noted the unflinching courage of La Compagnie de la Marine--the first marine corps in the world, from the Royal French Navy, who helped our ancestors convince the British to let this country be independent. A company of French Marines garrisoned Post Ouiatenon, which stood just 4 miles downstream on the banks of the Wabash River from where Lafayette IN, my hometown now stands. It was from that service that the inspiration for USMC came, and Thank God our Leathernecks took up the challenge! Art -
Happy 236th Birthday Marines
Art Anderson replied to Clay's topic in General Automotive Talk (Trucks and Cars)
Clay, One of my closest buddies when I was in Jr Hi and HS, left school at 16 to become a marine--he served from 1960 until retirement in 1990--always saw him as a true American hero! An uncle of mine was a decorated Marine in WW-II, have the utmost respect for him as well. Thank you for your service to this, our country! Art -
And Then There Were A Few Promos...
Art Anderson replied to Junkman's topic in General Automotive Talk (Trucks and Cars)
That pic reminds me of an old friend, the late Bill Harrison of Monta Vista CA. Bill's home was THE place to visit whenever I went to NNL West back in the 90's--ranch style home, chock full of models, model car kits, promo's and TONS of literature about both real cars and model cars! I think it could be said that if the "Big One" had ever hit, Bill's house would be the only one on the block still standing--it could not have collapsed due to the sheer cubic volume of model car kits (his attic space was also packed full! He showed me, with obvious pride, his "Ford room", AKA his bedroom, more model kits of Fords than I knew existed (one stack, floor to ceiling, of nothing but Revell '57 Ford Country Squire kits--you know, the unobtainium one!). The attached garage had been remodeled into a large family room before he bought the place in the 1960's, and it was a veritable museum of model cars, from diecasts to promos, to built kits, to even a few Gerald Wingrove scratchbuilds! If you ever saw the movie "Tucker, A Man And His Dream" where Harrison Ford mimicked the famous portrait of Tucker holding a 1/8 scale Tucker in his arms--Bill HAD that actual model Tucker!. In his model car workroom, Bill had perhaps a dozen 5' filing cabinets, each one filled with Xerox copies of magazine articles on flathead Ford V8 cars (Bill's first love), all organized, sorted, a gold mine of reference materials. Bill was on a first-name basis with not only many legendary modelers, but also museum curators all across the country. Bill's garage out back was cool as heck too! In the middle stall was a cherry 1941 Buick Century Sedanette, its straight eight engine factory equipped with dual carburetors, and next to that was a '32 Ford Panel Delivery. Out in the yard were TWO 1932 Ford pickups, both closed cab trucks. In his living room were literally aisles and tunnels (enough to make any film noir recluse drool with envy) of stacks of car magazines--and the bookshelves filled with virtually every book on antique and classic era cars ever printed up to the time of his death about 4 years ago. Nothihg like seeing that to get the creative juices flowing!!!! Art -
JO-HAN Molds?
Art Anderson replied to gbdolfans's topic in General Automotive Talk (Trucks and Cars)
Basically, X-EL Products was a brand name used by JoHan from about 1978 on to the end of the original JoHan company. X-EL models were "retro-promo's in the truest sense of the word--old promotional model tooling used to mold new promo's, but in styrene rather than the original acetate (through 1962) or Cycolac. Such long forgotten pieces as 1955-56 Pontiac Star Chiefs, 1957 Oldsmobile 98 Scenicoupe, 1958-60 Cadillac Fleetwood 60 Special sedans, 1962 Studebaker Lark, 1968 Chrysler Imperial hardtop, 1974/75 Oldsmobile Cutlass Hardtops--those got the retro promo reissue treatment. Art -
The Lindberg Chris-Craft Constellation is a HUGE model, for starters! IIRC, the tooling is that of a MARX (MARX Toys was the "Mattel" of the 1920's through the early 1960's--if it was an action toy, MARX had it!). This was designed from the outset as a motorized scale model, and when Lindberg acquired the tooling in the early 1980's, they updated the engineering (mostly internal) to accommodate a twin Mabuchi 540 (the same series Mabuchi DC motors that powered the hobby grade RC cars of the 80's) motors, with gear reduction, propellor shafts and 2-blade screws, all designed of rradio control. The boat is actually quite durable, with the hull being at minimum, 1/8 thick styrene (perhaps as thick as 1/4" on the bottom, for additional weight, and was designed to carry two 6-cell, 7.2V NiCad battery packs. While there is no interior detail (the large windows are screened off with injection molded plastic venetian blinds), the exterior is very nicely done, and it's actually quite accurate as well. I have the kit from Lindberg's 1985 reissue, not yet built, and it was costly even then--I seem to recall (and I stocked the kit in my hobby shop "The Modelmaker" then) $69.95 MSRP. I suspect that the price point was determined by the expected sales, which would have been far less than say, a 1/25 scale car kit, and the tooling had to be so large as to require more than one tool base, perhaps 3 injection molding presses to produce. One of my friends did build up one for radio control about that time, and I had the opportunity to run it, in a park pond in suburban Chicago--the thing looks incredibly realistic, especially as it rides in the water, and at full throttle, planes very much like the real thing. All Dave did besides building it, was to install a 2-channel radio control unit, an electronic speed control, and of course, the two 6-cell battery packs. Large scale boats such as this have always been far more expensive than the model car kits we like to build, but once built and a radio installed, they can be a ton of fun, especially in a public park setting, where they really draw a crowd of spectators. Art
-
AMT Double Dragster -Tin Edition
Art Anderson replied to Tom Jackson's topic in Car Kit News & Reviews
Blake and all who weren't around when kits like this were new: Plastic model kits are a combination of "art" and "technology". Now, the technology of injecting molten plastic into steel dies has been around for perhaps 75 yrs or so--and it hasn't changed all that much. However, the "artistry" of plastic model kit design and development has evolved considerably since the first plastic model car kits were produced about 1950-51. There were two major factors in the design and development of plastic model car kits in those early years: First, the types and grades of plastic available at the time, and second, the expected age range of the marketplace for those kits. Plastic model kits of all subjects began as an outgrowth of the toy industry (Yes Virginia, Revell started out as a plastic toy manufacturer!) The people involved in design and development were, at the outset--more industrial designers and pattern makers, given that there really weren't highly skilled scale modelers around back then, certainly not to the extent we see today. In those early days, "plastic" anything made primarily for kids had a rather bad reputation. Some of us can remember plastic stuff breaking, giving numerous cut fingers from the resulting shards which could be as sharp as shattered glass. To counter this, acetate plastic was pretty common--often termed "shatterproof" plastic. But that required rather thick sections, as acetate warps badly over time (witness all those warped 50's promotional model cars from the 1950's). Those early model kits had to evolve around parameters such as described above, frankly. There weren't all that many adults building model cars in the 50's, even into the 1960's--model cars (and even plastic kits of planes, ships and other subjects) were seen, and more than truly were, the province of kids from about the age of 8 or so, to perhaps 15 or 16. So, enter "buildability", or ease of assembly--our attention spans were really not that much different than kids of the same ages today--we wanted the model, we wanted to get it built, and get it built "right now". Being kids, we also wanted to play with them once built, and play with them we did. I still remember (and will be meeting up with, next September, my old schoolmates at our HS 50th anniversary class reunion) getting together with buddies, either my place or their's, finding a tabletop or a cedar chest that could serve as an aircraft carrier flight deck for "launching and recovering" those plastic model airplane kits we built. With the coming of more or less shatterproof styrene plastic compounds by the middle 1950's, the warping went away, and as multi-slide core molds came online-one piece bodies. However, that early styrene was still pretty brittle (even today, a MIB AMT or Johan body shell from the late 50's/early 60's can break like glass -- and that meant still thicker body shell thicknesses, and correspondingly "heavy" parts like frames, Ford I-beam front axles--all that. In addition, wire axles were pretty much standard--for all the reasons I noted above--not the least of which the ability of the finished model car to be played with by young hands. It wasn't until kits such as the AMT Double T 3in1, the Double Dragster (both kits originating in late 1961/early 1962, along with the Ala Kart/'29 Model A Roadster) that model car kits began to evolve into the much more highly detailed, more intricate kits that we know today. And that brings in the "artistry" of creating really neat model car kits, kits which once built, could not withstand much, if any play, but looked cool as all heck when finished. That took a lot of work on the part of kit manufacturers--and a considerable learning curve as well. Some of the Revell products of the mid-60's, for all their appeal (and MPC as well!) were highly designed, lots of minute, intricate parts, but exhibiting either tremendous fragility, sloppy fit and tolerances, or often, both. Remember too, CAD and CAM were light years into the future--those older model kits were first drawn up by drafting pens against T-squares, triangles, and "french curves" on vellum--no computer aided design back then, no laser scanning either. Tooling mockups were made in basswood blocks, 2-2.5 times larger than the production model kit as well. Tons and tons of hand work at every stage of the game. Tooling itself was cut on milling machines, using 3-dimensional pantographs which both created the 3D molds while being dialed in to reduce the shapes from say, a 1/10th scale mockup down to 1/25th scale, all the while translating a "male" 3D mockup to a "female" injection molding cavity. With all that, one should marvel at how well that all came about really! I think the bottom line ought to be: Round2 (and AMT/Ertl before them, in their Blueprinter Series) never has (to the best of my knowledge) pitched this double kit as something new, the latest and greatest; but rather exactly for what it is, a reissue of a long hibernating model car kit from 50 years ago, that some people might just want to build another one of. It's neither fish nor fowl, neither a plastic blob nor the latest and greatest--but it is a "blat from the past" for a lot of modelers with more grey than color in their hair. Art -
flathead supercharger
Art Anderson replied to southpier's topic in General Automotive Talk (Trucks and Cars)
Superchargers that work on flathead Ford V8's need to be on the mild side: Centrifugal units, such as the Frenzel, or turbine units like the Latham,, even the relatively mild positive displacement "Rootes Type" such as the S.C.O.T unit worked. However, the best known blowers in the hot rodding crowd, the GMC blowers, were built for supercharging 71-series Detroit Diesels ("71" meant 71cid per cylinder, and the blowers were meant to scavenge exhaust gasses from those engines, which were 2-cycle motors) and generally are far too potent for a flathead Ford. Flathead Ford V8's come out of the 1930's. and during those years, the occasional supercharger that was used in automotive applications was a centrifugal unit--think Duesenberg, Cord, Auburn, Graham Paige here. Positive displacement blowers such as the principle in the Jimmy blower, were confined largely to European engines, where their use was intermittent at best (Bugatti, BMW, Mercedes Benz) where if they were engaged 100% of the time, they'd simply destroy the engine they were mounted on. Art -
oil based enamel question
Art Anderson replied to foxbat426's topic in General Automotive Talk (Trucks and Cars)
Simple answer is: Lacquer thinner works very well with oil based enamels, always has and I assume always will. Now, with Tamiya, their enamels are waterborne, so that advice may well be off. Art -
I may have posted this earlier, but here goes again: Living where I do, and working where I do, there is absolutely no reason whatsoever for me to tie up thousands of dollars in a car, not to mention the annual expenses for same. I can get to work by bike weather permitting, go pretty much wherever I want by bike in good weather, and when it's inclement, Citybus is my best friend (and my employer, a Big Ten University, pays my bus fare--and the busses have bike racks on them--great for getting up the one steep hill I would climb coming home). In addition, I LOVE biking, and have since I got my first bike at age 11 in 1955--there is a "freedom" that comes on the back of a bicycle that cannot be duplicated any other way, IMHO--the freedom of being able to go wherever there is a pathway or bikeway, street, even a sidewalk. Nothing beats the excitement of making that "wild" move from street to sidewalk or bike path, or of beating city traffic by numerous minutes by being able to take advantage of shortcuts accessible only by bike. In addition, biking as often as possible (my parameters are temperature above 20F, no rain, no snow or ice on the ground), I've lost about 40lbs since I took it up seriously in 2007. My ride? Iron Horse Maverick 4.2 24spd offroader, three springs, all alloy, disc brakes (and yes, I have used EVERY one of those gears at one time or another!) Art
-
Buying more than is financially healthy
Art Anderson replied to Jantrix's topic in General Automotive Talk (Trucks and Cars)
I've been buying more model car kits than I build since perhaps 1961---When I learned that I couldn't get that kit I wanted to build when I wanted to build it. It really took off in my resin casting years--I HAD to get multiples of any kit I might want to do a conversion of. Still do it, although not to the extent I did years ago--but my klt stash still grows. Art -
Hudson never produced a station wagon in any form in their entire history. There were a few Hudson woodies in the years prior to WW-II, but they were all done outside the factory, not truly a listed body style from Hudson. Art
-
How do you do resins?
Art Anderson replied to SSNova70's topic in Car Aftermarket / Resin / 3D Printed
Yeah, a long commute from Lafayette! Seriously though, I need to get up to your place, perhaps do a photo shoot? Art -
As is the Monogram '30 Model A Phaeton, the Monogram 1930 Packard Speedster Phaeton, the Monogram 1931 Packard Dual Cowl Phaeton, the Monogram '32 Cadillac Dual Cowl Phaeton, the Monogram Duesenberg Torpedo Phaeton, the Monogram Duesenberg Town Car, the Monogram '31 Rolls Royce Sport Phaeton, The AMT 1907 Thomas Flyer, the Tonka 1913 Model T Touring Car, The AAM 1932 Duesenberg Limousine, the AAM 1937 Cord sedans, AMT/Ertl 1941 Ford Station Wagon, the Revell 1948 Ford Station Wagon, the Aurora 1950 Mercury Station Wagon (Mod Squad)..I may have missed a couple. Art
-
Missed: AMT 1963 Chevy II station wagon AMT Craftsman Series 1960 Impala Nomad wagon AMT 1964 Chevelle wagon JoHan 1960 Cadillac Fleetwood 60 Special 6-window sedan (4dr) JoHan 1962 Oldsmobile 98 4dr hardtop SMP 1960 Corvair 4dr Sedan SMP 1960 Chrysler Valiant Hubley 1960-62 Ford fullsize 4dr sedans AMT 1961 Pontiac Tempest 4dr sedan JoHan 1961 Cadillac Fleetwood 60 Special 4dr hardtop JoHan 1962 Cadillac Fleetwood 4dr hardtop John Heyer resin 1961/62 Corvair Lakewood station wagon Modelhaus makes/made several 1961 Chrysler and Dodge station wagons JoHan made a number of mid-size AMC Rambler Classic station wagons from this era as promo's Hubley produced (reissued by Minicraft) a 1959 Rolls Royce Silver Cloud 4dr Saloon (sedan) that differs from a 1960 ONLY in the headlights (1960 had quad headlights) Premier did a 1960 (?) Studebaker Lark 4dr sedan Art Check me if I'm wrong, but didn't Revell's 1962 model car kit line include a midsized Dodge and Imperial 4dr hardtops?
-
Brand New 65 Mustangs
Art Anderson replied to Skydime's topic in General Automotive Talk (Trucks and Cars)
Also, prior to January 1 1955, almost universally, cars were ID'd and titled by their engine number, NOT the frame or body number. Now, try to get THAT one past your local license branch today (especially if your collector car has had an engine transplant! Someone has already mentioned Duesenbergs: Certainly starting with the 1929 Duesenberg Model J, they were identified by both engine number (starting with the letter J), AND the Frame number, which was not stamped into the frame, but rather lettered on by hand in white paint! Model A Fords had engine numbers beginning with the letter A stamped into a flat rectangle on the left side of the engine block, and a frame number stamped into the top flange right under the front right body mount, where it could never be seen, and often rust pitted into oblivion. Art -
How do you do resins?
Art Anderson replied to SSNova70's topic in Car Aftermarket / Resin / 3D Printed
Not unless (or until) Gregg and I go through the process of making a full body shell. And therein lies the rub! Making simple parts is one thing, a body shell is a whole 'nuther animal indeed. (the same would be true of most cargo bodies). If you are thinking of reproducing a production cab or truck body, you would be well-advised to consider the cost: The first full body I ever cast was the very rare (and today EXPENSIVE!) MPC '32 Chevy Sedan Delivery. I did that one in late December 1988, used about $40 worth of Silicone RTV rubber to get there--but bear in mind, I had my mind set firmly on going into the business of producing resin cast products commercially--so this was a "five finger" exercise--the result wasn't something I would have considered commercially viable at that stage of my knowledge or skills). Now, at that point in time, I was looking at going forward, learning. However, if I had as my goal making perhaps one or two for myself, likely I would have just built the styrene kit (I had, and still have, 3 of those kits). But compare the costs of reproducing something like that vs just building the thing--most generally, costs should tell you that it's not cost-effective. Now, if you are thinking of doing a conversion of an existing truck body or cab, that's different--but even there, you need to consider a few things: Is there any advantage to building up a resin piece that you made solely for yourself, or do you plan to sell copies of it? If the first, probably again, the costs don't justify (at least for most people) going to all the work, and the considerable risk that you will damage, perhaps irreparably, the master you created--there are ways to minimize potential damage--by doing things in the process of converting/constructing the cab/body for use as a master. But in any event, there is a definite learning curve involved, and especially with a full body shell or other large, hollow 3D unit, to get a decent part. That's a bit involved right at the moment, as Gregg and I are starting at the very beginning, the "training wheels on the bicycle" stage if you will. Stay tuned to MCM, if this thing goes far enough, and Gregg is willing to do the work (I have no place in my apartment to do a full body shell, even if I wanted to, yet I still have ALL the equipment with which to do ome). But in the bottom line, consider what it is you are thinking of casting, determine if the $$ it will cost are worth investing, as opposed to just building either an available (even if an out-of-production kit body, or your own conversion or scratchbuilt unit) versus just building it up all the way, or building that seemingly rare kit you may be thinking of. Art -
Chuck, Welcome to the world of th e1950's! Art
-
Actually Harry, if you look at the kit parts, you will see not two frame rails, but four! At the rear wheels on the real car, the two frame rails are there, on inboard, and one outboard, of the wheels themselves. Stepdown Hudsons were built so stout, most scrapyards would not take them (back in the late 50's-early 60's, because they could not be crushed! Does that say stout, or what? (Dad's '54 is rusting away in a farmer's back lot as I write this, car retired in 1961 (after the engine threw a rod on me--geez, now who is gonna accuse ME of stoplight drags?) Art
-
Desktop Milling Machine
Art Anderson replied to bill w's topic in General Automotive Talk (Trucks and Cars)
Sheesh, just the thought of a machine weighing 144lbs on my desktop? Hang the price, gotta think of the floor load. -
Extra parts in the Hudson?
Art Anderson replied to Jon Cole's topic in General Automotive Talk (Trucks and Cars)
Jon, Those appear to me to be lap belts, for the Nascar version--seatbelts in passenger cars were an almost unheard of thing in 1953, but racers were using WW-II military aircraft lap belts to keep them from sliding sideways on those bench seats on the racetrack. Art -
As Harry P notes, the wheelbase and overall length are right on--those dimensions are easily found, in the Standard Catalog of American Cars, also from Hudson-Essex-Terraplane Club, The Hostetler Hudson Museum in Shipshewanna IN, who gave invaluable reference help to Dave when the kit was in development, as well as the October 2011 issue of Collectible Automobile Magazine: It's 124", overall length being 208". As an aside here: Where on most cars having fender skirts as standard equipment the skirts filled in the rear wheel arch for that smooth, streamlined look, Hudson had a real need for them: Behind that fender skirt is a frame rail, outboard of the rear wheels (not possible to put that in the kit given the material thickness of the plastic required--the stub ends of that rail are on the frame member itself though in the kit. Without the skirts, this area of the car would have looked VERY unfinished indeed, even though in production, that area of the frame got painted body color (I remember very well, as I not only washed and waxed Dad's Hudsons as a kid, and in HS, had to change a rear tire once--a B of a job, even with the "scissors" jack Hudson provided for their cars--not easy to work the spare wheel and tire up into that wheel well at all!). As for overhang, not all that much body overhang at front or rear, a good portion of that was in the bumpers, which are pretty deeply drawn steel, on brackets extending them well out from the body front and rear (also, for those of us who remember the 40's and 50's, the departure angles of driveways both at home and at the gas station and supermarket were a LOT steeper than seen today--meaning that there had to be a lot more limitation to the overhang at front and rear to avoid unnecessary scraping of bumpers on pavement). As John Cole notes, the cut lines of the fender skirts did come out in the wrong place a bit, which of course many modelers will correct, and it's my understanding that this is correctible in the tooling still. Art