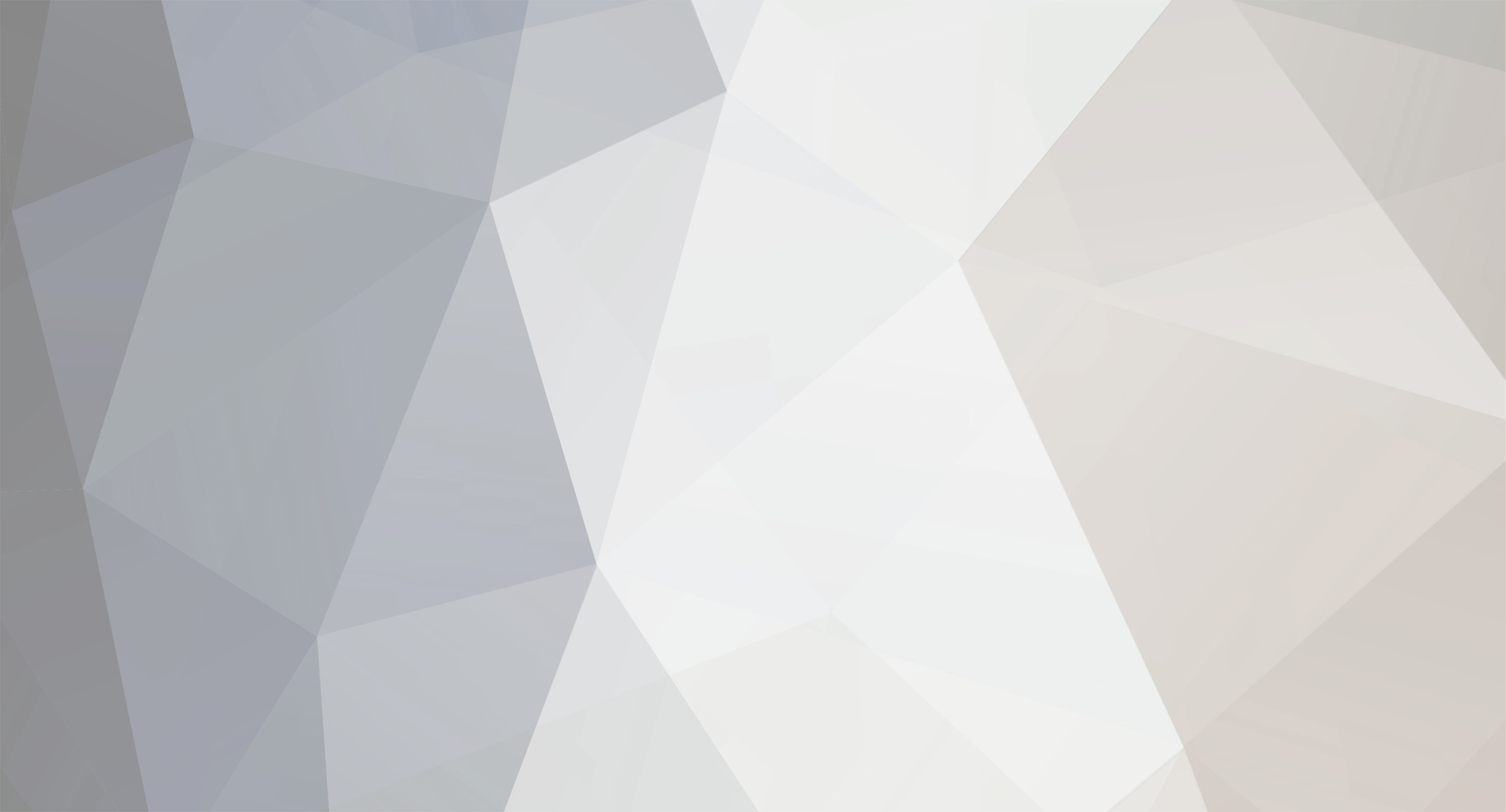
Art Anderson
Members-
Posts
5,052 -
Joined
-
Last visited
Content Type
Profiles
Forums
Events
Gallery
Everything posted by Art Anderson
-
The decline of the production of model kits of American cars in the 1970's had as much to do with the drop-off of the use of "promotional models" by the marketing & sales departments of the US "Big Three" (and American Motors); due to the rise of the large, mega-dealer showrooms and sales lots. Promotional models (or "promo's") had their heyday in the the time frame 1950 to about 1964-65; when. given the rather small size (compared to today) of new car dealerships, there was a need for some way to illustrate to potential car buyers the wide variety of body styles and colors and combinations of colors. From this came the idea of being able to have a whole pallette of colors of toy cars in the showroorm to show Mr and Mrs car buyer the possibilities. In addition, a promo was the perfect incentive for a salesman to give to the son of a prospect--pretty hard to turn down buying that new car you'd been looking at when your kid is busy ogling a scale model of it, given completely free of charge. It's from those promotional models of back then that our hobby really took off--those legendary 3in1 Annual series cars from AMT, JoHan, MPC stemmed first from promotional model tooling, with a few modifications, some added parts. Now, of course, while there were promo's of so-called "mainstream" cars (you know, 4dr sedans with 6 cylinder engines and bench seats), as model kits models of that sort of subject were guarranteed "dust catchers" on hobby shop shelves, so the emphasis very quickly became making customizing kits out of promo's of hardtops and convertibles--with the occasional station wagon thrown in. Additionally, by the early 1970's, the idea of annual major styling facelifts had given way to a particular set of sheetmetal being used for 3-4 years with only low-cost detail changes in stuff like grilles and headlights, interior upholstery patterns. The once-seemingly traditional fall outings by fathers and sons to see all the "new cars" at introduction time gave way to other pursuits. Yeah, the 70's saw their share of promotionals and model kits of more or less mainstream cars, driven by the desire still of automakers to have a promotional model/toy of their latest creation--think Gremlin, Pacer, Pinto, Vega, Aspen/Volare here. But the model kit market for models of new cars was still dominated by stuff like hardtops at the more desirable end of the spectrum--Olds Cutlasses, Cadillac Coupe DeVilles, Caprice Classics. Pickups and vans were one area that seemed to excite modelers, just as they were coming into their own in the 1:1 world. But, the 1970's began as the huge fad of building model cars (sheesh, in the 60's, I kinda think that virtually every red-blooded American boy at least tried to build a model car, somewhere about Jr High School) was starting to decline--the later Boomers had found other areas of pursuit it seems; by the end of that decade, the number of truly new kit announcements each year could be counted on the fingers of both hands, no need to take off your shoes to use your toes as counters! Had it not been for the tremendous "return" to the hobby of their youth by guys born say, 1944-50 (the leading edge of the Baby Boomer model car craze of the 60's) as adults, it's likely we'd not be having this conversation in August 2011. Art
-
The Bandai kit is only a "semi-clone" of the Monogram Duesenberg base kit. The body shell has one half of the hood molded in one piece with it, the other side (right side) is a separate part. The body shell is somewhat loosely done as the 1934 Figoni et Falaschi Berline, which was done in Paris. A Berline (pronounced "Ber-lin" just like the German capital city) is a sedan, designed to be either owner- or chauffeur-driven, with a retractable divider window at the back of the front seat. The actual car still exists, and differs a good bit from the Bandai kit. Bandai did the body shell to fit their 'clone" of the Monogram basic kit, meaning that the lower edge (sills) of the body are straight, and mate to the running board splash aprons on top of them, where the actual Figoni body is wider, almost predictive of the 1935-36 JN and SJN series Duesenbergs bodied by Rollston, having its sills outboard of the splash aprons, with a long sweeping curve below the top line of the frame. Other than that, the body lines are very, very close to the actual car. Bandai also did a much more crude knock-off of the Monogram '37 Cord 812 Supercharged Convertible Phaeton--hardly worth mentioning. An addition to the lists I've seen here should be the Monogram metal-bodied 1:24 scale 1931 Packard 845 Dual Cowl Phaeton. It's not done on the same chassis as their Speedster Boattail or their Speedster Phaeton, but the similarities would make one think so at first glance. I remember being shown drawings in 1981, for a second release on the Monogram 1932 Cadillac Model 452 V-16 Phaeton, that body being the Fleetwood Convertible Victoria, which would have been a stunning kit if it had been done. Another classic era car kit that was announced (even to the point of having a scratchbuilt display model built for the 1966 Hobby Industry Association Trade Show (used to be held every January at the old Sherman House Hotel in downtown Chicago--forerunner of RCHTA/iHobby); that being the 1928 Miller '91" Indianapolis 500 winner, the car driven by Louis Meyer (later of Meyer-Drake--producer of Offenhauser racing engines 1945-1979). This kit was stillborn however, probably due to a serious lack of pre-orders from hobby wholesalers and retail shops. Art
-
Chrome turned gold - Tamiya clear orange
Art Anderson replied to Jantrix's topic in Model Building Questions and Answers
Tamiya Clear Yellow will do the job as well. Art -
Of course, bear in mind that the aircraft carriers of the Royal Navy were considerably smaller than even the early "short hull" Essex Class ships of USN (more on a par with the first USS Ranger (first ship to be built from the keel up as an aircraft carrier). That meant smaller (in numbers) aircraft complements), and reduced storage capacity in the hangar deck (USN Essex Class carriers were built with the capability of slinging spare fighters, dive bombers, even torpedo planes from chain falls up underneath the underside of the flight deck, with room to spare below for dozens of Wilcats, Hellcats, Avengers, Dauntlesses and later, Helldivers). Art
-
While Britain's Royal Navy and the Imperial Japanese Navy built their carriers with steel flight decks, the US Navy specified flight decks built from fairly massive pine timbers from USS Lexington & USS Saratoga (commissioned in 1927) to USS Ranger (commissioned in 1938), to the legendary four prewar fleet carriers (Yorktown, Hornet, Wasp and Enterprise), the large class of Essex Class carriers, Independence Class light carriers, and the nearly 100 Escort or "Jeep" carriers. The reason was two-fold: First, the use of wood for the flight deck surface was lighter in weight than a similar-sized flight deck made of steel would have been (also, steel flight decks could not be of a thickness adequate to provide serious armor protection and still be high enough above the hangar deck for maximum storage space for a large number of aircraft), and were much more readily repairable from battle damage (USS Yorktown took an aerial bomb at Midway) and was back conducting flight operations within hours--witness what happened to the Japanese carriers in that battle--all were reduced to sinking condition from aerial attack, there flight decks damaged irreparably at sea--had they survived, they all would have limped back to shipyards in Japan for months of repairs. Second, the lighter weight of the wood flight deck surface allowed for tremendously better armor protection against aerial attack from dive bombers--Essex Class carriers had a 3" thick steel flight deck, serving as a "splinter deck" which could trigger the fuse on any bomb dropped from above; and a much heavier (5" thick I seem to remember) deck just below the flight deck which could stop virtually any aerial bomb in the Japanese naval inventory (No US Fleet carrier was sunk solely due to aerial bombs--USS Yorktown was sunk by a Japanese submarine, Wasp, Hornet, and Lexington were sunk by damage caused by fires that raged out of control due to aerial bombing and by a lack of understanding at the time of their construction as to how to prevent such from happening. The second USS Hornet is a museum ship today (the carrier that picked up all the Apollo astronauts upon their return to earth and splashdown in the Pacific), moored at Alameda CA. Hornet still has her wooden flight deck (even though she was seriously upgraded for the jet age), but that is covered with a steel surface, itself coated with a very abrasive high traction surface (you can see the outline of most of the planking timbers as the steel deck plating was pressed into the wood by thousands of jet aircraft over her nearly 25 yrs of launching and recovering jet fighters). In contrast, USS Forrestal (the first of the modern Supercarriers, launched about 1954) was built with a steel deck. In a severe flight deck fire off Vietnam in the late 1968's, that flight deck was holed by several aerial bombs cooking off, necessitating a return stateside for extensive repairs, effectively ending Forrestal's combat career. Imagine the effect something like that would have had on operations in the Pacific against the Japanese Navy in WW-II! Art
-
needed - R & D Unique Compressor photo
Art Anderson replied to southpier's topic in General Automotive Talk (Trucks and Cars)
Art -
I've used RenShape 440 since 1995, when Chris Etzel (then of Etzel's Speed Classics) introduced me to it. 440 carves beautifully, sands, files, drills just as nicely. it does have a certain "graininess", but any good lacquer primer will seal and fill the surface; once sanded it is smooth as any styrene. I've run a bit of the stuff through my Sherline mill, and it works very well there. Milling chips do come off, just as one would expect, but it's not particularly dusty, and a quick vacuuming with my hand vac--end of problem. Both epoxies and CA glues work very well with the stuff as well. Art
-
Aaron, I plead guilty to using a "cheap dryer vent", but you know what? My Pace still pulls ALL fumes out of the model room--in fact, i spilled most of a bottle of Aero Gloss Dope thinner the other day, the Pace kept the fumes from that from going beyond the model room, in fact, within minutes, I could no longer smell the stuff, and even better, neither of my neighbors downstairs ever had any indication that I had a problem. Sometimes, methinks that all the "engineering data" is a bit irrelevant, in addition to being rather severely misleading. I come from the old school I guess: If it don't fit, get a bigger hammer" (Mickey Thompson) Art
-
I too have made valve stems for model car wheels. Nick's tutorial is right on target, frankly. Modern valve stems most generally are in the 1.5" range, which means that less than that will be exposed to the eye when tires are installed. However, in my experience, there are wheels, there are tires, and it's wise to consider some of the differences: For example, someone building a model of a car produced prior to the universal adoption of tubeless tires, the valve stem is part of the innertube, not a bolted in device, which meant the valve stems on those older cars was longer; in order to clear not only the steel rims through which they extended, but also to allow for the installation of first "beauty rings" but also full wheel covers. With both of these, longer valve stems were a necessity, in order for them to extend far enough through the added wheel trim to allow for an air chuck sufficient room to seat down tightly on the valve stem. For cars of the era up to about 1930, valve stems were even longer, and thicker in diameter as well. For these reasons, I prefer using K&S brass rod for valve stems. For modern cars, when I've installed this detail, .020" gets the call. OK, so that translates to 1/2 inch, but sometimes I think that the "illusion of scale" is more important than being "exact". For those old-time metal valve stems with their long caps, such as were used almost universally from the beginnings of pneumatic tires to circa 1930, 1/16" brass rod gets my call. But still, Nick's technique is right on target IMO, and pretty much so are the rest of the comments in this thread. Art
-
All the excellent explanatory "engineering" information notwithstanding, frankly, my Pace Peacemaker does an EXCELLENT job of removing the paint particulates (overspray) and the solvent fumes from my model room, to the outside (well, particulates wind up captured in the filter). If we were talking 1:1 scale production spray guns, no way would the Pace, or any other modeler's spray booth system remove all the overspray, but we don't use production spray guns; rather airbrushes (which generally use less paint than a woman might use fingernail polish on all 20 fingers and toes--or at worst, a rattle can. And for that small volume of paint we modelers might use in any one sitting, Pace, or similar spray booths work just fine. How do I know this? This house has central heat and AC, for three apartments. Now, the neighbor lady downstairs will complain of the smell should a housefly pass gas anywhere near her--she's yet to even notice that I paint stuff upstairs here, and guess where there is a major cold air (winter)/warm air return? In the hallway right outside the room I have dedicated to model car building. Art
-
Of course, Tim Flock drove Hudsons in 1953 as well, but this version is a lot more colorful!
-
What John said! You want to use your shop vac for exhaust? Well, I don't know about your's, but I have a Shop Vac brand wet/dry vacuum at work, which has a bright orange warning label on it--warning the user to NOT use it for picking up any sort of flammable liquids or vapors! This is because such vacuums have electric motors having a commutator and brushes, which are open to the surrounding air, and use the air flowing through the unit to cool the motor (whatever air goes through it flows "over, under, around and through" the motor--perfect for an explosion which if it doesn't injure or kill you, can certainly spoil your day, by burning down your house around you0. That said, a properly designed small spray booth is not that expensive. I, like "Mr Can Am Garage" have a Pace Peacemaker spray booth. This has a sealed motor attached to a high efficiency "squirrel cage" blower, which puts that sealed motor COMPLETELY outside the air stream flowing though the blower--in other words, EXPLOSION PROOF. In addition, this unit uses a commonly available high-efficiency HVAC filter (replacements are available at home improvement stores, lumberyards, even WalMart) for not a lot of coin; and in the bargain, the unit is literally whisper-quiet. These are set up to use an ordinary dryer hose and vent to duct the vapors from the paint being used outdoors. OK, so you don't want to cut a hole in the side of the house? I made a "plug" for the sash window in my model room from a commonly available high-density particle board shelf that I cut to fit snugly between the sides of the window frame, the sash being raised, plug put in place, sash lowered to hold it in place. You will need a 4.25" hole saw for your electric drill (cheaper if you know someone who already has such a hole cutter, and a dryer vent and hose kit (mine cost me all of $7.99 at Menard's!). All this is a one time purchase--such a spray booth should last you DECADES, so the longer you have and use it, the less money per day/week/month/year it will have cost you to own. But more importantly, it is there to protect not only your environment (no overspray paint dust everywhere--nor any smell either), but also your health and safety. Think about it pretty seriously. Here's the link http://www.pacepaintbooths.com/pace/ Art
-
Mark, all the requisite parts for all planned versions have been tooled--they are in the test shots I have here. Sooooo.........Model King's Nascar project shouldn't take very long! Art
-
FWIW, Sean Svendsen posted these pics on Spotlight Hobbies Message board yesterday afternoon. It's the box art model for the upcoming Model King '52 Hudson driven by Tim Flock. Link: http://wwwboard.spotlighthobbies.com/index.pl?read=1685104 Art
-
BOOTH.
-
Having FUN painting the first of my Hudsons, black with cream colored roof and lower body side panels. BTW, this is the first model car body I have painted since 2004, when I lost my job as product development specialist for Johnny Lightning, after RC2 bought out Playing Mantis (moved back here to Lafayette, had no room for a spray booth--corrected now with a much larger apartment, and a new Pace Peacemaker booth!). Still as much fun as it ever was! Art
-
Scale caculater?
Art Anderson replied to ewaskew's topic in General Automotive Talk (Trucks and Cars)
EXACTLY! Or, if you are uncomfortable trying to use metric, just think .040" equals one inch in 1/25 scale. Art -
question about car model building
Art Anderson replied to allecb's topic in General Automotive Talk (Trucks and Cars)
Ditto to all the above. I have preassembled body panels whenever the actual car either had no seams in the area (1962-63 Ferarri 250 GTO comes to mind here), but certainly not limited to that. I've done this with more than one Corvette over time, which while having noticeable body seams for the front and rear "caps", the kits in question had severe misalignment problems. This does take some advance planning, however: Often times, when this sort of thing gets done on my workbench, there are issues regarding installing a chassis into the body without cracking or breaking the added on lower body panels--but that's just it--PLAN ahead. Why do model companies have to do body shells this way, you might ask? Well, simply "engineering". If there are severe "undercuts" at the ends of a body shell, it often is simply impossible to mold that body shell all in one piece without the body shell breaking under demolding, or at least suffering from cracking of the solidified plastic. Along with this, almost any model car kit is designed to the "lowest common denominator", meaning that it needs to be buildable by modelers of all levels of skills--so making assembly simpler for the greatest number of consumers is a key issue. But that does not mean that a particular builder cannot "bypass" all this, to achieve the results he/she wants to accomplish. Therefore, a lot of us move beyond the instruction sheets, step out of the box, build it up in a sequence that makes sense to each of us, in our own way. Art -
32 ford commercial grill
Art Anderson replied to Frank's topic in Truck Aftermarket / Resin / 3D Printed
Essentially, a '32 Ford Commercial" (trucks and station wagons) grille shell is the same as the '34, except that where the '33-'34 grilles are slanted backwards a few degrees, the '32 is straight up and down, perfectly vertical. This isn't a hard thing to correct, just a bit of filing and sanding of the top of the shell to mate it up to a '32 Ford hood is all it takes. Art -
So, when it comes to the fine arts, I plead guilty to being a mere layperson. OK?
-
Skip, the build from Dave Metzner's pics is truthfully the final round test shot of the kit, lacking only a tiny bit of engraving in the headlight lenses, which will happen before mass production. The test shot parts ARE the same as those in the production kits will be; it's no prototype. If one were to see the first issue boxart builtups of completely newly tooled model car kits from any manufacturers using photo's of the model in the boxtop--almost invariably, those were built up from test shots, no special advanced skills needed. Done from last round test shots for one very simple reason: The short lead time between when those test shots are ready for such assembly, and the production and packaging of the kit itself for shipment to the customer. Art
-
Actually, the Nascar stocker has been a part of the Hudson tooling from day one, before Model King got involved. Same with the upcoming Chrysler C-300. Art
-
With all due respect, Double D, in terms of model car kit product development, and the issues that have to be resolved therein, unless you are involved within the model kit industry, you are a layperson--that term merely indicates that you aren't involved in the industry--it's NOT a derogatory comment in any way, and I would have thought you would have taken it that way, but I guess I was badly mistaken. All I tried to do was to give a look at some of these issues from the point of view of being "on the inside looking out", sorry if I appeared to mislead you. As for "God" I acknowledge that there is just one of HIM, and he sure as heck ain't me. Art
-
Harry et.al., For starters, please consider that any model car kit (with the glaring exception of Accurate Miniatures' colossal commercial failures in this area), done in styrene, is or has been, tooled with a very broad market in mind. By this I mean that in order to be commercially successful, any plastic model car kit necessarily has to be designed, tooled, and molded to entice modelers of all skill levels, or at least those whose skills and model building "confidence" are above that of simple snap-fit kit assembly. I would submit, based on my now 59 years as a model builder, 29 years in retail hobby shops (full time, part time, owner of my own store 1984-92), 6 yrs building boxart and presentation models for AMT Corporation, 3 years developing diecast miniatures and so forth), that the vast majority of model car enthusiasts are very much "kit assemblers", the absolute scale fanatics/superdetailers/scratchbuilders being a small minority here (and I am NOT denigrating any segment of the model car building community here, just calling things as I have seen them for all but 8 yrs of my existence on this planet!). Some things about how a model car might be engineered for its assembly can be traced to structural integrity of the finished model, others may well have to be compromised for rapid mass-production (and injection molding of plastic parts for model kits is rapid in its cycling, both in the molding department as well as on the kit packing assembly line). Other things happen due to the limitations of molding styrene plastic in steel dies. Someone keeps mentioning, or at least alluding to the existence of a pretty thin locating "post" for mounting the rear axle onto the Hudson chassis. Well, considering that the rear leaf springs are "underslung" below the axle, this is a consideration. For the more average builder, using either tube glue (or whatever!) having the axle break loose from its perch somewhere AFTER this assembly stage has occurred could well be enough to make that "victim" shy away from this or any similar kit in the future--and frankly, I cannot believe that any model company would want that to happen. Now, for the more discriminating, more experienced (or daring, if you will) builder, the clipping off of this thin mounting post (which BTW, once the chassis is painted and assembled, is practically invisible to the vast majority of those who would look at the model upside down) should take no more than about 5-seconds per side to achieve--that's one of those little things that separate a model car BUILDER from that status as a "kit assembler". The same thing comes to mind when I consider another criticism, that being the oblong "tab" used to locate the Hudson Hornet "Rocket" emblem on the trunk lid: That assembly concept assures that this "Rocket" installs at the correct angle on the rotund, bulbous "Rubenesque" (look up Ruben, the 19th Century painter of very amply filled out women, "fat ladies" if you will!) trunk lid. I suspect this criticism comes from the idea that someone wishing to nose and deck this car might just have to fill that slot--to which I say, "Big Whoop!"--that is something easily accomplished by any model car builder with any of the various techniques that have been, are, and will continue to be, addressed on this very set of forums. Again, the difference between those who are still at the "kit assembler" stage (nothing wrong with that, BTW, we all started there, and many are quite happy to stay at that level--it's still FUN for them, and that should not be a deterrent for those who've taken their interpretation of this great hobby to that next level). Someone else has expressed a fear that the windshield might be too thick, with a "halo" surrounding it. The concept used here is that Moebius wanted the glass to be far more nearly flush with the outside of the car than is the norm for model car kits, all the while having very positive locating design, hence a slight, thin flange around the inside edge of the "glass" in order to achieve this. A more competent, perhaps slightly adventurous "model car builder" might step beyond the level of "kit assembler", and carefully trim away this flange, and guess what? The windshield glass will still locate in the opening, given that the center "divider" post used on most all cars until 1951-53 is a part of the body shell, not something simply tooled into the glass, as has been the case with far too many model kits of cars of those years. And, the fit is pretty precise in the bargain. As for the immediate subject of this part of the thread, those nasty hood props: For starters, the notion of adding hood hinges and the spring-loaded "scissors" props for both sides of the hood was something that we came up with upon looking at the first tooling mockup. Why not give builders the option of being able to display the car with the hood open, but without the usual heavy tabs into slots in the firewall, as most model companies have done this sort of thing (I've never seen that sort of tab and slot arrangement on any real Detroit car, have you?), and having the perfect option of providing factory hood props instead of expecting modelers to use toothpics, pieces of wire, or a straightened out paper clip to support the hood in the open position (have not most all of us seen that on a contest table?) or worse yet, simply having to lay the hood on a table or shelf next to the model (now how prototypical is that, outside say, a fiberglass or carbon fiber hood from a race car, hmmmm?). Even with this concept, it's not quite possible to mold those prop units even close to scale thickness--the originals were between 1/8 and 3/16 inches thick, rolled into a slight hat-section for stability (I had to remove one, along with a hood hinge, from Dad's '54 Hornet, take them to a local welding shop for repair, then reinstalled them -- AFTER taking the hood itself off, and then bolting it back on--now YOU try hefting a sheet metal structure weighing over 50-lbs at the age of 16, weighing yourself perhaps 95lbs soaking wet after a full meal--not easy!). To make those two struts even close to scale thickness would have meant their coming out somewhere between .005" and .0075" thick, which dimension in scale would equal that actual 1/8 to 3/16 inch thickness. To mold those, as has been done, with but one sprue attachment allowing for plastic flow (there are no ejection pin marks on this part, no other injection points for the molten styrene either) in scale thickness would have meant two problems--either "short shot" parts (where the plastic failed to fill the mold cavity), or considerable warping or even breakage of the parts in question anywhere from the packaging line, to shipping, to handling by the end user--again something that would be counter productive, period. For those who want that more correct, scale thickness part in an area such as this--it would surprise me if no photoetch aftermarket producer came up with those struts in metal. But, for someone in an official capacity with the magazine whose forum this is to make some rather blanket criticisms, particularly if that person has (to my knowledge anyway) never participated in any way in the design and development of any model kit--simply begs all reason. I should think that anyone in such a position with a model magazine would be far better served (and increase his or her credibility among readers) to ask a few questions off the board, do a bit of research before making any bald, blanket statements. Of course, I would not expect those who are laypersons in a situation such as this to do that, after all that is one of the definitions of "layperson" that being one who's not a professional in the area under discussion, not someone even indirectly involved in the process of developing a model kit. But perhaps my hopes are a bit too high--"SIGH!" Art