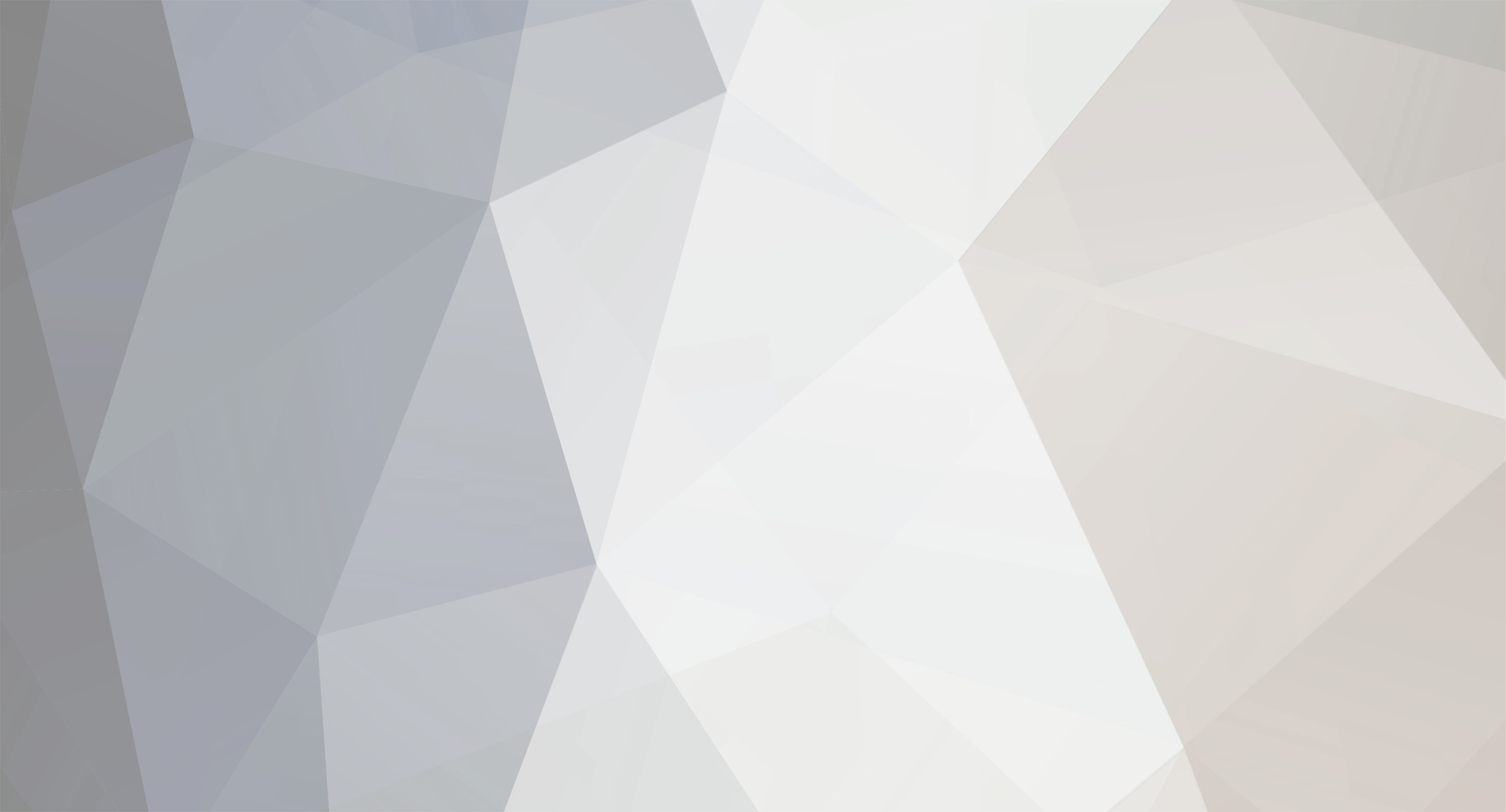
Art Anderson
Members-
Posts
5,052 -
Joined
-
Last visited
Content Type
Profiles
Forums
Events
Gallery
Everything posted by Art Anderson
-
There's an old saying that goes like this: Too many of us fail to plan, which leads us to planning to fail--and that is just as true with a model car as it is with life. With any model project, planning should be a key, and early step in the process--be that model "Out Of The Box" or a fully detailed major conversion or even a scratchbuilt project. Many of the problems I've seen addressed in this thread are very directly related to planning how the work needs to be done to overcome the inevitable shortcomings any builder will find in any model kit he/she attempts--it's been a part of the game since time immemorial, and likely will remain so even after we all assume room temperature. Treat each part of a model project as if it were a scale model in its own right--that's how most top-level builders do it. BUT, along the way, keep in mind that each component, each subassembly will have to relate to the rest of the project, otherwise unnecessary compromises wind up creeping in, compromises that could have been avoided with this sort of "planning". If you need an alternator or generator bracket, think about that for a bit--how can this be achieved, and still give at least the illusion of realism? It may actually be easier than you think! this is the chassis of a factory stock '27 Model T Tudor Sedan that I built 10 years ago. This model took a full 6 1/2 months to build, start to finish--started it on New Year's Day, finished it on July 15. What you see in this pic is the detailed chassis, with the rough engine set in for test fitting. Those running board brackets? They were done using the fender/running board assembly test-fitted to the frame, to ensure that the bracketry truly fit to both frame AND to the bottom sides of the running boards. What I did not do were the similar front fender brackets, which if I were to do this project again, would definitely be there. In addition, you can see the mechanical parking brake lever I scratchbuilt, installed in the chassis, which required test fitting the floorboard frequently to ensure that I could drop the assembled body onto the car once painted and trimmed without any trouble. The chassis, painted and ready to accept the fenders and body. In this step, the test fitted engine shown in the first pic above was fully detailed, THEN assembled permanently in the chassis. Finally, this is the finished chassis assembled with the completed body and fenders--the result of all the planning that was done at the very beginning of the project. Every part, every subassembly came together as I envisioned it, again by planning up front, and all along the way: The same sort of planning had to happen with using the Revell Li'l John Buttera '26 T Tudor Sedan/Sedan Delivery body with the fender/running board and radiator units from the AMT '27 T Touring car. In this case, the Revell body's cowling was too low to mate up properly to the AMT hood--due to Revell's not tooling in the "hood shelves", which on the real car are wooden blocks atop the front fender sheet metal where the fenders bolt to the frame--something I knew immediately, given my study of Model T Fords over the years (another important step here that all too many modelers forget--RESEARCH! You can never have too much reference material, take too many photographs, do too much research!) Once the cowling shape was corrected, it all came together "If it fits, you must convict" style: Unfortunately, I don't have any pics of what was done on the interior of the body, but one major goal of this project was to negate something I was told at an IPMS Convention about 35 years ago: "Model car builders always leave the edges of that overly thick "glass" showing inside the roof of the cars they build" or words to that effect. So one goal on this one was to eliminate that "bone of contention", by using clear plastic as close to scale thickness as I could get away with. Here's where the "illusion" of scale reality comes into play. Real plate glass as used on a Model T Ford was about 1/4" thick, which would have meant using .010" thick clear plastic--but that thickness tends to come out wavy, unrealistic, so .020" thick PET-G plastic was used. The driver's side window is depicted halfway rolled down, so the edge shows, but nobody has ever commented that the glass is a scale half inch thick--so the "illusion of realism" seems to have worked. In final assembly, making the chassis AND engine relate to the rest of the project was key--test-fitting, tweaking of the upper radiator hose (the lower hose had to be added, AMT never had that detail in their kit!) to make it mate up to the top tank of the radiator took a bit of fiddling, and then there was the matter of adding on the fuel outlet and sediment bulb, which was scratchbuilt, then connected to the float bowl of the carburetor. Unfortunately, I had a "failure to plan" event with the essential bell cranks and pull rods for spark advance (connecting to the "timer" or distributor at the front of the engine) and the throttle rods and bell cranks, both systems connecting to the sides of the steering column just in front of the firewall. Also, I didn't think to either thin down the thickness of the kit hood, or add the anti-rattle webbing around the lip of the firewall and radiator shell, but again, nobody but me (probably) ever noticed that, certainly no one ever commented on the lack of these details--but still, those were my failure to plan ahead for them, But, with all the planning, and even with a couple of failures to plan, the end result: The car has been shown numerous times, won Best Factory Stock at Goodguys Berrien Springs MI in 2002, Goshen IN (First place), Indianapolis IN (first place), Classic Plastic in MA, 2nd place award). It's now retired, only comes out for a couple of club displays a year. Does it have flaws? Yes it does--I know where they are, even if nobody else either notices or comments on them. But, have I learned from those mistakes? Yes you bet your bippy I have learned, and hopefully will avoid those in future projects. One of the mistakes that I think many of us make in modeling is to fail to notice our mistakes, our miscues, little things that could have been done but were overlooked. Nothing wrong with self-criticism--it's one of the ways we can grow as model builders, regardless of our age. Art
-
Those "raised edges" around otherwise recessed panel lines (doors, trunk lids) are actually in the tooling all too often. It's a result of the engraving process--just to correct this misunderstanding. That said, you are very correct that some block sanding of the body shell is often required to get rid of those imperfections. The same is true of those bothersome "sink marks" which happen where the plastic is thickened on the back or inside of say, a body shell, particularly on older kits which were engineered and tooled in a much earlier era, for use with harder grades of polystyrene than is used in today's model kit industry. Those need to be filled and smoothed out as well. Art
-
Another Bentley Question
Art Anderson replied to Harry P.'s topic in General Automotive Talk (Trucks and Cars)
Harry, On most any car with mechanical brakes, the pedal (or for that matter, a hand brake lever as well) has a short pull rod that runs to a cross-shaft BEHIND the brake pedal itself, which in turn has bellcranks at its outer ends which pull on the brake rods which in turn pull on individual bellcranks at each wheel having a brake. Why so, you ask? Why not just connect the brake pedal directly to each brake rod--skip the pull rod? Simple answer really: The foot pedals of any car with the engine in front, mounted longitudally (fore and aft) for rear drive, are right alongside the bell housing, and in order to have some sort of cross shaft in that place would mean its having to be formed around the bell housing, which would make it flex even more than a straight (or nearly straight) one would; and in fact, mechanical brake cross shafts do "twist" a little bit under hard braking, which does make mechanical brakes very difficult to set up properly for equal braking side-side (anyone who's ever worked on a Model A Ford (or for that matter, any Ford with mechanical brakes from 1928-38) knows what I am talking about here. As for hydraulic brakes, even though Lockheed developed the first hydraulic brake system in 1919-20 with Duesenberg becoming the first carmaker to offer them in 1921, acceptance was anything but rapid. The first major carmaker to offer hydraulics was Chrysler, beginning in 1924, but the rest of the industry took another 10-15 years to adopt them. There was a lot of distrust in the marketplace for years of anything hydraulic, squirting a fluid through flexible hoses was something adults of that era had a hard time getting their heads around the concept. Art -
Weigted Dremel Bits help
Art Anderson replied to MoparWoman Jamie's topic in General Automotive Talk (Trucks and Cars)
That is what is called in the trade as a "center drill" (I have a bunch of them here, used with my Sherline Mill) Center drills are meant to be used in drill presses (or as with me, I use my Sherline Mill as a drill press--witness the 550 holes I drilled in the aluminum cylinder for the cooling pins!). They are carbide, which is quite brittle, and if used in a pin vise, or in a hand-held power unit such as a Dremel tool, will break almost instantly, as carbide doesn't flex very far before it shatters. The colored collars on the ones that come in sets from Harbor Freight are there for diameter ID, makes it easy to remember what size the drill is, not a weight. Art -
1930s metallic paints
Art Anderson replied to sjordan2's topic in General Automotive Talk (Trucks and Cars)
While the color palette available to coachbuilders of the "Classic Era" was virtually unlimited (Brewster Body Company of Springfield MA --the Monogram '31 Rolls Royce Roadster and Sport Touring cars are models of Springfield MA Rolls Royces, with Brewster bodies--had literally several hundred different shades of their "Brewster Green" and "Brewster Maroon", each custom-mixed for a particular customer!), the colors seen on those cars when new depended almost entirely on who bought the car, and where they lived. The "Old Money" clientele in cities such as New York, Philadelphia, Baltimore, Washington, Boston and even Chicago or Detroit tended to be very conservative--they wanted the quality, but not the flashy appearance. On the West Coast, particularly Los Angeles, and certainly in Miami Beach FL, almost the opposite was true--bright, often almost gawdy colors were evidence of the conspicuous consumption of newly rich socialites, movie stars and the like. In addition, a lot depended on the body style--formal sedans, town cars, limousines were almost always dark and conservative (the 1931 Murphy-bodied Duesenberg Beverly was painted in 4 tones of rather bright green for its Auto Salon showings, the 1933 Duesenberg SJ Arlington--AKA "20-Grand", the Pierce Silver Arrow were painted in bright metallic silver, the Silver Arrow being accented with metallic gunmetal with red pinstriping outlining the darker trim color), with a highly visible almost rebellion in the form of Mrs Ethel Mars (of the Mars Candy Company, flush with the profits of the highly popular Snickers candy bar) who had Bohmann & Schwartz of Hollywood create a swoopy, ultramodern town car for her, painted entirely in metallic silver (even her chauffeur wore a metallic silver uniform!), but those were exceptions. Actor Gary Cooper drove a 1931 Duesenberg Model J Tourster, bodied by Derham out of Philadelphia, painted a bright green with bright yellow fenders and splash aprons (the Tourster was a dual windshield phaeton), and Clark Gable owned a bright white Rollston Dusenberg SJN convertible coupe. Actress and arguably the top of the A list Joan Crawford had her 1933 Cadillac V16 Fleetwood Town Car painted white--she'd have been the talk of all the gossips in the New York City 400, but her car stayed in and around Los Angeles. Mass production cars sort of followed this same pattern: While Ford, Chevrolet and others offered bright colors from about 1928 onward, particularly on roadsters, most of those got sold either in the sun belt or out on the West Coast. In any event, however, pigments used in automotive paints back then were anything but stable--about the only color that would not fade in the sun was black, carbon black being the principle black pigment back then. It wasn't until the early 1980's that UV-blocking carriers were available for general use. So, with that in mind, the more somber, darker colors tended to be the most popular across the board. Art -
1930s metallic paints
Art Anderson replied to sjordan2's topic in General Automotive Talk (Trucks and Cars)
From Wikipedia: <<<Zinc chromate, ZnCrO4, is a chemical compound containing the chromate anion, appearing as odorless yellow solid powder.[2][3][4]It is used industrially in chromate conversion coatings, having been developed by Ford Motor Company in 1920s>>> Aluminum powder was added to "aircraft dope" (actually, the same nitrocelluse lacquer I referred to above) used on fabric aircraft covering to "shrink" the linen up taut to cover the airfoil shape of wings, and make fuselages more aerodynamic; in order to protect not only the dope, but also the underlying fabric from UV rays of the sun. Keep in mind that not until the late 1930's did any navy's seagoing aircraft have all metal skins, wings and tail surfaces were still fabric covered. This was very much standard aircraft technology for military aircraft worldwide until the advent of such planes as the Curtiss P-36 Hawk and the Seversky P-35 in the mid-1930's, along with the Boeing B-9 and Martin B-10 bombers (I was just looking at the USAF Museum's Martin B-10B a little more than a week ago). Another reason for silver (aluminum bearing metallic finish) dope on military aircraft in the "inter-war" years of the 1920's and 30's was simply "flash and dash"--it was bright, captured the public's attention particularly when freshly applied. In US practice however, the Army Air Corps didnt use silver dope on planes at all during those years--most standard was olive drab dope on fabric covered fuselages, with insignia yellow dope on wings and tail surfaces. The US Navy used silver dope on fuselages pretty much, with insignia yellow dope on fabric flying surfaces. Of course, US military trainers used first a blue and yellow paint scheme, followed by all yellow, and finally all silver (but sometimes with yellow wings. Zinc Chromate, on the other hand came into wide use as an anti-corrosion primer used in all steps of metal aircraft construction almost simultaneously across the world, with the exception of Japanese military aircraft, which were primed on inside and hidden surfaces with clear lacquer that was often tinted either green or blue. But back to cars: While of course, metallic lacquers were available by the late 1920's, they tended for the most part to be dark colors, blues, greens, maroon, only occasionally silver, and were seldom every as "sparkly" as what is often seen today--the "bronzing powder" (paint industry term for metallic powders used to make metallic paints) of that era were much more finely ground than what is seen today, even those colors used in the 1950's and 1960's on American production cars. Luxury car makers, particularly Mercedes-Benz and BMW used that very finely ground bronzing powder in their metallic lacquers well into the 1970's. Art -
1930s metallic paints
Art Anderson replied to sjordan2's topic in General Automotive Talk (Trucks and Cars)
DuPont pioneered metallic lacquer for spraying in 1927--one of the very first cars to be painted with it was the 1928 Miller 91 driven by Louis Meyer (later of Meyer-Drake, manufacturer of the legendary Offenhauser engines). His car was painted gold, which was made by mixing finely ground brass powder in clear nitrocellulose lacquer. The problem with nitrate lacquer and metallic powder was that this early form of lacquer had very little resistance to UV light, even rain--and it wore away rather quickly. With metallics, that exposed the metallic powders, which then dulled, in addition to creating a rough surface, that no amount of polishing could repair. For that reason, metallic paints, although available pretty much all through the 30's to the 50's, were not all that popular, especially with older car buyers who just could not stand the idea of a repaint after a couple of years. Pearlescent paints have been around since at least the earlyy 1910's--but were difficult to paint, as all car painting in that era (save for Ford and their black japan enamel) was done by hand, with lots of rubbing and polishing afterward. I've seen a few "survivor" cars from that era that had pearlescent accents hand painted on their bodies--the effect must have been stunning when new. While early pearl paints were created using ground fish scale, even powdered mussel shells (mussels are "fresh water oysters", found in most of the rivers of the midwest and south--their shells used mostly for buttons for dress clothes for men and women years ago); it wasn't until the use of powdered mica that pearlescent colors became practical and popular. Art -
Question for the resin casters.....
Art Anderson replied to roadhawg's topic in Car Aftermarket / Resin / 3D Printed
Sulfur is deadly to resin--will keep it from hardening almost permanently, so any clay used must be sulfur-free. For years, I used nothing but AMACO (American Art Clay Company) X-11 moist pottery clay, which is gray in color, is a natural clay, softened with water. One HUGE advantage of this stuff is that any residues can be washed out of a master and mold before making a second pour of rubber for the second part of a 2-part mold. Art -
All original 1911 Mercer race car (not a raceabout, this was used strictly for racing on the east coast), found in a warehouse in this condition in Elizabeth NJ, photographed right behind the Tower Terrace Grandstand South at Indianapolis Motor Speedway during the Concours d'Elegance on May 14: Love the original patina! Art
-
1930 Bentley question
Art Anderson replied to Harry P.'s topic in General Automotive Talk (Trucks and Cars)
The two identical items at the bottom of the instrument panel appear to me to be oil level indicators--given the glass bulbs inverted, and the U-shaped tubes in them, tapered to nozzles, they just about have to be something to do with engine oil, I think. Art -
Lafayette IN here. Art
-
RESIN PRODUCT DIFFICULTIES
Art Anderson replied to Drake69's topic in Car Aftermarket / Resin / 3D Printed
With resin cast parts, bear in mind that regardless of the size of the manufacturer, or his line of products--it's a very labor-intensive process, and delays almost always happen. Even the best casters, such as Time Machine, Modelhaus, Motor City etc. experience this, and most always, they will quote you a lead time of 4-6 weeks from the time they recieve the order. Resin casting is not something where the maker simply punches a button and out comes the product. It's all hand work, all manually operated, and there is no way around that. Art -
What is the best putty
Art Anderson replied to car lover 1996's topic in General Automotive Talk (Trucks and Cars)
Brands of catalyzed putties are like brands of bread--everybody seems to have one! Seriously though--all catalyzed putties as used in the autobody trade that I have ever seen are polyester putty, which in itself is polyester resin with a filler added, the finer the grade of putty, the finer grind the filler material is. In short, in my experience--if you find spot-and-glaze catalyzed putty, it really matters very little the brand--chances are that in any event, many of these brands come out of the same holding tanks--just packaged in whatever label you see on the shelf. But in any event, as Harry P wrote--all one-part (evaporative solvent-based putties shrink upon drying--they have to, as a portion of their "bulk" is provided by the solvents that evaporate. And my experience with Squadron Green Putty has never been satisfactory--that stuff is what was known in the Autobody Trade 50 years ago as "Green Stuff", and it was simply not worth the powder and shot to blow it to kingdom come, IMO. Art -
Continuation kits
Art Anderson replied to Greg Myers's topic in General Automotive Talk (Trucks and Cars)
A '57 Chrysler New Yorker would require the tooling of a new grille and hood (the 300C trapezoidal grille and corresponding fiberglas hood were unique to the 300. Also, all the body side chrome trim on the New Yorker is very different from that on the 300. A single quad carb on the engine would also better fit what was pretty much standard Chrysler practice for the 392 Hemi in most regular production cars. Also, new wheel covers would be needed, those hubcaps in the 300C kit are unique to the 300. For a stock '32 Ford, the kit would require an all new frame, as the street rod frame lacks a stock rear crossmember, the center K-member, and a correct front crossmember. In addition, a stock front and rear axle would be needed, along with stock springs at both ends, along with stock 5:25-18 wire wheels with corresponding Firestone tires, and hubcaps to match. On the chrome tree, a stock headlight bar would be needed, with the V8 emblem for the middle of it. A stock firewall would have to be created for the body (could be the same for all the body shells, they were on the real cars), and of course, a complete stock interior for whichever body style was used for a stock kit. Art -
Continuation kits
Art Anderson replied to Greg Myers's topic in General Automotive Talk (Trucks and Cars)
Revell, if you are reading this: Your '32 Ford street rod series would make a perfect platform for any of the following (not necessarily in order of importance)! B400 Convertible Sedan Phaeton Woodie station wagon Roadster and closed cab pickups 1/2 ton panel delivery Sport Coupe Cabriolet Fordor sedan As for the sedan delivery, Ford built no sedan deliveries themselves in 1932 (only slightly over 250,000 Model B/Model 18--the V8 cars) were built worldwide that depths-of-The Great-Depression-year, and very low demand for a sedan delivery. What few (less than 200) sedan deliveries that were produced were conversions done on orders from Ford (when a dealer would order one) by the LeBaron custom body division of Briggs Body Company, who built many of the higher-end bodies for Fords back in those years. The conversion was very simple: Blank off the rear quarter windows of a Tudor Sedan with sheet steel welded in place on the inside of the body sides, then lead the seams in; cut out a door in the rear of the body, add the door jamb, add framing around the panel removed in this process, add hinges and a door handle and lock (this door opened from the right side for curbside deliveries), build a level cargo floor inside to level out the floor atop the kickup at the rear of the frame, add some wood framing on the insides of the body sides for keeping cargo from battering into the sheet metal, and that was it. The front seats from the the Tudor sedan were retained, as those were perfect for a sedan delivery, both seats folding down, the passenger side seat also folding forward against the dashboard for easy access to the rear area. Art -
32 Ford BB chassis
Art Anderson replied to Frank's topic in General Automotive Talk (Trucks and Cars)
The '32-'37 Ford BB truck is, of course, a 1.5 ton rated truck (considered "heavy duty" by Ford, Chevrolet/GMC, Dodge, Studebaker in the early 30's). It's a "ladder style" frame, having straight crossmembers unlike Ford 1932-48 passenger cars, which used at first a K-Member at the transmission mounting (1932) and then an X-member thereafter for torsional stiffness. The BB frame is almost identical to the 1930-31 AA truck frame, differing only in the thickness of the steel used, and having a 1" or so deeper side rail design. This is a '31 Model AA truck chassis: The AA chassis pictured is virtually the same as the BB as I noted above, with the exception of the rear suspension layout: The AA truck chassis pictured has parallel leaf springs at the rear, with the semi-elliptic springs mounted "upside down", bolted in their center to the side of the frame rail, the front of the spring shackled to the frame, the rear end of the spring shackled to the top of the rear axle, cantilever-style. This was an inherent weakness in the design, when one considers that for practical purposes, nearly all the weight of cargo was carried by the rear axle (55% forward, 45% rearward of the rear axle centerline), making the breaking of a rear spring an all-too-frequent problem. For the BB, the rear leaf springs were reversed, mounted in the same manner as they would be on a passenger car, the ends of the main spring leaf shackled to the chassis, the center of the spring bolted solidly to the top of the rear axle--which is standard practice to this day on heavy truck leaf springs. The front axle is the same design as Ford passenger cars, but was a steel forging (as were Ford "beam" front axles through 1948), but was about 25% heavier than the passenger car axle (you can use a passenger car axle on the model, most model kit Ford front axles are molded neavier than scale for strength). The front spring is transverse, just as on the AA truck chassis pictured, but was made of wider, thicker spring leaves, and had 4-more leaves in it than on the passenger car. The mechanical brake drums are much heavier as well, with cooling ribs around their circumference. The rear axle was much larger than the passenger car unit, and was a full-floating design (meaning that the axle housings carried the full weight and forces exerted of the axle shafts and the differential gear system (Ford passenger car rear axles from 1928-48 were 3/4 floating, the axle housing carrying the weight of the vehicle, but the axle shafts carrying the differential gearing). To find what this axle looked like, research Ford 1.5 ton trucks from 1930-52--they are ALL the same design, differing only in the part number, which changed yearly! As for engines: Model AA of course, used the same 200.5cid 40-hp flathead 4cyl as the passenger cars, with a 4-speed top loader manual transmission. 1932 Ford BB trucks used the Model B 4-cyl engine (an upgrade of the Model A engine, virtually identical in appearance, with only the oil overflow pipe on the left side valve galley cover plate being deleted, and of course, an AC mechanical fuel pump added to the right side front of the cylinder block. V8 engines were in very short xupply through most of the 9-month production run of 1932 vehicles from Ford, which lead to them being excluded form heavy duty truck use--beginning with the 1933 model year, however, V8's became available for heavy truck use, and by early 1934, the Model B 4-banger was discontinued for lack of demand for them. BB trucks, as with the AA, were offered in two wheelbases: 131" and 157". Hope this helps a bit! Art -
32 Ford BB chassis
Art Anderson replied to Frank's topic in General Automotive Talk (Trucks and Cars)
BB trucks were built from 1932-1937. There is a soft cover book with pics of that chassis--I have it, but never scanned the pics from it. Art -
Is styrene carcinogenic?
Art Anderson replied to sjordan2's topic in General Automotive Talk (Trucks and Cars)
Read the ENTIRE news story! If you melt the stuff, or burn it, yeah, it can be dangerous--and that info goes back perhaps 40 yrs or more! Enough of the hysteria! Art -
One of the biggest problems in laying out the tooling for a model kit (any subject) is simply that steel dies do not back out of the way of any undercut in the finished styrene part. This makes molding parts such as those 1950's-early 70's bumpers impossible to make in one piece without a mold parting line were tips of the bumpers, as they wrapped around the sides of the bodywork--it just cannot be done with the bumper as a one-piece unit (in stamping the real bumpers, it took several strikes of stamping dies to achieve that--the biggest reason why Chevy went to 3-piece bumpers for most of their cars from 1955 to the end of that sort of chrome bumpers (except for the so-called California bumpers, which were one piece units for many years (who knows why that was, I sure don't). It might be possible to mold say, a '55-later Chevy bumper in styrene, IF the hobbyist would accept a 3-piece assembly, which I rather doubt, particularly if one had to assemble the bumper guards over the top of that seam (which happened with a lot of Chevies of the era). Tires are always a huge consideration with any model company. Short of the body shell, a tire mold can easily be the most expensive single tool in the tool bank, and as such model companies try whenever possible to get the maximum mileage out of those molds. For 50's and 60's subjects (even 70's and 80's as well) it was a lot easier--there were numerous tires that fit a lot of cars, just slap them on (both model and in real life). But, in any product development conference, if the subject of tooling new tires comes up, someone (and rightly so) will ask "How many more units of Kit X will you sell if we spring for a new tire tool?". That is a legitimate question, and one that is very hard to answer; short of a crying need to replace a badly worn tool, the answer is almost surely to be "no". With the Japanese companies, the tradition has been, tires (and often wheels) come from sources other than the company who produces the kit they are a part of. The Japanese model kit industry has never been a stranger to outsourcing. Even Monogram, back in the late 1950's and early 60's, farmed out their model kit tire production (for models having rubber, as opposed to plastic, tires) to a toy company in the Chicago area who was making rubber tires for the toy vehicles they produced. Sometimes, the tooling for those Monogram rubber tires was unique to the model kit, sometimes not. The smaller subcontractors could, and have, sold their tires to muliple manufacturers many times, even sold them on the aftermarket (American Satco, for example). Neoprene rubber gives the most realistic model car kit tire, but it lacks long life--how many times have modelers lamented the cracking and splitting of tires on their Tamiya, Hasegawa, Aoshima et.al. builds? PVC works better, in that it doesn't fail upon exposure to light and air nearly as rapidly, but used to have universally that ability to rot styrene wheels ("Revell Tire Disease"), and still can if close attention isn't paid to the compound during manufacture. But, PVC won't give nearly the crisp detail, particularly with tread patterns as can be achieved with neoprene--so it becomes "trade-off" time. Side windows are another question: By tradition, US made model car kits seldom have had them, probably since promotional model cars didn't, for the most part once they got interiors. In the few kits that have had them as separate parts, I've not seen many installed. One of the reasons may be a combination of material thickness (actual scale kit glass would be only about .010" thick (1/4 inch in scale) to be proper, but that's too thin for injection molding without the glass being extremely fragile. Mold ejector pins in those old fashioned "tub style" interiors? Simply put, they have to be where they are, if the interior tub was to be successfully pulled from the mold in mass production, not much way around that, unfortunately. Hope this helps the discussion a little bit. Art
-
Jairus, Nope! Henning did a how-to for a 30's rail-frame midget (may have been in Rod & Custom, not the models version though). I actually built up one in 1965 or 66, long before I ever thought of getting any pics of it. Mine was carved from basswood, finished with Aero-Gloss sanding sealer, insignia red frame rails, Taylorcraft Cream for the bodywork. I used straight pins for the grill bars. An old Revell Highway Pioneers '32 Ford Jalopy kit provided the axles, wheels and tires (amazingly very close in scale. The model went to California in the fall of 1985, when a model race car collector came through here, paying insane (for the time) money for scale models of race cars. Art
-
For my fallen brothers and sisters.
Art Anderson replied to whale392's topic in General Automotive Talk (Trucks and Cars)
I grew up around a ton of adult relatives, but one who stands out in my memory is my Dad's favorite cousin, Crystal. Now Crystal was, to see her, just your average midwestern small town homemaker, but there was something about her that I noticed at an early age. She frequently (and surely at every family reunion) would mention "Wayne". Whenever she did that, the other adults would quiet down, while Crystal would relate some anecdote about "Wayne". Who was this person "Wayne" I wondered, as a young, peach-fuzz faced kid in the 1950's? One day (I was perhaps 10yrs old or so), on a quick stop with Dad (I rode with Dad a lot in the summer when he went to make his rounds on business); we stopped at Crystal's home in Oxford IN, just for a quick visit. "Aunt Crystal" I finally got up the courage to ask, "Who is Wayne"? (Ahhh, the innocence of youth!). She went quiet for several moments, put her hand on my head, then quietly took me into her parlor (one of those old-fashioned homes), and showed me a picture on a bookshelf: "That's Wayne", she said, pointing proudly at the photographic portrait of a young man, perhaps 20 years old, in his US Navy Dress Whites. Crystal stopped, said no more, and I watched as she closed her eyes, but too late, the tears leaked down her cheeks. Dad, as fathers are known to do, shushed me, and after a moment or so, Crystal regained her composure, and Dad and I excused ourselves, went on our way. That evening, Dad sat me down after supper (scared me a bit, what did I do wrong?) and then assured me I had done nothing wrong. He related to me, words to this effect: "Son, Crystal cried today, because Wayne was her oldest son, the pride of their family. When war broke out with Japan in 1941, he enlisted in the Navy, and got assigned to aerial gunners' school. Things moved VERY fast at that time, and by late spring, Wayne was flying in the back seat of a Navy dive bomber at the Battle of the Coral Sea." Dad paused for a bit, took a gulp of coffee (he was never without his coffee cup). "Wayne fought at Coral Sea, was cited for shooting down a Japanese plane (not a mean feat, considering he had but a pair of .50 Cal macnine guns in a rear-facing flexible mount on that SBD), and then just a few weeks later, his ship, USS Yorktown headed out to Midway Island to take on the van of the Imperial Japanese Navy." Dad paused again: "Wayne's squadron flew out to attack the Japanese carriers, and his flight and his comrades sank the carriers that had attacked Pearl Harbor just 7 months earlier. When Wayne got back to the States, he was given a month's leave, and he came home to Oxford (a little town of about 1000 in Benton County IN), and we all went out to see him, spend some time with him." Dad's eyes misted up. "Wayne reported back to his squadron at San Francisco in late July 1942. On a training flight over San Francisco Bay, his plane crashed, and he was killed, and he's buried at West Cemetery in Oxford." Whoa! I was both enthralled that I had a cousin (he died 2yrs before I was born) who had done those things, been where he'd been, seen what he'd seen. But tempering that was the sheer disappointment at knowing I would never meet him. A few years later, I was in high school, and assigned to write a paper for history class. I chose to write about Wayne, so back to Oxford I went, this time, a bit wiser, and certainly solemn, and interviewed Aunt Crystal and Uncle Ed, and they told me a lot about Wayne. After hearing of his growing up, the times he had as a school kid, Aunt Crystal went to the bookshelf where Wayne's picture sat, took a little box off the shelf, showed it to me and opened it: The Navy Cross. I was never more proud than I was at seeing that decoration, and at the same time, never more solemn, nor sad, when it sunk in that Wayne had risked it all on more than one occasion to help give ME the life I have lived in this great country. Today, I keep Wayne and the legions of his comrades, regardless of their branch of service, who gave the "last full measure of their devotion" (as Abraham Lincoln so eloquently put it), to "give this life to me" (thanks to Lee Greenwood for that sentiment). So, on Memorial Day, we need to seriously thank every fallen hero, from every war (and there are what, slightly over a million fallen heroes of the US Military since 1775?) for stepping up, bravely going forward, and making the ultimate sacrifice. Our lives we live today we owe to them, folks! Art -
It sort of depends on what style of prewar Midget you want to attempt, but no, there are no kits made of any of those cars, to the best of my knowledge. All is not lost though, as such a Midget can be a pretty easy scratchbuild--given that every prewar Midget was a "rail frame" car, the tubular chassis like the Kurtis not coming until after WW-II (Kurtis began building those in late summer 1945). Joe Henning (artist and writer for Rod & Custom and Rod & Custom Models magazines back in the 60's did an article on how to scratchbuild a late 30's rail frame midget in R&CM in 1964 (dunno which issue though). Thar article had scale drawings, and suggestions as to where to find correct-looking wheels and tires. His plans had no engine, simply because there were no engines in model kits back then that would have worked. But now, with the 110 Offy and the Ford V8 60 from the Revell kits, you'd have the two most popular engines with which to work. Those rail frame midgets generally used transverse leaf springs, although a few were "3-spring cars", meaning parallel leaf springs in the rear, transverse spring up front. Many of those cars used modified Model T Ford front springs, having probably half their leaves removed, and in back, either a modified Model T, or a Model A rear spring and crossmember. Front axles often were shortened Franklin (the air-cooled car) tubular units, shortened of course, and a lot of them used Model T or Model A Ford rear axles, with the axle housings shortened at each end to get the narrower track that AAA and most other Midget sanctioning bodies required back then. the body shell can be laid up by laminating sheet styrene to get the width, then carving, filing and sanding to shape. In short, see if you can find that copy of Rod & Custom Models, or someone who will photocopy the article out of one they have, a little thinking, a little bit of planning, some work and I suspect you can get there. Art
-
For starters, in 1:1 size, Ford pickups from 1925-1941 used passenger car frames, so the fenders would have to have fit whatever frame was used based on the model year. While '32 Ford pickups and 1/2 ton panel deliveries were built on the very same chassis as all Deuce passenger cars, the '33-'34 Ford Model 40 chassis was different, so even though the Model B/model 18 pickup of 1932 used the same front fenders as a passenger car, for 1933-34, there would have been differences where the inner edge of the front fender met the frame rails, while the overall shape stayed the same visually. The rear fenders, however on pickups, from 1925 onward, were different from those used on sedans, coupes and roadsters, due to the shapes of the sides of the various bodies. Art
-
Styrene Question
Art Anderson replied to car lover 1996's topic in General Automotive Talk (Trucks and Cars)
Evergreen has a ribbed styrene sheet stock that will be VERY close to replicating the aluminum covering on that trailer! Art