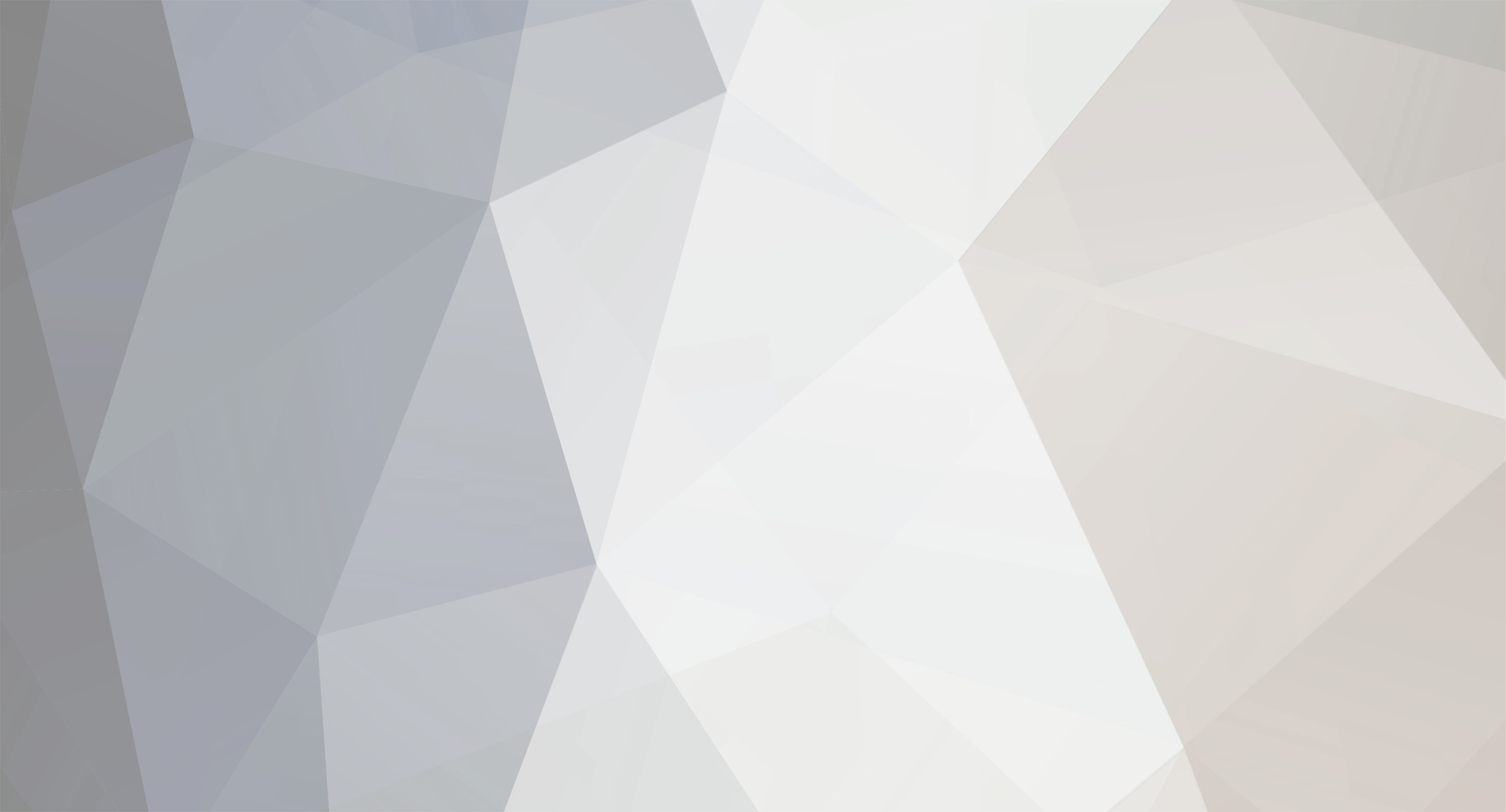
Art Anderson
Members-
Posts
5,052 -
Joined
-
Last visited
Content Type
Profiles
Forums
Events
Gallery
Everything posted by Art Anderson
-
Moebius International Lonestar Sleeper Cab
Art Anderson replied to Art Anderson's topic in Truck Kit News & Reviews
I just recieved corrected test shots of the Hudson kit from Dave Metzer on Friday, 5/27--looks to me as if all the major issues have been addressed! Art Anderson -
Moebius International Lonestar Sleeper Cab
Art Anderson replied to Art Anderson's topic in Truck Kit News & Reviews
John Dezan gave us all a photographic rundown of the Lonestar kit in the Model Trucks Forum on this site, starting right after NNL-East, where I gave him the very first preproduction sample kit to reach private hands. Check it out! Art -
I'm not altogether sure that the original issue of this kit had the wheel well on the left front fender for the stock spare, although the '31 Station Wagon did have the wheel well for at least the left side if my memory serves me correctly, but in any event, given that the first impetus for this kit seems to have been a street rod, chances are whomever built the actual truck used for reference probably installed a passenger car left front fender on which the wheel well was strictly optional--standard practice for Ford was a rear mounted spare on all passenger cars (the side mount spare was an option on those, costing all of about $7.50 factory installed). However, on all Ford commercial vehicles for 1928-29, a side mounted spare was standard, even on the Station Wagon, which from its introduction in 1929 through the 1939 model year was considered a commercial vehicle, and catalogued along with pickups, panels, and 1.5 ton trucks up through that model year (station wagons became part of the passenger car line starting with the 1940 model year). Someone mentioned Monogram Model A Ford pickups--however Monogram produced but one Model A pickup, that being the 1929 Model A Roadster pickup they introduced as the "Blue Beetle" about 1963 or so (not all that sure of the year though). Monogram's Model A Ford kits were just 4 in number (considering that their one multi-version kit was later split up into two separate offerings); the 1930 Model A Phaeton (issued in 1961), 1930 Model A Coupe/Cabriolet which came in 1966, and the 1930 Model A station wagon (which quickly had optional parts to make the VERY RARE '30 Model A Deluxe Sedan Delivery, which was a woodie sedel, modified from the regular 4dr station wagon--only a handful were produced ) which also came out in 1966 as a street rod only kit--but can be built stock by combining it with the coupe, cabriolet or phaeton underpinnings. Of these, ONLY the 1930 Cabriolet kit, wnen produced as a separate subject (no coupe body parts) in the early 1970's had side mount spares with wheel wells, and that only for just one release (the late Bill Harrison from Monte Vista CA gave me 4 fender units and spare wheel mounts from that short run of Cabrio's. Pyro produced a 1930 Model A roadster pickup in 1/32 scale, Hubley did the same subject in 1/20 diecast metal kit form, but nobody has ever done any 30-31 Model A Ford pickup in 1/25 or 1/24 scale, outside of a couple of resin offerings. Art
-
Revell actually introduced their '29 Model A pickup kit in the 4th quarter 1965. It's pretty much always been a multiple version kit (closed cab and roadster-pickup bodies included from day one, stock and street rod versions). Originally, the stock version of this kit had correct Ford AR wire wheels with correct Firestone tires, although in order to be able to use the same tire tool, Revell stuck with the 4:875-19 Firestone tire that was standard on the 30-31 Model A--those having been tooled for their excellent '31 Model A Tudor Sedan/Station Wagon kit which came a bit earlier in 1965. The only change in the tooling was the rear window on the closed cab: Originally, Revell's product development team used a modified truck as a reference. That pickup had it's original small rear window frame removed, and a new one fabricated--not uncommon with street rodders back in the 60's (the rear window frame reduced the size of the glass markedly, and was a simple panel bolted into a much larger opening, for reasons known only to Ford designers back in the day). This was corrected with the Rat Rod version which came out in the early 2000's, while the wire wheels and skinny Firestones (Firestone Tire & Rubber was Ford's exclusive rubber component/tires supplier from 1903 until the great Explorer "exploding tire" debacle of about 10-12 years ago--a little known fact of Ford production for all those decades). All in all, this kit, along with its companion '31 Tudor/Station Wagon kit is still the most accurately done Model A of all--AMT's '29 Roadster, along with the MPC '29 Station Wagon/Roadster Pickup both have issues with some body shapes and of course, their overly heavy-handed frame and suspension components (like the front axle!). But, in the bargain, like so many Revell model car kit offerings 1962 to well into the 1970's, these are very delicately engineered kits, some very fiddly construction, but with patience and perseverance, can be made into stunning, if somewhat fragile, models. Art
-
Terry, not to be terribly argumentative, but would you have the same objection were someone to do a bang-up job of painting and detailing out a plastic promotional model car (considering that promo's, like diecasts, come pre-assembled)? It's been a couple of years, but I have reworked a couple of diecasts in my time--and to do that as I did required the disassembly, complete stripping of all factory paint, smoothing and filling mold parting lines, followed by primer, paint, surface detailing, and reassembly. It seems to me that doing all that work was about the same as building a somewhat simplified plastic kit with the addition of needing to disassemble the thing to start with. The old IAAM (International Association of Automotive Modelers), which operated nationally from the early 1950's until the late 1980's had members with a HUGE prejudice against PLASTIC model car kits (perhaps you were unaware of them, or that controversy?), declaring almost officially that the only true car modeling was done in wood, card stock or metal--plastic need not apply for admission. Where is IAAM today? Gone, save possibly for a small group of increasingly elderly builders in the Los Angeles area, and the Chicago Area's Lake Michigan Model Car Club, which began as the home chapter of IAAM in 1951, and gradually morphed into one of the very first model car clubs in the US, embracing plastic kits and builders of such over the years (but as late as 1990, there were still members of that club who scratchbuilt in wood, paper and metal). In other words, the "old line" disdain for the plastic kits we on this board all embrace and love made IAAM very irrelevant over time. A diecast model car is just that, a model car. Now, it can be collected as manufactured, or reworked, reworked to whatever degree you or anyone else might imagine. At this year's NNL East, Vince Lobosco showed a beautiful 1934 Packard V12 Roadster by Dietrich, converted from the very well done Franklin Mint '34 Packard V12 convertible sedan. I would challenge anyone who saw Vince's masterpiece at NNL to say it was anything less than a tremendous automobile modeling example (any takers?). Bear in mind that not every car modeler works only with the popular subjects of drag cars, pro-street, street rods, customs or even big trucks. Some of us love the really OLD cars (you know, the ones with brass radiators and seemingly polished brass everything else). Trouble is, unless one is a scratchbuilder of Gerald Wingrove's caliber, such subject matter is available ONLY in diecast for the most part, there having been only a handful of acceptable-in-today's-world plastic kits out of the era 1895-1930. Now, with all that said, I found a great color scheme for a 1928 Stutz Blackhawk Speedster (that's a 1928 Muscle Car to the uninitiated BTW), which will require my taking apart one of my Danbury Stutz's, stripping the bodywork, repainting it, and probably scratcbuilding s set of 6 wire wheels, mebbe even the tires for it. I won't mince words here: If I do such, you can danged well bet your back teeth I will consider that to have been a model car building project of....a model car. Art
-
Just to add a bit of history to all this: AMT Corporation, while maintaining a high volume of sales through the 1970's, hit a real wall in terms of profitability by 1979--to the point that in midsummer that year, they had determined that the only course was bankruptcy. Lesney Corporation Ltd (maker of Matchbox Toys) stepped in at the last minute, just hours before AMT's attorneys were to go to US Bankruptcy Court in Detroit, and bought the company. AMT's Troy Michigan factory was closed, all production moved to their second plant in Baltimore MD, Lesney-AMT setting up their management and product development activities in Warren MI. However, the recession of 1981 proved to be Lesney's undoing--they in turn filed for bankruptcy in New Jersey, Baltimore and in the Detroit area in April 1982(I was privileged to see their sales figures for model car kits for the first quarter of 1981--they were worse than dismal!). The same malaise struck MPC, Revell-Ceji, even the then vaunted Monogram Models--in fact it was extremely hard on the hobby industry all over the US.). In mid-summer 1982, The Ertl Company (then owned by Union Carbide through their Victor Comptometer subsidiary) bought the AMT product line, with all tooling, rights and licenses. Production of AMT model kits resumed in Dyersville IA in early 1983. Art
-
As far as I know, the '34 Pickup tooling was the only tooling "forgotten" in htis manner. As for the dually rear wheel setup--that appeared for, I believe, the first time in a 1976 modified reissue of the kit, which saw the addition of the stake body (I built the box art models for that release in January 1976). Art
-
Best Product To Deal With Sink Marks?
Art Anderson replied to MILD's topic in General Automotive Talk (Trucks and Cars)
If you are talking about the "marks" resulting from raised details being removed (by filing and/or sanding), those aren't "sink marks" but rather what is commonly called "ghosting". To deal with "ghosting", let's start with an understanding about what is happening: Bear in mind, plastic model kits are molded under extremely high pressures (about 100 tons pressure!). The styrene is cooled, and solidifies at this pressure, which ordinarily causes no problems. However, when one sands, files, removes raised details by whatever means, and then paints with lacquers--the built-in stress of that high pressure injection molding is relieved (lacquer thinners penetrate styrene, soften the surface), causing the removed detail to swell up, reappear. I've found that the only real solution to this is to use primer, airbrush if possible. I spot prime areas where I have removed surface details or even mold parting lines, just as if I were a body shop, fixing imperfections. I then wet sand down the offending "ghosting" just to the point of smoothing down these areas, and repeat the process again as needed. This has always worked for me when tried--I started painting model cars in acrylic lacquers in the 1960's. Art -
Taking the Shine Out of a Grill
Art Anderson replied to Bruce Poage's topic in General Automotive Talk (Trucks and Cars)
'53-'55 Ford F-series truck grilles weren't aluminum--rather they were stamped from sheet steel, same material as the body parts. On low-line trucks those were painted "argent" or metallic silver, but for an extra charge, you could get a CHROME plated one (same trim levels included bumpers and hubcaps--headlight bezels were plated on all versions, IIRC. Art -
With any model kit, no matter the complexity or lack thereof, there will ALWAYS be compromises. Keep in mind, folks, that every time we, or a model company, consider the notion of "just a few more parts" here or there, that can mean additional tooling, a new parts tree, and that means more cost, often considerably more cost. And, as already noted here in this thread, added cost in tooling directly translates to added retail price by the time it gets to us. Why is this? With a kit the size of the Lonstar, each parts tree you see is a separate tool, and in modern kit production, each separate parts tree means the use of an additional injection mold machine, and an additional person to operate it. Addtionally, even one more parts tree can mean a larger or deeper box, and that translates into high shipping costs (which are not inconsiderable these days). And even more, added parts mean more complexity in any model kit. It's wise to bear in mind here folks: We who are the readers and frequent posters on this and other model car message boards are not exactly "Joe Average" model builders or even kit buyers. What may well suit our tastes, whet our model building appetites, delight us with tons of tiny parts; may well (and this has happened!) drive away a pretty large market--those who can't or won't buy a particular kit when it even has the appearance of being overly complicated, or just by looking at a bazillion tiny little parts. As a former hobby shop owner, I can attest with absolute certainty that such has happened over the years. Just how many Accurate Miniatures McLaren kits get bought, and even more, how few really got built? With that example, I rest my case. This of course, is in response to the question of why no separate clearance lights. On that same subject, why stop with clearance lights? Why not separate plated door handles, separate plated scripts and badges? Why not separate, separate, separate, separate. This is a list and an argument that could go on Ad Infinitum it seems to me. Art
-
question about this motor tool
Art Anderson replied to Lownslow's topic in General Automotive Talk (Trucks and Cars)
Any 120V moto tool can be slowed down. You can use the Dremel speed control box, or as I do, use a simple light dimmer which is on a separate plug, has a slide switch that allows you to change the voltage going into it. Art -
Hard to find, of course! A couple of sources (not by brand name, as I don't know) might be Superscale Decals or perhaps something from the RC plane or race car side of the hobby shop. Of course, if you are wanting to apply checkered patterns to a model car, it may well be that you would be better served to lay it out in masking tape, over the lighter color, then airbrush the darker/brighter color, and remove the tape. That will allow you to "bend" and "flex" the motif to fit the body lines, something that could well be nearly impossible to do with a decal sheet, whose checkered pattern will be pretty much set as if it were going on a dead flat surface. I've done a few checkered paintjobs on race cars in years past--not the quickest project, but it did work every time I tried it (Bardahl Indy Cars). Art
-
Actually, that Microbus is a development of a concept van that VW showed back about 2002-2003 at all the big new car auto shows. I got the assignment to develop the Johnny Lightning 1/64 scale diecast of it, in early 2003--I wasn't terribly impressed with the looks of the thing, dunno if it sold all that well, even when marketed in our VW-series assortments. Art
-
Has anyone built?
Art Anderson replied to High octane's topic in General Automotive Talk (Trucks and Cars)
The biggest problem I found with the kit is that done in styrene, the walls are WAY too thin--Ed's idea makes sense, foamcore is much thicker, 1/4" foamcore makes for a 6" thick wall, which with the styrene exterior, makes for 8" thick concrete block. The "missing" back wall can be easily fabricated, details such as the gas pumps can be modified to correct height, or replaced with aftermarket units. But, like any model kit, pretty much no way to add all the tools and equipment to the kit upfront, and make the price palatable. Art -
The Lonestar kit that John has shown here is as the kit will be produced. The aircleaner assemblies were modified to be 3-piece assembly, with the top part being one piece, the lower aircleaner bodies still being 2-pc (they have to be, given the amount of raised detail on them). What really distinguishes this kit from the test shot kits previously shown (and the one at NNL-East that was built) is that all the fine engraved details have been added--that work is seldom ever done until after a test shot has been approved. I recieved this kit from Dave Metzner about 3 weeks or so ago, the package was assembled in his home/office from bulk supplies of sprues, along with the decal sheet, instruction booklet, and a sample of the kit box. Art
-
1990 Contest annual - then and now
Art Anderson replied to Jantrix's topic in General Automotive Talk (Trucks and Cars)
The times, they have changed, for sure! Just looking at the pics I took at NNL-East, of the show itself reminded me of the first model car events I participated in: Bell Auto Supply, a locally owned Mom & Pop auto supply store, downtown, on the courthouse square here in Lafayette. Their first contest, in 1959, had perhaps 300 entries (which would be about par today for a small club show away from the big cities), but by their contest in the spring of 1962, their contest drew well over a thousand model cars. Difference? Well, for starters, in 1962, there were perhaps 50 or 60 model car kit subjects that had been done, not including the Revell 1/32 scale offerings from the 50's--today, how many possible kits (both in and out of production) can be called upon? THOUSANDS, literally thousands tooled up and produced over the past 50+ years. Aftermarket? Hmmm, some naugahyde upholstery kits (merely small squares of naugahyde, in a variety of colors), an engine wiring kit (we teenagers were just discovering Xacto knives, a pin vise was an exotic tool!), very little more than that. Paints? Well of course, Testors had their wonderful 75-color rack of those little 1/4 oz paints; but they hadn't hit on the PLA formula yet (PLA meant it had a plasticizer in it, which made it go tack free within an hour or so) meaning paints that dried to tacky in about 4 hours. Pactra 'Namel was very much where it was at--they'd started their line of Sof' Spray rattle cans, at the princely sum of 69-cents a can (3.5 oz), and only by the late summer of '61 did they introduce their wildly popular Candy Colors series (Candy Apple Red, Emerald Green, Tahitian Gold, and Emerald Blue (Candy Strawberry, Indian Turquoise, Aztec Copper would come in early '62). Pactra introduced a line of pearlescent paints in the fall of '62, but in bottles only. The price of those paints? Testors 1/4 oz retailed for a dime, the Pactra 1/2 oz bottles were 15-cents. There was a sea-shift with the coming of plastic-compatible rattle cans, and most of the older guys (in their late teens or early 20's who had perfected the art of laying down perfect enamel paint jobs on model cars with wide flat brushes found themselves being shoved aside by fresh-faced kids who'd mastered spray cans--many of those older builders left the almost adolescent hobby, never to return (which was a big loss, when I look back at it). Wiring a model car generally got done with common thread from Mom's sewing basket, a few modelers were discovering that carpet thread didn't have quite that fuzzy look of the cheaper thread Mom used to repair our school clothes with. Upholstery? Well, if you wanted rolled and pleated, there was corduroy, available in a range of colors, down at the fabric store--a huge remnant, enough to do dozens of model car interiors could be had for perhaps 50-cents. Just cut it out, glue it down. Add to that some braided trim from the fabric store, use some terry cloth or velvet for carpets and behold--custom interiors! Putty? Uh well, most of us made do with the likes of Plastic Wood (or Pactra's alternate, their Plastic Balsa--very quick drying, but VERY porous!), or made our own from tube glue and talcum aka Johnson's Baby Powder (Squadron, Tamiya, and the various catalzed putties weren't even on our radar screens back then!). Styrene stock? Hah! Not unless you had the tonneau cover from one of the 3 or 4 pickup truck 3in1 kits, nope, not in the spring of 1962. Moving fast forward to 2011--how fast, and how far the goalposts have moved. We teenagers of 1962 are now mostly in our 60's, older, moving slower, grayer (or should that read "white-er" of hair--if we indeed have much to show any color at all!), and still building models. And, the personal contact side of this? 50 years ago, we kids only knew of school friends, kids in our immediate neighborhood who built models--never dreaming that someday we'd be chatting and posting about models all over the world--and with a couple of great magazines to help carry the torch. Who'da thunk it, huh? Art -
Is it just me, or does the sidewall shape and siping make those tires look as though they came right out of about 1936? Art
-
37 ford truck grill
Art Anderson replied to BIG-JIM's topic in General Automotive Talk (Trucks and Cars)
There are rules, of course: To begin with, there are at least two entities involved as regards copyright issues involving a model car kit (or for many other subject areas as well). There are the copyrights owned by the manufacturer of the real car or truck, AND those copyrights rightfully owned by the company who made the model kit. In the case of a direct recast of a model kit part for sale, either the 1:1 automaker OR the model kit manufacturer can come after the individual or company doing such direct reproductions (and there have been instances in which either or both have happened). As a practical matter though, if a model kit has been out of production for so long a time as to lead others to believe that it will never be reissued (or if the manufacturer, such as Aurora has disappeared from the scene years ago) then I suppose that reasonably, nobody in the model kit industry is going to take issue with any reproduction of such kits or parts involved--Modelhaus and other resin casters have all done that over the years. But IF the part is a direct repop of a part from a currently available kit (or from a kit that gets reissued periodically) then the kit manufacturer can come after the person(s)reproducing said part. In any case, if there is a 1:1 automaker who owns (or claims to own) the rights to a formerly produced car or truck, they can also bring action to stop such reproductions in miniature if no authorization was obtained. Now, if the model kit part is substantially modified from its original form, say either to make it adaptable to a kit other than the one it was taken from (a chopped '37 Ford grille and shell, a chopped '32 Ford grille shell and grille) then it's going to be pretty hard for a model kit mfr to make any claims, and I don't believe any have ever done that. Additionally, 1:1 automakers aren't likely to be worried about such customized or modified parts in a model kit either. Trademarks, however, can be a different story, and often are: FORD is a registered trademark of Ford Motor Company, when applied to an automobile or truck, or parts therein. Years ago, Ford Motor Company blanketly would not even allow reproduction parts for antique Fords to carry the Ford script (ever see reproduction hubcaps for a Model A or Model T that read "FOOL" instead of "FORD"? That was the result (Ford saw the light, saw that people restoring old Fords correctly was a good thing, about 1970 or so, but that is the history of it. Chevrolet trademarked, over the years, not only Chevrolet, but Chevy, Bowtie, USA-1 and numerous other names and nicknames. But in the bottom line, why directly copy a part or parts from a currently available model kit? That to me seems just a bit unethical to day the least, if it's done for profit, profit gained by selling copies to others in an unlimited fashion. Now, if one wants to reproduce that part for their own use, I believe the "fair use" doctrine allows that, just as it allows a student to photocopy a page out of a book or magazine as part of a research project, or to lift directly text from someone else's publication (as long as it is credited, either directly in the body of that student's writing, or as a footnote at the bottom of the page (think High School Term Paper 101). But why bite the hand that feeds our hobby with not only old favorite kits, but even new product from time to time? (and why risk legal action from a real car manufacturer--who certainly can afford a bigger lawyer than any of us modelers can pay for?) Art -
Black Welly Tahoe decal question
Art Anderson replied to bigdodge88's topic in General Automotive Talk (Trucks and Cars)
Most diecast models/toys are decorated by spray painting for both the primary and secondary colors, and then logo's and emblems are applied by a process called "pad printing" which we know commonly as "Tampo Printing". This is an often multi-step process whereby each different color used in a particular logo or graphic is printed with fast-drying paint onto the surface of the model. With diecast models, the base color generally is sprayed, then baked hard, a secondary (think 2-tone schemes) such as the roof, or perhaps the upper part of a body, is then spray masked with that/those secondary color, then the Tampo printing is done. How to remove? Common ordinary enamel thinner will generally dissolve and wash away Tampo printing, because that's not baked on, but it may also remove or at least mar a secondary sprayed on color, as that color will not have been baked on. In short, experiment with the Tampo printing and enamel thinner, it should not harm the original overall color on the model. Just be careful if there is Tampo printing on a second color which appears to have been sprayed on, chances are that color can be marred or removed by even enamel thinner. Art (who used to work in product development of diecast miniature cars) -
How many car/truck modelers?
Art Anderson replied to Erik Smith's topic in General Automotive Talk (Trucks and Cars)
If one really thinks about it, the number 17,000 is rediculously low. Such a small number of individuals simply could not support the production of one single plastic model kit, let alone the wide variety of model kits offered by what, at least a dozen manufacturers with retail exposure in the US. There really isn't any good way to estimate how many model car and truck builders are out there, simply because no system exists to enumerate them. The range of model builders runs all the way from the person who might build one or two kits a year, to someone who cranks out several models a week. And with the vast majority of us model builders, a very high percentage are invisible, unknown to the rest of us. Even the largest of model car clubs in any city represent only a snall fraction of who's out there buying and building. Art -
Superboss--Tyrone Malone.
-
1940 chevy coupe??????
Art Anderson replied to lowriderphil's topic in Model Building Questions and Answers
Unless there has been a '40 Chevy done in 1/43 scale or smaller, no. 1940 saw a one-year-only body series for Chevrolet--nothing above the chassis was carried over from 1939, and the '40 shares nothing bodywise with the '41 or later cars, although 1940's styling did predict that of 1941. Art -
Revell, of course, was bought up by Monogram almost 25 years ago, and once that happened, over time, a lot of kits bearing the Revell brand, if newly tooled in 1/25 scale, actually used the older, but readily available Monogram 1/24 scale tires from tooling cut at Monogram over the years (Monogram, you may recall, was the bastion of 1/24 scale model car kits from the early 1960's until their now iconic 1959 Cadillac Eldorado convertible kit of 1992). This meant that newly tooled Revell kits from the merger with Monogram, until the early-mid 1990's had larger diameter wheels than would have been correct for 1/25 scale model kits. Even after their decision to tool new kits of American mass-production cars in 1/25 scale, Revell-Monogram chose to continue offering most all their racing cars (Nascar, Drag Cars, Sports-Racing cars) in 1/24 scale, to keep them compatible looking with past product. It seems to me that Modelhaus does suggest what wheels work with each of their tires, do they not? If not, then I've missed something along the way here. But, at the bottom line: Most every model company has their own standard for model kit tire and wheel compatibility. While Revell AMT MPC and JoHan, for example each produced model car kits in 1/25 scale of cars which were built with 15" or 14" tires in real life, in model kit form, they all used the same inner and outer diameters for whatever tire they individually produced, and back in the 60's, the tires of model company A generally fit the wheels from model companies, B C and D rather poorly, and often not at all--just different designers and different engineers and different pattern makers; each company's team doing it "their way". For both competitive reasons, and with at least a nod toward the "Anti-trust" laws here in the US, no effort was ever really expended by any of the model companies to make their wheels and tires interchange readily between kits--any interchangeability was probably co-incidental. As an additional thought here: Model companies (and this includes diecast producers as well, at least the more popular priced brands) have seldom wanted to invest serious money into creating a wide variety of tires for use in their kits. For years, most all the model car kits within any one company have been made around those tires available in that company's "tooling library". As one who's done a bit of product development, it can be awfully hard to get upper management to commit serious tooling dollars for a new tire mold, when there are existing tire tools in the library that are still more than usable, unless said new tire is necessary in order to have noticeably correct tires in a proposed new kit. And even at that, management is more than likely to ask some hard questions, not the least of which would be "what other model car kits will this new tire be used in?", and that can be a pretty tough question to overcome. Art