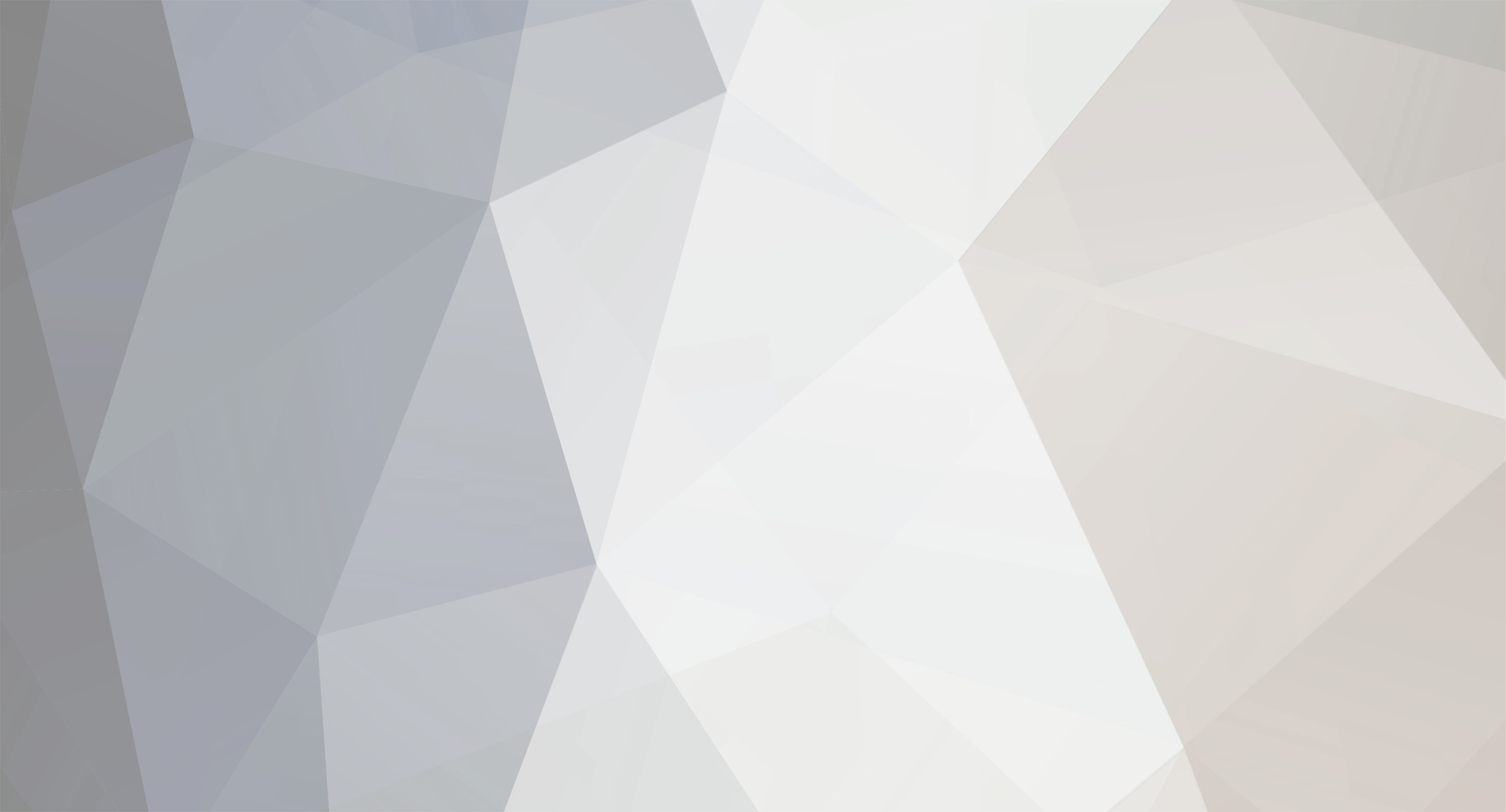
Art Anderson
Members-
Posts
5,052 -
Joined
-
Last visited
Content Type
Profiles
Forums
Events
Gallery
Everything posted by Art Anderson
-
Not Dave, but I would guess late November on the Hudson, Chrysler C300 probably in late December. Both are in tooling right now, but there's always the test shot phase to go through before everything is finalized. Art
-
best tooling of a 33 ford?
Art Anderson replied to hellonwheelz3's topic in Model Building Questions and Answers
While in real life, the windshields of the 33-34 Ford roadsters/phaetons are different than those used on '35-36 Fords of the same body styles, the overall look is very much the same. With that in mind, locating a '36 Ford roadster windshield from an old Monogram kit might be the way to go here. Of course, there are Duvall windshields available out there, currently only from Norm Veber, I believe. Art -
Revell-O-Gram 87 Thunderbird TurboCoupe
Art Anderson replied to whale392's topic in General Automotive Talk (Trucks and Cars)
Actually, Brian McIntyre (a Purdue student at the time, and a close friend) did scale out the '87 Thunderbird, and found it to be pretty darned accurate. Brian worked up a master of the 1986 Thunderbird Turbo Coupe for me to cast, using the pro stock body shell, and it fit the '87 chassis perfectly, with no alterations in length needed. Even the Pro Stock kit's hood fit with only a bit of modification to trim down the pronounced upward flare at its rear edge as well. '87 Thunderbirds did have a very noticeably longer nose on them, as part of their styling facelift, and coupled with the changed roofline (gone was the quasi-fastback of the 83-86 cars), that certainly makes the '87 Thunderbird look a LOT longer than the earlier versions. Another Purdue student modified the Monogram '87 body shell into the '87-'88 Nascar body, and that too fits the Monogram Nascar chassis like a glove, again with NO alterations as to length of the '87 body shell. I wound up casting slightly over 5,000 of that body in resin 1990-86. So, go figure? Art -
Offenhauser built DOHC 4-cyl engines in several sizes, actually, primarily to meet the formulae set out by AAA's Contest Board, and later USAC's displacement limits. The smallest of these engines was of course, the Midget engine. The Midget Offy started out at 91cid, and was later enlarged to 102cid, then to 110cid (where it remained until the mid-1960's when USAC allowed it 120cid, it's largest displacement). In addition, a few 74cid blocks and cranks were made, for a handful of supercharged engines. The Offenhauser Midget, just as with every Miller engine before it, and all Offies after it, was built up from a cast-iron cylinder block with blind-bored cylinders, bolted to an aluminum crankcase, its crankshaft suspended round, diaphragm-shaped main bearing webs that were mounted to the crank, then the assembly press-fitted into the case (3 mains in the small midget engine, 5-mains in the larger sprint and championship engines). This made displacement changes easy to do, along with repairs and rebuilds. The largest engine used in AAA/USAC competition was the Championship Offenhauser, which ran at 274cid (4.5 liters) from 1937-1955. USAC, coming on in 1956, after AAA (American Automobile Association) discontinued its sanctioning of Indianapolis, the Championship Trail, Sprint Cars and Midgets in the wake of not only the fatal crash of Bill Vukovich at Indianapolis in 1955, but also the disastrous crash of driver Pierre LeVegh at LeMans that year, which killed not only LeVegh, but nearly 90 spectators (a couple hundred spectators were also injured, many seriously, when Levegh's Mercedes Benz 300SLR crashed into the crowd, and burst into flames); reduced the displacement for pure racing engines to 255cid, which remained the displacement limit for normally aspirated Championship racing through the end of the Offenhauser and Drake-Goosen-Sparks engines in 1979. Offenhauser also produced a 220cid engine, to the same pattern as their 274/255 for sprint car racing, where it reigned supreme until Parnelli Jones introduced small block Chevy V8's to sprint cars in 1960, along with another young "hot shoe", Jim Hurtubise. With that, the 220cid engine faded from racing. Offenhauser also produced the big engine in 318cid form, for use in IMCA in the late 1930's, and at least one of those was installed in a sports car built up from a Miller-Ford frontdrive chassis, for sportsman Tonny Lee, son of the famed Don Lee, 1930's dealer in the likes of Cadillac, Packard, and a few import luxury cars (also campaigning Alfa Romeo and the legendary Mercedes Benz W-163 V-12 Grand Prix car at Indianapolis 1946-48). Frank Kurtis handled all the modifications made to the 1935 Miller-Ford front-drive Indy car chassis for Lee. Meyer-Drake Offenhauser built up a special 241cid Offy for car owner Merle Belanger, of Crown Point Indiana, which engine won Indianapolis in the Belanger Special, essentially a Kurtis Midget stretched out to 96" wheelbase (the Kurtis Midgets ran a 72" wheelbase, standard for AAA and USAC Midgets) to meet Championship specs, with stretched midget bodywork, and a stretched sprint car tail) with driver Lee Wallard up. In addition, Meyer-Drake Offenhauser built at least one 183cid engine, with centrifugal supercharger for car owner Roger Wolcott, of Wolcott IN, which he had installed in a couple of different chassis for Indianapolis and Championship Trail competition. For 1966, Meyer-Drake built up two versions of a 168cid Offy, one for use turbocharged, the other for car owner JC Agajanian, mounted with a Rootes-type supercharger (similar to a GMC blower common in drag racing back then). The Rootes equipped engine ran only in 1967, but the turbocharged versions, funded by Goodyear Tire & Rubber, carried on through the 1970's, first at 168cid, then 159 cubic inches, finally ending up at 151cid, with most of the developlent work done by the legendary chief mechanic, Herb Porter. Before pop-off valves limited turbo boost, 151cid Offies could crank out over 1100hp at approximately 10,000rpm, with one engine running away on Porter's dynomometer, reaching an astonishing 1,500hp before they shut it down! That does, I believe, represent the most power ever gotten from such a small displacement engine. The last variant of the Offy 4 was the DGS, or Drake-Goosen-Sparks, which name came from Dale Drake, by 1967 the sole owner of Offenhauser Engineering (Louis Meyer, Eddie Meyer's older brother, having sold out his part of Offenhauser to be the agent for the Ford 4-cam Indy V8, and involved in the Turbo-Ford project as well), Leo Goosen (by then nearly 90 years old and still the only man in the US making his living as a racing engine designer), and engineer Art Sparks of ForgedTrue piston fame. (Art Sparks was an accomplished engineer in both Civil Engineering and Mechanical Engineering, having designed the best of the board--wooden--superspeedways of the 1920's, which became pretty much the pattern for the likes of Daytona International, Charlotte, and Taladega along the way) and the brains behind the Sparks 6-cylinder DOHC's, which were funded by Millionaire Playboy Joel Thorne 1936-46, winning Indianapolis in 1946 with George Robson driving). The DGS was essentially an Offenhauser, with the valves set at an included angle of 60 degrees, rather than the 90-degree angle that had been used on Offy's and their predecessor, the famed Miller racing engines, and the engine that started it all, the 1913 Peugeot GP engine that won Indianapolis that year. The DGS powered numerous Champ cars 1977-82, but was pretty much overcome by the Cosworth Ford DGS, which was pioneered in USAC in 1975 by Vel's Parnelli Jones Racing, stemming from their aborted Formula 1 effort. For 1978, Drake Engineering built up a turbocharged Drake V8, using much of Offenhauser design tradition, along with DGS technology, but it wasn't successful, and only 2 or 3 were ever built (the weak point of that engine was the use of open Gilmer belts to drive the overhead cams--they never did get the bugs worked out of that. But by 1982, it was all over for the Offenhauser in serious racing, as Dale Drake closed Offenhauser Engineering shortly before he passed away, Leo Goosen passed away in 1979, and Art Sparks retired, by then himself a very old man. FWIW, as I know someone will wonder, and ask: Offenhauser Speed Equipment was originally produced by a nephew of Fred Offenhauser, who capitalized on his more famous uncle's name--they were not particularly close as relatives after that, from my readings. Fred Offenhauser would not be bothered by high compression heads for mere Fords. Art
-
I suppose acetone could be used to thin lacquers, however it may well craze the styrene badly. I much prefer using lacquer thinners, they are a known quantity to me at least. Art
-
I need help with a lincoln engine
Art Anderson replied to randx0's topic in Model Building Questions and Answers
Bingo! You are correct, my bad! http://lh4.ggpht.com/_xEwEhGrtCS4/RxxWzqjJHXI/AAAAAAAAGms/Tvxd18EB2_g/1928+Lincoln+Model+L+Dietrich+-4.jpg Art -
I need help with a lincoln engine
Art Anderson replied to randx0's topic in Model Building Questions and Answers
Part 13 is the intake manifold, the carb mounts underneath the middle of that, then the manifold mounts to the raised portion of each cylinder head. The exhaust manifolds (one for each head) mount to the inner sides of the cylinder blocks (that Lincoln, like all early Vee engines, used a pair of iron cylinder blocks, each bolted to its respective side of the aluminum crankcase--this was before Oakland, Viking--Oakland, the parent of Pontiac, Viking, a submake of Oldsmobile 1928-31-32--and later Ford pioneered the concept of a V8 engine cast enbloc, or "all in one piece"). The first generation Lincoln V8's, dating from 1921 used updraft carburetors, given that fuel delivery was by gravity from a reservoir tank on the firewall, above and behind the engine (fuel was sucked up to that reservoir by intake manifold vacuum from the gas tank mounted in the very rear of the chassis (this was before GM AC Division pioneered the mechanical fuel pump used for the next 45-50 years). As for cooling, those engines used water outlets on each cylinder bank, just like the later Ford flathead V8's, the water pump mounted on the front. I seem to recall (haven't looked at the kit in a long time) that MPC may not have done the hoses etc. The water pump is part 6, water inlets are parts 222 and 223, the pump needing to have a hose to it from the bottom tank on the radiator, upper hoses going to the radiator top tank. Art -
Lacquer thinners, those aimed at professional painters, were/are formulated to provide a pretty much standard drying time, at different ambient air temperatures. This was so painters could get lacquer to flow out, then dry, in hot weather, or dry reasonably quickly in winter weather, hence the various temperature designations. I use 50-degree thinner with lacquers on models for a completely different reason, though. Thinner made for use in 50-degree air dries much more quickly at ordinary room temperatures, say 70-72 degrees, giving it lots less opportunity to craze or etch styrene plastic, which lacquer thinners can dissolve if left wet on the surface long enough. Part of the stuff I learned while experimenting back there in the early 1970's. Sak, back then, I hooked up with our local NAPA dealer, who sold NAPA's house brand of automotive paints, Martin-Senour. The guy had literally hundreds of rattle touchup cans of paint, some going way back to the late 1950's. In more recent times, I've also used my share of Duplicolor. Art
-
I plead guilty. The technique is one I learned way back in the early-mid 70's when working with automotive acrylic lacquer on models. I'd done some of that earlier, for painting models of Indy cars (which I built almost exclusively for almost 20 years, only a few excursions into street automobiles). I had to relearn how to use the stuff, as overspray from ordinary recommended airbrush techniques of the time caused partially dry overspray to "eddy" around the back of body shells, making for a finish there that looked like the car was in a sandstorm, literally. It was in figuring out how to avoid that, that I came up with the idea (bear in mind, back then no internet, no model car websites, and very fiew model car clubs anywhere to allow the sharing of information and ideas!). In its most basic, it involves REALLY thinning out lacquers (the 2% milk consistency is a starting point), doing likewise with lacquer primers, using low temperature lacquer thinner (ambient air temp 50 degree) at room (shirtsleeve) temps, the lowest possible air pressure at the airbrush, opening up the material control to get a decent but fairly small spray pattern, and then moving in close. One step with lacquer primer that I figured out was to polish the primer first, to a satin finish. All this allowed me, back then, to get paintjobs that didn't hide the surface details, seldom needed anything more than a quick polishing with the finest grade compounds (later supplanted by NOVUS and MicroMesh, BTW), and best of all, no problems with overspray. The "Norbie" name came from John Dezan's suggesting that I come up with someone similar to his "Jackson" alter ego/figure, who is a bit of a fixture on Spotlight, has been since Hobby Heaven days. I've described this painting system countless times on just about every general model car message board, and in the 2 or 3 model car related internet chat rooms I've frequented over the past 14-15 years or so. It's not an exclusive technique/system, others have found it out on their own as well, and I make no claims to being some sort of Nobel Laureate for it. But, it does run counter to a lot of people's notions, and certainly deviates from what most airbrush artists recommend for artwork. And also, it works very well with just about any type or brand of airbrush, from feedback I've received over the years. There, does that explain things just a bit? Art
-
Mike, Both cars are V8-60 powered, given the exhausts on both sides of the body (Offy midgets almost always had their exhaust on the right side, carburetors or fuel injectors on the left (much less chance of dirt or gravel being thrown up into them that way). The car on the left is a Kurtis midget, but the car on the right is an older design, a rail frame car, which Kurtis didn't build, although it may well have some Kurtis body panels on it, which did happen. Eddie Meyer came from an illustrious racing family--his brother, Louis Meyer, was the first 3-time winner of the Indianapolis 500 Mile Race (1928--his winning Miller 91 also pioneered the use of metallic paint [gold metallic by DuPont] and is on dispiay in the museum at IMS, Meyer driving a ceremonial lap on the Speedway before the 1978 500, only the second Indy driver to drive his winning car there FIFTY years afterward); later partnered up with Dale Drake to form Meyer Drake Engineering, producing the Offenhauser engines 1945-1966 when he took over distribution of the Ford Indy V8. Louis Meyer won in 1928, 1933, and 1936, was challenging Wilbur Shaw for the lead toward the end of the 1939 race when he crashed (uninjured) and retired from driving. Eddie was best known for his creation of perhaps the most successful 2-carb intakes for Ford Flathead V8's, and his company built up a lot of those over the years, in addition to selling intake manifolds to hotroders all over the country. His racing career was more focused on power boat racing though. I have to wonder though, if your friend's car isn't a somewhat modified Kurtis, and bears the bodywork from the rail frame car in the pic above? Art
-
Dave, only if the tool was designed to get an alternative body, interior AND engine. It's not always possible to just slip this out, and than in, with an injection molding tool--seldom are such tools designed for that to happen. Couple that with new chrome tree tool, clear red for taillights, and likely it would be easier (and less costly) to just do an all new tool, going back to tooling mockups for such parts as may be common to both cars, if indeed those mockups are still around and usable (they may not be, may not have survived the original toolmaking processes (that happens a lot too). Art
-
One of the common misconceptions about using diecast tooling to produce styrene kits is that it should automatically work, but that's generally not the case. Where a styrene body shell, particularly with the styrene blends used today, will flex and bend enough to be ejected off the core mold forming the inner body shell surfaces, diecast (Zamak) does not do that (flex Zamak, it says "flexed" or in other words, bent and misshapen, may well even crack or split). So, diecast model car bodies get very straight-sided inner shapes, with a good bit of "draft angle" in order for the body shell to slide easily off that inner core mold. Increasing the thickness of styrene or any other thermoplastic can, and will, increase the noticeable shrinkage upon cooling (remember, styrene is heated so that it is a thick, pancake syrup like liquid for injection molding), which is what can make those nasty shrink marks in a body shell for which the tooling was done years ago, with harder, more brittle styrene blends no longer in use today. To see a plastic model kit body done in styrene but from a diecast tool, one need only look at Revell Monogram's 1/24 scale '48 MGTC, Jaguar XK-120, '53 Corvette or '56 Thunderbird. Those kits all started out as plastic models with diecast Zamak bodies back in 1978-79. All were fairly slabsided bodies, with few truly thick areas, although I've marveled that the Corvette, with its severe undercuts at front and rear, didn't seem to have that much in the way of sink marks (at least on the one I have). By comparison, the undercuts at the front of the Johnny Lightning 1/24 scale '51 Studebaker Commander Starlight (which I was in charge of product development, BTW) make for a "nose" that is literally almost 3/4 inch thick, and I simply cannot imagine the sink mark nightmares shooting that one in styrene would bring about. Then there is the issue of door and body panel lines. Those are made by tooling a body shell mold with raised ridges on the inside of the tooling slide cores, to make that recessed panel line we modelers like to see. Now in a mold engineered for styrene, those can be made seemingly as fine as a human hair, and they will show up in the final product. However with the far higher heat of diecasting Zamak, those ridges have a minimum dimension requirement, in order that the steel (while hardened) doesn't just burn away over time, which it eventually will. For that reason, diecast tooling has a far more limited life than any tools cut for molding styrene, measured often in hundreds of thousands of castings, as opposed to literally millions in the case of at least a few styrene plastic kits. With that in mind, the raised ridges to make door and body panel lines in a tooling made for a diecast have to be far heavier, making for overscale door lines, panel lines and the like. Revell Monogram has a tradition of going for the highest in scale appearance (I know, there have been serious criticisms of some of their releases over the years), and if they feel that a particular diecast tool, once shot in styrene, doesn't meet up with their expectations of what a decent plastic model kit should look like, who are we to argue? Not me. Art
-
I already mentioned several possible engines. In addition, there were a lot of variations on tires over the years, the neatest dirt track tires having been the earliest ones used: Ward's Riverside Knobbies. They did use steel wheels early on, then Halibrand came up with several varieties of magnesium alloy wheels. Firestone was pretty much the only tire supplier until Goodyear got into racing tires in a big way in the 60's, but Firestone still seemed to dominate. There was at least one Midget which used a supercharged, 75cid Offy in the 50's, the blower having been taken from a Bugatti Type 35B. Bob Higman, the most prolific midget chief mechanic of the 50's and 60's (also a car owner in his own right) built up a pair of turbocharged 75cid Offies in the early 70's, Larry Rice (later of the "Thunder" racing series on ESPN, drove a Kurtis clone with one of those to an all-time one lap record at Trenton International Speedway, in Trenton NJ. One Kurtis midget was fitted with a large, squarish fairing in place of the tail cone, to provide a windbreak for a World Land Speed Record bicycle run in the 1950's. Bob Peck, out of Chicago created a low nose with a smaller horizontal grille in the late 1950's, which a lot of Offy midget owners installed (this is the nose that is on the Monogram 1/24 scale Kurtis Midget slot car body/static shelf model kit). And of course, there were many car owners who made up their own nerf bars for the front, and for the sides, and those were as varied as the paint schemes and graphics. Many of them had the owner's initial welded into the front bars as well. Art
-
Also, the wheels look pretty large for a midget, as nearly every sanctioning body specified 12" diameter rims, about the only ones that size being from Crosleys. While Frank Kurtis built the vast majority of midgets in their heyday (when it was possible to watch midgets racing literally 7 nights and days a week!), there were others who also built some chassis, from one-offs, to perhaps a half dozen or so. Art
-
Doesn't look like any Kurtis midget I ever saw, for starters. Also, while of course early midgets did use stock Model A Ford rear ends, by the time of tube frames, quick change was where it was at in that department. Also interesting is the use of welded up steel wheels, instead of alloys. Art
-
Can anyone explain.........
Art Anderson replied to Pete J.'s topic in General Automotive Talk (Trucks and Cars)
Pete, Have you considered that in Europe, certainly post-WWII, the various national economies were dead flat on their backs? With very little in the way of petroleum deposits in Western Europe, gasoline could be in short supply, and expensive when you found it, according to friends and family who spent any serious time on the continent. While yeah, the luxury or high performance carmakers did make cars that were literally palettes for some of the finest, most daring of stylists; the vast majority of cars produced there for decades were not only tiny in comparison to what we Americans had at our disposal, they were much more focused on being affordable basic transportation. 10-12 feet of Volkswagen, Citroen 2CV, Renault's, Fiats, DKW's, and the like simply did not allow for the swoopy sculptured styling that the upper crust of European Society could afford, nor did they do much for any but the most eccentric of American buyers either. Tailfins on a British or European subcompact looked like, well mere nubbins. Long, low and wide styling as practiced in the US for about 30 years looks both short and stubby, the cars would come out narrow and tall, by comparison. The Renault Dauphine, if one looked beyond its quirks and it's serious mechanical failures, was at least a very neat looking little car in 1959. Fiat's 1964 1100D 4dr sedans were just neat as heck, while being one of the cars that drove US owners AWAY from Fiat for evermore (they were simply junk underneath). It's with sports cars that European and British makes excelled quite well in the styling department. While their forms followed functions very closely, they were at least serious attempts at being "flagship" designs for their respective makers. When the Detroit Big Three were forced to make compact cars, then subcompacts, they too looked short, stubby, tall and narrow in many cases. Some were just plain ugly upon later reflection as well. Most of them had their quirky periods as well. It just took time, stylists working hard (often with very tightly limited budgets) before they began to get some pizazz into such small packages. Art -
Paint Mixing Bottles
Art Anderson replied to Dave Ambrose's topic in General Automotive Talk (Trucks and Cars)
Those little plastic film containers are not affected by lacquer thinners or solvents, in my experience. Art -
Mark, As an AVID Indy car modeler for 19yrs (1966-85), I can offer this observation: If there is one constant about Indy cars since the late 1960's, it's that NOTHING is constant with them. Where before, the roadster was the roadster, only a few things got shuffled around on the cars from race to race, by the 1980's, major race teams had a stable full of cars, cars for Indianapolis, cars for shorter ovals, cars for road courses. While they all might have looked, at first glance, to be the same, each one was different--different wings, different suspensions, and often different markings. As such, while Revell-Monogram, and AMT/Ertl as well, liked to capitalize on the notion that "this is the Indianapolis Car", the truth was simply that by the time their people got to it, the car almost always had changed. That was simply due to the time lag, lead-times if you will, that exist in the world of plastic model companies. This is even true if one looks closely at several of the cars on display at the Indianapolis Motor Speedway's Hall of Fame Museum. Perhaps the most correct car in the place is Foyt's 1964 Sheraton Thompson Offy roadster. That car is exactly as it appeared at the finish of the Bobby Ball Memorial race at Phoenix Intl Raceway that October: It is very much as it raced at the Speedway in May, only a few fittings differ. Mario Andretti's 1969 Brawner Hawk was a backup short-track car--the REAL '69 STP Hawk resides in the Smithsonian. Foyt's 1961 winner is a restoration using a few parts borrowed from other cars in the Bowes Seal Fast stable in that era, the hood panels being from 1962 (no air scoop in the hood in 1961--I was there, saw that car run all day long, saw it up close and personal in Gasoline Alley after that race). The two restored 1968 Lotus 56 Turbines have some inaccuracies as well, notably the over-finishing of inner surfaces (raw aluminum in 1968, now painted grey), even the legendary 1967 STP #40 Turbine appears as it did in 1968 (it didn't run, but was at Indy), no airscoop on the top of the nose in '67. But, with the wide variety of wing designs used by even the mid-1970s from track to track, different nose cones, and later on, different side pods, even different ground effects undertrays, it's pretty hard for modelers, even model companies, to capture a particular car exactly as it appeared on a particular day, on a particular racetrack. It's just one of the handicaps that exist with such cars. Now of course, R-M did take some curious, but predictable shortcuts with those car kits, given that each was more or less predicted to be a "one hit wonder", given that modelers who are turned on by kits of them have pretty much only a rather narrow window of interest--by the time the kit comes out, it's already a year or more old in many cases, and "last year's racecar just isn't as commercially interesting as what TV and photographs are showing this year. Art
-
For starters, the Kurtis Kraft Midget was very likely the most prolific of all racecars, anywhere, any time, with somewhere between 500 and 700 built; KK produced them as complete cars, rolling chassis with body panels (for the buyer to install the engine of his choice), as kits (KK cut, bent and fishmouthed all the chassis tubing, supplied raw bodywork), and from Johnny Pawl of Crown Point IN who bought out the midget from Kurtis in the middle 1950's, offered them for sale well into the 1960's. There were 4 principal engines used in these midgets in their heyday (1947-about 1955): Of course, the Offenhauser, itself a miniature in many ways of the much larger 270 (Championship engine) and the 220cid (sprint car engine), the exception being that since it was such a small 4-cyl, only three main bearings. The engine began in 1935, with a request from Earl Gilmore (Gilmore Red Lion Gasoline) for a reliable engine for this then-new racing series gathering real steam in SoCal. Fred Offenhauser and Leo Goosen (Goosen was the ONLY American who earned a living virtually his entire life of nearly 90 years designing full-blown racing engines, from the late 'teens to the late 1970's) started with the idea of one cylinder block from a Miller 91 straight 8. At 45cid it was too small, so they worked up a new engine, basing it on that, but at 91cid as a 4-cylinder. Still though, it had the same style "barrel crankcase), was blind-bored (block was machined from a single casting, with no detachable cylinder head, DOHC with two valves per cylinder (the larger Offies pretty much all were 16 valve engines), and all the other little details that Goosen had worked up for both Miller and successor Offenhauser. The 1.5 liter Offy grew to 110cid by the late 1940's, finally allowed 120cid in the 1960's. While American Automobile Association's (AAA) Contest Board embraced the Offenhauser Midget Engine wholeheartedly (being the one "money no object" nationwide sanctioning body) several smaller, more regional midget racing organizations balked, citing the roughly $5000 pricetag (Hmmm, cost controls in racing back then?), most notably CRA (California Racing Assn), URA (United Racing Assn) in the East, and several in the Rocky Mountain states. Enter the 132cid Ford V8-60 flathead (originally designed for use in the Ford Popular built in the UK, introduced in the US as an "economy" engine in 1937, dropped midyear 1940 by Dearborn). It was perfect for postwar racing, given the tremendous interest in hotrodding that little V8. The V860 was actually faster on quarter and eighth mile tracks than most Offies, and occasionally gave the Offenhausers fits on even longer tracks, if it held together. For shorter tracks, the ELTO (Evinrude) outboard motor, with two cylinders ganged together, could outscream even the V8 60, with it's HUGE exhaust pipe (some 6" square) and 2-cycle scream letting fans know that it was in town. Another popular small engine was the Drake, produced by Dale Drake (the Drake of Meyer-Drake Engineering, producer of Offenhausers 1945-1979). Drakes were V-twins, made by producing water-cooled cylinders for the Harley Davidson "Knucklehead" '74'. But by the 60's, midget owners saw a need for something else to replace the aging V860 and the Drake. Enter the smaller of the two 6's introduced for the new Ford Falcon--those ran successfully for several years, but it was Sesco Engineering that finally broke the back of the Offy. Sesco simply sawed Chevrolet 283's in half, making a wicked inline slant 4 (they did a few, less successful V4's as well). Finally, in the late 1960's, Red Caruthers and others in SoCal added EMPI equipped VW flat fours to the scene, and shortly afterward, Caruthers and Bob Higman (among others) came out with their own, new midget chassis to finally replace 20-25 yr old Kurtis chassis, many with thousands of miles of hard racing on them. Some firsts for AAA Midgets (and Kurtis midgets in particular): The first serious use of aircraft-style fabricated tubular chassis construction; the first widespread use of disc brakes (from Crosleys), first racing cars to use Ted Halibrand's then new magnesium alloy wheels; and I believe they were where Stu Hilborn's fuel injection systems got their first sustained, real use, in racing. They also were built on an assembly line of sorts at KK, Frank Kurtis even having stamping dies made for the aluminum noses, hoods and tail sections. For decades, KK midgets never had a fuel pump (save for the injector pumps), rather relying on a hand-operated air pump to pressurize the fuel tank (on the left side of the bodywork), and relied on a hand lever to operate the hydraulic brakes. They all but pioneered the universal installation of the various quick change rear axle center sections as well, for quick rear end ratio changes at the track, and used several suspension methods: A few were equipped with 4 leaf springs, but early on, most were two spring (transverse front and rear), a few were built up with three springs, one front, two rear, but finally torsion bars found their way into midgets, before they became popular on Indy and dirt track cars. Early KK midgets used Model A Ford transmissions with V8 gears (just low and high gears), graduating eventually to single speed direct drive and an in-and-out dog clutch arrangement. Nearly every Indy car driver from 1950 until well into the 1970's cut their racing teeth in a Kurtis Midget, as well as World Champions Phil Hill, Jack Brabham (yeah, they raced midgets in Australia and New Zealand in summer down under (winter in the US), and Mario Andretti. Cool car subject from Revell--can't wait!!! Art
-
resin foams when sets
Art Anderson replied to Lownslow's topic in Car Aftermarket / Resin / 3D Printed
Low, The weather in Chicago isn't that much different than in my part of mid-north Indiana, and it's been humid enough here all summer long to make birds grow fins, scales and gills! What you describe is the result of moisture contamination of the polyol side of the urethane resin. That stuff is extremely hygroscopic, it soaks up moisture from the air, certainly when the container is opened, but to a lesser extent even through the polypropylene bottles it came packed in. Some have suggested using a vacuum chamber to draw out the C02 gas that is causing the foaming, but that almost never works. I've had limited success using pressure pots though, but even 75psi isn't enough to overcome severe moisture contamination. About the only solution is to get some fresh resin, and only that quantity that you will use in fairly short order. Art -
By and large, Hudson attracted the more affluent buyer, much as with Buick, Oldsmobile, Chrysler, DeSoto, even Packard Clippers and Lincolns of the first half of the 50's. However, the Hudson buyer tended to be, just as with Packard at the time, older, more conservative, and contrary to some advertising, not many people with young children. One had to look past the burgeoning V8 craze of the times in order to appreciate the fine road manners of Hudsons, coupled with their more-than adequate power from engines dating back longer than the legendary Ford flathead V8. The flathead 6's used in Hudsons (308cid in the Hornet, a slightly smaller flathead 6 in the slightly smaller, lesser Wasp) were almost legendary by the early 50's, having a characteristic not seen in any other carmakers offerings: Built in piston slap. Under hard acceleration and at high speeds (say in passing on those 2-lane blacktop roads of the time), those engines had the most purposeful yet powerful sounding "thumping" which meant that the pistons were moving (albeit in a controlled fashion) sideways in the cylinders, given the relatively loose setup, which was done on purpose. With horsepower ratings on the 7X Twin H-Power reaching past the 170hp mark, they were up there in a rarified league, only Cadillac and Chrysler's still-new Hemi approached that territory. Couple that engine with Hudson's step-down design, and careful suspension design, Hudsons were truly cars designed for the Interstate Highway System, before that was even a gleam in Dwight Eisenhower's eye, and equally at home on the racetrack. The only real problem with Hudson was, a relatively small dealership network, and an equally small company itself. They built perhaps the penultimate family touring sedans, but in doing so as built, far too costly to just restyle, even to build up an all new, more modern looking car after interest in late wartime streamlined styling had cooled off. Art
-
Just to clarify here: Hudson, from 1939 on, all the way to the end of Hudson production as an independent company, were unit bodies. Hudson called them "Monobilt" as in "built as if all one piece". Unlike today's unibodied cars which are built on a large stamped floor pan, a Hudson Monobilt car was built like steel railroad truss bridge, complete with steel beams in the A posts, roof sills, B-post, and C-pillar, all constructed on the fullest of full perimeter framing beneath the floor pan itself (all welded assembly). No frame members, save for a crossmember or so, was bolted into place, everything welded up as a unit. With Hudson, the rocker panels are those outboard frame rails, and you literally stepped over those, then down as the floor wells themselves are well below the tops of those side rails. Hence the term "Step Down". In a car with a body shell channeled down over a separate frame, you in essence step up to enter the car, ergonomically the opposite of the Hudsons of 1949-54. Hudson built those cars with a lower stance than all the others as well, but a couple of inches or so. Couple that with the engineering that was done in design, angling the engine/transmission downward to the rear, then using a two-piece driveshaft with U-joint in the middle, after which it angled up slightly to the rear axle gave those Hudsons an even lower floor, all but eliminating the driveshaft tunnel. This much lower floor meant a much-lower-than-other-cars seating position, resulting in a very low body height, making a stepdown several inches lower overall than any of its competitors. That translated into a radically lower center of gravity, making the cars much better handling than anything else coming out of Detroit. Art
-
Paint booth exhast
Art Anderson replied to slant6's topic in General Automotive Talk (Trucks and Cars)
Slant6 Best is not always the least expensive, especially where your safety, and that of your house is concerned. You are correct to be concerned about the potential of an explosion and fire here. A properly set up exhaust system for drawing paint fumes and overspray out of your basement should have an explosion-proof motor that is completely outside the airstream. The best type of blower to to that would be a small squirrel-cage unit, with the motor on one end, the airflow going through the squirrel cage completely away from, indeed blocked from even reaching the motor. The best explosion proof motors are sealed induction motors, which have no commutator or brushes to cause sparking. For example, motors that work like that in your electric drill, a Dremel tool, have brushes on a commutator, and if you look through the cooling vents in a dark room while one is running, you can see the blue flickering light of sparking. But, squirrel cage blowers aren't exactly cheap though, check suppliers such as Grainger for one that will work with 4" ductwork on both inlet and outlet, as that is what a dryer vent diameter is. Depending on the costs involved, your best bet might well be to just bite the bullet, buy a ready-made model spray booth--that would be a one-time buy, should last for years and years. Art -
Yup charlie! Dave and I have also conspired to dig out all the factory two-tone color combinations for both 1952 and 1953--those cars sure could get colorful in a hurry! Now, just for grins and giggles, why not do some research, figure out how to convert one of these puppies to a Commodore 8? Hmmmm? Art
-
Jeff, You make some very good points, but as with so many things, issues in either this hobby or in life itself, it's not always that a "one size fits all, broad paintbrush approach" truly fits. Without a doubt, there are all manner of goodies around the house, from Mom's (or your significant other's) sewing basket and the gadget drawer--I think I've been down just about every path in that woods (after 58 years of modelbuilding, I would hope so!). The use of superdetailing aftermarket parts, even those details created by one's own hands ought never be used to intimidate others, but rather to make one's builds speak for themselves. It's one thing to take a model to a show, and be justifiably proud to the point of wanting others to see it, but the line between that and purely boasting can be pretty thin, and only faintly gray. It's the latter that can turn others off, others who have yet to reach that high level of skills and artistic achievement. As for megabucks workbenches, I suspect mine qualifies (with a Sherline lathe and their vertical mill, a couple of airbrushes and numerous Dremels, and more hand tools than I care to count) but that is an accumulation of stuff gathered since the early 1960's. But, in the bottom line, I tend to show off my handiwork primarily to friends I know well, be they at a show I am attending, or online in places such as this. And yeah, with a project as involved as the Knox I am working on, I do wonder sometimes if my frequent in-progress pics don't turn some people off, so I tend to be pretty careful when I do let out pics, or put it on the primer table. Perhaps the worst thing a modeler can do, IMHO, is to assume that he/she can never achieve the level of so-called "supermodelers", so they don't even try. This hobby can be as much about pushing one's personal envelope in either great leaps forward, or tiny steps across the floor. But I do suspect that most builders who read pages like this one, do try to outdo their last project with each subsequent effort. Art