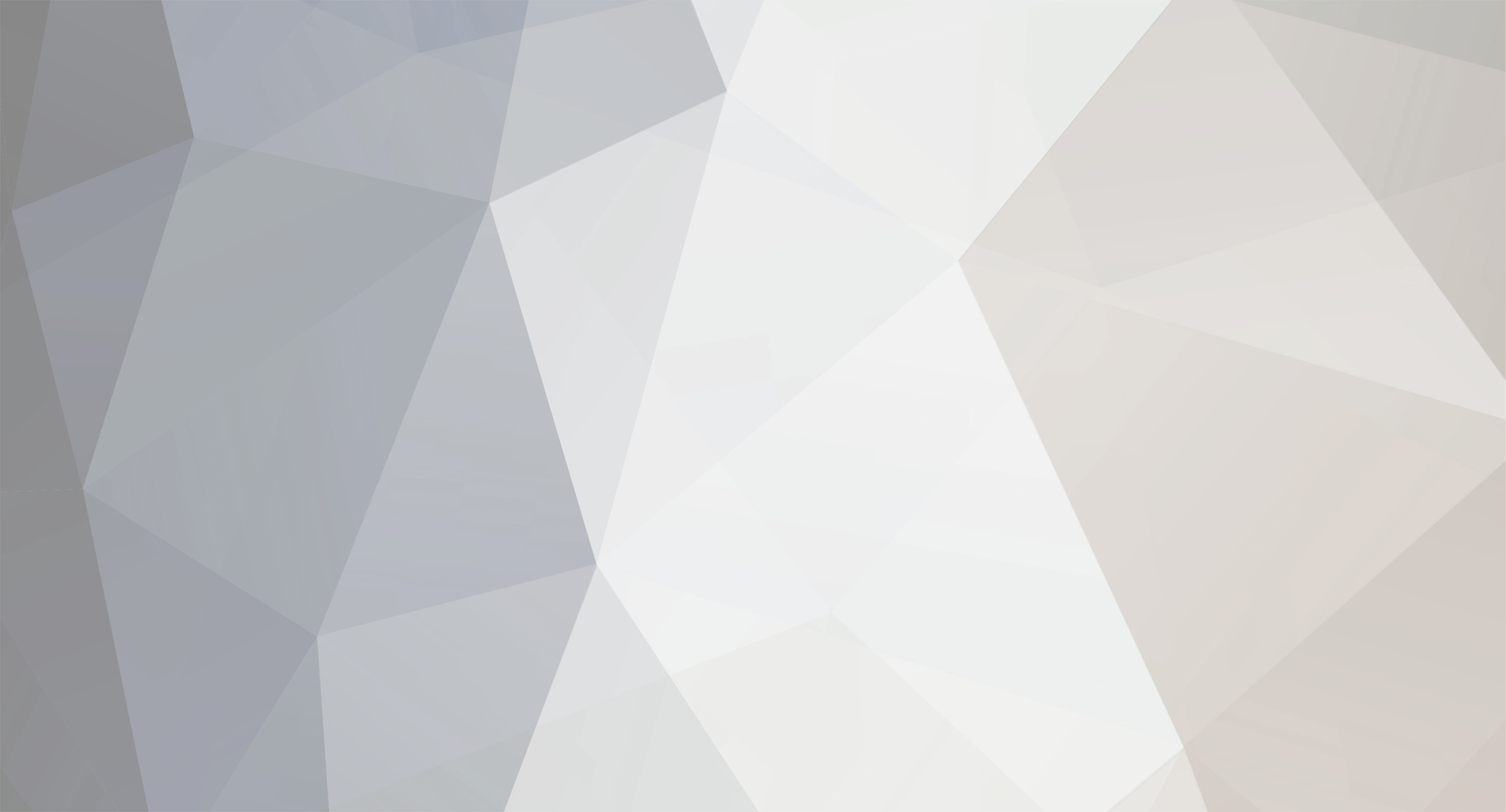
Art Anderson
Members-
Posts
5,052 -
Joined
-
Last visited
Content Type
Profiles
Forums
Events
Gallery
Everything posted by Art Anderson
-
Clarafacation I hope.
Art Anderson replied to DRG's topic in General Automotive Talk (Trucks and Cars)
Most all of us builders on this, and just about every other model car message board are, or at least were, rather average modelers at some point in time. For every newcomer in this hobby who seems to break out, explode on scene, there are dozens, if not hundreds who have't experienced that just yet. Teenager Jordan Romero, who before his 14th birthday had climbed 6 of the legendary 7 summits (the highest mountain on each continent) including Mt Everest while still a 13yr old, has an interesting challenge that he presents to any group he speaks to, be they kids, or adults of any age: Find your Everest, and climb it. For him, that has meant astounding accomplishment for one so young, but that challenge works no matter the pursuit, whatever a person's path through life might be--it even can apply to scale modeling in any subject area. That "climb" can be as gradual, or as stratospheric as one's imagination and dreams can make them. There's very little in this hobby that is "greek to me", or anyone else. One learned skill leads to another, then another,and still others over time. Even something as mundane as making an ill-fitting part fit can be the beginning of even simple kitbashing--trust me, the same skills will be needed. A simple conversion of a body shell from one style to another will plant seeds of the skills and knowledge needed to scratchbuild something, whatever that something might be. The use of aftermarket details or even a fairly complex transkit are merely quick paths to the goal of having something that one didn't have before, be that the look of realism, or something one never thought would be achievable. And face it, most of us don't have the requisite knowledge or perhaps the tools to make some of those details which are out there in anything from photoetched metal to cast resin parts or bodies. As for not having the wherewithal to gather expensive tools, or model kits bought for building someday out in the future, those things can have a tendency to come about in time--when perhaps one's priorities in other areas of life have been accomplished, whatever those might be. As for me, the things I work on today are the culmination of close to 60 years of building models--they didn't happen last week, or even within the last decade. But when I start on a project, no matter the delays that may happen for whatever reason(s), my motto is to "never give up". Art -
The Elusive 1904 Knox Waterless Truck project
Art Anderson replied to Art Anderson's topic in WIP: Model Cars
Almost everything there, Chuck, is done "by the numbers" on the handwheels of the mill. Pretty much this has been a matter of trusting the numbers along the way. Art I'll be at Classic Plastic, as will the Knox. I'll be at Classic Plastic, as will the Knox. -
The Elusive 1904 Knox Waterless Truck project
Art Anderson replied to Art Anderson's topic in WIP: Model Cars
OK, time for an update! Lots has happened since April 23, when this thread started. Engine is installed, as is the chain-drive driveline. But, the next two parts have been tons of fun! First the steering wheel. Now, I've never made a steering wheel before, never. But, I just hadda give this a try. So, where to start? Well, with some .016" thick K&S brass strip, an inch wide, that's where. With me so far? Now, there's nothing to cutting brass that thin, I've done it with heavy kitchen shears before, but this needed to be a bit more precise, and lots better looking at the end. So, off to the mill we go. But what to hold that piece of brass with? Presto! Dremel makes a mandril with a machine screw in the end, the one used for cutoff wheels. So, drill a 5/64" hole in the brass (that's the clearance diameter of the screw in the mandrel. Next, put screw through hole, thread into mandrel, tight it up. Worked too! Put mandrel in lathe chuck which was then mounted on a rotary milling table (crank-driven, each notch on the handwheel is one degree of a circle. Start the mill, nudge a side mill against the brass--oops! The dad-gummed thing just backed the screw out of its hole--scratch one piece of now screwed up brass. Make up another blank piece, but how to keep that from happening again? Why, a drop of gap-filling CA glue on the threads, thread into mandrel, tighten securely (and yes, the screw was still removable with a little bit of effort), and mill away. AFter cutting the brass into a perfect circle, exactly the diameter needed for a rim to be made, time to mill out the spokes. Now I know how to back the work away to one side of the side mill, to make spokes that are wide, but still centered on a perfect right angle, but I forgot to trust my mill, go by what the dials were telling me, made two attempts that came out with offset spokes, so for the third try, I decided I needed to use the dial only, trust that--and it worked. Next was the rim: The rim is 1/16" brass rod, annealed, and then formed by hand around a bar of aluminum which was the diameter chosen for the spoke unit--that rim scales out to a tiny bit over 1.5" in scale, which is about right for a brass era/horseless carriage era wood rimmed steering wheel. After trimming the cut ends very carefully, then touching those up with a flat needle file so the ends fit tightly together, a bit of silver solder to hold them, smooth out the joint was all it took. Then, put the spoke "spider" into the rim, and silver solder the joints. Done! (there will be a center nut that still has to be made, but that will happen once the steering column shaft is made) Now, for the steering column and throttle quadrant! This one took a lot more time, and figuring how to go about it. I actually started on the quadrant SIX times--each one ending in a lesson how not to make it! First couple of times, the side mill (.040") grabbed the work, ruined it, because I was making it out of too thin a stock. Then, when enlarging the center hole (for the steering column) I laid a nice second-degree burn on one finger--hey, brass does get that hot very quickly when you try holding it with bare fingers! The 6th try was done in .064" thick brass strip, but I made the arms at the ends of the arc just thin enough so when I started cutting the detents (those thingies that look like gear teeth), my little dental cutter got hold of that very thin section, made a nice golden little pretzel! Seventh try: This time, I marked out the arc (90-degrees, but not cut completely through. Now, I could cut detents in the arc, but without ruining the work. After doing this, I then retraced all the partially deep cuts with the end mill, until they were cut clear through. Also, I left a long tail, about an inch or so opposite the arc. This would make a perfect place to grip this part in a milling vise for enlarging the center hole, after which ( simply parted off the excess brass stock on that side of the part, It worked, and it made it possible to not only enlarge the hole, but I was able to use a 5/32 end mill to ensure a perfect slip fit of the finished quadrant onto the steering column. The last milling operation was to cut a 90-degree slot across the steering column, so that the throttle arm had a place to go there, and for ease in soldering it in place. The throttle lever is 1/16" brass rod, annealed, then flattened on its outer end, to make it slightly paddle-shaped. All that was needed then was to give it an elongated Zee bend, so that the lever goes under the quadrant at the hub, and on top of it at the arc. The detents were cut with a .030" diameter dental burr (Thanks Dr Misecko!). All done, soldered up: Comments? Art -
Life is good!!!!!! Yeah!! Art
-
More thoughts on the Kurtis midgets: While in the 50's, the diminuative 110cid Offy, Flathead V8-60, the Elto and the Drake stood in good stead--costs of buying an Offy were rising dramatically, and in the case of the other common engines, parts were becoming hard to get. By the early 1960's, the midget Offenhauser was nearly as expensive as its big brother, the mighty 255cid Championship Engine, the stuff of the legendary Indianapolis Roadsters. So, enter stock block production engines other than the little flathead Ford: For several years, the 170cid inline 6 developed for the Falcon was popular, did very well on the various circuits too. The little 4-banger Chevrolet developed for the baseline Chevy II got called upon, not nearly as successful as the Falcon 6. With EMPI, however, making ever more potent speed equipment for the VW flat four aircooled motor, it was only a matter of time before someone stuck one in a midget. I don't know for sure, but it may well have been "Red" Caruthers out of California who did the first one, to be driven by his rising star son, Jimmy--first in CRA (California Racing Association) moving over to USAC by 1969 or 1970. The VW "popcorn" engines ran with distinction and success throughout the 70's and into the 1980's, first in Kurtis midgets (so many of those were built, either by Kurtis or from kits supplied by Kurtis-Kraft, or built up from Kurtis plans, even copied off of existing Kurtis Midgets, that nobody seriously thought about anything new in a midget chassis until Caruthers in California and Bob Higman of Romney IN--just a few miles south of where I live--tried their hand at replacing aging Kurtis chassis. But, probably the most potent stock block based engine in Midgets was the Sesco Chevy. Those were 283's cut in half (two versions--as a V4, or inline 4--the latter being the left hand side of the cylinder block, but retaining the camshaft, timing gear and chain, and the entire crankcase--just covering over the resulting opening in the right side of the block where the right bank of cylinders was cut away). With Hilborn fuel injection, Sesco's were runners! On a further note, the first three Cosworth Vega engines to be let out of the factory were shipped to Bob Higman, who dropped one of them into a Kurtis midget, "Pancho" Carter driving it to more than a few track records. The Cosworth was so strong, that when the car got really low rear end gears for short tracks, Carter could actually do wheelies coming off the turns onto the straights. So, lotta possibilities for someone in the aftermarket to come up with even more engines! Art
-
Uh-yup!!! Cannot wait to get my mitts on a few of the Kurtis Midgets--finally, after more than 50yrs waiting, an ACCURATE KK Midget that isn't megabux resin (But that Etzel's Speed Classics resin midget kit was schweet!) There were enough of those built (nearly 700 all total) and literally several thousand paint schemes, sponsor logos/graphics--where to start? Art
-
Linberg kit releases
Art Anderson replied to jphillips1970's topic in Model Building Questions and Answers
Same kit as produced last by Testors & Union, and before that, IMC. It's always been buildable as a stock A-100 pickup, in addition to the LRW. Art -
Questions about these two AMT kits
Art Anderson replied to Car Crazy 81's topic in General Automotive Talk (Trucks and Cars)
AMT's '27 Model T Police Car shares virtually no parts with the AMT '25 T Roadster/Coupe kits. The '27 is a Touring Car, and while many parts look the same as in the '25, it is a completely different tool. The police car version of the AMT '27 T is the same as every other AMT '27 T, with the addition of clear plastic side curtains (to fit the raised top), plust a siren, red light, and a few small police-related bits and pieces. It saw just two releases, the first about 1966, where it was done up to cash in on the Gangbusters thing (MPC) , and the antique car kits taht Monogram was doing. Model King had a special run of the police car version produced about 7-8 years ago. Art -
59 Cadillac Question
Art Anderson replied to Tommy Kortman's topic in General Automotive Talk (Trucks and Cars)
Just the Eldorado Biarritz Convertible and the Eldorado Seville Sport Coupe (hardtop). There have been a number of resin conversion body kits done over the 18 years since Monogram first released the convertible though. Art -
As far as brands of styrene stock go, there really are only two out there in any general variety of sizes: Evergreen (pretty much the grandaddy of the field--a ton of sizes and shapes, been in business for better than 40 years), and Plastruct, who brought out their line of styrene strips,shapes and sheets about 10 yrs ago. (Be careful about Plastruct, as they still make their line of ABS shapes, not nearly as extensive, and ABS doesn't glue easily to styrene). A Google Search for both brands should turn up listings of every size and shape each company makes, so that's worth doing, printing off for easy reference. As for sizes, how high is up? I say that, because there are so many different dimensions, particularly thicknesses, that you will encounter over time. My best advice is: Get some sort of box (I have a couple of clear plastic boxes with hinged lids and long troughs in them which are perfect for keeping my stock of Evergreen handy at all times, and sorted out to some extent. Next thing, consider that Evergreen (in particular) isn't all that expensive, so if you order some from somewhere, I'd advise picking up complimenting dimensions of the stuff along with what you need at the time. Saves money on shipping, and eventually you will have a stash that will allow you to just jump right into a project regardless of the time of day or day or night of the week. As for measurements (sizes), Evergreen styrene comes in thicknesses (strips) all the way from .005" to .250", in both thickness and widths. Consider using metrics for measuring and figuring, particularly if you are working with a 1/25 scale project, as metric measure fits right in: One inch equals 25.4mm, and for our purposes, I'd drop the 4/10mm and go straight 25mm to the inch, just because you'll not likely be able to divide .4mm by 25 and be able to see it. So, 1mm can be said to be a 1/25 scale inch. If you prefer English (American) measuring, well that's easy too! .040" is one inch in 1/25 scale, and with both, even fractions of an inch in scale can be achieved. I suggest a digital calipers which you can get for not a lot of money, as that tool can give you readouts in both English and Metric. A good small pocket calculator will also help when you are figuring out just what size something should be. Others have mentioned glues so I won't, except to say that the only liquid cement at my bench is WeldOn #3 Art
-
1:1 Scale Modified Reissues
Art Anderson replied to Chuck Most's topic in General Automotive Talk (Trucks and Cars)
With the Graham Paige Hollywood/Hupp Skylark, those were highly modified underneath. Incorrectly represented by Monogram as a body-on-frame car, the Cord 810/812 was a true unit body, with one of the very first uses of a separate bolt-in front subframe which carried the engine and transaxle, the entire assembly being removable by unscrewing just 4 bolts, disconnecting the fuel line, exhaust pipes, and electrical system. The subframes telescope into the main frame "boxes" which on the Cord body, form the lower body sills (rocker panels). Upon receiving the body dies through a somewhat convoluted deal, Graham (who built the bodies and front subframes for Hupp, whose bank account was nearly empty) designed a new front subframe for rear-drive, and a new floor pan with transmission hump and driveshaft tunnel. This made for a shorter wheelbase and overall length, making it imperative for them to style a new front clip to fit as well. Contrary to popular opinion, the Hollywood/Skylark does not ride appreciably higher than the front-drive Cord, as there was sufficient room underneath for a driveshaft, and of course, a rear axle with differential. Graham-Paige produced all the bodies and front subframes for both cars, which carried exactly the same styling, the only differences being in the interior (dash and upholstery patterns) and of course badges and scripts. While the Graham-Paige Hollywood carried a fully chrome-plated grille up front, Hupp (quite probably for cost reasons) painted those otherwise diecast parts body color. What killed the cars for Graham-Paige and Hupp was the same thing that killed it for Cord--it was almost prohibitively expensive to build. Cord Corporation lacked the capital to purchase, install and create a die for a one-piece roof stamping for the Cord 810, and neither subsequent manufacturer was in any better shape financially (although they both had stamped out "turret" or one-piece roofs). So, just as with Cord, this meant that the roof had to be assembled on a jig from 11 separate smaller stampings, welded up, seams leaded and ground down smooth--very labor intensive, slow and expensive. When Auburn Automobile Company (maker of Cords) closed and liquidated, one Dallas Winslow of Detroit bought the factory buildings in Auburn, along with all remaining parts stock (Winslow's company was famous for doing this with failed carmakers from the 20's and 20's, and did likewise when Hupp, then Graham-Paige exited the automaking business by early-midyear 1941. All the remaining sheet metal parts were stored in buildings not far from the former Auburn Administration Building in Auburn IN (now the ACD Museum), and for at least a couple of decades, that stock provided NOS sheet metal for all three versions under restoration. Art -
Considering that Hudson, unlike the rest of the auto industry from the late 30's onward, made no convertibles from the ground up, choosing instead to take coupes off the production line, move them to a separate area for final work, literally cutting the roofs off of the coupes and installing the top mechanism for a convertible top, plus a different, distinct interior, along with window sill trim, it's not at all likely that their convertibles had any extra bracing either underneath or inside the body shell--after all, "Monobilt" unibody construction, as Hudson practiced it, made the common reinforcement of an otherwise closed body pretty much unnecessary. As an example, the very reason for the abnormally large (compared to competitors' convertibles) windshield header was that on a Hudson body, that was a MAJOR structural member. The underbody reinforcements on the convertible are the same as for the coupes and sedans, part of the unit body "Monobilt" construction, not separate frame members. They include a full perimeter frame, that on the real car, actually goes OUTSIDE the rear wheels, just above the rear wheel arch, plus a ton of other subframe members underneath, and beaucoup beams and such under the skin. With all that, the convertible was almost as rigid as the coupe it was cut down from, no further reinforcements needed. Art
-
1:1 Scale Modified Reissues
Art Anderson replied to Chuck Most's topic in General Automotive Talk (Trucks and Cars)
I stand corrected, although there sure is a commonality of shape and character lines in a lot of those cars. Art -
1950 or 1951 Chevy
Art Anderson replied to iBorg's topic in General Automotive Talk (Trucks and Cars)
Shows what little I know about who makes what anymore!!!!! Oh well! Art -
Packaging for mailing
Art Anderson replied to Greg Myers's topic in General Automotive Talk (Trucks and Cars)
You were EXTREMELY lucky! Lucky that the kit wasn't just mashed flat. Bear in mind that USPS, if the package is small enough, they will stuff it in a canvas mailbag along with other packages, and then toss that canvas bag into the back of a truck for shipping, along with other bags of mail--what if an anvil had been in the bag that landed on top of the one your kit was in? Another thing, while they will still accept packages wrapped in Kraft paper, the USPS would really rather you didn't--that worked 50-60 years ago, but with modern sorting equipment, it's very likely that the paper will be torn, and the address either munged beyond reading, or gone forever (UPS, and I believe FEDEX as well, refuse packages wrapped thus). Seriously though, take a tip from the kit manufacturers and hobby wholesale houses--they always pack products in sturdy corrugated boxes, and if the kit is loose in that box, they put plenty of packing around the kit, between it and the box. Just my thoughts, having sent literally thousands of parcels all over the US, indeed to just about every continent on the planet over the past 25 years or so. Art -
1:1 Scale Modified Reissues
Art Anderson replied to Chuck Most's topic in General Automotive Talk (Trucks and Cars)
Not only that, but shared sheet metal stampings as well: 79-92 Mustang, the last of the square Birds, 83-88 Thunderbird & Cougar, Lincoln Continental Mk VII all have the same windshields, cowlings, and door skins. Fairmont and Zephyr door skins are extremely close, if not the same also. Ford was most definitely into "modular" car construction in those years it seems. Art -
1:1 Scale Modified Reissues
Art Anderson replied to Chuck Most's topic in General Automotive Talk (Trucks and Cars)
Sounds implausible to me, frankly, as any comparison you do between the two era's of Jeepsters will show you that the only shared styling feature was the trademark Jeep 7-slot grille concept and that's it. 1948 Willys Jeepster: http://www.team-bhp.com/forum/attachments/vintage-cars-classics-india/27788d1215665020-rust-pieces-pics-disintegrating-classic-vintage-cars-1948-willys-jeepster-cabriolet-462-vj2.jpg 1967 Kaiser Jeepster: http://cgoodwin.com/JeepsterCommando/images/Photos/IMG_1630.jpg The differences are VAST, and easily seen. Art -
1950 or 1951 Chevy
Art Anderson replied to iBorg's topic in General Automotive Talk (Trucks and Cars)
Wagonrod would not be the correct body for that model--it's a prewar Chevy turned into a custom woody wagon. All is not lost however! Revell has produced tons of their '53-54 Chevy sedan delivery kits over the years, and they shouldn't bring much money at all on the secondary market. With the end of true Woodie station wagons at Chevrolet in midyear 1949, Chevrolet went to steel body for station wagons, and used that same shell for sedan deliveries, simply stamping out new quarter panels having no rear doors (their steel station wagon bodies 1950-54 were available as 4dr only) and using the shorter front door of the 4dr sedan and station wagon. That door is for all intents and purposes 6" shorter front-to-back than the 2dr doors in any of the AMT '51 Chevy kits (suggest you use the AMT/Ertl '51 Chevy Fleetline fastback for the front of the body forward of the B-posts, but cut away the Fleetline roof to the header over the windshield. Then simply graft in the Revell Sedan Delivery body which will work for this project, as Chevy's wagon/sedel bodies were identical in shapes and dimensions '50-54, but you will have some bodywork to do to blend in the Revell body with the AMT rear fenders, but that should be no biggie. Then, simply cut out the side (quarter) windows to the same shapes as the real car, and add in all the fake wood framing (the real Chevy steel station wagon body of those years had the sheet metal on the body sides, AND the tailgate, stamped with a tradional wood-framing motif, just as you see in the pics of the car you want to model. Should be fairly straight-forward to do, but certainly not a add-the-glue and shake-the-box proposition--but if you set that goal, then break it down into small parts, and persist, never giving up, you could have one awesome model! Art -
1:1 Scale Modified Reissues
Art Anderson replied to Chuck Most's topic in General Automotive Talk (Trucks and Cars)
Jeepster a modified reissue? Hardly. The first go-round of the Willys Jeepster was built on the Jeep station wagon chassis, just had a sporty phaeton body (in fact, the last true phaeton produced in the US) instead of the upright boxy station wagon body shell. It lasted just 5 years, 1948-53, while it's upright brother station wagon hung around until the early 1960's. The second Jeepster came in 1969, done off the long-running CJ-5/6 chassis, with modified CJ-5 styling and sheetmetal. Two completely different cars, with different starting points, only the name stayed the same. Art -
Trendy kits = goodby original
Art Anderson replied to Greg Myers's topic in General Automotive Talk (Trucks and Cars)
Hindsight is always perfect 20/20 vision. Of course, knowing what WE know today, and what model companies know today as well, nobody today is likely to irretrievably modify an existing model kit tool into another version, unless of course that original version was an absolute sales dog (case in point, the Revell-Monogram '92 Chevy Caprice, which never sold at all well until the tooling was modified into the 1995 Impala SS). But, back in the 1960's, very few of us could ever have imagined the day when there would be any interest in "last year's Annual 3in1 kits". We were most of us just kids back then--as say 15yr olds, very few of us could really imagine ourselves being even 25yr olds, let alone life in our 50's or 60's, and our hobby was very much dominated by our age group (Boomers!). Model companies recognized that fact back then as well, and so as tooling dollars got scarcer, and subject matter seemed to get harder to find that "killer" idea from, it was pretty natural to think about modifying old unused tooling that was just taking up expensive warehouse space. Why not make Saturday Night stockers out of some '65-'66 Annuals in 1968-69? AMT wasn't gonna be able to just squeeze out more of the originals, get any serious sales numbers out of them back then. And for sure, model companies weren't in the business of creating "Smithsonian Institution" type collections of 3000lb steel mold blocks, nor should they have been expected to. Geez, even the Big Three automakers scrapped old body tooling after they'd made up a sufficient stock of crash parts to last for say, 3-4 years or so after the real car was discontinued for the next year's model. Even today, if given the choice, most modelers do like their 60's subjects done from new, 1990's and 2000's "state-of-the-art" tooling. Remember back, about 10-11 yrs ago, when AMT/Ertl reissued their very nice '62 Buick Electra 225 Hardtop 3in1 kit? Yeah, we older guys that we'd died and gone to Heaven, but what about younger builders, who had no memory of kits tooled the way they were, in 1962 (where were YOU in '62? Huh?)? Builders then in their 20's and 30's dissed that Buick to death practically--it was "rude, crude and socially unacceptable" to produce a model car kit with the chassis as a plastic plate, with molded on details (Oh, the humanity!!), in short, younger builders seem to have thought of that one as a ripoff, not realizing that it was then a roughly 35-40 year old product. Time has a way of making us all stop to consider what we might do with stuff we buy, after all, "collectibility" has been a watchword in our hobby since its big resurgence in the early-mid 1980's, as it is with so many other toy and hobby products. But, in the late 1960's, indeed through most of the 1970's, that was not a driving force in this hobby, and model companies did what they did, in order to maximize their revenues and profits--be glad they did, otherwise it's likely that much of that old tooling would have been melted down into raw steel for other things. Art -
Scratchbuilding vs. Kitbashing
Art Anderson replied to Harry P.'s topic in General Automotive Talk (Trucks and Cars)
With the exception of the wheels (sourced from Grandt Line, and modified by me) every part of the 1904 Knox Waterless Truck I am building is made from raw metal stock (brass strip, angles, square tubing) and both aluminum and brass bar stock turned on my lathe, or shaped on my vertical mill. When it is done, you better believe I will say it is "scratchbuilt" with the added disclaimer that certain parts (identified in the description) will have been modified production parts. That I believe would be the most truthful description possible. Now, to describe my 1959 Chevy Biscayne 2dr Sedan, I would say that it's a resin piece, cast from a kitbashed body shell (Monogram '59 Impala Convertible, AMT '59 El Camino and a JoHan '59 Cadillac Fleetwood 60 Special 6-window sedan), which is again an accurate description of the car. If I had simply built up the body shell into the completed model rather than casting it, the proper description would have been "kit-bashed" as I "bashed" body panels & parts together that came from several different sources (existing kits). Art -
Scratchbuilding vs. Kitbashing
Art Anderson replied to Harry P.'s topic in General Automotive Talk (Trucks and Cars)
Highway, Technically, your project is "modified" from kit parts, with some raw materials used, added to get the final result. While this did involve some techniques used in scratchbuilding from the same basic materials (styrene plastic, putty and so on) it really wasn't done from scratch (meaning primarily from raw sheet and strip styrene in this case) so "scratchbuilt" doesn't quite describe it, nor does it do your fine work justice either. A lot of the terminology here comes from scale modeling hobbies that predate our Model Car hobby--principally model railroading, where scratchbuilding was the norm rather than the exception 60-80 yrs ago, until kits for buildings, bridges and rolling stock became widely used by the middle 1950's. The same is true of the flying model aircraft hobby--it started as a scratchbiulding hobby, very few flying model airplane kits were produced until after WW-II, those early fliers did their thing with a set of plans, a pile of sticks of balsa, some sheets of tissue paper, glue and dope. It's pretty hard, I suspect, for modelers much under the age of say, 40, to remember a time when scratchbuilding scale models was common--that sort of faded out pretty much as a major way of doing things by the end of the 1960's, although it never did quite die out, and is pretty strong today. Now, "kitbashing" is something we older car modelers should remember very well! Back in the 60's, when so many of us were teenaged modelers, we took bits and pieces from this kit, that kit, and the one over there, and created our own rods, customs and dragsters (even a few roundy-rounders!). That was kitbashing, even though we didn't know it as that quite yet. Hope this helps! Art -
Skip-- I believe the Tom Mix Cord is painted "Cigarette Cream" which was a popular Cord color. In 1993, at the behest of the late Bill Harrison of Monta Vista CA (Bill was model car kit collector personified!), I completely reworked a terribly inaccurate Cord 810 sedan body into two versions--Non-supercharged Westchester Sedan, and a supercharged Westchester trunkback sedan. In 1994, due to a vitriolic letter from Guido Fieuw of SA, I completely corrected every "error" in those bodies (and there were many!!!), as I had started with one of his early efforts which was completely unusable (made from fiberglas, thicker than battleship armor in places, paper thin in others, rougher'n a cob all over), and then supplemented those two with the Convertible Coupe a/k/a The Sportsman (the same Cord body style that AMT did in 1/12). Along with the late Lee Baker (out of Chattanooga TN, now deceased) we teamed up to research the Cord 810 color palette for Dave Dodge of MCW Automotive Finishes (interesting work, as Cord used paint vendors now long gone, and called out tinting colors known then by names that don't correspond with anything DuPont or PPG-Ditzler), and Dave managed to come up with most of them in very close factory matches (I believe Dave can still mix those colors for anyone interested, but they do come at a higher price than his normally stocked colors. One of the highlights of working up the Cord sedans was being introduced by Bill Harrison (who seemed to know EVERY Classic Car personality on the West Coast!) to Josh Malks, who met Lee and I at NNL West in 1994, driving his iconic metallic silver-grey World traveling '36 Cord Westchester (that car has been all over Europe and the UK, even driven on a rally from London to Tel Aviv, and dozens of round-trips from California to Auburn every Labor Day weekend) at the Santa Clara Convention Center, where Lee and I measured and photographed a ton of details, and which gave me the references for the parts to do the non-supercharged Lycoming V8. Then, Josh hustled Lee and I into the car, for a FAST ride down the 101 Freeway--about 25 miles or so--that thing had the acceleration of most modern cars! An Italian customer of mine (AAM) sent me several color pics (Packed away at the moment) of the AAM '37 Cord flatback sedan he built, and detailed with sterling silver wire laid on the edges of the grille louvers--have some of that wire, just haven't gotten up the courage to try that yet (one of these days!). Art