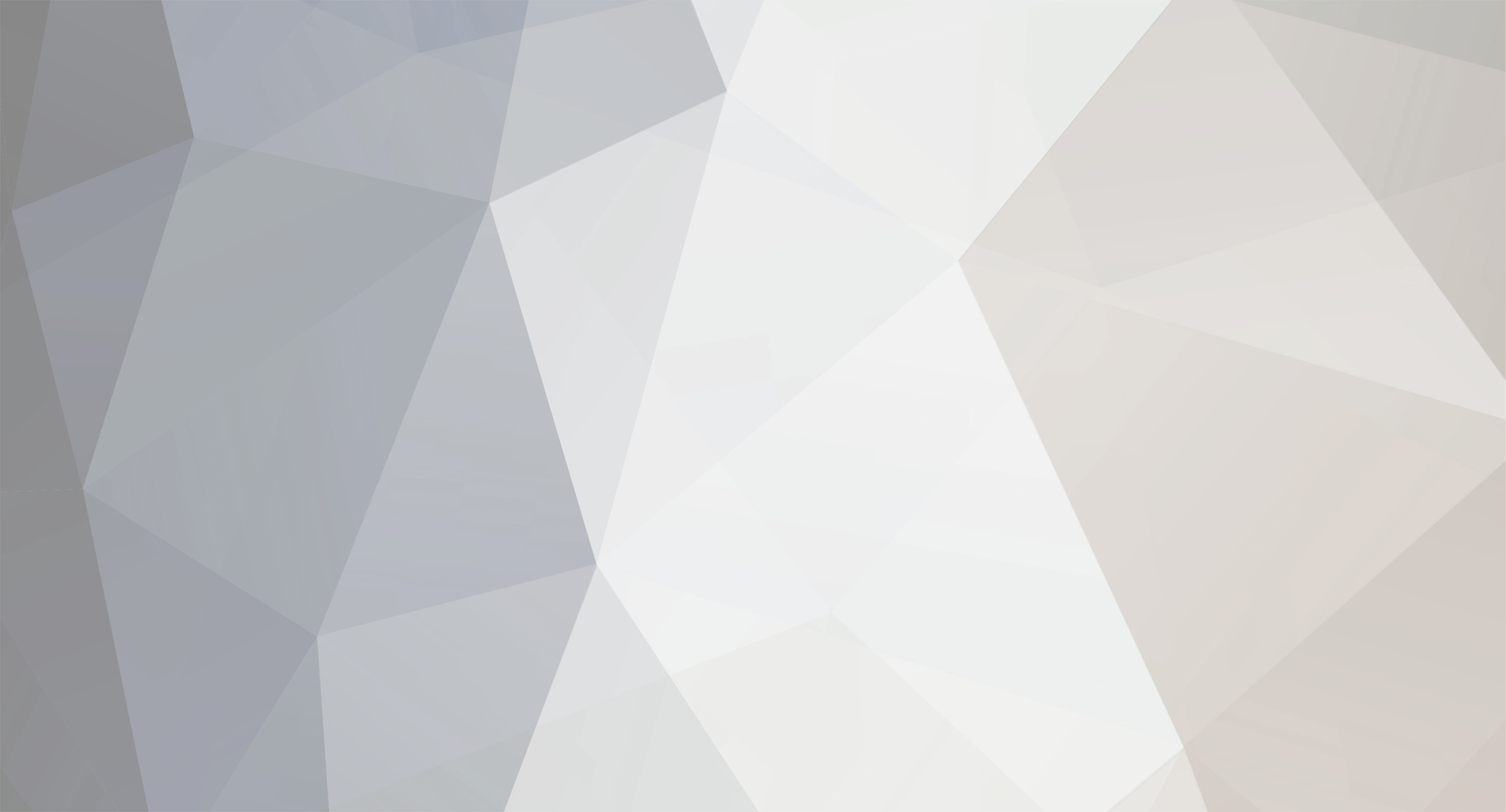
Art Anderson
Members-
Posts
5,052 -
Joined
-
Last visited
Content Type
Profiles
Forums
Events
Gallery
Everything posted by Art Anderson
-
what you guys use to glue a model
Art Anderson replied to Pierre_tec's topic in Model Building Questions and Answers
BSI also makes a line of applicator tips for their CA (also fit Goldberg Jet series CA bottles) bottles. They're polyethylene plastic, to which CA absolutely will not stick--if I find the end of their needle-point plastic applicator tips clogged, generally I can clear the tip with my fingernails. Art -
Help! Sticky rubber from alclad painted wheels.
Art Anderson replied to Stray's topic in Model Building Questions and Answers
Perhaps the only way to stop this would be to lay a "band" of BMF around the circumference of the rim itself--any plasticizer that might leach out of the tires won't penetrate that. Or, wipe a very thin layer of epoxy around the circumference/mating surface of the wheels before mounting the tires. Both of those techniques have been used for a long time on plated wheel rims, which can suffer from the same problem. Art -
Help! Sticky rubber from alclad painted wheels.
Art Anderson replied to Stray's topic in Model Building Questions and Answers
Most tires in model car kits, save for those from Japan (where Neoprene rubber seems to be the norm) are made from PVC--vinyl. With PVC, in order to make that plastic (which chemical formula goes all the way back to the 1890's) soft, a plasticizer is added to it. Trouble is, that plasticizer also will soften most any enamel, even lacquer based paints. Years ago, before model companies found that minimal plasticizer would greatly reduce, if not eliminate altogether, that softening effect, model car kit tires would actually soften the surfaces of styrene wheels (or any other styrene part they came in contact with for any length of time)--the once-dreaded "Revell Tire Disease". Art -
fish eyes in hood, need help (pics)
Art Anderson replied to iahawk's topic in Model Building Questions and Answers
Or household dust/lint; especially if you or your wife is fond of Johnson's Pledge furniture polish. Pledge furniture polish is loaded with silicones in order to give a shine--but those same silicones are the absolute enemy of paint jobs. A good vacuuming of your work area, perhaps closing the door to it when you spray might help as well. Art -
Harry, not all promo's of 50-60 years ago were "molded in the same color". While it was true, as a general rule, that body shells and interiors tended to be shot in the same color of plastic (first Tenite--acetate plastic--and after about 1962 or so, in Cycolac--ABS--the concept of "spray masking" for two-tone color schemes on body shells was well underway by about 1955 or so. Of course, to create parts of a promo to be molded in different colors of plastic, that requires the various component parts to be molded in tooling separate from any parts that need to be molded in a different color of plastic. There are two characteristics of promotional models that stand out to me nowadays (whenever we see the now-rather-rarely-done promotional model car: The use of two sets of molds to create the parts (and sometimes three!). Almost always nowadays, it seems that at least the chassis of a promo will be molded in black, the interior may be black, but a few promo's have been done with interiors in a color other than the black of the chassis, or the body color. The other change (I see it as an advancement) is the use of "pad printing" (Tampo printing if you will) to add small details such as scripts and badges, which often are multicolored, just as with their real counterparts; and "spray masking" which is used to create detail colors on surfaces which cannot be printed. On this Vette promo, all the vents, black window borders, and the taillight details were spray masked. That's a process which uses thin metal (usually hardened copper sheet), which is formed by hand to the body contour, very carefully, in order to get a tight "mask" against the model's material surface, then carefully cut out to expose just the area(s) to be sprayed a detail or secondary color (this is what was used, most likely, on 2-toned promo model car bodies back years ago!). The spray masks, once formed, and cut out to shape, are then hardened, and fitted into frames that can be inserted into machines so that a worker can simply hold the model body shell up against that mask, step on a pedal, which causes the machine to shoot a fast, timed shot of spray paint onto the exposed area within the mask. This sort of step may be repeated as many times as required to get the wanted detail colors. The taillights of this Corvette promo were done that way--a spray mask for the flat black bezel, and second one for the red taillight lens color. Spray masking is how multi-colored diecast toy and model cars have been 2-toned for decades, going all the way back to Matchbox, Corgi, Dinky and other toys, all the way out to all those modern-day high end diecasts of the 80's forward. I had to deal with that when I was in product development for Johnny Lightning 2002-early 2005. Art
-
1/25 Revell Ford Del Rio Ranch Wagon 2'n'1
Art Anderson replied to Matt T.'s topic in Car Kit News & Reviews
No matter how satisfactory any model kit is to one segment of the model building community, there will always be at least someone who's not happy with it--and it need not be the same person all the time, nor the same model kit mfr. 50+ years in and around the industry, and 63 years of model car building have taught me at least that much, Art -
Just a note on "Accelerators" for CA glues here: There are accelerators, and there are accelerators, and not all of them were born equal. Some of them will damage styrene plastic, due to their being made from chemical solvents that will attack and fog/craze polystyrene model car parts. HOWEVER, there is one accelerator that absolutely does not do that: "Insta-Set" from Bob Smith Industries (BSI) is an accelerator that comes in a brown plastic pump-spray bottle, and in my 30 years of experience with this accelerator, have NEVER had it damage plastic, nor any paint or decals on any model car on which I've used it. BSI Insta-Set also, in my experience, absolutely prevents any of the outgassing of CA glues from "fogging" the surface around the glue joint--the the point that I use gap-filling CA glue with this accelerator for attaching ALL chrome and clear parts, including headlight lenses--always successful with this. Insta-Set is sold in many hobby shops, particularly those with a well-stocked RC department, BSI putting a small silver label on the bottle carrying the name of the hobby shop. It's also available from Tower Hobbies. Highly recommended! Art
-
As the "framing" trim was hard maple, that is a very fine, close-grained wood, and once sanded and varnished, you really can't feel the grain with your bare hands (unless the body is weathered quite a bit). I did the "wood grain" effect on my Mercury build with paint. I started with an airbrushed coat of Testors #1141 Wood Tan, then "wiped" with "burnt sienna" artist's oil paint darkened slightly with a small drop of "raw umber"; using eye shadow foam applicators from Walgreen's cosmetics department. Once all of that was dry (artist's oil paints take several days to dry), I added the kit decals for the mahogany plywood paneling, then brushed a coat of Tamiya Clear Yellow over all the woodwork. This is how it came out, looks very much like a fairly new Mercury woodie that's seen a summer's worth of sun:
-
This kit was one of the first three kits that Revell did, as "state of the art" model car kits. I first saw those, as advance sales, at a Revell booth at the 1962 NHRA Custom Car Show at the Murat Shrine Temple in Indianapolis, over Labor Day Weekend in 1962 (held in conjunction with the 1962 National Drags at Indianapolis Raceway Park).' It is a very fiddly kit, as are the other two, the Mickey Thompson Challenger I, and Roth's "Outlaw", but it can be built, and done well, looks outstanding. Art
-
A retirement coming in the aftermarket!
Art Anderson replied to Art Anderson's topic in Car Aftermarket / Resin / 3D Printed
Yes, that's true, but Don and Carol started casting parts in 1982--35 years is a long time to do that. -
Connie kit on '37 Ford?
Art Anderson replied to JollySipper's topic in Model Building Questions and Answers
Hey, we build model cars--we can do what whatever we want to do with our's! Art -
Connie kit on '37 Ford?
Art Anderson replied to JollySipper's topic in Model Building Questions and Answers
It probably never happened all that much, putting a rear mounted spare tire on any '37 Ford body style, as that would have interfered seriously with access to the trunk. Ford offered, as near as I can determine, only one body style with a rumble seat, which was the '37 Ford Standard Roadster with the rumble seat option, and that had only a portion of the rear deck opening up for the rumble seat. I believe, however, that in this body style, the stock location for the spare tire was in a space just behind the "front" seat. As the rumble seat roadster appears to not have an opening trunk lid, per se', quite possibly there was an accessory "Continental Kit" spare tire setup, most likely afermarket. Art -
I used the engine from the '50 Ford pickup for one simple reason--while it's the pickup engine having pickup truck exhaust piping and oil pan--it's simply light years better and more accurately done than the now 53-yr old AMT '49 Mercury tooling. Sure, it took more work--but the results were well worth the effort. Art
-
I thought of that when I did my conversion (never finished it out though) using the Aurora Mod Squad Merc wagon--but determined that cutting the door skin to leave just "framing" would have been lots more difficult--given that everything needs to be as straight and true as possible, plus the need to have all edges of that "wood" framing be chamfered to match the rest of the body shell. To me, it seems far easier to simply set the '49 Ford door skin inward by the thickness of the Evergreen used to make the new framing, than any other way. Art
-
Which kits are.....
Art Anderson replied to snacktruck67's topic in General Automotive Talk (Trucks and Cars)
Quite simple: Moebius Models is a small, fairly young entrant into the business of model car kits--their first model car kit, the '53 Hudson Hornet just hit the shelves 3 years ago. It takes a lot more lead time than most would figure to do a truly comprehensive model car kit, believe me! Art -
The "wood" trim on the doors for making a '49 Ford wagon shouldn't be a major problem--pretty sure that Evergreen has a size of styrene strip that would work. The bigger issue would be "spacing" the door skins inward into the body surface to allow the wood framing to be flush not only with the front fender edge, but also match in that manner the positioning of the wood trim on the forward edge of the rear quarters. Art
-
Convert a '41 Woody into a 1940? Uh, might I suggest that Motor City Resin Casters has an excellent 1940 Ford station wagon body in resin--with fender/floorboard unit, all three seats, and all the interior door hardware? There's a huge difference between the 1941-48 Ford and the 1940, it's longer, wider, and completely different shapes (even though it still very much looks like a Ford. Just my thoughts. Art
-
Lindberg 31 Bugatti Victoria
Art Anderson replied to Petetrucker07's topic in Car Kit News & Reviews
As an aside, Bugatti built something like 50 Type 41 engines, and wound up with a huge oversupply. Solution? Use them to power lightweight self-propelled railway passenger cars--much like the BUDD RDC (Rail Diesel Car) in the US in the 1950's. Art