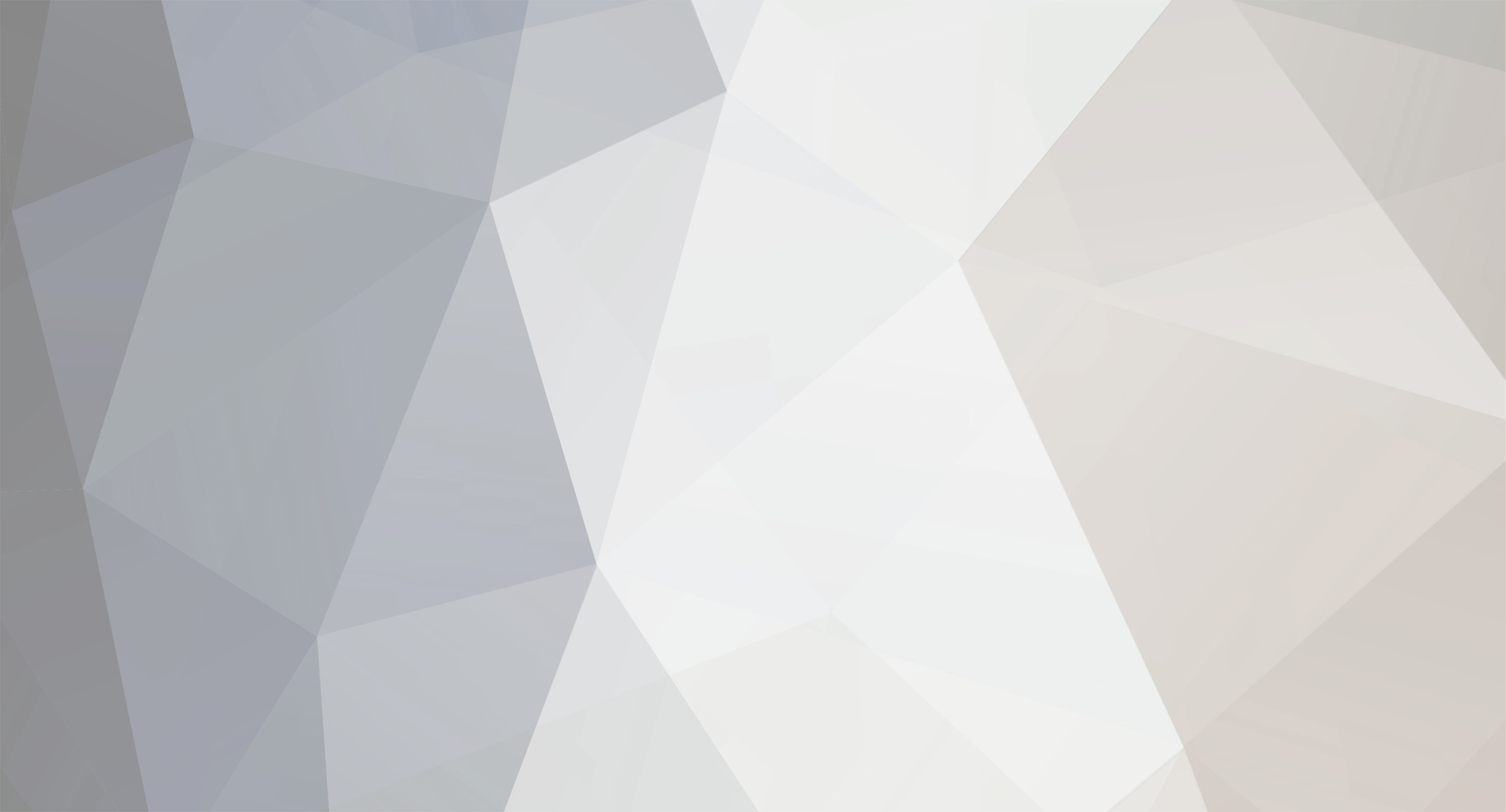
Art Anderson
Members-
Posts
5,052 -
Joined
-
Last visited
Content Type
Profiles
Forums
Events
Gallery
Everything posted by Art Anderson
-
BAck 35-40 years ago, first when my brother and his kid were in scouts, Pinewood Derby was pushed as a "father and son" thing, and for me in 1981 it was an "uncle and nephews" event--their Dad having passed away suddenly the previous fall. I helped my older nephew (and his Dad) the extent that I lent them my scratchbuilt 1/25 scale 1923 Miller 122 "HCS Special" Indy winner, as that was what Geoff wanted to build (he at the ripe old age of 9!). He carved out the body himself, using my model as his visual reference, with Dad helping make the fairly complicated frame rails and helping him install those on the sides of the solid wood body. Geoff insisted on painting the car, along with the "winged" HCS logo's on the side, and did a very respectable job of that for his age. The car didn't win the Derby, even though it came in 2nd or 3rd overall, but man-oh-man you should have seen the proud and wide smile on his face as he walked up to receive his award! What does Geoff do now at almost 53 years old? Designs and builds custom hardwood furniture for clients--makes a heckuva living doing that, and passing on his skills to his 4 kids! And, he lets them do the work on school projects etc, being a "resource person" and advisor--but THEY do the work themselves. Art
-
Decades of Decal "What The"s
Art Anderson replied to samdiego's topic in General Automotive Talk (Trucks and Cars)
Unfortunately, model companies often see decals as an expense, thus cheap decals happen far too often! Art -
Oh well!
-
Were I faster with a build like this, I'd just carry on with the original thread, but chasing that down after all these days/weeks? Nahhh. OK?
-
Hey, it's easier this way! Art
-
Buncha tedious addtions here! All the little parts in white styrene were added: Crossmember to carry the rear of the engine, under the transmission, an extension to space the steering gear in alignment with the steering column and the clutch arm. Also added is the clutch/brake pedal shaft mechanism, with pedal arms made from .020" brass rod stock: More to come, as this thing is moving right along! Art
-
Revell 49 Merc Decal Question?
Art Anderson replied to slusher's topic in Model Building Questions and Answers
I've made my own hole punches for cutting small decals by using a matching diameter of K&S brass tubing cut to perhaps 2" long. I simply use an Xacto knife with a #11 blade, and turn the tubing against that blade with the tip of the knife inside the end of the tubing. It takes perhaps 5 minutes to get a pretty sharp edge (I finish by rotating the tubing against some 400-grit sandpaper to get an even sharper edge. I can simply place the decal sheet face up on a block of hard wood, then align the sharpened end of that piece of tubing to the decal I want, and tap with a small hobby hammer. This punches out the decal, on its paper. It goes without saying, I think, that such homemade brass punches are pretty much a one trip thing, but they are quick and easy to make, and not particularly expensive either. Of course, I'm not likely to apply the decal in the normal manner after this, especially a really small one, but I've had good success simply gluing such small dial decals into their respective bezels on the model dash, then putting a drop of Devcon epoxy on top of it to create the lens. Art -
You are pretty correct. The chassis and bodywork were a Kurtis 4000 dirt track AAA (American Automobile Association) Championship car built in either 1953 or 54. This car still exists, restored, as part of the Indianapolis Motor Speedway Hall Of Fame Collection, but I've not seen it on the display floor of the Museum in probably 25 years or more. Art
-
No, the Rounds Rocket was not first built as a turbine car. I don't believe it was even built by Kurtis-Kraft, although it may well have used some Kurtis components. It was built for the 1949 Indianapolis 500 Mile Race. It was a 1949 attempt at a rear engine car for Indianapolis (not the first one, that honor went to a home-built rear engine car powered by a Marmon V16 engine, appearing at Indianapolis in either 1937 or 1938, the second was the Harry Miller constructed Mobilgas rear engined 4WD car which entered Indianapolis in 1939, as a team of two cars. One of those was destroyed in a fire in Gasoline Alley which took out one entire row of garages on the morning of May 30, 1941, the survivor being entered as the Tucker Torpedo Spl at Indy in 1948).. The Rounds Rocket pracitced at Indianapolis in 1949, made an attempt to qualify, but was too slow to make the field--apparently it was quite heav--and was powered by a 274 cid Meyer-Drake Offenhauser 4cyl engine. Art
-
Something to consider though: Aurora, just like most other HO slot car manufacturers, used a standard chassis underneath their cars, and designed body shells to fit that standardized chassis. As such, most body shells for this type/scale of slot car tended to be compromised at least somewhat to get a body that fit well, but still looked pretty much like the real thing. You may want to search for more detailed dimensional information on the Web, if your goal is to make as accurate a 1/25 scale model. Art
-
The idea for that jig came from the late Lee Baker, of Chattanooga TN about 1995 or so. The first ones I made were cut on a radial arm saw in hard maple blocks, by setting the saw blade at a 45-degree angle. While those worked well for larger strips of styrene, particularly square stock, to make right triangular cross section strips for scratchbuilt louvers, in order to make something fine enough to work with .020" rod or strip stock meant using metal. Art
-
The taillights presented another "big challenge"! They are small, as you can see in this picture, had to have mold parting lines polished off, painted, and then foiled with Stoplight Red metallic added to create the lenses! I simply drilled out the bottom side (mating surface to the rear fenders) of the taillight housings, mounted them on toothpicks with CA glue, then primed and painted them. Once dry, I foiled what have to be the smallest parts I've ever applied BMF to. One foiled, the other one not yet as of this pic: OK, enough for today! Art
-
On to the body shell! Knowing a bit about 30's, even 40's cars, with their bolted on fenders, the Opel needed to have fender "welting" added to the body shell--again, styrene rod stock got the call. In addition, while this kit is very precisely tooled, all of the panel lines left a bit to be desired, precise they were, but too shallow to escape being obliterated by even a fine paint job they were as well, so my Xacto razor saw (I use Xacto's razor saw blades here, as they are far thinner than a Zona Saw!) got the call. In addition, this is a multipiece body, shades of Revell of 1956-1960 or so (but so very much more precisely tooled!), which builds up on the floor pan (hey, it's an open car, a Kabriolet!). Considering that I want this car to represent what it is, Opel's entry into the German luxury car market, I figured that it had a highly finished body shell--no exposed primer on the underneath surfaces, but body color all over. That meant that the body shell, once built and proofed out, had to be painted UPSIDE DOWN on my paint stand! This entailed also remounting the body right side up after the first paintwork was completely dry, and airbrushing the upper sides of the body once more, to get a deep, even coat of Tamiya Racing White: On to the last segment! Art
-
ICM, unfortunately, put a huge (1/8" diameter) ejector pin right in the middle of the Chevrolet valve cover, which obliterated the crossing of the raised cross rib and dual front-to-rear ribs in the valve cover, so that just had to be fixed. Using a digital caliper, I found that the molded on ribs are just a gnat's whisker narrower than 20-thousandths of an inch, but there was a nasty depressed round area from that ejector pin--so a little bit of .015" Evergreen styrene strip stock got the call, cut it down to size, and use gap-filling CA glue to mount it, fill in the gaps around the edges. Next I made up a small flat sanding stick using a piece of basswood (from my local model RR store) with some 400-grit sandpaper glued to it with CA and then cut to the edges of the wood stick with an Xacto knife. This was used to sand away the raised ribs in the center of the valve cover, and sand the little Evergreen "filler and its surrounding CA glue flat. A few years ago, I needed a jig, or form to lay Styrene rod stock in, so that it could be sanded to half-round shape, by milling a Vee groove into a 3/8" square brass bar. With help from a friend who stayed much more awake in HS math than I did (sine, cosine and tangent stuff--remember trying to learn that??) I got the depth correct for making several sizes of styrene half round from rod stock, so this was fairly easy, just lay the rod into the appropriate groove, take that same sanding stick described above, and wet sand to get half-round. Here's the result: Art
-
Lots of preliminary work to this project! Let's start with the engine: Opel, having been bought up by General Motors at the depths of Germany's economic troubles in 1929, introduced the Admiral as their entry into Germany's luxury car market. While the chassis uses a lot of Buick layout, with its X-member frame, much of it was pure Chevrolet--the Dubonnet "knee-action" front suspension, and with Admiral coming in 1937, Opel used the then-new Chevrolet 216cid inline 6 (built in Flint MI, shipped to Germany!). Here is the kit engine as built straight from the kit: Note the very shallow pan--I suspect ICM had the same problem I have here, a distinct lack of information as to just how the bottom of the engine and chassis looked (I've found just two images online of the rolling chassis, one black & white photo, and a color cutaway illustration of the complete car, both showing only upper surfaces). So, I decided to take matters into my own hands, work at least somewhat logically, to give the engine/transmission the look if not perfectly accurate: Due to necessary clearances for the front suspension and tie rod, I really could not deepen the forward part of the oil pan very much, but I could add a sump to the rear of it, which I did with bits of sheet styrene and CA glue (my go-to for work like this a lot), as well as the "neck" at the rear of the oil pan covering the rear main bearing. In addition, I added, a bottom side to what should be the bell housing, again something ICM omitted, by laminating some thick sheet styrene together, and simply whittling that out with Xacto knife, needle files and sandpaper: More in the following installment! Art
-
How to paint two colors?
Art Anderson replied to angelo7's topic in Model Building Questions and Answers
To minimize the chance of "pulling the first color of paint off the model", I always remove masking tape by pulling it back AGAINST ITSELF, rather than just pulling straight up. Art -
How to paint two colors?
Art Anderson replied to angelo7's topic in Model Building Questions and Answers
Roger's suggestions are what I've been doing since I learned to 2-tone car models back a good 50 yrs ago. Art -
Clear Coat question!
Art Anderson replied to 1hobby1's topic in Model Building Questions and Answers
Absolutely! White plastic picnic spoons are great for testing out new colors, learning new paint techniques etc. Art -
reducing a photograph to scale
Art Anderson replied to landman's topic in Model Building Questions and Answers
Irfanview is also a free photo-editing program--which I've used for years now. Their photo resizing is very easy to use--just know the size you want in either decimals of an inch or metric! Art -
Something to bear in mind: With perhaps the exception of the two largest makers of Classic Era luxury cars, just about every other super luxury carmaker back in the era of this one built only the chassis, engine, and supplied identifier parts such as radiator, fenders & running boards and lights. The body shells tended to be stylied by the various coachbuilders themselvs, rather than the factory. Art