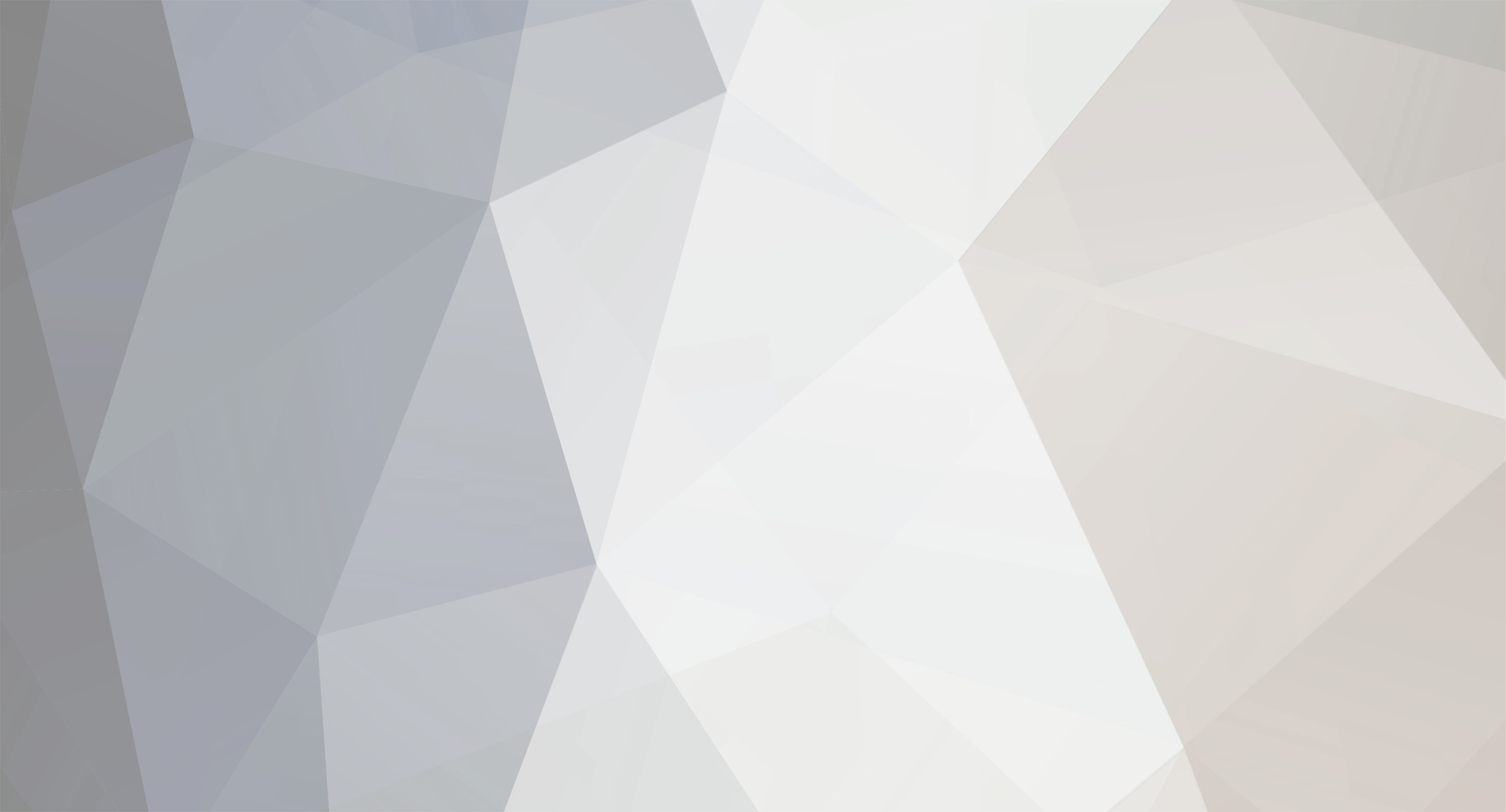
Art Anderson
Members-
Posts
5,052 -
Joined
-
Last visited
Content Type
Profiles
Forums
Events
Gallery
Everything posted by Art Anderson
-
It's up on wheels for the first time. Lotta miscues, mis-steps, fits and starts--like being cut from whole cloth, but it begins to look like something besides a collection of parts: Starting to be a fun project again! Art
-
What kind of music.....
Art Anderson replied to Hot_Rod_Bob's topic in General Automotive Talk (Trucks and Cars)
In the years 1956-58, I spent a lot of 50-cent pieces on 45rpm records (you know, those 7" vinyls with that one inch holes, that required either a snap-in disc in the middle, or a fat spindle overlay (which my Webster-Chicago High Fidelity portable record player came with as an accessory!). I wasn't into rock & roll yet--in those years it was country or folk music--Johnny Horton was big with me, as was the Kingston Trio. So, it was records like "Sink the Bismarck" or "The Battle of New Orleans" (that was a hit right at the time that Queen Elizabeth II made her first State Visit to the US, caused a ton of controversy, that song right then!), and a year or so later, the likes of "Charlie and the MTA", Tom Dooley and such by the Kingston Trio. In late 1957, a grad student at Purdue, a customer on my Indianapolis Star paper route, told me he was getting his PhD in January, and moving, and would I be interested in buying his stereo? Yeah sure, I said, and then on the way home it was like "gulp!"--what would my parents say when I told them I had agreed to spend $100 of my hard-earned money on that? Mom and Dad were more than sympathetic, they encouraged me to go right ahead--so that week, I took 5 crisp $20 bills to Philip's apartment, with Dad in tow, and I bought the outfit--and we packed it in Dad's Hudson and back home we went (4 blocks) with Philip in tow to help me get it set up in my new basement digs (a 15x30 foot room that was ALL MY OWN--it was to be part of a basement apartment my parents planned for when I left the nest). I built all of my model cars in HS to music from that stereo, and I had an eclectic taste, partially pushed on me by Dad (who really loved classical music). But it was those country and folk records that I used to get the creative juices flowing. Customs, rods, even factory stock model cars got those tunes imprinted into their bodywork, their paint jobs. I still like country, but it has to be classic country--and every now and then, I dig out some CD's of old folk songs, Kingston Trio, Peter, Paul and Mary; Simon and Garfunkel. Where once it was my favorite music that drove my model car building, now it's whatever tickles me that I listen to. Art -
Cars named after fish
Art Anderson replied to Pete J.'s topic in General Automotive Talk (Trucks and Cars)
Dauphin was the French term for "Prince", Dauphine means "Princess" I believe. Art -
That's a repop of the styrene lump from Monogram's '55 Kurtis Kraft 500C Indianapolis Roadster--crude for 1956 (when it was introduced, even more crude by today's high expectations). Norm Veber's 255cid Offy is correctly done in 1/25 scale, and is HIGHLY detailed. It was first done by Etzel's Speed Classics, and any who knew Chris Etzel, or ever had any of his ESC race car kits can attest to their accuracy and perfection. Art
-
Pic #1 AMT '61 Buick Invicta convertible Pic #2 AMT '61-'62 Lincoln Continental Convertible Pic #3 AMT '61 Falcon Ranchero Pic #3 AMT Trophy Series '53 Studebaker Starliner HT Pic #4 AMT '61 Mercury Comet Hardtop Pic #5 JoHan '61 Plymouth Fury Hardtop Pic #6 AMT Trophy Series '57 Ford Thunderbird Art
-
Cars named after fish
Art Anderson replied to Pete J.'s topic in General Automotive Talk (Trucks and Cars)
AMT Corporation actually produced a 1:1 size Corvair powered sports car in very limited numbers, called the Pihrana, in the middle 1960's Art -
Not at all ficticious! It was prototyped by Plymouth Division for the 1971 model run, so it could be entered in Nascar, but a rules change, outlawing the streamlining nose cap and wings for Grand National racing (this a year before the Winston Cup came about), so there was no production version offered (actually, the Daytona Charger and the Superbird were tough cars to sell at the time--the last Daytona Charger was finally sold off the lot, still a new car, in the summer of 1973, by Twin City Dodge in Lafayette IN, fully 4 years after it was produced!). Art
-
Anyone hear from Gregg?
Art Anderson replied to Tom Kren's topic in General Automotive Talk (Trucks and Cars)
Watching FoxNews right now, tsunami is expected to hit Hawaii in about 15 minutes or so--hope people near the shoreline are heeding the warning! Just checked on a website for a 16yr old California girl who is attempting a solo non-stop circumnavigation of the World, and is about 1500 miles off the coast of northern Chile. Her team onshore says that she is OK, likely not even experiencing a noticeable swell in the deep South Pacific Ocean. But, I am thinking about the people in Chile, prayers going up for their safety in all this. Art -
Not saying that any of these are your specific problem, but there are things that decals do not like, for adhesion: 1) Decals don't stick well to a surface painted in flat finish paints, as these have a rough, grainy surface. Decal film can't really conform to such a surface. 2) Decals don't stick well to even a glossy surface, unless it's clean, and free of finger oils, and especially if the paintjob has been waxed beforehand. 3) And this is perhaps the biggest error that modelers make, soaking the decal too long. The "glue" that decals use is common, ordinary gelatin, same stuff that postage stamps used to use. Water soaks through the decal paper (in reality, this is blotting paper, very porous). Wet the decal just long enough so that it will slide, NO LONGER, and then position the decal, on the paper, where it is going to be, as closely as you can, and gently SLIDE the paper out from underneath it (rather than peeling it off the paper first). This keeps the glue on the underside of the decal, and it can still be positioned a bit while wet. If you need to use a wetting agent for your surface, that's OK, and of course, the available setting agents (used to soften the decal film so that it can snuggle down over details and over compound curves) work as well. But, the key issue, and the one I suspect is causing your problem, is to not use so much water as to wash away that gelatin adhesive. Art
-
Activated charcoal filters aren't all that expensive, frankly. At Playing Mantis, where I did Product Development for Johnny Lightning, we had a ventless spray booth, downdraft style, and that one got a lot of use, mostly from the action figure guys using spray contact cements, right there in the offices, and the only odor we smelled was the residual smell from the glue solvent drying after sprayed, as the guys were working on their projects on the plan table nearby. Art
-
For starters, Pontiac, from their introduction of the Straight 8 in the early 1930's used a chassis that was 6" longer in wheelbase than their Chevrolet cousins, through the 1957 model year. From 1953 through 1957, the extra wheelbase was split between front and rear on the top of the line cars, something like 4" in front, 2" in the rear (which moved the rear wheel arches back by that much, compared to the same body used on a Chevrolet. The extra length was needed in order to accommodate the longer, straight 8 engine, which went out of production at the end of the 1954 model run, although Pontiac retained the longer front clip for proportions--that said PONTIAC back then. As station wagons were only a minor part of Pontiac's lineup in the 50's, they used exactly the same body shells, albeit trimmed, and using some unique sheetmetal, to differentiate them from Chevrolets which used exactly the same body shell, so they had a slightly shorter wheelbase than did the upper line Star Chief hardtops and convertibles. As for X-members, nearly everyone building convertibles (and hardtops, which originated as convertible body structures but having a steel roof welded on) used an X member to provide extra stiffness and torsional rigidity, which compensated for the lack of body strength in a topless car. Some carmakers used X-members under all their cars well into the 1950's, most notably Buick. long after Ford (for example) went to straight ladder-style frames. GM's so-called X frame, having that heavy, very rigid center box-section, and no side rails, debuted in 1957 at Cadillac, and spread across the company's divisions for 1958. Even after Buick and Oldsmobile began adding side rails, and then going to ladder frames once more in the early 60's, Chevrolet and Cadillac carried on with the X frame through the 1964 model year, Cadillac's low-volume Series 75 Sedan Limousine retaining them for another year or two after that. All this said, your best bet for a realistic looking frame for a '56 Pontiac Star Chief would be a stretched Tri-Five Chevy frame and floorboards. It will have the "look" whether or not it is completely accurate. The body of that '56 Star Chief is an A Body, but looks as big as the B Bodied cars from Olds and Buick, simply because of its longer trunk (incidently, the trunks on those 50's cars were not considered to be a part of the basic body structure, that ended at the base of the rear window--the trunk merely being a sheet metal extension out back), so the roof from any '55-'57 hardtop should do the job, just fine--in the 1:1 world, it was the same stamping and structure as a Chevrolet. Hope this helps! Art
-
spray booth explosion
Art Anderson replied to Bowtienutz's topic in General Automotive Talk (Trucks and Cars)
Kitchen exhaust hood fans surely are exposed to flammables! Try grease fires, for example. Exposed windings of an induction (brushless motors) are almost never the issue here. What is the issue is, static electricity--which causes more exhaust system explosions and fires than sparks from electric motor brushes. The answer here is to keep your system clean, by vacuuming it frequently. The overspray from your airbrush is very finely divided particles of a very flammable substance--dried enamel or lacquer burns readily. So, vacuuming the booth, AND the exhaust ductwork is highly advised, on a frequent basis, AND washing out the filters as well (or replacing them if they are replaceable. I learned all I want to learn about flash fires and explosions when I was 12, back in the summer of 1956. It was one of my chores to burn trash (back then, everyone had a burn pile or burn cage out at the back of the yard for that purpose it seemed). Unbeknownst to me, Dad had tossed an empty turpentine can in the trash, cap off, and when I lit a match to start that fire, it when WHOOM! Right in my face! The flash fire ruined my eyeglass frames (plastic) even though the lenses were glass, burned away my eyebrows, and all the hair on the front half of my head, left me with first and second degree burns all over my face, neck and upper chest (no shirt to catch fire, the weather was too hot for that!). I've never forgotten the tears in my parents' eyes when they got home in response to my frantic phone call to Mom at her office, nor will I ever forget the intense pain of those burns. Fortunately, I fell back onto the ground when it happened, so I didn't inhale any of the flame, back then that would have been crippling, if not fatal. (After a month or so, it all healed up, I didn't have any scars to show off when I started the 7th grade, but the experience has stuck with me ever since.) So, be careful, keep your spray booth and its filter clean as much as possible, OK? And, be sure to ground your motor AND the booth, if it's metal. Art -
I've seen more than a few older Corvettes, barn finds, or just plain old cars out on the street. For starters, paint peeling and cracking was very common on early Vettes, even through the 1st generation Stingrays. The body had a tendency to flex, and when that happened, real stress was placed on the areas where the various body panels were joined together by fiberglassing the panels together. The acrylic lacquers used (nitrocellulose lacquer prior to the 1960's) cracked at these areas, and then as the adhesion of paint to fiberglas failed, the lacquer actually peeled up along those cracks, chipping away where the cracks in the paint intersected each other. Bear in mind that the primer was permanently adhered to the color layer--that's one of the characteristics of lacquers, each succeeding layer of lacquer penetrates, dissolves itself INTO the primer, and preceding coats of color, but the bond between the primer and the material surface isn't nearly that strong, the primer itself pulls away from (in this case) the fiberglass. In severe cases, even the fiberglassed joints themselves would crack--fiberglass resin doesn't bond all that perfectly to previously cured fiberglass, so it can crack, and peel up a bit as well. This was particulary visible on roadsters, at the corners of the hood opening (where the front fenders were joined to the cowling, and at the rear corners of the interior opening. In addition, '53-'62 Corvettes were notorious for this cracking at the front corners of the hood opening as well. Hope this helps a bit! Art
-
Real or Model #129 FINISHED!
Art Anderson replied to Harry P.'s topic in Real or Model? / Auto ID Quiz
Real. Art -
i got a question?
Art Anderson replied to B_rad88's topic in General Automotive Talk (Trucks and Cars)
PSAB Model Car Chat Room generally gets going around 8pm ET every night, with the biggest nights being Friday and Saturday nights. Lots of regulars there those two nights. Art -
If you upgrade your browser to at least IE8, the toolbar goes back where it belongs. Art
-
Check out the new Indycar Concept
Art Anderson replied to Ryan S.'s topic in General Automotive Talk (Trucks and Cars)
With the exception of the very narrow track up front, this thing looks very much a throwback to the Gurney Eagle "Pencil Cars" from about 1980 or so. Art -
Time for an update on the EMK (Elusive Model Knox) truck
Art Anderson replied to Art Anderson's topic in WIP: Model Cars
Original uploaded pic from Fotki Art -
Time for an update on the EMK (Elusive Model Knox) truck
Art Anderson replied to Art Anderson's topic in WIP: Model Cars
Casey, Frankly, the hub detail is pretty sparse--pretty much what you see there is how it looks, even under a magnifier. Simple turning on the lathe, with brass tubing pressed into it, 12 1mm Scale Details rivets soldered in place to replicate the round carriage bolt heads. Art -
Chuck, Very much urban legend, I'm afraid! The legends about the Soviets using obsolete Packard body tooling go all the way back to WW-II, when ZIS produced a few gigantic limousines for Marshal Stalin that looked so very much like the discontinued 1940 Packard 180 series sedan limousines. During the Korean Conflict, a couple of those were captured and sent back to this country--and they resemble Packards, but that is all--there is absolutely no comparison in proportions or dimensions, not even contours--just the "look". Packard's body dies didn't go overseas, unless as melted down for artillery or naval shell casings. I've seen ZIL's and Chaikas with that 1955-56 Packardesque styling, and they only loosely resemble any Packard--frankly, they more resemble a Checker Marathon customized to look like a Packard. Art
-
It's been awhile, I know, but the wheels for this thing have driven me nuts! I had planned on using the wheels and tires, with machined brass hubs, from the Ertl Knox Truck, but the wheels turned out to be made from polyethylene plastic, completely unmachinable! So, Plan B went into action. I found, at an IPMS show, some 1.3" styrene wooden wagon wheels by Grandt Line, and had snagged a couple of sets of them a year ago. It didn't take much planning to figure out how to make brass hubs, with brass rivet details to replicate the round-headed carriage bolts used to secure the flanges of the hub to the spokes (except that machining those has been tons of fun!). Next was figuring out how to replicate the solid rubber tires most often used on early commercial vehicles--that was solved by wrapping .100" X .060" strip styrene around the circumference of the Grandt Line wheels. The outer center hub was turned off in the lathe, the wheel drilled out to 5/32", and the brass hubs installed with a bit of CA glue to secure them. So, without any further adeu: The wheel And, two wheels mounted up on the front axle (which will be steerable from the steering wheel) Art Anderson
-
What engine is in the Ala Kart
Art Anderson replied to Madd Trucker's topic in General Automotive Talk (Trucks and Cars)
241cid Dodge Red Ram Hemi Art -
3D printers.....
Art Anderson replied to roadhawg's topic in General Automotive Talk (Trucks and Cars)
Until rapid prototyping by CAD reaches the point of being truly "plug and play", it's not going to be that much a factor in a cottage industry with relatively small resin casting businesses. What everyone, enamored with such technology forgets, or fails to mention is "the upfront costs". While resin casting itself is expensive, compared to the material and labor costs of injection molded styrene, its key is that it is relatively INEXPENSIVE when one considers the very low production numbers VS a mass produced styrene model kit. But, what are the upfront costs? While I have never looked at any of this CAD stuff even casually, it does seem to me that somewhere between $5000 and $10,000 would be the range for buying into the equipment, and the software. Then, to learn to operate it, unless one is already trained in this technology adds even more cost, and a fairly long lead-time before an operator would be capable of using it to any degree of sucess (think of this as going to school on the technology). Then, there is the obvious necessity of having a real 1:1 prototype with which to work, to get all the measurements, shapes and contours, and that will be one HUGE stumbling block. Just to amortize the upfront costs mentioned above will necessarily have to be included in the selling price of a resin part or transkit--unless one wants to make a small fortune--out of a much larger fortune. And, while the 21st Century prototype maker is working with his puter, the added equipment which will do the actual shaping--I can still see an old-fashioned 20th Century modeler knocking out a very acceptable master for that same subject, by the old-fashioned way of doing it by hand, and getting it to market way ahead of the computer actuated RP. Perhaps someday, but I don't expect to see this technology in the model car aftermarket anytime soon. Art -
Hoosier by birth, Boilermaker by the Grace Of God. 'Nuff said. Art
-
What Happens to the Molds and Masters When...
Art Anderson replied to Casey's topic in Car Aftermarket / Resin / 3D Printed
Believe it or not, RTV rubber molds are perishable, they deteriorate over time, whether used or not. For body shell molds, it takes a relatively soft rubber, in order to be able to flex the mold to remove the finished casting, and that generally means "tin-cured rubber". Trouble is though, that tin cured rubber has a very short life--the mold starts to deteriorate immediately starting with the very first pour--as some of the components of the resin leach, or penetrate into the rubber starting with that very first time you pour resin into it. Most tin-cured RTV molds are good for no more than say, 35-40 pulls before the surfaces that make the part deteriorate to the point that the quality of the finished part is nowhere near what you'd want as a finished part. Over time, tin-cured RTV breaks down to the point that merely picking up a heavy body mold off the shelf can make the mold itself tear in two simply from its own weight. Platinum-cured RTV doesn't do that, but it has two drawbacks--first it's about twice as expensive up front, and second, it has a much higher hardness, making it very hard on not only cured castings, but also on the masters themselves. There is also the matter of material fatigue where masters are concerned. Most of the AAM masters were themselves massive conversions of existing styrene body shells--I learned early on, that specific techniques had to be used in order to ensure that a heavily converted body shell from a kit be sturdy enough to resist breakage when demolding it from a new RTV mold--an awful lot of my bench time was consumed in repairing broken masters. Even at that, some body shell masters eventually broke into literally dozens of pieces at some point, the styrene just got fatigued to that point. For that reason, I used to save the first 3 castings from any new project, so that I could use the resin body shell to create new molds from--but even that was fraught with troubles--given the even slight shrinkage factor (an RTV rubber mold can shrink the part cast at least by a factor of -5%). I still have all the masters that exist from AAM, save for perhaps a dozen or so that broke up irreparably, except for all the pre-WWII stuff that I sold to R&D Unique back in late 2000--none of which ever got reissued. I have absolutely no plans whatsoever to ever cast those again--too much effort, too much space required for that--those will remain with me, either as just dust-gathering archives, or perhaps to be built up by me at some point in the future, so don't ask any further. Art