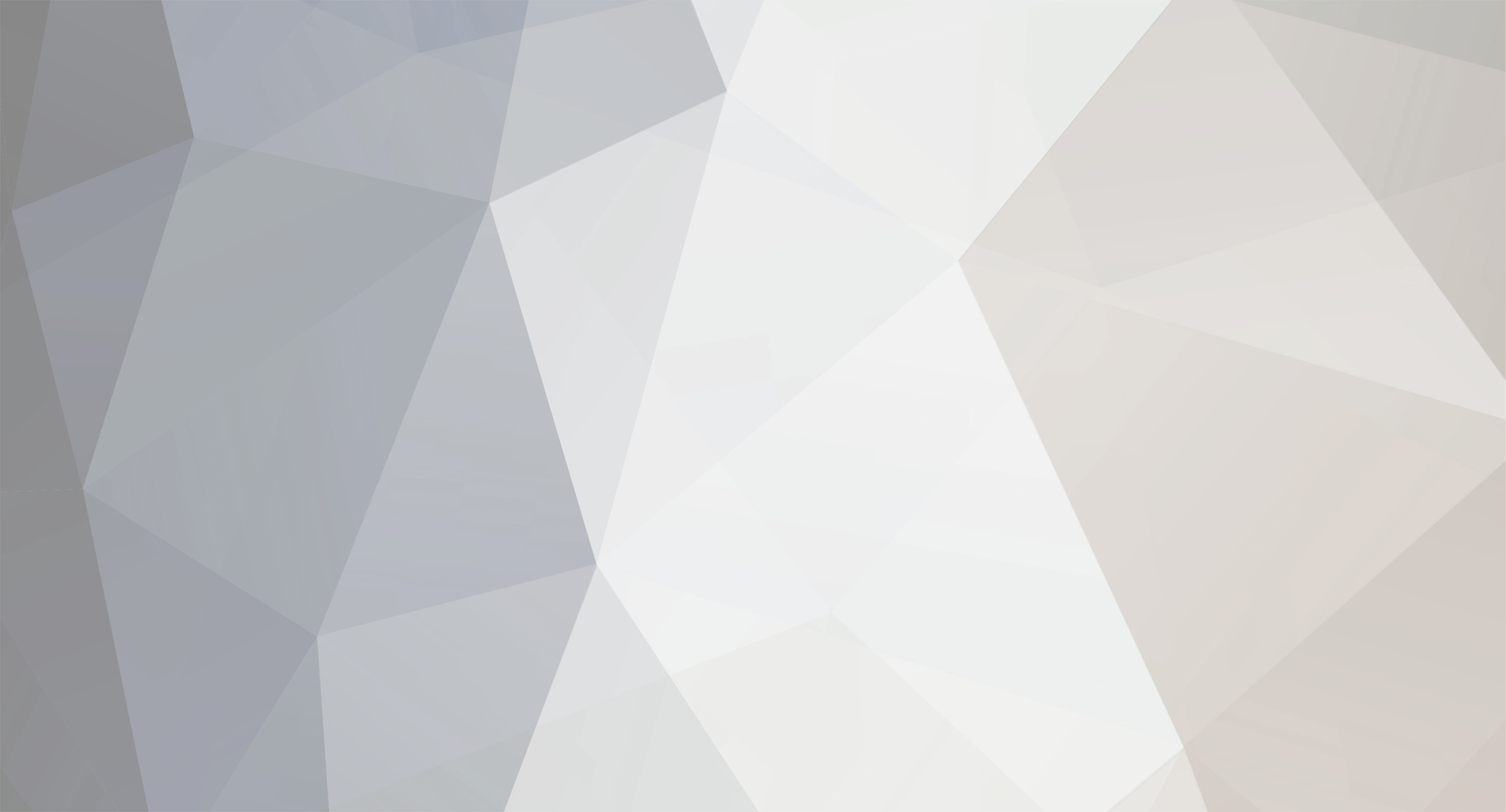
Art Anderson
Members-
Posts
5,052 -
Joined
-
Last visited
Everything posted by Art Anderson
-
"Brass Age" car maintenance?
Art Anderson replied to Harry P.'s topic in General Automotive Talk (Trucks and Cars)
At first, leather was the material of choice for automobile upholstery (particularly in open cars), even folding tops on buggies and those early roadsters and touring cars. Pyroxylin, a nitro-cellulose compound, dating from before our Civil War, could be dissolved in various alcohols and was used as the "resin" base for nitrocellulose lacquer. In household use, pyroxylin was the component of common Collodion, sometimes referred to as "new skin", which could be applied (with excruciating pain BTW) to cuts, scrapes, abrasions even minor burns, because it stuck tightly, stretched and gave with movement, the flexing of the underlying skin. Ford and several others started using heavy cotton fabric, coated with the stuff to make a water-resistant fabric that could be patterned to look just like leather, and at a fraction of the cost of real leather. But, it didn't wear nearly as long as genuine tanned cowhide. Ford and the other carmakers went on to use this pyroxylin impregnated cloth for the fabric coverings of the roofs of closed car bodies (coupes, sedans and the like) until all steel "turret top" body construction took over in the middle 1930's. Ford even called the stuff "Art Leather" which sort of disguised the fact that it was an artificial substitute for the real thing. Ford also advertised their use of "fine pyrolylin lacquer" to counter Chevrolet's bragging about using DuPont Duco, even though chemically, they were both the same stuff, Ford's paints coming from Ditzler (now PPG-Ditzler). Vinyl, on the other hand, while discovered accidtently in a laboratory in the 1890's, found no use until the late 1920's, when it began taking over, for example, in the record industry--replacing the pyrolylin lacquer coatings used up to that time for making early 78rpm records. One of the first uses of PVC in cars was as seals for hydraulic shock absorbers and even hydraulic brake systems in the 1930's, expanding into homes as shower curtains about the same time frame. It didn't become popular in cars until the early 1950's however, when first Kaiser-Frazer and then the Big Three found it to be useful in creating those wildly popular colorful interiors that replaced the old mousey-gray and taupe fabric seats. Vinyl also played a role in WW-II, as a component of the earliest synthetic rubber tires. Art -
1/32 scale or 1/24?
Art Anderson replied to Matt Bacon's topic in General Automotive Talk (Trucks and Cars)
Japan, very much like the US, saw model building as a primarily "kid" thing back in the 60's-70's, just as did our model kit companies in the 1950's and 60's. Bear in mind that avout 1955-56 or so, Irwin and Nate Polk, of Polk's Hobbies in New York City began importing the newly offered Mabuchi line of miniature DC electric motors (incidently, those two had the exclusive import rights to ALL Mabuchi motors during the 1960's slot car craze, all the way out until the middle 80's and the rise of electric RC cars as well--I've been told they made more money on those than their hobby shop operations produced, for several years. Revell, Lindberg, Aurora, Monogram and AMT all made at least a few motorized model car kits, for example, as did Strombecker (their very neat series of sports and grand prix cars in 1/24 scale in 1958-59 were all motorized). Monogram's Kurtis Indy Roadster was motorized for a couple of years around 1960, as was the Revell '57 Ranchero, and their little Porsche race car (designation escapes me at the moment). A number of Lindberg's 1/32 scale hot rods were motorized at one point. Revell's first two model car kits, their 1/16th scale 1909 Maxwell, and their 1912 Model T Ford coupe started out as motorized plastic toys, then morphed into motorized model car kits as well. Lindberg was perhaps the King of motorized plastic model kits though--they carried it forward into uncharted territory. They had a line of small, 12-15 inch long model kits of US Navy ships which had their electric motor in KIT form as well--build the motor, then build the model, find a pond! Lindberg's MUCH larger kits of the Bismarck, HMS Hood, the long-running kit of a USN Fletcher Class destroyer were all introduced first as motorized models, complete with a cam-system for preset cruising patterns in water (wonder how many wrecks of those lay in the mud and slime at the bottoms of park lagoons and ponds across the US?) Ideal Toy Company did several large scale model cars which had "Cam-O-Matio" drive systems as well. It's little wonder to me that Japanese mfr's jumped onto the motorizing bandwagon early on, given their cultural passion for things mechanical, which was very much like that which existed in this country as well. Many of Tamiya's early armor models were motorized, with soft neoprene rubber tracks and they did work. But they carried the motorizing thing to the extreme! As late as the mid-70s, there were even model kits of electric fans that actually worked! So, go figure. Art -
Are Smart Cars too big?
Art Anderson replied to Harry P.'s topic in General Automotive Talk (Trucks and Cars)
I dunno! My 24speed off-road bicyle is not only smaller, but way more fuel efficent (Nancy Pelosi, are you paying attention?????) Art -
"Brass Age" car maintenance?
Art Anderson replied to Harry P.'s topic in General Automotive Talk (Trucks and Cars)
To add to this thread a little bit: Maintaining the finish on a brass era car (for that matter, most any automobile up to 1924 or so) was a chore completely unto itself. From the beginning of the automobile age, painting a car was no different than painting a horse-drawn carriage--the first automobile bodies (such as they were) were built in the same manner as fine carriages--from wood. After the body shell was constructed, all moldings and other surface trims added, then carefully sanded, and any filler work done; the body shell was primed, with a sandable primer made largely from varnish and heavy pigments, with a lot of talcum powder added. This had to be set aside to dry for several days (weeks even, in cold or wet weather) until it hardened completely. The body shell would then be carefully sanded smooth. Once the primed body was ready, color coats were added, by hand, with very soft paintbrushes (camel's hair, or squirrel hair), the color being simply the most basic of enamels--varnish with finely ground pigment added. Incidently, there were "pearlescent" colors available, IF you had the money--fish scales mixed into clear varnish!. After perhaps 3 or 4 coats, the body shell would be placed in a clean, dry evironment for several days, often weeks, until this color coat dried "click hard". Once completely dry, the body shell would be rubbed down by hand, with pumice and oil, until the color coat was completely smooth, if satin-finish. This was laborious, labor-intensive, but it was the only way. Once smoothed out, the color coat was washed, to clean it of all pumice residue, and of course, to get rid of the oil, so that the clear coat would stick. The clear coat? Spar Varnish! Now, if you have ever used spar varnish, you know that it also takes many days to dry without the addition of any "driers". Finally, after the spar varnish was dry, the body would be taken out of storage, and the pumice and oil rubbing repeated, this time, to a high sheen. With the introduction of sheet metal as a "cladding" around 1904-05 or so, the painting technique remained the same, laborious work, long lead times. But being the "state of the art", this is pretty much the pattern followed by every automaker, world-wide until 1914. It is generally accepted that Ford Motor Company introduced the concept of "spraying" paint on car bodies. For them, it was a matter of necessity. Where most all carmakers produced only a few thousand (at best) cars per year, by 1914, Ford was looking at half a million (and they did pretty much achieve that), so something had to give. The story goes that Henry Ford observed that the hand tools, the wrenches, etc., that were being purchased for use in the factory had a black enamel finish on them, that would not flake or peel (no chrome-plated Snap-On tools back then!), but could only be scratched, or chipped off the steel. Intrigued, the story goes, Henry Ford inquired, and was told that the tools came from Stanley Tool Company. Henry Ford (according to Stanley Tool's history) tried to get the paint formula from Stanley, only to be refused. He then tried to buy out Stanley, but the owners refused a generous offer to sell (those hard-nosed Connecticut Yankees anyway!!!), but they would be willing to vend their black enamel to Ford, and the rest, as they say, is history. This enamel used the then new-tech "Japan Drier", a chemical which, when added to oil based paints, greatly speeded up the drying time. But how to apply the stuff? Stanley, of course, merely dipped their hand tools into it, then baked it dry. Now that would work for small parts, even fenders, splash aprons, hoods and running boards. But what about a body shell? Baking a body shell made up largely of wood, covered in sheet metal, the wood being coated with asphaltum (the same stuff that copper radiator cores used to be painted with) not only presented a shrinkage problem, but also at 400-degrees, a serious fire hazard as well! So, enter the first "spray painting" applications. Ford settled on a very primitive spray painting operation for the T--simply pumping the black japan enamel through large "garden hoses", and out through a simple hose nozzle, more "squirting" the stuff than finely atomizing it. The bodies could then be run through a long, lower temp baking oven, which had hundreds of heat lamps to heat the sheetmetal, thus force-drying the paint. But, what about maintaining the finish in service? Careful washing, by hand, flowing water from a hose over the body surfaces, to flood away dust and mud was part of the equation, followed by a careful scrubbing with soft natural bristle brushes, followed by a chamois drying. Polishes were available, but had to be used by someone well versed, as those hand-painted, hand rubbed varnish surfaces had to be treated with great care. Even at that, in a fairly short time, those early cars dulled out badly, in the case of early wooden bodies, the wood expanded and contracted with the seasons, even with changes in humidity. On steel or aluminum, the carriage era paintwork checked and peeled in just a couple of years, requiring a complete repaint. Brewster Body Company of Springfield MA, was legendary for their customer care--many of the buyers of luxury cars bearing Brewster bodies (mostly from the region New York City to Boston) often had two body shells for their cars--closed bodies for winter, open bodies for summer. At the change of seasons, their chauffeurs would take Milady's car back to Brewster, who would remove the winter body, and withdraw that customer's summer body and mount it on the chassis. While they had the customer's body shell in storage, they would completely refinish it, so that come the next season change, the remounted body would be in pristine condition. Brewster maintained a meticulous file for each customer, with chips of their favorite color (most Brewster Green paints, for example, were custom mixed to customer order, and were exclusive--the Vanderbilts would NOT be seen in a car the same exact color as the Whitneys, or the Astors, for example!). This all began changing in 1923, with the development of a sprayable, fast drying lacquer, Duco, from DuPont. By 1924, the principle owner (even savior) of GM was DuPont, so that is where modern spray painting of cars began, in 1924. But, the lowly owner of a black Model T Ford had no such luxury. As that black Japan Enamel eventually faded, dulled out beyond polishing, it was down to the hardware store or the paint store, buy a can of so-called 4hr enamel (the stuff dried to sticky in 4 hours, took a day or more to dry hard), a brush, and some thinner, went home, and got to work. Ford eventually went to a synthetic lacquer for the '28 Model A, called Pyroxylin, which was made from the same resin derived from wood, that they used to make artificial leather for seats, waterproof top material for open cars and the fabric roof inserts for closed bodies. Those early lacquers required lots of polishing, and a ton of handwork to wax and shine--all the way into the 50's, to get a Simoniz wax job meant something, it meant that you cared enough about your car to spend all day long, waxing, then polishing out by hand, to the point of serious fatigue (I know, as I got paid the princely sum of $5 bucks about every month to wash, wax and polish the cars that a couple of my aunts owned back then--Dad's cars? Well, he considered it just compensation for a comfortable home, clothing, and three square meals a day!) How times have changed, huh? Art -
Who has even a clue? Tonka Toys as a free-standing company is no more, the brand is now owned by Mattel, and has been for years. As for the "Diorama" kits, there were 6: 1903 Winton, 1913 Model T Touring Car (two variants of this--the stock T, and one done in red, as a fire chief's car), 1903 Wright Flyer, Lindbergh's "Spirit of St. Louis", Chicago & Northwestern locomotive "Pioneer" (a 4-2-0 steamer from the 1850's), and the Western& Atlantic "General" (the famed 4-4-2 steam locomotive from the Civil War's "Great Locomotive Chase". The kits just didn't sell well at all--they were out for only one or two seasons, and then disappeared into the mists of time. Art
-
Does the roll cage look too big?
Art Anderson replied to oldman23's topic in General Automotive Talk (Trucks and Cars)
In 1/25 scale, .060" equals exactly 1.5 inches. Art -
"Brass Age" car maintenance?
Art Anderson replied to Harry P.'s topic in General Automotive Talk (Trucks and Cars)
Harry, The concept of lacquering brass to maintain the shine never did find any usage outside of household decor items and of course, musical instruments (you know, cornets, trumpets, trombones, baritone's, bass's, Sousaphones, and of course saxophones). Certainly it wasn't at all used on automotive brass, mostly due to the exposure to the elements, and the heat generated by acetylene or kerosene flame inside headlights, cowl lights, and taillights back then--those suckers get HOT when lit for any length of time. In addition, as any brass musician knows, if the clear lacquer got scratched or chipped, the exposed raw brass tarnished quickly, and could never be polished to look at all like it should, the only solution being to have the instrument disassembled, the lacquer stripped, the brass repolished all over, then re-lacquered for that like-new appearance. I suspect that no car owner would have cared to have had that done. Another issue would have been the method of assembly of lights, even radiator shells. Brass doesn't take deeply drawn stamping without cracking, light bodies having to be either made up from shallow stampings and then soldered together, or their shapes (round headlights for example) being formed by the process of "spinning" or working the sheet brass to shape on a mandrel turning at high speed, being constantly annealed in order to prevent it's splitting during manufacturer. Then, there was the issue of the inside surfaces! Those old brass headlights, while many using glass parabolic mirrors behind the gas or kerosene flame, generally had their inside surfaces made either from German (Nickel) Silver, or on cheaper cars, silver-plated. That, and the need to solder those parts for assembly, would have made lacquering an after-the-fact proposition. All that said, there was a trend some years ago, among antique auto owners/restoreres, to lacquer the brass trim, but I believe that is now long out of favor there. 60 years ago, or so, I was surrounded by people my parent's age, even older, who constantly reminded me that polishing the brass on those early cars was a real chore--one best consigned to the kids in the family (once old enough to be trusted around that treasure of treasures) or the hired man on the farm, or the family's chauffeur). That is why, by about 1914-15, polished brass trim began to disappear, replaced first by nickel plating (which required polishing still, but not nearly so much nor as often) and radiator shells began to be painted (often over brass) the same being true of headlight, cowl lamps and taillight bodies, those having only the rims around the lens in either nickel or on some cars, polished brass. By 1917 or so, in the US, brightwork had all but disappeared on new cars, at least in the US. Nickel plating was considered by many, particularly with luxury cars (the 3 P's for example, Packard, Peerless and Pierce Arrow), nearly all components on the exterior being painted including the radiator shells) as being somehow "cheap". Nickel did return in the flashy days of the 20's, tolerated when new, loathed with age and the dulling that happens with nickel, until Oldsmobile pioneered chromium plating in 1927-28. At last a brightwork finish that remained so for a long time. Of course, Ford Motor Company introduced polished stainless steel (Ford called it "Rustless Steel) for 1930, and by the end of the 30's, most of the low priced (even a number of mid-priced as well)cars came out of Detroit with all but bumpers and diecast metal trim items in stainless steel. Art -
1/32 scale or 1/24?
Art Anderson replied to Matt Bacon's topic in General Automotive Talk (Trucks and Cars)
Matt, Of course, you are addressing an audience which is largely from the US and Canada, but at the same time, one fact seems to be operative here: Modelers, for several decades now, have voted (with their dollars, their Pounds, Francs, etc.) for the larger scales of 1/24 scale, or in North America, the much more popular 1/25th scale, There's a plurality there which may well be an impossible nut to crack now. I think this is just as true on the eastern shores of the Atlantic today as it was over 30 years ago, when Matchbox tried introducing a new line of then-contemporary racing cars in 1/32 scale. Now perhaps it was that in the day, the US was still the single largest market for model car kits, but that probably isn't nearly so true nowadays. Nearly all model car kits I see coming from Europe are 1/24 scale, as are the ones coming from Japan and other Pacific Rim countries, unless those are produced for US distributors who are paying the bill for tooling them. Just my thoughts. Art -
It's quite possible that the "wrapped" spare tire appeared as a "moment in time", both from pictures taken of the Winton on it's epic journey, and the restoration done with that in mind. With that in mind, the car as seen by Tonka's product development people may not have had it installed. My only memory of the Smithsonian comes from age 5. Now I was pretty observant at that age, but not given to studying details (that took years to develop), but I seem to remember the display of antique cars as being a bit "grungy" given the Smithsonian Institution's role as "The Nation's Attic" back then--it's only in recent decades that the museum has become an interpretive exhibition. With the beginning of displays of artifacts as they would have appeared when either new or active (witness the National Air & Space Museum--a part of the Smithsonian, and their incredibly realistic restorations of famed aircraft, the Spirit of St Louis and the 1903 Wright Flyer excepted--those are too important to be restored, I suspect). In 1995, as part of the commemoration of the first run of the Haynes Automobile, the Smithsonian transported the original car to Kokomo IN, for a summer-long display in the climate controlled environment of the carriage house at the Seiberling Mansion (of Seiberling Tire fame). It was obvious that the 1895 Haynes had been meticulously restored, by craftsmen who worked hard to recreate the look of such a vehicle as built, not necessarily all shiny with highly polished brass (it doesn't have much brasswork at all nor a million dollar catalyzed enamel paintjob!) The late William Harrah, who created the former and fabulous Harrah's Automobile Collection in Reno NV, did this when he acquired the legendary 1907 Thomas Flyer, winner of the 1908 New York to Paris Race. That car had resided in the hands of the late George Schuster (who drove it on that epic trek) for years, passing to New York opera tenor James Melton (one of founders of AACA) and then to noted collector Henry Austin Clark Jr--who sold it to Harrah's in the early 1960's. Instead of restoring the Thomas to its factory new appearance (as it started the race in New York City), he had his people research the car as it finished the event, in which configuration it had remained all those years. Essentially, the car was disassembled, cleaned up (prolly a lot of cobwebs all over it), then reassembled it exactly as it had been, complete with the well-known field repair of the stripped transmission gear that had been fixed somewhere in Siberia with ordinary machine screws threaded into hand-tapped holes, then hand filed roughly to the shape of the missing gear teeth!. Once the car was assembled, it was started, and run on muddy Nevada roads, where the soils apparently are very close in color to those of western Germany and eastern France, the last legs of the journey in 1908, resulting in very believable mud spatters and dust. The damaged left side headlight was left as it had been on the Champs de Elysee that victorious day, bracket bent, lens broken out. The brasswork was left to tarnish to a brown cast. Harrah's had an advantage in authenticating what they had done--George Schuster was in his 80's, still living when in the late 1960's, he was invited to Harrah's, to see the restoration, and he authenticated what had been done. This is the 1907 Thomas Flyer as seen today at the National Automobile Museum in Reno (and occcasionally shown on loan at other significant antique car museums). I suspect that this might explain why the Smithsonian chose to present the 1903 Winton in the manner described--but that it probably did not look that way in the mid-1970's when Tonka (thankfully!) kitted it. As for the diorama background, that may well be fanciful, believable, but not necessarily an accurate representation of any western town of 1903. But, who knows for sure? I don't! The few pics I have seen of it show the car in semi-desert, and that wouldn't have made for much of a diorama aimed at younger builders wanting to make a project for history class in say, middle school. Art
-
Has anybody seen this kit?
Art Anderson replied to droogie's topic in General Automotive Talk (Trucks and Cars)
Actually, it's a repop, with mods, of the old Strombecker battery powered 1/24 scale Scarab kit which dated from 1958-about 1960. Art -
NBC also covered Dr Kesling's Centennial Re-enactment with daily updates on his progress across the continent. IIRC, WNDU-TV, the station then owned by The University of Notre Dame, and located on that campus, provided the news crew that followed Kesling, as it was considered a major local story for them (LaPorte IN is only about 25 miles west of South Bend). It was a fascinating series of updates, every day for a month, on the 6:00pm news. Art
-
Yes, there was a kit produced of "Vermont", complete with the driver and his pet dog. It was produced in kit form by the unlikely source, Tonka Toys, but it is a very nice 1/25 scale plastic model kit. It's one of a series of "Diorama" kits, comes with a showcase to build as well, in two versions: The most expensive version (in the middle 1970's when they were produced) is the one sold through hobby shops, as it has a wooden showcase with glass panels (you have to build the showcase in either version), but they also made the kit in a less-expensive version, with the showcase being done in clear and black styrene plastic. In either one, the model and the diorama stuff is identical. They aren't on every streetcorner, for sure, but not completely unobtainium--the higher value one with wooden showcase will go for perhaps $120 or so on eBay, while the all plastic version may well be less than that. Noted antique and Classic Car restorer and collector, Dr. Peter Kesling of LaPorte IN restored a 1903 Winton to replicate as exactly as possible, "Vermont", then drove it from San Francisco to New York City in 2003, the centennial of the original first transcontinental run, traveling as much as possible the original route, finishing the trip exactly 100yrs to the day after the original. Art
-
Anyone remember the P M C company
Art Anderson replied to Eshaver's topic in General Automotive Talk (Trucks and Cars)
Why not cut those bombshell shaped farings off the bumper you have there, glue and putty them into the bottom lower edge of the front fenders (on the real RAnchero and lower line Fords, that is exposed painted sheetmetal, covered with a stainless steel cap on Galaxies). You can also use the Revell '57 Ranchero for an accurate chassis, and that chassis will take AMT '57 Fairlane 500 suspension, wheels and tires with very little modification as well. As for an interior, combining the side panels (retrim for accuracy) and the seat from the Revell '57 Ranchero, with the dash and steering wheel AND the windshield glass from the Revell '59 Galaxie Skyliner (the glass will fit with only minor tweaking!). Also, use the piepan taillight bezels and the taillight lenses from that same Revell Skyliner, and the rear bumper as well. Just send the PMC grille/front bumper unit after you cut away the farings mentioned above out to be replated. If you are still daring--you can also cut open the PMC hood, the '59 Skyliner engine bay fits almost like a glove there as well. Art -
Anyone remember the P M C company
Art Anderson replied to Eshaver's topic in General Automotive Talk (Trucks and Cars)
PMC made acetate plastic promo's for Ford, Chevrolet, Plymouth in 1/25 scale, also as toys. In addition, starting about 1949, they produced nicely detailed promotional models of International Harvester trucks, most in 1/20th scale, although one of their KB tractors was done in 1/25th scale, complete with a roundnose Fruehauf 36' semi-trailer (they also marketed this combo in Mayflower Moving Van colors and markings). Additionally, PMC produced an acetate promo of the 1957 Centennial Series IH wide box pickup in 1/25th scale. PMC had the deal to do Chevrolet promo's from about 1953 through at least 1958, by which time they were doing Bel Air hardtops where AMT had gotten the deal to do the Impala HT and convertible promo's. They also produced some '55-59 Ford promo's as well, in 1/25th scale, in body styles not offered by AMT (who concentrated on hardtops and convertibles). Most interesting of their Ford promo's were their 1957-58 Country Squires, their 1959 Ranch Wagon and Ranchero. The only Plymouth promo I am aware of was their 1954 Suburban 2dr station wagon. For a few years, their Ford and Chevy promo's were done in a variety of color schemes, apparently so dealers could have a large display in the rather small showrooms of the time--so prospective buyers could see a number of different color combinations without the dealer having to have the large inventories that today's new car dealers must floor plan. PMC also made highly detailed (for the time) 1/16 scale promotional models, in acetate plastic, of IH Farmall tractors, Allis Chalmers farm tractors and construction equipment, as well as a few farm implement promo's. PMC exited the promotional model business about 1960, but then pulled out several of their promo tools and shot the models in styrene, with very plain wheels and tires, metal chassis, which they packaged in polybags with cardboard headers, selling them mostly through "rack jobbers" calling on supermarkets and drugstores, for their small toy sections--at 99-cents apiece. In their promotional model era, several of their promo's were also offered as knocked down kits (kind of following AMT's example--their 3-car assembly kits from 1953-54). As a 10-11yr old, I had several of those, my most remembered ones being a '54 Corvette and several '56 Bel Air 4r hardtops. Some of their styrene assembly kits were also sold built up in the early 60's, notably the IH Centennial pickup, which was imprinted as a promotional toy for several different companies. Apparently though, PMC was at a considerable disadvantage by being located in Milwaukee, pretty distant from the headquarters of the Big Three, while for AMT and JoHan, their's was but a trip across town. Art -
AMT 25 T Double kit review with pics
Art Anderson replied to Mr. Metallic's topic in Car Kit News & Reviews
What about the stock Model T wheels and tires? The original issue kit (fall 1961 IIRC) had these wheels molded with tires mounted, making for a very accurate wheel and tire combo. The Mid-70's modified reissue "23 T Roadster" kit had the wood wheels and rather crudely done vinyl tires. My understanding from the original iHobby announcement of this kit was that the original, hard plastic wheel/tire combo's would be back in the kit. Are they? Art -
1/25 wire wheels - help me find them
Art Anderson replied to sjordan2's topic in General Automotive Talk (Trucks and Cars)
Well, for starters, your Monogram Maserati 3500GT is the old Aurora tool, and it is 1/24 scale. Art -
Key moments in auto history
Art Anderson replied to Flymeister's topic in General Automotive Talk (Trucks and Cars)
OK, some specific cars, and the milestone they represent: 1903 and later Cadillac--the concept of completely interchangeable parts--as acknowledged when Cadillac won the prestigious Dewar Trophy for that very feature. Packard in the horselss carriage era: The H-pattern gear shift, and popularizing, for all time in the US, left hand drive. Duesenberg: The introduction in production from the start in 1921, 4-wheel hydraulic brakes. Making the modern DOHC engine a production reality in 1928-29 (the Model J). Popularizing the use of centrifugal supercharging, first at Indianapolis in 1924, then on production street cars in 1932 (the Model SJ). First car to use low pressure balloon tires, at Indianapolis in 1925. Cadillac: The hydraulic valve tappet, on their superlative V16 in 1930, along with synchromesh. For introducing the driving public to independent "Short-Long Arm" front suspension in 1933 (they beat Mercedes Benz to this, doing their's independently of what Daimler Benz was working on, and simultaneously). The all steel turret top for closed cars, starting in 1935. Dodge, in the late 'teens, for their development of the all steel body--using wood only for attachment of upholstery. Buick, beginning with the first one, in 1903, for featuring only OHV layout--Buick never built a flathead. GM in general, for introducing the first reliable mechanical fuel pump in 1928, just in time to feature them on 1929 cars--replacing the fire-prone vacuum fuel systems which required a half gallon or more gasoline in a tank right above the engine, on the firewall, and of course, making Ford's dependence on gravity fuel feed obsolete forever. Oldsmobile, in 1939, for introducing the famed Hydramatic automatic transmission--leading to a nation of "shiftless" driving. Ford, for their introduction of laminated safety glass in a low priced car, the 1928 Model A. Prior to this, so-called safety glass was glass with a wire grid inside it, just like the safety glass used regularly in fire doors in the stairwells of thousands of buildings. Ford, for their introduction of dual action (Houdaille) shock absorbers in the 1928 Model A. Ford, for their introduction of the complete use of ball and/or roller bearings in the entire driveline behind the engine, including the newly developed cushioned roller bearings from Timken in their rear axle hubs, on the 1928 Model A. Stutz, in 1927, for their "double drop" frame, which lowered the center of gravity of the upright cars of the 20's, the so-called "Safety Stutz". Auburn Automobile Company, for the 1929 L-29 Cord, which introduced the world to front wheel drive. Cornelian, for being the first to have a fabricated sheet aluminum monocoque chassis/body, AND 4 wheel independent suspension, in 1915, the body and suspension of the Cornelian entry at that year's Indianapolis 500 Mile Race having been designed by Louis Chevrolet (ever hear of him?). The double leaf spring independent suspension system was later used by Fiat in their postwar 500, and had it's finest hour in the sports cars from AC, including the legendary 289 Shelby Cobra's! Cadillac, for offering not only electric lighting, but the generator/storage battery system to support it, along with the first reliable electric self starter in the industry, in 1912. Cadillac, for popularizing the V8 engine, beginning in 1915, and in 1924, creating the first 90-degree crankshaft for mass production, making the V8 as vibration-free as any inline engine. Crosley (yeah, the lowly tiny Crosley!) for introducing the aircraft-style disc brake to automobiles. Chrysler, for their introduction of "fingertip" power steering in 1951, on the Imperial. Ford, for making the V8 engine available to the masses, and doing that with the first mass-produced en-bloc V8, in 1932. Plymouth, for introducing "Floating Power", the first successful flexible engine mounting system, in 1932 on the PB series. No longer would drivers and passengers have the fillings in their teeth jarred by the power impulses of inline 4's or 6's! Chrysler, for offering, from day one, in 1924, 4-wheel hydraulic brakes in cars meant for the ordinary car buyer. Mercedes Benz, for offering the first all wheel independent suspension circa 1933, designed by the legendary Ferdinand Porsche. British Motors Corporation, for their Austin 850 Mini, which put transverse front drive engine and driveline on the map in 1959 (OK, so this layout was first offered by Walter Christie, but save for a handful of racing cars, and dozens of fire apparatus drive units --mostly for converting horse-drawn fire equipment to motor driven, the Christie system found it's greatest proponent in the Soviet's Red Army, notably the legendary T-34 tanks of the Second World War. Subaru, for their development of the first reliable, hands-off AWD. Art -
Reference pics are where you find them--and that includes many sources. For many GM cars, it doesn't get any better than the combination of factory service manuals, and factory assembly manuals! The latter read like a super-model instruction book, showing each and every detail of the car as it was to be assembled (even down to the amount of adhesives to be used in attaching some of the trim!). Nowhere else will you find, for example (Bill Geary, are you listening?) column shift linkage, its shapes, and how it is connected to both the gearshift shaft on the steering column and to the shifting arms of the transmission. This is all laid out in very clear drawings, often in multiple views, all for training assembly line workers on the then-new cars they will be building. Dealer brochures have a very real place, but be aware that many 50's and 60's brochures show the cars in question in dimensionally altered artwork, so they aren't all that good for proportioning out a conversion. By the same token, the commercial artwork showing engines more often than not, shows incorrect colors, the artwork meant more to convince you to buy, than to be an accurate representation. The same also can be true of interior appointments, particularly given that brochures were underway before many final decisions were made as to upholstery patterns and/or colors. One can build a great database of knowledge from such notable magazines as Collectible Automobile, and the former Special Interest Auto's (and the subsequent publication from Hemmings, Hemmings Classic Car, as well as Hemming's Muscle Car. Oh, and don't overlook Cars & Parts magazine as well--often there are great pics in that mag. It should go without saying that taking lots of pics of cars, on the street, at the dealer's, or at shows--while a digital camera of serious quality might be pricey, the pics are free--no developing or printing charges need apply, so take them by the dozens of any car you want to model--don't worry about "beauty shots"--go for pics that tell YOU what the areas of the car look like that you don't necessarily see well in magazine or advertising photo's--you will be glad you did. Of course, online pics are a great resource, but often they need the backup that only a large collection, garnered from extensive research can give. Don't be afraid to keep looking, that elusive shot of that hard-to-see detail may well show up online tomorrow! And, above all, read--read as much as you can about the car in question. In such mags as CA, for example, there are often gems of information (such as, did you know that ALL '58 Chevies are the same length--no Virginia, the Impala wasn't longer than the lower line Bel Air, just unique rear panel, decklid and top were exclusive to the Impala that year!). It was by reading that I learned the various body lines from GM, Ford and Chrysler--and how sheet metal got shuffled around to make the plethora of body styles the Big 3 produced in their heyday. Phew, there I think I've covered a lot of it--!!!! Art
-
Aluminum Model Toys produced just one cast aluminum car, the '48 Ford Tudor sedan (I had one as a 4yr old!). It wasn't a bank though, just a promotional model. They were meant to be displayed in Ford dealerships with a placard reading "Watch The Fords Go By!". It was the only cast aluminum toy car made by AMT though (even though aluminum was mere pennies a pound back then, due to the wholesale scrapping of some 400,000 surplus aircraft from the Army and Navy following WW-II). It was a full diecasting, unlike the Master-Caster version of the Fordor, which was slush cast, as were Banthrico's of the same era all the way out to the late 1950's. AMT started producing plastic promotionals for 1949, in acetate plastic, with pressed steel chassis and plated steel stampings for bumpers and grilles, as well as plated steel stamped window "glass". Art
-
Yeah, I was a newly minted HS graduate when AMT announced the Turnpike sets. I did, however, become acquainted with Budd "The Kat from AMT" Anderson when he was at the National Rod & Custom Show at the Murat Shrine in Indianapolis, put on simultaneously with the 1962 NHRA National Drags out at Indianapolis (now O'Reilly) Raceway Park that year. (FWIW, that was the weekend that Revell introduced their first modern model car kits: Roth's Outlaw, the '56 Ford F100 pickup, and Mickey Thompson's Challenger I) Art
-
Removing Chrome ?
Art Anderson replied to Mark R's topic in General Automotive Talk (Trucks and Cars)
Yes it will. However, it's the clear base coats that made for "gloppy" chrome plating on those model car parts--not the vacuum metalizing itself--that is but a few molecules thick. To recover the little details on plated parts when stripping, removing that clear coating will reveal details that most of us have never seen before--that is why I use sodium hydroxide or products containing it. Art -
ebay Jo-Han POLICE PURSUIT CAR
Art Anderson replied to tuffone20's topic in General Automotive Talk (Trucks and Cars)
Thousands were produced in the time frame 1979-1992 or thereabouts, when JoHan reissued the police car in their "USA Oldies" series. They weren't all that popular as model kits then, mostly given their 4dr body style, so it's very possible to find them even today, although they aren't on every streetcorner. Many may not recall, but about the time that JoHan started this series of reissues, Walmart, then a chain of small town discount department stores (their move to the big cities was yet to come) carried massive stocks of JoHan kits--the '68 Plymouth police car among them. Walmart, even then, would have accounted for a minimum of 20,000 or so kits, just to stock their stores that existed at the time, and they had them on the shelves in half dozens to full cases back then. Like so many other discontinued model car kits, once the kit goes away from the mfr's lineup, eBay charlatans proclaim it to be "RARE!" whether or not the item was in production for years, or was a one-year, one-hit wonder. Give those characters a pass, that kit should be available for far less money, for those patient enough to slow down, and continue their search. Art -
Removing Chrome ?
Art Anderson replied to Mark R's topic in General Automotive Talk (Trucks and Cars)
My old standby for decades is lye, known also as sodium hydroxide. Lye is death to aluminum, which is what model chrome plating is--micro thin aluminm applied to the model parts. Lye will not only strip the aluminum, but will also get rid of the base coat that all vacuum-platers use for both adhesion and to give a wet-look shine to the plastic parts. That allows you to see all the details molded into the parts, and also to be able to polish out mold parting lines and such without any "ghose" of the edge of the basecoatings. Lye is hazardous, so use carefully, use PPE (Personal Protective Equipment), like protective gloves on your hands (lye will eat your skin away, burning you), and eye protection is an absolute MUST. But, used with caution, basic following of the instructions on the package, it works very well, and is biodegradeable. Lye is the active ingredient in stuff like Easy-Off oven cleaners, drain openers, and is available by itself in powder (crystal) form, as "Lewis Red Devil Lye" (with this, follow the directions to the letter on the package!). Oven cleaner and Purple Power/Castrol SuperClean are used full strength, and will strip the "chrome" and base coatings in about 10 minutes. Lewis Lye can be mixed stronger, I find it can strip the chrome in seconds, the base coats become soft in a couple of minutes. An old toothbrush works well to scrub away base coats from nooks and crannies. Always rinse the parts thoroughly with clear tap water, and lay out to dry on clean paper towels. Been doing this since the late 1960's, with nary an accident, and I know it works. Art -
One year after the start of the 1904 Knox project
Art Anderson replied to Art Anderson's topic in WIP: Model Cars
The Knox project is a composite of a couple examples I found online--not very many decent pics exist (but then not many Knox Waterless cars or trucks exist anymore either--probably about half a dozen or so). They were all chain drive, but in two layouts, some had a single drive-chain system, utilizing a single sprocket in the middle of the rear axle having a differential enclosed in it, while others were built with a three-chain system, one chain connecting the crankshaft/transmission drum (Knox used a planetary, contracting band transmission not unlike that of a Model T Ford--and for that matter, just like the basic layout of a GM Hydramatic of 3-4 decades later) to an intermediate "jackshaft", which then transmitted power to the rear wheels by individual sprockets and chains on each end of both the jackshaft, and on each wheel hub. In this setup, the differential was in the middle sprocket of the jackshaft, which shaft was suspended by bearings in mid-frame. I've chosen to to this latter style, just like the look of the very exposed drive chains outboard of the frame, I guess. Every 4-wheel Knox I've seen pics of (Knox also made a number of three-wheeled cars and fire apparatus tractors) had the fore-and-aft spring systems I've done on my model. This is a common trait of the Knox cars of which I found pics. It's a very common early Horseless Carriage suspension--the most popular car with them was the legendary Oldsmobile (My Merry Oldsmobile of song and vaudeville) Curved Dash (produced from 1902-1908). These very long leaf sprngs are bolted to the underside of the frame rails, and extend forward to the front axle, and rearward to the rear axle, functioning as cantilevered quarter-elyptical leaf springs. Ertl Collectibles made a 1/25 scale diecast bank of a "1904 Knox Waterless Truck" which they did with full-eliptical leaf springs, three at each end, two at the ends of the axles, one in between those across the end of the frame--but I cannot find any pics to verify if that was indeed done for real, or did Ertl take some license there? The Ertl diecast is the model that started all this--I was just going to enhance it, superdetail it, but found way too many problems with it, mostly that Ertl made the diecast far too narrow (about 42" treadbase--the width between the wheels--where the real ones are much close to the almost standard 56" treadbase of horsedrawn vehicles and early autos of the time. But, the Ertl model has a body style I really like, so that is gonna be replicated in wood and styrene: This is the inspiration for the chassis layout I am doing But this pic really got me to thinking about doing my own, instead of trying to rework the Ertl diecast One of very few pics showing a Knox engine closeup (and which made me decide to simplify the cylinder a little bit--I estimate that there are at least twice as many cooling pins in that real engine, and they were less than half as thick as what I used--but I have 550 of those pins in my cylinder The truck body I will build will look like the restored truck up top, except that it will have a screen-side express body (think a rudimentary pickup truck box) with a canopy over the bed and extending out over the driver's area, with rollup curtains for weather protection, but no side curtains, not even a windshield for the driver--but then a delivery vehicle of that time period almost never saw the open road in the country, being a city delivery type truck, and likely never saw more than say, 15mph. That is also why the solid rubber tires. Art -
One year after the start of the 1904 Knox project
Art Anderson replied to Art Anderson's topic in WIP: Model Cars
It's turning out to be a composite of several Knox trucks, actually