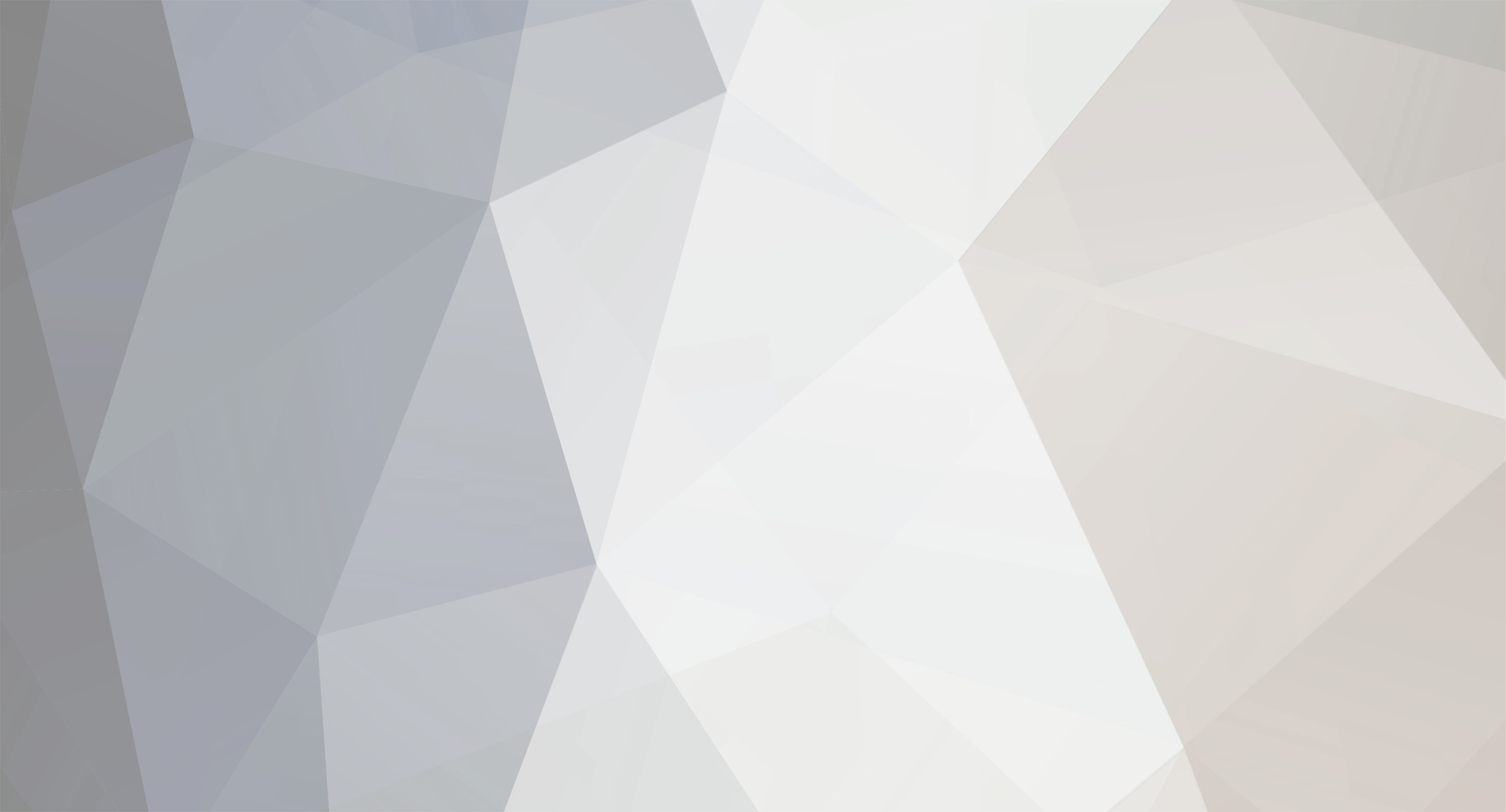
Art Anderson
Members-
Posts
5,052 -
Joined
-
Last visited
Content Type
Profiles
Forums
Events
Gallery
Everything posted by Art Anderson
-
As an addendum, famed Los Angeles race car and engine manufacturer, Harry A. Miller, producer of a number of highly successful straight 8 and inline 4 cyl DOHC racing engines (and the cars to put them in) back in the 1920's and early 30's, built, in 1932, a pair of 4WD cars for Indianapolis, which were powered by 300cid DOHC V8 engines which had a then exotic center-of-the-cylinder-head (even though Miller engines almost NEVER had detachable heads) design. The cars and engines ran at Indianapolis during the so-called "Junk Formula" which drew production "stock block" engines into the 500 for a couple of years in the depths of the Great Depression. While those two DOHC V-8 engines didn't win the 500, they captured the attention of Ford's racing engineers in the summer of 1963. Ford Motor Company located one of those engines at a funeral home & car museum in Frankfort IN, owned by an acquaintance of mine back then, William Goodwin. Goodwin was a major Indiana antique and classic car collector, with a side interest in old Indianapols racers. Ford arranged to rent that engine from Goodwin's, took it back to Dearborn, where they studied it, and adopted Miller's pioneering intake layout, which helped result in the unique and still somewhat exotic-looking layout of Ford's 4-cam Indianpolis engine. Art
-
Yes. Although if you look really closely--the injectors are in the same place as on the Indianapolis configuration. That cannot change with the 4-Cam Indy Ford V8, simply because the intake passages are in the middle of the cylinder heads, between the cam towers. What the builder of this car did was to swap the heads side-to-side, which put the exhaust cams and ports outboard, as opposed to inboard above the center "valley" of the engine block. I want to say that Ford actually experimented with that setup, but determined that the tuned headers ("tuned" as in each pipe in the header is exactly the same length, which explained the very convoluted "bundle of snakes" look) actually added more HP and rpm's, due to better, more balanced breathing. Art
-
Tamyia TS-13 is back
Art Anderson replied to martinfan5's topic in General Automotive Talk (Trucks and Cars)
YESSSSS!!!!!!!! Art -
Will GM's problems ever end?
Art Anderson replied to Harry P.'s topic in General Automotive Talk (Trucks and Cars)
I do think, however (with all due regard to the various situations) that much of this is driven by the Trial Lawyer's Industry. Art -
1937-39 Opel Admiral Kabriolet Updated 9/21/14
Art Anderson replied to Art Anderson's topic in WIP: Model Cars
Yes, upon deeper research, Opel used a modified version of the Chevrolet "Knee Action" front suspension, A/K/A the Dubonnet System. Art -
Will GM's problems ever end?
Art Anderson replied to Harry P.'s topic in General Automotive Talk (Trucks and Cars)
Bring back the Model T! Dad always used to swear that all Grandpa needed for his Model T tool kit was a monkey wrench, a pair of slipjoint pliers, a roll of baling wire, and a little sack of oatmeal. (why OATMEAL? Easy, that was the original radiator StopLeak!). Life must have been lots simpler a century ago, huh? Art -
Well, the '63 Indy Lotus Fords used modified 260cid stock block engines, with pushrod heads, and they had that bunch of snakes look to their headers, albeit splity between the two cylinder heads having their exhaust ports in the conventional, outer side of the heads.
-
Can brass tube be annealed for bending?
Art Anderson replied to LDO's topic in Model Building Questions and Answers
Most certainly, any K&S brass can be annealed--just heat up to dull red, let cool, and it's softened. But I would wonder, would it not be easier to anneal and bend 1/4" brass rod, seeing as how the very thin-walled K&S tubing is very prone to breaking (as in tearing apart) if bent at sharp angles. Art -
The 4-cam Indianapolis Ford V8 was done at least 4 different times back in the 60's in 1/25 scale. The first one in kit form was in the 1965 Lotus Ford Indy winner, by Industro-Motive (IMC). However, given that their kit was simply a retooling of their 1963 Lotus Ford kit, the tub was too narrow for their designers to stuff an accurate 4-cammer in it, so they made the heads too small, and much too plain (little if any surface detailing). The second was by AMT, who introduced their 1963 Lotus Ford with an optional 1964 4-cam, but it lacked the "bundle of snakes" exhaust system, instead having a set of individual exhaust stacks, which were used on test engines at Ford, and in a test mule Lotus 34 (the upgraded Lotus 29 chassis from 1963). IMC also featured a 4 Cam in their earliest version of the Ford GT40, I believe. The original plan was to run that engine at LeMans, but I don't believe it made the grade. And then, of course, there was the MPC version, which is by far the most accurate model of that engine in 1/25 scale. Art
-
How to weather chrome?
Art Anderson replied to clovis's topic in Model Building Questions and Answers
You might bear in mind that there were just three components on a '30-31 Model A that were chromium plated--the front bumper, and the two rear bumperettes. EVERY other bit of brightwork was polished stainless steel! Ford was the first automaker to use stainless (Ford called it "rustless steel") for automotive trim. Made by Aleghany Ludlum Steel Corporation, the stuff simply will not rust at all, but it will turn a bit dull, and the minute surface scratches from years of polishing will show up with age as well. Art -
1937-39 Opel Admiral Kabriolet Updated 9/21/14
Art Anderson replied to Art Anderson's topic in WIP: Model Cars
The chassis, while a very nice set of pieces, got really complicated with the strangest independent front suspension I've ever seen! What looks like a front axle is really nothing more than a tubular crossmember, bolted to the bottom of the frame rails, and trails rearward at its outer ends. On each end there is a very large "cannister" which holds (inside!) whatever spring arrangement was used (can't seem to find any information as to just what the system was inside there, but no matter. There are a total of 10 pieces to the front suspension and steering, the axle/crossmember thingie mentioned above being in three parts. There's a "scissors-like" double arm attached at either end, which captures the ends of the tie rod, and then a single, rather heavy arm extending forward from that which has the spindle and kingpin arrangement at the front end (wonder how that fared in military service, seeing as how several thousand Admirals were commandeered by the German Army for conversion to ambulances, and used as officers' staff and command cars?). In any event, everything there assembled smoothly, once I finally figured out just how the stuff laid out (instruction drawings weren't very clear on that!). Once finally assembled, it was time to test fit the chassis to the underside of the body, and "CLICK"! It fits like a glove, very precise indeed! Hmm, it's getting there (and that's half the fun, according to those old Cunard ocean liner ads!) Art -
1937-39 Opel Admiral Kabriolet Updated 9/21/14
Art Anderson replied to Art Anderson's topic in WIP: Model Cars
This weekend's project is two-fold: First was to install body welting, which was used for years, back in the days when fenders were bolted on to the sides of car bodies. Welting appears as a small "rib" along those joints, actually being a strip of PVC-impregnated cloth wrapped around cotton cording and pinched into a flange which can be trapped between the mounting flanges of the fenders, and the adjoining body panels. I used some ,020" styrene rod stock, which may be a bit heavy, but that's about as small a size that I felt comfortable working with, given the liquid cement I used. At any rate, it does show up quite prominently in pictures of the real cars, so probably I'm not all that far off base. In addition, I've rescribed (deepened) the very shallow trunk panel lines, and cut in the bottom panel line which wasn't tooled very well (given it's location on the curved trunk panel, I'm not surprised at that!) Next up, the completed chassis! Art -
The 255cid 4-cam Ford Indianapolis V8 had a sound all its own back in the 60's. The very high rpm's (IIRC, that engine was capable of 9,500 rpm) coupled with the legendary "bundle of snakes" tuned headers which exited into that pair of megaphone tailpipes made for a hair-raising, shrill scream on the straightaways at Indianapolis. They were, to put it mildly, fairly labor-intensive to start up from cold though: Where the Offenhauser required but the driver and a single crewman on the remote electric starter, the 4-cam Ford took four--Driver, the starter operator, and a crewman on EACH side of the engine. These latter two crewmen each had a trigger-operated oil can, which was used to squirt raw methanol into each injector stack, and in the correct firing order in order to prime the engine sufficiently to fire up! Art
-
That's the old Hudson Miniatures kit, which consisted of wood, Strathmore board (a very fine grade of card stock) with wheels/tires, radiator, headlights and a few other smaller details molded in acetate plastic. Hudson Miniatures was a line of 1/16 scale kits introduced by Oscar Kovaleski Sr. in 1948, and lead to the founding of the original Auto World hobby shop and mail order business made famous to thousands of Baby Boom generation model builders back in the 1960's/70's, by his son, Oscar Jr. Art
-
Having been an avid Indy car builder back in the years 1966-84, and built more than one car using the 4-cam Indy Ford engine, MPC's is the way to go for 1/25 scale, as it's the only really accurate rendition of that engine. As said in another posting, it's one of the two engines in the MPC Olsonite Eagle Indy car (Dan Gurney, Dennis Hulme). Art
-
Round 2/MPC Arnie Beswick "Boss Bird"?!
Art Anderson replied to MitchP's topic in General Automotive Talk (Trucks and Cars)
Arnie's probably pretty well acquainted still with Tom Lowe, owner of Round2, which would go back 10-15 years when Lowe owned Playing Mantis, who produced the Johnny Lightning line of 1/64 scale diecast cars. There was a miniature of Beswick's -62-'63 Tempest AWB funny car in the JL line. Beswick would stop in at Playing Mantis on occasion--met him there once when he stopped by on his way home, with a load of Hoosier racing tires in his pickup (Hoosier Tire is only a few miles south of Mishawaka/South Bend, where Playing Mantis was located. Art -
1937-39 Opel Admiral Kabriolet Updated 9/21/14
Art Anderson replied to Art Anderson's topic in WIP: Model Cars
It's the Admiral, Opel's luxury car (captured fully 25% of the German luxury car market 1937-39). The Kapitan was a smaller car. Art -
1937-39 Opel Admiral Kabriolet Updated 9/21/14
Art Anderson replied to Art Anderson's topic in WIP: Model Cars
I'm not sure I'd wait very long to pick up this kit, were I you; given that ICM kits are produced in Kiev Ukraine, where there's a lot of turmoil these days! The supply (more kits) could be a bit questionable. Art -
1937-39 Opel Admiral Kabriolet Updated 9/21/14
Art Anderson replied to Art Anderson's topic in WIP: Model Cars
As promised, some in-progress pictures, and some description: ICM did this kit in 1/24 scale, following their first release of the subject in 1/35 scale for the military modeler. A bit of reason why: With the onset of World War II, the German Wehrmacht and Luftwaffe commandeered a lot of larger cars for use as staff cars, even for conversion to ambulances and other support vehicles. Many, if not most, of the 1937-39 Opel Admirals produced (over 6,400 were built) suffered this fate, leaving only a few behind, probably kept hidden by their owners for the duration. But in 1/24 scale, this kit reaches a whole new audience--us. In asssembly so far, I am impressed by the outright precision of this kit--while a few parts have "interesting" mold parting lines (particularly at the bottom rear edges of the rear fenders--don't understand why, but it is what it is), they are very easily removed. On the rear fenders, a bit of needle file work, followed by some 400-grit sandpaper, and they came out very smooth. I did take the time to round off, slightly, the lower edges of all 4 fenders, as Opel stamped those with a small radius rolled edge at the factory. Even though the body shell is multi-piece assembly (floor with the rear fenders molded in as a part of it along with the inner halves of the front fenders), a pair of body sides which include the outer front fender halves, the cowl/firewall/windshield frame, and the trunk section) all parts assembled very precisely, the only noticeable gap being the rear edges of the rear doors, but even that was easily reduced to a more proper width. A little bit of test fitting beforehand showed me that the body could be pre-assembled and the interior panels, dash, seats and details installed after painting, which is often NOT the case with multiple piece body shells. All parts are molded in a very stiff (but easily trimmed) grey styrene, and the floor panel in my kit was ABSOLUTELY flat and true, which is essential on a kit such as this if it's to build up with all 4 wheels touching the table top. Liquid cement applied with my Flexi-File needle tip "Touch & Flow applicator made for very clean assembly, with a couple of drops of gap-filling CA in the inside of the joint between the edges of the floor and the inside of the lower edge of the body panels for added stability. The chassis is also multi-piece, necessary given all the "Swiss Cheese" holes in the side rails, which themselves are 3-piece, each rail having two short "box sections" which are separate parts, also with lightening holes. I again went "off sequence" with the frame, opting to assemble the X-member into the frame rails rather than onto the bottom of the floor, for ease in adding details, along with better realism. I simply used the locating slots on the bottom of the floor, and assembled the X member sections to the frame with gap-filling CA. A bit of block sanding on the bottom side of the joints, and they will look one-piece with the side rails (and yes, ICM allowed for assembling the exhaust system into the frame after the X-member is installed! This ends today's installment! Art -
Just fo clarify: It was A. J. Watson who was the legendary Indy roadster builder, and who built Parnelli's #98, which first ran Indianapolis in 1959, as a virtual twin to the roadster that carried Rodger Ward to Victory Lane (Ward's 1959 Leader Card Spl. is also a part of the Speedway Museum collection. Art
-
Yes, it was Dean Jeffries who did so many of the iconic, flashy, literally show-car-appearance USAC Championship cars back in the early to middle 1960's. If you ever get the opportunity to visit the Indianapolis Motor Speedway Hall Of Fame Museum you will see one Offy roadster still wearing it's original Dean Jeffries paintwork and graphics: A. J. Foyt's 1964 Indy winning Sheraton-Thompson Spl albeit faded from a season of racing in the bright sun, plus the obligatory chips and scratches from duking it out nose-to-nose that season. In addition, "Ol' Calhoun" is there, fully restored to its 1963 race day appearance. Art
-
Detailing Die-Cast Kits?
Art Anderson replied to bigbluesd's topic in Model Building Questions and Answers
From my experience (and 10-12 yrs ago, I was deeply involved in the development of diecast model cars at Johnny Lightning), the biggest reason you see such soft edges and rather fuzzy details on most popularly priced diecast models isn't in the tooling, but rather the very heavy coats of paint on them. Disassembling them, stripping all that paint off often will reveal surface detailing nearly as sharp and crisp as on a plastic kit. Art -
1937-39 Opel Admiral Kabriolet Updated 9/21/14
Art Anderson replied to Art Anderson's topic in WIP: Model Cars
1/24 scale -
I bought this kit a month or so ago in Indianapolis, figuring that if ICM had an established reputation among the Armor building crowd, their stuff must be pretty good, and so far I'm very pleased with the fit and finish of all the parts in this kit! It's very precisely done. A lot has been said online about its having a multipiece body, and indeed the instruction sheets say to assemble the interior parts to the floor and body sides before assembling the body shell (ala' Revell from the 1950's), but I decided to see if the body could be built up and the interior installed later--and YES, it can! Oh, and the body seams resulting are quite tight, although a bit of finessing had to be done to keep the door lines at the rear edges of the rear doors from appearing too wide, too prominent, but with a Fiexi-File liquid cement applicator along with some reinforcement in hidden areas with gap filling CA glue, those are now pretty unobtrusive. Pics tomorrow when I have a bit more time! Art