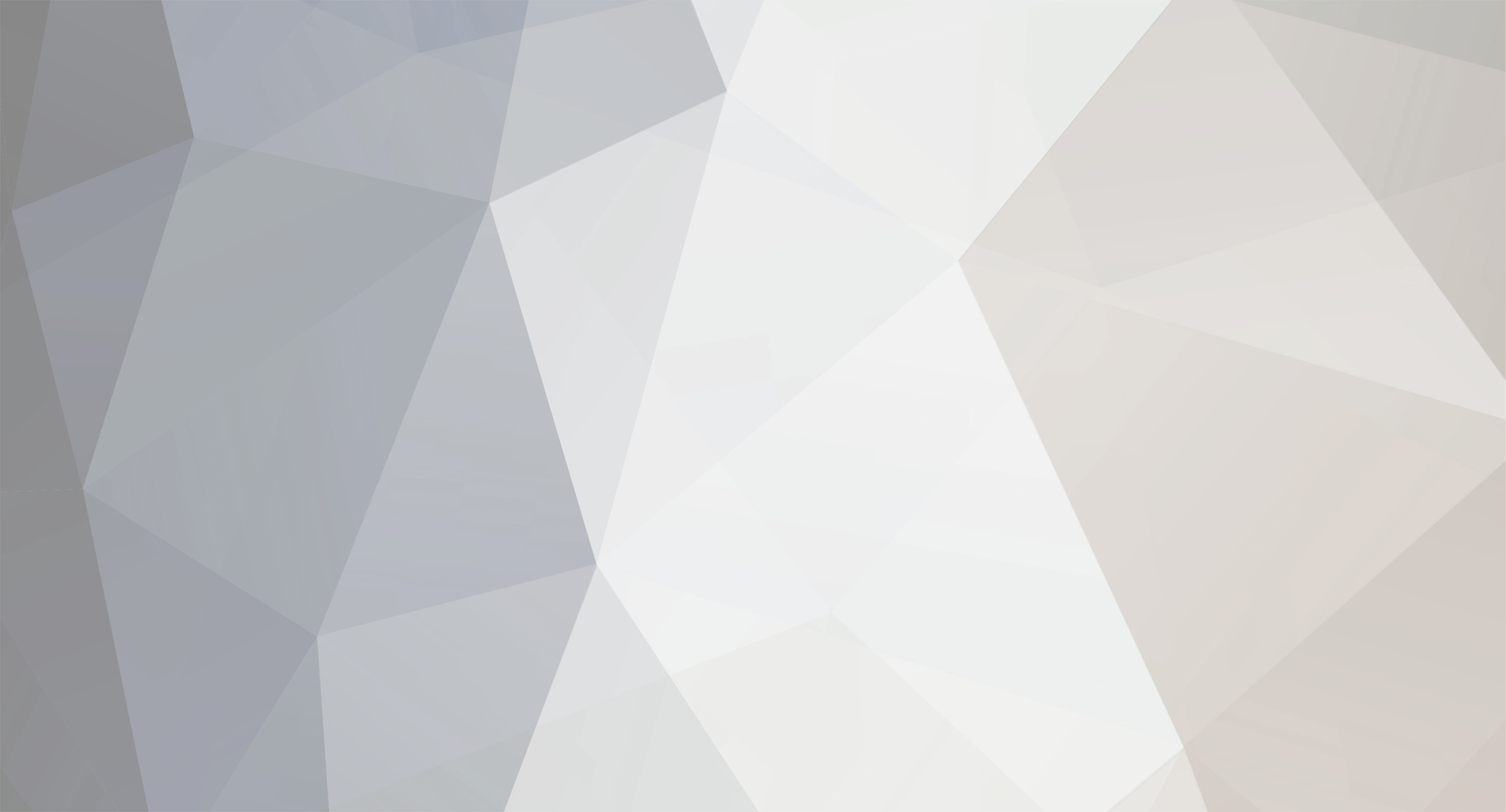
robdebie
Members-
Posts
386 -
Joined
-
Last visited
Content Type
Profiles
Forums
Events
Gallery
Everything posted by robdebie
-
We bought one with a small group from our club, and have it's been doing rounds since then. The thing is clunky, but I would say it works well enough. The chrome ball knob needs to be in exactly one position, in my experience - I think the photo shows the correct one. And I never use the (what I think is) ball bearing holder, the first metal-colored thing from the bottom. Leaving it off gives you a flatter and slighter larger area to work with. Rob
-
CA-glue-induced severe cracking of polystyrene
robdebie replied to robdebie's topic in Model Building Questions and Answers
Thanks all for the replies so far. A small update: I planned to do some experiments, with bent / folded plastic card strips, but I ran out of Zap thin CA, my prime suspect. The cracks in the tank trailer are repaired, and no new problems have surfaced. Rob -
I had noted before that small polystyrene strips would crack severely if I bent them first, then glued them on a model's curved surface. Say a 1 x 1 mm strip would break up in 2 to 3 mm segements, and the segments themselves would also show many more tiny cracks. It difficult to photograph, so I can't show it (yet). Yesterday I made an extension for a 1/25 scale tank trailer (MPC / Lindberg). I first extended the top side of the tank forward with five plastic card 'stringers'. Then I cut a piece of 1 mm plastic card to the required (complex) shape, then pre-curved (rolled) it on the edge of a table. The edges were glued together to form a tube / pipe, and I installed an elliptical bulkhead internally. Lastly added the curved front face of the tank, as an oversize piece, glued on with Zap thin CA, purple label. And then it happened: severe cracking of the bent plastic card - something I had never experienced before. Is there anyone who understands what's going on here? I have a feeling it's not happening with all CA glues that I use, I should do more experiments. Rob
-
Can someone give me a painting tip, please?
robdebie replied to dazzed's topic in Model Building Questions and Answers
You are right: I meant to say the atomization principle is crude, not the manufacturing or finish. Rob -
Can someone give me a painting tip, please?
robdebie replied to dazzed's topic in Model Building Questions and Answers
I forgot to point out that your 'new expensive airbrush' is likely a large part of the problem. It atomizes the paint too fine, creating a very large total surface area of the atomized paint. That in turn causes a lot of thinner evaporation in the short distance between the airbrush and the model. The paint arrives thicker (more viscous) on the model that it was before you added thinner, and is so thick it cannot flow out to a smooth paint layer. Hence the orange peel. One solution is a cruder cheaper airbrush, that atomizes coarsely - see the 'Donn Yost' technique as mentioned in my previous reply. Rob -
Can someone give me a painting tip, please?
robdebie replied to dazzed's topic in Model Building Questions and Answers
Yet another route to try: the 'Donn Yost' paint technique, as demonstrated here: https://www.youtube.com/watch?v=lCKZ_fo4eW0 I had 30 years of problems like you describe, but this really works well, with all of the brands of enamel paint that I have in stock. No polishing, no clearcoat, simply smooooth paint ? The Paasche H, or a similar *crude* airbrush, is the key ingredient I believe. You need to crank it wide open for the final coat. Rob -
Let's See Some Glue Bombs!
robdebie replied to Snake45's topic in General Automotive Talk (Trucks and Cars)
I made a Blues Brothers Pinto Wagon from a glue bomb of the 46 year old MPC kit: Rob -
I have exactly the same experience. I always use Future under the decals, although I recently started using Tamiya decal adhesive. The edges of the clear film curl up a bit, and need coaxing down, usually with a little bit more Future. But other than that, I would give them the same note as the average silkscreen printed kit decal sheet. I'm happy with them. Here's another model done with SpotModel decals, the 1976 F-16 model by Revell. Rob
-
THe good news is that a newly made custom decal sheet will look 10x better than the original decal sheet, I'm sure of that! Here's a sheet that I designed recently, and was printed by Spotmodel: I do custom decal assignments too, a few every year. Here's a page about that service: https://robdebie.home.xs4all.nl/models/customdecals.htm It has six examples of decal projects, that hopefully make clear why drawing decal art takes considerable time. It's like Dave Van asked: "Q is are you willing to pay for art and printing??".. Rob
-
Chris (who started this thread), could you check the power of the fan? It's a simple indicator of the air flow. In my current paint booth, I use a ~75 Watt blower from a kitchen hood, and it's marginal if I'm using my air brush wide open, like in the 'Donn Yost' technique. I have a 150 Watt blower waiting to be converted into a paint booth. Now that's maybe a tad too much, but better too much than too little. Rob
-
Peterbilt 359 'needle nose' conversion
robdebie replied to robdebie's topic in Model Building Questions and Answers
Peteski, that sounds like how I learned how an Alps printer worked from you and others, some 20 years ago ? One more comment is that the 'sphere and cone' markers are a bit misleading, the real supports are way bigger. In this case the real ones overlap the lower side and rear side of the louvers. Please note that I'm very much a beginner with this, I started doing the supports maybe a month ago, and applied the new knowlegde to maybe 10 parts. I don't have a printer myself, a club member does the printing for me. But having control over the supports is a great plus, it improved the results a lot. And it saves the club member some time too. Rob -
Peterbilt 359 'needle nose' conversion
robdebie replied to robdebie's topic in Model Building Questions and Answers
I don't have total control over the supports. In the software I'm using (PrusaSlicer), you put a small sphere where you want a support, and it has a cone that defines the direction of the support. But the rest is up to the software, and it sometimes has a mind of its own. Rob -
Peterbilt 359 'needle nose' conversion
robdebie replied to robdebie's topic in Model Building Questions and Answers
Peteski, that is an excellent question. I had to learn a thing or two on the subject of supports before the part came out right (out of the printer of a club member). I added the supports manually, because automatically generated supports did not yield good prints. It's my own interpretation of what was required, and I went for 'safe' regarding the thin louvers, giving them 10+ supports each. The overall result was a true forrest of supports. But that's mainly because this a strange part to print. The part now printed near perfect, but it was difficult to get all the supports off. I worked my way down from the grille's top, and maybe spent half an hour. I had positioned the supports on the louvers such that I could get to them with a razor blade saw from the front (as you see in the picture). I would then snip away the supports from the rear side. Still I broke three louvers, but the breaks are so brittle that they fit perfectly back together, and could be glued invisibly with thin CA. Rob -
Peterbilt 359 'needle nose' conversion
robdebie replied to robdebie's topic in Model Building Questions and Answers
Here's a follow-up on the 'needle nose' conversion. It took a few attempts to get the grille printed correctly. The first parts shown on page 1 had many problems. The next print is shown on the left of the photo below. The louvers were made 0.45 mm thick instead of 0.3 mm, and still look thin enough to my eye. Each louver had about eight print supports. But I forgot to add supports to the frame above the louvers, so that came out deformed. Another problem that kept coming back were 'dog ears' at the bottom of each printed part. The next print was perfect! I added extra supports at the 'dog ear' corners, and that solved the problem 95%. A bit of sanding solved the remaining 5%. That part of the conversion is done, next is the hood. I will do a 3D design of that part too. Rob -
Fan set up for a paint booth
robdebie replied to porschercr's topic in Model Building Questions and Answers
Here's a great webpage on the subject: https://modelpaint.tripod.com/booth2.htm Rob -
Fan set up for a paint booth
robdebie replied to porschercr's topic in Model Building Questions and Answers
Simply judging from the fan's power, it won't be strong enough. In my current paint booth, I use a ~75 Watt blower from a kitchen hood, and it's marginal. I have a 150 Watt blower waiting to be converted into a paint booth. I too use (acrylic) lacquers, and you really need a good paint booth for those. Another thing is the ducting. The flow resistance it creates is expressed as 'back pressure' and reduces the flow. Search on 'blower back pressure graph' or similar to see what I mean. Using OSHA rules for paint booths, plus the dimensions of your booth, you can calculate the required flow. Rob -
Early 60s Indycars -- Watson Roadsters
robdebie replied to Matt Bacon's topic in Model Building Questions and Answers
Here's a great build report of the Lotus-Ford on another forum: https://forum.f1m.com/viewtopic.php?t=33637 I would try to replace the thick glass with a vacform piece. Rob -
Well..... I bit off more than I can chew, in several ways.. At the start, I cut the kit in 10 pieces. I then had quite a problem getting all the parts properly aligned again. And now that that's sorted, I find that playing car designer is not as easy as it looks.. The model looks kind of weird. Maybe the wheels/tires are too big? Possibly the rear wheels need to move forward? The real car had its trunk lengthened 12 mm (in scale), maybe that helps? I'm kind of stuck. Rob
-
I have a WIP report of the AMT custom 1949 Ford, with a section on the flathead engine: https://robdebie.home.xs4all.nl/models/49ford.htm Rob
-
Yesterday I attended a model show in Geel, Belgium, organized by KMK Mol model club. One of the highlights was a stand by 'Diolex Production' , of whom I had never heard before. It's a Ukrainian company producing 3D and resin model cars and accessories. On the table were various American, European and Asian car models, all looking very nice. The owner, Dmytro Oleksenko, told me he produced 230 different cars! American cars are in 1/25 scale, the others in 1/24 scale. He runs eight 3D printers. He said he sells on Ebay. I can't find a company website, just a Facebook (blech) discussion group that doesn't show the catalog: https://www.facebook.com/groups/DiOlexProduction/ The Euro/Asian stuff is sold by Hiroboy: https://www.hiroboy.com/shop.php?p=each_manufacturers&id=193&page=4 If I check Ebay, I get a message saying: "Ths store has no inventory available in your location". Thank you very much. But I found one example of the products they sell, '68 Caprice: https://www.ebay.com/itm/256384936401 Rob
-
Custom Local police Department Decals
robdebie replied to jjsipes's topic in Model Building Questions and Answers
I'm happy to see that my cost estimate isn't far removed from theirs: they list a '$100 Exclusive Decal Fee' for single-user custom decals. It's reduced to half of that if they can add the decals to their catalog, but I don't have that option. Rob -
Custom Local police Department Decals
robdebie replied to jjsipes's topic in Model Building Questions and Answers
I would guess it's 2-3 hours of drawing + communication, plus printing. Roughly 100-120 US$? I realize that's triple the cost of the kit, but that's the reality of custom decals. I do a couple of decal projects every year, here is more information: https://robdebie.home.xs4all.nl/models/customdecals.htm Rob -
I am ready for 2k
robdebie replied to Mike 1017's topic in General Automotive Talk (Trucks and Cars)
The motor's power will give you a rough idea of its 'pumping' capacity. I use a 55 Watt ex kitchen hood blower, and it's not enough when I paint 'full blast'. I have a 150 Watt blower waiting to be installed. Rob