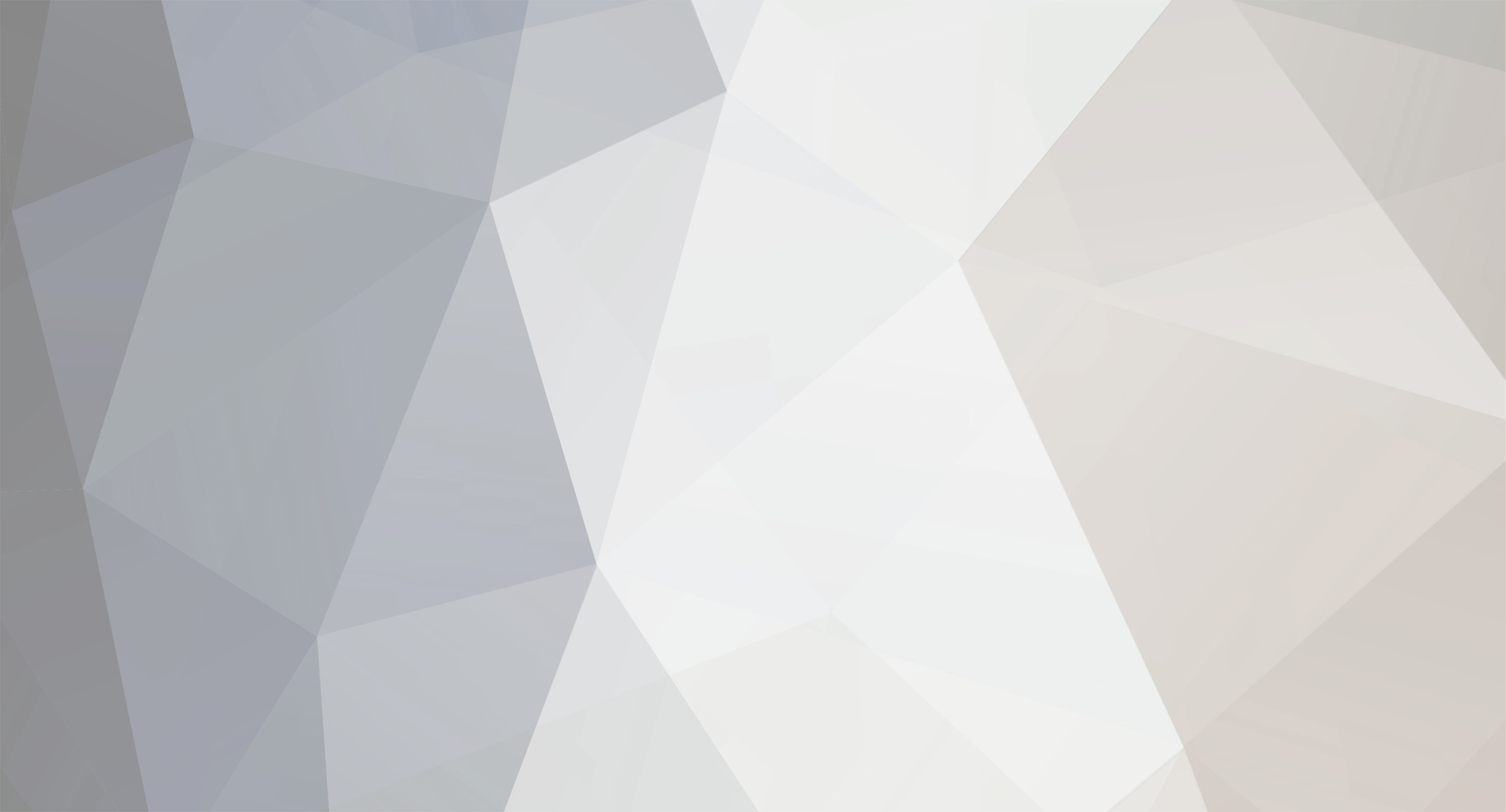
Art Anderson
Members-
Posts
5,052 -
Joined
-
Last visited
Content Type
Profiles
Forums
Events
Gallery
Everything posted by Art Anderson
-
A tip for all AMT Mopar builders
Art Anderson replied to oldscool's topic in Tips, Tricks, and Tutorials
Just be sure that it's the correct 2-spd BEEP BEEP horn though! -
I hope this helps in understanding at least one way to scratchbuild a leaf spring. The ideas and techniques I've shown here are not entirely my own--I watched Chris Etzel do leaf springs this way for his now legendary 1920's Indianapolis race cars. Just keep in mind the dimensions of the springs you want to model, and when doing a pair of leaf springs, be sure to make two of each leaf, so that you have identical springs from one side to the other of your model. If you can't find a common household bottle or other ready-made object having the curvature you need, you can always carve the shape from a piece of basswood, which is readily available at most large craft stores, such as Michael's or Hobby Lobby, even a lot of LHS's have the stuff as well. Just remember, it's a simple template you want, not high tech tooling. Also, since I made this tutorial in 2006, Tenax 7R has gone away, but there are very similar liquid cements out there, the best being either Ambroid, or if you have an industrial plastics supply house in your city, WeldOn #3 (which I highly recommend, as it comes in larger quantities at very inexpensive prices. Art
-
Completed! The springs are now completed. Eyes have been added to each end of the spring, and on one end, a "forged steel" shackle has been added as well. .020" holes were drilled into the spring eyes on the inner side of the springs, with .020" brass rod stock glued in place with CA glue, to act as locating pins for positive assembly to a chassis (in this case, a 1920 Oldsmobile 1-ton truck chassis.
-
Building the spring I start this process by giving each spring leaf a curve. This is done by drawing the leaf between my thumb and forefinger, against my fingernail to force a bit of pre-curvature into each leaf. This makes them lay down, one against the other, as they get stacked together, without seriously trying to "spring" apart. The leaves are laid, one at a time, first onto the main leaf which is taped at its ends to the template. Each successively shorter leaf is then laid on, with Tenax 7R liquid cement applied with a small brush, letting "capillary action" wick the cement into the space between the leaves. You don't want to have to press the leaves together, as that can squeeze melted plastic out from between the leaves, so check the curve of each leaf before applying it, making sure each one lays down cleanly. Here you can see the first spring completely assembled. Once dry, I will take it off the deodorant package, trim the ends of the main leaf to length, add the eylet to one end, a scratchbuilt shackle to the other end, and it will be all done! Time elapsed to make this spring? About 45 minutes!
-
Getting the curvature of the spring Leaf springs, by their very nature, are curved, when not mounted in a chassis, with the weight of the empty vehicle pressing them out to a lesser curve, but they are still curved. A template is needed here, to give a uniform curve to both leaf springs. Finding a template for making this curvature is pretty simple; common household bottles and packaging generally can give approximately the curve you need. In this case, an empty deodorant stick case works. Small liquor flasks also work, as do dishwashing detergent bottles, numerous glass bottles--in short, look around, keep your eyes open--as you just never know where you will find something that has the curve you want for parts like these!
-
Tapering the ends of the leaves Spring leaves are almost always tapered (as in this unit) or rounded in manufacturing, which aids them in sliding against each other, without binding, and reducing wear. I do this by stacking each pair of identical leaves together, and slicing off the corners of the ends. The trick here is to make them look as uniform as you can, again for a realistic look.
-
Here is a tutorial I created back in 2006 on how to make leaf springs. These were made for the rear springs of a still-unfinished 1920 Oldsmobile Truck, but the principal is the same, all leaf springs are made in essentially the same way: Part 1: Making spring leaves This is an easy step. Keep in mind that spring leaves are progressively shorter, from the main leaf to the final one. One thing to do, that makes the strip styrene into well-defined spring leaves, is to "chamfer" the edges of the styrene strip first. This can be done by adzing (scraping) the edges of the strip (all 4 of them) to round off them, so that when stacked in a spring, you can readily see each leaf. Real spring leaves are rounded slightly on their edges as well, so this is a "realism" step. For main leaves, I prefer .030" Evergreen styrene strip, however wide the leaf needs to be, for structural strength. I realize that .030", scaling out to 3/4 inch in scale, is too thick for exact scale fidelity, but sometimes, strength is the issue in scratchbuilding. All the other leaves are .020" thick. This spring will be one of two rear spring for a 1:25 scale 1922 Oldsmobile 1-ton truck, so an 8-leaf spring was decided upon. Notice that all 8 spring leaves were cut at the same time, to get two of each leaf exactly the same length.
-
Actually, GM sold the rights, designs and tooling for their motorhome to another company about 1981-82. The Hess training van would be cool to rework--had a couple, almost did just that, but knocking one apart given its assembly with liquid cements turned out to be almost insurmountable, so I sold both of mine on eBay about 7-8 yrs ago. RV's could be fun, but where to start? I for one keep hoping some mfr will come up with at least a slide-in, bunk over cab camper for a pickup. Art
-
Those who have known me for decades will remember my concentrating on Indy cars from the late 60's until 1984, building perhaps 200 or so models of cars that faced the green flag on race day. About 1975, I began digressing into antique and classic cars, when the thought occurred to me "what is missing from my dashboards?"/ The answer was easy, lenses covering the instruments! I thought about making my own hollow punches, to punch out clear plastic for instrument lenses, but two problems cropped up: First, every model would have meant machining punches to match the diameter of whatever instrument I needed a lens for (and not all of them were round!). Second, by the late 20's, instrument lenses were becoming "domed" in shape, no longer flat glass, I suspect due as much to designers wanting to minimize the reflection coming off flat glass, particularly in open-bodied cars, glare that made it pretty hard at times to really read speedometers etc (having had a few antique cars of the era, I can attest to that having been a problem. By the early '30's, DuPont's Plexiglas was everywhere, and notably in domed instrument lenses--so, how to do those? The solution was so easy, it escaped me for weeks--until I realized that a drop of clear epoxy would do that, with a bit of practice. Here is the latest result of domed instrument lenses--on the round dials on the Moebius Hudson dashboard: This was done with a generous dollop of DevCon 5-minute epoxy--practice over the years has taught me just how much (by fit and feel) to use to get the effect. A side benefit of this is that the epoxy lens actually makes the instrument decal "pop", it becomes slightly magnified, and the optics allow the dials to be seen at the oblique angle one views the dash when looking through the side windows as well. I am well aware that DevCon Epoxy, as with many, can yellow at least slightly over time, but with the black background of the decals, and the off-white used for detailing, I don't think that presents any problem. Time to make? Oh, only about 5 minutes start to application! (I didn't bother to make epoxy lenses on the radio dial nor the temperature/fuel gauge panel, as those had flat glass covers on them. Art
-
Well, you must remember, it was hard to get that thing "out of second gear!"
-
I would start with a spray black. Reason? Those older convertibles with black tops tended to keep that black color pretty much until the top rotted away--black dyes don't really fade that much, rather it's dirt and grime that makes it seem dark grey, but even at that, the grey isn't an even color at all. Start with pure black perhaps, add a light "wash" with thinned dark grey, and varigate it, because if you really look at the actual tops, they aren't a uniform weathered black, but lighter and darker from one area to another. Art
-
Modifying Resin Bodies
Art Anderson replied to Swifster's topic in Car Aftermarket / Resin / 3D Printed
Any polyurethane resin body can be modified in pretty much the same manner as you would with a styrene kit shell. The stuff razor saws easily, can be sliced and spliced to whatever it is you want to do with it. Of course, ordinary plastic cements don't work with urethane resin--epoxy or CA is what it takes. Art -
Don't get the AMT '61 Ford Galaxie
Art Anderson replied to '08SEAL's topic in General Automotive Talk (Trucks and Cars)
'08SEAL.... I'm gonna jump in here with my 2-cents worth: As others have already stated, in this day and age, with a set of forums as you participate in here, along with the numerous model car building related message boards elsewhere on the Web, there really is no excuse for not knowing what is in a particular model car kit, what's there, and perhaps for you, MORE importantly, what is NOT there in a particular kit. In short, it takes only a minimum effort to become an informed consumer. OK, 'nuff scolding. Let's take a look back to 1961-62, when AMT Styline kits were all over hobby shop shelves: Model car kits got their start in the early 1950's as sort of a way to build a scale model that could almost be a toy--the market for those early kits (even the more sophisticated customizing kits that came about starting in 1958) were aimed principally at KIDS, kids from about 8 or 9, until the age when they discovered girls and real cars, or about age15-16. Most kids who built models back in those days had no adults with any experience whatsover to guide them, so it was very much a self-taught hobby for them, sorta like learning to swim by being picked up, thrown into the deep end of the pool (either learn to swim, or drink the pool dry trying!. VERY few grownups build plastic model kits of any sort back then, and if they did, it much more likely they would build plastic models of sailing ships, or perhaps aircraft kits, such as those were at the time. Model car kits (indeed plastic model kits of all kinds, if sold in stores other than a hobby shop, were almost always found in the toy departments of "five and dime" stores, variety stores, drugstores and assorted other types of retail outlets. Well, "toy" implies kids, not adults as being the expected market for those early kits. This is almost completely the opposite of the market age for model car kits today. While certainly there are preteens and younger teenagers building model car kits today, they are vastly outnumbered by the adult modelers--most of whom are back doing (unless like me, they never quit building the stuff that lit their fires as kids decades ago), and adult modelers now being pretty much in the "driver's seat" are demanding far higher levels of detail than any kit designer of 40-50-60 years ago would ever have dreamed. Reissues of cars such as the Styline '61 Ford Galaxie HT (or for that matter, almost any model car kit originally developed prior to say, 1980, have at best limited appeal, as much due to subject matter as to their rather simple construction. Thus, if a company such as Round2, now owners of AMT model kit tooling, is going to put out a car kit from those dark ages, it will almost always be a reissue from tooling that exists--perhaps most of the subject matter produced in "Annual Series 3in1 kits" simply would not generate enough sales to warrant the considerable investment in all new, state-of-the-art tooling--so reissue it will be, or not at all. That is a plain, unvarnished and yet simple fact of life in the model car kit industry. As for what most consider to be "state of the art" in model car kits in this, now the second decade of the 21st Century--kits like those only evolved over time, in many cases the last 20 years or so. With very few exceptions, kits of 1950's though the 1970's era cars were done in the old, simple way until about 1980-81, when newer, younger product development people began replacing the original "old guard" types who'd been doing that work since the beginnings of the plastic model car kit industry. But more importantly, it is up to the consumer (you, me and the other guy too!) to educate ourselves as to what is to be found in any model car kit--and for my money, the members of this set of forums does that as well or better than those who frequent any other model car message board out there. Should you have a question such as "Is this a good kit?" or "Does that kit I see new on the shelf at my hobby shop have an opening hood and an engine" Asked in the New Kits topic area will surely get you the answers you ought to be seeking in a New York Minute (and I am not exaggerating here one bit! I've seen it many times, as have most of the rest of the members of MCM Forums. Even better, and quicker, is to use the search function on any message board setup out there, to find out if someone has already reviewed the kit, be it newly tooled, or a reissue from your grandfather's era. Long winded, I know, but that is how I call it, pretty much like I see it. Art -
Those are gas-powered "tether" race cars. That form of model car racing started just prior to WW-II, and picked up after the war. The early cars ran 2-cycle engines, using battery/coil ignition with miniature spark plugs (so-called ignition engines), in sizes from .19 cid up to .60 cid, fueled with gasoline mixed with castor oil. Where prewar cars tended to be mostly scratchbuilt from aluminum and steel, after the war, with scrap aluminum being extremely cheap, cast aluminum chassis, even complete bodies, began to turn up in hobby shops around the country. In the late 1940's, engine makes such as Thimble Drome, McCoy, K&B, Dooling came into production as well, along with cast aluminum rear axles with ring & pinion gears. A lot of gas tether racers learned to make their own car bodies to fit available kit belly pans by carving wooden bucks, then laying up Japanese tissue with ordinary model airplane glue (sorta like the "common man's" fiberglas!), finishing them with fuel proof model airplane dope. Tracks sprang up all over the country (here in Lafayette, the track surface in our city park survived well into the 1990's as the base for the merry-go-round), with a strong steel post in the center of a paved circular track. Those cars ran against the clock only, tethered to the center pylon, with classes based on engine size. The speeds attained could be pretty amazing--upwards of 100mph actual speed! Leroy Cox was the man behind Thimble-Drome, his engines were in the .15-.19 range, cast aluminum crankcase and cylinder barrel (later, in the early 1950's, Cox dropped those engines, and began producing the famous .049 Babe Bee, with an extruded aluminum, turret lathed crankcase, extruded cylinder again machined inside and out, with a reed valve for pumping fuel into the crankcase to be mixed with air and pushed into the cylinder by the downward stroke of the piston. About the same time, model airplane engines began converting to glow plug ignition, and the gas-oil mixture gave way to methanol/nitromethane/castor oil mix. Of the engine makes, Cox was the only one to live beyond the early 1970's, McCoy's disappearing in to the Testors fold about 1965 or so, Dooling fading away, and K&B being pretty much driven under by first Italian (Supertigre) and the various Japanese model engines. Of course, Cox kept up producing gas powered model cars for decades, both wheel and propellor driven--Testors bought up the Wen-Mac series of 1/2A (.049) engines and produced WenMac's cars until the early 1970's. These cars could be tethered, or run down a straight guideline, but the handwriting was on the wall by about 1970 or thereabouts, when radio-controlled gas powered race cars began showing up. Still, some neat cars though, and those old, now antique gas powered tether racers do bring some SERIOUS coin at shows, auctions etc today. Art
-
Source for scale cobblestone street?
Art Anderson replied to Harry P.'s topic in General Automotive Talk (Trucks and Cars)
Harry, There's new kid on the block in the realm of styrene sheets--JTT Architectural Model Parts--I have their brick street sheets (7.5" X 12"), pretty sure they have cobblestone as well. These sheets come 2 to the package, and in a WIDE variety of scales, up to at least 1/16 or so in some styles. I'd be willing to bet that at least one of the many hobby shops in your neck of Illinois carries JTT, if not, online. Art -
There is no reason why one can't use the stuff (lacquer) on styrene plastic model bodies--I and a number of others on these forums have been doing just that for years. In fact, MCW Automotive finishes has been packaging 1-oz bottles of pre-thinned acrylic lacquer for going on 25yrs, and a lot of modelers have achieved great results with the stuff as well. For best results, it does take a decent airbrush, and a good primer that will allow a bit of "frosting" of the plastic surface while not causing deep crazing, followed by the color coats. All that said, I wonder how cost-effective this Duplicolor paint line would be when considering a model car body though. It's shown as being packaged in 32-oz cans, and 32 fluid ounces is a QUART, and at that, it will need to be thinned in order to be airbrushed. Sounds like overkill to me. Art
-
Time was when aerosol cans used Freon (which is essentially non-flammable) as the propellant. However, with the removal of CFC's from just about everything, propane and butane have replaced Freon as the propellants of choice. Either of those gasses makes a rattle can of lacquer or enamel even more hazardous if exposed to high heat. I've been using spray cans of paint for better than 50 years, and NEVER once have I had a can leak, weep nor explode. It goes without saying that spray cans need to be kept in the coolest evironment available--but lacquers and petroleum-based enamels aren't particularly vulnerable to freezing, otherwise the stuff couldn't be delivered in unheated trucks from factory to warehouse to retail store in the dead of winter in most of the US, now could they? Even water-based enamels, such as Tamiya, MM Acryl and the like, while their labels may say prevent freezing, have to go through the same conditions in freight service--and I've never encountered any problem with those paints either, winter or summer. Just sayin' Art
-
Burger Chef Systems started in Indianapolis in the early 1960's, and spread rapidly across the eastern US, Rob. By 1970 they had more stores than did McDonald's. but lacked the corporate controls over their franchisees that McDonald's has always excercised (McD's owns every bit of real estate in the US where a McD is located, owns the building, the franchisee being the "owner-operator" of the business, paying rent on the property, plus a percentage of the gross of the restaurant. People may still remember Burger Chef birdhouses that were all over the place in the late 60's to early 70's--those were produced by the guy who owned the first LHS in Greater Lafayette at one time, he closed his store to concentrate on producing those birdhouse kits, which were wood, prepainted and silkscreened in BC colors and lettering. Toward the end, Hardee's took up most of the remaining BC stores, converted them to Hardee's, the rest simply faded away. Hmmm, makes me wish I could go out right now--get a Big Chef, fries and a chocolate shake! Mmmmmmm!!! Art
-
Ordinarily, you would be right about the body tooling, but not on the Manx: This kit body is molded in a simple 2-piece tool, as evidenced by it's being on a parts tree with two other pieces, none of them requiring slide cores. With virtually every full-bodied model car kit ever produced with a one-piece body shell (early Premier kits done in 1953-54 and Ideal Toy Company's 1955-issued screwdriver kits excepted), it takes 6 cores to mold the body shell: One to mold all the upper surfaces of the body shell, one for the right-hand side, one for the left-hand side, one for the front, one for the rear, and the last one being a "male" core which molds all the surfaces of the inside of the body shell. Of these, the front, rear and both side molds are "slide core" tools, so-called because in the process, these literally slide inward to mate up against the upper core, then the mold closes, bringing all 6 cores together tightly, at which point the molten styrene is injected under very high pressure. After the mold's water jacket is injected with cold water, which cools the tooling to the point that the molten styrene solidifies, the mold bases open apart, the four slide cores retract, and ejector pins push the body shell off the inner core mold. But, if you look at the Manx body in the kit, the only parting line there is around the "lip" of the body, which would have been a natural call, seeing as how the Meyers Manx fiberglass bodies were made--simply by laying up resin and chopped glass fiber into a one piece mold, in exactly the same manner as a fiberglass boat hull, or for that matter, any fiberglas bathtub. Actually a very simple process indeed! As for all parts being molded in the same tool base, yes, that is how AMT tooling was cut back in the day--those tool bases are huge, mininum of 2' X 4', and about 3' thick when both halves are mated together. The slide core cavity for the body was part of the very same mold in almost all model car kit tooling. This tool also included the cavity for the chrome parts tree, while clear parts (windshields etc) and clear red parts (taillights) were run on much smaller injection mold presses. Vinyl tires, of course, were run separately, in tool bases as large as I described for the kit itself, each tool having as many as 48 cavities all for the same tire. Hope this explains a bit! (drawn from numerous walks through the production area of AMT Corporation, on East Maple, in Troy MI, 1975-79) Art
-
Actually, the "Wiktop" architecture is that of a former fast-food hamburger chain which, at the time the Manx kit was first issued, was bigger than McDonald's--they being Burger Chef, based out of Indianapolis. Apparently AMT Corporation decided to not bother with licensing from Burger Chef Systems, which themselves went away by 1981. Art
-
'Open' ended question?
Art Anderson replied to ValvEasy's topic in Model Building Questions and Answers
Probably nobody on these boards has mastered the art/science/engineering of opening doors better than our own Bill Geary (Mr Obsessive). Basically if one remembers that door hinges are mounted to the lower A-post (or B-post in the case of the rear doors of a4dr), and to the framing of the door itself, rather than simply to the inside of of the bodywork skin itself and the insides of the door skins. That's how it's done in real life, of course. Now, this does take some work, given that our model kits almost never have the body pillars (posts) represented on the inside of the shell. Not since the days of straight upright body shells with relatively thin side panels and exposed hinges (think 'teens through the mid-1940's here) have car doors been purely "plug doors", but rather as bodywork got thicker, and designers wanted the hinges hidden from view more modern car doors appear to "turn in" to the body, at least at the front fender edges. Now, this isn't rocket science, but it sure does take some thought in order to make work, but modelers have conquered it over the years. Art -
Worlds Rarest Automobile
Art Anderson replied to dougp's topic in General Automotive Talk (Trucks and Cars)
I spotted that car at the Blackhawk Collection Collector Car Dealership at Blackhawk Center in Walnut Creek CA back in 1995 (hadda run to a store, replace my Canon EOS Rebel camera that I'd inadverdently left on an airliner when I deplaned at SFO on my way to NNL West that year!) to photograph it. Some of the story of this car: Yes, it was done by GM Styling Division in 1954, one of 3 built. This car was a "runner" from day one--meaning it was fully driveable. Sometime after the 1954 GM Motorama circuit, GM Vice President Harley Earl gave the car (by then in pieces) to Erett Lobban Cord (he of Auburn-Cord-Duesenberg fame from the late 20's though 1937) in recognition of E L Cord's cooperation in using the display hall in LA (which Cord owned at the time) for the GM Motorama displays in the early 1950's). The car as I saw and photographed it, was immaculately done, front to rear, side to side, top to bottom, and it is drop-dead gorgeous! At the Blackhawk (in the same upscale shopping center that featured the Behring Museum), the car was displayed in a showroom complete with a mirrored ceiling worthy of the finest "house of ill repute!), so the pics I got could include not only a full walkaround, but by aiming my camera at the ceiling, I was able to capture all the details of the interior!). I have the master that I started of that car for resin-casting, but due to my limited engineering capabiltities fof the time, it has yet to be finished, yet the unfinished masters still rest here in my apartment. One of these days! Art