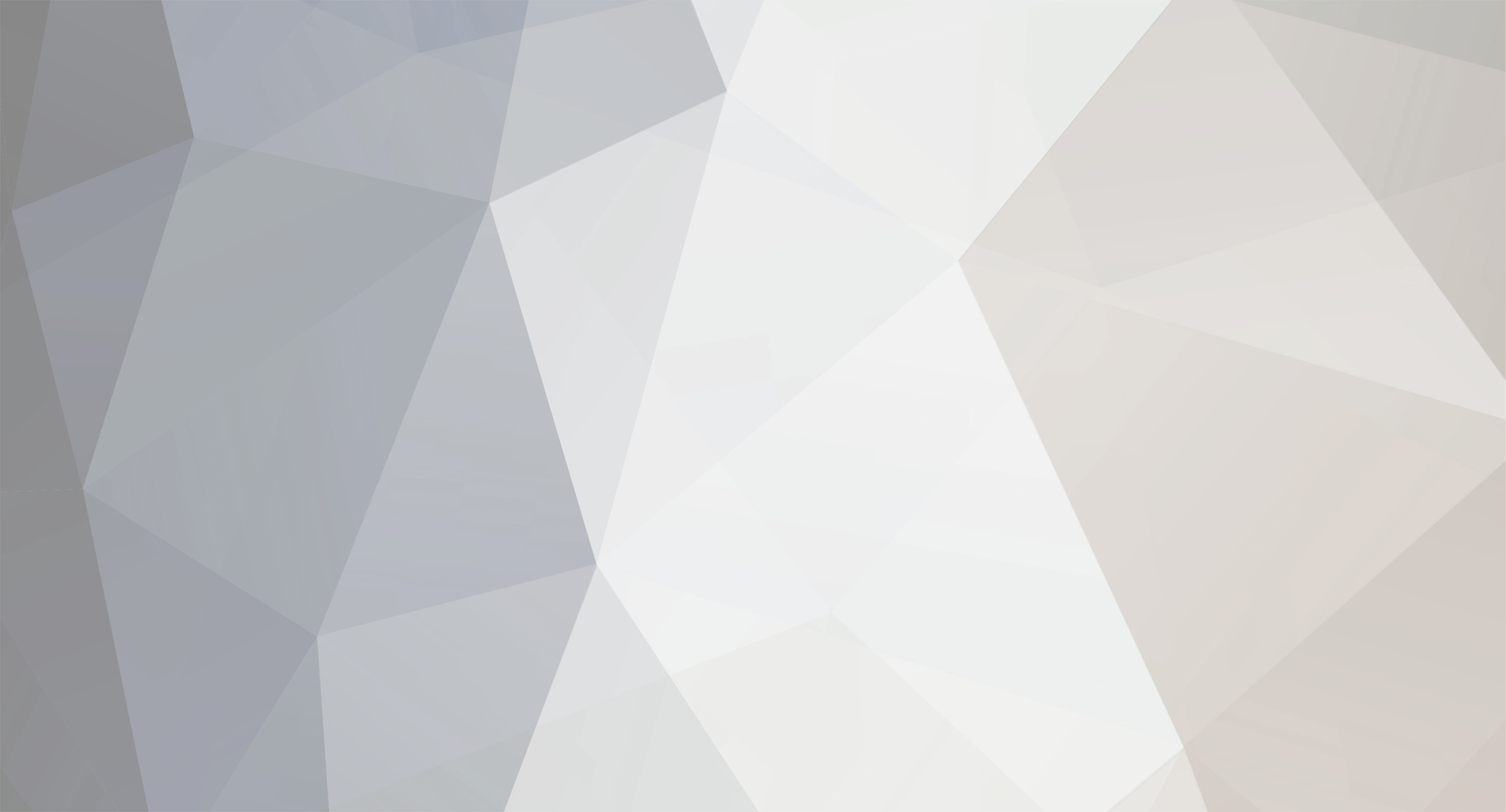
Art Anderson
Members-
Posts
5,052 -
Joined
-
Last visited
Content Type
Profiles
Forums
Events
Gallery
Everything posted by Art Anderson
-
I built up that Autocar dump truck for AMT's HIAA trade show when it was first released, fun build, but sales of the kit were in the tank, frankly! Art
-
Kookies Tee in a plastic kit ?
Art Anderson replied to Greg Myers's topic in General Automotive Talk (Trucks and Cars)
Also, if one looks closely at Kookie's T. the body is a cut-down T Touring, not a true roadster T-bucket. The body side forward of the rear door area clearly shows at the rear of the front seat. Art -
Chevrolet engine grey paint
Art Anderson replied to GeeBee's topic in Model Building Questions and Answers
Except that the gloss version of this color was what was specified--flat finishes and cleanliness on engines notorious for leaking oil wasn't at all recommended. Art -
Chevrolet engine grey paint
Art Anderson replied to GeeBee's topic in Model Building Questions and Answers
When I was researching the color of my 1941 Chevrolet pickup model (Revell kit), I discovered that the Gull Gray that was used on the crankcases of Pratt & Whitney and Wright radial engines purchased for US Navy use in WW-II, "Gloss Gull Gray" was adopted, using Chevrolet Engine Gray as their standard. Art -
AMT Ford Courier Pickup. Any good?
Art Anderson replied to pharoah's topic in Truck Kit News & Reviews
Actually. at least into the 90's, ALL Japanese pickups were shipped to the US sans the beds! That was due to a clause in the 1951 Peace Treaty between the US and Japan, wherein the Japanese agreed to never ship any military vehicles overseas--and that included pickup trucks. So, Toyota, Nissan, and Mitsubishi all contracted with US companies to build and install the beds of trucks that landed on the US Coast for distribution. Hence, there were no factory-fitted pickup boxes on any of those trucks (I owned three Toyota's in the 1980's-early 1990's). As for Subaru's, those were virtually unknown in most of the US east of California etc., until Subaru of America opened its massive plant here in Lafayette IN, to produce the then new Legacy and Outback back in the late 1990's. Art -
Who is this resin seller? Any info?
Art Anderson replied to Ace-Garageguy's topic in Car Aftermarket / Resin / 3D Printed
Mark, there is one small part in the pic of that Edsel wagon--a Federal Sirenlite! What the guy has replicated is the uber-rare '58 Edsel Ambulwagon, which was a factory-built ambulance version--those did have an upper tailgate section that differed from the Bermuda. Art -
And, it doesn't have the orginal "U-16 183cid Miller engine that powered the actual Blackhawk. The engine still exists, having wound up in the hands of Speedway carbuilder Alden Sampson, who installed in a newly-built 2-seat race car in the mid-1930's. That car still exists, restored, with the U-16 (which was made by joining two Miller 91.5 cid supercharged straight 8's in a "U-shaped" layout, each crankshaft geared to a center shaft--and reputedly was capable of some 550hp (phenomenal for any such engine in the 30's!). Art
-
How to Remove "Ghost Trim"
Art Anderson replied to diymirage's topic in Model Building Questions and Answers
I got my pint can of Weld-On #3 at our local plastics supply house, one pint can cost me all of about $6 or so, perhaps 5 yrs ago. I just use a "basting" squeeze bulb thingie, that is readily available in the kitchen utensils aisle of any "Big Box" store, even your favorite supermarket, to transfer that from the pint can to my glue bottle! Art -
I'm working up a set of final test shots for the '65 Flareside w/6cyl as we speak. My best guess is that this one should be available very early in '19.
-
Also, a search on YouTube! Art
-
Have you done a Google Image Search for pics of the real car? (of course, bear in mind, that race cars don't always keep the same colors on generally unseen portions as chassis all the way along the line).
-
Always will be that 2-pc body. Consider that kit reissues generally are in runs of perhaps 10,000 kits or so, the economics simply do not justify a retooling of a body shell. Art
-
Glue for Revells 2 piece tires?
Art Anderson replied to MPi-KM's topic in Model Building Questions and Answers
Those Revell (and other manufacturers) 2-pc tires were molded in polyethylene plastic, in the late 70's, when there was a massive "cancer scare" over polyvinyl chloride (PVC)--due to the outgassing that happened during it's being melted under heat for injection molding (I was the Personnel Manager at an Essex Group Wire Assembly Plant here in Lafayette IN, responsible for OSHA compliance back then--it was a HUGE issue for us as well, given that we were molding thousands of soft PVC plugs onto the ends of wires for producing the largest automotive wiring harnesses, for the massively large 70's Lincoln Continental MK-IV and MK-V, along with their companion Ford Thunderbirds. Fortunately, DuPont (and other companies) were able to come up with processes that greatly reduced that gas from being an issue, which also almost eliminated the often oily BLAH_BLAH_BLAH_BLAH that would leach out of such molded PVC items. The most visible benefit? It's been decades since we've had to put up with "tire burns" on the polystyrene plastic parts in our model kits, along with the same reaction to tires eating into the wheel rims of our builds! Art -
Best 60s Ford Mustang Kit?
Art Anderson replied to Harpo's topic in General Automotive Talk (Trucks and Cars)
Actually, that is the 1960's rendition of the 1963 Mustang II Concept Car from Ford that was designed, tooled and originally issued by Industro-Motive Corporation (IMC). It's a bit fiddly due to parts count, but does build up pretty darned well. Art -
Best 60s Ford Mustang Kit?
Art Anderson replied to Harpo's topic in General Automotive Talk (Trucks and Cars)
Except of course, that it has an opening hood, and an engine (albeit from typical 60's AMT 3in1 tradition), but the body along with the chrome and interior is actually very well scaled down. Art -
Yes, GAZ M1 it is. Back then, the Soviet Union's GAZ (Government-owned marque during the Stalin era) was in many ways, a sort-of copy of the '33-'34 Ford, which this one is. Art
-
The first pic is of a 1933 Ford Fordor Sedan (the slightly concave grille denotes it as a '33), but the second picture is NOT a Ford at all (note the independent front suspension, and the parallel leaf springs in the rear, neither of which any Ford had, until 1949, and Ford, while having "Artillery-style" spoked wheels 1936-39, their wheels were nothing at all like these. Art
-
Bonding Clear to Opaque Styrene
Art Anderson replied to Joe Handley's topic in Model Building Questions and Answers
Actually, I would not! CA glues are rather brittle once they harden, and with any torque (twisting even slightly) that glue joint can break. Since you are wanting to do these to replicate a solid-roof car model, I'd suggest a good liquid cement for styrene--Methyl Ethyl Ketone works the best, as once it's dry, that joint will be as close to as solid as the surrounding styrene. Alclad markets small bottles of MEK; Hobby Lobby (n their model kit & supply department) carries this, as do many hobby shops and mail-order houses that cater to plastic model builders. Art -
As for the resin, nothing beats Urethane resin--which is what most all professional aftermarket model car resin-casters use.
-
Professional resin-casters do use vacuum chambers, but only for "degassing" the Silicone RTV rubber after mixing in the catalyst (that rubber is almost like a moderately thick pancake batter in its liquid form. Air bubbles in the cured resin, if close enough to the surface of the master, can actually "bulge', as virtually all catalyzed RTV Rubber shrinks ever so slightly in volume, giving pressure to any airpocket or bubble (if close to the surface of the mold "cavity", even a small, trapped airbubble can actually force a "dent" into the surface of the casting. You may be confusing a vacuum chamber with a pressure chamber or pot though. Professional casters (and I was one for 12 years) use pressure chambers to hold two-part molds in, while the resin itself cures and hardens--that goes a long, LONG way toward eliminating tiny airbubbles against the surfaces of the mold cavity, which will appear as anything from almost miniscule "pin holes" to rather serious gaps. I used to use Campbell-Hausfeld pressure pots that were manufactured for propelling paint into spray guns, for the likes of painting houses and other buildings The ones I had were rated to 150psi, but I set the pressure regulator on my shop aircompressor tank at 75 psi, which left me a considerable "safe zone", and yet did the job of crushing small airbubbles into oblivion before the resin hardened. Art
-
Residue from decal solution-UPDATE
Art Anderson replied to shoopdog's topic in Model Building Questions and Answers
Gelatin is what, at least, was used as the adhesive for Decals--going all the way back to the invention the stuff over a century ago. And guess what? We are both right and both a bit incorrect! Animal hide glue (Gelatin) has been used, modern decal adhesive starts with a layer of glucose (sugar) to give the decal the ability to slide easily into place, with dextrose (corn sugar) on top of that, to increase the adhesion! https://en.wikipedia.org/wiki/Water_slide_decal Art -
Residue from decal solution-UPDATE
Art Anderson replied to shoopdog's topic in Model Building Questions and Answers
Just another thought here: Seeing the pics of your model, and such decals that were applied, those were going on over fairly smooth surfaces, with no "raised" details? If so, WHY even think of using anything as a decal setting solution? Beginning with the legendary Solvaset (which was first marketed in the middle-to-late 1950's) which gained popularity with model railroaders who were building, painting and decaling RR cars and such, with incredibly sharp raised and/or recessed details on them. Solvaset is little more than Isopropyl Alcohol, which will soften the lacquer-based decal film, and is intended to allow the decal to "snuggle down" over raised and/or recessed surface detailing, which the water used to dissolve the gelatin adhesive (yes, water-slide decal adhesive is nothing more sophisticated than unflavored gelatin, same stuff we get sweetened and flavored -- "There's always room for Jell-O"!!). While nearly 100% pure isopropyl alcohol will soften and strip most any hobby paint from a surface, lower concentrations tend not to do that. For example, rather than buying any of the pre-packaged decal setting solutions, I've used simply 70% rubbing alcohol since at least the late 1960's (even have used a Kleenex soaked in aftershave lotion in a pinch on occasion!). Unfortunately, a great many modelers use decal setting solutions of various brands on decals that are being applied to smooth surfaces having little if any raised or recessed detail, apparently in the mistaken belief that this will increase the adhesion of the decal, which it doesn't--that's the job of the gelatin adhesive. The problem lies not with any residue from the decal setting solution you used, but rather what the solution did to the "Pledge With Future Shine" you used as a clear coat--I'm a crew leader for a custodial crew where I work, and the floor strippers we use contain Isopropyl alcohol and believe me, that stuff will soften water-born acrylic floor polish in perhaps a minute or so off of Terrazzo, even off of vinyl floor tile. My advice: First, clear coat, if you prefer using whatever type/brand, should be the very last thing applied, AFTER decals are on, and the gelatin adhesive is dry (bear in mind, it has to evaporate from around the edges of the decal, as water vapor will not penetrate the decal itself in order to evaporate---let the project sit for at least a couple of days after the last decal is on, THEN clear coat over the entire surface. Art -
I'll do some checking with our show chairman and get back here, as it if Okey will be at our Lafayette Miniature Car Club contest this coming Saturday (August 18) Art