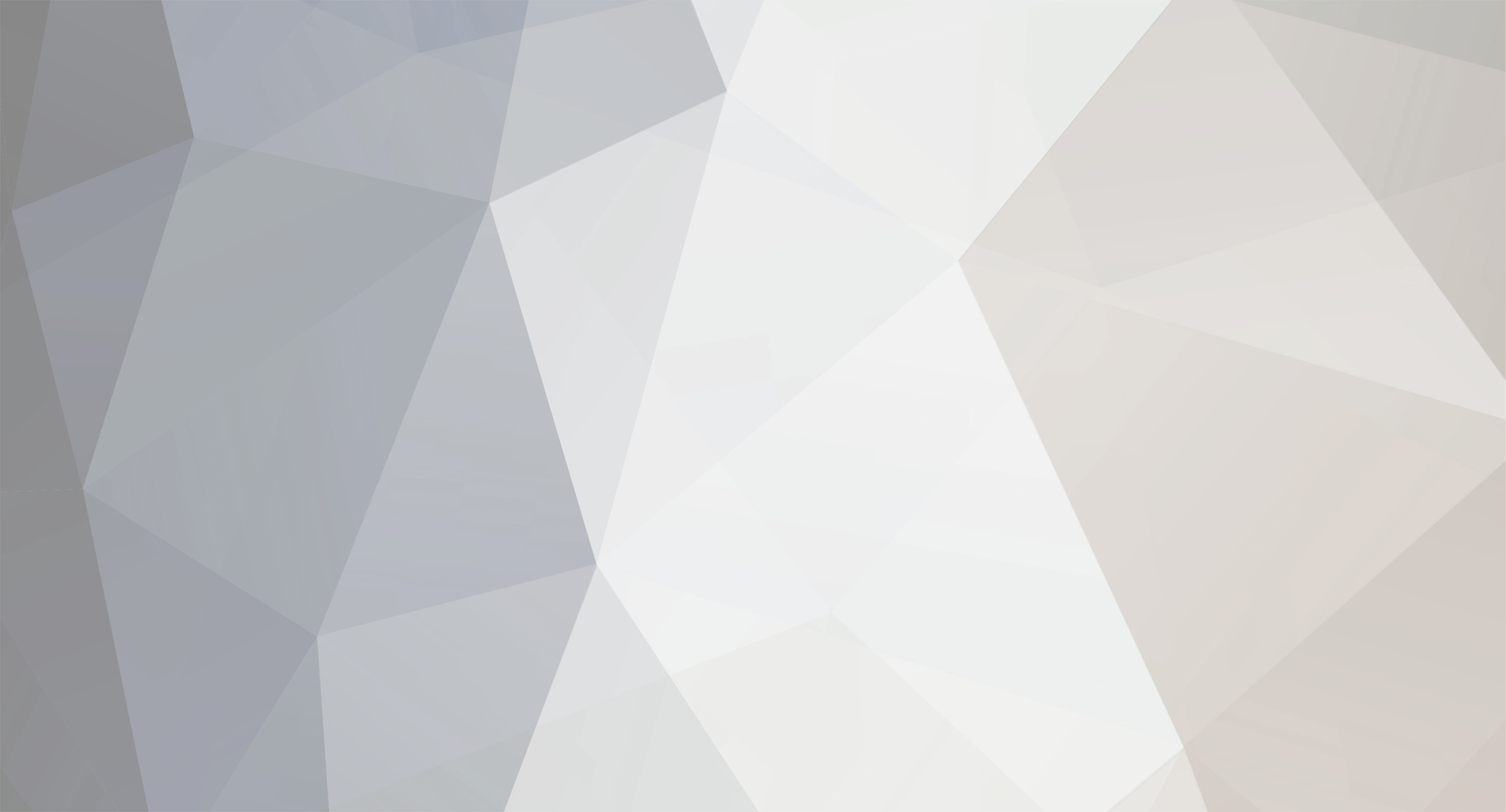
Art Anderson
Members-
Posts
5,052 -
Joined
-
Last visited
Content Type
Profiles
Forums
Events
Gallery
Everything posted by Art Anderson
-
Plastic vs. diecast
Art Anderson replied to oldcarfan's topic in General Automotive Talk (Trucks and Cars)
Henry, I don't think I forgot Europe at all here. I am very aware of many of the offerings in diecast model cars in, and from Europe and the UK (for years I collected Matchbox, Corgi, Dinky, Solido and Rio miniatures. I carried some of the first Bburago 1/18 scale diecast models in my hobby shop back in the 1980's. However, the plastic scale model hobby, building from kits, pretty much began here in the United States starting about 1951, and of course that's tended to be oriented toward model kits of American cars, with a few European and British cars done in model kits by US companies over the decades. I've also seen, and built at least a few of the kits of European cars produced by such as Airfix, Heller, Italeri, Revell of Germany--even have a couple of kits here made in the former Soviet Union. The original question at the start of this thread asked a much simpler question, which I at least attempted to answer, based on my experiences, where I've been in this hobby (and parts of the industry as well) over the past now 61 years. Art Anderson -
Plastic vs. diecast
Art Anderson replied to oldcarfan's topic in General Automotive Talk (Trucks and Cars)
With only a couple of notable exceptions (Revell being one) pretty much where diecast models/collectible toys and plastic model kits are concerned, seldom ever have these two genre's ever been joined under the same company roof. They are, still, very different companies that do one or the other, and very different markets. Sure, there are modelers who "cross over" and buy at least a few diecasts, and vice-versa there are diecast collectors who from time to time will build a model car. As for development costs, unless one is looking at a seriously high-end diecast (those that retail above $100), yes pretty much, the development costs are considerably less for a diecast model car in 1/25-1/24, than for the same subject in 1/25 scale plastic. For example, a model company might well invest well over $150,000 in a new model car kit tool, where that Plymouth pickup you mention (based on my experience several years ago developing diecast cars) might represent a total of less than $30,000 to bring into production. As a result, for much of the past 20 years or so, there have been a lot more different car and truck subjects done in diecast than were model kits created in the same time frame. I would also submit that model car kits appeal to an audience, while certainly larger than most of us might think, are a much narrower market than the market for diecasts, as those can appeal to a much wider age range, and tend to give that "instant gratification" of being able to hold the finished item in your hand as soon as you can get it out of the package. Additionally, diecasts can be played with at least to some degree (the more expensive, more highly detailed, and those having lots of opening or movable parts tend to be considerably more delicate--more susceptible to wear and breakage), and do attract those who want the model without "the hassle" of having to build it (even though we here probably prefer the building experience!). From the retail perspective, a diecast can create more sales dollars into the cash register in a shorter period of time, and doesn't have, from the merchant's viewpoint, the aggravation of having to stock paint, glue, or any tools; not to mention a lot less "returns" do to at-least-alleged missing parts. While this probably doesn't bother your LHS, it's pretty certain to me that the management of the mass retail 'big box" stores see that. It's just that there are a lot of reasons, not any one in particular as why there seems to be more emphasis on one medium over the other. As for the companies who make either diecast or plastic model kits--there really isn't much crossover there, even though Revell's done their share of diecast model cars over the years, and Round2, because of the owner's own business model, produces both lines of model vehicles, albeit mostly limited numbers of reissued older product. However, for whatever it's worth in this discussion--the market for diecast model cars, in pretty much every scale, is a great deal smaller than it was 15 years ago--many of the companies producing diecasts back in 1998 have disappeared completely, and those that are still in that business have shrunk considerably over the last 10-12 years. On the other hand, the market for plastic model car kits is in pretty good shape, and surprisingly (I think, and happily so) stable. Art -
Skyline BMF question
Art Anderson replied to lordairgtar's topic in Model Building Questions and Answers
If the plastic surface is "squeaky clean", I see no reason why BMF shouldn't stick to it as well as it does on a painted surface. Art -
68-69 AMC engines were painted a very bright, sparkly turquoise metallic. Art
-
Dan, there are multiple version parts in the tooling--but I doubt you will see more than one version per kit release. However, it does make sense to work up a project like this one several potential variants of the vehicle "waiting in the wings". Other model companies have tooled up parts for more than one variation of whatever their "first release" was going to be--and over time they've gone forward with more versions (Revell's excellent '32 Ford street rod series comes to mind here). And, if one thinks about it, that's how AMT started out with the Trophy Series--one '32 Ford Roadster eventually became a coupe, a phaeton and a Tudor sedan--their '40 Ford coupe became a Tudor Sedan and a sedan delivery--and so on. Art
-
I just learned, this afternoon, that I can expect the first round test shots of this anticipated series of kits by Saturday! Whoo-hoo, I can hardly wait (I'll forgo my diuretics for that long--don't want to pee my pants prematurely!) Long bed, short stepside box, 2WD,. 4WD, small and large V8, and the I-block six--can't wait! These will be first round test shots--so evaluation is required--gotta help make these as excellent kits as you all expect them to be from Moebius Models! Art
-
History of AMT & MPC's Action Line Pickup Kits
Art Anderson replied to Fabrux's topic in Truck Kit News & Reviews
This diecast had to be done from newly-cut tooling, simply because while injection-molding is injection-molding, the difference in materials used for the injection molding process are completely different--each has its advantages, and its limitations. The biggest, and most important difference will be the inside surfaces of the body shell: Where styrene plastic can flex a bit to allow demolding of a body shell having some "undercuts" inside, particularly on the inside surface of the body sides--which cuts down some on the amount of plastic being used, which means the cooled body shell has to flex outward a bit to come away from the inner core mold--Zamak (the metal used virtually universally for diecasts) does not give any tolerance for such--therefore, the inner core mold for a one piece body shell mold must have straight sides with a few degrees of "draft angle" to allow the solidified metal body shell to come away from the inner core mold freely--with no chance of any flexing outward of the body sides themselves. In addition, raised details on the exterior of a diecast body almost always will be thicker/heavier than those on a plastic counterpart; and the door & other recessed panel lines perhaps twice as wide and that much deeper. In the case of recessed panel lines, those require raised "ridges" in the tooling. While molten styrene plastic doesn't readily harm such tiny, thin-section "ridges", with the much higher heat used in Zamak diecasting (heated to very dull red heat), over time that heat from the molten metal will destroy the hardness of those little ridges, causing them to begin breaking off, resulting in noticeable imperfections in door and panel lines. For this reason, diecast tooling doesn't last nearly as long as that used for injection molding styrene plastic. Art -
I first saw that hand drill from Xacto at Christmas 1963, when at home on Christmas break from college, I worked at our local hobby shop (where I went to work full-time in June 1964). The gears were diecast Zamak, just as the one pictured. Sometime in the late 60's, Xacto changed the gears to molded plastic--which they remain. Art
-
That dates from the 1960's. Art
-
1/25 Revell '70 Plymouth HEMI 'Cuda 2'n1
Art Anderson replied to MachinistMark's topic in Car Kit News & Reviews
Craig, If done well, this type of parts breakdown makes a body shell easier to line up and mount onto the chassis or platform. Also, if there are recessed areas in something such as the inner fender panels that would result in an unworkable "undercut" were these panels molded as part of the body, they can be accomplished in a part separate from the body shell itself. Just a couple of pennies worth here. Art -
Station wagons started out as horse-drawn "depot hacks", used by resorts and hotels to pick up guests at railroad stations (the forerunner of today's hotel and resort shuttles going to and from airports). As automobiles replaced horses, this body style continued, the paneled wood construction being very much the technology available in the years prior to WW-1 and beyond, just as were so-called steel auto bodies which were mostly wood construction, albeit overlaid with sheet steel panels. Wooden station wagon bodies continued through the 1940's more out of tradition than anything else. Chevrolet is generally credited with producing the first steel bodied station wagon in 1935--the first Chevrolet Suburban, but even that body has a fair amount of structural wood in it although it had no exposed wooden surfaces. Willys-Overland actually produced the first truly all steel station wagon by the simple expedient of putting rear quarter windows and a back seat (with their "Station Sedan" version having a single-person "third seat" set sideways behind the full rear bench seat. Of the Big Three, Plymouth introduced their first steel station wagon for 1949, as a mid-year release, having started that first postwar model year with a couple hundred wooden bodied station wagons (the wooden bodies were produced by US Body & Forge of Frankfort, IN--just 20 miles SE of me). For 1949, Ford introduced their last "woodies", with a body shell shared by both Ford and Mercury (only the doors differed, due to the lower front fender line on Mercury's. This body is structurally all steel, the wooden panels being molded plywood with an outer layer of mahogany veneer. The blond wood framing was also molded, as opposed to being cut, milled to shape with "dovetail" joints as was done on all previous Ford station wagons going back to 1929. The hard maple was cut into thin strips, which were then "stacked", with glue in between the layers and then pressed to shape under steam heat. The resulting molded wood parts were then milled to their softer rounded contours. The "framing" was bolted to the molded plywood panels and those assemblies bolted into the steel body framework. For 1951 Ford had planned to replace the molded plywood panel inserts with sheet steel, but steel shortages due to the Korean Conflict along with a massive military buildup at the outset of the "Cold War", the molded plywood panels were continued, although late in the 1950 model year steel tailgates replaced the wooden version used up to that time. For more about woodies in general and Ford woodie station wagons in particular, the Lorin Sorenson book "The Fabulous Ford Woody" is fascinating--loaded with stories about how those wagons came to be, how they evolved; with lots of photographs of woodie station wagon design, engineering and production. Art
-
Tamiya....lets get it right.
Art Anderson replied to roadhawg's topic in General Automotive Talk (Trucks and Cars)
And here, all my life long, I was sure it was pronounced "Porch-A" Art -
The rarest AMT truck model?
Art Anderson replied to Mr mopar's topic in General Automotive Talk (Trucks and Cars)
As far as original-issue AMT truck kits go, the rarest of the breed probably was the Richard Petty Ford LN-series "wedge race car hauler'/Dodge "kit car" modified stocker in Petty #43 trim. Apparently, AMT tried to slip this one in under Petty Enterprises licensing they had back in the 70's, only to get shut down on it very quickly when Petty Enterprises found out. Only a few thousand kits ever made it into customer hands as AMT Corporation had to do a recall on the kits (Petty was running Olds Cutlass HT's at the time). I have three of the kits, still sealed, as received back in 1977 or 1978 as complimentary kits, for being part of AMT's group of box art model builders. Art -
Wheelstanders , who was first ?
Art Anderson replied to Greg Myers's topic in General Automotive Talk (Trucks and Cars)
Of course, organizations such as the American Legion, Veterans of Foreign Wars, The 40&8 people, and of course, the Shriners, all these organizaitions have had chapters who were altering the wheelbase of Model T Fords as far back as the late 1920's, to perform wheelstands (often extended for several city blocks) in parades and at other public functions. Does that count? Art -
Hobby Shops... Are They Viable Today?
Art Anderson replied to Tom Geiger's topic in General Automotive Talk (Trucks and Cars)
Brick and Mortar hobby shops will continue to survive as well as thrive as long as they are well-capitalized (meaning they are able to have and maintain a well-stocked, comprehensive inventory), understand, live and breath merchandising, and pay attention to their bottom line. It's pretty much always been thus. Art -
For what it is worth: Ford's Iron Mountain wood-product factory used two types of wood on 49-51 Ford and Mercury woodie station wagon body panels: Hard maple for the framing, and Honduran Mahogany for the molded plywood "panels". The Mahogany has a fairly straight grain, typical of most tropical hardwoods, that is fairly visible even in 1/25 scale. The maple used for the framing, on the other hand, is a very close-grained wood, meaning that the grain isn't all that visible even in 1:1 scale, due also to its being a very "blond" wood, without much color to it. While maple grain can be made to show by staining it, when finished blond with a clear varnish (which is what Ford used throughout the years of their woody station wagon production (1929-51), they did not stain it. Over the years, many restorers and street rodders have built reproduction woodie body shells, and intent on "effect", they've stained the wood; some have used curly grained maple (which Ford did not use) while others built their replacement framing from oak, which was almost never used in wooden station wagon construction, maple being by far and away the industry standard back in the day. While Ford woodies, from their introduction in 1929 through the 1948 model run, were built using cabinet-making construction and techniques, the '49-'51 station wagon bodies, due to their now rounded, curved body panels, were made by laminating thin strips of maple in molding presses to give them the required curvatures to match the shapes of the molded plywood (birch with a mahogany veneer on the outer surface) panels. This meant that there was virtually no milling done, except at the ends of some framing sections that would have exposed the end of the grain. Thus the grain of the maple, on a new '49-'51 Mercury or Ford station wagon was not readily visible, and in 1/25 scale would be nigh to invisible. The Mahogany grain would have been seen though, but it would be fairly straight, with virtually no knots or burling present. The pic that Casey Littman put up is actually quite accurate: You can see the subtle mahogany grain, but barely a hint of the grain in the maple framing. Art
-
Question for the Ferrari aficiondos
Art Anderson replied to DrKerry's topic in Model Building Questions and Answers
In years past, when the FIA assigned national colors, apparently no regulations or consideration of shade of color was specified. French racing blue was blue--anywhere from a light powder blue to fairly dark. British racing green ranged from almost grass green to very dark "green black" to the transparent "candy" green used by BRM OVER sanded aluminum bodywork. In short, it was the color, not the shade of that color, that denoted the nationality of the particular race car. Art -
Question for the Ferrari aficiondos
Art Anderson replied to DrKerry's topic in Model Building Questions and Answers
Years ago, I had a conversation with Dave Dodge of Model Car World (MCW Automotive Finishes), when he was just first starting. Dave told me he'd researched Ferrari's red colors (this was about 1990, when he was leaving his job at a local NAPA outlet in Northern Indiana to start MCW), and discovered that there were a couple of dozen shades of red that Ferrari used up to that time. Apparently, a few more have been added since then? Art -
53 Chevy Bel Air paint question
Art Anderson replied to o-man's topic in Model Building Questions and Answers
Interesting, given that I've never had a primer "leach" its color into the finish (and I've been painting model cars for at least 54 years now. Part of the problem with color coats can be that they are mixed from a combination of pigments and "toners", the latter of which are transparent, very much like dyes, and can bleed at times into color coats (reds are, in my experience the worst offenders at this). True primers, on the other hand, generally don't have toners in them, the most common, red oxide, white, gray and black, are, I believe, all pigment, with no toners or dyes in them. Of course, whenever I use anything as a primer, it is that, just that: primer, made and packaged as such. Now, with colored plastic, red being the prime offender, often times styrene gets "colored" with dyes, particularly reds and yellows, and those will bleed through most paints at times, although I have never had that experience (I dunno why--either I've been lucky, or the red plastic demons are scared of my disposition?) This situation does require a sealer of some sort or another, in order to prevent bleed-through. Art