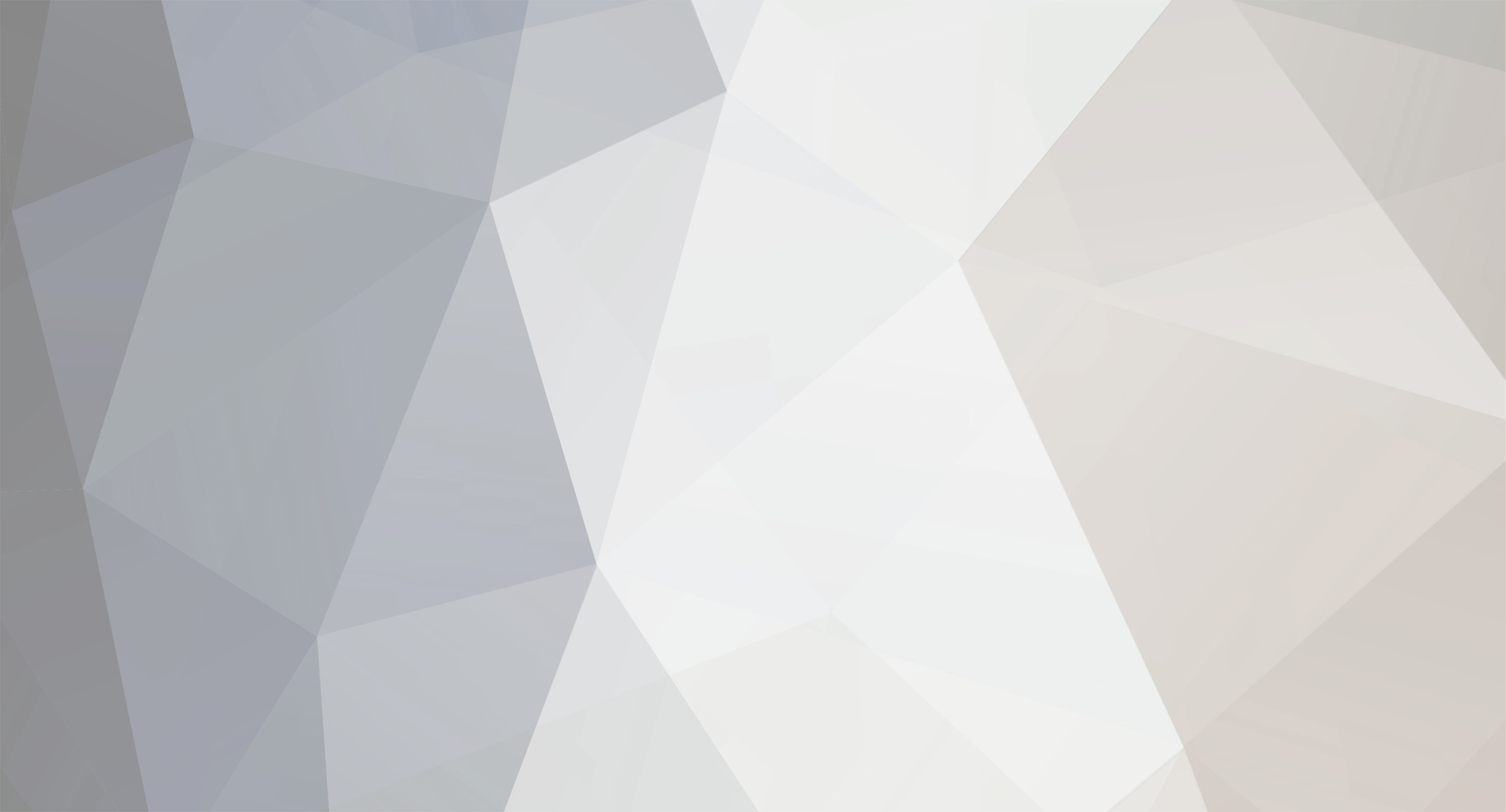
Art Anderson
Members-
Posts
5,052 -
Joined
-
Last visited
Content Type
Profiles
Forums
Events
Gallery
Everything posted by Art Anderson
-
cutting and splicing roofs/panels help needed
Art Anderson replied to fun9c1's topic in Model Building Questions and Answers
I absolutely use some filler or another--however, I came up with the systems I use (and described) due to the fact that putties and even CA (Cyanoacryliate glues--chemical name for the various brands and formulae "Super/Crazy Glues) don't have the strength and resilience of a much more solid material such as styrene plastic. Art -
Custom hood issue - Final solution
Art Anderson replied to Jantrix's topic in Model Building Questions and Answers
Styling-wise, a hood "bulge" (the late Harley Earl, VP of Styling at GM for about 30 years called that concept the "Power Dome" look), which if done to fit in with the lines of that hood would be very impressive. Those Unibody Lincoln Continentals were HEAVY cars, certainly for their size--the convertibles tipping the scales at over 5000lbs, so performance cars they weren't, but certainly very good-looking luxury cars--so I'd stay with the rather squarish lines of the car for that hood bulge. Should be easy to do with some Evergreen sheet and strip styrene and a bit of putty and sanding. Art -
cutting and splicing roofs/panels help needed
Art Anderson replied to fun9c1's topic in Model Building Questions and Answers
If I might suggest something here: I've cut and stretched any number of model car bodies over the years, but have never used any sort of putty, CA or other fillers to fill in the resulting gaps, as all fillers, including CA can, and often will shrink or crack over time. What I do use is either sections from a second body shell, or if the resulting gap isn't too wide, is to use Evergreen strip styrene to fill the gap. Evergreen styrene strips come in a wide variety of widths from .005" (generally too thin, to narrow, to be of much use in this, out to .250" wide (1/4 inch). The thinner strips are very flexible, and can be bent or curled to mate up to say, the shape of the roof of most any model to the point that CA glue (and in some cases, a good, pure solvent liquid plastic cement will hold them very well (Ambroid Pro-Weld, Tenax 7R, or Weld-On #3--which in my experience nearly every industrial plastics dealer stocks, especially if they stock plexiglas or do plexiglas fabrication work!) I've found that most modern-made plastic model car kit bodies tend to have a minimum plastic thickness of about .040", perhaps as thick as .050" in many areas of the body shell, particularly in the roof and in the body sides out to perhaps 1/4" in from either front or rear ends. I make any cuts in a body shell with a razor saw, trying to be as straight and true with cuts as possible, and try to calculate the amount of "stretch" so I can match up an available width of .040" styrene strip to create the stretch needed. Sometimes, it takes a bit of "eyeball" engineering to trim down an added strip or panel if I can't come up with the exact width of the filler strip or panel in a ready-made strip of Evergreen. Sometimes, particularly with any model car body shell coming from tooling originally cut, say, back in the 1960's when model companies made body shells a lot thicker (for reasons best explained some other time), thin --say .040" thick Evergreen strips-- won't work very well) I've resorted to using thicker pieces of Evergreen strip styrene, to get the width of the stretching pieces I need, which almost always results in the Evergreen strips protruding out beyond the exterior surface of the body shell--but that's generally pretty easy to dress down with needle files and sandpaper to match the exterior body surface of the model I've stretched. If the body panels being stretched go beyond the range of Evergreen, or if the model being worked on is a conversion of say, a hardtop into a stretched limousine (extreme example here) then I've found it's a lot easier to use a second body shell to achieve that stretch. In doing this, as with the other types of stretches, often it's a wise thing to "reinforce" those splices, preferably from the inside, or if that is not an option, using a "tab and slot" arrangement: Cut one of the body panels and create a "slot" in the cut, perhaps 1/8" deeper into the panel or panels, then when cutting the second body shell or panel to mate up to that, allow extra material in the area where the "slot" is on the first body, and trim out a "tab" that at least closely matches the "slot" on the first shell. Care of course is key here, so that the two panels will line up straight and true--and then this is where gap-filling CA works very well--done carefully, this results in a stretched body or panel that is very nearly as strong as the original body shell was to start with. This I've used in making resin-casting masters of subjects such as a stretched limousine, where the master had to withstand the stresses and rigors of making the RTV rubber molds without just simply disintegrating. I hope this helps a bit. Art -
This helps me figure out what "gauge" copper wire to use (I prefer using bare copper wire, as I can get it far closer to scale thickness/diameter than with most of the coated/insulated wire often used. It's called "American Wire Gauge" or AWG, which are the standard sizes for nonferrous wire in the US; http://en.wikipedia.org/wiki/American_wire_gauge#Tables_of_AWG_wire_sizes Michael's and Hobby Lobby both carry a fairly wide range of uncoated soft copper wire in spools which are actually pretty inexpensive--and the spools are marked as to their AWG size. Art
-
I'll second that opinion! I've used masking tape a number of times to replicate vinyl tops, and once built and painted, it looks remarkably like the real thing, AND it can be overlapped where you see the two seams in the roof on that Riv very realistically. However, in studying several pics of actual '69 Rivs, the vinyl top material used seems to not have much of a texture to it--several cars I looked at with Google Chrome Image Search show vinyl tops that appear merely a semi-gloss, but smooth finish. If that is the case, then simply paint, followed by a semi-gloss clear should do the job, and that shouldn't obsure those little vents. Art
-
Hobby Shops... Are They Viable Today?
Art Anderson replied to Tom Geiger's topic in General Automotive Talk (Trucks and Cars)
Back in the 60's and early 70's, I worked at a very large, well-stocked hobby shop here. The owner did not deal at all in "used" or "pre-owned" model kits, simply because there was, back then, no market for any such model kits. We did, however, deal in used trains, primarily Lionel Standard Gauge trains from the 20's and 30's, and the owner built an extensive collection of pristine examples. In addition, on buying trips to one of our wholesale sources in Chicago, we did bring back a number of then-collectible gas powered cars which of course, were all in mint condition-brand new if you will. Fast forward to my own store, the Modelmaker: The 1980's and early 1990's saw the last big go-around of retirement of the parents of the Baby Boom generation here, and Modelmaker was located in a shopping center directly across the street from several large subdivisions populated by the WW-II generation, who were retiring, moving to the Sun Belt--that sort of thing. There were any number of those couples whose sons had bought, built and even collected the great model car kits of the 1960's, but had left those unbuilt kits behind as they went off to college, got married, moved away, leaving Mom and Dad stuck with, in a lot of cases, literally dozens of those old kits (some of which I'd put pricetags on, and sold back in the 60's while working at Weber's!). I started checking the garage sales in those neighborhoods on Friday mornings on my way into my store to open up for the day--bought a lot of those old kits that way. On more than one occasion, someone would stop by my store, ask me if I was interested in buying old kits. Many of those sellers (not all of them elderly parents BTW, several were former teenagers who'd hung onto unbuilt model kits they'd had since they discovered real cars and girls, and never went back to building models again). My pattern was simple: I let the seller tell me what they wanted for those stashes of old model car kits--sometimes having to suggest that they were worth more than the original $1.50-$2.00 pricetags--much like the people on Pawn Stars today. Whenever we'd come to an agreement, payment made, the model kits were mine, in inventory at Modelmaker. I will admit to latching onto a fair number of those kits, some of which I still have, but sold the rest in the store, at collectible prices but not necessarily at the highest value I might have seen at any of the numerous model car shows and swap meets back then. I did, however, check over each kit closely, to make sure that all parts were there, that there was no warpage, and that the chrome sprues were still good, bright and shiny. But, they were always sold "as is", and with no returns accepted on them. In addition, I did sell, both directly purchased by the store, and on consignment, a number of those handmade brass railroad locomotive models such as were produced in Japan and Korea during the late 1950's into the middle 1970's, but that again, like collectible model car kits, wasn't a serious focus. That was never a big part of my retail store though--just a small sideline, and I never bothered with any model kits that were even close to current product, and never bothered to give a second look to ordinary kits from say, the 1970's with badly shopworn boxes either. Would I do the same today, were I still in the retail business? I don't know, frankly. There is, I believe, a pretty fine gray line between being a true, fully functioning and professional hobby shop and some sort of low-end antiques & collectibles store specializing in old, but not necessarily "ancient" items. Art -
please tell me i didnt ruin this permanently.
Art Anderson replied to allecb's topic in Model Building Questions and Answers
So, strip the thing, start all over? Art Anderson -
Hobby Shops... Are They Viable Today?
Art Anderson replied to Tom Geiger's topic in General Automotive Talk (Trucks and Cars)
Not Tom Geiger (whom I know face-to-face) but I will drop an answer here: Well, for the first objection--a bit of philosophy I learned from the owner of the hobby shop where I worked my first full-time job 50 years ago. It was a small sign, clearly visible IF you managed to spot it: "I'm not upset at those who sell for less--they know what their merchandise is worth". Basically, we weren't to argue about price, but concentrate on service with the sale. In the end, the simple understanding that "If your outgo exceeds your income, your upkeep is your downfall". Hobby Lobby's 40% off coupon? Pfft! While that's neat if you have a Hobby Lobby close by, AND they have what you want to buy--HOWEVER, while I stop in HL pretty regularly, there is NO WAY they would ever have bothered me back in my days as a hobby shop owner--I had their model kit/tools/supplies inventory smothered (in 1200 sq. ft. of selling space, I carried over $65,000 in inventory, where today's HL MIGHT have perhaps $7,500. While Hobby Lobby is a formidable force in the area of crafts for women, they really are no serious competitor for any truly well-stocked hobby shop--and a knowledgeable staff? Fuggedaboudat! Art -
Hobby Shops... Are They Viable Today?
Art Anderson replied to Tom Geiger's topic in General Automotive Talk (Trucks and Cars)
My thoughts on starting a hobby shop (been there, done that, got the T-shirt): In all but the very largest of markets, no hobby shop is likely to succeed without being what we used to call "full function", that is, catering to the wide variety of hobbies that are out there. Going in, no hobby shop owner should expect to be an all-encompassing "expert" on every area of hobby merchandise, but needs to be willing to work hard to at least understand each and every department (category of merchandise). While the owner of a hobby shop should have knowledge in one or more hobby categories, he or she simply needs to be at least basically conversant with all of them: Things such as plastic models, trains, RC planes & helicopters (boats if the trading area market has sufficient bodies of water adequate for model boats). Supplies, such as paint, glues, building materials (balsa, hardwoods, plywoods, styrene, K&S brass--all the way down to nuts & bolts, the bits of hardware necessary for completing model railroads and such RC categories as the shop might carry, and it goes without saying, repair/service parts and add-on accessories for every category of models. Also, tools should be a significant category, for the reason I mention next! I was able to predict, within just a few months of being open, that having all these things meant that any plastic model kit I sold tended to generate its own retail value in things such as glue, paint, tools (anything from Xacto knives and blades, to airbrushes (funny, when I was doing my opening buys, several wholesalers questioned my insistence on stocking at least two different levels of airbrushes and compressors--I won that one, as I averaged perhaps 20 complete airbrush outfits yearly--where they insisted I might sell MAYBE one outfit a year, perhaps 2-3 airbrushes!). The same was true with parts for RC cars, planes and boats--if a customer comes back with an RC car busted in a crash,for example, only to hear that "I'll have to order that part for you"--well he can just as easily go online, order the part(s) even if he has to wait several days for it to arrive--why do that to him, when you could just as easily have set him up with the repair parts right then and he's back on the track that day? No online source can match that! Also, nothing is more frustrating for a modeler than to see that kit he wants, only to find that the paint rack(s) are all but empty! Since almost no hobby retailer can be an expert on everything in the store, searching out and recruiting sales help who ARE KNOWLEGEABLE is key as well, and for more than one reason: First and foremost, having someone on staff, certainly at the busier times of the day or of course, the busiest days of the week (weekends) who can assist customers in any one of the specialties the store carries again is key to countering online sellers (back in the 1980's when I had my store online did not exist, but phone & mail order certainly did!). In addition, there is no way one person can always take care of ringing up sales, reach out to the new guy who just walked in perhaps for the very first time, answer the phone, fix that kid's RC car, describe the in's and out's of this or that RC system, explain to the novice model railroader that he cannot lay track in a "reverse loop" without insulated rail joiners, and a "double pole double throw" electrical switch. Thus some additional staff is necessary if the store is to survive, grow and prosper. When I needed to add staff, I simply did not just put a mirror under the nose of the first person walking in the door looking for a job, and if steam on the mirror, hire him--in fact, my recruitment concentrated on customers I knew, whom I figured might like working there, and had a passion for at least one area of hobbies. In recruiting them, I explained my philosophy that while I didn't expect my staff to be expert hobbyists, I needed them to have an interest in at least some category in the store, use that to their (and my advantage) AND THEN be willing to learn, to try out other types of hobbies that we carried. Above all, I tried to instill in them that while I didn't want any customer to feel "pressured" to buy, I was adamant that they suggest add-on items that would enhance the hobby experience they were looking at (that's why at McDonald's, it's "would you like fries with that?"). Why so you might ask? Well simply put: If a customer walks leaves after a purchase, without being at least exposed to that bottle of paint, or some fresh sharp Xacto blades (you can add in anything here you might think of), then that's money walking out the door! It's those little add-on's that build business (and no, it's not trying to fleece anyone--after all if they have to come back for something they discovered they need once they get home, they have to burn gasoline at $3+ a gallon to come back--so the simple act of suggesting actually can save them some $$--not to mention their leisure time!). It should go without saying that customer service, especially if a model kit has a defective or missing part: I do know that wholesalers today still do allow returns of defective items, certainly with plastic kits: In all my years of being in the retail hobby business, I NEVER saw ,model kit returns for defective or missing parts even approach 1% of my sales, and I never had a wholesaler refuse to accept returns on those. The same was true with many other items, although for their own reasons, manufacturers of RC gear and at least some Model RR products do not accept returns except direct to the manufacturer, so that is an area where real diplomacy comes in--and sometimes, outright "eating" of a product (I found it better to just replace that first burnt-up, overcharged 9.6V battery pack the first time, along with a careful explanation of why that happened, than to lose that customer forever (Oh yeah, there will always be those few who try to "game" or abuse the setup, but my experiences were more than positive. Lastly, owning a hobby shop is a FULL TIME job, no way around that: Anyone going into the business thinking they can just slip out whenever to play a round of golf won't last long. You will be enslaved to that sign that says "OPEN" or "CLOSED", and be expected to be at work on time every business day, but also it will be anticipated that if the customer shows up 2 minutes past closing, you'll smile, unlock the door, and take care of them. Just a few of the things I learned from working full time in a large hobby shop here 1963-73, part time and as a "consultant" from 1973-1983, and then my own store from 1984-92. Art Anderson -
Painting with Nail Polish question....
Art Anderson replied to kitbash1's topic in Model Building Questions and Answers
Or get a package of those white plastic picnic spoons--"spoon test"? Art -
Painting with Nail Polish question....
Art Anderson replied to kitbash1's topic in Model Building Questions and Answers
Nail polish (fingernail polish) can most certainly be thinned for airbrushing! Virtually all fingernail polish is lacquer, regardless of what the label might say, so thin it with ordinary lacquer thinner, to approximately the consistency of 2% milk. As with all lacquers, use an automotive lacquer primer on the plastic first. Most fingernail polish is at least somewhat translucent, and in my experience, the "fluorescent" colors are themselves translucent given that fluorescent colors (also called "dayglo") use a type of dye rather than pigment--so they need to be sprayed over a white base coat--use white automotive lacquer for this (Tamiya or Modelmaster lacquers are a non-penetrating type of lacquer--meaning that their solvents do not "attack" or penetrate/craze styrene plastic, and the "hotter" solvents in nail polish will attack the milder hobby-type "lacquers", making a mess). As for airbrushing the nail polish (for that matter the automotive primer and white base coats), I like to add just a little bit of lacquer thinner to these as well, then use as little air pressure as I can (you can reduce the air pressure by several means, including loosening a threaded coupling to "bleed off" air pressure). I bleed off excess airpressure at my moisture trap by opening the water drain petcock on it, then closing it down just to the point where my airbrush starts to spray. I then open up the material control on the airbrush to get a spray pattern that's about 3/4 inch wide, at about 1 to 1 1/2 inches from the surface of the model. I then move the airbrush fairly quickly to give a fine coat, that with the primer may cause a bit of fine "frosting" look to the surface, but with successive passes, the primer will cover that with no noticeable crazing. When the primer coating is dry, I polish that to a satin finish with a #6000 Micro Mesh polishing cloth and water. I then follow that with the color coats. If you wish a clear coat over your final color of nail polish, may I recommend using a lacquer clear coat rather than Future, as a lacquer clear coat will bond to the lacquer finish underneath it, and it can be polished out with the MicroMesh polishing system. Art Anderson -
Except that there were no Ford or Mercury woodies built with wood veneer over steel panels. In 1950, due to the deepening Korean Conflict and the military buildup at the outset of the Cold War, Ford cancelled the planned replacement of molded plywood with steel stampings after only a handful of these bodies were built that way, and went back to using the molded plywood (which in the case of the car pictured, is what that is--splitting, delaminating molded plywood, so no steel panel would show behind the distressed wood. Art
-
Ranchero was a version of the two-door station wagon body, which used the same doors as the Tudor sedans. That was pretty much the standard across the US auto industry back then. Art
-
Jairus makes some very valid points here: In truth, it is virtually impossible to make any model car kit that we'd buy in any quantities that will be PERFECTLY accurate. Any really close inspection of the real car vis-a-vis the model will surely show up some compromises, someplace. Some of us are "the older generation", myself for example: I've at least waved my hand over virtually every 1/25 (even 1/24!) model kit that's been done of an American car since 1958 (or even before that with several of the Premier kits that came out just about 60 years ago), and have seen compromises. Why? Well, for starters, those of us in this "older generation" voted strongly, vociferously for model car kits having 1-piece body shells for example--that happened with the very first AMT 3in1 Customizing kits in 1958. All of a sudden, the then newly introduced Revell kits of say, the 1957 Ford Country Squire, with their multipiece body shells were ancient technology--not many of us then 13-14 year old kids bought those, one-piece body shells in those AMT kits took a LOT less work. But, a unitized, one piece body shell, certainly in the case of American cars of the day certainly had its compromises in some areas, simply because what AMT was replicating in one piece were car bodies which in real life, had at least a couple of dozen INDIVIDUAL sheet metal panels, with a lot of sculptured shapes. In some subjects, there exist what would be called in a plastic model, rather severe undercuts, particularly with those cars having dramatic tail fins--for example, where the tailfin "sculpture" meets the beltline, which was more often than not within the bottom edge of the rear quarter window openings of a hardtop body (Think almost every Chrysler product 1957-60, and certainly 1957-59 Ford Motor Company cars--not a one of those body shells has quite the correct contour of the inner side of the leading edges of their tail fins due to the limitations of injection-molded plastic in steel dies IF the body shell is to be done as a single part. Look at a JoHan or Revell-Monogram '59 Cadillac: Do you see any fairing detail on the inner side of the fins, forward of the taillight bezels that is molded as a shape part of the body shell? No, of course not--that's virtually an impossible shape to capture in the tooling for a one piece body of any 1959 Cadillac. (JoHan took care of that by molding both the inner and outer taillight fairings in unit with the taillights & bezels, and the chrome "cap" at the rear of the fins, which Revell provided those "spear-shaped fairings as separate parts to be glued in place. (AMT and Polar Lights, with their snap-tight iterations of the Ecto-1a and Ecto-1 had to make the fins as separate, add-on parts, due to the impossibly tight areas between those fins and the rear sides of the basic Miller-Meteor ambulance body. Other areas of model car kit bodies have their "compromises" as well, again part of the problem of creating in one piece what Detroit used multiple complicated sheet metal panels to achieve. Model kit "glass" is almost always (and this includes those kits from just about every manufacturer of plastic model kits) far thicker than the real glass is--even the .020" thick Pet-G clear plastic that the top resin casters use for vac-forming windshields and back glass scales out to 1/2" thick--more than twice the true scale thickness of real automotive glass. Under the hood, similar compromises often exist, given that sand-cast iron cylinder blocks, bell housings and certainly transmission cases can and do have raised details on just about every plane--something that cannot be accurately represented in injection molded plastic without much more expensive and fussy tooling or say, an engine block made up of 4 or more individual parts. The same is also true of frames, particularly those having X-members with lightening holes punched into them--almost always, this is/has been a place of compromise. Even wheel rim lips generally are far thicker than they would be if truly in scale. I know, long story here: But, for the vast majority of builders, the Revell '57 Ford looks pretty decent, even if it hasn't got exactly the right front splash pan. But that's something a serious modeler can work beyond, IMO. Art
-
lacquer dos and donts... help please
Art Anderson replied to ratchetman87's topic in Model Building Questions and Answers
Andy's on this pretty good, IMO. Like him, I've been using automotive lacquers since the middle 1960's, and here's what I use: A good grade of automotive lacquer primer, followed by the lacquer color coats, every coat being laid down with a Paasche H-series airbrush. For thinning, I settled on low temperature lacquer thinner--preferably "50-degree" (meaning that it's meant to dry at 50F ambient air temperature--at ordinary shirt-sleeve room temperature, it will dry quicker, which is good for model work). As for how much thinner to use, frankly, IMO "formula's" are for the birds here--rather, mix lacquers and lacquer thinners to the consistency of 2% milk (this visual mix works just as well for enamels thinned with lacquer thinners in my experience). With the primer, do exactly the same thing, and AIRBRUSH the primer! Why go to all the work to get a nice paintjob and then "firehose" lacquer primer on the model first? I airbrush primer on a body shell lightly at first--just enough that the thinner might "frost" the surface of the plastic only slightly. Once that has dried for just a few minutes, I can repeat the passes with the primer, and find that by the end of the second round, no more frosting (actually very slight crazing) goes away, and the solids in the primer will fill that. I use just enough primer to get to that point and then stop. Before I lay on color coats, I simply polish the primer with a piece of 8000-grit polishing cloth first. That way, I get smooth color coats from the get-go. Color I airbrush on all at one sitting, with lacquer thinned as I describe above, but using the lowest pressure I can get away with, opening up my airbrush for a decent "fan" or pattern of about 3/4 inch with the airbrush about an inch from the surface. Now, I have to move the airbrush along a bit quickly to avoid any puddling of the paint, but that is a technique that is easily learned with a bit of practice. I just keep making passes around the model, sides, ends and upper surfaces (as well as the bottom edges and in the window areas) until I get full color buildup, and if I've done it right, the way I always do, I get a paint job that will be smooth, somewhat shiny, needing only a flannel polishing cloth and polishing compound to rub out to a high shine. Unless I am using a metallic paint, I almost never use clear over color, as I don't like burying any raised details if I can help it--why pay for a nice model, then bury all that under paint so thick it can't be seen nor foiled? Clear, of course is almost a requirement over metallic lacquers, as any serious polishing will alter the shade of color, as the carrier gets polished off the metallic powder. Art Anderson (Norbie approves of this posting) -
You do realize that behind the front clip--those two bodies are completely different? The Fairlane 500's are a longer car overall, with a longer wheelbase, and a lower roof line than Ford's 1957 Custom and Custom 300 series sedans and station wagons. Revell's new kit looks very spot-on to me. Art
-
so how do i fix my boo-boo?
Art Anderson replied to allecb's topic in Model Building Questions and Answers
In the real world, pearlescent paints are actually clear coat with pearlescent powder added to them (Tom Gaffney's LMG Enterprises explained that years ago when he and his wife were marketing pearls for custom car modelers). For a pearl white: Primer, then a gloss white color coat, followed by the pearlescent clear coat. Art -
Check the new issue of Model Cars Magazine guys! Charles Rowley (whose scratchbuilt trucks and fire apparatus have become legendary) wrote a great article on soldering brass--lots of pics and easy-to-follow text. Art
-
Brett's calling this one pretty right, actually (and unfortunately)! With the possible exception of three Indy car subjects from the 1960's (Jim Clark's Lotus 29/38, Parnelli Jones STP #40 and the Graham HIll/Joe Leonard STP Lotus 56 turbines) model kits of Indianapolis cars have virtually never set the World on fire for market popularity. Yes, they have traditionally had a good run in the Midwest (within say, 500-600 mile radius of Indianapolis), and perhaps a flurry of interest across the rest of the US around race time, but that's about it. In my years of working in, and owning hobby shops, I was able to buy stocks of Indy car model kits from our hobby distributors for years after the kits had been produced--they were pretty much "dead stock" (imagine being able to buy case lots of those MPC 1968 Eagles and Wedge Turbine model kits in case lots all the way out to 1984-85!). Somehow, I doubt seriously that any model kit manufacturer is likely to sink any money into new Indy car kits, unfortunately. Art
-
That's either maple or birch (another hardwood with a very fine grain pattern). FWIW, oak was never used by Ford (or for that matter any of the other makers of wooden station wagon bodies, due to its weight and oak's tendency to break easily when cut into thin, small sections). As produced, all the wood "framing" on the last series of Ford and Mercury woodie station wagon bodies (both marques used exactly the same station wagon body, only the front doors being different due to the styling differences in the front clip) was made by bansawing hard maple into thin, flat strips which were then coated with glue, and placed into molding dies and pressed into the curves needed for the shape of the body shell, under heat to cure the glue quickly. After removal from the molding press, each piece was then milled slightly to give the rounded edges, and hand-fitted to the molded plywood panels, then sanded and varnished. The plywood panels were made in the same manner as the framing--thin layers of birch, with an outer layer of Honduran mahogany were coated with glue, then placed in a molding press which formed them into the curved body side panels you see on that car. This was not a new technology for Ford--their Iron Mountain MIchigan factory produced hundreds of wooden gliders along with other molded plywood components for the US war effort during WW-II, and molded plywood furniture was very modern, very popular from the late 30's until at least the early 1970's (ever sit at a grade school desk in those years? Those molded seats were made by the very same process!) The confusion can come very easily from the efforts of early restorers of these, and other woody station wagons, as furniture-grade hard maple in sections large enough for milling such dramatically curved parts isn't easy to come by, where many woodworking shops can access oak pretty easily. Why were these wooden panels so hard to come by as restoration parts years ago? For starters, those panels are absolutely not structural: Once made, they are simply that, panels, and were fastened into recessed areas of what was otherwise essentially an all-steel station wagon body, where from 1929-48, Ford station wagon bodies were entirely wooden construction, built using hard maple structural frame work glued together with common cabinet-working dovetail and mortise & tenon joinery, then attached to flat plywood panels by means of plated "jail bolts". A note about the finished look: Maple, being a very fine, close-grained wood, does not have the very prominent "light-dark", closed-open rings that oak and other larger hardwood trees have. Therefore, especially when molded as these '49-'51 Ford Motor Company bodies were, even in the few areas (at the exposed ends of some of the framing sections) where the end-grain is visible, there isn't all that much variety in color to be visible--certainly almost none along the flatter surfaces. Another confusion that can come from looking at the picture Bill Barrett has put up here comes from the "swirling" grain on some areas of the framing. By the time these bodies were built, the parts had to be made as described, simply due to the depletion of furniture-grade maple in any serious quantities from the vast forest holdings of Ford Motor Company in the Upper Peninsula of Michigan, resulting in some of the less desireable grain patterns that can be seen on these wagons. The color of the wood panels is also darkened/enhanced by the use of spar varnish, which isn't water-clear, but rather has an amber hue to it. Several coats of varnish were applied at the factory, and the owner's manual recommended a light sanding and re-coating with fresh spar varnish every year. Art
-
What happened to all the pinned tutorials?
Art Anderson replied to sjordan2's topic in Tips, Tricks, and Tutorials
Yeah, that gets frustrating at times! Art -
Plastic vs. diecast
Art Anderson replied to oldcarfan's topic in General Automotive Talk (Trucks and Cars)
Except for the very high-end diecast scale models such as Franklin or Danbury Mint, Highway 61, Auto-Art, which are masterpieces of ready-assembled, painted and detailed scale models, the vast majority of diecast model cars and trucks are actually quite simple. Case in point: Nine years ago, while at Johnny Lightning Division of Playing Mantis, I was assigned to develop a small series of 1/24 scale diecast models, one of which was their '57 Ford Courier Sedan Delivery. Now, to the untrained eye (less sophisticated, probably not a model car builder), from say, 3 feet away, it looks as nice as the new Revell '57 Ford Custom 2dr sedan. It's when you look closely, pick it up, turn it over that the differences between this $35 MSRP diecast and the $25 Revell model kit become very apparent. The diecast body is a one piece shell with hinged hood--that's not a lot different in engineering than the Revell body. The interior is at best 4 ABS plastic pieces (most popularly priced diecasts have an interior molded in one piece flat, with relieving "grooves" molded in to allow the sidewalls to be folded upright to form an "interior tub", the two seats being molded as part of the floor (it's a sedan delivery, so no rear seats. The dash and steering wheel are separate parts, engineered to be snap/press fit in assembly. There is a clear windshield and back window. The ABS plastic engine under the hood is just two pieces, the engine itself with a separate air cleaner, again, two parts simply press-fitted together. The ABS plastic chassis is one piece with some surface detail, very much like a 1960's promotional model. Each ABS wheel is three parts (rim, plated hubcap and PVC tire). There are clear headlight lenses, with a pair of clear red taillight lenses. The ABS plastic plated parts are the grille, front and rear bumpers, of course the hubcaps, along with a pair of outside rear view mirrors, making a total of just 30 parts. Now, compare that with the 90-100 parts, all pretty much correctly scaled and detailed, in the Revell model kit, and that is where the difference in upfront, or capital investment cost lies with diecast vs plastic model kit. For every part or piece in both a diecast model and a plastic model kit, there is a cost--that of course varies according to the complexity of the particular part, but most generally I suspect the cost per component is pretty close one versus the other, although the body shell for a popularly priced diecast doesn't require nearly the engineering/pattern-maker's finesse that a plastic kit does--almost all the work in developing a diecast body shell goes into exterior shapes and detailing. The same is true also of many of the ABS parts, as only those which are clearly visible with the model sitting on a shelf have to be particularly accurate and finely detailed. In cutting the tooling, there is a fixed cost for each tool-base (the basic block of steel in which all the parts cavities are engraved, plus generally a charge for each part engraved there. So, the upfront costs of a popular-priced diecast model (such as you might see on an ordinary retail store's shelf) is certainly a great deal less than they necessarily are for the type of model car kit we on forums like this expect to see when we open the box. Of course, many wonder why a diecast sells for as much or more than a nice model kit: That's due to the fact that almost without exception, diecast models are sold as assembled and finished products as opposed to kit form. Probably with this '57 Courier, there were upwards of 75 or 80 production "stations" set up to mass-produce this model. While the basic body color on this model is white, which was painted in groups of perhaps 25 or 30 body shells at a time by one worker using an ordinary production spray gun (such as you might see in a body shop!), and then the painted bodies run through a drying oven to bake the white paint on, every other color was either "spray-masked" or Tampo (pad printed) on. "Spray masking" uses a simple semi-automatic sprayer fitted with a specially formed copper "mask" against which the part of the body shell to be painted a second color is held, the operator simply stepping on a pedal and "pssssst", the second color. Depending on the complexity of the color scheme, there can be multiple spray mask steps to complete all the secondary colors (in the case of this Courier, it's done in 1950's Coca Cola livery, so the secondary colors sprayed are Coca Cola Red, and Coca Cola yellow), along with silver paint spray-masked where "chrome trim" would be on the real car--each mask and spray operation here is a separate one as well. Last comes the pad, or "Tampo" printing. Each emblem, stripe and logo is a separate pad print operation, and in the case of the Ford crest on the tailgate handle, four pad print operations (black, red, white and blue). Just as with the spray mask, every pad print step is a single operation, one operator and one machine. All the rest were pretty much hand operations, what we in the US call "light assembly". These range from the filing and cleanup of casting flash and attachment points (diecast is done on sprues, just like styrene plastic kit parts, to the folding up of the interior molding, adding the dash and steering wheel, inserting the clear windows, adding each part to the body shell and so on. Every production step was broken down in true mass-production fashion, each worker performing just one operation and then passing the product on to the next station. By contrast, the packaging line for a model kit has a lot fewer stations. I hope this long description helps! Art