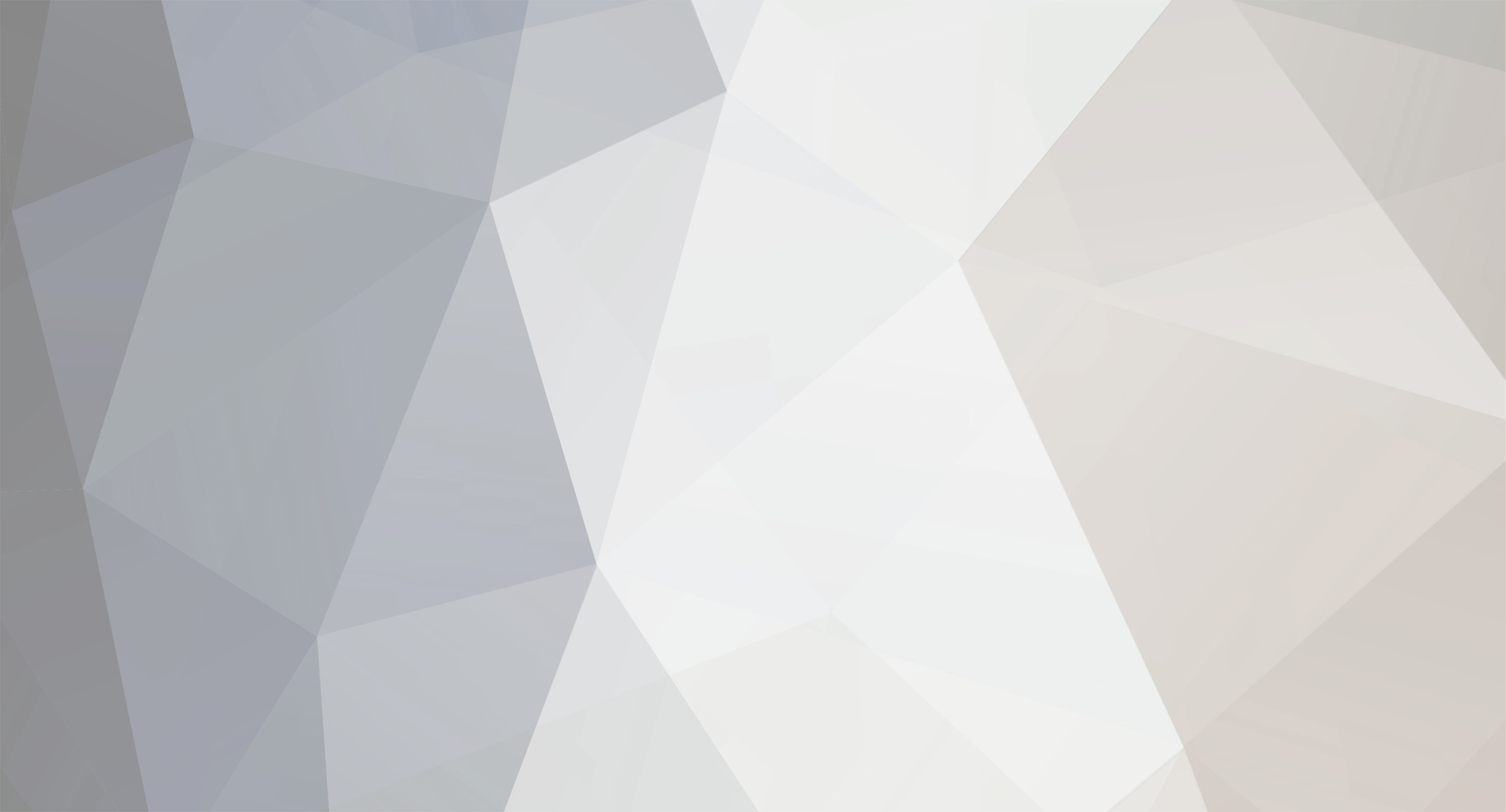
Art Anderson
Members-
Posts
5,052 -
Joined
-
Last visited
Content Type
Profiles
Forums
Events
Gallery
Everything posted by Art Anderson
-
(NEW Update! 6/19/15) IN progress, ICM '13 Model T For
Art Anderson replied to Art Anderson's topic in WIP: Model Cars
Test fitting of the completed wooden dashboard and the steering column--it all fits! (even though perhaps the clearance through the dash for the column is just a bit smaller than I had hoped, but I'm not going to modify any further. -
MPC/ERTL Indianapolis 500 Hall of Fame Set # 6426
Art Anderson replied to Miatatom's topic in Car Kit News & Reviews
If anything, the tires that AMT has used on the Lotus 29 (actually almost a Lotus 34) and the Agajanian Willard Battery Special are larger than the 1964 and later-out-to-modern era Indy car tires. The story goes like this, pretty much: Indianapolis Motor Speedway owner, Anton Hulman Jr., worked pretty hard to entice European Grand Prix teams to come to Indy (what most do not know is, the Indianapolis 500 paid World Driving Championship points from the mid-1930's through the late 1950's!), and as such, there were accommodations made in this regard. When Ford approached Team Lotus with the idea of a Ford powered Indianapolis effort (remember, this was the era of Ford-advertised "Total Performance"!), Lotus Cars responded with a chassis based on their conquering Lotus 25 F1 car, which became the Lotus 29. In those days, the standard USAC Championship race car tires were 8:00-18 rears, and 7:50-16 fronts, on those sizes of Halibrand magnesium wheels. Team Lotus persuaded Halibrand to come up with 15" wheels for their entries, and Firestone Racing Division provided this diameter tire for them, for the 1963 500. (For 1964, Lotus, driven by a dutiful patriotism toward British manufacturers, had Dunlop build the same size tires, with disastrous results!). Those 1963 Firestone Speedway Specials built for Lotus were large, with nearly the same outside diameter as the 16 and 18 inch rims and tires used on all the roadsters--and war broke out in Gasoline Alley. Halibrand and Firestone both went into overdrive, and managed to equip about half of the Offy Roadster teams with the new size wheels and tires. The remaining entries were stuck with the older tire and wheel sizes. It wasn't until 1964 that Firestone brought out what they advertised as the "Wide Oval" tire configuration. The original soft PVC tires that AMT used in their Offy roadster and Lotus Ford kits were much more correct--having the proper tread pattern but with no sidewall detailing. Art Tom, Models of Indy cars were a big thing in my hobby life for so many years, it all comes out when I see a thread like this! Art -
MPC/ERTL Indianapolis 500 Hall of Fame Set # 6426
Art Anderson replied to Miatatom's topic in Car Kit News & Reviews
For starters, the McLaren is supposed to represent Rutherford's 1974 Indy winner, which actually was the M16D, but the AMT kit was a slightly modified version of their 1973 Penske McLarens, which were -C's. This image shows the major difference in layout that AMT ignored (more than likely for cost reasons--as AMT was beginning their slide into oblivion by 1974-75 when the Rutherford kit was in development: http://blog.ims.com/wp-content/uploads/2013/01/jr_qual.jpg Note that the exhaust header and the placement of the turbocharger are quite different from the AMT kit you have, in that for the 74 Team McLaren M16D, the turbo is turned upside down, in an "undershot" position (virtually every other Turbo Offenhauser engine had the turbocharger mounted as an overshot unit (meaning the exhaust pipe goes into the top side of the turbo, where the undershot exhaust goes into the underside. In addition, McLaren fitted their Offies that year with a tuned exhaust header. To acommodate the moving of the turbo forward of the rear suspension mounting points, McLaren Cars added an extension to the driveline, in the form of a spacer that was approximately 10 inches long, between the flywheel housing and the front of the transaxle, increasing the wheelbase by pretty much that distance. On the right hand side of the engine cover, your kit has a rather crudely done blister as a separate part for the engine cover, which is pretty incorrectly done as well: It's nowhere near as prominent on the real car as depicted in the kit parts, the forward end of the blister should be rounded, rather than having a blunt, squarish profile as the AMT kit, when viewed from the right side. The rear wing, IIRC, is still the 1973-type, which was way wider than allowed after the disastrously fatal Month of May in 1973. USAC mandated a much narrower wing starting with the Milwaukee race a week following Indy back in those days. On the tub, AMT left the right side fuel filler plug, which for 1974 and beyond, could no longer be installed--in fact, for the '74 and subsequent seasons (Both USAC and later CART) banned right side fuel tanks completely. Note also that the remaining two filler ports on the left side are very nearly flush with the surface of the bodywork, not just "laid on" the outside as in the AMT kit--that's pretty easily fixed on the model BTW. Also, while AMT made the panel immediately behind the cockpit as part of the cowling/engine shroud part in the kit, those "panels" are actually 3 separate sections on any McLaren M16 series cars. The cowling around the cockpit is a separate, lift-off panel, as is, of course, the engine shroud--the part in between that looks like a headrest is actually integral with the tub chassis, and was one of two fuel tanks on this car (1972 and 1973 M16's had 3 tanks), the so-called seat tank. This is Gary Bettenhausen's 1973 M16D, as it qualified for the 500 in 1973--the kit on which your Mclaren was based--note that it has the longer, blunt nose, but with a flat upper surface rather than the curved shape depicted in the AMT kit. http://i489.photobucket.com/albums/rr259/racebrown27/GaryBIMS1972_zpsd4db13b3.jpg Up front, the nose cone is completely wrong, even for a 1973 M16--that downward-curved, long nose cone appeared only in the first few days of practice back then (up through 1973, practice for the Indianapolis 500 Mile Race began on the 1st of May, which gave 2 to 2 1/2 weeks of practice before pole day--LOTS of changes got made to cars in that period, in the annual search for speed!), and was replaced by the shorter, tapered, flat-topped nose cone you see in Rutherford's official 1974 qualificactions picture. That can be made from pieces of Evergreen sheet styrene rather easily. I modeled Rutherford's '74 winner in the summer of 1979, after having been given a quart of REAL McLaren Orange lacquer by none other than "Lone Star JR", while touring Gasoline Alley during a rain delay on the Friday before Pole Day that year (Team Mclaren's support vehicles--golf carts, battery carts, push tractors were still painted in McLaren Orange that year), so I know the work can be done--even whittling out that driveline extension casing from two layers of 1/8" sheet styrene went very quickly--all that was left was to make longer trailing arms for the rear suspension. As for the tuned header, cutting up a couple of Offy exhaust manifolds and some creativity worked there. Also, note that Rutherford's '74 winner has it's rear wing mounted on a single, central pylon--again easy to make from some thick Evergreen stock, with files and sandpaper. As a bit of backstory here: From 1966 through 1983, my model car building passion was doing the cars of the Indianapolis 500 from 1911 out to whatever the present day might have been at the time. Along with several other local modelers, I put on an annual Month of May 500 Mile race display in the 20' wide show window of Weber's, then the dominant hobby shop here in Lafayette IN (and one of the most comprehensive hobby shops in the Midwest back then). At it's peak, our display included over 200 1/24-1/25 scale models of cars that faced the Green Flag at the Speedway on Race Day, with their car name, driver's name, qualifying speed and start-finish record, on small wooden plaques placed in front of each car. We created a 15' long wooden platform, covered in Walthers O-Scale red brick paper, to replicate the original brick front stretch, with the open pit area used through 1956, complete with a 1/25 scale wooden model of the original "Pagoda" which was the forerunner of the Bombardier Timing & Scoring Tower used today. We also got the use of display Goodyear Speedway Special racing tires every year from our local Goodyear Tire Store, and a wheel & tire from Bill Vukovich's 1952-54 Kurtis 500-A roadster. A couple of times we had an actual Offenhauser racing engine in the display, gutted of all internals--but it got attention! By 1970, the window display attracted so much attention from race fans, even racers, mechanics and car owners (even the Speedway Oldtimer's Club), that the store owner put in a Guest Register, for visitors to sign in on--and that reads like both a geography lesson and a veritable Who's Who At Indianapolis Motor Speedway from back then. I've also been told by Chris Etzel (who grew up here, and I knew from the time he was a kindergartener) that the window display is what inspired him to start Etzel's Speed Classics, as a maker of exacting 1/25 scale Indianapolis cars staring in 1995. Art -
(NEW Update! 6/19/15) IN progress, ICM '13 Model T For
Art Anderson replied to Art Anderson's topic in WIP: Model Cars
To elaborate, the top four posts are for the ignition wires from the "timer", in order 1 through 4: Black, Red, Blue, Green, just as Ford made them. The lower left-hand wire is from the flywheel magneto, and is red. The lower right hand terminal is for a battery, for starting an early T which had no storage battery. Art -
(NEW Update! 6/19/15) IN progress, ICM '13 Model T For
Art Anderson replied to Art Anderson's topic in WIP: Model Cars
The dashboard is done, ready to install on the model! For those who haven't followed this, I replicated (and corrected slightly) the kit dashboard (on a Model T, the dash is what most would call a firewall, but the correct styling term for years for what we call a firewall is "Dashboard"--that panel inside with instruments is correctly termed the "Instrument Panel. Anyway, here it is, in all its glory: -
Guys, didn't Gregg commission a set of MCM logo decals not more than about 10 years ago, Hmmmm? And, has nobody responding to this thread ever bothered to consider that creating a decal version of the MCM logo STOMPS all over the registered (surely it is registered!) trademark of the very magazine which sponsors these online forums? Hmmmmmm? Art
-
Any chemists out there?
Art Anderson replied to Harry P.'s topic in General Automotive Talk (Trucks and Cars)
For starters, hemp wasn't grown industrially in any quantity until WW-II, when the Japanese conquests in the Southwest Pacific Ocean (Indian Ocean too) pretty much cut off the supply of hemp for rope making (hemp rope was then an absolute necessity for just about every naval force in the entire world, not to mention merchant shipping!). Even at that, the emphasis on farming hemp was centered primarily in northern Indiana and northern Illinois, which produced a grade of hemp inferior to that which had come from India and other regions in far southern Asia. As a result of that encouraged cultivation, we still fight a battle against so-called "ditch weed" here, as the stuff spread like wildfire (I well remember having to pull the BLAH_BLAH_BLAH_BLAH out of the ground at the back of the lot in West Lafayette 50-60 years ago, pile it in Dad's trashburning cage, and setting it on fire--I knew what burning pot smelled like well before it became the recreational drug it is today! Actually, Henry Ford briefly considered promoting ethanol as a motor fuel--made from corn, the economics of which he understood pretty well, having grown up on a farm very close to Dearborn MI--but he soon gave up on that idea and with good reason: It took a LOT more acreage to grow a bushel of corn a century ago than it does today--probably 3-4 times as much. My dad, who grew up on a very fertile farm in Benton County IN (some of the most fertile farmland on the planet!), explained to me in the early 1970's that in Henry Ford's day the bushel per acre yield of corn was about 15% of what it was in 1970, and while that yield has gone up tremendously since then, it's still a very costly proposition--made possible only by the ever widening uses for corn today. What Ford did to, was to show what could be done with soybeans--and it was Professor George Washington Carver, teaching and researching at Tuskegee Institute, what could be made from soybeans--which in his time were an exotic crop imported here from--CHINA. A 1940 Ford Deluxe, the version modeled by both AMT and Revell, had as most of it's dashboard and interior trim, plastic parts (in 1940, plastic was the exotic, the new, the high tech thing!) made from soybean oil. Henry Ford, the former farm boy from SE Michigan, never really forgot his rural roots, and he did aim much of his thinking toward farmers. Art -
Any chemists out there?
Art Anderson replied to Harry P.'s topic in General Automotive Talk (Trucks and Cars)
Not to mention the methane emissions from some 8 BILLION human beings on this planet, and the probably trillions of termites as well. Art -
Any chemists out there?
Art Anderson replied to Harry P.'s topic in General Automotive Talk (Trucks and Cars)
Uh, the Brazilians didn't need Henry Ford to sell them on the ethanol idea--in fact almost no country needed that! Ethanol is what Granny Clampitt called "Corn Squeezin's, better known as White Lightning, Moonshine, and more politely, just about any alcoholic beverage you can name. Of course, ethanol for motor fuel has to be far more completely distilled than hooch, in order to get the water out of it, a process that in itself is not particularly energy efficient. In the case of Brazil, they settled on the idea of making ethanol from cane sugar at a time BEFORE their considerable oil reserves were discovered (mostly offshore rigs), so it was the best alternative for a developing but still 3rd World country having not much in the way of exports to fund the purchase of foreign sourced crude oil. Motor fuel has always been ruled by two things: Cost, and portability. As for cost, consider that there isn't much "free" hydrogen in our atmosphere, given that it's the most flammable of all gasses, combines readily with oxygen. It can be reduced from air, by supercooling the air, and then as the various gasses that compose our atmosphere evaporate from the resulting liquid, can be "skimmed off" so to speak, before any other gasses can evaporate (that's one of the products of Linde, for example. Hydrogen can be gotten by breaking down water, but that's not exactly energy efficient either--it takes a LOT of electricity to produce hydrogen in that way, at least to this point. Perhaps someday, the "magic bullet" will be discovered or created that does it, but it ain't there yet. Ab out 5 or 6 years ago, researchers at Purdue University found a micro-organism that in water, actually breaks that water down into hydrogen and oxygen, but yet that process, as it exists right now--would take innumerable acres of land in order to do that, not to mention the immense collection system it would take just to capture the resulting hydrogen. On the way to that, however, is CNG, or Compressed Natural Gas. That is a very clean-burning fuel, and with all the gas discoveries in the past decade or so, a very plentiful fuel. On Wednesday of this week, CityBus of Lafayette IN (where I live) opened the first CNG dispensing station in the State of Indiana--to fuel their new generation of city busses--CNG fueled. Some day, who knows when or how far out in the future, SOMEBODY is going to figure out how to make a combustible fuel for automotive engines that is both energy-profitable (meaning that the input of energy is significantly less than the energy output of the end product--something that is still very illusive in today's technologies), but until that time comes, most all the schemes for creating synthetic fuels is at best an even trade of one form of energy for another. Art -
DECANTING QUESTION - BIG 3 LACQUER-MAKERS
Art Anderson replied to fseva's topic in Model Building Questions and Answers
I've been decanting rattle can paints for use in an airbrush since the middle 1960's, and settled, years ago on simply spraying the paint directly into the color jar of my airbrush! Now, at first, I did get paint all over the fingers holding that jar, but over time I've learned to carefully modulate the spray so that the paint being decanted doesn't just blow right back out of the bottle. It took some practice to get that, to be honest, but that's how I still do it, 50 years later, and I seldom get more than just a bit of overspray on the fingers holding the color jar. The secret? I learned to spray the rattle can stuff against the side of the bottle, NOT directly to the bottom of it. As for "out gassing", I never worry about that--after all, if one sprays rattle can paint directly from the can to the model, it's not outgassed before it hits the body shell, now is it?. Of course not. In addition, where 40 years ago, paint manufacturers were using FREON as the propellant, which took a lot longer to bubble out of the paint--nowadays, since the International ban on the use of Fluorinated Hydrocarbons (which is what FREON was), most all aerosol cans, from paint to shaving cream, use propane or butane gas as the propellant, and that evaporates very, very quickly out of the liquid paint once it's out of the spray can. That's my technique, and I'll stand on it. Art Art -
AMT 1958 Ford roof question
Art Anderson replied to ChrisBcritter's topic in Model Building Questions and Answers
I don't have one handy at the moment, but here's an excellent rear view of a real '58 Ford: http://www.webseitenwartung.de/Kuba/Ford-Fairlane500-1958-1.JPG Note two things: First, there are 7 grooves, all evenly spaced. Then note that the outer-most grooves are almost exactly where the sides of the roof panel flatten out, inboard from the drain moldings. I would measure the roof of the model you wish to groove the top on, then find, as closely as you can, and mark that as the location of the very middle groove. Then outward from there, to each side, measure outward (a set of digital calipers will make this easier!), from the center, toward the sides of the roof, first one side, then the other, a distance that looks right from this picture but yet will be easily divisible by 4 (keep in mind that using the line of the center groove, and going outward to either side, there will be FOUR grooves, counting the center one!). This might not be PERFECTLY accurate, but if you think about it, most people (not having the real car to measure!), will be hard-pressed to argue that that outer groove is a fraction of a millimeter too far in or too far out! Sometimes, the illusion of perfect overwhelms most any observer having no real clue to the EXACT spacing of those grooves (in other words, come as close as you can!) Just the ramblings of a nearly 71 yr old model car builder! Art -
(NEW Update! 6/19/15) IN progress, ICM '13 Model T For
Art Anderson replied to Art Anderson's topic in WIP: Model Cars
Eric, It is getting very close---but some details just take seemingly forever to do. Got the replacement dashboard finished (and I got the angled hole in it for the choke rod in the right place this time. I also made a much better looking coil box (from pictures I found), this time in 1/32" birch plywood, stained and finished the same way as the dash--couple details on the face of that and it's ready to install. It's gonna be fun hooking up the throttle linkage--my T will have the revolutionary ACME Gas Mizer thottle control (Made by the W.E.C Company out of New Mexico--guarranteed to put gasoline back in the tank! . Pics probably tomorrow afternoon! Art -
Herbie Variations - anything out there?
Art Anderson replied to Jonathan's topic in Model Building Questions and Answers
As for variations of Herbie--most of them would require all new tooling, as the original Herbie was pretty much the only stock one. An interesting side note on Herbie: The actual Herbie from "the Love Bug" is a '63, purchased new by Walt Disney as his dailly commuter car to and from the studio. Art -
Jim Clark Museum
Art Anderson replied to eferrari's topic in General Automotive Talk (Trucks and Cars)
I never met Clark--but was absolutely amazed to watch him in practice at Indianapolis in 1965--very easily the smallest driver there--his helmet barely showed above the top edges of the windscreen on his Lotus 30. And smooth? Oh yeah! Those 4-cam Ford Indianapolis V8's were notorious for backfiring when drivers let off setting up for turns 1 and 3, but not Clark--he obviously simply "feathered" the gas pedal preparing for the turns. Then in 1966, his Lotus broke a sway bar--causing him to spin twice during the race--he drove as if completely non-plussed by either 360. The only other driver in '65-'66 that compared to Clark's style at Indy was Mario Andretti. Art -
Jim Clark Museum
Art Anderson replied to eferrari's topic in General Automotive Talk (Trucks and Cars)
A correction: Jim Clark died on April 7, 1968, or 47 years ago today. He was slated to have driven one of the Lotus 56 "Wedge" Turbines at Indianapolis that year. Art -
Galaxie Limited's '48 Chevy Coupe
Art Anderson replied to lordairgtar's topic in Car Kit News & Reviews
The Chevy body won't work very well, as the car your picture shows is a B-bodied car, top of the line for Oldsmobile back then. Olds did build a junior series of cars that used GM's A body though. -
And yet, I used MCW's lacquer primer on my '50 Olds body with no problems whatsoever (They use DuPont lacquers I believe). Oh well, huh? Art
-
Actually, Federal regulations as to automobile headlights didn't happen until the middle 1960's--prior to that they were on a state-by-state basis--some states allowed non-sealed beams, others did not (wonder how they dealt with all the pre-1940 cars that were still on the road with old fashioned bulb headlights?). But yes, the likes of Lucas and Cibie' were illegal in most states--it was a matter of law enforcement either ignoring them, or stopping cars so equipped. Art
-
Well, if you have Scale Finishes primer, I'd go ahead with that. As for spraying other kinds of paint over automotive lacquer primers, I've done that more times than I can count. And yes, automotive primers work quite well on resin bodies. Art
-
Bill Engwer: The patterns, or "swirls" (the lines that indicate where the plastic hesitated flowing during mold-filling) in the surface are a dead giveaway that there'scrazing of the plastic itself going on under the primer. If the primer is not a sufficient barrier, you shoot the color on the "wet" side, and the solvent in the paint is on the "hot" side, you'll get this effect...especially these days as manufacturers continue to experiment with cheaper and cheaper grades of polystyrene that is increasingly LESS solvent resistant. I've been airbrushing model cars with automotive lacquers for a good 50 years now, and have a pretty standard technique I use every time. First, bear in mind that while Scale Finishes paints started out being acrylic enamels (which don't craze plastic, BTW), their modern "base coat/clear coat" car colors are lacquers, and lacquers do take some special handling. And no, it's not something that just cropped up more recently with "cheaper plastics"--that was a huge problem to overcome back in the 60's when AMT, etc. model car kits were being molded in a very hard styrene grade. First, on plastic bodies, I use automotive lacquer primer, and have done so exclusively from the very start of my process decades ago. I thin the stuff to the consistency of 2% milk (done by eyeball, not some set formula, BTW--just by observing how the thinned primer--and finish color--"sheets" down the sides of my airbrush color jar). Then, I use what I call TSC, meaning "Thin, Soft, and Close" with the airbrush. Properly thinned automotive primer won't cover quickly, rather it takes numerous passes with the airbrush to get full primer coverage. By "Soft", I mean as low a pressure in my airbrush as will spray the primer or paint. By "Close" I mean moving my airbrush in close to the surface, generally an inch or so away. Now, when I primer a body shell, I watch very closely. Even very light coats of primer will at least "frost" the surface of the model car body slightly--you can actually see that, but it's a form of "crazing" that is so miniscule that it disappears with each succeeding pass (now on model car kits made in Japan, they tend to use a rather hard styrene blend, which will be subject to frosting much worse than say, the softer styrene blends used by many other manufacturers, so greater care is a requirement here, but it can be done). Lacquer thinners, even the so-called "non-penetrating" thinners will penetrate styrene plastic to some extent. The crazing (even the minute frosting I mentioned above) happens when the solvent releases the locked in stress in injection molded styrene, which causes that "swirled effect" seen in Joe's pics above. So what to do? This is where primer comes into its own on a model car body, in my experience. The solids in the primer will fill fairly tiny crazing/frosting, and the primer can actually be polished out before color coats, and almost always the primer tends to "shock proof" the plastic surface, in my observations over the years. Lacquer primers do not need to have a rough surface in order for the color coats to adhere--all lacquers tend to penetrate preceeding coats of lacquer to at least some extent, so I "wet sand" my primed body shells with 5600 to 6000 grit polishing cloths, which gives me a satin finished primer surface. Then, I use exactly the same "TSC" approach to my color coats--often even to the point of the last passes (particularly with metallics) being thinned even more than when I started. This system works for me, and has for so long that I cannot even use a rattle can anymore--lost my touch with those years ago. Art
-
Dirt tires from the '50
Art Anderson replied to carsntrucks4you's topic in Model Building Questions and Answers
The only separate 1950's style dirt track racing tires I've seen in model kits are the tires in the Revell Kurtis Midgets, but unfortunately those are on 12" rims, and as such are too small for most larger car installation. They are, however, a very reasonable representation of the dirt track racing tire pattern sold by Firestone back then. Art -
I think most all gel pens use an oil-based enamel, which on PVC (vinyl) tires almost never dries. This is due to the "plasticizer" added to the PVC used to make our vinyl model car tires soft and at least somewhat rubber-like. That plasticizer is what caused (and still will cause) the "dreaded tire disease" as it also will leach into styrene plastic, as was certainly the case with those Revell kits of 40-50 years ago. That's why we kids had such a horrible time trying to paint whitewalls on AMT Trophy Series tires back in the 60's, with Testors or Pactra enamel paints. I think there are some brands of gel pens now that use acrylic paint as their medium--and acrylics tend not to be affected by PVC plasticizers. (Bear in mind, that PVC has been around for more than a century now, and in its pure state, is a hard plastic--it was the discovery of chemical additives that made it possible to have soft PVC, for upholstery and the like. Today, the clear plastic "Clinging" food wrap is a very soft clear PVC film--don't even think of wrapping a plastic model car with it--it will mar the surfaces of your model car or parts--even decal sheets, as I learned from bitter experience years ago.) Art
-
Uh, to be really fair, neither Citroen, Ford, nor even Tucker were the first to have turning driving lamps up front! The "Pilot-Ray" system was available as far back as the late 'teens (or a century ago), and was an option on many luxury cars (the lower "driving lights" on every Monogram Duesenberg kit represent Pilot Ray lights, but the kits lack the complete linkage) into the middle 1930's. Pilot Ray lights were swiveling, connected to each other by a small tie rod, and then linked to the steering linkage on the car itself, and swiveled side-to-side as the car was steered in any direction--pointing the light where the car was going, exactly. Trouble was (and Tucker would have had to face this as well), prior to USDOT all automobile lighting specifications were under the control of the individual states, with many state laws prohibiting the use of more than 2 headlights, even a few states specifying that headlights must remain fixed in a forward position permanently. It's hard to imagine now, but the sealed beam headlight was developed by GE several years before they were allowed to be installed on American cars (it took an interstate compact by all the then-48 US states to allow that to happen for the 1940 model year). As for Tucker and their "safety" features, perhaps most notable was the installation of "pop-out" windshield panes, with their "safety chamber" being highly touted (you were supposed to tuck yourself quickly under the instrument panel in the event of an impending head-on collision (remember, Tucker was a rear-engined car), but it's not likely that would have saved many lives It's hard to imagine now, but it wasn't until the introduction of Ford's Model A for 1928 that laminated safety glass came into use in a mass-production car, and yet that was limited on the Model A to just the windshield (Ford added safety glass to the side and rear windows for 1932). Prior to that, ordinary plate glass was used across the industry, with countless severe injuries as the result (some luxury cars had "wired" glass (such as you see in many putblic buildings still), but that was extremely expensive to manufacture--and still is). And this list could go on, and on, of course. Art