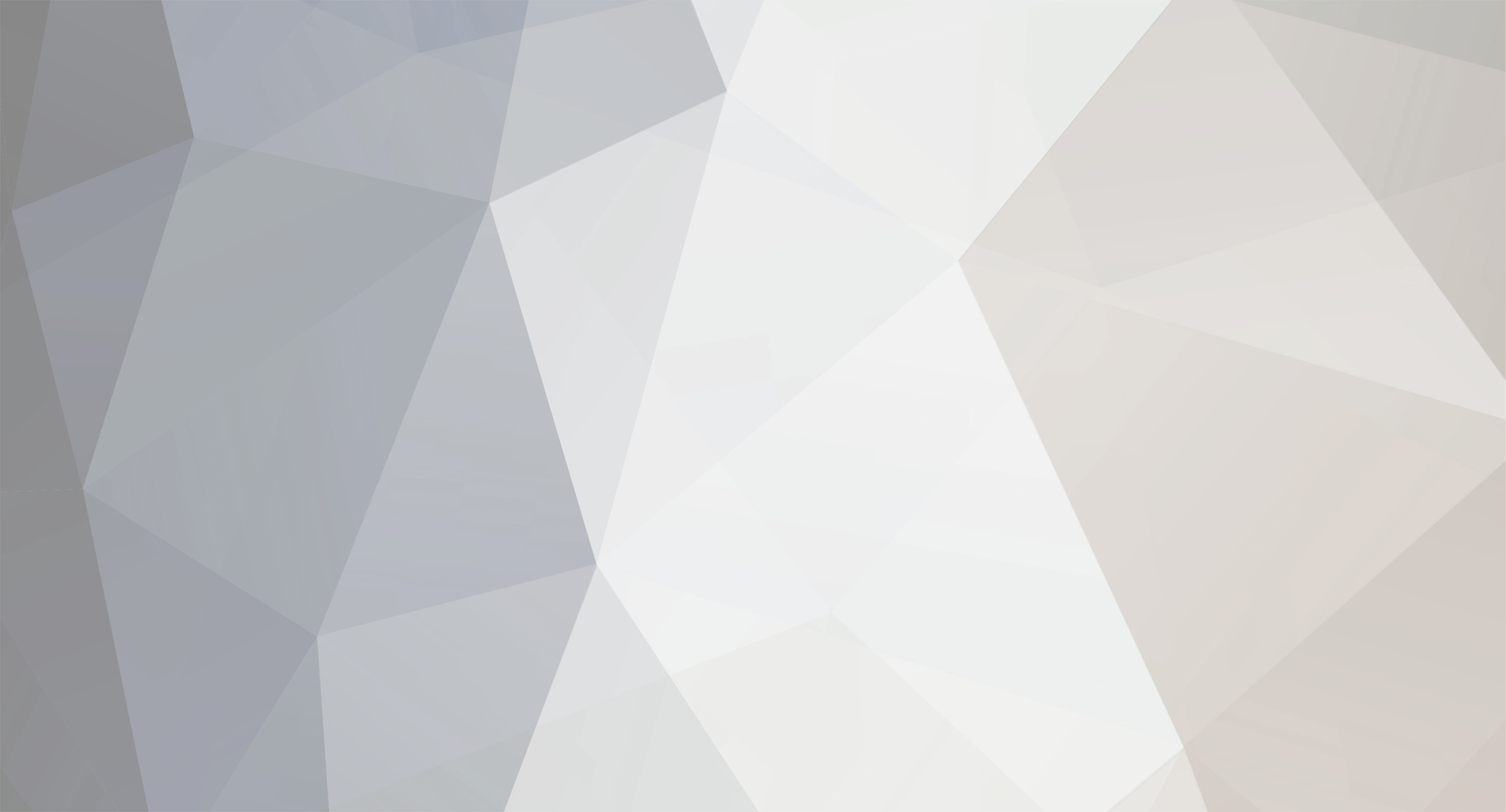
Matt Bacon
Members-
Posts
3,158 -
Joined
-
Last visited
Content Type
Profiles
Forums
Events
Gallery
Everything posted by Matt Bacon
-
1/24th. Vodafone McLaren Mercedes MP4-25 "L. Hamilton"
Matt Bacon replied to Luc Janssens's topic in Car Kit News & Reviews
They’ve announced the 2024 McLaren which should be available towards the end of the year. I’m expecting to see a built up one at Scale Model World (IPMS UK Nats) in November, but probably not to be able to buy one until later. No one is going to give them access to a current season car early enough to kit it in the same year, I don’t think… best, M. -
This color is rather hard to photograph, especially in the velvet texture of the Zero basecoat. Anyone who's used them will also know how much the appearance of Zero Paints colors changes when you apply the clearcoat. I'm not sure when I'll get to do the clearcoat. As a two part mix that actually cures rather than just drying, it's very sensitive to heat. Your working time drops rapidly the hotter it is, and the last thing I want is to be trying to apply the final wet coat when the mix has started to cure (that way you get orange peel, for sure). The workshop is about 34 degrees C at the moment... 😜 best, M.
-
1/24th. Vodafone McLaren Mercedes MP4-25 "L. Hamilton"
Matt Bacon replied to Luc Janssens's topic in Car Kit News & Reviews
I assume this one is just warming us up for the last-season one coming towards the end of the year… best, M. -
The 250 GTO is one of Fujimi's gems, for sure. It's a much later kit than the Enthusiast Model series, but has engine detail, and you can pick up a box with a fabulous set of metal wire wheels in it, though the regular plastic ones are pretty darn good. best, M.
-
Definitely worth doing some research. You can find unboxing videos, and 1999.co.jp (Google “name of kit 1999.co.jp”) has viewable instructions for most kits. Fujimi kits in my experience are a mixed bag. As mentioned, the Enthusiast Model kits are complex and amazingly detailed. They are also often boxed without the Enthusiast branding (often as Manga tie-ins) or as regular “Red box” kits, sometimes without detail parts trees (eg no engine). Check instructions for particular boxings to see what you’re going to get. There are regular curb side kits. Many newer ones are well shaped and have accurate if simplified detail. Older ones are often over-simplified and sometimes compromised by having been designed to be battery powered back in the day. But they are often the only game in town. Some kits are not strictly 1/24 scale: the accurate Tamiya 240Z body fits neatly inside the Fujimi one, for example. Fujimi often plays fast and loose with versions of the basic car. The box may call it one thing, with accurate, well done box art, but it’s writing checks the plastic can’t cash. What you get inside is the same in three boxes, perhaps with an extra parts tree (say, seats and steering wheel). The FIAT mentioned above is one example. The RX-7 Spirit R is another: you get a few different decals and some Recaro seats, but the nose/front clip is not modified at all into the distinctively different Spirit R version with more aggressive aero. Your best bet is to tell us what cars you want to build, and the collective wisdom of the MC tribe will chime in on which kits/boxes to get, and which to avoid. Plus you might get a chorus of “Buy the Aoshima/Tamiya kit instead”… best, M.
-
Quick test fit with the wheels: Well, they certainly fill the arches. Arguably a bit too much, but I think that might be the price for using the Fujimi wheels, which are probably "inch-up", on the Tamiya kit. best, M.
-
The suspension is finished. Like the rear, the front assembly is primarily two big parts, a main frame with upper wishbones and the lower frame. Very nicely detailed and molded, though. Engine in place for a test. It looks reasonable through the mesh, but I think I'll add a few wires and hoses to busy up the space at the left between the heads and the airbox/fluid reservoir parts. Now I need to make some progress on the body. best, M.
-
What is your favorite sports car?
Matt Bacon replied to WillyBilly's topic in General Automotive Talk (Trucks and Cars)
I had the good luck to drive one at a nearby museum’s “Drive Dad’s Car” experiences. Getting in and settling down feels like climbing into the cockpit of a WW2 fighter and strapping it on… it’s so compact. Your feet are way out against the footwell wall because of the huge transmission tunnel. But get it going… that smell is so evocative. Leather, old rubber, fuel. It took me straight back to Air Cadet days flying a 1950s era Chipmunk. I loved it, but I can now imagine just how much hard work it must have taken to wrestle and pilot one non stop Rome-Liege-Rome at ten-tenths. Those folks had real cojones. Or in Pat Moss’s case, didn’t… best, M. -
What is your favorite sports car?
Matt Bacon replied to WillyBilly's topic in General Automotive Talk (Trucks and Cars)
You're making that one up.... best, M. -
What is your favorite sports car?
Matt Bacon replied to WillyBilly's topic in General Automotive Talk (Trucks and Cars)
In increasing order of the likelihood of actually owning one: a 911 Reimagined by Singer, a Cayman GT4, an Alpine A110, a Lotus Elan, a regular Cayman, an Aston Martin DB7, a Jaguar XKR and an MX-5... best, M. -
Sounds like it could be Model Factory Hiro… they started in 1989. best, M.
-
It was too hot to hit the bench early last week, and work got in the way the second half, but things are moving again now... Again, very typical Tamiya... that perfectly-fitting lower subframe with wishbones and control arms is one crisply molded piece with slightly complex painting instructions... The back end looks properly busy, though. "Kevlar" backed seats. You're probably thinking "they look pretty crude..." ...but given that this is what you can see (BEFORE the body goes on), perhaps I might be excused..? 😜 best, M.
-
Sadly, I don’t… best, M.
-
Sections 1 and 2 of the instructions completed! The engine is very typical Tamiya: only 6 parts, but with very complex painting instructions, enhanced by the many detail photos of the real thing that are available online. Similarly, the exhaust is only three parts, but this time the "all-over chrome" painting directions are a bit simplistic, especially for an NSX-R... The single-piece chassis is also nicely detailed with a little careful painting. Quick mockup suggests it will fit together nicely. From the other side.... One of the reasons it's worth spending a bit of time on the engine. The NSX-R has a mesh panel over the engine, whereas the NSX has a solid trimmed "parcel shelf." On the left, the Fujimi part, trimmed and extended to match the size and shape of the Tamiya part on the right. This should mean that the engine is visible even with cover closed, but also the Tamiya rear window is hinged and can open, so it's possible to expose the engine to full view... best, M.
-
Now, this is scary...
Matt Bacon replied to Matt Bacon's topic in General Automotive Talk (Trucks and Cars)
As someone who's building the earlier kit now, I _think_ from time to time it is confusing the "new NSX" kit with the old one, but without some pretty specialist hands-on experience you wouldn't know...best, M. -
For various (professional) reasons, I've had a to do a bit of work with Claude the AI large language model today. Now, I'm very skeptical about LLMs generally, and also deeply unhappy about the way their training is plundering real actual creative people's efforts, to create a money-generating tool for billionaires... So this is just an experiment. What follows is what Claude produced when I asked for a build review of the early '90s Tamiya NSX kit (which I happen to be building right now, so I'm well-attuned to what you might or might not say about it....) ---------- Build Diary & Review: Tamiya 1/24 Honda NSX-R A Classic Kit That Still Delivers After Three Decades Kit: Tamiya 24100 Honda NSX-R Scale: 1/24 First Release: 1992 Review Sample: Re-release version Skill Level: Intermediate Estimated Build Time: 15-20 hours Introduction When Tamiya first released their 1/24 scale Honda NSX-R in 1992, the real car was making waves as Honda's answer to Ferrari and Porsche. Now, over thirty years later, this kit remains a testament to Tamiya's engineering excellence and attention to detail. As someone who's built dozens of automotive models, I was curious to see how this classic kit holds up against modern standards and whether it still deserves a place in today's model builder's collection. The NSX-R represents Honda at their absolute peak of engineering prowess – a naturally aspirated V6 VTEC masterpiece wrapped in aluminum bodywork that could embarrass supercars costing twice as much. Tamiya's interpretation of this iconic machine promised to capture that essence in 1/24 scale, complete with the car's distinctive pop-up headlights and clean, purposeful lines. First Impressions & Kit Contents Opening the familiar Tamiya box immediately reveals why this manufacturer has maintained such a stellar reputation. The parts are molded in a beautiful pearl white plastic that captures the NSX's signature Championship White perfectly. The plastic quality is exceptional – minimal flash, crisp detail lines, and that characteristic Tamiya "feel" that experienced builders will recognize instantly. The kit contains approximately 120 parts across six sprues, plus chrome-plated pieces, clear parts, rubber tires, and a comprehensive decal sheet. What immediately strikes you is the thoughtful engineering – parts are logically arranged and sized appropriately for hand assembly. Unlike some manufacturers who seem to split parts arbitrarily, every separation here serves a purpose, whether for assembly ease or detail enhancement. The instruction manual is typically excellent Tamiya fare – clear exploded diagrams, logical assembly sequence, and helpful notes about paint colors and assembly techniques. The color callouts reference both Tamiya and generic color standards, though I'd recommend sticking with Tamiya paints for the best color match. Assembly: Day One - Interior & Chassis I began with the interior, always a good starting point for automotive models as it sets the foundation for everything else. The NSX-R's cabin is beautifully detailed, with separate pieces for the seats, dashboard, center console, and door panels. The attention to detail here is remarkable – the bucket seats have proper bolster definition, the dashboard includes separate instrument clusters, and even the gear lever is a separate piece. One immediate challenge presents itself: the interior is molded in black plastic, but the real NSX-R featured extensive use of carbon fiber-look trim pieces. The kit provides decals for these areas, but they're quite extensive and require careful application. I chose to paint these sections with Tamiya X-18 Semi Gloss Black first, then apply the carbon fiber decals over the painted surface. This extra step provides much better adhesion and a more convincing finish. The pedal assembly deserves special mention – three separate pieces that perfectly capture the NSX's distinctive pedal layout. These tiny parts are almost too delicate, requiring careful handling and a steady hand during assembly. I used CA glue sparingly, as the fit is so precise that excess adhesive would easily ruin the detail. Builder's Tip: Test fit everything twice before gluing. Tamiya's engineering is so precise that if something doesn't fit perfectly, you're probably doing something wrong. Day Two - Engine Bay Detail The NSX's longitudinally-mounted V6 engine is one of the kit's highlights. Split into multiple sections – block, heads, intake manifold, and accessories – the engine builds into a convincing representation of Honda's legendary C30A unit. The level of detail is impressive for a kit of this vintage, with separate pieces for the throttle bodies, various covers, and even the engine mounts. However, this is where the kit's age begins to show slightly. While the basic architecture is correct, some of the finer engine bay details that we'd expect in a modern release are simplified or missing entirely. The wiring harnesses are represented by raised plastic detail rather than separate parts, and some of the smaller accessories are molded integrally with larger components. That said, what's here is beautifully executed. The engine block splits horizontally, allowing the builder to see into the V-formation – a nice touch that adds visual interest even though it won't be visible in the finished model. The exhaust headers are separate pieces that attach convincingly to the block, and the intake manifold features separate throttle body details. Painting the engine requires patience. I used a combination of Tamiya X-10 Gun Metal for the block, X-12 Gold Leaf for the heat shields, and various metallics for accessories. The key is building up the colors gradually and using washes to bring out the detail lines. Day Three - Body Preparation & Paint The NSX's body is molded as a single piece – a bold choice that eliminates panel line issues but requires careful preparation. The surface quality is exemplary, with minimal sanding required beyond basic cleanup of the attachment points. The distinctive character lines that define the NSX's profile are crisply molded and need only light sanding to perfect. However, the real test comes with the pop-up headlights. These iconic features can make or break the model's resemblance to the real car. Tamiya provides them as separate assemblies that can be positioned up or down. The mechanism isn't functional (this isn't a working model), but the choice allows builders to display the car in either configuration. I chose the "up" position as it's more distinctive and showcases one of the NSX's most memorable features. Surface preparation took considerable time. Even though the molding is excellent, achieving a show-quality finish requires progressive sanding with 600, 800, and 1200-grit papers, followed by polishing compound. This is especially critical when using light colors like the Championship White, as any imperfections will be glaringly obvious under the final clear coat. Critical Point: Don't rush the body preparation. The NSX's clean, simple lines mean there's nowhere to hide imperfections. Day Four - Paint Application For the main body color, I chose Tamiya TS-26 Pure White spray can, which provides an excellent color match for the NSX-R's Championship White. Application required three light coats, with light sanding between each coat using 2000-grit paper. The key to a professional finish is patience – rushing this stage will result in orange peel texture or worse. The window trim presented an interesting challenge. The real NSX features black rubber seals around all glass areas, but the kit molds these integrally with the clear parts. I masked these areas carefully and painted them with semi-gloss black, which provides a convincing representation of the rubber seals without the complexity of adding separate parts. The rear spoiler and side air intakes required special attention. These areas feature a textured surface on the real car, which Tamiya has represented through subtle surface texturing on the parts. I highlighted this with a slightly darker shade of white mixed with a tiny amount of gray, applied with a detail brush and immediately blended while wet. Days Five & Six - Final Assembly & Details With all major components painted and detailed, final assembly proceeded smoothly. This is where Tamiya's engineering excellence really shines – everything fits exactly as intended, with no forcing or modification required. The engine drops into the chassis perfectly, the interior assembly slides into place with satisfying precision, and the body fits over everything with minimal adjustment. The wheel and tire assembly deserves special mention. The wheels are beautifully detailed multi-piece affairs that capture the NSX-R's distinctive five-spoke design perfectly. The tires are proper rubber compounds that look and feel realistic. I chose to use the provided tire lettering decals, which add a nice touch of authenticity. The headlight units are perhaps the most critical detail for achieving realism. The clear parts are crystal clear with no distortion, and the internal reflector details are convincingly molded. I enhanced these with a touch of silver paint on the reflector areas and carefully masked the lens areas during painting. One area where the kit shows its age is in the final details. Modern kits often include photo-etched parts for items like grilles, badges, and trim pieces. This kit relies entirely on molded plastic and decals. While the results are good, they lack the ultimate refinement that PE parts can provide. This is a minor criticism, though – the overall effect is still highly convincing. Accuracy Assessment Comparing the finished model to reference photos of the real NSX-R reveals remarkable accuracy in the overall proportions and major design elements. The characteristic profile is spot-on, with the correct relationship between the greenhouse and body sides. The front overhang, wheelbase, and rear proportions all match the real car convincingly. Where the kit particularly excels is in capturing the NSX's distinctive details – the side air intakes are correctly sized and positioned, the rear deck spoiler has the proper profile, and the wheel arch flares are subtly but correctly represented. The pop-up headlights, when raised, provide the correct "surprised" expression that makes the NSX instantly recognizable. Some minor accuracy issues exist, primarily in areas where tooling limitations of the early 1990s show. The door handles are slightly oversized, some of the smaller trim pieces lack the refinement of the real car, and the exhaust outlets are somewhat simplified. However, these are minor nitpicks that don't detract from the overall impression. The interior accuracy is particularly impressive. The distinctive dashboard layout, with its sweep of controls toward the driver, is correctly represented. The seat bolstering, center console design, and even the placement of minor controls like the hazard switch are accurate to the real car. Build Quality & Engineering This kit showcases why Tamiya has maintained their reputation for over six decades. The engineering is logical and builder-friendly, with each assembly step building naturally on the previous one. Parts fit is exceptional throughout – I used minimal amounts of adhesive, relying mainly on the precision fit to hold assemblies together during test fitting. The instruction manual deserves special praise. The exploded diagrams are clear and unambiguous, with helpful notes about paint colors and assembly sequence. Unlike some manufacturers who seem to assume builders have telepathic abilities, Tamiya explains each step clearly and logically. One area where modern kits have surpassed this classic is in the use of alternative materials. Current high-end automotive kits often include photo-etched details, turned metal parts, and even fabric seat belts. This kit is entirely plastic and decals, which limits the ultimate level of detail possible. However, what's here is executed so well that you don't feel shortchanged. Final Assessment After completing this build, I'm struck by how well this thirty-year-old kit holds up against modern standards. While it may lack some of the ultra-fine details found in contemporary releases, the overall execution is still exemplary. The finished model captures the essence of the Honda NSX-R beautifully – the clean lines, purposeful stance, and distinctive character are all present and correct. This kit represents excellent value for money, particularly for intermediate builders looking to develop their skills. The parts quality and fit ensure a frustration-free build experience, while the level of detail provides plenty of opportunities for advanced techniques without being overwhelming. The resemblance to the real car is striking. Viewing the finished model from across the room, you'd be hard-pressed to identify it as a scale replica rather than a photograph of the real thing. The proportions are spot-on, the stance is correct, and the attention to signature details like the pop-up headlights and side intakes makes it instantly recognizable as an NSX. Pros: Exceptional parts fit and quality Accurate proportions and major details Builder-friendly engineering Excellent value for money Clear, comprehensive instructions Cons: Some simplified details show the kit's age Limited use of alternative materials Decals require careful application for best results Recommendation: Highly recommended for intermediate to advanced builders. This classic kit proves that good engineering and attention to detail never go out of style. While it may not have every bell and whistle of a modern release, it delivers where it matters most – an accurate, well-engineered representation of one of the greatest sports cars ever built. Rating: 8.5/10 The Tamiya Honda NSX-R remains a worthy addition to any automotive modeler's collection, proving that some classics never truly age. ___________ This what it produced first time through. I haven't edited the text, or asked it to refine any elements of the "review". Frankly, I'm a wee bit scared by how good it is... best, M.
-
Are you going to pop the engine into a Hasegawa Stratos? best, M.
- 38,736 replies
-
- johan
- glue bombs
-
(and 1 more)
Tagged with:
-
I've had a quick look, and I think it's rather more work than it seems at first glance, and the opportunities to mess it up are significant: you have to do 28 spokes exactly the same. Just filling the gap between the raised parts of each spoke will result in a very chunky appearance and an odd looking centre. What you really need to do is remove the raised ridges, which are actually made up of a V-shape which runs down one spoke and up the one next door, smooth the curve of the well around the centre cap, and readjust the part where each spoke meets the rim. If I had a spare set of wheels, I might give it a try, but since I don't, I've decided the balance between risk of stuffing the whole project and absolute accuracy comes down in favor of leaving them as they are! I'll have a look in some of my other 90s JDM kits and see if any have tuner rims that are closer, but if not I'll plough on with what I've got now. best, M.
-
You'll have to take my word for it, but the NSX paint is actually a deep bluish green with a fine pearl flake. I've been inspired by @galaxygs Tamiya GT3RS finished in a single color without carbon, which looks great, to get on with mine. This is not that color (his is a tasteful ice blue metallic). I'm sure this will elicit a love it or hate it reaction (unless _everyone_ but me hates it...), but the Porsche dealers opposite IKEA in Sheffield has got a 911 Carrera cabrio in this color, and in the flesh it's really striking and different: https://www.jct600.co.uk/new-cars/porsche-911-2dr-pdk-convertible-cartagena-yellow-metallic-automatic-petrol/id-12634/ It'll stand out in my display cabinet, that's for sure! best, M.
- 38,736 replies
-
- 2
-
-
- johan
- glue bombs
-
(and 1 more)
Tagged with:
-
Thanks, Rich... that color was what sealed the deal, so I have a bottle of color-matched Zero Paints Honda G70P on its way to me as I write... best, M.
-
I quite often find inspiration for what to pull out of the stash in the current edition of Octane, and this is the latest in a long-ish line. A pretty unusual NSX-R built to order for a wealthy expat Brit who worked in Japan at the time. It's the full NSX-R spec in a slightly stealth package with standard headlights, no extra scoops, a single color body and roof in a tasteful pearl Brooklands (aka Charlotte) Green, and the interior trimmed in black alcantara. The wheels are a bit more in your face, mind you... This is another Frankenbuild, but this time it's 90% Tamiya with just a few parts stolen from a Fujimi NSX-R kit that's gathering dust. I think the Tamiya is a much better and more detailed kit overall, so all I've stolen from the other box are the Recaro seats, gear shift lever and steering wheel, and the wheels. They aren't quite right, but they have seven thin spokes and look a lot more like the prototype than the ones in the Tamiya kit. I thought I might be able to find something closer, but 16" seven-spoke "Custom Order Programme Step Three" Enkeis don't seem to feature in any aftermarket wheelset I can find from the usual makers and vendors... So far, all I've done is the tedious process of converting Fujimi-fit wheels to Tamiya-fit spindles. The Tamiya body shell is lovely and clean, though, with no visible parting lines at all... best, M.
-
Farrari "Testa Rossa" head wrinkle paint help
Matt Bacon replied to BWDenver's topic in Model Building Questions and Answers
For the same reason we accept engraved panel lines and recessed “rivets” on model aircraft, and laud manufacturers who manage to reproduce “oil-canning” and lapped panels. It’s not about accurately reproducing the detail 24 (or 32 or 48 or 72 or 144) times smaller, because in most cases it would just not be there. It’s about providing the illusion or impression or effect of structure, detail, texture or material. In our world, ribbon doesn’t look like seat belt material, and flocking for sure doesn’t look like scale carpet. The crackle effect on full size heads scatters the light differently from a smooth painted piece, or a chrome plated piece. It may be that in real life, making it 25 times smaller would just result in something that looks like matt paint or frosted plastic, but just painting the heads matt doesn’t give that qualitative difference in what you perceive that a crackled finish does, even if it’s over scale… To my mind, it’s just about trying to achieve a variety of colours and finishes and texture to hint at the complexity there is in the real thing, so your eye and brain fill in the details. best, M. -
Farrari "Testa Rossa" head wrinkle paint help
Matt Bacon replied to BWDenver's topic in Model Building Questions and Answers
Plasti-kote does "Velvet" or "Suede" textured paint which I use straight onto the plastic (keep the coat light), and follow up with Tamiya Fine Surface Primer before applying the final color. Or if you're feeling brave, paint the heads using enamel paint, let it dry and then apply a VERY light coat of "hot' acrylic clear varnish which should crackle the enamel. Practice this first on some scrap before applying it to your model parts... best, M. -
1/20th Revell Fendt 728 Vario Gen7
Matt Bacon replied to Luc Janssens's topic in Truck Kit News & Reviews
https://revell.de/en/shop/product/078279090-fendt-728-vario-tractor-easy-click?srsltid=AfmBOoqw5pRjM3bBBjGFSwca08jrlJWsyu2VPAG82kCq50juoGnvdMku All the dimensions in the main page above scale out within a reasonable margin of error to 1/24 of the real thing: "With a final size of 235 mm in length, 110 mm in width and 137 mm in height, you will experience the engineering of the original on a scale of 1:24." The kit dimensions on the right (different from the body copy) are roughly 1:20, but the scale in the same panel shows 1/24 I guess we just have to wait and see whether the one the German reviewer has hold of is actually the same thing as the commercial public release under the Revell brand. It wouldn't be the first time a model manufacturer has produced a promo for a company distinct from the widely available retail version for the public. It would be really odd to suddenly make one tractor in the whole series a different scale from the rest of the range... wouldn't it? Especially if you have been telling your retailers and customers something different for months... best, M. -
1/20th Revell Fendt 728 Vario Gen7
Matt Bacon replied to Luc Janssens's topic in Truck Kit News & Reviews
Well, the last picture of the tractor also shows both a box corner and a product label clearly saying "1:24", so I don't think much German is required... This is intended to sit alongside the existing Porsche and Deutz tractors, both of which are 1/24. I just wish they'd add one of the classic Lamborghini tractors to the range (not the modern one Clarkson bought which looks like every other modern tractor...) best, M.