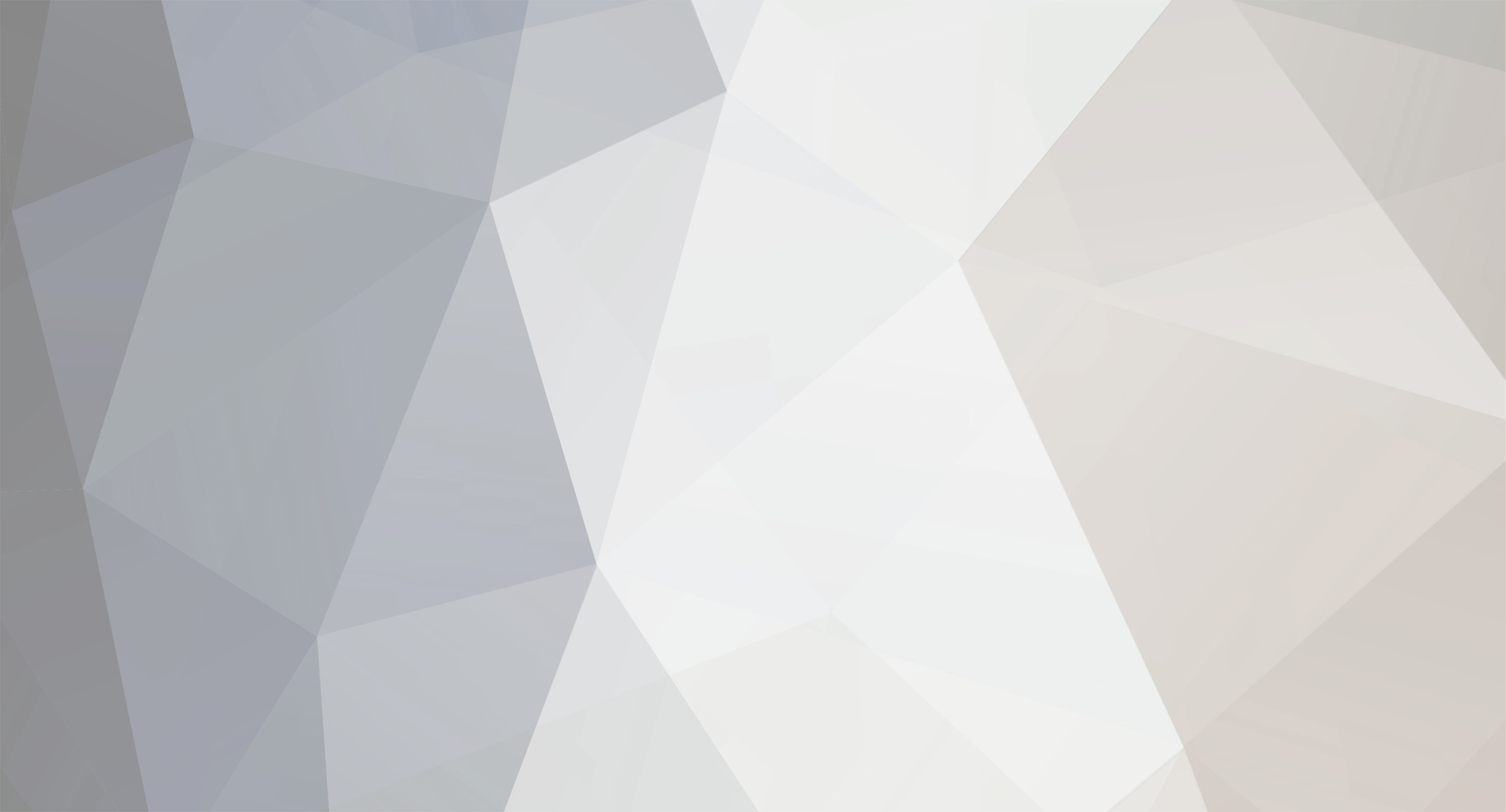
Matt Bacon
Members-
Posts
3,158 -
Joined
-
Last visited
Content Type
Profiles
Forums
Events
Gallery
Everything posted by Matt Bacon
-
Source for white metal requested
Matt Bacon replied to fcriscuo's topic in Model Building Questions and Answers
Well, it's described as low temperature soldering. This is the tutorial I found: I just use my regular soldering iron at its standard temperature, and if you look at the pictures in the thread I linked to above, you can see that the join completely disappears when you use low temperature solder on white metal parts -- the two pieces become one, essentially. So I'm going to say if it's not exactly the same composition, then low temp solder and casting white metal are very, very similar. On the "melting" part, you never touch the white metal parts directly with the soldering iron, and you don't hold the iron in place with the liquid solder on the tip touching the white metal parts either. Not to get too "physics" about it, but there's a certain amount of heat energy in your blob of molten solder, which is enough to keep it liquid. When you touch the blob onto the two parts, it runs along the seams. If the soldering iron is no longer touching anything, all the heat energy you have got is in that small amount of molten solder. As it runs along the joint, it cools as the heat energy goes into the bulk white metal (which is a good conductor of heat) on each side of the joint, and the heat is dissipated into a much larger amount of room temperature white metal. There isn't enough energy to melt any more metal, just warm it up a bit. In practice, all the soldering I did (a bit at a time) to join the top and bottom shells of a 1/24 race car made it noticeably warm to the touch, but not hot. With a bit of practice, and keeping the iron moving, you can "stroke" the solder along the join, just melting it under the tip and letting the capillary action take it further and further. You have to be careful with small parts, where there's not enough material to dissipate the heat of the molten solder, so I still use epoxy or superglue for those. But for joining major parts low melt solder is great. And if you have to repair broken white metal (which is not as flexible and easy to just to bend as you might think) it means you get an invisible repair that's as strong as the original material instead of having to mess around with pins and epoxy... best, M. -
Source for white metal requested
Matt Bacon replied to fcriscuo's topic in Model Building Questions and Answers
Welcome to the club! First of all, you need to know that you don’t solder white metal kits like you’d solder electrical components or brass. You need “low temperature solder” (which is basically the same stuff as white metal itself). And instead of heating the parts you are soldering with the iron and touching the solder to the hot parts, you melt the low temperature solder on the iron and let it flow onto the cold parts you are joining and into the gap between them by capillary action. So you need to be able to hold the parts you are joining together as you want them to be when joined. Use clamps or tape, and do the bits that are exposed, then move the tape and do the other bits. The solder sets really fast. You can probably source some old gaming figures or model soldiers to practice on if you want, but when I took the plunge with the white metal Finecast kits I have been building I just went ahead and did it, after watching a couple of videos online. Google “low temperature soldering” to find them. Any questions, just ask… best, M. -
1931 Cadillac V16 Convertible Coupe, Jo-Han, 1/25
Matt Bacon replied to Matt Bacon's topic in WIP: Model Cars
Yes... I didn't realise until I started reading the instructions carefully, but the original owner had put together the ladder frame sides, under engine floor and a couple of the transverse frames before I got it. Again, although there are some sink marks in the frame sides, they are both as straight as a die and the cross-pieces fit perfectly between them and lock into position. best, M. -
1931 Cadillac V16 Convertible Coupe, Jo-Han, 1/25
Matt Bacon replied to Matt Bacon's topic in WIP: Model Cars
Starting to make some progress... The engine stripped of chrome and repainted. Given the brittleness of the plastic, I didn't try to disassemble it any further and contented myself with repainting. Look closely, and you can see (and read) the "Delco" badge on the water pump bottom right. I "wired" the distributor using thread, smoothed with PVA glue, making up two eight-strand skeins which are fixed into slots cut in the distributor cap. I wouldn't try and use it if the wires had to be routed visibly to each cylinder but as it is the fabric-covered wires just have to disappear into the front of the cylinder head. In case you're wondering how big this engine is (and it's a monster) here it is in comparison to a 1/24 427 V8 from a Monogram Cobra that I had lying around. The main elements of the chassis. I've added the exterior brake drums,, held on by the green pins so they rotate. The white-ish patches on the frame rails are the sink marks I mentioned, filled using superglue and microballoons. Quick test of the engine in the chassis. You can see why the car has such a long nose. An example of that ambition and attention to detail I mentioned above. This is the steering actuator lever. If you look closely you can see that the hole in the chassis is extended vertically by a slot, and there are two tiny pins moulded on the axle of the lever. This means that the lever can be inserted through the chassis with the lever lying along the chassis rail, and then rotated to its correct vertical orientation where it is retained in the hole by the pins which are now behind the chassis. I've never seen that done before. That gives plenty of wiggle room for clipping together the steering mechanism. The suspension is very nicely detailed with the shock absorber dampers and arms applied separately. And the steering works prototypically. The rear suspension is equally well detailed: note the hex nuts on the differential and brake actuator rods as well as separate damper arms. Here's the completely assembled chassis. I'm going to paint it as one piece because it is all black, and given the plastic's general resistance to glue I wanted to be sure I was always gluing plastic directly to plastic and using hot MEK liquid cement wherever possible. The engine fits perfectly on its mounts and to the prop shaft. Now to pop it out and paint the chassis and powertrain. And make some decisions about what color the car is going to be! best, M. -
Get some black drafting/technical pen ink. Rotring pretty much owns the market this side of the pond, not sure if the same is true in the US, but someone will still make it. Very dense black but with very fine pigment. Add it a drop or two at a time until you get the density you want (though bear in mind it’ll get a bit darker as it dries…) best, M.
-
1931 Cadillac V16 Convertible Coupe, Jo-Han, 1/25
Matt Bacon replied to Matt Bacon's topic in WIP: Model Cars
Not much to show yet, but things I have learned. 1) The styrene in this older boxing is really hard, and brittle, which I guess is the price you pay for the sharpness of detail and the lack of flash. 2) There are serious sink marks in many of the thicker parts (see above) 3) They thought very hard about how to mold it so you can build without paint. Unfortunately, not all "silver" parts are "chrome", and not all "body color" parts are the same green, even if your basic body color is green. This also means the paint call-outs are very limited: the section in the instructions only mentions things that you can't in all conscience leave the color they are molded. 4) On the plus side, I was very pleased to read that the designers of the Chevy V16 made it very "neat" with all the plumbing and wiring hidden. In practice, this means that the 16 spark plug wires from the distributor come out one side and disappear down around its base rather than having to be led to each cylinder in both blocks. Go Chevrolet. 5) It's designed beyond the limits of early-60s injection molding technology. For example, there are a couple of parts that are intended to be the folded "irons" for the fabric roof. They are slim, accurate, beautiful... and distorted and broken. I think even Meng with 2020s slide molding tech and using ABS instead of polystyrene would have struggled to make them work. But someone mastered them and they tried, so well done. 6) I genuinely don't think I've ever come across a "classic" kit so completely uncompromising in its ambition to get everything right, so of its time, and so close to succeeding, with the possible exception of some of Heller's greatest hits from the late 60s and early 70s. (And by that I also mean never taking the "easy to assemble/foolproof/fun to build" design solution if accuracy is on the line...) best, M. -
Amerang is just a UK distributor of other people’s kits. In the 70s snd 80s, before the Japanese brands were well known here, distributors like Amerang, AA Hales and RiKo (Richard Kohnstam) used to put stickers on or even brand boxes from Bandai, Gunze, Tamiya and Hasegawa. best, M.
-
And now, as they used to say, for something completely different... Clearly my subconscious had been working on what I should build after the RX-7 kitbash, because this came to me in a dream, literally. More accurately, maybe because I'd been reading some vintage modelling magazines, I woke up knowing I should build one of the Jo-Han oldies in my stash, or one of the Monogram 1/24 "The Classic...." series. After weighing up this one, the Jo-Han Carraciola Mercedes 500K, and the Monogram Duesenberg, I plumped for this. It couldn't be further from a JDM rotary of the early 2000s... I've never built a Jo-Han kit before, but opening the box everything I've heard about these (compared to their annuals) is borne out, even though it had been slightly started by the previous owner. The detail is astonishing for any vintage, never mind the late 60s, and the way the parts trees lock together to protect everything in the box is genius. The instructions are properly old school, like vintage Heller, where you have to read the words three times and trial assemble everything before committing to glue. I've stripped all the chrome (mostly the trees at the bottom right of the picture) and will repaint the bits that need it. This is a first-release boxing (the later re-release has a largely white box) and the whole kit, including the chromed tree, is 99% flash-free. The engine had been mostly assembled (albeit with chromed parts) and the front axle had been part built, but that's as far as it went. I'm not sure why the previous builder had stopped... nothing seems to be FUBARed and all the parts are there. Anyway, their loss is my gain. So, just a straightforward build of a regular (and rather nice-looking albeit classic) kit according to the instructions. What could possibly go wrong? best, M.
-
Now, you may be wondering "Why Tamiyujimi?" Well, I saw this ad on an auction site: And not having the requisite £80,000 spare, I decided to build one. Shouldn't be too difficult, surely? Fujimi makes a kit of this very car, the FD3S RX-7 Spirit R Type A. But... the body in the box doesn't have the unique nosecone or aggressive splitter. And a fellow Britmodeller pointed out some time ago that the chassis in the kit is actually from an R-32 GTR, not an accurate RX-7 chassis, and the brakes are far too far inboard. So I resolved to use the chassis from a spare Tamiya RX-7R1 (an earlier vintage FD-3S) mated with the much-modified Fujimi body and essential Spirit R parts like the unique wheels and Kevlar-backed Recaro seats. And this is the result: Paint is a Zero Paints Gunmetal intended for a R35 GT-R that I had to hand, with Zero 2K clear coat. The tires are Michelin Pilot Sports that I found in the spares box, because I wanted something a little less "rubber band" than the ones that came in the kit, and I wanted them to fit the wheels without stretching (I have a couple of nice models in the cabinet whose tires have started to crack as they've aged because they were stretched over a 1" bigger wheel than they were made for...). The track is just slightly too wide front and back, which is a consequence of the chassis swap and Tamiya's way of molding the suspension with a small number of large and complex parts including wishbones, links etc in one piece, which makes it much more difficult to take a couple of mm out of each side... There is an engine in there as well, but with the amount of work the body needed already, I wasn't going to open the hood and build hinges! But I now have my very own Spirit R Type A... best, M.
-
Mazda RX-7 Spirit R Type A, Tamiyujimi, 1/24
Matt Bacon replied to Matt Bacon's topic in WIP: Model Cars
Suspension and chassis coming together: Very much in the classic Tamiya mold of a small number of large and complex parts requiring detail painting rather than many separate, this rear suspension is made up of a top frame, one-piece differential with drive shafts, two wheel carriers, two brake disks and a one-piece lower frame with integrated suspension arms and underbody panels. There are just 16 molded parts visible in the picture above (and four polycaps hidden in the wheel hubs). I think they do a pretty convincing job of representing the suspension and drivetrain (and certainly better than using the chassis from an R32 GT-R...) I'm calling it a day in this thread... I have battled to the end, but was utterly useless at documenting the process. It was "just" fitting the body to the chassis, adding the wheels and few more details, and decalling. But it was kinda frustrating and way more difficult than it should have been (which is mostly my fault...). Anyway, see you over in Under Glass... best, M. -
Mazda RX-7 Spirit R Type A, Tamiyujimi, 1/24
Matt Bacon replied to Matt Bacon's topic in WIP: Model Cars
...and the engine bay and the interior, of course... You can see a faint "crocodile skin" texture on the one piece airbox/ducting part at the front of the bay. I have no idea what happened there -- my trusty can of Citadel Chaos Black primer/base went on too thick and "curdled" into clumps, and the lines where it didn't cover ended up etched by, I assume, neat solvent. I dumped it straight into IPA, but the damaged had already been done. The IPA removed all the paint overnight, but left the ghost texture behind. If it was ever going to be seen again, I'd have had to do more about it, but as things are in this basically curbside model, I'm just going to chalk it up to a "learning experience". The interior is pretty simple, but the decals add some nice details and further splash of colour. Note to self... brush off that dusty fingermark on the dash top... best, M. -
A Starship still flying would be really rare groove, however cool… It’s a bit hard to figure out from the published stats, but there are maybe two in the US and one in Europe still extant. When Beech washed their hands of them, it became really hard to keep one in the air. Another possibility is a Diamond: https://www.diamondaircraft.com/en/private-owners/aircraft/da42/overview/ Best, M.
-
That looks absolutely beautiful. Great job. best, M.
-
Mazda RX-7 Spirit R Type A, Tamiyujimi, 1/24
Matt Bacon replied to Matt Bacon's topic in WIP: Model Cars
If you're thinking "This is taking a while," so am I... On the plus side, I have now completed Stage Two of the instructions... One of the standout features of the Spirit R is carbon/Kevlar-shelled Recaro race seats... a must-do highlight in an otherwise grey and black cabin. These are mostly Tamiya Flat red, and yellow oversprayed with black through a handy piece of gauze for the backs. In reality they are a bit more muted, but in the gloom of that dark cabin, I think they'll be fine. I'm not sure why I'm spending time on the engine, other than "Because it's there." I'm not planning to open the hood in the Fujimi body shell, and I'm certainly not building hinges for it like I did for the Super Samuri. But Tamiya moulded it, so I guess I'd better color it in a bit... Terrible picture, but the blacked out tail light bar is now in position. Hard to tell from this angle, but the outer lens is the orange indicator, and the inner pair are red tail and brake lights. The glass is temporarily tacked in place, and needs a darn good clean before it's fixed. I mostly wanted to check that the tub would fit under it, and it would all close up with the engine in place. Which it mostly does, though I may need to glue the splitter under the nose to make it stay where it should. And though I might moan about them when they are provided, I really could have done with some masks or templates for the black areas around the window borders, even though they are frosted on the plastic molding... Just the suspension, wheels and stance now, then... best, M. -
There seem to be quite a few warped, broken or short shot parts in these, as well… best, M.
-
Zero Paints Primer - what am I doing wrong?
Matt Bacon replied to YellowHound's topic in Model Building Questions and Answers
I understand the concern, but I’ve used the Zero system without sanding on dozens of models over the last two decades without any issues no matter what the colour or finish. In my experience, the biggest challenge is with two (or in one case three: solid base colour, tinted metallic, and transparent topcoat) layer basecoats: getting each layer evenly dense across multiple part assemblies. For example when I’m painting doors, engine cover, opening clips and pop up lights separately before final assembly. But I’ve always found the Zero system just works when I do exactly what the instructions say. It’s not for everyone, because of the noxious chemicals, extensive precautions, and the kit you need to use it safely (I wouldn’t be using it if my modelling den was in the house, for example…) But for modern cars and colour matched finishes, it’s hard to beat… especially if you’re in the UK and the alternatives come from overseas with the additional shipping cost and difficulty that brings. best, M. -
Whatever they are, their drivers seem pretty accident-prone… 😜 best, M.
-
What did you see on the road today?
Matt Bacon replied to Harry P.'s topic in General Automotive Talk (Trucks and Cars)
I guess that means that there are now Charger chargers… M. -
Zero Paints Primer - what am I doing wrong?
Matt Bacon replied to YellowHound's topic in Model Building Questions and Answers
You shouldn’t sand the base colour coat, unless you’re knocking off a small speck of crud or fibre. It’s meant to lay down slightly rough (like 400 grit sandpaper). Repeated light coats are the way to go… if the base colour ever looks wet on the model you’ve laid it on too heavy. I use both Tamiya Fine Surface primer and Stynylrez under Zero Paints with no issues. best, M. -
Mazda RX-7 Spirit R Type A, Tamiyujimi, 1/24
Matt Bacon replied to Matt Bacon's topic in WIP: Model Cars
And the clear coat is on: This is Zero Paints 2K Diamond straight out of the brush, without any sanding or polishing. There are a couple of dust specs to be dealt with, but overall I'm very happy with how it turned out. The wing was prepainted to the base coat stage before fixing in position, to make sure the coverage under it was complete and even. best, M. -
Mazda RX-7 Spirit R Type A, Tamiyujimi, 1/24
Matt Bacon replied to Matt Bacon's topic in WIP: Model Cars
I looked at the pictures I'd posted of the real thing above, and you know what? I spotted that the splitter needed a bit more upfront airfoil. And I couldn't unsee it. So after gluing on a plastic card extension, some filler, a bit more of the superglue and glass microballoons, I got to somewhere I'm happier with... The body is painted with a Zero Paints "Nissan Gunmetal KAD", intended for an R35 GT-R, but it's the closest I have in the paint locker to the Mazda RX-7 Titanium Grey Metallic special colour for the Spirit Type R. I mean, how many shades of grey can there be? 50? 😜 And yes, it does look rough... that's what Zero base colours are meant to look like before the clear coat goes on... best, M. -
I saw this JDM exotic on a Pistonheads auction, and decided I'd really like one on my shelves: Ah, great, thinks I, Fujimi do a kit of exactly what I want: Except, despite the box art, not exactly. The Spirit R Type A kit has the wing, the special red Recaro seats, and the right wheels. What they haven't done, though, is change the nose of the standard kit. So instead of the separate aero splitter and subtle fairings in front of the wheel arches as depicted on the box art, there's just a blunt air dam that goes all the way around the lower nose. Bother. What to do? As it happens, I had a spare cheap-as-chips Tamiya RX-7R1, the 1992 top of the line sports model of this generation (FD3S). It has a more aggressive front splitter, as well as a much more accurate chassis and I'm hoping better dimensioned suspension than the Fujimi kit. So this "quick build" has become a FrankenSpirit, combining the Tamiya running gear and chassis (and full engine) with the later-model Fujimi body and Spirit R details. Fortunately, the Fujimi and Tamiya bodies and chassis are very close dimensionally, which is not always the case with Fujimi kits. First job, as you can see, was to remove most of the air dam from the Fujimi body. Then many rounds of fettling, building up, filling and fine tuning have got me to this point: It's not perfect, but I think it looks a lot more like the real thing now! And finally, I think I can actually start building the rest of the model... best, M.
-
I think this is he: https://www.writermag.com/improve-your-writing/poetry/virgil-suarez-reinventing-a-writer/ I didn't know any of the poet and writer part, but his Instagram handle is "Dr Cranky", and in the interview (from last year), he says: "I have plenty of hobbies. I build models (cars, mostly), and in the last decade I’ve started to build guitars. I love building things, so I figure I would’ve ended up having my own shop. What am I talking about? I have my own shop. I build things. When I’m not writing, I’m building things or making art or taking photographs. These are my passions." He goes on to say he's working on a couple of film projects and that he's "had to learn many software programmes in order to be able to shoot and edit." So I guess he's been busy with poetry and movies and teaching and hot rod modelling has taken a back seat. best, M.
-
I think they built about 120 all told. But the concept of two kinds of tanks — heavyweight mobile guns and fast, lighter “cavalry” was becoming obsolete. The Conqueror was supposed to partner with the Centurion, but the latter could do everything that was needed, especially in the later versions, so the Conqueror became obsolete. The Chieftain was explicitly designed to replace both, and the “Main Battle Tank” was invented… best, M.