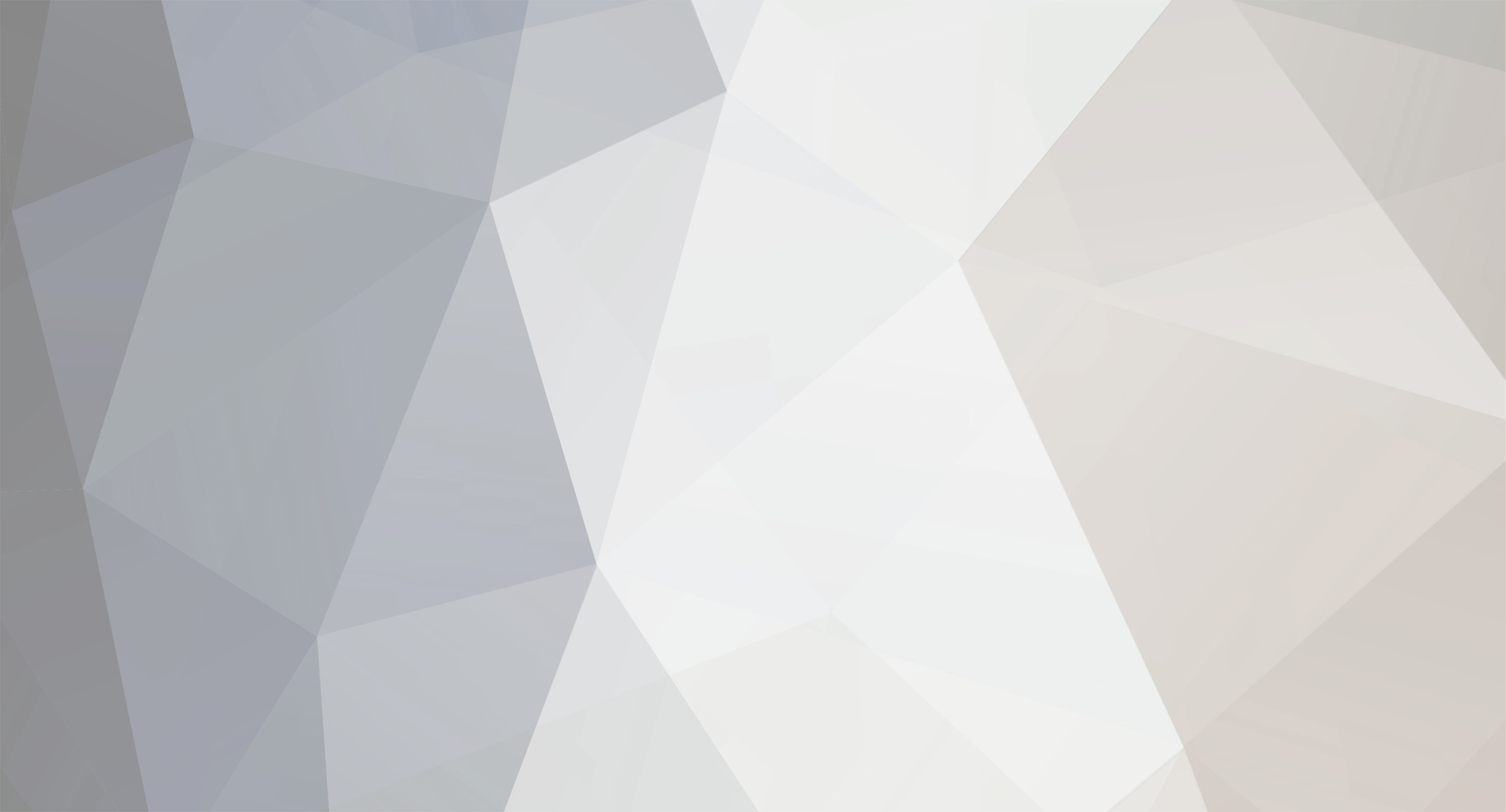
Mr. Metallic
Members-
Posts
2,727 -
Joined
-
Last visited
Content Type
Profiles
Forums
Events
Gallery
Everything posted by Mr. Metallic
-
The body was only tooled up in the 90's, so it surprises me that the mold has deteriorated that much. The rest of the kit is the 55 Nomad tooled in the 60's, so you're correct that some of the kit is old. Just thinking about it now though, i guess the 90's are 30 years ago, so could be considered old ?
-
Those are a great looking wheel. Glad i finally have a name to go with the ones on my Son of Ford build. But these AMT ones are cool because they have a bit more detail on the rim and are a different offset than the Monogram parts.
-
I don't believe I've ever seen those 4 spoke Rader ribbed wheels before. Wild
-
"Simple" Revell 30 Model A Coupe. finished 4/11/2022
Mr. Metallic replied to Mr. Metallic's topic in WIP: Model Cars
YESSSS!!!! This is exactly why I've tried to be as descriptive as possible in this WIP. I've been helped along the way by so many builders over the years that I wanted to try to do help someone else. Seeing someone actually use what I described is very rewarding. glad it worked out for you, they look great! BTW, didn't know they ever offered the 41 Lincoln in blue. i may have to seek out that version if I ever decide to build a box stock Lincoln. They are a beautiful car -
What Putty or Fillers to Use
Mr. Metallic replied to Chevy II's topic in Model Building Questions and Answers
I use 2 different items depending on the application. Tamiya for fine finish work right before paint, and very minor imperfections caused by sanding. i always wait at least overnight before sanding Tamiya filler to allow for any shrinking and a full cure. For everything else, especially heavy customization I use Dolphin Glaze (I know, weird name) It is also an automotive grade 2 part filler, and sands at the same rate as the surrounding plastic. I've been using it for quite a few years now, with no apparent issues showing up on long completed projects. It comes in a pouch, instead of a can like many other auto grade catalyzed fillers, so it lasts a long time because it's not exposed to air within the can. -
Convert AMT 65 Riviera to convertible
Mr. Metallic replied to BadJuju's topic in Model Building Questions and Answers
Ha, I did try his top chop, and now I'm thinking of turning it into a roadster. It has nothing to do with Tim's method, just my rushed execution. -
Halibrand Quick Change
Mr. Metallic replied to spike morelli's topic in Model Building Questions and Answers
@Spex84 recently started offering one in his Shapeway store for anyone that's looking for one. He even designed a crossmember to go with it that is designed to drop into the new Revell Model A coupe or roadster kits -
Question about an AMT single axle trailer
Mr. Metallic replied to VW93's topic in Model Building Questions and Answers
I could use them since Mr. Geiger passed on them? -
Very nicely done. You nailed the paint job. I received a set of the Mako specific parts from my good friend Chuck, and will combine that with the Enforcer version of this tooling to build mine.
-
"Simple" Revell 30 Model A Coupe. finished 4/11/2022
Mr. Metallic replied to Mr. Metallic's topic in WIP: Model Cars
Get your motor running... Lets turn our attention to the engine. As much as it may pain some (especially Mr. Tim Boyd) I'm keeping the Chevy small block (SBC) in this one, for the sake of simplicity. Remember, that's how this whole project started, right? However, I'm going to do my best to backdate the SBC with traditional speed equipment. Let's get started. The headers that come in the kit are really nicely molded, with an open end which is quite a feat executed by Revell using the sliding mold technology. I just don't care for the shape of the bent tube exit. This is just my personal preference, so feel free to skip this step. First I trimmed the end off, sanded the flange flat, and then drilled a pilot hole in the center of the flange with a #70 drill bit. Then I progressed up though several sizes of drill bits, until the diameter of the hole is just slightly smaller than the diameter of the exhaust tube on the other side of the flange, taking care not to dill though the other side. Next we're going to pin the exhaust headers to the block to ease installation during final assembly. By now you know the drill, pun intended. Drill a hole through the flange that butts against the engine block into one of the exhaust pipes, Which ones you choose is up to you, but if you make your choices different on the left and right headers it will help you from accidently installing the wrong header on the wrong side of the engine. Drill gently and straight because those tubes are small. You don't have to go very deep, maybe 1mm, just enough to anchor the pin. Glue your pin in place, let glue dry, and then use the pin and ink method to mark your new hole location on the block. This method leaves no doubt that your header is in the right place and has a solid mount. Rather than the nicely done supercharged or 3 carb setups that come in the Revell kit I'm going to use the classic 6 carb intake that comes in the long running Revell Tweedy Pie kit (or any of it's variants issued over the last 50+ years). If you choose this setup you can use the carbs that Revell includes which are fine, but I had already stolen those carbs for a different project from my parts kit, so I chose to gather up 6 carbs from the Nailhead equipped versions of the modern Revell Model a kits. Trim the molded in mounting pins off the carbs and replace with metal pins. You can also take a moment and drill a hole in the side of the carb for eventual installation of a fuel line. Be sure to clean up the mold lines on the carbs too. At the top of the pic you can see the scoops I've chosen to use as well. these are 3D printed Cal Custom scoops from Maple Leaf Modelworks shop on Shapeways, which I also drilled a hole in the bottom to set atop the carbs during final assembly. This little scoops are beautiful, and feature an open mouth for added detail. @Spex84Once painted inside and chromed outside they're really going to pop. The Tweedy Pie intake drops right on the SBC block. I took the time to nip off the tall mounting point for the coolant hose at the front of the intake and drill it to accept a pin. I'll be using the beautifully done pre-wired distributor from Morgan Automotive Details on this build. Enlarge the hole for the kit supplied distributor to accept the MAD dizzy, and then place the intake on the block. Once you get the intake where you want it continue drilling that hole into the top of the block, that way you use the base of the distributor as the locating pin for the intake to the block. You can also drill holes into the center of all 6 of the inlet ports for the carbs on the top of the intake. Again, align the intake on the block and continue drilling those holes through the intake ports into the top of the block. Now it's ready to accept all 6 of your carbs. Finally it's time for a mockup. The only other mods I'll be making are using the stock style oil pan from the Tweedy Pie to replace the billet style kit supplied oil pan, and swapping the kit alternator for the short generator from the Tweedy Pie as well. It needs to be a short generator in order to use the kit supplied fan belt and water pump with molded in bracket for the generator, or else it will hit the front of the cylinder head. I also chopped off the automatic transmission to replace it with a manual transmission designed specifically for this block from Replicas and Miniatures of Md. A real hot rod has to have four pedals, right? Now, lets take a look at where we've landed with our alterations. -
Nice clean build of what can be a tough kit. Revell tried to provide max detail at the time, but made it tricky to get clean results sometimes. You nailed it.
-
Pro touring 70 1/2 Camaro (Dutchboys 2015 SEMA tribute)
Mr. Metallic replied to Steve H's topic in Model Cars
This thing came out so nice. It's a study in beautifully aggressive styling. You really did a great job. -
"Simple" Revell 30 Model A Coupe. finished 4/11/2022
Mr. Metallic replied to Mr. Metallic's topic in WIP: Model Cars
Body, louvers and a grille- It's time to pay some attention to the body. Revell's kit features a mildly chopped body. If you noticed in the mock ups I've decided to go a bit lower, using the further chopped roof from Altered States. I actually did the master for this chopped top 5-6 years ago when the first version of this kit came out. I also mastered an un-chopped body for it. Sadly, the owner of Altered States has been having health issues and has stopped casting. However, the changes I'm making to this top also apply to the top from the kit. The roof insert Revell decided to put in the kit is kind of a rare bird, not often seen on 1:1 Model A's, whether stock or hot rodded. The roof insert on the stock 1:1 30 Coupe bodies extends forward of what Revell created, all the way to the visor. Modifying the kit roof just requires a little time and some plastic. Lets give it a shot. First, take the kit supplied roof insert and lay it on top of a piece of sheet plastic. I used .020 Evergreen sheet. Use the straight factory edge of the plastic sheet to your advantage to create the squared off front edge of the stock roof insert by setting the kit insert back about 3mm from the edge. The distance is not critical, but leave it a little longer to allow you some excess to trim for exact fit. Trace the kit insert onto the sheet, but as you trace down the sides instead of following the curve around the front keep extending that line forward to the edge of the sheet (as seen here) Cut out the new top, keeping in mind that the piece you traced will be slightly larger than the original. You can compensate for that by cutting just inside the line, or cutting the line itself and then finessing the size with sanding sticks. Make the piece so it fits the existing hole in the roof, except for the front edge which we still need to cut out of the body. Once you are happy with the fit of your new part lay it on top of the roof to use as a template for modifying the opening in the roof. Trace around the front of your new piece. Then remove your roof insert and you'll see what material you need to remove. Remember, cut inside the line and then finesse with sanding sticks. While you're doing that go ahead and remove all the areas marked with red, which includes the lip detail around the inside since we will have to replace it. Leave the rear part of the lip for now to keep your insert from constantly falling through the hole as you do your multiple sand/fit/repeat trial fittings. If you are going to permanently attach your insert you don't need to remove the inner lip. Once you are happy with the new opening you have created give the new insert one last fit before you remove that rear lip. You can bend and tweak the contour of your insert to match the profile of the roof. Once you are happy with the fit you can add a bead detail around your roof insert with plastic strip, I used .020 x .020, one long piece for the sides/back. When you cut the piece for back/sides make sure you leave it long to allow for trimming at the front edge. Start applying the strip a little at a time along the rear edge and be sure to keep the strip straight and follow the edge of the insert. Work carefully around the corners and down the sides. A trick is to pre-bend the corner areas a bit by pulling the strip between your fingers with light pressure to introduce a curve to the strip. Once all the glue has dried, trim the ends of the strip flush with the front end, and then use a new piece across the front To give the insert a place to rest take strips of .030 x .100 strip and attach it to the underside of the roof to create a new lip. If you like you can omit the lip at the front edge because there is not a lot of space on the underside if the roof near the visor. Once that is done set your new insert in the roof and admire the results. Here's an technique I've been wanting to try for awhile, now seems like the perfect time. Archer makes some pretty cool detailing items for the model railroad part of the hobby, and this item in particular can be adapted to 1/25 scale. It is rows of resin louvers, applied to a very this clear decal, which makes applying them quite simple. I cut out 5 rows of louvers, soaked the paper for 10 second, let the glue loosen from the paper backer, and then carefully guided the decal onto the trunk. The clear decal is VERY thin so that the edge disappears under a coat of paint, but it also makes it prone to tearing, so use a light touch. The directions suggest using decal setting solution, but I would recommend that only as a last resort. Placing the decal and then hitting it with a little heat from a hair dryer (set on low) will really snuggle up that decal to the body. If you have any wrinkles you need to smooth out very carefully apply a small amount of setting solution with a small brush. But honestly most applications shouldn't require the setting solution. I used setting solution per the instructions and I really feel it made the decal tear more easily, and gave me some tense moments where three of the louvers separated from the rest. It took a few minutes with a toothpick gently maneuvering them back into place. And finally, the grille. The grille that Revell supplied looks good and can be used with just a little detail painting. However, it comes with molded in electric fan detail, which just won't stand for a traditional hot rod. I'll use this as an opportunity to upgrade. I'm using the piece from the Monogram Blue Bandito, the tooling for which has seen multiple revisions since it started as the Blue Beetle in the early 60's. You can use the rad/shell from any Model A kit you choose. To securely attach it to the frame I used my standard pin and hole method, drilling two small holes into the bottom of the radiator, and then inserting pins. To get the top of the radiator at the right level in comparison to the top of the cowl so it has a nice profile from the side I had to add a .080 x .080 plastic strip to the top of the front crossmember. Glue it in place, and I made the choice to add a little filler to make it all look like one piece. Drill matching holes in the top of the new strip to allow the radiator to pin on top of it. -
"Simple" Revell 30 Model A Coupe. finished 4/11/2022
Mr. Metallic replied to Mr. Metallic's topic in WIP: Model Cars
Thank you. Yes, the further chopped top is resin from Altered States. -
"Simple" Revell 30 Model A Coupe. finished 4/11/2022
Mr. Metallic replied to Mr. Metallic's topic in WIP: Model Cars
Interior- Not a ton of modifications happening here because Revell did a solid job with their interior straight out of the kit, just a few subtle things to help the overall appearance. There is always one thing that jumps out to me when I see these Revell Model A's built if it's not addressed. It's the notches in the sides of the interior where the side panels key into the floor. Those notches are highly visible from underneath. I started the process of addressing this earlier in the build buy making the floor pan sit flush on the frame. This helps hide those notches quite a bit, and you can stop there if you like, but I'm going a step further and just eliminating them altogether. First, select the size of plastic strip you will use to fill the gaps. It helps to select a size slightly larger than the notches themselves. Here is what you need, the floor, and 6 filler pieces. Enlarge the notches lightly to accept the strips. Cut the strips a little long to give you something to hold on to and allow for precise trimming later. Glue your fillers into the notches and let the glue cure. I also took this opportunity to fill the round holes for the crossmember. You may also note that I cut off the tail end of the floor pan to accommodate the new spring crossmember. This will be covered in a later installment. Trim the filler pieces flush with the floor, and then treat the areas with a little filler to blend them in. Then you're ready to prime. The extra holes in the rear axle have also been filled, and the mods to the K-member from a Revell 32 Ford kit have been completed. Now we can address the side panels. Revell made the interesting choice to mold the rear inner fenderwells in conjunction with the interior side panels. They are meant to be a part of the body, so lets make things easier on ourselves and just remove them and attach them to the body. Draw a straight line from the upper rear corner of the pleated interior down to just in front of the fenderwell. Sever the fenderwell insert and glue it to the body. We are going to fill this notch that ends up below the rear windows (arrows), so square up that opening to accept the styrene strip of your choice. You will want to pick a strip that will be flush or taller than the rest of the top of the panel so you can sand it flush. Also clip off the the tabs at the bottom marked with red X's. Here is why we are filling that notch below the back windows. It was probably made to allow space for the clear piece to fit there, but I'll be replacing these windows with acetate, so I don't need the room and this will look better. If you're going to use the kit glass here, omit this mod. The top panel in the pic has been hit with a little filler to the notch, and now has been fully modified and is ready for primer/paint. This is the extent I'll be going with modifications to the interior on this project, but the canvas Revell has provided is great for personalization, including seat swaps and adding detail. -
"Simple" Revell 30 Model A Coupe. finished 4/11/2022
Mr. Metallic replied to Mr. Metallic's topic in WIP: Model Cars
Ok, before I do another step in the build, here's the moment you've all been waiting for, the mock-up... yes, the body is shifted back slightly on the frame. This was a result of me being in a hurry ? The rear axle is also shifted back ? After working on this for a week I was just excited to see it up on 4 wheels finally -
I really want to build a version with that 4 cam motor, or at least put it in something. I have a minty Dream Rod kit that I of course want to build as the DR, but that means I'll have the 4 cam engine left over. I could always throw it in one of the Tiger Shark Toy Fair kits I got cheap at the Ertl store way back when.
-
"Simple" Revell 30 Model A Coupe. finished 4/11/2022
Mr. Metallic replied to Mr. Metallic's topic in WIP: Model Cars
Can you tell me which Shapeways store you found those wheels in please? I will say that I've seen a few of the 3d printed SCOT and Ardun parts around and they are nice, but the Replicas and miniatures Co of Md resin parts are still the best IMHO. -
"Simple" Revell 30 Model A Coupe. finished 4/11/2022
Mr. Metallic replied to Mr. Metallic's topic in WIP: Model Cars
Looks like a chromed early Ford rear end. There are quite a few of those out there, but there is one in full chrome dress in the old Revell 29 Ford pickup, 30 Sedan and 30 Woody station wagon kits. You should be able to drill out the front axle without a problem. The Revell front axle is kind of thick, so I'm not sure what it will look like if drilled. But I might try it. -
"Simple" Revell 30 Model A Coupe. finished 4/11/2022
Mr. Metallic replied to Mr. Metallic's topic in WIP: Model Cars
Armed and dangerous. (sorry, couldn't help myself) Now that we have the front and rear axles sorted out we need arms to locate them to the frame. Revell gives you two different sets of arms for the front axle, one for the channeled version, and one for the body-on-frame version. Select the set for the body-on-frame version and put the other set aside. To locate the front axle I'm using the kit supplied arms, slightly modified. The arm pictured at the top has had the head of the pivot bolt sanded off and is ready to have a hole for a pin drilled through it (marked in red). This area can get delicate, so take your time and make sure you keep the drill bit straight. After the hole is drilled all the way though you can carefully sever the mounting bracket from the arm. I use a photoetch saw blade for this because it is thinner than your standard razor saw. After the bracket is removed glue your pin in the hole on the arm. Once you're done with those mods you'll be left with the arm and bracket as pictured on the bottom here. You are now ready to glue the bracket into it's corresponding notch in the frame and the front suspension mods are essentially complete. Since the spring now occupies the former mounting points for the suspension arms, we need to drill a couple holes, just outboard of the spring to receive the pins in the arms. Those holes are highlighted here in red. On to the rear! First off, that's not blood in the pic. We are going to use that second set of arms meant for the channeled version front axle and repurpose them for the rear. Here on the top arm in the picture I have removed one of the tiny tabs that are meant to locate the arm when you use it on the front axle, but because the rear axle is larger that tab gets in the way. In the second pic you can see I also went ahead and removed that plastic pin and replaced it with a metal one, and drilled a corresponding hole for it in the axle. The hole will be just inboard of that step on the outside of the axle where the brake backing plate will eventually rest. Go ahead and cut off the molded in "wishbone" arms from the axle at this time. Here are the arms, I went ahead and performed the same pin procedure I did on the front arms, but instead of severing the bracket I removed it completely. It's now time to mark and drill your pivot points. Place your spring/axle assembly in the crossmember on the frame. Take your arms and touch the pivot pin with a bit of ink, insert the pin on the other end into the axle, and then press the pivot pin against the frame, keeping the arm level with the axle and parallel to the bottom of the frame. The ink mark that is left tells you where to drill your hole to accept the pin. Drill your hole, and then mock up everything together like this. And here is the frame after the front arm brackets have been molded in and the rest of the frame smoothed out. Note the deletion of the notches for the kit supplied rear suspension arms. Now your suspensions are done. Normally I perform a mock up to check that I am happy with the stance and that everything fits together properly, but I forgot to snap a pic. I'll come back and add it in here later. EDIT- MOCKUP TIME (body is shifted back on frame, rushed photo opportunity) -
Those louvers aren't meant to bring air in for cooling, like a scoop. In old hot rods they were either meant to let hot air out of an enclosed space (engine compartment) or allow air flow through the body that develops at speed (air under the car getting trapped in the interior/trunk) So in this instance they would be allowing air that's trapped under the truck to escape and alleviate any lift it could cause at speed. That being said, that louvered panel is sick. Glad you got it tp print successfully. Now, if you could print it on a thin enough piece that would allow you to bend it slightly to make a trunk lid or roof side panels. Just had a thought, what if you made another louvered panel for your roof insert?
-
This is a cool project. From my experience with Tamiya fillers, they're best used for filling minor imperfections right before final primer due to the fact that they tend to shrink quite a bit. If you're going to do heavier bodywork in the future I would recommend one of the automotive grade 2-part fillers because they don't shrink hardly at all and cure quickly to keep your project moving. I personally use Dolphin Glaze (I know, weird name) that I bought for about $20 on eBay. It will last a long time and tends to stay fresher longer than the fillers that come in cans because this comes in a big pouch, kind of like a tube of toothpaste. Looking forward to seeing your further enhancements to this project
-
DeLorean Time Machine: WIP (Photos Restored)
Mr. Metallic replied to David G.'s topic in WIP: Model Cars
Nicely executed build. Looks like you had fun with it which is the whole point, right? If I was going to ever build this one I'd want to do the Polar Lights with pre-finished body. Good to know that the finish isn't that durable.